What Is Dtf

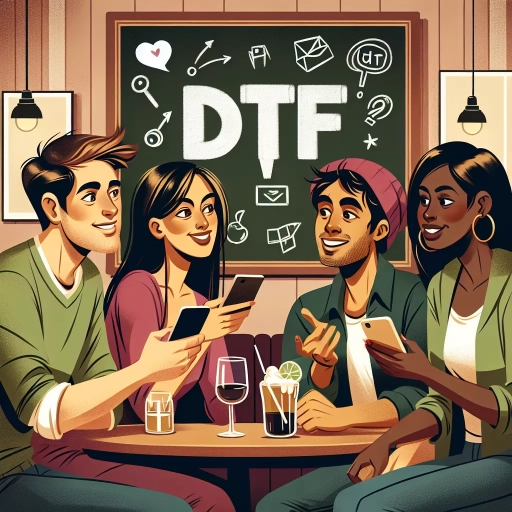
In the realm of modern printing technology, Direct-to-Film (DTF) printing has emerged as a versatile and innovative method that is revolutionizing various industries. This cutting-edge technique offers a unique approach to producing high-quality prints with unparalleled flexibility and durability. To fully appreciate the potential of DTF printing, it is essential to delve into its core components. This article will explore the fundamentals of DTF printing, starting with **Understanding the Basics of DTF Printing**, where we will dissect the key elements that make this technology stand out. We will then examine **The Process and Technology Behind DTF Printing**, uncovering the intricate steps and advanced machinery involved in this process. Finally, we will discuss **Applications and Benefits of DTF Printing**, highlighting how this method is transforming industries from apparel to signage. By understanding these aspects, readers will gain a comprehensive insight into why DTF printing is becoming an indispensable tool in today's printing landscape. Let us begin by **Understanding the Basics of DTF Printing**.
Understanding the Basics of DTF Printing
In the ever-evolving world of textile printing, Direct-to-Film (DTF) printing has emerged as a versatile and highly sought-after technique. This innovative method offers unparalleled flexibility and quality, making it a favorite among printers and designers alike. To fully appreciate the potential of DTF printing, it is essential to delve into its core aspects. This article will provide a comprehensive overview, starting with the **Definition and History of DTF Printing**, which will explore its origins and evolution. We will then examine the **Key Components and Materials Involved**, highlighting the critical elements that make DTF printing so effective. Finally, we will conduct a **Comparison with Other Printing Techniques**, allowing readers to understand where DTF stands in the broader landscape of textile printing. By understanding these fundamental aspects, you will gain a solid foundation in the basics of DTF printing, enabling you to harness its full potential in your creative and professional endeavors. Transitioning seamlessly into the heart of our discussion, let's begin by understanding the basics of DTF printing.
Definition and History of DTF Printing
**Definition and History of DTF Printing** Direct-to-Film (DTF) printing is a versatile and innovative method of textile printing that has revolutionized the industry with its ease of use, flexibility, and high-quality results. Unlike traditional screen printing or direct-to-garment (DTG) printing, DTF involves printing designs directly onto a special film that is then applied to the fabric using heat and pressure. This process eliminates the need for pre-treatment of fabrics, making it particularly appealing for small to medium-sized businesses and hobbyists. The history of DTF printing is relatively recent, emerging as a response to the limitations of other textile printing methods. In the early 2000s, advancements in ink technology and film materials led to the development of DTF. Initially, it was used primarily for promotional products and custom apparel but quickly gained popularity across various sectors due to its adaptability and cost-effectiveness. The process involves several key components: a special DTF film, ink specifically formulated for this method, and a heat press. The ink is printed onto the film using an inkjet printer, and then the film is applied to the fabric using heat and pressure, ensuring a durable and long-lasting finish. One of the significant advantages of DTF printing is its compatibility with a wide range of fabrics, including cotton, polyester, blends, and even stretchy materials like spandex. This versatility makes it an ideal choice for creating custom apparel, accessories, and home textiles. Additionally, DTF printing allows for full-color designs with intricate details, making it suitable for complex graphics and photorealistic images. The environmental impact is also noteworthy; DTF printing requires less water and energy compared to some traditional methods, contributing to a more sustainable production process. Over the years, improvements in technology have enhanced the quality and efficiency of DTF printing. Modern ink formulations offer better color vibrancy and durability, while advancements in film materials have improved adhesion and wash resistance. These developments have solidified DTF's position as a preferred method for many in the textile industry, from small-scale entrepreneurs to large-scale manufacturers. As the demand for custom and personalized products continues to grow, DTF printing stands poised to remain a cornerstone of innovative textile production techniques. Understanding the basics of DTF printing is essential for anyone looking to leverage this technology effectively, whether for personal projects or commercial ventures.
Key Components and Materials Involved
Understanding the basics of DTF (Direct-to-Film) printing involves a deep dive into its key components and materials, which are crucial for achieving high-quality prints. At the heart of DTF printing lies the film itself, typically a PET (Polyethylene Terephthalate) film coated with a special adhesive. This adhesive layer is designed to bond well with various fabrics, ensuring that the printed design adheres securely without compromising the fabric's texture or comfort. The film also features a release liner that protects the adhesive until it is ready for application. Another vital component is the ink used in DTF printing. These inks are specifically formulated to be highly pigmented and durable, ensuring vibrant colors and long-lasting prints. The ink set usually includes CMYK (Cyan, Magenta, Yellow, and Black) colors, which can be combined to produce a wide range of hues. Additionally, some DTF inks may include special additives to enhance print quality and resistance to fading or washing. The printer itself is another critical element. DTF printers are typically inkjet printers modified to handle the unique requirements of printing on film. These printers must be capable of laying down precise amounts of ink to achieve detailed and consistent prints. The print head technology is often advanced, featuring multiple nozzles that ensure high resolution and speed. Heat press machines are also essential for the DTF process. After printing on the film, the design needs to be transferred onto the fabric using heat and pressure. A heat press applies uniform heat and pressure to bond the adhesive layer of the film with the fabric, ensuring a strong and lasting bond. The temperature, pressure, and time settings of the heat press are critical factors that need to be optimized for different types of fabrics. Other supporting materials include powder or adhesive powder, which is applied over the printed film before transferring it to the fabric. This powder helps in creating a strong bond between the film and fabric by enhancing the adhesive properties of the film. It also aids in preventing ink bleeding or smudging during the transfer process. In summary, understanding DTF printing requires knowledge of its core components: the PET film with adhesive coating, specialized inks, modified inkjet printers, heat press machines, and adhesive powders. Each of these elements plays a pivotal role in ensuring that DTF prints are of high quality, durable, and visually appealing. By mastering these key components and materials, users can unlock the full potential of DTF printing for various applications such as custom apparel, promotional products, and more.
Comparison with Other Printing Techniques
When comparing DTF (Direct-to-Film) printing with other printing techniques, several key differences and advantages emerge. Unlike traditional screen printing, which requires a significant setup process and is often cost-effective only for large quantities, DTF printing offers the flexibility to produce small to medium-sized batches without the need for extensive preparation. This makes it particularly appealing for businesses looking to offer customized products without the high minimum order requirements. In contrast to sublimation printing, which is limited to specific types of materials like polyester and ceramics, DTF printing can be applied to a wide range of fabrics including cotton, polyester, and blends. This versatility is a significant advantage as it allows for a broader application across various textile products. Additionally, while sublimation printing requires the fabric to be pre-treated with a special coating, DTF transfers can be applied directly onto the fabric without any pre-treatment, simplifying the production process. Another technique often compared to DTF is heat transfer vinyl (HTV). While HTV is also versatile and can be used on various fabrics, it typically requires more labor-intensive steps such as weeding and cutting individual designs. DTF printing, on the other hand, allows for full-color prints with intricate details and gradients without the need for manual cutting or weeding, making it more efficient for complex designs. Furthermore, DTF printing stands out from digital direct-to-garment (DTG) printing in terms of durability and ease of application. DTG printing directly onto garments can sometimes result in fading or cracking over time, especially if not properly cared for. In contrast, DTF transfers are known for their long-lasting vibrancy and resistance to wear and tear when applied correctly. Overall, DTF printing offers a unique combination of flexibility, versatility, and efficiency that sets it apart from other common printing techniques. Its ability to handle small batches, diverse fabric types, and intricate designs without extensive setup or labor makes it an attractive option for businesses and individuals looking to produce high-quality custom prints efficiently. This adaptability ensures that DTF printing remains a valuable tool in the world of textile customization.
The Process and Technology Behind DTF Printing
Direct-to-Film (DTF) printing has revolutionized the textile industry with its versatility, efficiency, and high-quality output. This innovative technique allows for the creation of intricate designs on a wide range of fabrics, making it a favorite among apparel manufacturers and custom printers. To fully appreciate the capabilities of DTF printing, it is essential to delve into the process and technology behind it. This article will provide a comprehensive overview, starting with a **Step-by-Step Guide to the DTF Printing Process**, which will walk you through the stages involved in transforming digital designs into tangible prints. We will also explore the **Role of Heat Transfer and Adhesives in DTF**, highlighting how these components ensure durable and vibrant prints. Additionally, we will discuss **Advancements in DTF Technology and Equipment**, shedding light on recent innovations that have enhanced the precision and speed of this printing method. By understanding these key aspects, you will gain a deeper insight into the mechanics and benefits of DTF printing, setting the stage for **Understanding the Basics of DTF Printing**.
Step-by-Step Guide to the DTF Printing Process
**Step-by-Step Guide to the DTF Printing Process** The Direct-to-Film (DTF) printing process is a versatile and efficient method for creating custom apparel and accessories. Here’s a detailed, step-by-step guide to help you understand the technology and execution behind DTF printing. 1. **Design Preparation**: Begin by creating your design using graphic design software. Ensure the design is mirrored since it will be applied to the fabric in reverse. Save the design in a high-resolution format suitable for printing. 2. **Printing**: Use a DTF printer to print the design onto a special heat transfer film. This film is coated with a layer of adhesive that helps it stick to fabrics during the application process. The printer applies ink directly onto the film, creating a vibrant and detailed image. 3. **Curing**: After printing, the film needs to be cured to allow the ink to dry and set properly. This step is crucial for ensuring the longevity and durability of the print. Curing can be done using a heat press or an oven, depending on the equipment available. 4. **Weeding**: Once the film is cured, remove the excess film around the design using a weeding tool or by hand. This process leaves only the printed design on the transfer film. 5. **Applying Powder**: Sprinkle a special adhesive powder over the printed design. This powder enhances the adhesion of the film to the fabric during the heat pressing process. 6. **Heat Pressing**: Place the fabric on a heat press, positioning the printed design where desired. Apply moderate to high pressure and heat (usually around 300°F) for about 10-15 seconds. This step bonds the adhesive powder and the film to the fabric. 7. **Peeling**: After heat pressing, allow the fabric to cool slightly before peeling off the transfer film. The design should now be securely attached to the fabric. 8. **Finishing Touches**: Inspect the print for any imperfections and make necessary adjustments. The final product is now ready for use or distribution. This step-by-step guide highlights the precision and care required in each phase of the DTF printing process. By following these steps meticulously, you can achieve high-quality prints that are both durable and visually appealing, making DTF printing an excellent choice for custom apparel and promotional items.
Role of Heat Transfer and Adhesives in DTF
In the realm of Direct-to-Film (DTF) printing, heat transfer and adhesives play pivotal roles in ensuring the quality and durability of the final product. DTF printing involves printing designs directly onto a special film, which is then transferred to the desired substrate using heat and pressure. Here, heat transfer is not just a step but a critical process that dictates the success of the entire operation. Heat transfer in DTF printing is facilitated by a heat press, which applies precise temperatures and pressures to bond the printed film onto the substrate. This process involves several key factors: temperature, pressure, and time. The optimal temperature range typically falls between 300°F to 320°F (150°C to 160°C), while the pressure must be sufficient to ensure full contact between the film and the substrate. The duration of the heat press cycle is also crucial; it needs to be long enough to allow for complete bonding but short enough to prevent damage to either the film or the substrate. Adhesives are another essential component in DTF printing. The adhesive layer on the DTF film is designed to bond strongly with various substrates such as fabrics, plastics, and metals. This layer must have the right balance of tackiness and durability; too little tackiness may result in poor adhesion, while too much can lead to residue issues post-transfer. Modern DTF adhesives are formulated to be flexible yet robust, ensuring that they can withstand wear and tear without compromising their bonding strength. The synergy between heat transfer and adhesives in DTF printing is what makes this technology so versatile and reliable. When correctly applied, these elements ensure that designs are transferred with high fidelity and remain vibrant over time. For instance, in textile applications, the heat transfer process helps to embed the adhesive deeply into fabric fibers, creating a durable bond that resists washing and wear. Similarly, in non-textile applications like plastics or metals, the adhesive layer ensures a strong mechanical bond that withstands environmental stresses. In summary, the interplay of heat transfer and adhesives in DTF printing is fundamental to achieving high-quality results. By optimizing these parameters—temperature, pressure, time, and adhesive formulation—DTF printing can deliver consistent performance across a wide range of substrates. This precision and reliability make DTF an attractive option for various industries seeking to produce durable, visually appealing products with complex designs. As technology continues to evolve, advancements in heat transfer techniques and adhesive formulations are expected to further enhance the capabilities of DTF printing, expanding its applications and improving its efficiency.
Advancements in DTF Technology and Equipment
Advancements in Direct-to-Film (DTF) technology and equipment have significantly transformed the landscape of textile printing, offering unparalleled efficiency, quality, and versatility. At the heart of these advancements is the evolution of DTF printers, which have become more sophisticated and user-friendly. Modern DTF printers now incorporate high-resolution printheads capable of producing detailed prints with vibrant colors, ensuring that even intricate designs are replicated with precision. Additionally, advancements in ink formulations have led to the development of eco-friendly and UV-resistant inks that not only reduce environmental impact but also enhance the durability of printed designs. The integration of automation technologies has further streamlined the DTF printing process. Automated systems for film cutting, weeding, and heat pressing have minimized manual labor, reducing production time and increasing throughput. These automated solutions also ensure consistency in quality, eliminating human error and variability. Furthermore, advancements in software have enabled seamless integration with design tools, allowing for real-time adjustments and previews, thereby enhancing the overall efficiency of the printing process. Another critical area of advancement is in the materials used for DTF printing. Newer films are now more flexible and easier to handle, making them ideal for a wide range of applications from apparel to promotional items. These films also offer improved adhesion properties, ensuring that prints adhere well to various fabric types without compromising on comfort or durability. Moreover, the development of hybrid DTF printers that combine multiple functionalities—such as printing, cutting, and heat pressing—into a single unit has revolutionized small-scale and medium-scale production. These hybrid printers are particularly beneficial for start-ups and small businesses looking to enter the textile printing market without significant capital investment. In terms of sustainability, recent innovations focus on reducing waste and energy consumption. Eco-friendly DTF films and inks are becoming more prevalent, aligning with industry trends towards greener practices. Energy-efficient printers and optimized production processes also contribute to a more sustainable operational model. Overall, the advancements in DTF technology and equipment have not only elevated the quality and efficiency of textile printing but have also expanded its applicability across various industries. As technology continues to evolve, it is likely that DTF printing will become even more integral to the world of textiles, offering innovative solutions that meet both aesthetic and functional demands.
Applications and Benefits of DTF Printing
In the rapidly evolving world of printing technology, Direct-to-Film (DTF) printing has emerged as a versatile and innovative method that is transforming various industries, particularly the apparel and textile sector. This cutting-edge technique offers a multitude of applications and benefits, making it an attractive alternative to traditional printing methods. The article delves into the common uses of DTF printing in the apparel and textile industry, highlighting its widespread adoption and the reasons behind its popularity. It also explores the advantages of DTF printing over traditional screen printing methods, including its flexibility, cost-effectiveness, and superior image quality. Additionally, the environmental impact and sustainability considerations of DTF printing are examined, providing insights into how this technology aligns with modern eco-friendly standards. By understanding these key aspects, readers will gain a comprehensive overview of the applications and benefits of DTF printing, setting the stage for a deeper exploration into the basics of this revolutionary printing technique. Understanding the Basics of DTF Printing will provide a detailed look at how this technology works and its potential for future innovation.
Common Uses in Apparel and Textile Industry
In the dynamic and ever-evolving apparel and textile industry, Direct-to-Film (DTF) printing has emerged as a versatile and highly sought-after technique. This innovative method offers a myriad of applications that cater to various needs and preferences within the sector. One of the most significant uses of DTF printing is in custom apparel production. Unlike traditional screen printing, DTF allows for small to medium-sized print runs without the need for extensive setup costs or minimum order quantities. This makes it ideal for boutique fashion brands, event merchandise, and personalized clothing lines where uniqueness and flexibility are paramount. Another key application lies in promotional products and corporate wear. Companies can leverage DTF printing to create branded items such as t-shirts, hoodies, and hats with intricate designs and vibrant colors. The process ensures high-quality prints that are durable and long-lasting, making them perfect for marketing campaigns and employee uniforms. Additionally, DTF printing is gaining traction in the sports apparel segment due to its ability to produce detailed graphics and logos on a variety of fabric types, including polyester blends commonly used in athletic wear. The textile industry also benefits from DTF printing in home decor and upholstery. Designers can now easily print complex patterns and designs onto fabrics used for curtains, pillow covers, and even furniture upholstery. This opens up new creative avenues for interior designers looking to add personalized touches to living spaces. Furthermore, DTF printing's compatibility with a wide range of fabrics means it can be used for producing high-quality prints on delicate materials like silk or cotton, making it a favorite among luxury textile manufacturers. From a practical standpoint, DTF printing offers several benefits that align well with the demands of the apparel and textile industry. It provides excellent color accuracy and consistency, ensuring that each print meets high standards of quality. The process is also relatively quick compared to other methods, allowing for faster turnaround times which are crucial in meeting tight production deadlines. Moreover, DTF prints are known for their softness and flexibility, making them comfortable against the skin—a critical factor in consumer satisfaction. In summary, DTF printing has revolutionized various aspects of the apparel and textile industry by offering unparalleled flexibility, quality, and efficiency. Whether it's custom fashion lines, promotional products, sports apparel, or home decor textiles, this innovative technique continues to expand creative possibilities while meeting the stringent demands of modern manufacturing. Its ability to deliver high-quality prints on diverse fabric types makes it an indispensable tool for designers and manufacturers alike. As the industry continues to evolve, the applications and benefits of DTF printing are likely to grow even further, solidifying its position as a leading technology in textile production.
Advantages Over Traditional Screen Printing Methods
**Advantages Over Traditional Screen Printing Methods** DTF (Direct-to-Film) printing offers several significant advantages over traditional screen printing methods, making it a preferred choice for many in the textile industry. One of the most compelling benefits is its versatility and flexibility. Unlike screen printing, which requires a separate screen for each color and design, DTF printing allows for full-color prints with intricate details and gradients without the need for multiple screens. This reduces setup time and costs, making it ideal for small to medium-sized orders or custom designs where traditional screen printing might be economically unfeasible. Another key advantage is the ease of use and minimal equipment requirements. DTF printing involves applying a heat transfer film to the fabric, which can be done with basic heat press equipment, eliminating the need for large, expensive screen printing machinery. This accessibility makes it possible for smaller businesses and even hobbyists to produce high-quality prints without a substantial initial investment. In terms of environmental impact, DTF printing is also more sustainable. Traditional screen printing involves using large amounts of water and chemicals for screen preparation and cleanup, contributing to environmental pollution. In contrast, DTF printing uses a dry process that minimizes waste and does not require hazardous chemicals, making it a more eco-friendly option. Additionally, DTF printing offers superior durability and wash resistance compared to traditional methods. The heat transfer process ensures that the ink is deeply embedded into the fabric, resulting in prints that are less prone to fading or peeling off after washing. This makes DTF prints particularly suitable for garments that will be subject to frequent wear and tear. From a design perspective, DTF printing allows for greater creativity and precision. It supports a wide range of colors and can handle complex designs with fine details, enabling designers to bring their most intricate ideas to life without compromising on quality. This level of detail is often difficult or impossible to achieve with traditional screen printing techniques. Lastly, the turnaround time for DTF printing is significantly faster than traditional methods. With no need for screen preparation or drying times between colors, DTF prints can be produced quickly, allowing businesses to meet tight deadlines and satisfy customer demands more efficiently. Overall, DTF printing's advantages in terms of versatility, ease of use, sustainability, durability, design flexibility, and speed make it an attractive alternative to traditional screen printing methods for various applications in the textile industry.
Environmental Impact and Sustainability Considerations
When considering the applications and benefits of Direct-to-Film (DTF) printing, it is crucial to delve into the environmental impact and sustainability considerations associated with this technology. DTF printing, known for its versatility and high-quality output, offers several advantages that align with sustainable practices. Unlike traditional screen printing methods, DTF printing does not require large quantities of water or chemicals for setup and cleanup, significantly reducing the environmental footprint. The process involves transferring ink onto a film which is then applied to the fabric, eliminating the need for extensive pre-treatment and post-treatment processes that are often chemically intensive. Moreover, DTF printing allows for on-demand production, which reduces waste by enabling businesses to print only what is needed. This just-in-time approach minimizes excess inventory and the associated environmental costs of storage and disposal. Additionally, the ink used in DTF printing is generally more eco-friendly compared to other printing methods. Many modern DTF inks are formulated to be free from harmful substances such as lead and phthalates, ensuring a safer working environment for operators and a reduced risk of environmental contamination. Sustainability is further enhanced by the durability of DTF prints. The high-quality finish and long-lasting nature of these prints mean that garments and other materials do not need to be replaced as frequently, contributing to a reduction in the overall lifecycle impact of the product. This longevity also supports a more circular economy by extending the useful life of products and reducing the demand for new, resource-intensive materials. Incorporating DTF printing into production workflows can also support broader sustainability goals by enabling the use of recycled materials and sustainable fabrics. For instance, businesses can opt for recycled polyester or organic cotton fabrics that are then printed using DTF technology, combining sustainable materials with an environmentally friendly printing process. Overall, the environmental impact and sustainability considerations of DTF printing make it an attractive option for businesses seeking to reduce their ecological footprint while maintaining high-quality output. By leveraging the advantages of DTF printing—such as reduced water and chemical usage, on-demand production, eco-friendly inks, durable prints, and compatibility with sustainable materials—companies can contribute to a more sustainable future without compromising on product quality or performance.