What Are Three Things Required On A Workplace Label

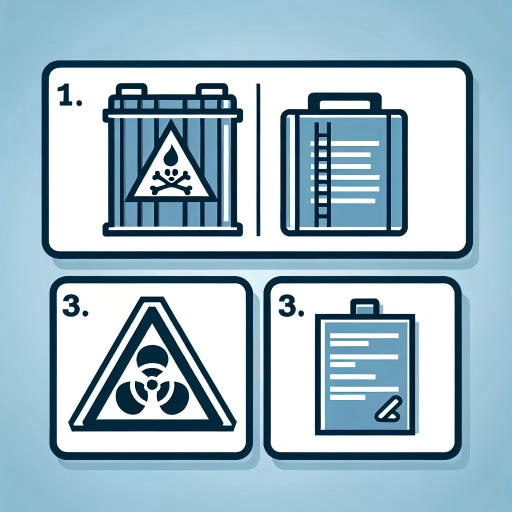
In today's fast-paced and increasingly complex work environments, the importance of clear and comprehensive workplace labeling cannot be overstated. Effective labels serve as critical communication tools, ensuring that employees, visitors, and regulatory bodies have the necessary information to operate safely and efficiently. This article delves into the three essential components that must be included on a workplace label to achieve this goal. First, we will explore the **Essential Information** that labels must convey, such as product names, usage instructions, and handling guidelines. Next, we will discuss the **Safety and Health Warnings** that alert individuals to potential hazards and provide critical safety advice. Finally, we will examine the **Regulatory Compliance** aspects that ensure labels meet legal standards and industry regulations. By understanding these three key elements, organizations can create labels that are not only informative but also protective and compliant. Let's begin by examining the first crucial aspect: **Essential Information**.
1. Essential Information
When it comes to ensuring safety and compliance, having access to essential information about a product is paramount. This article delves into the critical details that users need to know, focusing on three key areas: the product name and manufacturer, hazard identification, and precautionary statements. Understanding the product name and manufacturer provides clarity on who is responsible for the product's quality and safety standards. Hazard identification is crucial as it alerts users to potential risks associated with the product, enabling them to take necessary precautions. Precautionary statements offer guidance on how to safely handle and use the product, minimizing the risk of accidents or adverse effects. By exploring these aspects comprehensively, this article aims to equip readers with the knowledge they need to make informed decisions and ensure safe usage. Here, we will provide a detailed overview of these essential pieces of information, starting with **1. Essential Information**.
1.1 Product Name and Manufacturer
### 1.1 Product Name and Manufacturer When it comes to ensuring compliance with workplace safety regulations, one of the most critical pieces of information on a label is the **Product Name and Manufacturer**. This essential detail serves multiple purposes, making it a cornerstone of effective hazard communication. Firstly, the product name helps identify the substance or material being used, which is crucial for workers who need to handle, store, or dispose of it safely. Knowing the exact name of the product allows employees to quickly refer to safety data sheets (SDS) or other resources for specific handling instructions, thereby reducing the risk of accidents and exposure to harmful substances. Secondly, the manufacturer's name provides a point of contact for further information or support. In cases where additional safety guidance is needed or if there are concerns about product quality, knowing who manufactured the product allows workers and supervisors to reach out directly for clarification. This can be particularly important in situations where a product's safety profile is complex or where there have been changes in formulation that might affect its handling. Moreover, including the manufacturer's name on the label enhances accountability. It ensures that the producer of the product takes responsibility for providing accurate and comprehensive safety information, which aligns with regulatory requirements such as those set by OSHA (Occupational Safety and Health Administration) in the United States. This accountability mechanism helps maintain a culture of safety within workplaces by ensuring that manufacturers adhere to stringent standards for labeling and hazard communication. In summary, the product name and manufacturer's details are fundamental components of workplace labels. They facilitate safe handling practices, provide a resource for additional information, and promote accountability among manufacturers. By including these details prominently on labels, workplaces can significantly reduce risks associated with chemical exposure and other hazards, creating a safer environment for all employees. This adherence to labeling standards is a key aspect of maintaining compliance with essential workplace safety regulations.
1.2 Hazard Identification
**1.2 Hazard Identification** Hazard identification is a critical component of workplace safety, serving as the foundation for effective risk management and compliance with regulatory standards. In the context of workplace labeling, hazard identification involves clearly communicating the potential dangers associated with a substance or product to ensure that employees, visitors, and emergency responders are aware of the risks involved. This process is particularly important for substances classified as hazardous under the Globally Harmonized System of Classification and Labelling of Chemicals (GHS), which mandates specific labeling requirements to standardize safety information globally. When identifying hazards on a workplace label, it is essential to consider several key elements. First, the label must include **pictograms** or symbols that visually represent the type of hazard. These pictograms are standardized under GHS and include images such as a skull and crossbones for toxicity, a flame for flammability, and an exclamation mark for irritation or other health hazards. These symbols provide immediate visual cues about the nature of the hazard, which is crucial in emergency situations where time is of the essence. Second, the label should include **hazard statements** that describe the nature and degree of the hazard. These statements are also standardized and provide detailed information about the specific risks associated with the substance. For example, "Toxic if swallowed" or "Causes severe skin burns and eye damage" are examples of hazard statements that clearly convey the potential harm. Third, **precautionary statements** must be included to advise on safe handling, use, storage, and disposal practices. These statements provide guidance on how to mitigate or prevent adverse effects, such as "Wear protective gloves/protective clothing/eye protection/face protection" or "Do not breathe dust/fume/gas/mist/vapors/spray." By combining pictograms, hazard statements, and precautionary statements, workplace labels ensure that all stakeholders have comprehensive information to handle substances safely. In summary, hazard identification on workplace labels is a multifaceted process that relies on standardized pictograms, hazard statements, and precautionary statements to communicate critical safety information effectively. This approach not only enhances workplace safety but also ensures compliance with international safety standards, thereby protecting employees and the environment from potential hazards. By understanding and adhering to these labeling requirements, organizations can significantly reduce the risk of accidents and injuries, fostering a safer and more responsible work environment.
1.3 Precautionary Statements
When it comes to ensuring safety in the workplace, one of the critical components is the inclusion of precautionary statements on labels. These statements are designed to alert workers to potential hazards and provide them with the necessary information to handle substances safely. Under the Globally Harmonized System of Classification and Labelling of Chemicals (GHS), precautionary statements are categorized into four types: prevention, response, storage, and disposal. **Prevention Statements** are aimed at preventing adverse effects from occurring in the first place. These might include instructions such as "Wear protective gloves/protective clothing/eye protection/face protection," or "Avoid breathing dust/fume/gas/mist/vapors/spray." These statements are crucial because they inform workers about the personal protective equipment (PPE) they need to use and how to avoid exposure to hazardous substances. **Response Statements** provide guidance on what actions to take in case of an emergency or exposure. For example, "If on skin (or hair): Take off immediately all contaminated clothing. Rinse skin with water/shower" or "If inhaled: Remove person to fresh air and keep comfortable for breathing." These statements are vital for immediate response and can significantly reduce the severity of an incident. **Storage Statements** offer advice on how to store substances safely to prevent accidents. Examples include "Store in a well-ventilated place. Keep cool" or "Store locked up." Proper storage is essential to prevent chemical reactions, fires, or other hazardous situations. **Disposal Statements** guide workers on how to dispose of substances safely. These might include "Dispose of contents/container to an approved waste disposal plant" or "Collect spillage." Proper disposal is crucial to prevent environmental contamination and ensure that hazardous materials do not pose a risk after their use. Incorporating these precautionary statements on workplace labels ensures that workers are well-informed about the risks associated with the substances they handle and know how to mitigate those risks effectively. This not only enhances workplace safety but also complies with regulatory requirements, making it an essential component of any workplace safety protocol. By understanding and adhering to these statements, workplaces can significantly reduce the likelihood of accidents and create a safer environment for everyone involved.
2. Safety and Health Warnings
In today's fast-paced and often hazardous environments, understanding safety and health warnings is crucial for preventing accidents and ensuring well-being. These warnings are not just mere cautions but critical pieces of information that can save lives. This article delves into the essential components of safety and health warnings, breaking them down into three key areas: **Hazard Pictograms**, **Signal Words**, and **Risk Phrases**. Hazard Pictograms provide visual cues that quickly convey the nature of potential dangers, while Signal Words such as "Danger" and "Warning" alert individuals to the severity of risks. Risk Phrases, on the other hand, offer detailed descriptions of the hazards associated with a substance or situation. By understanding these elements, individuals can better navigate potentially hazardous situations and make informed decisions. This comprehensive overview is designed to equip readers with the knowledge necessary to interpret and respond to safety and health warnings effectively, leading seamlessly into the **Essential Information** section that follows.
2.1 Hazard Pictograms
### 2.1 Hazard Pictograms Hazard pictograms are a crucial component of workplace safety and health warnings, serving as visual cues that quickly communicate potential dangers to employees. These pictograms are standardized symbols designed to be universally understood, transcending language barriers and ensuring that all workers, regardless of their linguistic background, can recognize and respond appropriately to hazards. The Globally Harmonized System of Classification and Labelling of Chemicals (GHS) has established a set of nine hazard pictograms that are widely adopted across industries. These include symbols for explosive, flammable, oxidizing, corrosive, toxic, harmful or irritant, health hazard, environmental hazard, and gas under pressure. Each pictogram is carefully designed to convey specific types of hazards. For instance, the explosive pictogram features a bursting bomb, indicating substances that may explode or react violently. The flammable pictogram depicts flames, warning of substances that can catch fire easily. The corrosive pictogram shows a hand and surface being corroded, signaling substances that can cause severe skin burns and eye damage. These visual representations are not only intuitive but also immediate in their impact, allowing workers to take necessary precautions without needing to read detailed text. The use of hazard pictograms on workplace labels enhances safety in several ways. Firstly, they provide instant recognition of potential dangers, enabling workers to act swiftly in emergency situations. Secondly, they ensure compliance with regulatory standards, as many jurisdictions mandate the use of GHS-compliant labeling. Thirdly, they contribute to a safer work environment by fostering a culture of awareness and vigilance among employees. By integrating these pictograms into workplace labeling, employers can significantly reduce the risk of accidents and injuries, thereby protecting both their workforce and their operations. In addition to their practical benefits, hazard pictograms also play a critical role in employee training and education. They serve as teaching tools that help workers understand the nature of various hazards and how to mitigate them. This educational aspect is particularly important for new employees or those transitioning to different roles within the workplace. By familiarizing workers with these standardized symbols, employers can ensure that everyone is equipped with the knowledge needed to handle hazardous materials safely. In summary, hazard pictograms are essential elements of workplace safety and health warnings. They provide immediate visual cues that alert workers to potential dangers, enhance compliance with regulatory standards, and contribute to a safer work environment. Their inclusion on workplace labels is a critical step in ensuring that all employees are aware of and prepared to handle the hazards they may encounter on the job.
2.2 Signal Words
In the context of workplace safety and health warnings, signal words play a crucial role in communicating the level of hazard associated with a particular substance or situation. Signal words are standardized terms used on labels to alert workers to potential dangers and guide their actions accordingly. There are two primary signal words: "Danger" and "Warning." **Danger** is used to indicate an immediate hazard that can cause severe injury or death. This signal word is reserved for situations where there is a high probability of serious harm if proper precautions are not taken. For example, a label on a container of highly toxic chemicals might use the word "Danger" to emphasize the severe health risks associated with exposure. On the other hand, **Warning** is used for hazards that could result in injury or illness but are not as severe as those indicated by "Danger." This signal word alerts workers to potential risks that require caution but do not pose an immediate threat of severe harm. For instance, a label on a machine that could cause physical injury if not operated correctly might use the word "Warning." The use of these signal words is critical because they help workers quickly understand the level of risk involved and take appropriate actions to mitigate those risks. By standardizing these terms, organizations ensure consistency across different workplaces and products, reducing confusion and enhancing overall safety. Additionally, signal words are often accompanied by other essential information such as hazard statements, precautionary statements, and pictograms to provide a comprehensive understanding of the hazards present. In summary, signal words are a vital component of workplace labels, serving as a clear and immediate indicator of potential hazards. By distinguishing between "Danger" and "Warning," these words help workers prioritize their safety actions and respond appropriately to different levels of risk. This clarity is essential for maintaining a safe working environment and ensuring compliance with safety regulations. As part of the broader framework of safety and health warnings, signal words contribute significantly to preventing accidents and protecting worker well-being.
2.3 Risk Phrases
When it comes to ensuring safety and health in the workplace, one of the critical components is the use of risk phrases on labels. These phrases, often denoted as "R-phrases," are part of a broader system designed to communicate potential hazards associated with chemical substances. Under the subtitle "2. Safety and Health Warnings," understanding risk phrases is essential for compliance and employee safety. Risk phrases are standardized warnings that highlight specific dangers related to the handling, storage, and use of chemicals. For instance, R-phrases such as "R20: Harmful by inhalation" or "R36: Irritating to the eyes" provide immediate and clear information about the potential risks involved. These phrases are typically used in conjunction with safety phrases (S-phrases) which offer advice on safe handling, storage, and emergency procedures. The combination of R-phrases and S-phrases ensures that workers are well-informed about both the hazards and the necessary precautions. In a workplace setting, the inclusion of risk phrases on labels is mandated by various regulatory bodies to protect employees from chemical hazards. For example, the European Union's Classification, Labelling and Packaging (CLP) Regulation requires that all hazardous chemicals be labeled with appropriate R-phrases to alert users to potential dangers. This regulatory framework ensures consistency across different countries and industries, making it easier for workers to understand and respond to chemical hazards. The use of risk phrases also extends beyond compliance; it is a proactive measure to prevent accidents and injuries. By clearly indicating the risks associated with a chemical, employers can ensure that employees take necessary precautions such as wearing personal protective equipment (PPE), following specific handling procedures, and being prepared for emergency situations. This not only safeguards the health and well-being of workers but also contributes to a safer and more efficient work environment. In summary, risk phrases are a vital component of workplace safety and health warnings. They provide critical information about chemical hazards, enabling workers to take appropriate measures to mitigate risks. As part of a comprehensive labeling system that includes safety phrases and other safety information, risk phrases play a crucial role in maintaining a safe and compliant workplace. By understanding and adhering to these risk phrases, employers can significantly reduce the likelihood of accidents and ensure a healthier work environment for all employees.
3. Regulatory Compliance
In today's complex and highly regulated business environment, regulatory compliance is a critical aspect that companies must adhere to in order to ensure operational integrity and avoid legal repercussions. This article delves into the essential components of regulatory compliance, particularly focusing on three key areas: compliance with GHS (Globally Harmonized System of Classification and Labelling of Chemicals) standards, adherence to local regulations, and the mandatory label elements that must be included on chemical products. Understanding these elements is crucial for businesses to navigate the intricate landscape of regulatory requirements effectively. By exploring these topics in depth, we aim to provide a comprehensive guide that helps organizations maintain compliance and avoid potential pitfalls. This introduction sets the stage for a detailed examination of these critical aspects, leading seamlessly into the essential information that follows. --- **1. Essential Information**
3.1 Compliance with GHS Standards
Compliance with the Globally Harmonized System of Classification and Labelling of Chemicals (GHS) is a critical aspect of regulatory compliance in the workplace, particularly when it comes to labeling chemicals. The GHS standards provide a unified approach to classifying and communicating the hazards of chemical substances, ensuring that workers are adequately informed and protected. For workplace labels to be GHS-compliant, they must include three essential elements: **hazard statements**, **precautionary statements**, and **pictograms**. **Hazard statements** are concise phrases that describe the nature of the chemical hazard. These statements are assigned based on the classification of the chemical and provide clear information about the potential risks associated with its use. For example, a flammable liquid might have a hazard statement like "Highly flammable liquid and vapour." This information is crucial for workers to understand the immediate dangers posed by the chemical. **Precautionary statements**, on the other hand, offer advice on how to minimize or prevent adverse effects resulting from exposure to or improper handling of the chemical. These statements can include recommendations for safe handling, storage, and disposal practices. For instance, a precautionary statement for a corrosive substance might read, "Wear protective gloves and eye/face protection." These statements help workers take proactive measures to ensure their safety. **Pictograms** are visual symbols used to convey hazard information quickly and effectively. GHS specifies nine pictograms that correspond to different types of hazards, such as explosive, flammable, toxic, and corrosive substances. These pictograms are designed to be easily recognizable and understood across different languages and cultures, making them an essential component of GHS-compliant labels. For example, a label for a toxic substance would feature the skull and crossbones pictogram, immediately alerting workers to the potential danger. By including these three elements—hazard statements, precautionary statements, and pictograms—workplace labels ensure that workers have the necessary information to handle chemicals safely and responsibly. This not only helps in preventing accidents but also fosters a culture of safety and compliance within the workplace. Adhering to GHS standards for labeling is thus a fundamental requirement for maintaining a safe and healthy work environment.
3.2 Adherence to Local Regulations
Adherence to local regulations is a critical component of maintaining regulatory compliance in the workplace, particularly when it comes to labeling. Ensuring that workplace labels comply with local regulations not only helps in avoiding legal repercussions but also contributes significantly to workplace safety and efficiency. Here are three key aspects that highlight the importance of adhering to local regulations for workplace labels: 1. **Safety Standards**: Local regulations often mandate specific safety standards for labeling hazardous materials, equipment, and areas. For instance, the Occupational Safety and Health Administration (OSHA) in the United States requires that hazardous chemicals be labeled with information such as the chemical name, hazard statements, and precautionary statements. Adhering to these standards ensures that employees are aware of potential dangers and can take necessary precautions to avoid accidents. 2. **Consistency and Clarity**: Local regulations typically specify the format, content, and placement of labels to ensure consistency and clarity. This consistency helps in reducing confusion among employees and visitors, making it easier for them to understand the information provided on the labels. For example, the use of standardized symbols and color codes can quickly communicate critical information about hazards or instructions without requiring extensive reading. 3. **Legal Compliance**: Non-compliance with local regulations can result in severe penalties, fines, and even legal action. By adhering to local regulations, organizations demonstrate their commitment to legal compliance and ethical business practices. This not only protects the organization from legal liabilities but also enhances its reputation and trustworthiness among stakeholders. Moreover, regular audits and inspections become smoother when all labeling is in accordance with local laws, reducing the risk of non-compliance issues. In summary, adherence to local regulations for workplace labels is essential for ensuring safety, maintaining consistency, and complying with legal requirements. By following these regulations meticulously, organizations can create a safer, more efficient work environment while avoiding potential legal and financial consequences. This proactive approach to regulatory compliance underscores the importance of diligent adherence to local standards in all aspects of workplace labeling.
3.3 Mandatory Label Elements
In the realm of workplace safety, adherence to regulatory compliance is paramount, and one crucial aspect of this is the inclusion of mandatory label elements. Under the umbrella of 3. Regulatory Compliance, understanding what constitutes a compliant label is essential for ensuring a safe and informed work environment. Specifically, 3.3 Mandatory Label Elements outlines the critical components that must be present on any workplace label to meet legal and safety standards. First and foremost, **hazard identification** is a fundamental element. This involves clearly indicating the type of hazard associated with the substance or equipment being labeled. For instance, labels must specify if a chemical is toxic, flammable, corrosive, or poses other risks. This information is typically conveyed through standardized symbols and pictograms that are universally recognized, ensuring that workers can quickly identify potential dangers regardless of their language proficiency. Second, **precautionary statements** are another mandatory label element. These statements provide guidance on how to safely handle the substance or equipment to prevent accidents. They may include instructions such as wearing personal protective equipment (PPE), avoiding certain conditions like heat or sparks, or following specific procedures for use and disposal. By including these statements, labels empower workers with the knowledge needed to mitigate risks effectively. Third, **supplier information** must also be included on workplace labels. This typically involves the name, address, and contact details of the supplier or manufacturer. This information is vital for several reasons: it allows workers to access safety data sheets (SDS) which provide detailed information about the substance; it facilitates communication in case of emergencies or inquiries; and it ensures accountability by tracing the origin of the product. In summary, the inclusion of hazard identification, precautionary statements, and supplier information on workplace labels is not just a regulatory requirement but a cornerstone of workplace safety. These elements collectively ensure that workers are well-informed about potential hazards and know how to handle substances and equipment safely. By adhering to these mandatory label elements, organizations not only comply with regulatory standards but also foster a culture of safety and responsibility within their workforce. This proactive approach to labeling significantly reduces the risk of accidents and enhances overall workplace well-being.