What Whmis Stands For

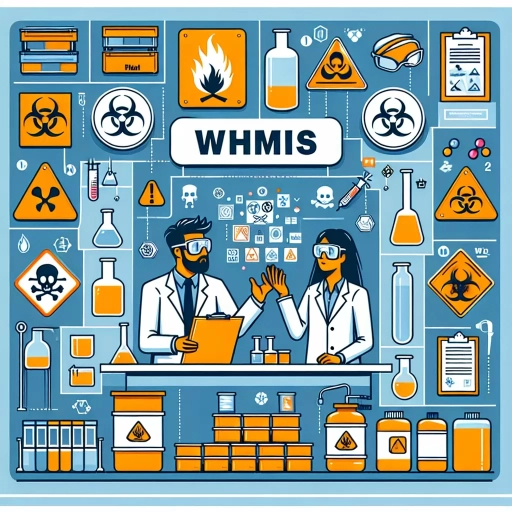
In the realm of workplace safety, few acronyms are as crucial as WHMIS, which stands for Workplace Hazardous Materials Information System. This comprehensive system is designed to protect workers from the dangers associated with hazardous materials by providing essential information and guidelines. At its core, WHMIS encompasses three key components: labels, safety data sheets, and training, each playing a vital role in ensuring that workers are well-informed and equipped to handle hazardous substances safely. Understanding these elements is fundamental to implementing WHMIS effectively, which involves adherence to specific regulations and best practices. This article will delve into the intricacies of WHMIS, starting with an overview of its foundational principles, followed by an examination of its critical components, and concluding with a discussion on implementation and compliance. By grasping these aspects, employers and employees alike can foster a safer and more informed work environment. Let's begin by **Understanding WHMIS: An Overview**.
Understanding WHMIS: An Overview
Understanding WHMIS (Workplace Hazardous Materials Information System) is crucial for ensuring safety and compliance in workplaces that handle hazardous materials. This comprehensive system provides essential information to workers, employers, and regulatory bodies about the safe handling, use, and disposal of hazardous substances. To fully grasp WHMIS, it is important to delve into its core components. First, a **Definition and Acronym Breakdown** will clarify the meaning behind the acronym and the key elements that constitute WHMIS. This foundational understanding sets the stage for a deeper exploration of the system. Additionally, examining the **Historical Context and Evolution** of WHMIS reveals how it has adapted to changing safety standards and regulatory requirements over time. Finally, identifying the **Key Stakeholders Involved** highlights the roles and responsibilities of various parties in implementing and maintaining WHMIS protocols. By understanding these aspects, individuals can better navigate the complexities of WHMIS and contribute to a safer work environment. Let's begin by breaking down the definition and acronym to establish a solid foundation for our exploration of WHMIS.
Definition and Acronym Breakdown
**Understanding WHMIS: An Overview** **Definition and Acronym Breakdown** WHMIS, or the Workplace Hazardous Materials Information System, is a comprehensive Canadian regulatory framework designed to ensure the safe handling, use, and disposal of hazardous materials in the workplace. The acronym itself breaks down into key components that highlight its core objectives: - **W**: **Workplace** - Emphasizing the focus on occupational safety and health. - **H**: **Hazardous** - Indicating the presence of substances that can pose risks to health or safety. - **M**: **Materials** - Referring to the substances themselves, which include chemicals, biological agents, and other hazardous products. - **I**: **Information** - Stressing the importance of providing accurate and accessible information about these substances. - **S**: **System** - Describing the structured approach to managing hazardous materials through classification, labeling, safety data sheets (SDS), and worker training. This system is crucial for protecting workers from chemical hazards by ensuring they have the necessary information to handle these substances safely. WHMIS involves a multi-step process that includes classifying hazardous products based on their physical and health hazards, labeling them with standardized symbols and information, providing detailed safety data sheets for each product, and training workers on how to safely use these materials. By understanding WHMIS, employers and employees can better navigate the complexities of hazardous material management, fostering a safer and more compliant work environment. This integrated approach not only aligns with Canadian regulations but also contributes to a broader culture of workplace safety and health.
Historical Context and Evolution
The historical context and evolution of WHMIS (Workplace Hazardous Materials Information System) are pivotal in understanding its current role in ensuring workplace safety in Canada. WHMIS was first introduced in 1988 as a national standard for the safe handling, use, storage, and disposal of hazardous materials. This initiative was a collaborative effort between the federal, provincial, and territorial governments to harmonize the various regulations and standards that existed across different regions. The primary goal was to provide workers with consistent and reliable information about the hazards associated with the chemicals they handle, thereby reducing the risk of injuries and illnesses. Over the years, WHMIS has undergone significant changes to keep pace with international standards and advancements in chemical safety. One of the most notable updates came in 2015 when WHMIS 2015 was implemented, aligning Canada's system with the Globally Harmonized System of Classification and Labelling of Chemicals (GHS). This alignment ensured that Canadian workplaces could better integrate with global supply chains while maintaining high safety standards. The GHS-based system introduced new classification criteria, hazard communication elements such as safety data sheets (SDSs), and standardized labels featuring pictograms to convey hazard information more effectively. The evolution of WHMIS has also been influenced by technological advancements and changes in workplace practices. For instance, the rise of digital platforms has made it easier for employers to provide workers with access to SDSs and other critical safety information. Additionally, training programs have become more sophisticated, incorporating interactive modules and scenario-based learning to enhance worker understanding and compliance. Regulatory updates have continued to refine WHMIS, addressing emerging issues such as the handling of nanomaterials and biohazards. These updates reflect a commitment to adapting the system to new scientific knowledge and workplace realities. Furthermore, public awareness campaigns have played a crucial role in promoting WHMIS among employers and workers, emphasizing the importance of proper training and adherence to safety protocols. In summary, the historical context and evolution of WHMIS highlight a continuous effort to improve workplace safety through standardized hazard communication. From its inception to its current alignment with GHS, WHMIS has evolved to address new challenges while maintaining its core mission of protecting workers from hazardous materials. Understanding this evolution is essential for appreciating the comprehensive nature of WHMIS and its critical role in ensuring a safe working environment across Canada.
Key Stakeholders Involved
In the context of Understanding WHMIS (Workplace Hazardous Materials Information System), identifying key stakeholders is crucial for the effective implementation and compliance with this regulatory framework. At the forefront are **Employers**, who bear the primary responsibility for ensuring that all hazardous materials in their workplaces are properly labeled, and that employees are adequately trained to handle these substances safely. Employers must also maintain up-to-date Safety Data Sheets (SDSs) and ensure that workers have access to this critical information. **Employees** are another vital stakeholder group, as they are directly exposed to hazardous materials on a daily basis. It is essential for employees to understand the risks associated with the chemicals they work with and to follow the safety protocols outlined by their employers. This includes participating in WHMIS training programs, reading and understanding SDSs, and using personal protective equipment (PPE) as required. **Suppliers** of hazardous materials also play a significant role in the WHMIS system. They are responsible for providing accurate and comprehensive information about the products they sell, including proper labeling and the preparation of SDSs. Suppliers must ensure that their products comply with WHMIS regulations before they are distributed to workplaces. **Regulatory Bodies**, such as Health Canada and provincial occupational health and safety agencies, are key stakeholders in enforcing WHMIS standards. These bodies set and update regulations, conduct inspections, and impose penalties for non-compliance. They also provide guidance and resources to help employers and suppliers meet their obligations under WHMIS. **Health and Safety Professionals** are instrumental in implementing and maintaining WHMIS programs within organizations. These professionals conduct risk assessments, develop safety policies, provide training, and ensure that workplaces are compliant with all relevant regulations. Their expertise is invaluable in creating a safe working environment. **Unions and Worker Representatives** also have a significant stake in WHMIS compliance. They advocate for worker safety, ensure that employers are meeting their obligations, and provide support to employees who may have concerns about hazardous materials in their workplace. Lastly, **Training Providers** offer essential services by delivering WHMIS training programs that equip employees with the knowledge they need to handle hazardous materials safely. These providers must ensure that their training content is accurate, up-to-date, and compliant with WHMIS standards. In summary, the successful implementation of WHMIS relies on the active participation and cooperation of multiple stakeholders. Each group has distinct responsibilities but shares a common goal: to create a safer workplace by managing the risks associated with hazardous materials effectively. By understanding the roles and responsibilities of these key stakeholders, organizations can better navigate the complexities of WHMIS and foster a culture of safety and compliance.
Components of WHMIS: Labels, Safety Data Sheets, and Training
The Workplace Hazardous Materials Information System (WHMIS) is a critical component of workplace safety in Canada, designed to ensure that workers are aware of the hazards associated with the chemicals they use. At its core, WHMIS consists of three key elements: labels, Safety Data Sheets (SDS), and training programs. Each of these components plays a vital role in safeguarding employees from potential dangers. Labels provide immediate visual warnings about the hazards of a chemical, using standardized symbols and information to quickly convey essential safety details. Safety Data Sheets offer more detailed information about the chemical's properties, handling procedures, and emergency response measures. Employee training programs are essential for ensuring that workers understand how to safely handle these chemicals and respond to emergencies. By understanding these components, workplaces can significantly reduce the risk of accidents and ensure a safer environment for all employees. This article will delve into each of these critical aspects, starting with the importance of label requirements and symbols.
Label Requirements and Symbols
Label requirements and symbols are crucial components of the Workplace Hazardous Materials Information System (WHMIS), ensuring that workers can identify and handle hazardous materials safely. Under WHMIS, labels on hazardous products must adhere to specific standards to provide clear and consistent information. These labels are designed to be easily understood by workers, regardless of their language proficiency or technical background. A WHMIS label typically includes several key elements: the product identifier, which is the name or identifier of the hazardous product; hazard statements that describe the nature of the hazard; precautionary statements that provide advice on how to minimize or prevent adverse effects; and pictograms or symbols that visually represent the type of hazard. These pictograms are standardized and include images such as a skull and crossbones for toxicity, a flame for flammability, and an exclamation mark for irritation or other health hazards. The use of these symbols is not arbitrary; each pictogram corresponds to a specific hazard class and category as defined by the Globally Harmonized System of Classification and Labelling of Chemicals (GHS). For instance, the "corrosion" pictogram features two test tubes with a hand and a metal surface being corroded, indicating that the substance can cause severe skin burns and eye damage. Similarly, the "explosive" pictogram depicts exploding bombs, warning of substances that may explode under certain conditions. In addition to these pictograms, WHMIS labels must also include supplier information, such as the name, address, and telephone number of the supplier. This ensures that workers can quickly contact the supplier for additional information or in case of an emergency. The label must be legible and prominently displayed on the container in a manner that ensures it remains visible and intact during normal handling and use. Compliance with these label requirements is mandatory for suppliers of hazardous products in Canada. Non-compliance can result in serious legal consequences, including fines and penalties. Moreover, employers have a responsibility to ensure that all hazardous materials in their workplace are properly labeled according to WHMIS standards. Overall, the careful design and implementation of WHMIS labels play a critical role in protecting worker health and safety by providing essential information about the hazards associated with chemical products. By adhering to these strict guidelines, workplaces can significantly reduce the risk of accidents and ensure a safer environment for everyone involved in handling hazardous materials. This comprehensive approach aligns with the broader objectives of WHMIS, which aims to educate workers about the safe handling of chemicals through labels, Safety Data Sheets (SDS), and training programs.
Safety Data Sheets (SDS) Content
Safety Data Sheets (SDS) are a crucial component of the Workplace Hazardous Materials Information System (WHMIS), providing essential information to ensure the safe handling, use, storage, and disposal of hazardous materials. An SDS is a detailed document that outlines the properties, hazards, and safe handling practices for a specific chemical product. It is designed to be easily accessible and understandable by workers, employers, and emergency responders. An SDS typically consists of 16 sections, each addressing a specific aspect of the chemical's properties and hazards. Section 1 includes the identification of the substance or mixture and the supplier's contact information. Sections 2 through 3 cover hazard identification and composition/information on ingredients, respectively. Sections 4 through 6 provide first aid measures, fire-fighting measures, and accidental release measures. Section 7 details handling and storage requirements, while Section 8 outlines exposure controls/personal protection. Sections 9 through 11 describe physical and chemical properties, stability and reactivity, and toxicological information. Sections 12 through 15 cover ecological information, disposal considerations, transport information, and regulatory information. Finally, Section 16 provides other information such as date of preparation or last revision. The content of an SDS is standardized to ensure consistency across different products and suppliers. This standardization allows workers to quickly locate critical information in emergency situations or during routine handling procedures. For instance, if a worker is exposed to a chemical during an accident, they can refer to Section 4 of the SDS for immediate first aid instructions. Employers are responsible for ensuring that SDSs are readily available to all workers who may be exposed to hazardous materials. This can be achieved through physical copies in a designated area or electronic access through a company's intranet. Regular training on how to read and interpret SDSs is also mandatory under WHMIS regulations to ensure that workers understand the information provided. In addition to their role in workplace safety, SDSs play a critical role in emergency response situations. Emergency responders rely on SDSs to understand the nature of the hazard they are dealing with and to take appropriate actions to mitigate risks. This underscores the importance of accurate and up-to-date information being included in these documents. Overall, Safety Data Sheets are an indispensable tool in maintaining a safe work environment by providing comprehensive information about hazardous materials. By adhering to the standardized format and ensuring accessibility and understanding among workers, employers can significantly reduce the risks associated with chemical handling and contribute to a safer workplace culture.
Employee Training Programs
Employee training programs are a crucial component of any workplace health and safety strategy, particularly when it comes to the implementation of the Workplace Hazardous Materials Information System (WHMIS). WHMIS is designed to protect workers from the hazards of chemicals in the workplace by providing them with the necessary information and training. A well-structured employee training program ensures that workers understand the risks associated with hazardous materials and know how to handle them safely. At the heart of WHMIS training are three key components: labels, Safety Data Sheets (SDS), and training itself. Labels provide immediate visual warnings about the hazards of a chemical, while SDSs offer detailed information on safe handling, use, storage, and emergency procedures. However, these tools are only effective if employees are properly trained to interpret and act upon the information they provide. Effective training programs should include both theoretical knowledge and practical skills, ensuring that employees can recognize and respond to potential hazards. A comprehensive WHMIS training program typically begins with an introduction to the basics of WHMIS, including its history, purpose, and key components. This foundational knowledge sets the stage for more in-depth training on how to read and understand labels and SDSs. Employees should learn how to identify the different types of labels and the information they contain, such as hazard symbols, risk phrases, and precautionary statements. Similarly, they should be taught how to locate and interpret the various sections of an SDS, which includes details on chemical composition, first aid measures, and environmental impacts. Beyond theoretical knowledge, practical training is essential for ensuring that employees can apply their learning in real-world scenarios. This may involve hands-on exercises where employees practice reading labels and SDSs, as well as simulations of emergency situations such as spills or exposure incidents. Role-playing activities can also help reinforce understanding by allowing employees to practice communicating about hazards and safety procedures. Regular updates and refresher courses are also vital to maintain employee proficiency. Chemicals and their associated hazards can change over time, and new regulations or guidelines may be introduced. Therefore, ongoing training ensures that employees remain current with the latest information and best practices. Moreover, effective WHMIS training programs should be tailored to the specific needs of the workplace. Different departments or roles may require different levels of training based on their exposure to hazardous materials. For instance, warehouse staff may need more detailed training on handling and storage procedures compared to administrative staff who may only need general awareness training. In conclusion, employee training programs are indispensable for the successful implementation of WHMIS in any workplace. By combining theoretical knowledge with practical skills and ensuring regular updates, these programs empower workers to safely manage hazardous materials. This not only protects individual health but also contributes to a safer and more productive work environment overall. As a critical component of workplace safety protocols, robust WHMIS training is essential for compliance with regulatory standards and for fostering a culture of safety within organizations.
Implementation and Compliance: Regulations and Best Practices
Implementing and complying with regulations is a multifaceted process that requires a thorough understanding of legislative frameworks, effective workplace strategies, and adherence to best practices. At the heart of any compliance initiative lies a robust legislative framework, which sets the standards and guidelines that organizations must follow. This framework is crucial as it provides the legal foundation upon which all other compliance efforts are built. However, merely understanding the regulations is not enough; organizations must also develop and implement workplace strategies that ensure these regulations are integrated into daily operations. This involves training employees, establishing clear policies, and monitoring compliance continuously. Finally, best practices for compliance are essential to ensure that organizations not only meet but exceed regulatory requirements, fostering a culture of transparency and accountability. By combining these elements—legislative framework, workplace implementation strategies, and best practices—organizations can achieve high levels of compliance and maintain a positive reputation. Let us begin by examining the legislative framework and regulations that underpin all compliance efforts.
Legislative Framework and Regulations
The legislative framework and regulations surrounding Workplace Hazardous Materials Information System (WHMIS) are crucial for ensuring the safe handling, use, and disposal of hazardous materials in Canadian workplaces. WHMIS, which stands for Workplace Hazardous Materials Information System, is a comprehensive system that provides workers with the information they need to safely handle hazardous materials. At its core, WHMIS is governed by federal, provincial, and territorial legislation that mandates the classification, labeling, and provision of safety data sheets (SDSs) for hazardous products. The primary legislative framework for WHMIS is established under the **Hazardous Products Act** and the **Hazardous Products Regulations**, which are enforced by Health Canada. These regulations outline the requirements for suppliers to classify hazardous products, label them appropriately, and provide SDSs that detail the hazards associated with each product. The SDSs must include critical information such as the product's composition, first aid measures, fire-fighting measures, accidental release measures, handling and storage instructions, exposure controls/personal protection, physical and chemical properties, stability and reactivity data, toxicological information, ecological information, disposal considerations, transport information, regulatory information, and other relevant details. Provincial and territorial authorities also play a significant role in enforcing WHMIS through their respective occupational health and safety (OHS) legislation. For example, provinces like Ontario have their own OHS Acts and Regulations that align with federal standards but may include additional requirements or specific enforcement mechanisms. Employers are responsible for ensuring that all workers are trained on WHMIS and that the workplace is compliant with all relevant regulations. This includes conducting regular training sessions, maintaining up-to-date SDSs in accessible locations, ensuring proper labeling of hazardous materials, and implementing control measures to mitigate risks. Compliance with WHMIS regulations is not just a legal requirement but also a best practice for maintaining a safe work environment. Employers who fail to comply with WHMIS regulations can face significant penalties, including fines and legal action. Moreover, non-compliance can lead to serious health risks for workers and potential environmental hazards. Therefore, it is essential for employers to stay updated on any changes to WHMIS regulations and to implement robust compliance programs that include regular audits and training programs. In addition to legal compliance, best practices in WHMIS implementation involve a proactive approach to workplace safety. This includes conducting regular risk assessments to identify potential hazards associated with hazardous materials, implementing engineering controls such as ventilation systems or personal protective equipment (PPE), and fostering a culture of safety where workers feel empowered to report any concerns or incidents related to hazardous materials. By combining rigorous compliance with best practices in workplace safety, employers can ensure that their workplaces are not only legally compliant but also safe and healthy environments for all employees. In summary, the legislative framework and regulations surrounding WHMIS are designed to protect workers from the risks associated with hazardous materials. Through a combination of federal and provincial legislation, employers must ensure that they classify, label, and provide safety data sheets for all hazardous products in their workplaces. By adhering strictly to these regulations and adopting best practices in workplace safety, employers can create a safer and healthier work environment while also avoiding legal penalties.
Workplace Implementation Strategies
When implementing workplace safety strategies, particularly those related to WHMIS (Workplace Hazardous Materials Information System), it is crucial to adopt a comprehensive and structured approach. This begins with thorough training programs that ensure all employees understand the hazards associated with the chemicals they work with, how to read and interpret Safety Data Sheets (SDS), and how to use labels correctly. Effective communication is key; employers should establish clear channels for reporting incidents and near-misses, fostering a culture where employees feel empowered to speak up without fear of reprisal. ### Training and Awareness 1. **Comprehensive Training**: Develop training modules that cover the basics of WHMIS, including the classification of hazardous products, understanding SDSs, and recognizing label elements. Regular refresher courses can help maintain awareness and compliance. 2. **Hands-On Training**: Incorporate practical exercises where employees can practice handling hazardous materials safely and respond to emergency situations. 3. **Role-Specific Training**: Tailor training to specific job roles, ensuring that each employee understands the unique hazards they may encounter. ### Policy Development and Enforcement 1. **Clear Policies**: Establish and communicate clear policies regarding the handling, storage, and disposal of hazardous materials. These policies should be easily accessible and regularly updated. 2. **Enforcement Mechanisms**: Implement robust enforcement mechanisms to ensure compliance. This includes regular audits, inspections, and disciplinary actions for non-compliance. 3. **Continuous Improvement**: Encourage feedback from employees to identify areas for improvement in safety protocols. ### Technology Integration 1. **Digital Tools**: Utilize digital tools such as mobile apps or software platforms to manage SDSs, track chemical inventories, and provide real-time access to safety information. 2. **Automated Systems**: Implement automated systems for tracking training completion, incident reporting, and compliance monitoring. ### Employee Engagement 1. **Safety Committees**: Form safety committees comprising representatives from various departments to oversee safety initiatives and provide a platform for employee input. 2. **Recognition Programs**: Develop recognition programs to incentivize safe practices and reward employees who contribute to a safer work environment. 3. **Open Communication**: Foster an open-door policy where employees feel comfortable reporting concerns or suggesting improvements without fear of retaliation. ### Regulatory Compliance 1. **Stay Updated**: Ensure that all policies and procedures are aligned with the latest regulations and standards set by governing bodies such as Health Canada. 2. **Documentation**: Maintain meticulous records of training sessions, audits, inspections, and compliance activities to demonstrate adherence to regulatory requirements. 3. **Audits and Inspections**: Conduct regular internal audits and inspections to identify gaps in compliance and implement corrective actions promptly. By integrating these strategies into your workplace implementation plan, you can create a robust safety culture that not only complies with WHMIS regulations but also fosters a proactive approach to managing hazardous materials safely. This holistic approach ensures that every aspect of workplace safety is addressed systematically, leading to a safer and more compliant work environment.
Best Practices for Compliance
**Best Practices for Compliance** Implementing and maintaining compliance with regulations such as WHMIS (Workplace Hazardous Materials Information System) requires a structured approach that integrates best practices into daily operations. At the core of effective compliance is a robust training program that ensures all employees understand the hazards associated with the materials they handle and the procedures for safe handling, storage, and disposal. This training should be comprehensive, regularly updated, and tailored to the specific roles and responsibilities of each employee. Another critical best practice is the accurate labeling and signage of hazardous materials. Labels must conform to WHMIS standards, including the use of hazard symbols, risk phrases, and safety precautions. Additionally, Safety Data Sheets (SDSs) should be readily accessible to all employees who work with hazardous substances. These documents provide detailed information on the safe handling, use, storage, and emergency procedures for each chemical. A well-organized inventory management system is also essential for compliance. This involves tracking the quantity and location of hazardous materials, ensuring that only authorized personnel have access to these substances, and implementing a first-in-first-out policy to prevent older materials from becoming obsolete or hazardous over time. Regular audits and inspections are vital for identifying and addressing any gaps in compliance. These should be conducted by trained personnel who can assess whether all procedures are being followed correctly and whether any updates or changes are needed to maintain compliance with evolving regulations. Moreover, fostering a culture of safety within the workplace is crucial. Encouraging open communication where employees feel comfortable reporting incidents or near-misses without fear of reprisal helps in identifying potential hazards early on. Recognizing and rewarding safe practices can also motivate employees to adhere strictly to compliance protocols. Finally, maintaining detailed records of training sessions, audits, inspections, and any incidents involving hazardous materials is indispensable for demonstrating compliance during regulatory inspections. These records should be easily retrievable and kept for a specified period as mandated by relevant regulations. By integrating these best practices into their operations, organizations can ensure not only regulatory compliance but also a safer working environment for their employees. This holistic approach to compliance underscores the importance of ongoing vigilance and continuous improvement in managing workplace hazards effectively.