What Does Mro Stand For

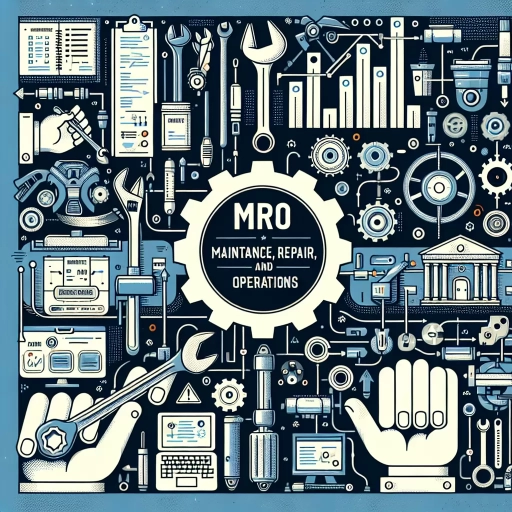
In the vast and complex world of industrial operations, business management, and financial transactions, acronyms play a crucial role in streamlining communication and enhancing efficiency. One such acronym that holds significant importance across multiple sectors is MRO. Standing for Maintenance, Repair, and Operations, MRO encompasses a broad range of activities essential for the smooth functioning of various industries. This article delves into the multifaceted nature of MRO, beginning with an in-depth **Understanding of the Acronym MRO**, where we explore its origins and core components. We then examine **MRO in Maintenance and Operations**, highlighting its critical role in ensuring the reliability and performance of equipment and facilities. Finally, we discuss **MRO in Business and Finance**, revealing how it impacts budgeting, procurement, and overall business strategy. By understanding these facets, readers will gain a comprehensive insight into the importance and applications of MRO. Let's start by **Understanding the Acronym MRO** to lay the foundation for our exploration.
Understanding the Acronym MRO
Understanding the acronym MRO is crucial in various industries, as it encapsulates a critical aspect of operational efficiency and cost management. The term MRO, which stands for Maintenance, Repair, and Operations, is often overlooked but plays a pivotal role in ensuring the smooth functioning of equipment and facilities. To delve into the significance of MRO, it is essential to explore three key areas: its definition and common usage, industry-specific applications, and historical context and evolution. Firstly, understanding the definition and common usage of MRO helps in recognizing its importance in daily operations. This involves identifying the types of activities and materials that fall under the MRO umbrella. Secondly, examining industry-specific applications highlights how different sectors, such as manufacturing, healthcare, and aviation, rely on MRO to maintain their infrastructure and equipment. Lastly, tracing the historical context and evolution of MRO reveals how this concept has adapted over time to meet changing technological and operational demands. By exploring these facets, one can gain a comprehensive understanding of how MRO contributes to the overall health and productivity of an organization. Let us begin by examining the definition and common usage of MRO, which forms the foundation of its significance in modern operations.
Definition and Common Usage
**Definition and Common Usage** MRO, an acronym for Maintenance, Repair, and Operations, is a term widely used across various industries to describe the activities and resources necessary for maintaining and optimizing the performance of equipment, facilities, and other assets. In its most basic form, MRO encompasses all the tasks required to ensure that machinery, buildings, and other physical assets remain in good working condition. This includes routine maintenance to prevent breakdowns, repairs to fix issues when they arise, and operational activities that support the day-to-day functioning of these assets. In common usage, MRO is often associated with manufacturing, aviation, healthcare, and other sectors where equipment reliability is critical. For instance, in manufacturing, MRO involves scheduled maintenance of production machinery to avoid downtime and ensure continuous production. In aviation, it includes the maintenance and repair of aircraft to meet stringent safety standards. In healthcare, MRO is crucial for maintaining medical equipment and facilities to ensure patient safety and care quality. The scope of MRO extends beyond just technical maintenance; it also involves procurement and inventory management of spare parts, tools, and consumables necessary for these activities. Effective MRO practices are essential for reducing operational costs, improving efficiency, enhancing safety, and extending the lifespan of assets. Companies often have dedicated MRO departments or outsource these services to specialized providers to ensure that their assets are well-maintained and operational at all times. Understanding the nuances of MRO is vital for any organization seeking to optimize its operations and minimize downtime. By integrating robust MRO strategies into their operational frameworks, businesses can achieve higher levels of productivity, reliability, and overall performance. This not only enhances operational efficiency but also contributes significantly to cost savings and improved customer satisfaction. In summary, MRO is a critical component of asset management that underpins the smooth functioning of various industries by ensuring that all necessary maintenance, repair, and operational activities are executed effectively.
Industry-Specific Applications
In the context of understanding the acronym MRO, it is crucial to delve into industry-specific applications where Maintenance, Repair, and Operations (MRO) play a pivotal role. Across various sectors, MRO activities are tailored to meet unique operational demands, ensuring efficiency, safety, and compliance. **Aerospace and Defense:** In the aerospace and defense industry, MRO is critical for maintaining aircraft and defense systems. This includes routine inspections, component replacements, and overhauls to ensure airworthiness and combat readiness. Advanced technologies like predictive maintenance and digital twins are increasingly used to optimize these processes. **Manufacturing:** In manufacturing, MRO involves the upkeep of production equipment and facilities. This encompasses preventive maintenance schedules, spare parts management, and repair services to minimize downtime and maximize productivity. Industry 4.0 technologies such as IoT sensors and AI-driven analytics are being integrated to enhance predictive maintenance capabilities. **Healthcare:** In healthcare, MRO focuses on medical equipment maintenance to ensure patient safety and compliance with regulatory standards. This includes regular calibration of diagnostic equipment, sterilization protocols, and emergency repairs to prevent disruptions in patient care. **Energy and Utilities:** The energy sector relies heavily on MRO for power generation, transmission, and distribution infrastructure. This involves scheduled maintenance of turbines, transformers, and other critical assets to prevent failures and ensure reliable energy supply. Renewable energy sources like wind farms and solar panels also require specialized MRO services. **Transportation:** In the transportation sector, MRO is essential for maintaining vehicles, rail networks, and maritime vessels. This includes routine servicing of engines, brakes, and other components to ensure safety and efficiency. Advanced data analytics are used to predict maintenance needs and optimize fleet performance. **Construction:** For the construction industry, MRO involves the maintenance of heavy machinery and equipment such as cranes, excavators, and bulldozers. Regular maintenance helps prevent accidents, reduces downtime, and extends the lifespan of these assets. **Maritime:** In the maritime industry, MRO is vital for maintaining ships and offshore platforms. This includes hull inspections, engine overhauls, and compliance with international maritime regulations to ensure safe and efficient operations. Each industry has its unique set of challenges and requirements for MRO activities. By understanding these specific needs, organizations can implement tailored strategies that enhance operational efficiency, reduce costs, and improve overall performance. The integration of advanced technologies further optimizes these processes, making MRO a cornerstone of modern industrial operations.
Historical Context and Evolution
The acronym MRO, standing for Maintenance, Repair, and Operations, has its roots deeply embedded in the historical context of industrial and manufacturing processes. The evolution of MRO is closely tied to the development of modern industry, particularly during the Industrial Revolution. In the late 18th and early 19th centuries, as factories began to replace traditional craftsmanship with mechanized production, the need for systematic maintenance and repair became paramount. Initially, maintenance was often reactive, with repairs being made only after equipment failed. However, as industries grew and production lines became more complex, the importance of proactive maintenance to prevent downtime and ensure efficiency became clear. In the early 20th century, the rise of mass production further emphasized the necessity of well-organized maintenance practices. Companies like Ford Motor Company, under the leadership of Henry Ford, implemented rigorous maintenance schedules to keep assembly lines running smoothly. This period also saw the introduction of preventive maintenance (PM) programs, which involved regular inspections and maintenance tasks to prevent equipment failures. The post-World War II era saw significant advancements in MRO practices. With the advent of new technologies and materials, industries began adopting more sophisticated maintenance strategies. The introduction of Total Productive Maintenance (TPM) in Japan during the 1950s and 1960s revolutionized MRO by involving all employees in maintenance activities and focusing on continuous improvement. This holistic approach not only improved equipment reliability but also enhanced overall plant efficiency. In recent decades, the integration of technology has transformed MRO practices. The advent of computerized maintenance management systems (CMMS) in the 1980s allowed for better tracking and scheduling of maintenance activities. The rise of Industry 4.0 technologies such as IoT (Internet of Things), AI (Artificial Intelligence), and predictive analytics has enabled real-time monitoring and predictive maintenance. These advancements allow for proactive interventions before equipment failures occur, significantly reducing downtime and improving operational efficiency. Today, MRO is a critical component of any industrial operation, ensuring that equipment runs at optimal levels while minimizing costs associated with repairs and downtime. The evolution from reactive to proactive maintenance strategies has been driven by technological innovations and the need for continuous improvement in industrial processes. Understanding this historical context is essential for appreciating the significance of MRO in modern manufacturing and operations management.
MRO in Maintenance and Operations
In the realm of Maintenance and Operations (MRO), the role of MRO is multifaceted and crucial for ensuring the smooth operation of any facility or equipment. This article delves into three key aspects that highlight the significance of MRO: its role in preventive maintenance, its impact on inventory management and procurement, and its overall effect on operational efficiency. By understanding these dimensions, organizations can better appreciate how MRO contributes to the longevity and performance of their assets. Preventive maintenance, for instance, is a cornerstone of MRO, as it involves scheduled inspections and repairs to prevent unexpected failures. Effective inventory management and procurement strategies are also essential, as they ensure that the right parts are available at the right time, minimizing downtime. Finally, the impact on operational efficiency cannot be overstated, as well-maintained equipment and streamlined processes directly influence productivity and cost savings. This article will explore each of these areas in depth, starting with the critical role of MRO in preventive maintenance.
Role in Preventive Maintenance
Preventive maintenance plays a crucial role in the realm of Maintenance, Repair, and Operations (MRO), ensuring that equipment and facilities operate at optimal levels while minimizing downtime and reducing costs. By scheduling regular maintenance activities, organizations can proactively identify and address potential issues before they escalate into major problems. This proactive approach not only extends the lifespan of equipment but also enhances overall system reliability, thereby improving operational efficiency. In preventive maintenance, routine tasks such as inspections, cleaning, lubrication, and part replacements are performed according to a predetermined schedule. This systematic approach helps in early detection of wear and tear, allowing for timely interventions that prevent sudden failures. For instance, regular oil changes in machinery can prevent overheating and mechanical breakdowns, while periodic inspections of electrical systems can identify potential hazards before they cause disruptions. Moreover, preventive maintenance supports safety protocols by ensuring that all equipment is in good working condition. This is particularly critical in industries where safety is paramount, such as manufacturing, healthcare, and transportation. By adhering to a preventive maintenance schedule, organizations can significantly reduce the risk of accidents and injuries, thereby protecting both personnel and assets. From an economic perspective, preventive maintenance offers substantial benefits. It reduces the need for costly repairs by addressing minor issues before they become major problems. Additionally, it minimizes downtime, which is essential for maintaining production levels and meeting customer demands. For example, in manufacturing plants, unplanned downtime can result in significant financial losses; preventive maintenance helps mitigate this risk by ensuring that production lines remain operational. Furthermore, preventive maintenance fosters a culture of continuous improvement within an organization. By analyzing data from maintenance activities, teams can identify trends and patterns that help in optimizing maintenance schedules and improving overall operational efficiency. This data-driven approach also aids in resource allocation, enabling organizations to prioritize their maintenance efforts effectively. In conclusion, preventive maintenance is a cornerstone of effective MRO strategies. It ensures that equipment operates reliably, enhances safety, reduces costs associated with repairs and downtime, and supports continuous improvement initiatives. By integrating preventive maintenance into their operational frameworks, organizations can achieve higher levels of efficiency, reliability, and profitability.
Inventory Management and Procurement
Inventory management and procurement are critical components of Maintenance, Repair, and Operations (MRO) in ensuring the smooth operation of any organization. Effective inventory management involves the systematic control of the flow of goods, products, and resources from raw materials to finished goods. This includes monitoring stock levels, tracking inventory movement, and optimizing storage to minimize waste and maximize efficiency. In the context of MRO, inventory management focuses on maintaining the right quantities of spare parts, tools, and consumables necessary for maintenance activities. This ensures that maintenance teams have the necessary resources readily available to perform their tasks promptly, reducing downtime and increasing overall productivity. Procurement, on the other hand, is the process of acquiring goods, services, or works from an external source. In MRO, procurement involves sourcing high-quality spare parts, equipment, and services that meet specific standards and requirements. A well-structured procurement strategy can help organizations negotiate better prices, ensure timely delivery, and maintain compliance with regulatory standards. By integrating procurement with inventory management, organizations can streamline their supply chain operations. For instance, just-in-time (JIT) procurement can be aligned with inventory levels to ensure that materials are received exactly when needed, thereby reducing storage costs and minimizing the risk of obsolescence. The synergy between inventory management and procurement is essential for optimizing MRO operations. Advanced technologies such as Enterprise Resource Planning (ERP) systems and Internet of Things (IoT) devices can enhance these processes by providing real-time data on inventory levels, automating reordering processes, and predicting future demand. Additionally, data analytics can help in identifying trends and patterns in inventory usage and procurement needs, enabling more informed decision-making. In summary, robust inventory management and procurement practices are foundational to efficient MRO operations. By ensuring that the right materials are available at the right time and in the right quantities, organizations can enhance their maintenance capabilities, reduce operational costs, and improve overall performance. This integrated approach not only supports the immediate needs of maintenance teams but also contributes to long-term strategic goals by fostering a culture of efficiency and reliability within the organization.
Impact on Operational Efficiency
The integration of Maintenance, Repair, and Operations (MRO) into an organization's maintenance and operations framework significantly enhances operational efficiency. By streamlining the procurement, inventory management, and maintenance processes, MRO ensures that all necessary materials and services are readily available when needed. This proactive approach minimizes downtime and reduces the likelihood of unexpected equipment failures, thereby optimizing production schedules and improving overall productivity. Effective MRO practices involve meticulous planning and execution, including predictive maintenance strategies that leverage advanced technologies such as IoT sensors and AI-driven analytics. These tools enable real-time monitoring of equipment health, allowing for timely interventions that prevent major breakdowns. Additionally, MRO fosters a culture of continuous improvement by encouraging regular audits and assessments to identify areas for optimization. Inventory management is another critical aspect where MRO excels. By implementing just-in-time inventory systems and optimizing stock levels, organizations can avoid both stockouts and overstocking scenarios. This not only reduces storage costs but also ensures that critical spare parts are always available, further reducing downtime. Moreover, MRO promotes standardization across different departments and locations within an organization. Standardized procedures and best practices ensure consistency in maintenance activities, which in turn enhances the reliability of equipment and reduces variability in performance. This standardization also facilitates better communication among teams, leading to more efficient collaboration and problem-solving. From a financial perspective, MRO can lead to significant cost savings. By reducing the frequency of unplanned repairs and minimizing the need for emergency purchases, organizations can lower their maintenance expenditures. Furthermore, optimized inventory levels help in avoiding unnecessary purchases and reducing waste. In conclusion, the impact of MRO on operational efficiency is multifaceted and profound. It enhances productivity by minimizing downtime, optimizes resource allocation through better inventory management, promotes a culture of continuous improvement, and leads to substantial cost savings. As a result, integrating MRO into maintenance and operations strategies is essential for any organization seeking to maximize its operational efficiency and competitiveness in today's fast-paced business environment.
MRO in Business and Finance
In the realm of business and finance, Maintenance, Repair, and Operations (MRO) plays a crucial role in ensuring the smooth operation of physical assets and infrastructure. Effective MRO strategies are multifaceted, encompassing several key areas that collectively contribute to operational efficiency and cost optimization. First, **Budgeting and Cost Management** is essential for allocating resources effectively, preventing unexpected expenses, and maintaining financial stability. Second, **Supplier Relationships and Contracts** are vital for securing reliable and high-quality supplies, negotiating favorable terms, and fostering long-term partnerships. Third, **Technology Integration for MRO Processes** enhances efficiency through automation, data analytics, and real-time monitoring, allowing businesses to make informed decisions quickly. By focusing on these three pillars, organizations can significantly improve their MRO practices. Let's delve into the first of these critical components: **Budgeting and Cost Management**.
Budgeting and Cost Management
**Budgeting and Cost Management in MRO** Effective budgeting and cost management are crucial components of Maintenance, Repair, and Operations (MRO) in business and finance. MRO involves the procurement, storage, and distribution of materials and equipment necessary for maintaining and repairing physical assets. A well-structured budget ensures that these activities are carried out efficiently without overspending. To begin with, **budgeting** in MRO involves forecasting and allocating financial resources for maintenance activities, spare parts, and labor costs. This process starts with a thorough analysis of historical data to predict future maintenance needs. Companies must identify critical assets, estimate downtime costs, and plan for preventive maintenance to minimize unexpected expenses. Budgeting also includes setting aside funds for capital expenditures such as new equipment or technology upgrades that can enhance operational efficiency. **Cost management** is equally important as it involves controlling and optimizing the expenses associated with MRO activities. This includes implementing cost-saving strategies like just-in-time inventory management to reduce storage costs and minimize waste. Companies can also leverage technology such as Enterprise Asset Management (EAM) software to track asset performance, schedule maintenance, and manage inventory levels more effectively. Additionally, negotiating contracts with suppliers and vendors can help secure better prices for spare parts and services. Another key aspect of cost management is **labor cost optimization**. This involves ensuring that the right skills are available at the right time to perform maintenance tasks efficiently. Training programs can help upskill existing staff, reducing the need for external contractors. Furthermore, adopting a Total Productive Maintenance (TPM) approach encourages all employees to take ownership of maintenance activities, leading to improved productivity and reduced labor costs. **Inventory management** is another critical area within MRO budgeting and cost management. Overstocking can lead to unnecessary holding costs, while understocking can result in costly downtime. Implementing a robust inventory management system helps in maintaining optimal stock levels, ensuring that critical spare parts are always available when needed. This can be achieved through techniques like Economic Order Quantity (EOQ) analysis and Vendor-Managed Inventory (VMI) agreements. In conclusion, robust budgeting and cost management practices are essential for effective MRO operations. By accurately forecasting maintenance needs, optimizing costs through efficient inventory management and labor utilization, and leveraging technology to streamline processes, businesses can ensure their physical assets are well-maintained while controlling expenses. This not only enhances operational efficiency but also contributes significantly to the overall financial health of the organization.
Supplier Relationships and Contracts
Supplier relationships and contracts are pivotal components in the realm of Maintenance, Repair, and Operations (MRO) within business and finance. These relationships are built on trust, reliability, and mutual benefit, ensuring that the necessary materials, equipment, and services are consistently available to maintain operational efficiency. Effective supplier relationships involve clear communication, transparent expectations, and a robust contractual framework. A well-crafted contract outlines the terms and conditions of the partnership, including delivery schedules, quality standards, pricing, and dispute resolution mechanisms. This legal agreement protects both parties by defining responsibilities and liabilities, thereby reducing the risk of misunderstandings or disputes. For instance, a service-level agreement (SLA) can specify response times for maintenance requests, ensuring that downtime is minimized and operations remain uninterrupted. Moreover, strong supplier relationships can lead to strategic partnerships that go beyond mere transactional interactions. Suppliers may offer value-added services such as inventory management, technical support, and training programs, which can enhance the overall efficiency of MRO operations. These partnerships can also foster innovation as suppliers may provide insights into new technologies or best practices that can be integrated into the business. In addition to contractual obligations, building trust through consistent performance and reliability is crucial. Suppliers who consistently meet or exceed expectations are more likely to be considered for long-term contracts or preferred supplier status. This trust can also lead to more flexible terms and conditions, such as just-in-time delivery arrangements or negotiated pricing based on volume commitments. From a financial perspective, well-managed supplier relationships can significantly impact the bottom line. By negotiating favorable terms and ensuring timely deliveries, businesses can reduce costs associated with inventory holding, minimize downtime-related losses, and optimize resource allocation. Furthermore, a stable supply chain reduces the financial risks associated with supply disruptions, allowing for better budgeting and forecasting. In conclusion, supplier relationships and contracts are essential for effective MRO management in business and finance. By establishing clear contractual frameworks and fostering trust through reliable performance, businesses can ensure continuous operational efficiency, reduce costs, and enhance overall profitability. This strategic approach to supplier management not only supports day-to-day operations but also positions the organization for long-term success in a competitive market.
Technology Integration for MRO Processes
Technology integration is revolutionizing Maintenance, Repair, and Operations (MRO) processes by enhancing efficiency, reducing costs, and improving overall asset performance. In the context of MRO in business and finance, technology plays a pivotal role in streamlining operations. Advanced software solutions such as Enterprise Asset Management (EAM) systems and Computerized Maintenance Management Systems (CMMS) enable organizations to track asset health, schedule maintenance, and manage inventory more effectively. These systems provide real-time data analytics, allowing for predictive maintenance strategies that prevent unexpected downtime and extend the lifespan of equipment. The adoption of Internet of Things (IoT) technology further enhances MRO by enabling the collection of data from sensors installed on equipment. This data can be used to monitor performance metrics, detect anomalies, and trigger maintenance alerts before issues escalate. Additionally, Artificial Intelligence (AI) and Machine Learning (ML) algorithms can analyze historical data to predict future maintenance needs, optimizing resource allocation and reducing unnecessary repairs. Mobile technologies also play a crucial role in modernizing MRO processes. Mobile apps allow technicians to access work orders, update status in real-time, and receive notifications on their handheld devices. This improves communication between teams and ensures that all stakeholders are informed about the status of maintenance activities. Moreover, digital twin technology is being increasingly used in MRO to create virtual replicas of physical assets. These digital twins simulate real-world conditions, enabling organizations to test maintenance scenarios without affecting actual operations. This approach helps in identifying potential issues before they occur and in optimizing maintenance schedules. Blockchain technology is another emerging trend in MRO, offering enhanced transparency and security in supply chain management. By creating an immutable record of transactions, blockchain ensures that spare parts are genuine and traceable, reducing the risk of counterfeit components. In terms of financial benefits, technology integration in MRO leads to significant cost savings. By reducing downtime through predictive maintenance, organizations can minimize lost productivity and associated revenue losses. Additionally, optimized inventory management reduces waste and unnecessary purchases. Overall, the integration of advanced technologies into MRO processes is transforming how businesses manage their assets. It not only improves operational efficiency but also provides a competitive edge by ensuring that assets are always in optimal working condition. As technology continues to evolve, it is likely that MRO processes will become even more sophisticated, driving further improvements in business operations and financial performance.