What Is A Machinist

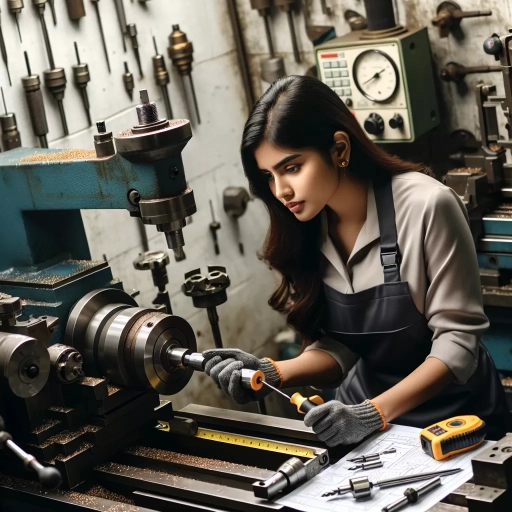
What is a Machinist?
The profession of a machinist is quite fascinating and holds immense importance in the industrial and manufacturing sectors. This article dives into the world of machinists, offering a comprehensive insight into what exactly the role entails, their key responsibilities and tasks, and the various specializations within the field. Initially, we'll outline a clear definition and role overview, offering a basis of understanding for readers who may be unfamiliar with this profession or those seeking to deepen their knowledge of the subject. Subsequently, we'll delve into the key tasks and responsibilities of a machinist, and how their meticulous craftsmanship impacts sectors from automotive to aerospace. Finally, we're going to examine the specializations within the machinist field, which showcase the breadth and depth of this career. One of the fascinating things about being a machinist is that it's a profession that requires precision and a level of expertise that comes from extensive training and experience. Now, let’s move to the detailed explanation and start with the definition and detailed role overview of a machinist.
Definition and Role Overview
A machinist is a skilled professional with a vital role in the manufacturing industry. Essentially, they are the individuals who make things work by transforming pieces of metal into precision parts or tools. They are skilled in using both manual and computer-controlled machinery such as lathes, grinders, and milling machines to create or modify parts used in various industries. These parts could comprise an assortment of objects, from simple nuts and bolts to complex engine parts. The role of a machinist is incredibly varied and carries immense responsibility. A generic day for a machinist includes designing and creating parts based on detailed schematics or blueprints as well as using precise measurements to ensure these parts fit together perfectly within larger systems. In addition to that, they maintain and repair heavy-duty machines, diagnose issues, and even predict component failures. Moreover, they must understand properties of different kinds of metals and how they react under specific conditions. They should be proficient with CAD/CAM technology, which aids them in creating high-quality parts more efficiently. Machinists play an indispensable role in manufacturing and other related processes. They ensure smooth operation of machines and systems, and their expertise gives life to concepts and designs brought forth by engineers. With responsibility for the final product’s quality, they have a direct impact on the safety and reliability of diverse products we use daily, including automobiles, airplanes, and even our household appliances. Furthermore, a machinist maintains a harmonious relationship with other professionals in the industry, for instance, engineers, assemblers, toolmakers, and inspectors. They aid in identifying possible design flaws and provide valuable input to optimize production processes. In essence, the role of a machinist demands a high level of skill, accuracy, and meticulous attention to detail. They are vital cogs in the manufacturing system and play an instrumental role in the creation and maintenance of the physical world around us. Thus, the vocation of a Machinist is a cornerstone in the industrial sector that demands in-depth knowledge, precision, and a knack for problem-solving.
Key Responsibilities and Tasks
The integral role of a machinist encompasses a variety of key responsibilities and tasks. Foremost, machinists are responsible for reviewing blueprints, sketches, or mechanical drawings of a product to be manufactured. This involves examining specifications and work orders and comprehending the complexities of the design, its dimensions, and the materials to be used. The job invariably entails intricate calculations to measure, mark, and arrange the materials before the machining process can commence. Once the groundwork is complete, machinists proceed to the operation of various equipment and machinery, which can range from lathes and millers to grinders and drill presses. The type of machine they use completely depends on the product's requisite specifications. Striking a fine balance between accuracy and efficiency is paramount and it is indispensable for machinists to possess well-honed skills in order to set up, regulate and operate machines that cut or slice metal and other materials. Quality is a foundational element, thus, machinists are also obliged to conduct regular inspections of either the raw materials or the final product. They utilize a wide variety of measuring tools such as calipers, micrometers, and depth gauges to confirm the conformity of the components with the original design. Any troubleshooting or necessary modifications are also handled by them. Advancement in technology has also influenced the machinist field, resulting in the advent of Computer Numerical Control (CNC) machines. These allow machinists to work with greater precision and speed. Thus, a modern-day machinist also assumes the critical responsibility of programming these CNC machines, inputting the design software, and managing the manufacturing process digitally. In addition, machinists are responsible for providing routine maintenance to their machines and equipment, ensuring they are in optimal working condition, minimizing downtime, and maintaining productivity. This includes diagnosing issues, replacing worn parts, and conducting preventative maintenance. Finally, safety cannot be understated in this role. Machinists must adhere to all safety protocols, use personal protective equipment appropriately, and ensure their workspace is free from hazards. They must also possess the knowledge to safely handle hazardous materials and waste, underlining the breadth and depth of responsibilities that fall under the remit of a machinist. Thus, the work of a machinist is intricate, demanding precision, technical knowledge, proficiency in the use of an array of tools and machinery, and a constant eye for safety and quality control.
Specializations Within the Field
In the field of Machining, there are several intriguing specializations, each showing its unique blend of technical skill, precision, and creativity. For instance, a Tool and Die Machinist specializes in creating and repairing cutting tools, gauges, and other tools used in manufacturing processes. They possess a comprehensive understanding of complex geometric shapes and structures. Another specialization is a Mold Machinist, who possesses expertise in designing and making molds used in metal casting or plastic injection molding processes. Furthermore, Industrial Maintenance Machinists fall under a specialization that is crucial for the smooth operation of manufacturing units. They maintain and repair different types of machinery, ensuring their prolonged efficiency and longevity. Meanwhile, a CNC Machinist is another primary specialization in this field. CNC stands for Computer Numeric Control, and these machinists are skilled professionals who precisely operate CNC machines - complex devices that can mill, drill, and shape materials with incredible accuracy using computer-generated commands. Next, a Prototype Machinist works mainly in research and development fields, creating batches of trial products before their mass production. These professionals need an enhanced level of precision as they often handle costly and complex materials. There are also Production Machinists who excel at high-volume production assignments, where speed is just as important as precision. On the contrary, a Manual Machinist is a specialization that may seem a bit archaic in this era of automation, but such professionals are still in demand. Their specialization revolves around machines which are manually controlled, and they are often sought after for custom, small-batch manufacturing or repair jobs. Lastly, in the field of machining, no mention of specialization is complete without discussing the Hydraulic Machinist. These mechnists possess the understanding of hydraulic systems and are skilled at creating and repairing parts of hydraulic equipment. Each of these specializations within the field of machining highlights a distinct set of skills and knowledge. Anyone considering a career as a machinist should carefully explore these specific areas and their requirements. By choosing a particular specialization, machinists can focus their skills and excel in a niche area, increasing their value as professionals. Whether you find the digital precision of CNC machinists fascinating, or you are drawn to the hands-on, meticulous work of a Manual Machinist, there's no denying the opportunities for professional growth and satisfaction in the field of machining.
Skills and Qualifications Required
In today's dynamic workplace, possessing the right set of skills and qualifications is paramount. From technical expertise and soft personal attributes to educational backgrounds and training pathways, every dimension plays an integral role in shaping one's career trajectory. The importance of being technically accomplished in one's field cannot be overstated, as it constitutes the foundation of competence. Soft skills and personal attributes, on the other hand, facilitate effective interaction and team collaboration within the workspace, ensuring harmonious work relationships and optimal productivity. Equally vital is the necessity of education and training pathways, which opens doors to new job prospects, while also allowing one to remain abreast with evolving industry trends. In this comprehensive exploration into the qualifications and skills required for success in the professional sphere, we'll delve into each of these aspects in further detail, beginning with technical skills and knowledge, to help you equip yourself for a highly successful journey in your respective field.
Technical Skills and Knowledge
Technical skills and knowledge are the backbone of a machinist’s capabilities, impacting all facets of their role and directly contributing to both the quality and safety of their work. One of the key technical skills required is understanding and operating machine tools. Machinists must be adept at using a variety of industrial machines such as lathes, milling machines, and grinders to shape metal. Another essential technical skill is blueprint and schematic reading, which enables them to decipher complex diagrams and instructions to ensure the precise creation and assembly of parts. Estimates, measurements, calculations, and a crucially accurate sense of scale are all part of this critical comprehension. In addition, Machinists also need to have a strong understanding and knowledge of different types of metals. This includes the properties and characteristics of various materials (such as hardness, heat resistance etc.), and how they change when shaped or exposed to certain conditions, as well as the appropriate tools and techniques to use with each one. Furthermore, a machinist requires competency in the use of precision measuring tools such as micrometers, calipers, and gauges, to ensure components are manufactured to exact specifications. A proficiency in Computer Numerical Control (CNC) operation is becoming increasingly important due to the prevalence of automated processes in modern manufacturing. Understanding CAD/CAM software, programming machines, setting up feeds and speeds, and monitoring the production process are all key capabilities for a modern machinist. Aside from these specific skills and knowledge, a machinist must also acquire a solid understanding of safety procedures, troubleshooting methods, and preventive maintenance to ensure a smooth operation and minimize potential issues in the workshop. The importance of these technical skills and knowledge is significant. They not only allow a machinist to perform their tasks competently and efficiently, but they also contribute to their problem-solving abilities, innovation capacity, and adaptability. As such, these skills are fundamental for a machinist’s capacity to excel in their role, continuously improve their performance, and contribute positively to their place of work. Moreover, keeping up-to-date with evolving technology, new materials, and advanced machinery forms a key part of their ongoing skill development, as it enables them to stay competitive in their field and adapt to the ever-changing landscape of manufacturing.
Soft Skills and Personal Attributes
Employers looking to hire a machinist not only focus on technical skills and qualifications but also strongly consider soft skills and personal attributes as they contribute significantly to the success of an individual in the role. Soft skills are interpersonal skills that affect your ability to work and interact with others in a work setting whilst personal attributes refer to the unique traits or qualities that make up an individual's character. A vital soft skill for a machinist is problem-solving. With most tasks posing certain complexities, machinists are expected to troubleshoot issues, make accurate calculations, and implement practical solutions. Attention to detail, a personal attribute, is indispensable for this role. Machinists need to work with precision to ensure that pieces are cut and shaped correctly, avoiding costly mistakes and ensuring quality production. Strong communication skills are another pivotal requirement. Machinists often work alongside other professionals; hence the ability to exchange information effectively guarantees seamlessness in the production process. This includes both verbal communication, for day to day interactions, and written communication, for understanding complex blueprints and technical manuals. Additionally, it enhances coordination, eliminating misunderstanding and promoting overall efficiency. Irrefutably, machinists need to be physically fit and possess steadfast stamina. The role involves working with heavy machinery and standing for extended periods, making physical endurance a significant personal attribute. Furthermore, machinists often operate under tight deadlines; hence time-management skills are essential. This includes punctuality, staying organized and prioritizing tasks to maximize productivity in the limited time. Dependability is another crucial personal attribute. Employers look for machinists they can trust to perform their duties consistently and reliably. This means showing up on time, fulfilling responsibilities, and meeting production quotas. A dependable worker helps in maintaining the rhythm of the workplace, resulting in high productivity. Lastly, adaptability plays a key role in the ever-evolving industrial sector. As technology continues to advance, machinists must be open to learning and incorporating new methodologies into their routine. This not only maintains ones' relevance in the field but also enhances efficiency and quality in machining operations. In conclusion, whereas technical expertise and qualifications are vital, the role of machinist equally requires an array of soft skills and personal attributes. Balancing these components undoubtedly improves not only the individual's prowess but also the overall team's performance, thus boosting the company's production quality and output.
Education and Training Pathways
Education and training pathways considerably contribute to the skills and qualifications required to become a competent machinist. Typically, the journey of a machinist begins with a high school diploma, where students take relevant courses in math, drafting, metalworking, and blueprint reading. Building a sound base in high school instigates an initial understanding of the trade and helps develop foundational skills. Post high school, aspiring machinists have several educational pathways to choose from. Vocational schools and community colleges offer diploma programs or associate degrees in precision machining, CNC machining, or related fields. These programs, often lasting one or two years, provide hands-on training on machine tools and techniques. Introductory coursework envelops basic machining practices, while advanced classes deal with CNC programming, multi-axis machining, and precision measurement. Furthermore, the inclusion of internships provides students with the golden opportunity of applying classroom learning to real-world practice. An alternative route is apprenticeships, which combine on-the-job training with classroom instruction. These programs usually last three to five years and enable trainees to earn while they learn. Apprentices gradually gain experience from basic skills to more complex tasks under the supervision of experienced machinists. They acquire vital skills such as setting up, operating, and maintaining machine tools, reading blueprints, measuring and inspecting parts, and programming CNC machines. On completion, apprentices obtain a journeyman's card certifying them as proficient machinists. This is a highly regarded credential in the industry and a pathway leading to advanced roles. Some machinists opt for professional certifications to specialize, enhance credibility, and boost employability. The National Institute for Metalworking Skills (NIMS) offers multiple certification paths appropriate for varying experience levels. Industry standards-based credentials signify that a machinist possess a particular skill set, such as CNC mill, lathe programming, or tool grinding, and meets the requirements of the national standards. Earning these certifications are a testimony to the machinist's commitment to their career, and they garner greater respect and opportunities in the industry. Continuous learning forms an integral part of this profession, as technologies and methods in the manufacturing industry inherently evolve. Employers often sponsor training programs to keep their machinists updated, and individuals also independently pursue further learning to stay ahead in their careers. In conclusion, the educational and training pathways for a machinist span from basic high school subjects to advanced degrees, apprenticeships, and professional certifications. Although the journey is arduous, having these skills and qualifications paves the way to a rewarding and successful career in machining.
Career Path and Opportunities
Choosing the right career path is a vital decision that affects an individual's future growth and job satisfaction. With a broad range of industries and positions to choose from, individuals often find it challenging to identify a path that not only aligns with their skills and interests but also offers growth potential and a promising future outlook. This article will delve into three critical aspects of career planning: Entry-level Positions and Growth Potential, Industry Variations and Specializations, and Future Outlook and Job Market Trends. Initially, one might start with entry-level positions that provide a stepping stone into a career. However, focusing on growth potential is crucial to lasting success. Similarly, understanding industry variations can help tailor one's career path to individual interests and aptitudes. Furthermore, keeping abreast of job market trends is crucial for future-proofing one's career. In the first instance, we will explore Entry-Level Positions and Growth Potential, which is the springboard for every successful professional journey.
Entry-Level Positions and Growth Potential
Entry-level positions in the field of machining provide a gateway for aspiring machinists, offering them an opportunity to showcase their aspiring potential and grow within the company. Starting off as a machine operator, trainee, or a helper, these positions often require minimal or no previous experience and are thus perfect for newcomers aiming to gain practical experiences in manufacturing settings. However, they require good mechanical aptitude, an excellent understanding of mathematics and physics, and a fast-paced learning capacity. Despite being entry-level, these positions offer a unique, hands-on experience and expose one to a vast array of devices and machinery operations. Moreover, the growth trajectory in the machining industry is quite progressive. With the right determination and proactive learning approach, entry-level machinists can rise through the ranks towards more sophisticated roles. These positions may include CNC machinist, a tool and die maker, or a machine setter. Each of these advanced roles entails more responsibilities, demand higher skill-level, and indeed, offer better remuneration. In-depth knowledge of craftsmanship, CAD/CAM software, CNC programming, precision measurement techniques, among other areas, significantly boost your chances of up-scaling in the career ladder. Furthermore, as automation and digitization become more integrated into manufacturing processes, machinists with these advanced skills are becoming increasingly desirable. Continuous learning and training also play a critical role in advancement. Companies often provide on-the-job training opportunities, and external certifications are also available to help improve your skillset. It is notable that apart from vertical climb, one can also opt for lateral movement into related fields such as manufacturing engineering, quality control, and even sales and service of manufacturing equipment, offering even more career avenues. The bottom line is, while entry-level positions in the machining industry might seem tough and challenging due to the rigorous physical work and steep learning curve, they act as stepping stones towards more rewarding roles. Thus, they are extremely crucial in shaping your career path as a successful machinist. With an influx of new manufacturing technologies, it's an exciting time to step foot in this field and explore the myriad of growth opportunities it provides. It's not just about job stability, but the prospect of personal development and the achievement of higher professional goals that make a career as a machinist rewarding and fulfilling.
Industry Variations and Specializations
Industry Variations and Specializations
The field of machinist work comprises both varying industry applications and increasing specializations, contributing to diverse career opportunities. Choosing a specialization is a critical career step for machinists, as it enables them to hone their expertise, drive their professional growth, and open up a variety of job opportunities. To begin with, industries utilizing machinists' skills vary widely, from aerospace manufacturing to automotive industries, and from oil companies to the defense sector. Moreover, this job sector is not limited to manufacturing industries; a machinist with specialized skills can even find employment opportunities in research and development departments of advanced technology industries, where precision and intricacy are paramount. Such diversity reflects the broad utility of machinist work across various industries and the multiple career paths available. As for specializations, evolving technologies and processes in manufacturing have introduced a host of new subfields. Foremost among these are CNC (Computer Numerical Control) Machinists, who apply computer skills to operate and control machine tools, produce components, manage calibration, and perform maintenance. CNC machining has not only revolutionized the industry but also created a surge in demand for skilled personnel, making it a promising specialization. Additionally, aspiring machinists, they can concentrate on tool and die making, focusing on crafting and maintaining specialized precision tools and dies, which are used to manufacture other products. Another up-and-coming specialization is Precision Machining specializing in creating intricate parts and components, often for the medical and aerospace industries. Furthermore, other specializations are available at a more granular level, such as jig and fixture machining, maintenance machining, and production machining. Each of these areas involves a specific application or type of machinery and offers unique advantages and challenges. It is also important to note that the field provides opportunities to advance and transition between areas. For example, one might start as an entry-level machinist, work up to a machine operator role, specialize as a CNC machinist, and eventually become a team supervisor or shop manager. Therefore, the wide variations in industry applications and offering specialization has expanded the career trajectory for machinists, making this field varied and dynamic. With continual professional development, machinists have the opportunity to not only carve a niche for themselves in the industry but also significantly contribute to technological advancements in various sectors. In conclusion, understanding the industry variations and specializations in machinist work is crucial to comprehending the depth of career path possibilities and opportunities available in this field.Future Outlook and Job Market Trends
In the current technologically-driven economic environment, the career path and opportunities for machinists are proliferating. The future outlook and job market trends demonstrate a promising landscape for individuals seeking a career in this field. As more industries continue to explore the potential of automated and computer-aided manufacturing processes, machinists will increasingly find themselves at the forefront of a dynamic and rewarding career trajectory. The US Bureau of Labor Statistics predicts a modest but steady growth of around 3% in machinist jobs over the next decade. This growth is driven by sectors such as aerospace and transportation, where precision parts are essential. Moreover, as technology enables more complex manufacturing designs, industries will seek out machinists capable of translating these designs into high-quality industrial components. This implies more challenging and high-paying opportunities for the skilled machinist. However, the future job trends also suggest a significant shift towards advanced manufacturing techniques. The increasing adoption of Computer Numerical Control (CNC) technologies by industries signals a growing need for machinists trained in this advanced skillset. Traditional machining skills remain vital, but the ability to program, operate, and maintain CNC machines puts any prospective machinist in a competitive position. Moreover, additive manufacturing, often referred to as 3D printing, is predicted to redefine manufacturing processes, further enhancing job prospects for machinists with training in this cutting-edge technology. This is because 3D printing enables rapid prototyping and production of complex designs which would be difficult to achieve through conventional machining methods. But the change is not just limited to the tools used. The job market is also evolving in terms of the type of products that machinists will be working on. Renewable energy is one such booming sector where demand for machinists is projected to increase. As traditional energy sources are gradually replaced by more sustainable options, there will be an increasing need for machinists to manufacture parts for wind turbines, solar panels, and other renewable energy infrastructure. Given these trends, professionals wishing to forge a fruitful career in machining will need to be prepared to continuously update their skills and adapt to new technologies. Vocational schools and community colleges are already updating their curriculum to incorporate advanced manufacturing techniques, and many companies are also offering on-the-job training in these skills. This ensures that machinists are well-armed with the necessary tools to thrive in the evolving job market. In summary, the future outlook for machinists offers a promising landscape, teeming with career growth and skill development opportunities. As industries across the globe continue to innovate and evolve, the role of the machinist becomes ever more critical, creating an environment rich with exciting challenges and rewards for the right professionals.