What Is Ink Made Out Of

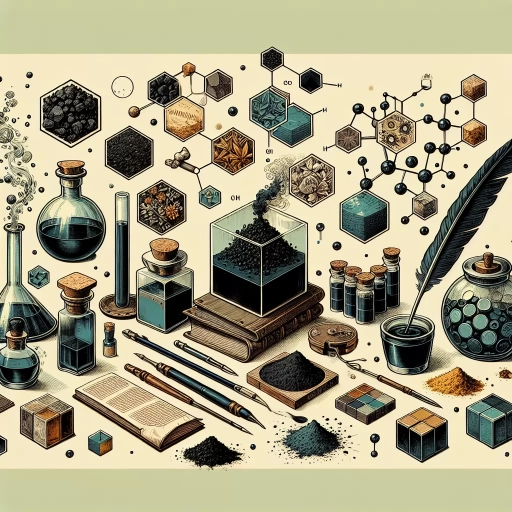
Ink, a fundamental tool in human communication and artistic expression, has a rich history and complex composition. From ancient civilizations to modern times, ink has evolved significantly, reflecting advancements in technology and changing societal needs. This article delves into the multifaceted world of ink, exploring its historical development, chemical composition, and various types with their applications. We begin by tracing the historical development of ink, from its earliest forms derived from natural sources such as soot and plant dyes to its sophisticated modern formulations. This journey through time sets the stage for understanding the chemical composition of modern ink, which involves a blend of pigments, dyes, solvents, and additives. Finally, we examine the diverse types of ink and their specific uses, ranging from traditional calligraphy to cutting-edge digital printing. By understanding these aspects, we gain a deeper appreciation for the versatility and importance of ink in our daily lives. Let us start with the historical development of ink, a story that spans millennia and reveals the ingenuity of our ancestors.
Historical Development of Ink
The historical development of ink is a rich and multifaceted narrative that spans thousands of years, influenced by various ancient civilizations, evolving ingredients, and cultural and technological advancements. From the earliest formulations in ancient China, Egypt, and Greece to the sophisticated inks of modern times, this journey is marked by significant milestones. **Ancient Civilizations and Early Ink Formulations** highlight the initial discoveries and innovations that laid the groundwork for ink production. The **Evolution of Ink Ingredients Over Time** reveals how different eras introduced new materials and techniques, enhancing the quality and durability of ink. Additionally, **Influence of Cultural and Technological Advancements** underscores how societal changes and technological breakthroughs have continuously shaped the development of ink. By exploring these facets, we can gain a comprehensive understanding of how ink has transformed over centuries. Let us begin by delving into the contributions of **Ancient Civilizations and Early Ink Formulations**.
Ancient Civilizations and Early Ink Formulations
Ancient civilizations played a pivotal role in the development of ink, a substance that has been integral to human communication and artistic expression for thousands of years. The earliest known ink formulations date back to around 4000 BCE, during the Neolithic period. In ancient China, ink was made from soot or lampblack mixed with animal glue or plant resin, creating a durable and water-resistant writing medium. This early Chinese ink, known as "India ink," was highly valued for its deep black color and was used extensively in calligraphy and art. In ancient Egypt, around 2500 BCE, ink was primarily composed of a mixture of soot or carbon-based pigments with gum arabic, a natural adhesive derived from the sap of the acacia tree. This combination allowed for smooth writing on papyrus and was essential for recording historical events, religious texts, and literary works. The Egyptians also developed red ink by using iron oxide or ochre, which they used to highlight important sections of texts. The ancient Greeks and Romans adopted similar ink formulations, often using soot mixed with gum arabic or other plant-based adhesives. These early inks were not only used for writing but also for artistic purposes, such as in the creation of illuminated manuscripts. The durability and versatility of these early ink formulations facilitated the spread of knowledge and culture across ancient civilizations. In addition to these primary components, various additives were used to enhance the properties of ink. For example, ancient Chinese ink makers might add other substances like beeswax or plant oils to improve flow and consistency. Similarly, medieval European scribes used iron gall ink, which was made by mixing iron salts with tannins extracted from plants like oak galls. This type of ink was particularly durable but had the drawback of being corrosive over time. The historical development of ink is a testament to human ingenuity and the need for effective communication tools. From ancient soot-based inks to more sophisticated formulations involving natural adhesives and pigments, each civilization contributed to the evolution of ink technology. These early formulations laid the groundwork for modern ink production, which now includes a wide range of synthetic and organic materials tailored to specific applications such as printing, writing, and artistic expression. Understanding the origins and development of ink provides valuable insights into the technological advancements and cultural achievements of ancient societies.
Evolution of Ink Ingredients Over Time
The evolution of ink ingredients over time reflects a journey of innovation and adaptation, driven by technological advancements, environmental considerations, and the quest for superior performance. **Ancient Civilizations:** The earliest inks, dating back to around 4000 BCE, were derived from natural sources such as soot, charcoal, and plant dyes. In ancient China, ink was made from soot mixed with animal glue and other binders, while in ancient Egypt, ink was often based on lampblack (carbon particles) mixed with gum arabic. **Middle Ages:** During the Middle Ages, ink recipes became more sophisticated with the addition of ingredients like iron salts and tannins, which improved durability and color intensity. The use of gallnuts (galls) to create iron gall ink became widespread; this ink was known for its dark color and permanence but had the drawback of being corrosive. **Industrial Revolution:** The Industrial Revolution marked a significant shift with the introduction of synthetic dyes and pigments. Aniline dyes, discovered in the mid-19th century, offered vibrant colors but were often toxic and unstable. The development of carbon-based inks, such as India ink, provided a more durable alternative. **20th Century:** In the 20th century, the advent of modern chemistry led to the creation of a wide range of synthetic inks. Dye-based inks became common in ballpoint pens and printers, while pigment-based inks were used in high-quality printing applications due to their lightfastness and durability. **Modern Era:** Today, ink formulations are highly specialized and tailored to specific applications. For instance, archival-quality inks are designed to be lightfast and non-reactive to ensure long-term preservation of documents. Eco-friendly inks made from biodegradable materials and plant-based dyes are gaining popularity as environmental concerns grow. Additionally, advancements in nanotechnology have led to the development of nano-inks with enhanced properties such as improved flow characteristics and increased color intensity. Overall, the evolution of ink ingredients has been a continuous process driven by technological innovation and changing societal needs.
Influence of Cultural and Technological Advancements
The influence of cultural and technological advancements has significantly shaped the historical development of ink, transforming it from a primitive substance to a sophisticated medium. Initially, ancient civilizations such as the Egyptians, Chinese, and Greeks used natural materials like soot, plant dyes, and animal products to create ink. These early formulations were often crude but effective for their time, reflecting the technological limitations and cultural practices of their respective eras. As civilizations evolved, so did the composition and quality of ink. The invention of the quill pen in ancient Rome necessitated a more viscous and durable ink, leading to the development of iron gall ink. This innovation, which combined iron salts with tannins from plants, became a standard for centuries due to its dark color and longevity on parchment. The advent of the Industrial Revolution marked a pivotal moment in the history of ink. New manufacturing processes and the discovery of synthetic dyes enabled mass production of higher-quality inks. Aniline dyes, introduced in the mid-19th century, offered vibrant colors and greater lightfastness, expanding ink's applications beyond writing to include printing and art. Technological advancements in the 20th century further diversified ink formulations. The invention of ballpoint pens required quick-drying, low-viscosity inks that could flow smoothly through tiny metal balls. This led to the development of modern gel inks and rollerball inks, which combined the benefits of traditional fountain pen inks with the convenience of ballpoint pens. Cultural influences also played a crucial role in shaping ink's evolution. In Japan, for example, the art of calligraphy drove the refinement of sumi ink, which is still highly valued today for its rich texture and expressive qualities. Similarly, in Islamic cultures, intricate calligraphy necessitated the creation of finely tuned inks that could produce delicate lines and intricate designs. In recent years, technological innovations have continued to push the boundaries of what ink can achieve. Digital printing technologies have given rise to specialized inks for inkjet printers, capable of producing high-resolution images with remarkable color accuracy. Additionally, advancements in nanotechnology have led to the development of conductive inks used in electronics and wearable technology. Overall, the interplay between cultural demands and technological innovations has been instrumental in transforming ink from a simple writing medium into a versatile tool with diverse applications across various fields. This dynamic relationship continues to drive the evolution of ink, ensuring its relevance in an increasingly complex and technologically advanced world.
Chemical Composition of Modern Ink
The chemical composition of modern ink is a complex blend of various components, each playing a crucial role in its performance and quality. At the heart of ink formulation are pigments and dyes, which provide the color and lightfastness essential for vibrant and durable prints. Additionally, binders and viscosity modifiers are critical for ensuring the ink adheres well to different surfaces and maintains the right consistency for smooth application. Furthermore, additives such as surfactants, UV stabilizers, and anti-foaming agents enhance the ink's overall performance by improving its flow, stability, and resistance to environmental factors. Understanding these components is vital for appreciating the sophistication of modern ink. Let's delve into the first of these key elements: **Pigments and Dyes Used in Ink Production**.
Pigments and Dyes Used in Ink Production
In the production of modern ink, pigments and dyes play crucial roles in determining the color, durability, and overall performance of the ink. **Pigments** are finely ground powders that are dispersed in a liquid carrier to create the ink. Unlike dyes, pigments do not dissolve in the carrier but instead remain suspended, providing vibrant colors and excellent lightfastness. Common pigments used include carbon black for black ink, titanium dioxide for white ink, and various iron oxides for red, yellow, and brown hues. These pigments are often derived from natural sources or synthesized chemically to ensure consistency and quality. For instance, carbon black is produced through the incomplete combustion of fossil fuels, while titanium dioxide is synthesized through the chloride process or sulfate process. **Dyes**, on the other hand, are dissolved in the liquid carrier and are typically used in water-based inks due to their solubility. Dyes offer a wider range of colors compared to pigments but generally lack the lightfastness and durability that pigments provide. They are commonly used in food coloring, textiles, and certain types of printing inks where color intensity is more important than longevity. In ink production, dyes such as Direct Blue 199 and Acid Yellow 17 are used to achieve specific shades and hues that might be difficult to obtain with pigments alone. The choice between pigments and dyes depends on the intended application of the ink. For example, inks used for artistic purposes or high-quality printing often rely on pigments due to their superior lightfastness and color stability over time. Conversely, inks used for temporary applications or where cost is a significant factor may use dyes due to their lower production costs and ease of formulation. In addition to their primary function of providing color, both pigments and dyes must be compatible with other components of the ink formulation, such as binders, surfactants, and solvents. The chemical composition of these additives can affect how well the pigments or dyes are dispersed and how they interact with the substrate (paper, fabric, etc.) during the printing process. Overall, the careful selection and combination of pigments and dyes are critical in modern ink production to ensure that the final product meets the required standards of color accuracy, durability, and performance. This balance is essential for achieving high-quality prints that retain their vibrancy and integrity over time.
Binders and Viscosity Modifiers in Ink Formulations
In the realm of modern ink formulations, binders and viscosity modifiers play crucial roles in determining the performance, durability, and overall quality of the ink. **Binders** are polymers or resins that serve as the backbone of the ink, holding the pigment particles together and adhering them to the substrate. Common binders include acrylic polymers, polyvinyl acetate (PVA), and polyurethane. These binders not only ensure that the ink adheres well to various surfaces but also contribute to its resistance against wear, tear, and environmental factors such as light and moisture. For instance, in flexographic inks used for packaging, acrylic polymers are often chosen for their excellent adhesion properties and flexibility. **Viscosity modifiers**, on the other hand, are additives that adjust the flow characteristics of the ink to meet specific printing requirements. Viscosity is a critical parameter because it affects how easily the ink flows through the printing system and how it spreads on the substrate. Thickeners like cellulose derivatives or synthetic polymers can increase viscosity, making the ink more suitable for screen printing or gravure processes where higher viscosity is needed. Conversely, solvents or surfactants can reduce viscosity, making it ideal for processes like offset printing where smooth flow is essential. The balance of viscosity is particularly important in digital printing inks, where precise control over droplet formation is necessary for high-resolution images. The interplay between binders and viscosity modifiers is intricate; binders influence the rheological properties of the ink by affecting its flow behavior, while viscosity modifiers fine-tune these properties to optimize printability. For example, in UV-curable inks used in digital printing, photoinitiators initiate polymerization upon exposure to UV light, forming a solid film that adheres well due to the binder. Simultaneously, viscosity modifiers ensure that this process occurs smoothly without clogging the print heads or causing uneven spreading. In summary, binders provide structural integrity and adhesion in ink formulations, while viscosity modifiers adjust the ink's flow characteristics to suit various printing techniques. Together, they ensure that modern inks meet the demands of diverse applications, from high-speed commercial printing to precise digital imaging. Understanding these components is essential for formulating inks that deliver consistent performance and quality across different substrates and printing processes.
Additives for Performance Enhancement
In the realm of modern ink formulation, additives play a crucial role in enhancing performance characteristics that are essential for various applications. These additives are meticulously selected and integrated into the ink composition to improve its functionality, durability, and overall quality. One key type of additive is **wetting agents**, which reduce the surface tension of the ink, facilitating better flow and wetting properties on different substrates. This is particularly important for ensuring consistent print quality across various materials, such as paper, plastics, and textiles. Another critical category is **rheology modifiers**, which adjust the viscosity and flow behavior of the ink. These additives help maintain optimal ink flow during the printing process, preventing issues like clogging or uneven distribution. **UV stabilizers** are also vital, as they protect the ink from degradation caused by exposure to ultraviolet light. This is especially important for inks used in outdoor applications or those that will be exposed to sunlight for extended periods, ensuring that the color remains vibrant and stable over time. **Antifoaming agents** are another essential additive, as they prevent the formation of foam during the manufacturing and printing processes. Foam can lead to defects in the printed output, such as bubbles or uneven surfaces, so these agents are crucial for maintaining print quality. **Corrosion inhibitors** are also included to protect metal components in printing equipment from corrosion caused by the ink's chemical composition. This extends the lifespan of the equipment and ensures smooth operation. Additionally, **antimicrobial additives** may be incorporated to prevent the growth of bacteria and fungi within the ink, which can lead to spoilage and affect print performance. These additives are particularly important for water-based inks that are more susceptible to microbial contamination. **Fillers** such as silica or calcium carbonate can also be added to enhance the ink's opacity and improve its covering power, making it more effective for certain printing tasks. Lastly, **pH adjusters** and **buffering agents** are used to maintain a stable pH level in the ink, which is crucial for ensuring consistent performance and preventing chemical reactions that could degrade the ink over time. These additives work together to create a balanced and robust ink formulation that meets the demands of modern printing technologies and applications. By carefully selecting and combining these additives, manufacturers can produce high-quality inks that deliver superior performance, durability, and aesthetic appeal.
Types of Ink and Their Applications
In the world of inks, diversity and specialization are key to meeting various needs across different industries and applications. Understanding the types of ink and their unique properties is essential for selecting the right ink for specific tasks. This article delves into three critical areas: the distinction between dye-based and pigment-based inks, the specialized inks designed for printing and writing, and the industrial and artistic uses of different ink types. By exploring these categories, readers will gain a comprehensive understanding of how different inks are tailored to serve distinct purposes. For instance, dye-based inks are known for their vibrant colors but may lack durability, while pigment-based inks offer longevity but can be less vibrant. Specialized inks for printing and writing are engineered to optimize performance on specific surfaces, ensuring clarity and longevity. Additionally, industrial and artistic applications of inks reveal their versatility in fields such as manufacturing, art, and even medical technology. To begin this journey, let's first examine the fundamental differences between dye-based and pigment-based inks, a crucial distinction that sets the stage for understanding the broader spectrum of ink applications.
Dye-Based vs. Pigment-Based Inks
When it comes to understanding the different types of inks, one crucial distinction lies between dye-based and pigment-based inks. These two categories differ significantly in their composition, performance, and applications. **Dye-Based Inks** are formulated with dissolved dyes, which are typically dissolved in a liquid carrier. These inks penetrate the paper or substrate, creating the color from within. Dye-based inks are known for their vibrant colors and are often used in inkjet printers for home and office use. However, they have some drawbacks; they tend to fade more quickly over time, especially when exposed to light, and may not be as durable as pigment-based inks. Additionally, dye-based inks can bleed or feather on certain types of paper, affecting the print quality. **Pigment-Based Inks**, on the other hand, contain finely ground pigments suspended in a liquid carrier. Unlike dyes, these pigments sit on the surface of the paper rather than being absorbed into it. This results in more durable and lightfast prints that resist fading and bleeding better than dye-based inks. Pigment-based inks are commonly used in professional printing applications such as fine art photography, archival printing, and high-end commercial printing where longevity and color accuracy are paramount. They also offer better resistance to water and UV light, making them ideal for outdoor signage and other applications where exposure to elements is a concern. In terms of **applications**, dye-based inks are suitable for everyday printing needs such as documents, emails, and casual photos. They are generally less expensive than pigment-based inks and provide adequate performance for most home users. However, for more demanding tasks like professional photography or archival purposes where print longevity is critical, pigment-based inks are the preferred choice due to their superior durability and color stability. In summary, while both types of inks have their own strengths and weaknesses, understanding these differences is essential for selecting the right ink for specific printing needs. Dye-based inks offer vibrant colors but lack durability, making them best suited for casual use. In contrast, pigment-based inks provide long-lasting results with excellent color retention but come at a higher cost and are typically used in professional settings where print quality is paramount. This distinction highlights the importance of choosing the appropriate type of ink based on the intended application to ensure optimal performance and satisfaction.
Specialized Inks for Printing and Writing
Specialized inks for printing and writing are tailored to meet specific needs and applications, offering unique properties that set them apart from standard inks. **Conductive Inks**, for instance, are designed to facilitate the flow of electricity and are commonly used in the production of electronic devices, such as circuit boards and sensors. These inks contain metallic particles like silver or copper, which provide high conductivity while maintaining flexibility and durability. **UV-Curable Inks** are another type of specialized ink, known for their rapid curing process under ultraviolet light. This property makes them ideal for high-speed printing applications, particularly in digital printing technologies. They offer excellent adhesion to various substrates, including plastics and metals, and are widely used in packaging, labels, and signage. **Thermochromic Inks** change color in response to temperature changes, making them popular for novelty items like temperature-sensitive stickers and smart packaging. These inks contain leuco dyes, weak acids, and cholesteric liquid crystals that react to heat variations, providing a dynamic visual effect. **Biodegradable Inks**, on the other hand, are formulated from renewable resources such as plant-based oils and natural pigments. They are environmentally friendly and decompose more easily than traditional inks, making them suitable for applications where sustainability is a priority, such as in eco-friendly packaging and printing. **Security Inks** are designed to prevent counterfeiting and unauthorized reproduction. These inks can be invisible under normal light but become visible under specific conditions like ultraviolet light or when exposed to certain chemicals. They are commonly used in banknotes, passports, and other secure documents. **Fluorescent Inks** emit light at a longer wavelength than they absorb, resulting in a glowing effect. These inks are often used in safety signs, highlighters, and artistic applications where high visibility is required. **Magnetic Inks** contain ferromagnetic particles and are used in applications requiring magnetic properties, such as in the production of magnetic stripes on credit cards and identification cards. Each type of specialized ink has its own set of characteristics and uses, catering to diverse industries and needs. Understanding these different types of inks is crucial for selecting the right ink for specific printing and writing applications, ensuring optimal performance and functionality.
Industrial and Artistic Uses of Different Ink Types
Ink, a versatile medium, has been a cornerstone in both industrial and artistic applications for centuries. **Dye-based inks**, commonly used in printing and writing, are dissolved in water or other solvents, making them ideal for everyday use such as ballpoint pens and inkjet printers. Their vibrant colors and quick-drying properties make them a favorite among artists for watercolor and calligraphy. **Pigment-based inks**, on the other hand, consist of finely ground pigments suspended in a liquid carrier. These inks are more lightfast and durable, making them suitable for high-quality printing, such as offset printing and screen printing. In artistic contexts, pigment-based inks are used in tattooing due to their permanence and resistance to fading. **Iron gall ink**, historically significant, is made from a mixture of iron salts and tannins extracted from plants. This ink was widely used in medieval manuscripts and is still valued by calligraphers and artists for its distinctive blue-black color and durability. However, its corrosive nature requires careful handling. **Carbon-based inks**, including India ink and Chinese ink, are derived from soot or lampblack mixed with a binding agent. These inks are renowned for their deep black color and are often used in traditional Asian art forms like sumi-e and calligraphy. Their high lightfastness and water resistance also make them popular in technical drawing and illustration. **Fountain pen ink** is another specialized type, designed to flow smoothly through the nib of a fountain pen. Available in a wide range of colors, these inks are formulated to be non-corrosive and maintain consistent flow, making them a favorite among writers and artists who value precision and expressiveness. In industrial settings, **UV-curable inks** are used in digital printing technologies where they are cured instantly by ultraviolet light. This process allows for rapid production and is commonly seen in label printing, packaging, and signage. **Thermal transfer inks** are used in thermal transfer printing processes, where heat is applied to transfer the ink onto materials like plastics and metals, often used in barcode labels and identification tags. **Conductive inks**, containing metallic particles like silver or copper, are used in electronics manufacturing to create circuits and electrodes. These inks play a crucial role in the production of printed circuit boards, RFID tags, and flexible electronics. **Biodegradable inks**, made from natural materials such as plant dyes or algae-based pigments, are gaining traction due to environmental concerns. These inks are used in packaging and printing applications where sustainability is a priority. Each type of ink has its unique characteristics, advantages, and applications, making them indispensable tools across various industries and artistic disciplines. Understanding the properties and uses of different ink types allows for better selection and utilization in both creative and industrial contexts.