What Are Guitar Strings Made Of

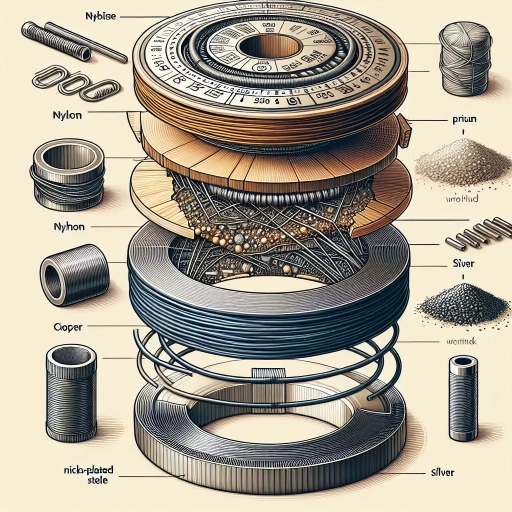
Guitar strings are a crucial component of any guitar, significantly influencing the instrument's sound quality and playability. Understanding what guitar strings are made of, how they are manufactured, and the various types available can enhance a musician's performance and overall musical experience. This article delves into the intricacies of guitar strings, starting with the materials used in their construction. We will explore the diverse range of materials such as steel, nylon, and bronze, each contributing unique tonal characteristics. Following this, we will examine the manufacturing process that transforms these raw materials into functional strings. Finally, we will discuss the different types of guitar strings and their specific applications, whether for acoustic, electric, or classical guitars. By grasping these fundamental aspects, musicians can make informed decisions about their equipment and optimize their sound. Let's begin by looking at the materials used in guitar strings.
Materials Used in Guitar Strings
Guitar strings are a crucial component of any guitar, significantly influencing the instrument's sound quality and playability. The choice of material for guitar strings can vary widely, each offering unique characteristics that cater to different musical styles and preferences. This article delves into the three primary categories of materials used in guitar strings: metal alloys, synthetic materials, and natural fibers. Metal alloys, such as nickel, bronze, and stainless steel, are renowned for their durability and rich tonal qualities. Synthetic materials, including nylon and fluorocarbon, provide a softer feel and are often used in classical and folk guitars. Natural fibers, like gut and silk, offer a warm, vintage sound that is prized by many musicians. By understanding the properties and applications of these materials, guitarists can make informed decisions about which strings best suit their needs. Let's begin by exploring the first category: metal alloys, which have been a cornerstone in the world of guitar strings for decades.
1. Metal Alloys
Metal alloys are a crucial component in the manufacture of guitar strings, offering a blend of strength, durability, and tonal quality that is essential for producing high-quality sound. These alloys are created by combining two or more metals to achieve specific properties that individual metals cannot provide on their own. For guitar strings, the most commonly used metal alloys include nickel-plated steel, stainless steel, and bronze. **Nickel-Plated Steel:** This alloy is widely used for electric guitar strings due to its bright, crisp tone and smooth playing feel. The nickel plating enhances the string's corrosion resistance and provides a warm, balanced sound. The steel core gives the string its strength and stability, making it ideal for various musical genres. **Stainless Steel:** Known for its high tensile strength and resistance to corrosion, stainless steel strings are often preferred by jazz and fusion musicians. They produce a clear, bright tone with excellent sustain and are less prone to rusting compared to other materials. However, they can feel slightly stiffer under the fingers. **Bronze:** Bronze alloys, typically made from a combination of copper and tin, are commonly used for acoustic guitar strings. Phosphor bronze and 80/20 bronze are popular variants; the former adds phosphorus for increased corrosion resistance and a warmer tone, while the latter offers a brighter sound with good balance between warmth and clarity. The choice of metal alloy in guitar strings significantly influences the sound quality and playing experience. For instance, bronze strings tend to produce a warmer, more mellow sound suitable for folk and country music, whereas nickel-plated steel strings are better suited for rock and pop due to their brighter, more aggressive tone. The durability and resistance to wear of these alloys also ensure that the strings maintain their performance over time, making them a vital part of any guitarist's toolkit. In summary, metal alloys play a pivotal role in guitar string construction, providing the necessary balance of strength, tone, and longevity that musicians demand from their instruments.
2. Synthetic Materials
Synthetic materials have become a significant component in the production of guitar strings, offering unique properties that cater to various playing styles and preferences. Unlike traditional materials such as steel, bronze, or nylon, synthetic strings are made from man-made polymers like polyamide, polyurethane, and fluorocarbon. These materials are engineered to provide specific benefits that enhance the overall playing experience. One of the primary advantages of synthetic strings is their durability. They are less prone to corrosion and wear compared to metal strings, which makes them ideal for players who live in humid climates or those who sweat a lot during performances. Additionally, synthetic strings tend to maintain their tone and tension longer, reducing the need for frequent tuning adjustments. Another key feature of synthetic strings is their smooth playing feel. Polymers like polyamide and polyurethane have a lower friction coefficient than metal, resulting in less finger fatigue and a more comfortable playing experience. This is particularly beneficial for beginners or those with sensitive fingers. In terms of sound quality, synthetic strings offer a distinct tonal profile. They often produce a warmer, more mellow sound compared to the bright, crisp tone of metal strings. This makes them suitable for genres such as jazz, folk, and classical music where a softer, more nuanced sound is desired. Fluorocarbon strings, a subset of synthetic materials, are known for their clarity and brightness. These strings are often used on classical and flamenco guitars because they provide a clear, projecting sound without the harshness associated with some metal strings. Moreover, synthetic materials allow for greater versatility in string design. Manufacturers can tailor the physical properties of these polymers to achieve specific tonal characteristics or playing sensations. For instance, some synthetic strings are designed with a textured surface to mimic the feel of traditional gut strings but with the added durability of modern materials. In conclusion, synthetic materials bring a range of benefits to guitar strings, including enhanced durability, a smooth playing feel, and unique tonal qualities. These advantages make them an attractive option for guitarists seeking alternatives to traditional string materials, allowing for a more personalized and satisfying playing experience.
3. Natural Fibers
Natural fibers have been a cornerstone in the production of guitar strings for centuries, offering unique tonal qualities and playing characteristics that many musicians prefer. Here are three key natural fibers commonly used: 1. **Silk**: Historically, silk was used as a wrapping material for guitar strings, particularly in classical and flamenco guitars. Silk-wrapped strings provide a smooth, mellow tone with reduced finger noise. The silk wrapping helps to dampen the high-frequency overtones, resulting in a warmer and more balanced sound. 2. **Cotton**: Cotton is another natural fiber used in guitar string construction, often as a wrapping material or as part of the string's core. Cotton-wrapped strings are known for their clear, crisp tone and are often preferred by jazz and blues musicians. The cotton wrapping adds a layer of warmth and sustain to the sound without compromising clarity. 3. **Nylon**: Nylon, while technically a synthetic material derived from natural resources, is often categorized alongside natural fibers due to its organic origins. However, when discussing purely natural fibers, it's worth noting that some early nylon strings were made from plant-based polymers. In modern times, pure nylon strings are more common and are widely used in classical and flamenco guitars. These strings offer a bright, clear tone with good sustain and are known for their durability and resistance to wear. Each of these natural fibers contributes distinct sonic and tactile qualities to guitar strings, making them popular choices among musicians seeking specific tonal profiles. The use of these materials allows for a rich, expressive sound that resonates with both the player and the audience. Whether it's the smoothness of silk, the clarity of cotton, or the brightness of nylon, natural fibers continue to play an essential role in the world of guitar string manufacturing.
Manufacturing Process of Guitar Strings
The manufacturing process of guitar strings is a meticulous and multi-step procedure that ensures the production of high-quality, durable, and sonically superior strings. This process can be broadly divided into three critical stages: Wire Drawing and Winding, Coating and Treatment, and Quality Control and Testing. Each stage plays a vital role in transforming raw materials into the precise, consistent strings that musicians rely on. The journey begins with Wire Drawing and Winding, where raw metal wires are carefully drawn to precise diameters and wound onto spools. This initial step sets the foundation for the string's tone, strength, and playability. Following this, the strings undergo Coating and Treatment to enhance their performance and longevity. Finally, rigorous Quality Control and Testing ensure that every string meets stringent standards before it reaches the market. By understanding these stages, we can appreciate the craftsmanship and technology that go into creating the perfect guitar string. Let's delve deeper into the first stage: Wire Drawing and Winding.
1. Wire Drawing and Winding
In the manufacturing process of guitar strings, wire drawing and winding are crucial steps that significantly impact the final product's quality and performance. Wire drawing involves the reduction of wire diameter to achieve the desired thickness for guitar strings. This process begins with large spools of raw wire material, typically made from metals such as steel, nickel, or bronze. The wire is then pulled through a series of dies, each progressively smaller, to reduce its diameter while maintaining its strength and durability. This precise control over wire thickness ensures consistency in string tension and tone. Following wire drawing, the next step is winding, which adds the wrap wire to the core wire to create the final string. For wound strings, a thin wrap wire is wound around a core wire using specialized machinery. The core wire provides the string's structural integrity, while the wrap wire enhances its tone and sustain. The winding process must be meticulously controlled to ensure even spacing and tension of the wrap wire, as any irregularities can affect the string's playability and sound quality. Different winding patterns and materials can be used to achieve various tonal characteristics, making this step highly customizable based on the desired sound profile. The combination of precise wire drawing and careful winding ensures that guitar strings meet the high standards required by musicians. These processes not only influence the string's physical properties but also its acoustic performance, making them essential components in the overall manufacturing process of guitar strings. By understanding these steps, manufacturers can produce strings that offer optimal balance between playability, durability, and tone, ultimately enhancing the musical experience for guitarists.
2. Coating and Treatment
In the manufacturing process of guitar strings, coating and treatment play a crucial role in enhancing the performance, durability, and overall quality of the strings. After the wire drawing and winding processes, guitar strings undergo various coatings and treatments to achieve specific tonal characteristics and longevity. One common coating is the application of a thin layer of material such as nickel, bronze, or stainless steel over the core wire. For example, bronze-coated strings are known for their warm, rich tone and are often used in acoustic guitars. Nickel-coated strings, on the other hand, offer a brighter sound and are frequently used in electric guitars. Another significant treatment involves applying a protective layer to prevent corrosion and wear. This can include a clear or colored epoxy coating that shields the string from moisture and environmental factors, thereby extending its lifespan. Some manufacturers also use advanced treatments like nanotechnology-based coatings or specialized polymers to reduce finger squeak and improve string smoothness. Additionally, some guitar strings undergo a process called "winding" where a thin wire is wrapped around the core wire to increase the string's mass and alter its tone. This winding can be done with different materials and techniques to achieve various tonal profiles. For instance, flatwound strings have a smooth surface due to the flat shape of the winding wire, which reduces finger noise and provides a smooth playing feel. The final step often involves stretching and tuning the strings to ensure they meet the desired pitch and tension standards. This process helps stabilize the string's tuning and prevents excessive stretching or sagging over time. Overall, the coating and treatment stages are critical in defining the sound quality, playability, and durability of guitar strings. By carefully selecting and applying these coatings and treatments, manufacturers can produce strings that meet specific musical needs and preferences, ensuring that guitarists can achieve their desired sound with optimal performance.
3. Quality Control and Testing
Quality control and testing are crucial components of the manufacturing process for guitar strings, ensuring that each string meets the highest standards of performance, durability, and consistency. Here’s how it works: 1. **Material Inspection**: Before any string is produced, raw materials such as steel, nickel, bronze, or nylon undergo rigorous inspection. This involves checking for purity, tensile strength, and other physical properties to ensure they meet the required specifications. 2. **String Winding and Drawing**: After material selection, the wire is wound onto spools and then drawn to achieve the desired gauge (thickness). Quality control checks are performed at this stage to verify that the wire meets the specified gauge and has no defects such as kinks or irregularities. 3. **Twisting and Wrapping**: For wound strings, a thin wire wrap is applied over a core wire. The twisting process must be precise to maintain even tension and prevent uneven wear. Inspectors check for consistent wrap spacing and tension. 4. **Tension Testing**: Each string is subjected to tension tests to ensure it can withstand the stresses of tuning and playing. This involves stretching the string to its breaking point to verify its tensile strength. 5. **Frequency and Pitch Testing**: Strings are tuned to standard pitches and checked for accurate frequency response using electronic tuners or specialized equipment. This ensures that every string produces the correct pitch when played. 6. **Visual Inspection**: A thorough visual inspection is conducted for any visible defects such as corrosion, scratches, or uneven winding. Strings that fail this inspection are removed from production. 7. **Play Testing**: Sample strings are installed on guitars and played by experienced musicians to assess their tone quality, sustain, and overall performance. Feedback from these tests helps in fine-tuning the manufacturing process. 8. **Packaging and Storage**: Finally, strings are packaged in protective sleeves or envelopes to prevent damage during shipping and storage. The packaging is also inspected for quality before being shipped out. By integrating these rigorous quality control measures into every step of the manufacturing process, guitar string manufacturers can guarantee that their products deliver consistent performance and meet the expectations of musicians worldwide. This attention to detail not only enhances the playing experience but also extends the lifespan of the strings, making them a valuable investment for any guitarist.
Types of Guitar Strings and Their Applications
When it comes to selecting the right guitar strings, musicians must consider the specific needs of their instrument and the sound they aim to produce. The world of guitar strings is diverse, catering to various types of guitars and playing styles. This article delves into the three primary categories of guitar strings: Acoustic Guitar Strings, Electric Guitar Strings, and Specialty Strings such as Bass and Classical. Each type has its unique characteristics and applications, ensuring that musicians can find the perfect fit for their musical endeavors. For instance, Acoustic Guitar Strings are designed to enhance the natural resonance of acoustic guitars, while Electric Guitar Strings are optimized for the amplified sound of electric guitars. Specialty Strings, on the other hand, cater to specific genres and instruments like bass guitars and classical guitars. Understanding these differences is crucial for achieving the desired tone and performance. Let's start by exploring the nuances of Acoustic Guitar Strings, which are essential for bringing out the rich, warm tones that define acoustic music.
1. Acoustic Guitar Strings
Acoustic guitar strings are a crucial component of the instrument, significantly influencing its sound quality, playability, and overall performance. These strings are typically made from materials such as bronze, phosphor bronze, brass, or nylon, each offering distinct tonal characteristics and applications. **Bronze strings**, for instance, are known for their bright and clear tone, making them ideal for folk and country music. **Phosphor bronze strings** add a touch of warmth to the sound while maintaining clarity, making them versatile for various genres including bluegrass and pop. **Brass strings** produce a crisp, sharp tone that is often preferred by jazz and rock musicians who seek a more aggressive sound. **Nylon strings**, commonly used on classical guitars, provide a softer, more mellow tone suitable for classical and flamenco music. The gauge (thickness) of the strings also plays a critical role in their application. Thicker strings (higher gauge) produce a fuller, louder sound but can be harder on the fingers, while thinner strings (lower gauge) are easier to play but may lack depth in tone. For beginners, lighter gauge strings are often recommended due to their ease of playability. Experienced players, however, may prefer heavier gauge strings for their richer sound. In addition to material and gauge, the winding technique of the strings can affect their performance. **Coated strings**, such as those with a nanoweb or polyweb coating, offer extended string life by reducing corrosion and wear. These are particularly useful for players who perform frequently or in humid environments. **Flatwound strings**, with their smooth surface, reduce finger noise and are favored by jazz and blues musicians who emphasize smooth playing styles. The choice of acoustic guitar strings is highly dependent on personal preference, playing style, and the type of music being played. Understanding the different types of materials and gauges available allows musicians to tailor their sound to suit their needs, enhancing their overall musical experience. Whether you're a seasoned professional or an aspiring beginner, selecting the right acoustic guitar strings can make a significant difference in your instrument's sound quality and your enjoyment of playing it.
2. Electric Guitar Strings
Electric guitar strings are a crucial component for musicians who play electric guitars, offering a distinct sound and playing experience compared to acoustic or classical guitars. These strings are typically made from a combination of materials, with the most common being nickel-wound, stainless steel, and chrome-plated steel. Nickel-wound strings are popular for their warm, vintage tone and smooth feel, making them ideal for genres like rock, blues, and jazz. Stainless steel strings, on the other hand, provide a brighter, more aggressive sound and are often preferred by metal and hard rock players due to their clarity and sustain. Chrome-plated steel strings offer a balance between warmth and brightness, making them versatile for various musical styles. The construction of electric guitar strings involves wrapping a thin wire (the wind) around a thicker core wire. The core can be made from steel or another metal alloy, while the wind can vary in material and thickness to achieve different tonal characteristics. The gauge (thickness) of the strings also plays a significant role; lighter gauges are easier to bend but may lack sustain, while heavier gauges provide more sustain but can be harder on the fingers. Many players experiment with different gauges and string sets to find the perfect balance for their playing style and musical genre. In terms of application, electric guitar strings are used across a wide range of musical genres. They are particularly favored in rock, metal, and pop music where the amplified sound of the electric guitar is central to the overall sound. However, they are also used in jazz, blues, and even some forms of folk music where the unique tonal qualities of the electric guitar add depth and complexity to the music. When choosing electric guitar strings, musicians consider factors such as tone, durability, and playability. Some players prefer coated strings which have a layer of material like Elixir's Nanoweb or D'Addario's EXP to reduce finger squeak and extend string life. Others may opt for flatwound strings which have a smoother surface for faster playing styles. Overall, electric guitar strings are designed to deliver a specific sonic experience that complements the amplified nature of the electric guitar. By selecting the right type and gauge of string, musicians can tailor their sound to suit their musical needs, ensuring optimal performance and expression. Whether you're a seasoned professional or an aspiring musician, understanding the nuances of electric guitar strings can significantly enhance your playing experience and musical output.
3. Specialty Strings (Bass, Classical, etc.)
Specialty strings, such as bass and classical guitar strings, cater to specific musical genres and playing styles, offering unique tonal characteristics and performance attributes. **Bass Guitar Strings** are designed for the lower-pitched bass guitar, typically made from materials like nickel-wound steel, stainless steel, or flatwound steel. These strings are thicker and heavier than standard guitar strings to produce the deep, resonant tones required in bass music. They often feature a roundwound or flatwound construction to balance brightness and smoothness, making them suitable for various bass playing techniques. **Classical Guitar Strings**, on the other hand, are tailored for nylon-stringed guitars used in classical, flamenco, and folk music. These strings are usually made from nylon, fluorocarbon, or a combination of materials. The treble strings are often clear nylon or fluorocarbon, while the bass strings are wound with bronze or silver-plated copper wire. This combination provides a warm, rich tone with good sustain and a softer feel on the fingers, ideal for fingerstyle playing and intricate fingerwork. Some classical strings also include synthetic materials like fluorocarbon for enhanced clarity and durability. Other specialty strings include **Flatwound Strings**, which have a smooth, flat surface rather than the traditional roundwound texture. These are often used by jazz and fusion players who prefer a mellow, smooth tone with reduced finger noise. **Coated Strings**, such as Elixir or Nanoweb strings, feature a thin layer of coating that reduces corrosion and extends string life while maintaining tone quality. **Baritone Strings** are designed for baritone guitars, tuned lower than standard guitars, requiring heavier gauges to maintain tension and produce clear, deep notes. In summary, specialty strings are engineered to meet the specific demands of various musical genres and instruments. Whether it's the deep resonance of bass strings, the warm tones of classical strings, or the smooth playability of flatwound strings, each type is crafted to enhance performance and deliver the desired sound quality. Understanding these differences allows musicians to choose the right strings for their instrument and playing style, ensuring optimal sound and playability.