What Is Gross Weight

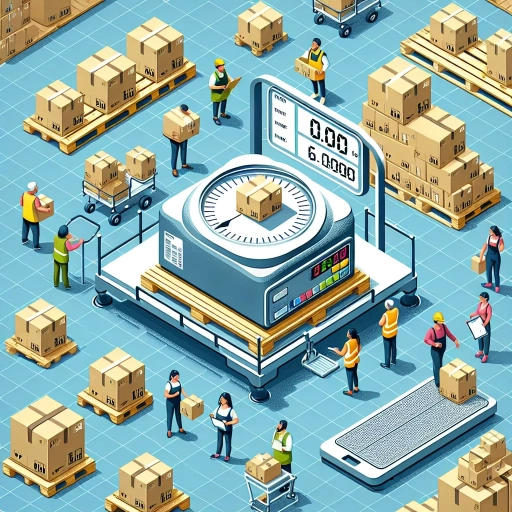
In the realm of logistics, transportation, and engineering, the concept of gross weight plays a crucial role in ensuring safety, efficiency, and compliance with regulations. Gross weight, often misunderstood or overlooked, is a fundamental metric that encompasses the total weight of a vehicle, cargo, and all other components. This article delves into the intricacies of gross weight, starting with a comprehensive definition and the basic principles underlying it. We will explore how gross weight is calculated, including the various methods and considerations that must be taken into account to avoid errors and potential hazards. Additionally, we will examine the practical applications and implications of gross weight in real-world scenarios, highlighting its significance in industries such as shipping, construction, and automotive manufacturing. By understanding these aspects, readers will gain a deeper appreciation for the importance of accurately determining gross weight. Let us begin by Understanding Gross Weight: Definition and Basics.
Understanding Gross Weight: Definition and Basics
Understanding gross weight is a fundamental concept that underpins various industrial and logistical operations. At its core, gross weight encompasses the total mass of an object or shipment, including all its components. To grasp this concept fully, it is essential to delve into three key aspects: the definition of gross weight, its components, and its importance across different industries. Firstly, defining gross weight accurately is crucial as it sets the foundation for all subsequent calculations and considerations. This definition will clarify what constitutes gross weight and how it differs from other weight measurements. Secondly, breaking down the components of gross weight helps in understanding the various elements that contribute to the overall mass. This includes the weight of the item itself, packaging materials, and any additional items that are part of the shipment. Lastly, recognizing the importance of gross weight in various industries highlights its practical applications and significance. From transportation and logistics to manufacturing and trade, accurate gross weight calculations are vital for efficiency, safety, and compliance. By exploring these facets, we can gain a comprehensive understanding of gross weight and its role in modern operations. Let us begin by examining the definition of gross weight in detail.
1. Definition of Gross Weight
**Definition of Gross Weight** Gross weight, a fundamental concept in various fields such as logistics, transportation, and engineering, refers to the total weight of an object or a shipment, including all its components and packaging. This comprehensive measure encompasses not only the weight of the actual product or goods but also any additional elements that contribute to the overall mass. For instance, in shipping, gross weight includes the weight of the cargo itself, as well as the weight of the container, pallets, packaging materials, and any other ancillary items that are part of the shipment. Similarly, in aviation and automotive contexts, gross weight would account for the vehicle or aircraft's own mass plus that of its fuel, passengers, cargo, and any other onboard items. Understanding gross weight is crucial for ensuring compliance with safety regulations, calculating transportation costs accurately, and optimizing load distribution to prevent damage or accidents. It serves as a critical metric in operational planning and risk management across diverse industries, highlighting its importance in maintaining efficiency and safety standards. By accurately determining gross weight, businesses can make informed decisions regarding resource allocation, capacity utilization, and compliance with legal requirements, thereby enhancing their operational effectiveness and reducing potential liabilities. In essence, gross weight is a holistic measure that provides a complete picture of an object's or shipment's total mass, facilitating better management and decision-making processes.
2. Components of Gross Weight
When delving into the concept of gross weight, it is crucial to understand its constituent components. Gross weight, often referred to as the total weight of a shipment or vehicle, encompasses two primary elements: the tare weight and the net weight. **Tare Weight** is the weight of the empty vehicle or container, including all permanent fittings and equipment but excluding any cargo or fuel. This component is essential because it provides a baseline measurement that helps in calculating the actual weight of the goods being transported. For instance, in logistics, knowing the tare weight of a truck allows for accurate determination of how much cargo can be safely loaded without exceeding legal weight limits. **Net Weight**, on the other hand, refers to the weight of the goods or cargo being transported. This is calculated by subtracting the tare weight from the gross weight. The net weight is critical for various reasons, including billing purposes in freight transportation and ensuring compliance with safety regulations. For example, in international trade, accurate net weights are necessary for customs clearance and tariff calculations. Understanding these components is vital for several reasons. Firstly, it aids in efficient load planning and distribution, ensuring that vehicles are not overloaded and thus reducing the risk of accidents and structural damage. Secondly, it facilitates accurate billing and cost allocation in transportation services. Lastly, it helps in maintaining compliance with legal and regulatory requirements related to weight limits on roads and highways. In practical terms, when calculating gross weight, one must meticulously account for both tare and net weights. For instance, if a truck has a tare weight of 5,000 pounds and is loaded with cargo weighing 10,000 pounds, the gross weight would be 15,000 pounds. This precise calculation is indispensable in industries such as logistics, shipping, and construction where weight management is a critical aspect of operations. Moreover, the distinction between these components highlights the importance of precision in weight measurement. Incorrect calculations can lead to significant consequences, including fines for overweight vehicles, damage to infrastructure, and even safety hazards. Therefore, understanding and accurately determining both tare and net weights are fundamental to managing gross weight effectively. In conclusion, the components of gross weight—tare weight and net weight—are interdependent yet distinct elements that collectively define the total weight of a shipment or vehicle. Recognizing their roles and importance is essential for operational efficiency, legal compliance, and safety in various industries. By grasping these basics, individuals can better navigate the complexities associated with gross weight and ensure smooth, safe, and compliant operations.
3. Importance in Various Industries
The importance of gross weight extends far beyond its basic definition, permeating various industries where precise weight measurements are crucial for safety, efficiency, and compliance. In the **transportation industry**, gross weight is a critical factor in ensuring road safety and compliance with regulations. For instance, trucks and trailers must adhere to specific gross vehicle weight ratings (GVWR) to avoid overloading, which can lead to accidents and damage to infrastructure. Exceeding these limits can also result in fines and penalties, making accurate gross weight calculations essential for logistics and freight companies. In **aviation**, the gross weight of an aircraft is vital for determining its performance characteristics, such as takeoff distance, climb rate, and fuel efficiency. Airlines must meticulously calculate the gross weight of their aircraft to ensure safe operations and optimal fuel consumption. This includes accounting for the weight of passengers, cargo, fuel, and other onboard items. Incorrect calculations could compromise flight safety or lead to inefficient operations. The **construction industry** also relies heavily on accurate gross weight measurements. Building materials like steel beams, concrete blocks, and heavy machinery must be weighed precisely to ensure structural integrity and compliance with building codes. Misjudging the gross weight of these components can result in structural failures or delays in project completion due to the need for rework. In **manufacturing**, understanding gross weight is essential for quality control and product specification. Manufacturers need to ensure that their products meet specific weight standards to guarantee performance and safety. For example, in the automotive sector, car parts must meet precise weight specifications to maintain vehicle performance and safety standards. Furthermore, **agriculture** benefits from accurate gross weight measurements in terms of crop yield and livestock management. Farmers use gross weight to measure crop production accurately, which helps in pricing and market transactions. Similarly, livestock producers rely on gross weight to monitor animal health and determine market value. Lastly, **healthcare** and **pharmaceuticals** industries require precise weight measurements for drug formulation and medical device manufacturing. The gross weight of ingredients in pharmaceuticals must be accurately calculated to ensure the correct dosage and efficacy of medications. In medical devices, such as implants or surgical instruments, precise weight measurements are critical for ensuring safety and performance. In summary, the importance of gross weight is multifaceted and far-reaching across various industries. It underpins safety protocols, operational efficiency, regulatory compliance, and product quality. Accurate gross weight calculations are not just a matter of administrative detail but a cornerstone of responsible and effective industry practices.
Calculating Gross Weight: Methods and Considerations
Calculating gross weight is a critical task in various industries, including logistics, manufacturing, and construction. It involves determining the total weight of an object or shipment, which is essential for safety, compliance, and cost management. To accurately calculate gross weight, several key considerations must be taken into account. First, **measurement techniques for gross weight** are crucial, as they provide the foundational data needed for calculations. These techniques can vary depending on the type of object or shipment being measured. Second, **factors affecting gross weight calculations** must be understood, as they can significantly impact the accuracy of the final weight. These factors include the density of materials, moisture content, and any additional components that contribute to the overall weight. Finally, **tools and equipment used for measurement** play a vital role in ensuring precision and reliability. By understanding these elements, individuals can ensure that their gross weight calculations are accurate and reliable. Let's delve into the first of these critical aspects: **measurement techniques for gross weight**.
1. Measurement Techniques for Gross Weight
When calculating gross weight, the accuracy of measurement techniques is paramount. Several methods are employed to ensure precise determination of this critical parameter. One of the most common techniques is the use of **scales and weighbridges**. These devices are calibrated to provide accurate readings, with weighbridges being particularly useful for large vehicles and heavy machinery. For smaller items, **platform scales** or **bench scales** are often utilized, offering high precision and ease of use. Another method involves **dimensional analysis**, where the volume and density of an object are measured to calculate its weight. This approach is particularly useful for irregularly shaped items or when direct weighing is impractical. **Hydrostatic weighing** is another sophisticated technique that leverages Archimedes' Principle to measure weight. By submerging an object in water and measuring the displaced volume, the weight can be calculated with high accuracy. This method is especially valuable for objects that are difficult to weigh directly due to their size or shape. In industrial settings, **load cells** are frequently used; these sensors convert the weight into an electrical signal, providing real-time data that can be integrated into automated systems. For more complex scenarios, such as determining the gross weight of vehicles or large containers, **axle load scales** and **portable wheel load scales** come into play. These tools allow for the measurement of individual axle weights, ensuring compliance with transportation regulations and preventing overloading. Additionally, **dynamic weighing systems**, which measure weight while the vehicle is in motion, offer a convenient and efficient solution for high-volume operations. In all these methods, **calibration** is a crucial step to ensure accuracy. Regular calibration against certified standards helps maintain the reliability of the measurements. Furthermore, adherence to industry standards and guidelines, such as those set by the International Organization for Standardization (ISO), is essential for consistency and comparability across different measurements. The choice of measurement technique depends on the specific application, the size and type of the object being weighed, and the required level of precision. By selecting the appropriate method and ensuring proper calibration and adherence to standards, one can confidently calculate gross weight, which is vital for various industries including logistics, manufacturing, and transportation. Each technique has its own set of advantages and considerations, making it important to understand the nuances of each to select the best approach for any given scenario.
2. Factors Affecting Gross Weight Calculations
When calculating gross weight, several critical factors must be considered to ensure accuracy and compliance with regulatory standards. **1. Cargo Distribution and Loading:** The way cargo is distributed within a vehicle or container significantly impacts gross weight calculations. Uneven loading can lead to improper weight distribution, potentially causing safety issues and affecting the overall gross weight. For instance, if cargo is concentrated in one area, it may exceed the axle weight limits or alter the vehicle's center of gravity, necessitating adjustments in loading patterns to maintain stability and adhere to weight regulations. **2. Vehicle Specifications:** The specifications of the vehicle itself play a crucial role in determining gross weight. This includes the vehicle's tare weight (the weight of the empty vehicle), its payload capacity, and any additional equipment or modifications that could add weight. For example, adding aftermarket accessories such as heavy-duty tires, reinforced suspension, or specialized cargo handling equipment can increase the tare weight, thereby reducing the available payload capacity and affecting gross weight calculations. **3. Fuel and Fluids:** The weight of fuel, lubricants, and other fluids in the vehicle also contributes to its gross weight. As fuel levels change during operations, so does the vehicle's overall weight. This is particularly relevant for long-haul trucking where fuel consumption varies significantly over time. Accurate accounting for these fluids is essential to avoid underestimating or overestimating the gross weight. **4. Passenger and Crew Weight:** In vehicles designed to carry passengers or crew members, their combined weight must be factored into gross weight calculations. This is especially important for buses, coaches, and other passenger vehicles where the number of occupants can vary widely. **5. Environmental Conditions:** Environmental factors such as weather conditions can indirectly affect gross weight through factors like fuel consumption and cargo moisture content. For example, heavy rainfall can increase the weight of cargo due to water absorption, while extreme temperatures may alter fuel efficiency. **6. Regulatory Compliance:** Different jurisdictions have varying regulations regarding maximum allowable gross weights for different types of vehicles. Compliance with these regulations is mandatory to avoid legal penalties and ensure public safety. Understanding local and national weight limits is crucial for accurate gross weight calculations. In summary, calculating gross weight involves a multifaceted approach that considers various dynamic factors including cargo distribution, vehicle specifications, fuel and fluid weights, passenger and crew weights, environmental conditions, and regulatory compliance. By meticulously accounting for these elements, operators can ensure safe and efficient transportation while adhering to legal standards. This comprehensive understanding is vital for maintaining operational integrity and preventing potential hazards associated with overweight vehicles.
3. Tools and Equipment Used for Measurement
When calculating gross weight, the accuracy and reliability of the tools and equipment used for measurement are paramount. Here, we delve into the essential tools and equipment that play a crucial role in this process. ### Scales and Weighing Machines At the forefront of gross weight calculation are scales and weighing machines. These devices come in various forms, each designed to handle different types of loads and environments. **Industrial Scales**, for instance, are robust and durable, often used in warehouses and manufacturing facilities to weigh heavy goods. **Platform Scales** offer a large surface area, making them ideal for weighing pallets and bulk items. **Digital Scales**, with their high precision and ease of use, are widely used in both industrial and commercial settings. These scales can provide readings in multiple units (e.g., kilograms, pounds) and often come with additional features such as tare functions and data logging capabilities. ### Measuring Tapes and Calipers While scales measure weight, other tools are necessary to measure dimensions which can be crucial for calculating volume or verifying the size of items being weighed. **Measuring Tapes** are versatile and essential for measuring lengths, widths, and heights of objects. They are available in various lengths and materials (e.g., fiberglass, steel) to suit different applications. **Calipers**, on the other hand, provide precise measurements of internal and external dimensions as well as depths. These tools are particularly useful when dealing with irregularly shaped items where exact dimensions are critical. ### Load Cells and Strain Gauges For more sophisticated and precise weight measurements, especially in high-stakes environments like aerospace or pharmaceuticals, **Load Cells** and **Strain Gauges** come into play. **Load Cells** convert the weight applied to them into an electrical signal that can be read by a display device or integrated into a larger system. They offer high accuracy and are often used in automated weighing systems. **Strain Gauges**, attached to structural elements like beams or platforms, measure the deformation caused by weight, providing real-time data on load distribution and total weight. ### Software and Data Loggers In today's digital age, software and data loggers are integral components of the measurement process. **Weighing Software** can interface with scales and load cells to record, analyze, and report weight data efficiently. These programs often include features such as data export options, statistical analysis tools, and compliance reporting modules. **Data Loggers** capture weight data over time, allowing for trend analysis and quality control checks. They can be particularly useful in environments where continuous monitoring is required. ### Calibration Equipment To ensure the accuracy of these tools, regular calibration is essential. **Calibration Weights** and **Certified Standards** are used to verify the precision of scales and weighing machines. These standards are traceable to national or international standards, ensuring that measurements are reliable and consistent across different locations and devices. In conclusion, the tools and equipment used for measurement in calculating gross weight are diverse yet interconnected. From basic scales and measuring tapes to advanced load cells and software solutions, each tool plays a vital role in ensuring that weight calculations are accurate, reliable, and compliant with industry standards. By selecting the appropriate tools for the task at hand and maintaining their calibration, professionals can confidently rely on their measurements to make informed decisions.
Applications and Implications of Gross Weight in Real-World Scenarios
The concept of gross weight is a critical metric that permeates various sectors, influencing operations, safety, and compliance. In real-world scenarios, understanding and accurately calculating gross weight is essential for efficient logistics and transportation, streamlined manufacturing and production processes, and adherence to regulatory standards. In logistics and transportation, gross weight determines the capacity of vehicles, affects fuel consumption, and impacts route planning and scheduling. In manufacturing and production, it plays a pivotal role in material handling, inventory management, and quality control. Additionally, regulatory compliance and safety standards heavily rely on accurate gross weight measurements to ensure safe transportation and storage of goods. This article delves into these applications, starting with the crucial role of gross weight in logistics and transportation, where precise calculations can significantly enhance operational efficiency and reduce costs. By examining these facets, we can appreciate the multifaceted importance of gross weight in modern industries. Let's begin by exploring how gross weight shapes the landscape of logistics and transportation.
1. Gross Weight in Logistics and Transportation
In the realm of logistics and transportation, gross weight plays a pivotal role in ensuring the safe, efficient, and compliant movement of goods. Gross weight, defined as the total weight of a shipment including the weight of the goods, packaging, and any pallets or containers, is a critical metric that influences various aspects of the supply chain. From freight calculations to vehicle load optimization, understanding gross weight is essential for logistics professionals. One of the primary applications of gross weight is in freight billing and cost estimation. Shipping companies use gross weight to determine freight charges, as heavier shipments typically incur higher costs. This necessitates accurate measurement and documentation to avoid discrepancies that could lead to financial losses or disputes. For instance, in air freight, where weight is a significant factor due to fuel consumption and aircraft capacity constraints, precise gross weight calculations are crucial for optimizing cargo loads and minimizing costs. Gross weight also has significant implications for vehicle load management. Overloading vehicles can lead to safety hazards, increased wear and tear on the vehicle, and potential legal penalties. Therefore, logistics operators must carefully calculate the gross weight of each shipment to ensure that it does not exceed the vehicle's maximum permissible weight. This is particularly important for long-haul trucking, where adherence to weight limits is strictly regulated to prevent accidents and maintain road infrastructure. Moreover, gross weight affects the operational efficiency of warehouses and distribution centers. Proper weight management helps in optimizing storage space and streamlining the handling process. For example, knowing the gross weight of incoming shipments allows warehouse managers to allocate appropriate storage areas and plan for efficient unloading and stacking procedures. This enhances overall productivity and reduces the risk of damage to goods during handling. In addition, gross weight has environmental implications. Heavier shipments generally require more fuel for transportation, contributing to higher carbon emissions. As companies increasingly focus on sustainability, accurate gross weight calculations can help in optimizing routes and loads to reduce fuel consumption and lower their carbon footprint. This aligns with broader industry trends towards greener logistics practices. From a regulatory standpoint, gross weight compliance is mandatory. Various international and national regulations, such as those set by the International Air Transport Association (IATA) for air freight or the Federal Motor Carrier Safety Administration (FMCSA) for road transport in the United States, stipulate strict guidelines regarding weight limits. Non-compliance can result in fines, delays, or even the seizure of goods. Therefore, logistics providers must ensure that all shipments are accurately weighed and documented to avoid legal repercussions. In conclusion, gross weight is a fundamental concept in logistics and transportation that impacts multiple facets of the supply chain. Its accurate calculation and management are essential for cost optimization, safety compliance, operational efficiency, environmental sustainability, and regulatory adherence. As the logistics industry continues to evolve with technological advancements and changing regulatory landscapes, understanding and effectively managing gross weight will remain a cornerstone of successful logistics operations.
2. Gross Weight in Manufacturing and Production
In the realm of manufacturing and production, gross weight plays a pivotal role in ensuring efficiency, safety, and compliance with regulatory standards. Gross weight, which includes the total mass of a product along with its packaging and any other components, is crucial for various stages of the production process. For instance, during the design phase, understanding the gross weight helps engineers optimize product dimensions and materials to achieve the desired balance between functionality and portability. This is particularly important in industries such as automotive and aerospace, where even slight variations in weight can significantly impact performance and fuel efficiency. In the manufacturing stage, accurate gross weight calculations are essential for inventory management and logistics planning. Manufacturers need to know the gross weight of their products to determine shipping costs, storage requirements, and handling procedures. Incorrect weight estimations can lead to over- or under-charging for shipping services, which can result in financial losses or legal issues. Moreover, knowing the gross weight ensures that products are properly labeled and packaged according to international shipping regulations, reducing the risk of delays or confiscation during transit. Quality control is another critical area where gross weight is vital. By comparing the actual gross weight of finished products against specified standards, manufacturers can detect any discrepancies that might indicate defects or irregularities in the production process. This helps in maintaining consistent product quality and adhering to industry standards. For example, in food processing, gross weight is used to ensure that packaged goods meet the declared net weight, thereby protecting consumer rights and preventing potential legal disputes. From a safety perspective, gross weight is indispensable for ensuring that products are handled and transported safely. In industries like construction or heavy machinery, understanding the gross weight of equipment and materials is crucial for planning lifting operations and ensuring that cranes or forklifts are not overloaded. This prevents accidents that could result in injuries or damage to property. Finally, gross weight has significant implications for environmental sustainability in manufacturing. By optimizing product design to minimize packaging while maintaining structural integrity, companies can reduce material usage and lower their carbon footprint. For instance, companies like Amazon have implemented initiatives to reduce packaging weight through innovative designs that use less material without compromising on protection during shipping. In summary, gross weight is a fundamental metric in manufacturing and production that influences various aspects of the supply chain, from product design and quality control to logistics and safety. Its accurate calculation and application are essential for maintaining operational efficiency, ensuring compliance with regulations, and promoting sustainable practices. As industries continue to evolve with technological advancements and changing consumer demands, the importance of gross weight will only continue to grow.
3. Regulatory Compliance and Safety Standards
Regulatory compliance and safety standards play a crucial role in the accurate determination and management of gross weight across various industries. In real-world scenarios, adhering to these standards is not only legally mandatory but also essential for ensuring public safety and preventing potential hazards. For instance, in the transportation sector, gross vehicle weight rating (GVWR) is a critical parameter that must be strictly adhered to. Regulatory bodies such as the Federal Motor Carrier Safety Administration (FMCSA) in the United States set specific guidelines to ensure that vehicles do not exceed their GVWR, thereby reducing the risk of accidents caused by overweight vehicles. Similarly, in aviation, the Federal Aviation Administration (FAA) enforces strict weight limits for aircraft to maintain airworthiness and prevent overloading, which could lead to catastrophic consequences. In the maritime industry, compliance with safety standards related to gross weight is equally paramount. The International Maritime Organization (IMO) and local maritime authorities impose regulations on the gross tonnage of ships to prevent overloading, which can compromise stability and increase the risk of capsizing. These regulations also extend to cargo handling practices, where accurate weight calculations are necessary to ensure that ships are loaded within safe limits. Beyond transportation, regulatory compliance in manufacturing and construction also hinges on accurate gross weight calculations. For example, in construction projects, the gross weight of materials and equipment must be carefully managed to ensure structural integrity and compliance with building codes. Failure to adhere to these standards can result in structural failures, accidents, and significant financial losses. Moreover, industries such as healthcare and pharmaceuticals rely on precise weight measurements for regulatory compliance. For instance, the gross weight of medical devices and pharmaceutical products must be accurately recorded to comply with labeling requirements and ensure patient safety. Non-compliance can lead to product recalls, legal penalties, and damage to brand reputation. In addition to legal and safety implications, regulatory compliance in gross weight management also has economic benefits. Companies that adhere to these standards can avoid costly fines and penalties associated with non-compliance. Furthermore, maintaining accurate records of gross weight helps in efficient resource allocation, reduced waste, and improved operational efficiency. In summary, regulatory compliance and safety standards related to gross weight are indispensable in various real-world scenarios. These standards not only ensure public safety but also contribute to operational efficiency and economic sustainability. By adhering to these regulations, industries can mitigate risks, avoid legal repercussions, and maintain a competitive edge in their respective markets. Therefore, understanding and implementing these standards is crucial for any organization dealing with gross weight in their daily operations.