What Does Rma Stand For

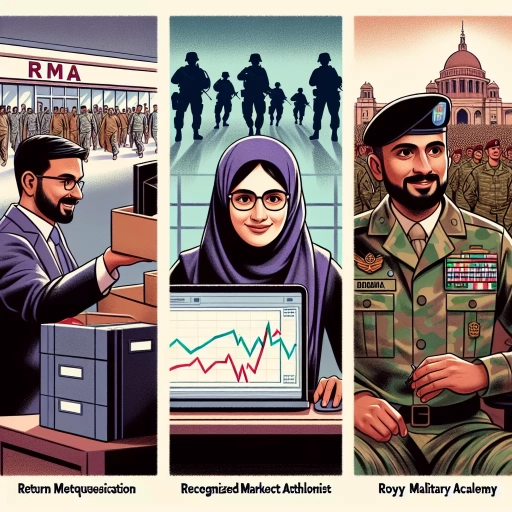
Understanding the Acronym RMA
encompasses anyone who has encountered the term "RMA" within any business context. Short enough to be easily overlooked, this acronym quietly carries significant importance across various industries. At its core, it's an integral tool that creates a more efficient and streamlined system within companies, particularly those dealing within hardware, electronics, and other consumer goods. This high-quality, informative, and engaging article will steer you through an in-depth understanding of the acronym RMA. This tour will consist of three vital pivots: Firstly, we'll explain RMA in its simplest terms, considering its definitions and common usage across different industries. Secondly, we'll delve into a thorough exploration of its industry-specific applications, shedding light on how different sectors have uniquely integrated RMA into their operational systems. Lastly, we'll take a step back in time and examine the historical context of RMA, detailing its development and evolution over years. After these guiding lights, a clear and comprehensive understanding of the term “RMA” will be within your grasp. Starting with the basics; let's dive into the definition and common usage of RMA.
Definition and Common Usage
RMA stands for Return Merchandise Authorization, a protocol used by companies in the retail, manufacturing, and ecommerce industries, among others, to track returned items and navigate the complexities of refund, replacement, and repair processes. An RMA process is initiated when a customer isn't satisfied with a product, thereby requesting to return the product to the manufacturer, distributor, or retailer for either a refund, replacement, or repair. So, when you ask, "What does RMA stand for?" The answer is straightforward - it's an integral aspect of customer service in several industries, synonymous with the product return protocol. The common usage of RMA illustrates its significance in the business realm, specifically in fostering optimal customer relations. For companies offering physical products, the RMA process is instrumental in managing unsatisfied customers. It provides a clearly defined avenue for customers to express discontent with a product and benefits companies by creating a system that helps them track returns, identify product defects, and develop strategies for product improvement. Moreover, the RMA process allows companies to reclaim value from returned products in some instances. For example, a product may be returned because of minor issues that can be fixed, essentially making the product just as useful as before. RMA numbers are usually issued for customers to attach to their return package. These numbers enable quick identification and processing of the returned product once received by the company. The customer fills an RMA form detailing the reasons for the return, thus helping the company gain valuable insights into how to improve their product offerings. Also, in tech and electronics industries, RMAs are issued when a product (like a computer, printer, or any electronic gadget) malfunctions or becomes defective within the warranty period. In such instances, the customer is usually expected to send the product back to the manufacturer for repairs or possibly replacement, all guided by the RMA process. It's, therefore, safe to assert that RMAs are fundamental to smooth business operations, primarily where physical goods are involved. They streamline the return process, mitigate losses, facilitate effective tracking, help to spot recurring issues, and ultimately keep customers satisfied, often turning a potentially negative experience into a positive one. Without an efficient RMA process, businesses may find it hard to manage returns, leading to customer dissatisfaction and potential business loss. Thus, understanding the acronym RMA is vital for both customers and businesses alike, as it stands at the core of effective customer service and product quality management.
Industry-Specific Applications
Industry-specific applications, including RMA (Return Merchandise Authorization), play a critical role in shaping the structure and operation of numerous sectors, including logistics, manufacturing, and e-commerce, among others. RMA is an industry-specific application widely utilised to streamline and manage product returns, an aspect frequent in several industries. This standard industry procedure ensures an efficient, systematic process for exchanging defective goods, tracking the movement of inventory, and maintaining customer service quality. Primarily, in the logistics and supply chain industry, RMA is applied to handle customer product returns. With this procedure, customers are required to get an approval in the form of an RMA number before they can send back the product. This system helps monitor the returned item more effectively, from the initial return request to the final warranty or refund. The RMA process safeguards the interests of both the company and the customer, ensuring that fraudulence is decreased, and transparency is improved. E-commerce and retail sectors also benefit enormously from the RMA application. With the surge in online shopping, return requests have become more common. Implementing an effective RMA procedure can improve customer satisfaction by making the returns process seamless and organized. It also helps businesses manage their inventory by knowing what product is being returned, why it’s being returned, and when it will arrive. Furthermore, the manufacturing industry utilizes RMA systems to control faulty product return from clients. The use of RMA in this context is not only to manage returns but also to do thorough quality checks and analyze faults. By identifying the reason behind product failures or customer dissatisfaction, manufacturers can endeavor to enhance their products, thus enriching their brand quality. Additionally, for companies that deal with IT hardware, such as computer components, networking equipment, and server hardware, RMA is an integral part of their business operations. When a piece of equipment fails, clients need reassurance that their defective items will be replaced or repaired efficiently. An RMA process allows these companies to manage these requirements effectively and maintain their service level agreements with clients. Therefore, the RMA system is beneficial in industry-specific applications across various sectors. Its prominence reaffirms the importance of having comprehensive return policies and efficient tracking systems. It is a crucial part of maintaining product quality, consistent customer service, and analysis of defective goods. Recognizing the RMA process's significance is vital to comprehend how various industries operate and manage customer problems or product issues. After all, understanding the RMA process contributes to an overall appreciative of these industry-specific applications' crucial role.
Historical Context
Historical Context provides vital grounding for our understanding of the acronym RMA, which stands for 'Revolution in Military Affairs'. This term may seem inherently modern given its connection to technological advancements within the defense sector, but the concept actually has deep historical roots and significant implications across the centuries. To truly comprehend and appreciate RMA, a delve into its historical context is warranted. Firstly, back in the late 18th and early 19th centuries, the advent of railroads, telegraphs and breech-loading weapons revolutionized military affairs. These developments effectively transformed the strategies and tactics of war, leading to alterations in the structures and operations of armed forces. In essence, this could be considered an RMA situation. Innovation and technology have always been key drivers shaping the landscape of military operations, and this period was no different. Fast-forwarding to the mid-20th century, we witness another RMA in action, as highlighted by the introduction of nuclear weapons. The aftermath of World War II saw the world grapple with the unprecedented destructive power of nuclear weapons, prompting a profound shift in military strategy and geopolitics. The historical context here served to underscore the emphasis on deterrence, a strategy that has had an enduring impact on how nations approach their defense doctrines, even today. However, the historical context of RMA hit its apogee journey in the late 20th and early 21st centuries, when the advent of information technology has brought forth changes that are considered revolutionary. Precision-guided munitions, stealth technology, reconnaissance satellites, and cyber-warfare are among the cutting-edge tools of modern military strategy and operations. This era's RMA demonstrates again that although technology changes, its role in stirring military transformation remains constant. As we trace the conceptual voyage of RMA through the corridors of history, it becomes evident that the meaning of the term is anchored not just in technological advancement but also in strategic evolution. The understanding of RMA, consequently, demands an appreciation of these historical trends and responses. This adds depth and richness to the term RMA, encouraging a longitudinal perspective which stresses constant evolution rather than abrupt, singular change. By exploring these multiple epochs of history, we peel away the layers of the RMA construct, illuminating a much broader, more nuanced understanding that resonates across centuries of military affairs. The historical context provides a knowledgeable backdrop that allows us to discern continuities and changes, making the study of RMA an even more fascinating discipline.
Applications of RMA in Various Fields
The emerging efficacy of Returned Merchandise Authorization (RMA) has turned heads in various fields due to its cutting-edge applications in improving efficiency. RMA, a crucial part of customer service operations, plays an instrumental role in the disposal, return, refurbishment, and resale of products from consumers to suppliers. Its expanding usage in sectors such as technology and electronics, healthcare and medical devices, and logistics and supply chain management, provides a testament to its transformational potential. Firstly, in technology and electronics industries, RMA has emerged as an innovative tool to manage product returns efficiently, resulting in significant cost savings and improved customer satisfaction. Further, its application in the healthcare and medical devices sector has revolutionised the process of handling returns, fostering increased scrutiny and compliance with safety regulations. Lastly, with its incorporation in logistics and supply chain management, RMA has enhanced operational efficiency and transparency at every echelon. Engaging in an in-depth study of these distinct sectors not only unveils the versatility and scope of RMA but also its capacity to redefine conventional operations. Delving into its role in technology and electronics to begin with, lets us uncover how RMA's return policy framework greatly streamlines pre and post-sale processes.
RMA in Technology and Electronics
In the realm of technology and electronics, RMA or Return Merchandise Authorization plays a pivotal role in maintaining smooth customer transactions and delivering excellent service. RMA is a procedural system used by companies to manage the return of products sold to customers that could be defective, damaged, or not meeting their expected standards of quality. This procedure is vital to industries working with technology & electronics as these fields revolve around goods that are vast, complex, and, at times, susceptible to flaws or defects. Understanding RMA is key to appreciating how technology and electronics companies manage post-sales service effectively. Applications of RMA in the field of technology and electronics are diverse. It can range from dealing with a simple return of a damaged smartphone to managing significant recalls of faulty electronic equipment. RMA procedures allow companies to track the product's issue, identify the reason for the return, and offer suitable resolutions like repair, replacement, or refund. This systematic process ensures customer satisfaction and trust while protecting the company's brand reputation. Additionally, RMA helps to promote efficiency and improve after-sales service in electronics and technology companies. Detailed diagnostic reports generated during the RMA processes allow businesses to identify recurring problems in their products and implement corrective measures. By analyzing these trends, companies can troubleshoot and modify their manufacturing processes, eliminating faulty or substandard practices. This not only results in better products being offered in the market but also reduces instances of returns, saving the company a significant amount in logistics and reverse logistics costs. In the realm of technology, where products are continually evolving and becoming more complex, RMA provides a crucial service to effectively handle and manage returns. Companies like Amazon and Apple, for instance, have efficient RMA procedures in place underscoring the system's importance in the vast and dynamic field of technology and electronics. Moreover, RMA acts as a critical communication channel between the customer and the company. It provides customers a straightforward and user-friendly method to return their purchases if unsatisfied and allows companies to maintain a healthy relationship with their clients by promptly addressing their post-purchase concerns. In conclusion, RMA is a cornerstone tool in the fast-paced world of electronics and technology. It enshrines customer rights and ensures quality control, efficiency, and continuous improvement in products and services – all essential for a business to thrive in this competitive sector.
RMA in Healthcare and Medical Devices
A significant application of Return Merchandise Authorization (RMA) is observed in healthcare institutions and the medical devices sector. Considering the critical nature of the healthcare industry, RMA plays a vital role in securing patient safety and maintaining operational efficiency. Its objective is to control the return and exchange process of faulty or damaged healthcare equipment. With complex and sophisticated machinery being commonplace in healthcare settings, device malfunction could lead to serious healthcare risks. Thus, implementing a comprehensive RMA process ensures that any such malfunctioning device is systematically returned, examined, and replaced or repaired promptly, minimizing interruptions in patient care. For instance, an MRI machine or a cardiac monitor, developing sudden technical issues, can have serious implications. To minimize any potential downtime, a well-structured RMA process provides an organized procedure to troubleshoot the issue, facilitating swift repair or replacement. Furthermore, RMA in healthcare provides a crucial data point for managing quality control, tracking recurring problems, and identifying any persistent device related issues, consequently assisting manufacturers in improving their products. Moreover, the significance of RMA in healthcare is accentuated due to stringent regulatory requirements governing medical devices. The U.S. Food and Drug Administration (FDA), for example, mandates a tracking system that includes methods of device identification, tracking, and recall processes. In this case, RMA systems help healthcare institutions adhere to such regulations, facilitating detailed record-keeping of device performance, maintenance, and associated services including returns. Hence, RMA in healthcare and the medical device sector offers a safety net by providing a systematic procedure to address device-related issues while complying with regulatory standards. Often operating behind the scenes, the impact of RMA on patient safety, service reliability, and device quality cannot be overstated. As technology in healthcare continues to evolve at a rapid pace, the importance and application of RMA processes in the sector are set to become even more critical in the future.
RMA in Logistics and Supply Chain Management
Return Merchandise Authorization (RMA) plays an indispensable role in logistics, supply chain management, and the overall customer satisfaction journey in diverse business operations. RMA incorporates strategies aligned with reverse logistics designed to optimize the process of returning goods for replacement, repair, or refund. In the realm of logistics and supply chain management, RMA contributes to higher efficiency, reduced costs, and enhanced customer relations. An important application of RMA is in product recalls, an inevitable part of many industries, including automotive, electronics, pharmaceuticals, and food & beverages. Through effective management of RMA, companies can streamline the recall process, expedite customer communications and successfully execute the recall strategy, thereby minimizing the regulatory and financial risks linked with product recalls. Equally significant is the role of RMA in product returns. Whether due to buyer remorse, a change of mind, or receiving defective products, product returns are an integral part of e-commerce and retail operations. By integrating a robust RMA system, businesses can effectively track each returned product, control stock levels, and prevent loss due to untracked or unauthorized returns. Moreover, a well-managed RMA system aids in speeding up the returns process, reducing manual intervention, and ultimately leading to customer satisfaction and brand loyalty. Additionally, the implications of RMA in warranty management cannot be underestimated. RMA helps businesses manage warranties efficiently, mitigating the risks and complexities associated with this process. It provides a transparent system where customers can initiate warranty claims and track their status. Simultaneously, businesses can encounter false claims, assess warranty costs, and gain valuable insights into product quality and reliability. RMA also enables businesses to execute effective repairs and refurbishments. With a clear and systematically managed RMA process, companies can reduce turnaround times for repair and refurbishment, minimizing customer dissatisfaction and enhancing brand reputation. Through data accumulated during the RMA process, businesses can also identify recurring product faults and implement corrective measures to improve product quality. Moreover, RMA contributes to the efficient management of excess inventory and obsolete products. It promotes sustainable business practices by assisting in reusing, recycling, or responsibly disposing of unwanted items. In conclusion, the application of RMA in logistics and supply chain management is multi-faceted. It noticeably aids in optimizing various operational aspects ranging from product recalls, returns, warranty, repairs, refurbishments, and the management of excess inventory. Crafted right, the RMA process can promote greater operational efficiency, customer satisfaction, and sustainability while providing a competitive edge for businesses.
Best Practices for Implementing RMA Processes
Increasing customer satisfaction and trust is a key aspect of any successful business, making the Returns Merchandise Authorization (RMA) process strategically valued. Aligning RMA processes with business goals can effectively minimize losses and cultivate customer loyalty. To achieve an optimized RMA process, three best practices need to be implemented: Efficient Return Procedures, Effective Customer Communication Strategies, and astute Quality Control and Analysis. Efficient Return Procedures streamline the return process, reducing time and resource wastage while boosting customer satisfaction. Employing suave Customer Communication Strategies keep the line of communication open, ensuring clarity, transparency, and consequently trust with customers. Furthermore, engaging in thorough Quality Control and Analysis assists in identifying recurring issues, enabling continual improvement of products and procedures. With these best practices in place, businesses can anticipate and effectively manage product returns, turning potential losses into opportunities for further growth and deeper customer relationships. To start with, we will delve deeper into establishing Efficient Return Procedures and how these can impact positively on the entire RMA process.
Efficient Return Procedures
In the context of Return Merchandise Authorization (RMA), efficient return procedures are a cornerstone to enhancing buyer satisfaction and fostering long-term customer loyalty. An RMA process that is meticulously streamlined not only simplifies the tasks for your team but also expedites the process for your buyers, generating an overall positive customer experience. To start, creating a clear and straightforward RMA policy is critical. Customers should easily understand the steps they need to follow to return an item, what items are returnable, and within what timeframe. This policy ought to be easily accessible on your e-commerce platform and emphasized during the sales process. Moreover, automating your RMA procedures where possible can significantly speed up the process and reduce paperwork. Many CRM and ERP systems include functionalities for handling RMAs effortlessly. In your RMA process, a mandatory inclusion should be a pre-printed return label along with the initial shipment. This avails the customer with an effortless, quick and cost-free way to return merchandise. Having easy access to these labels enhances the satisfaction levels of clients and increases the likelihood they will continue doing business with your company. Next, efficient tracking is a fundamental aspect of a comprehensive RMA process. Tracking systems not only provide businesses with an overview of the returned products, but also ensure customers can check the status of their return and reimbursement. By doing so, customers can feel a sense of control over the process, further cementing their trust in your operation. Moreover, upon receiving the returned goods, there should be a strong inspection process to check the condition of products. This will help businesses decide whether the item can be re-sold, needs repairing, or should be discarded - a crucial factor in managing costs. It is vital to communicate with the customer as soon as the inspection is done and the decision on refund or exchange is made. Communication throughout the process is key - customers should be notified at every stage of their return. This could include when you have received the item, when it is being inspected, and when the refund or exchange has been approved or denied. This open and consistent communication can significantly increase customer satisfaction and reduce the volume of customer service inquiries about the status of returns. Finally, it is beneficial to regularly review your return procedures to ensure they are maximally efficient and customer-friendly. Consider seeking customer feedback on the process and making necessary tweaks based on their experiences and suggestions. Mnemonic: this will ensure your RMA process remains a tool for boosting sales, enhancing customer loyalty, and generating brand trust, instead of becoming a source of frustration and loss of revenue.
Customer Communication Strategies
Effective customer communication strategies are paramount when implementing Return Merchandise Authorization (RMA) processes. RMA, an integral part of product return management, necessitates a well-thought-out communication route that ensures customer satisfaction and loyalty while maintaining operational efficiency. The foremost strategy involves setting clear and concise RMA policies. These rules should be easily accessible, ideally on the company's website, detailing the item return conditions, the process to initiate an RMA, and what the customer can expect during each stage. Another integral part of successful customer communication within RMA processes is transparency. The entire RMA shift necessitates a high degree of openness, including acknowledging receipt of the returned product, notifying status updates, and confirming refund or replacement. By keeping the customer informed at each step, companies not only build trust but also help minimize potential misunderstandings or disputes. It's also important to make communication two-way. Allowing customers to ask questions or report issues during the RMA process promotes engagement, resolves issues faster, and showcases commitment to providing excellent service. This requires establishing efficient feedback channels, like email, phone support, or live chat options. Moreover, personalizing communication can significantly enhance the customer's experience. Addressing customers by name in correspondences or using past interactions to tailor conversations shows that you value them as individuals rather than just as a transaction number. Lastly, it's crucial to train customer service representatives to be professional, empathetic, and patient throughout the RMA process. They must be skilled at handling potentially frustrated customers, explaining complex processes in understandable language, and offering helpful solutions. In summary, excellent customer communication strategies should include clear policies, transparency, interactive communication, personalized service, and well-trained representatives. Implementing these strategies in the RMA process can enhance the customer experience, boost satisfaction, and ultimately increase brand loyalty and trust.
Quality Control and Analysis
Quality control and analysis are integral aspects of an effective Return Material Authorization (RMA) process, ensuring the optimum level of product quality and reliability. When implementing RMA best practices, assigning dedicated personnel to conduct rigorous quality control and analysis can significantly enhance the process. Quality control is an evaluative process that checks whether a product or service meets a predefined set of quality standards. Here, specialists meticulously determine if the returned items are defective, and if they are, the nature of the defect is identified. The data recorded from these evaluations is then subject to thorough analysis to identify any recurring trends or patterns. This insight can be invaluable as it assists organizations in pinpointing systemic issues in their production process that may be causing repeated defects or malfunctions of their products. This could include a recurring flaw in design, materials, or manufacturing techniques. Once these root causes are identified, implementations can then be made to rectify these issues and prevent future returns due to a similar problem. Quality analysis also incorporates the testing and inspecting of repaired products before they are shipped back to the customer. This ensures that the returned product is free of defects and performs as expected, enhancing customer satisfaction and loyalty. In the context of RMA, effective quality control and analysis significantly minimize the chances of repeat returns from the same customer, a scenario that would otherwise escalate the cost of RMA processing. Moreover, quality control and analysis serve as a valuable source of actionable customer feedback. By taking into account the specific reasons why a product was returned, organizations can undertake measures to improve product quality and meet customer expectations better. This proactive approach to quality management promotes continuous improvement, a critical aspect of preserving the reputation of a brand, and ensuring long-term survival in a highly competitive marketplace. In essence, quality control and analysis constitute an indispensable aspect of RMA best practices. Through these methods of quality assurance, organizations can directly impact the success of their RMA processes, minimize loss, enhance customer satisfaction and boost overall operational efficiency. It underscores the objective not just of rectifying issues that lead to product return but also of preventing similar issues from occurring in the future. This inherently drives a culture of quality within the organization, contributing to the success of its RMA processes and its overall operations.