What Does Smd Mean

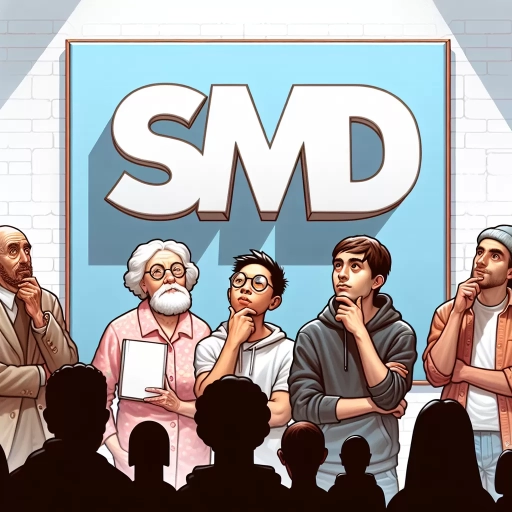
In the realm of modern electronics, the term "SMD" has become synonymous with innovation and efficiency. Standing for Surface Mount Device, SMDs represent a significant advancement in the field of electronic components. These tiny devices have revolutionized the way we design and manufacture electronic circuits, offering a multitude of benefits over their through-hole counterparts. But what exactly does SMD mean, and how do these components impact the world of electronics? This article delves into the intricacies of SMDs, starting with a comprehensive understanding of their definition and basic principles. We will explore the various applications and uses of SMDs, highlighting their role in modern technology. Additionally, we will discuss the advantages and challenges associated with these devices, providing a balanced view of their impact. By the end of this journey, you will have a thorough grasp of what SMDs are and why they are so crucial in today's electronic landscape. Let's begin by understanding the fundamental aspects of SMDs in the next section: **Understanding SMD: Definition and Basics**.
Understanding SMD: Definition and Basics
In the realm of modern electronics, Surface Mount Devices (SMDs) have revolutionized the way we design and manufacture electronic circuits. These tiny components are the backbone of contemporary technology, from smartphones and laptops to medical devices and automotive systems. To fully appreciate the significance of SMDs, it is crucial to delve into their fundamental aspects. This article aims to provide a comprehensive understanding of SMDs by exploring three key areas: **What is SMD?**, which will define and explain the nature of these devices; **History of SMD Technology**, which will trace the evolution and development of SMDs over time; and **Key Components of SMDs**, which will detail the essential parts that make up these miniature marvels. By examining these facets, readers will gain a thorough grasp of the technology that underpins many of today's innovations. Understanding SMD: Definition and Basics is essential for anyone interested in electronics, engineering, or simply how modern technology works.
What is SMD?
**Understanding SMD: Definition and Basics** **What is SMD?** Surface Mount Device (SMD) refers to a type of electronic component that is mounted directly onto the surface of a printed circuit board (PCB) rather than being inserted into holes. This technology has revolutionized the field of electronics by enabling the production of smaller, more efficient, and cost-effective devices. Unlike traditional through-hole components, SMDs are designed with flat leads or terminations that are soldered to the PCB's surface. This design allows for higher component density, which is crucial for modern electronic devices that require compactness and high performance. The use of SMDs has significantly reduced the size and weight of electronic assemblies, making them ideal for applications in consumer electronics, automotive systems, medical devices, and aerospace. The manufacturing process for SMDs involves automated pick-and-place machines that accurately position the components on the PCB before soldering. This automation enhances production speed and reliability, contributing to lower production costs. SMDs come in various forms, including resistors, capacitors, inductors, diodes, and integrated circuits. Each type is designed to meet specific requirements such as voltage handling, current capacity, and frequency response. For instance, surface mount resistors are available in different values and tolerances, while surface mount capacitors can be ceramic, tantalum, or electrolytic. The advantages of SMDs extend beyond their physical attributes; they also offer improved electrical performance due to shorter lead lengths and lower parasitic inductance. This results in better signal integrity and reduced electromagnetic interference (EMI), which are critical factors in high-speed digital circuits and radio-frequency (RF) applications. Despite their numerous benefits, working with SMDs requires specialized tools and techniques. Handling these tiny components demands precision and care to avoid damage during assembly and rework processes. However, the widespread adoption of SMD technology has driven the development of advanced tools and methodologies that make it easier for engineers and technicians to work with these components effectively. In summary, Surface Mount Devices are a cornerstone of modern electronics manufacturing, offering a blend of miniaturization, efficiency, and cost-effectiveness that has transformed the industry. Their widespread use underscores their importance in creating the compact, high-performance devices that are integral to our daily lives. Understanding SMDs is essential for anyone involved in electronics design, manufacturing, or repair, as it opens up new possibilities for innovation and advancement in this field.
History of SMD Technology
The history of Surface Mount Device (SMD) technology is a narrative of innovation and evolution, transforming the landscape of electronics manufacturing over several decades. The journey began in the 1960s, when the first surface mount components were introduced as an alternative to traditional through-hole technology. These early SMDs were primarily used in military and aerospace applications due to their reliability and compactness. However, it wasn't until the 1980s that SMD technology started gaining widespread acceptance in the consumer electronics industry. During this period, advancements in semiconductor manufacturing and the development of new materials enabled the production of smaller, more efficient components. The introduction of leadless chip carriers (LCCs) and small outline integrated circuits (SOICs) marked significant milestones, as these components could be mounted directly onto the surface of printed circuit boards (PCBs), reducing board size and increasing component density. The 1990s saw a surge in SMD adoption, driven by the demand for miniaturization in consumer electronics such as mobile phones, laptops, and other portable devices. This era also witnessed the introduction of ball grid array (BGA) packages, which further reduced component size while enhancing performance. The use of BGAs allowed for higher pin counts and improved thermal management, making them ideal for complex digital circuits. In the 21st century, SMD technology continued to advance with the development of even smaller packages like quad flat no-lead (QFN) and wafer-level packages (WLPs). These innovations have enabled the creation of ultra-compact devices with enhanced functionality, contributing significantly to the proliferation of IoT devices, wearables, and high-performance computing systems. Today, SMDs are ubiquitous in modern electronics, from simple household appliances to sophisticated medical devices and automotive systems. The ongoing quest for miniaturization and improved performance continues to drive research and development in SMD technology. Advances in materials science, such as the use of nanomaterials and 3D printing techniques, are expected to further push the boundaries of what is possible with surface mount devices. In summary, the history of SMD technology is a testament to human ingenuity and the relentless pursuit of innovation. From its humble beginnings in niche applications to its current status as a cornerstone of modern electronics, SMD technology has revolutionized how we design, manufacture, and use electronic devices. Understanding this history provides a deeper appreciation for the complexities and advancements that underpin our increasingly interconnected world.
Key Components of SMDs
**Key Components of SMDs** Surface Mount Devices (SMDs) are integral to modern electronic manufacturing, offering compact, efficient, and reliable solutions for a wide range of applications. The key components of SMDs include the **substrate**, **conductors**, **dielectric layers**, and **termination finishes**. 1. **Substrate**: This is the base material on which the SMD is built. Common substrates include ceramic, glass, or organic materials like FR4 (a type of epoxy laminate). The substrate provides mechanical support and acts as an insulator between different components. 2. **Conductors**: These are the pathways through which electrical signals flow. In SMDs, conductors are typically made from copper or other conductive materials and are patterned onto the substrate using techniques such as photolithography or screen printing. 3. **Dielectric Layers**: These layers separate the conductive paths to prevent electrical shorts and ensure proper signal integrity. Dielectric materials can be organic or inorganic and are chosen based on their electrical insulation properties and compatibility with other components. 4. **Termination Finishes**: These are critical for ensuring reliable connections between the SMD and other components on a printed circuit board (PCB). Common termination finishes include solderable finishes like tin-lead solder, lead-free solders, or gold plating. These finishes enhance the solderability and corrosion resistance of the SMD's terminals. Additionally, SMDs often incorporate **passive components** such as resistors, capacitors, and inductors, which are miniaturized to fit within the compact footprint of an SMD. **Active components** like integrated circuits (ICs) and transistors are also frequently used in SMD configurations to perform complex functions. The design and fabrication of these components involve sophisticated processes including **pick-and-place** assembly, where tiny components are precisely placed onto the PCB, and **reflow soldering**, which melts the solder paste to secure the components in place. The precision and miniaturization of SMDs have revolutionized electronics manufacturing by enabling the production of smaller, lighter, and more efficient devices that power everything from smartphones to medical equipment. Understanding these key components is essential for appreciating the complexity and functionality of SMDs, which are at the heart of modern electronic design and manufacturing. By leveraging these components effectively, engineers can create highly integrated circuits that meet stringent performance requirements while minimizing space and weight. This integration has been a driving force behind technological advancements in various fields, making SMDs an indispensable part of contemporary electronics.
Applications and Uses of SMDs
Surface Mount Devices (SMDs) have revolutionized the electronics industry with their compact design, high performance, and versatility. These tiny components are integral to modern electronics, enabling the creation of smaller, more efficient, and reliable devices. In this article, we will delve into the diverse applications and uses of SMDs across various sectors. We will explore their critical role in **Electronics Manufacturing**, where they streamline production processes and enhance product reliability. Additionally, we will examine their widespread adoption in **Consumer Electronics**, transforming everyday devices such as smartphones, laptops, and televisions. Furthermore, we will discuss their **Industrial and Automotive Uses**, where SMDs contribute to the development of sophisticated systems and safety features. Understanding these applications is crucial for appreciating the significance of SMDs in today's technological landscape. To fully grasp the impact of SMDs, it is essential to start with a solid foundation: **Understanding SMD: Definition and Basics**. This foundational knowledge will provide the context necessary to appreciate the innovative ways in which SMDs are shaping our world.
Electronics Manufacturing
In the realm of electronics manufacturing, Surface Mount Devices (SMDs) play a pivotal role in the production of modern electronic devices. These tiny components, such as resistors, capacitors, and integrated circuits, are mounted directly onto the surface of a printed circuit board (PCB) rather than being inserted through holes. This method has revolutionized the electronics industry by enabling the creation of smaller, more complex, and highly reliable electronic systems. The use of SMDs in electronics manufacturing offers several key advantages. Firstly, they significantly reduce the size and weight of electronic devices, making them ideal for applications where space is limited, such as in smartphones, laptops, and wearable technology. Secondly, SMDs enhance the speed and efficiency of manufacturing processes. Automated pick-and-place machines can quickly and accurately place thousands of SMDs onto a PCB in a matter of minutes, reducing labor costs and increasing production throughput. This automation also minimizes human error, leading to higher quality and reliability in the final products. Moreover, SMDs facilitate better thermal management and improved electrical performance. Their compact design allows for closer spacing between components, which can reduce signal delays and improve overall system performance. Additionally, the smaller footprint of SMDs enables more efficient heat dissipation, which is crucial for high-power applications like power supplies and automotive electronics. The versatility of SMDs extends across various industries. In consumer electronics, they are integral to the development of smart home devices, gaming consoles, and televisions. In the automotive sector, SMDs are used in advanced driver-assistance systems (ADAS), infotainment systems, and safety features like airbag controllers. Medical devices also benefit from SMD technology, enabling the creation of portable diagnostic equipment and implantable devices such as pacemakers. In aerospace and defense, the reliability and compactness of SMDs make them essential for mission-critical systems where failure is not an option. They are used in satellite communications, navigation systems, and military electronics where size, weight, and power (SWaP) constraints are stringent. Overall, the widespread adoption of SMDs in electronics manufacturing has driven innovation across multiple sectors by enabling the development of smaller, faster, and more reliable electronic systems. As technology continues to evolve, the role of SMDs will remain crucial in shaping the future of electronic device design and production.
Consumer Electronics
Consumer electronics play a pivotal role in modern life, and their widespread adoption is largely driven by the advancements in Surface Mount Devices (SMDs). These tiny components, which include resistors, capacitors, and integrated circuits, are crucial for the miniaturization and performance enhancement of electronic devices. In consumer electronics, SMDs are ubiquitous, found in everything from smartphones and laptops to televisions and gaming consoles. Their compact size allows for the design of sleeker, more portable products that are both aesthetically appealing and functionally superior. The integration of SMDs in consumer electronics has significantly improved device reliability and efficiency. For instance, in smartphones, SMDs enable the packing of numerous functionalities into a small form factor, allowing for features like high-resolution displays, advanced camera systems, and robust processing capabilities. Similarly, in home entertainment systems such as smart TVs and soundbars, SMDs facilitate the implementation of advanced technologies like 4K resolution and Dolby Atmos without compromising on size or power consumption. Moreover, the use of SMDs in consumer electronics has led to substantial cost savings. By reducing the need for through-hole components and manual soldering processes, manufacturers can automate production lines more effectively, thereby lowering production costs. This cost efficiency is then passed on to consumers, making high-tech gadgets more affordable and accessible to a broader audience. Another critical application of SMDs in consumer electronics is their role in enhancing device durability. Because SMDs are mounted directly onto the surface of printed circuit boards (PCBs), they are less prone to mechanical stress compared to traditional through-hole components. This results in fewer failures due to vibration or impact, making consumer electronics more resilient and longer-lasting. In addition to these benefits, the versatility of SMDs has also driven innovation in wearable technology and IoT devices. Smartwatches, fitness trackers, and smart home devices all rely heavily on SMDs to achieve their compact designs while maintaining robust performance. The ability to integrate multiple functions into a small footprint has enabled the development of these devices that seamlessly integrate into daily life. In conclusion, the applications and uses of SMDs in consumer electronics are multifaceted and transformative. By enabling miniaturization, improving reliability, reducing costs, enhancing durability, and driving innovation across various product categories, SMDs have become an indispensable component of modern consumer electronics. As technology continues to evolve, it is clear that SMDs will remain at the forefront of advancements in this field.
Industrial and Automotive Uses
In the realm of industrial and automotive applications, Surface Mount Devices (SMDs) play a pivotal role in enhancing efficiency, reliability, and performance. These compact components are integral to modern manufacturing processes, where space and weight are critical factors. In industrial settings, SMDs are used extensively in control systems, power supplies, and automation equipment. For instance, they are found in programmable logic controllers (PLCs), which manage and monitor complex industrial processes. The small size of SMDs allows for denser circuitry, enabling more sophisticated control mechanisms within a smaller footprint. This miniaturization also reduces heat dissipation issues, making the overall system more robust and less prone to failures. In the automotive sector, SMDs are ubiquitous in various electronic systems that drive vehicle safety, comfort, and efficiency. They are integral to engine control units (ECUs), which optimize fuel consumption and emissions. SMDs are also used in anti-lock braking systems (ABS), traction control systems (TCS), and advanced driver-assistance systems (ADAS) such as lane departure warning and adaptive cruise control. The reliability of SMDs under harsh environmental conditions—such as extreme temperatures and vibrations—is crucial for ensuring the consistent performance of these critical automotive systems. Additionally, their compact design facilitates the integration of multiple functionalities into a single module, thereby reducing the complexity and weight of automotive electronics. The use of SMDs in both industries also promotes cost-effectiveness and faster production times. Automated assembly lines can handle SMDs more efficiently than through-hole components, leading to higher production rates and lower labor costs. Furthermore, the reduced material usage and lower power consumption of SMDs contribute to a more sustainable manufacturing process. As technology continues to evolve, the role of SMDs in industrial and automotive applications will only expand, driving innovation and pushing the boundaries of what is possible in terms of performance, reliability, and efficiency. By leveraging the advantages offered by SMDs—such as miniaturization, reliability, and cost-effectiveness—these sectors can achieve significant improvements in product design, functionality, and overall system performance.
Advantages and Challenges of SMDs
The advent of Surface Mount Devices (SMDs) has revolutionized the field of electronics, offering a myriad of advantages over traditional through-hole technology. These compact components have significantly reduced the size and weight of electronic devices, enabling the creation of more sophisticated and portable products. However, the transition to SMDs is not without its challenges, particularly in design and assembly processes. As the industry continues to evolve, understanding the benefits and hurdles associated with SMDs is crucial for engineers and manufacturers alike. This article delves into the key advantages of SMDs over traditional through-hole technology, explores the challenges encountered during design and assembly, and examines future trends and innovations that are shaping the landscape of surface mount technology. By grasping these aspects, readers will gain a comprehensive understanding of SMDs, setting the stage for a deeper exploration into the fundamental principles outlined in "Understanding SMD: Definition and Basics."
Benefits Over Traditional Through-Hole Technology
The transition from traditional through-hole technology to Surface Mount Devices (SMDs) has revolutionized the electronics industry, offering a myriad of benefits that significantly enhance the design, manufacturing, and performance of electronic circuits. One of the most compelling advantages of SMDs is their compact size, which allows for much denser component placement on printed circuit boards (PCBs). This miniaturization enables the creation of smaller, lighter, and more portable electronic devices, making them ideal for modern applications where space is a critical factor. Additionally, SMDs reduce the need for drilling holes in PCBs, a process that can be time-consuming and prone to errors. This streamlined manufacturing process not only speeds up production but also decreases the likelihood of defects, thereby improving overall product reliability. Another significant benefit of SMDs is their improved electrical performance. With shorter lead lengths and lower inductance, SMDs exhibit better high-frequency characteristics compared to through-hole components. This is particularly important in today's high-speed digital and RF circuits, where signal integrity is crucial. Furthermore, the reduced lead length minimizes parasitic effects such as capacitance and inductance, leading to more stable and efficient circuit operation. From a mechanical standpoint, SMDs offer enhanced durability due to their soldered connections directly onto the PCB surface. This eliminates the risk of loose or bent leads associated with through-hole components, which can compromise the structural integrity of the board. The robust solder joints in SMDs also provide better resistance against thermal and mechanical stresses, ensuring that devices remain functional under various environmental conditions. Moreover, the use of SMDs facilitates automated assembly processes, which are faster and more accurate than manual through-hole assembly methods. Automated pick-and-place machines can quickly position and solder SMDs with high precision, reducing labor costs and increasing production volumes. This automation also enables the integration of more complex designs with multiple layers and finer pitch components, further expanding the capabilities of modern electronics. In summary, the adoption of SMD technology over traditional through-hole methods brings about substantial improvements in terms of component density, manufacturing efficiency, electrical performance, mechanical robustness, and automation capabilities. These advantages collectively contribute to the development of more sophisticated, reliable, and compact electronic devices that meet the demands of contemporary technology. While there are challenges associated with SMDs—such as higher initial investment in equipment and training—these are often outweighed by the long-term benefits they provide in terms of product quality and production efficiency.
Challenges in Design and Assembly
**Challenges in Design and Assembly** The integration of Surface Mount Devices (SMDs) into modern electronics has revolutionized the industry, but it also presents several challenges in design and assembly. One of the primary hurdles is the miniaturization of components, which demands precise engineering and manufacturing processes. Designers must navigate the complexities of compact layouts, ensuring that components are correctly placed and spaced to avoid electrical interference and thermal issues. This requires advanced software tools and a deep understanding of electromagnetic compatibility (EMC) and thermal management. Another significant challenge is the assembly process itself. SMDs are much smaller than their through-hole counterparts, making manual placement nearly impossible. Automated pick-and-place machines are essential for high-volume production, but these machines require careful calibration and maintenance to ensure accuracy. Moreover, the soldering process for SMDs is more delicate due to the smaller solder pads and the risk of overheating, which can damage components or cause solder bridges. Quality control is also a critical aspect, as defects can be difficult to detect visually due to the small size of SMDs. Advanced inspection techniques such as X-ray imaging and automated optical inspection (AOI) are often necessary to identify issues like misaligned components or insufficient solder. Additionally, the handling of SMDs during assembly poses unique challenges. Static electricity can easily damage these sensitive components, necessitating the use of anti-static equipment and environments. This adds an extra layer of complexity and cost to the production process. From a design perspective, ensuring that the printed circuit board (PCB) layout is optimized for SMDs involves careful consideration of factors such as signal integrity, power distribution, and mechanical stress. This often requires iterative design cycles and simulations to validate performance before moving to production. Finally, the environmental impact of SMDs should not be overlooked. The use of lead-free solder and other eco-friendly materials has become increasingly important, but these alternatives can sometimes compromise on performance characteristics like melting points and reliability. In summary, while SMDs offer numerous advantages in terms of size reduction and performance enhancement, they introduce several challenges in design and assembly that must be meticulously addressed to ensure reliable and efficient production processes. Overcoming these challenges requires a combination of advanced technology, rigorous quality control measures, and a deep understanding of the intricacies involved in working with these tiny but powerful components.
Future Trends and Innovations
As we delve into the future trends and innovations surrounding Surface Mount Devices (SMDs), it becomes evident that these components are at the forefront of technological advancement. One of the most significant trends is the miniaturization of SMDs, which continues to push the boundaries of what is possible in terms of size and functionality. This downsizing enables the creation of smaller, more efficient electronic devices that are crucial for emerging technologies such as the Internet of Things (IoT), wearable technology, and autonomous vehicles. Another key innovation is the integration of advanced materials and technologies into SMDs. For instance, the use of nanomaterials and graphene is enhancing the performance and durability of these devices. Additionally, advancements in 3D printing are allowing for the rapid prototyping and production of complex SMD designs, which can significantly reduce development time and costs. The rise of Industry 4.0 and smart manufacturing also plays a pivotal role in the evolution of SMDs. Automated assembly lines equipped with AI and machine learning capabilities are improving the precision and speed of SMD placement, reducing errors and increasing overall efficiency. Furthermore, the integration of sensors and IoT capabilities within SMDs is enabling real-time monitoring and predictive maintenance, thereby enhancing reliability and reducing downtime. However, these innovations also come with their own set of challenges. The increasing complexity of SMD designs requires highly skilled labor and sophisticated manufacturing equipment, which can be a barrier for smaller manufacturers. Moreover, the environmental impact of producing and disposing of SMDs is a growing concern, necessitating the development of more sustainable practices and materials. Despite these challenges, the future of SMDs looks promising. As technology continues to advance, we can expect to see even more innovative applications of SMDs across various industries. For example, in the field of healthcare, SMDs are being used to create wearable devices that monitor vital signs and provide real-time health data. In aerospace, they are integral to the development of lighter, more efficient aircraft systems. In conclusion, the future trends and innovations in SMDs are not only driving technological progress but also presenting new opportunities and challenges. As we navigate these advancements, it is crucial to balance innovation with sustainability and to ensure that the benefits of these technologies are accessible to all. By doing so, we can harness the full potential of SMDs to transform industries and improve lives.