What Is A Brushless Motor

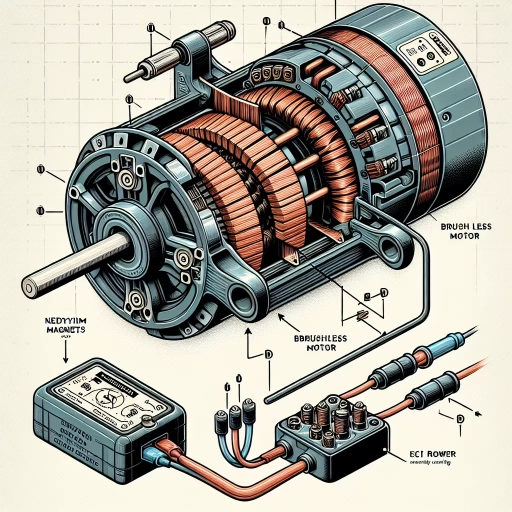
Introduction to Brushless Motors
Brushless motors have revolutionized the world of electric motors, offering superior efficiency, reliability, and performance compared to their brushed counterparts. These motors are integral in a wide range of applications, from consumer electronics and industrial machinery to aerospace and automotive systems. To fully appreciate the significance of brushless motors, it is essential to delve into their definition and basic principles, historical development and evolution, and key components and structure. Understanding the **definition and basic principles** of brushless motors provides a foundational grasp of how they operate. This involves exploring the role of electronic commutation, the absence of brushes, and the interaction between the stator and rotor. The **historical development and evolution** of brushless motors highlight the technological advancements that have led to their current state. From early experiments with brushless designs to modern innovations in materials and control systems, this history underscores the continuous improvement in motor technology. Lastly, examining the **key components and structure** reveals the intricate design elements that contribute to the motor's efficiency and durability. This includes the stator, rotor, control electronics, and other critical parts that work in harmony to achieve optimal performance. By starting with a clear understanding of the **definition and basic principles**, we can build a comprehensive knowledge base that supports a deeper exploration into the historical and structural aspects of brushless motors.
Definition and Basic Principles
**Definition and Basic Principles** A brushless motor, often abbreviated as BLDC (Brushless Direct Current), is a type of electric motor that operates without the use of brushes and a commutator. Unlike traditional brushed motors, which rely on mechanical brushes to transfer electrical current to the rotor, brushless motors employ electronic controllers to manage the flow of current. This fundamental difference in design leads to several key advantages, including higher efficiency, longer lifespan, and reduced maintenance. At its core, a brushless motor consists of a rotor and a stator. The rotor is typically a permanent magnet, while the stator is made up of multiple windings that are energized in sequence by an electronic controller. This controller, often referred to as an ESC (Electronic Speed Controller), uses sensors to monitor the position of the rotor and adjust the current flow accordingly. By precisely timing the energization of each winding, the controller creates a rotating magnetic field that interacts with the permanent magnet on the rotor, causing it to rotate. The basic principles of operation for a brushless motor can be broken down into several stages. First, the ESC receives input from sensors such as Hall effect sensors or encoders that track the position and speed of the rotor. Based on this data, the ESC determines which windings should be energized to maintain optimal torque and efficiency. This process is known as commutation and is crucial for smooth operation. The ESC then sends the appropriate signals to the power electronics, which switch on and off to direct current through the selected windings. One of the primary benefits of brushless motors is their ability to achieve high efficiency due to the absence of frictional losses associated with brushes. This results in less heat generation and longer motor life. Additionally, brushless motors are more reliable and require less maintenance compared to their brushed counterparts because they lack moving parts that can wear out over time. In terms of applications, brushless motors are widely used in various industries including aerospace, automotive, and consumer electronics. They are particularly suited for high-performance applications where reliability and efficiency are paramount. For instance, in electric vehicles, brushless motors are preferred for their ability to deliver consistent power output while minimizing energy consumption. Understanding the definition and basic principles of brushless motors is essential for appreciating their role in modern technology. By leveraging advanced electronics and precise control mechanisms, these motors offer significant improvements over traditional designs, making them a cornerstone in many cutting-edge applications. As technology continues to evolve, the importance of brushless motors will only grow, driving innovation and efficiency across diverse sectors.
Historical Development and Evolution
The historical development and evolution of brushless motors are deeply intertwined with advancements in electrical engineering, materials science, and technological innovation. The journey began in the early 20th century when the first DC motors were developed, which relied on brushes to maintain electrical contact with the rotor. However, these brushes were prone to wear and tear, limiting the motor's lifespan and efficiency. The advent of semiconductor technology in the mid-20th century laid the groundwork for brushless motors. In the 1960s, the introduction of thyristors (silicon-controlled rectifiers) enabled the control of high currents, paving the way for more sophisticated motor designs. The 1970s saw significant progress with the development of power electronic devices such as insulated gate bipolar transistors (IGBTs) and power MOSFETs. These components allowed for precise control over motor speed and torque, making brushless motors a viable alternative to traditional brushed motors. The 1980s witnessed the integration of microcontrollers and digital signal processors, which further enhanced the performance and reliability of brushless motors by enabling sophisticated control algorithms. In the 1990s, advancements in magnetic materials and manufacturing techniques led to the development of high-performance permanent magnets, such as neodymium iron boron (NdFeB), which significantly improved motor efficiency and power density. This period also saw the widespread adoption of brushless motors in various applications, including aerospace, automotive, and industrial automation. The 21st century has seen continued innovation, with advancements in sensorless control techniques, which eliminate the need for position sensors, thereby reducing complexity and cost. The integration of brushless motors with other technologies like lithium-ion batteries and advanced control systems has made them indispensable in modern electric vehicles, drones, and renewable energy systems. Today, brushless motors are characterized by their high efficiency, reliability, and versatility. They offer superior performance compared to traditional brushed motors due to their reduced maintenance requirements, longer lifespan, and ability to operate at higher speeds. The ongoing evolution is driven by research into new materials, improved manufacturing processes, and the integration of artificial intelligence and IoT technologies, ensuring that brushless motors remain at the forefront of technological advancement in the field of electrical engineering. This rich historical context underscores the significance of brushless motors as a cornerstone of modern technology, highlighting their transformative impact across various industries and applications.
Key Components and Structure
In the realm of electric motors, the brushless motor stands out for its efficiency, reliability, and versatility. A key component of understanding these motors lies in their structure and the critical elements that make them function. At the heart of a brushless motor is the stator, which consists of a series of copper windings arranged in a specific pattern to generate a magnetic field. The rotor, on the other hand, is typically made of permanent magnets that rotate within the stator's magnetic field. This design eliminates the need for brushes and a commutator, which are prone to wear and tear in traditional brushed motors. The electronic speed controller (ESC) is another crucial component, acting as the brain of the motor by regulating the flow of electrical current to the stator windings. The ESC ensures that the rotor's magnetic field is always aligned with the stator's field, thereby optimizing torque and efficiency. Additionally, sensors such as Hall effect sensors or optical encoders are often integrated to provide real-time feedback on the rotor's position and speed, allowing for precise control over the motor's operation. The structure of a brushless motor also includes bearings that support the rotor, enabling smooth rotation and minimizing friction. These bearings are typically high-quality components designed to withstand the motor's operational stresses. Furthermore, the motor housing and mounting system are engineered to provide structural integrity and facilitate easy installation in various applications. In terms of construction, brushless motors can be categorized into different types based on their configuration. For instance, the inrunner design features a rotor that is enclosed within the stator, while the outrunner design has the rotor on the outside. Each configuration has its own set of advantages and is suited for specific applications, such as drones, electric vehicles, or industrial machinery. Understanding these key components and their interplay is essential for appreciating the performance and reliability of brushless motors. The absence of brushes reduces maintenance needs and increases lifespan, making these motors ideal for high-performance and long-duration applications. Moreover, advancements in materials and manufacturing techniques have further enhanced their efficiency and durability, solidifying their position as a preferred choice in modern technology. By grasping the fundamental structure and components of brushless motors, one can better appreciate their role in driving innovation across various industries.
How Brushless Motors Work
Brushless motors are a cornerstone of modern technology, powering everything from drones and electric vehicles to industrial machinery. Understanding how these motors work is crucial for appreciating their efficiency and versatility. At the heart of a brushless motor's operation lies the intricate dance of electromagnetic forces, which we will delve into in the section on **Electromagnetic Interaction and Torque Generation**. This fundamental principle is what allows brushless motors to generate torque without the need for mechanical brushes, significantly enhancing their lifespan and performance. Additionally, the role of **Electronic Speed Controllers (ESCs)** is pivotal in regulating the motor's speed and ensuring optimal performance under various conditions. Furthermore, the distinction between **Sensorless vs. Sensored Brushless Motors** highlights different approaches to motor control, each with its own set of advantages and applications. By exploring these key aspects, we can gain a comprehensive understanding of how brushless motors function and why they are so integral to contemporary technology. Let's begin by examining the electromagnetic interaction and torque generation, the very foundation upon which the efficiency and reliability of brushless motors are built.
Electromagnetic Interaction and Torque Generation
Electromagnetic interaction is the fundamental principle behind the operation of brushless motors, enabling the efficient generation of torque. In these motors, electromagnetic forces are harnessed to convert electrical energy into mechanical energy. The process begins with the interaction between magnetic fields produced by the motor's stator (the stationary part) and rotor (the rotating part). The stator consists of multiple windings that, when energized by an electrical current, generate a magnetic field. Conversely, the rotor is equipped with permanent magnets or electromagnets that produce their own magnetic fields. When the stator windings are energized in a sequence controlled by an electronic controller, they create a rotating magnetic field. This rotating field interacts with the magnetic field of the rotor, causing it to rotate. The key to efficient torque generation lies in the precise timing and sequencing of the electrical current supplied to the stator windings. By ensuring that the magnetic field of the stator is always slightly ahead of the rotor's magnetic field, a continuous force is applied, driving the rotor to rotate. The electronic controller plays a crucial role in this process by monitoring the position of the rotor and adjusting the current flow to the stator windings accordingly. This is typically achieved using sensors such as Hall effect sensors or back-EMF (electromotive force) detection. These sensors provide real-time feedback on the rotor's position, allowing the controller to synchronize the electrical pulses with the rotor's movement. This synchronization ensures optimal torque production and minimizes energy loss due to inefficiencies. The design of brushless motors also includes features that enhance torque generation. For instance, the use of multiple poles in both the stator and rotor increases the number of magnetic interactions, thereby increasing the overall torque output. Additionally, advancements in materials and manufacturing techniques have led to more efficient and powerful permanent magnets, further enhancing the motor's performance. In summary, the electromagnetic interaction in brushless motors is a sophisticated interplay between the stator's rotating magnetic field and the rotor's magnetic field, orchestrated by an electronic controller. This interaction results in efficient torque generation, making brushless motors highly reliable and efficient for a wide range of applications, from consumer electronics to industrial machinery. Understanding this principle is essential for appreciating how brushless motors work and why they are preferred over traditional brushed motors in many scenarios.
Role of Electronic Speed Controllers (ESCs)
In the realm of brushless motors, Electronic Speed Controllers (ESCs) play a pivotal role in ensuring optimal performance and efficiency. An ESC is essentially the brain behind the motor, acting as an intermediary between the power source and the motor itself. Its primary function is to regulate the speed of the brushless motor by controlling the frequency and amplitude of the electrical pulses supplied to it. This is achieved through sophisticated algorithms and real-time feedback mechanisms that monitor motor performance and adjust power delivery accordingly. One of the key responsibilities of an ESC is to manage the commutation process, which involves switching the phases of the motor to maintain continuous rotation. Unlike brushed motors, where physical brushes handle commutation, brushless motors rely on ESCs to electronically switch between phases. This electronic commutation not only eliminates wear and tear associated with physical brushes but also enhances reliability and reduces maintenance needs. ESCs also incorporate various safety features to protect both the motor and the entire system. Overheat protection, overcurrent protection, and low-voltage cutoff are common safeguards that prevent damage from excessive heat, current surges, or depleted batteries. Additionally, many modern ESCs come equipped with advanced features such as soft-start capabilities, which gradually increase power to prevent sudden spikes that could strain the motor or other components. Another critical aspect of ESCs is their ability to optimize motor performance under different operating conditions. By adjusting parameters like timing and braking settings, users can fine-tune their brushless motors for specific applications—whether it's high-speed racing, precise control in robotics, or efficient operation in industrial machinery. Some ESCs even support telemetry functions, allowing real-time monitoring of vital parameters such as temperature, voltage, and current draw. The integration of ESCs with other electronic systems further enhances their utility. For instance, in drone technology, ESCs often communicate with flight controllers to ensure synchronized and balanced operation across multiple motors. This synchronization is crucial for maintaining stability and achieving smooth flight characteristics. In summary, Electronic Speed Controllers are indispensable components in the operation of brushless motors. They not only control speed but also manage commutation, implement safety protocols, optimize performance, and integrate seamlessly with other electronic systems. By leveraging these capabilities, ESCs enable brushless motors to operate at peak efficiency and reliability across a wide range of applications.
Sensorless vs. Sensored Brushless Motors
When delving into the world of brushless motors, one crucial distinction to understand is the difference between sensorless and sensored configurations. This distinction significantly impacts the motor's performance, reliability, and application suitability. **Sensorless Brushless Motors:** Sensorless brushless motors operate without the need for position sensors, such as Hall effect sensors or encoders, which are typically used to determine the rotor's position relative to the stator. Instead, these motors rely on back-EMF (electromotive force) detection to estimate the rotor's position. This method involves measuring the voltage generated by the motor's coils when they are not being actively driven. By analyzing this back-EMF, the motor controller can infer the rotor's position and adjust the phase sequence of the power supply accordingly. Sensorless motors are generally simpler and more cost-effective due to the absence of additional sensors, making them ideal for applications where high precision is not critical, such as in many consumer electronics and power tools. However, they may suffer from reduced accuracy at low speeds and during startup, which can lead to potential issues like cogging or hesitation. **Sensored Brushless Motors:** In contrast, sensored brushless motors incorporate position sensors to provide precise information about the rotor's position. These sensors, often Hall effect sensors or optical encoders, feed real-time data to the motor controller, allowing it to accurately synchronize the power supply with the rotor's position. This precise control enhances the motor's performance across a wide range of speeds, including low-speed operations where sensorless motors might struggle. Sensored motors are preferred in applications requiring high precision and reliability, such as in robotics, medical devices, and high-performance drones. While they offer superior performance and smoother operation, they are more complex and expensive due to the additional hardware and software required for sensor integration. **Comparison and Applications:** The choice between sensorless and sensored brushless motors hinges on the specific requirements of the application. For instance, in high-torque applications or those demanding precise control over speed and position, sensored motors are the better choice. However, for cost-sensitive applications where moderate performance is sufficient, sensorless motors can provide a viable alternative. Understanding these differences is crucial for selecting the appropriate motor type and ensuring optimal performance in various industrial, commercial, and consumer contexts. In summary, while both sensorless and sensored brushless motors have their own set of advantages and disadvantages, the key lies in understanding the trade-offs between simplicity, cost, and performance. By selecting the right type of motor based on the specific needs of an application, users can maximize efficiency, reliability, and overall system performance. This nuanced understanding is essential for harnessing the full potential of brushless motor technology across diverse fields.
Advantages and Applications of Brushless Motors
Brushless motors have revolutionized various industries with their superior performance, making them a preferred choice over traditional brushed motors. The advantages of brushless motors are multifaceted, contributing to their widespread adoption in diverse applications. This article delves into the key benefits and uses of brushless motors, highlighting their efficiency, reliability, and longevity. We will explore how these attributes make brushless motors indispensable in industrial, automotive, and consumer sectors. Additionally, we will compare the performance of brushless motors with their brushed counterparts to underscore their superiority. By examining the efficiency, reliability, and longevity of brushless motors, we can better understand why they are the go-to option for many modern applications. Transitioning to the first supporting idea, we will discuss how the efficiency of brushless motors sets them apart from other types of motors, leading to enhanced performance and reduced energy consumption. This is crucial for understanding the foundational advantages that make brushless motors so valuable across various industries.
Efficiency, Reliability, and Longevity
Efficiency, reliability, and longevity are the cornerstone advantages of brushless motors, making them a preferred choice across various applications. Unlike their brushed counterparts, brushless motors eliminate the mechanical wear and tear associated with brushes and commutators. This design innovation significantly enhances efficiency by reducing energy losses due to friction and electrical resistance. As a result, brushless motors achieve higher power-to-weight ratios and better thermal management, leading to improved overall performance and longer operational lifetimes. The absence of brushes also contributes to increased reliability. Brushed motors are prone to brush wear, which can lead to intermittent operation, reduced motor life, and eventual failure. In contrast, brushless motors operate with electronic commutation, which is more robust and less susceptible to mechanical failures. This reliability is crucial in critical applications such as aerospace, medical devices, and industrial automation where downtime can have significant consequences. Longevity is another key benefit of brushless motors. The elimination of brushes and the associated mechanical components means fewer parts that can fail over time. This results in a longer lifespan for the motor, reducing maintenance needs and extending the time between replacements. Additionally, the reduced heat generation in brushless motors due to lower electrical losses further extends their operational life by minimizing thermal stress on internal components. In terms of applications, these advantages make brushless motors ideal for a wide range of uses. In consumer electronics, they power everything from high-performance drones to precision medical equipment. In automotive systems, they are used in electric vehicles and hybrid cars for their efficiency and reliability. Industrial settings benefit from their robustness and longevity in applications such as pumps, fans, and conveyor systems. Even in renewable energy systems like wind turbines and solar panels, brushless motors play a critical role due to their ability to operate efficiently under varying conditions. Overall, the combination of efficiency, reliability, and longevity in brushless motors underscores their versatility and superiority over traditional brushed motors. These attributes not only enhance performance but also reduce operational costs and improve system reliability, making them an indispensable component in modern technology. Whether it's high-speed applications requiring precision or heavy-duty operations demanding robustness, brushless motors consistently deliver superior results, solidifying their position as a cornerstone of modern engineering and technology.
Industrial, Automotive, and Consumer Applications
Brushless motors have revolutionized various industries with their superior performance, reliability, and efficiency. In the industrial sector, these motors are widely used due to their high torque-to-weight ratio and long lifespan. They power machinery in manufacturing plants, such as conveyor systems, pumps, and fans, ensuring continuous operation with minimal downtime. Their ability to operate at high speeds without overheating makes them ideal for applications requiring precision and consistency. In the automotive industry, brushless motors are integral to electric vehicles (EVs) and hybrid electric vehicles (HEVs). They serve as the primary propulsion system in EVs, offering high efficiency and reliability. Additionally, they are used in ancillary systems like power steering, air conditioning, and cooling fans. The compact size and lightweight design of brushless motors make them perfect for automotive applications where space is limited. Consumer applications also benefit significantly from brushless motors. In household appliances such as vacuum cleaners, blenders, and power tools, these motors provide high power density and efficiency. For instance, cordless power tools like drills and saws utilize brushless motors to deliver consistent performance over extended periods without the need for frequent recharging. This enhances user experience by offering more runtime and less maintenance compared to traditional brushed motors. Furthermore, brushless motors are increasingly used in medical devices, drones, and robotics due to their precise control capabilities and low noise operation. In medical equipment like ventilators and dialysis machines, the reliability and quiet operation of brushless motors are crucial for patient care. Drones rely on these motors for stable flight and efficient battery use, while robotic systems benefit from their high precision and durability. The advantages of brushless motors in these applications are multifaceted. They offer reduced maintenance costs due to the absence of brushes, which eliminates wear and tear associated with brush friction. This results in longer motor life and fewer replacements. Additionally, their high efficiency leads to energy savings and extended battery life in portable devices. The compact design allows for greater flexibility in product design, enabling manufacturers to create smaller yet more powerful devices. Overall, the versatility and performance of brushless motors make them an indispensable component across various industries. Their ability to provide reliable operation under diverse conditions has transformed how machinery operates in industrial settings, how vehicles are powered in the automotive sector, and how consumer products function in everyday life. As technology continues to evolve, the role of brushless motors is expected to expand further, driving innovation and efficiency in multiple fields.
Comparison with Brushed Motors
When comparing brushless motors to their brushed counterparts, several key differences emerge that highlight the distinct advantages and broader applications of brushless motors. One of the most significant distinctions lies in the design and operation mechanism. Brushed motors rely on physical brushes and a commutator to switch the current flow to the windings, which can lead to wear and tear, sparking, and eventual failure. In contrast, brushless motors use electronic controllers to manage the current flow, eliminating the need for brushes and commutators. This design change significantly enhances the reliability and lifespan of brushless motors, making them ideal for applications where high uptime and minimal maintenance are crucial. Another critical aspect is efficiency. Brushless motors generally offer higher efficiency due to reduced energy losses associated with friction and sparking. The absence of brushes means less heat generation, which contributes to longer motor life and improved performance under continuous operation. This increased efficiency is particularly beneficial in applications such as electric vehicles, drones, and industrial machinery where energy consumption and performance are paramount. In terms of control and precision, brushless motors excel due to their ability to be precisely controlled by sophisticated electronic controllers. These controllers can adjust speed, torque, and direction with high accuracy, making brushless motors suitable for applications requiring precise control, such as robotics, medical devices, and aerospace systems. The advanced control capabilities also enable features like regenerative braking and dynamic braking, further enhancing their versatility. Additionally, brushless motors are more adaptable to various environmental conditions. They can operate in harsh environments with minimal degradation because they lack the vulnerable components found in brushed motors. This makes them a preferred choice for outdoor and industrial settings where exposure to dust, moisture, or extreme temperatures is common. From an application standpoint, the advantages of brushless motors are evident across diverse sectors. In consumer electronics, they power high-performance devices like cordless power tools and vacuum cleaners. In the automotive sector, they drive electric vehicles and hybrid cars, offering superior efficiency and reliability. In aerospace, their precision and reliability make them critical components in aircraft systems. Furthermore, in renewable energy systems such as wind turbines and solar panels, brushless motors play a vital role in optimizing energy conversion and output. In summary, the comparison between brushless and brushed motors underscores the superior reliability, efficiency, control precision, and adaptability of brushless motors. These attributes make them indispensable in a wide range of applications where performance, longevity, and minimal maintenance are essential. As technology continues to evolve, the role of brushless motors is likely to expand further into new domains, solidifying their position as a cornerstone of modern engineering and innovation.