What Does Item Processed Mean

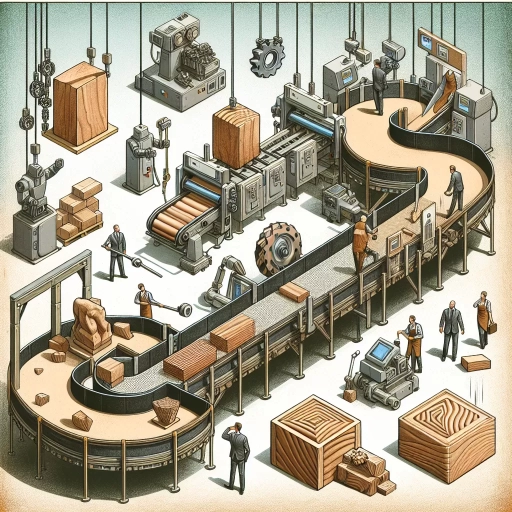
In the realm of logistics, supply chain management, and e-commerce, the term "item processed" is a critical milestone that signifies the transition of an item from one stage to another within a system. This concept is multifaceted, involving not just the physical movement of goods but also the intricate processes that ensure efficiency and accuracy. To fully grasp what "item processed" means, it is essential to delve into three key aspects: understanding the concept itself, exploring the process behind it, and examining its implications and benefits. **Understanding the Concept of "Item Processed"** is the foundational step, where we define what it means for an item to be processed and how this status update reflects in various systems. This understanding sets the stage for a deeper exploration of **The Process Behind Item Processing**, which reveals the mechanisms and technologies involved in moving items through different stages. Finally, **Implications and Benefits of Item Processing** highlight how this process impacts businesses, consumers, and the overall efficiency of operations. By examining these facets, we can gain a comprehensive insight into the significance of "item processed" in modern commerce. Let's begin by **Understanding the Concept of "Item Processed"**.
Understanding the Concept of "Item Processed"
In the realm of operational efficiency and data management, the term "Item Processed" holds significant importance across various industries. This concept is not just a simple metric but a multifaceted idea that requires a deep understanding to fully appreciate its implications. To grasp the essence of "Item Processed," it is crucial to delve into its definition and context, exploring how it fits within broader operational frameworks. Additionally, examining industry-specific applications reveals how different sectors leverage this concept to optimize their processes. However, common misconceptions about "Item Processed" can lead to inefficiencies and misinterpretations, making it essential to clarify these misunderstandings. By understanding the definition, industry-specific applications, and addressing common misconceptions, we can gain a comprehensive insight into the concept of "Item Processed," ultimately enhancing our ability to manage and analyze data effectively. This article aims to provide a detailed exploration of these aspects, leading to a clearer understanding of the concept of "Item Processed."
Definition and Context
Understanding the concept of "item processed" requires a clear grasp of its definition and context. At its core, "item processed" refers to the completion of a specific task or operation on an individual unit within a larger set, such as data entries, orders, or physical products. This term is often used in various fields including logistics, manufacturing, data processing, and customer service to denote that an item has been successfully handled according to predefined procedures. In the context of logistics and supply chain management, "item processed" signifies that a product has been received, inspected, and possibly packaged or shipped. For instance, in an e-commerce setting, when an order is marked as "item processed," it indicates that the order has been picked from inventory and is ready for shipment. This status update is crucial for maintaining transparency with customers and ensuring timely delivery. In data processing, "item processed" can refer to the successful execution of a data entry task or the completion of a computational operation on a dataset. Here, it ensures that each piece of information has been accurately captured and validated, which is vital for maintaining data integrity and reliability. In manufacturing, this term might denote that a raw material or semi-finished product has undergone a specific stage of production. For example, if an item is processed through quality control checks, it means that the item has been inspected for defects and meets the required standards before moving on to the next stage of production. The context in which "item processed" is used also influences its implications. For instance, in customer service, this term could indicate that a customer's request or complaint has been addressed and resolved. This provides assurance to the customer that their issue is being actively managed. Overall, understanding what "item processed" means involves recognizing the specific task or operation being referred to and the stage at which it occurs within a broader process. By doing so, organizations can streamline their operations, enhance efficiency, and improve communication both internally and with external stakeholders. This clarity is essential for maintaining high standards of quality, reliability, and customer satisfaction across various industries.
Industry-Specific Applications
Understanding the concept of "item processed" is crucial across various industries, each with its unique applications and challenges. In **manufacturing**, for instance, an item processed could refer to a product that has undergone a specific stage in the production line, such as assembly, quality control, or packaging. Here, tracking each item processed helps in managing inventory, optimizing production workflows, and ensuring compliance with quality standards. For example, in automotive manufacturing, every car part that is inspected and cleared for assembly is considered an item processed, enabling the manufacturer to maintain high-quality output and meet regulatory requirements. In **healthcare**, the term takes on a different meaning. An item processed might be a patient's medical record that has been updated, a lab test result that has been analyzed, or a medication order that has been fulfilled. This tracking is vital for patient care coordination, billing purposes, and maintaining accurate medical histories. For instance, when a patient undergoes a diagnostic test, the lab results are processed and recorded in their medical file, ensuring that healthcare providers have up-to-date information for making informed decisions. In **e-commerce**, an item processed typically refers to an order that has been received, processed, and shipped. This includes activities such as order verification, payment processing, inventory management, and logistics coordination. For example, when a customer places an order online, the e-commerce platform processes the order by checking inventory availability, processing payment, and scheduling shipment. Each step in this process ensures that the customer receives their purchase efficiently and reliably. In **financial services**, items processed can include transactions such as deposits, withdrawals, or loan applications. Banks and financial institutions process these items to manage accounts accurately, prevent fraud, and comply with financial regulations. For instance, when a customer deposits a check into their account, the bank processes the transaction by verifying the check details, updating the account balance, and clearing the funds through the banking system. Across these industries and others like **logistics** and **education**, understanding what constitutes an "item processed" is essential for operational efficiency, compliance, and customer satisfaction. It allows organizations to streamline their processes, reduce errors, and enhance overall performance. By accurately tracking each item processed, businesses can make data-driven decisions, improve service delivery, and maintain high standards of quality and reliability. This concept is a cornerstone of modern business operations, enabling organizations to operate effectively in an increasingly complex and interconnected world.
Common Misconceptions
When delving into the concept of "item processed," it is crucial to address and dispel common misconceptions that often cloud understanding. One prevalent misconception is that "item processed" refers solely to the completion of an entire task or project. However, this term is more nuanced and specifically pertains to the status of individual items within a larger process. For instance, in a manufacturing context, "item processed" might indicate that a particular unit has been through a specific stage of production, such as assembly or quality control, but not necessarily that the entire production cycle is complete. Another misconception arises from the assumption that "item processed" implies immediate availability or readiness for use. In reality, an item may be processed but still require additional steps before it is deemed ready for distribution or consumption. For example, in logistics, an item might be processed at a warehouse but still need to be packaged and shipped before reaching its final destination. Moreover, there is a common misunderstanding that "item processed" is synonymous with "item completed." While these terms are related, they are not interchangeable. An item can be processed without being fully completed if it has undergone only part of the required procedures. This distinction is particularly important in fields like software development where an item might be processed through various stages of testing and debugging but still require final validation before being considered complete. Additionally, some individuals mistakenly believe that "item processed" is a static state, whereas it is often part of a dynamic workflow. Items can move through multiple stages of processing, each stage updating their status until they reach their final form. Understanding these misconceptions is vital for effective communication and efficient workflow management. By recognizing that "item processed" refers to a specific point in the lifecycle of an item rather than its overall completion, teams can better track progress, identify bottlenecks, and ensure that all necessary steps are taken to bring an item to its final state. This clarity also helps in setting realistic expectations and timelines, thereby enhancing productivity and reducing errors. In summary, clarifying these misconceptions about "item processed" fosters a deeper understanding of the concept and its practical applications across various industries.
The Process Behind Item Processing
In the intricate world of logistics and supply chain management, the process behind item processing is a critical yet often overlooked aspect that ensures the smooth operation of businesses. This complex sequence involves multiple steps, stakeholders, and technological tools, all working in harmony to transform raw items into usable products. To fully grasp the concept of "Item Processed," it is essential to delve into the step-by-step breakdown of this process, understanding each phase from receipt to delivery. Additionally, identifying the key stakeholders involved—ranging from warehouse staff to quality control specialists—provides insight into the human element that drives efficiency. Finally, exploring the technological tools and systems that facilitate item processing, such as inventory management software and automated sorting machines, highlights the innovative solutions that streamline operations. By examining these three pivotal components, we can gain a comprehensive understanding of what it means for an item to be processed, and how this process underpins the success of modern commerce. Understanding the concept of "Item Processed" requires a holistic view of these interconnected elements, which will be explored in detail throughout this article.
Step-by-Step Breakdown
### Step-by-Step Breakdown Understanding the process behind item processing involves a meticulous step-by-step breakdown, ensuring each stage is executed with precision and efficiency. Here’s a detailed look at how items are processed from inception to completion: 1. **Receipt and Inspection**: The journey begins with the receipt of items, whether they are goods, documents, or any other form of material. Upon arrival, these items undergo a thorough inspection to verify their condition, quantity, and compliance with specifications. This initial check helps identify any discrepancies or defects early on. 2. **Sorting and Categorization**: Once inspected, items are sorted and categorized based on their type, destination, or other relevant criteria. This step is crucial for streamlining the subsequent processes and ensuring that each item reaches its intended recipient or storage location efficiently. 3. **Data Entry and Tracking**: Each item is then logged into a database or tracking system. This involves capturing detailed information such as item description, serial numbers, batch numbers, and any other pertinent details. This data entry process enables real-time tracking and monitoring of the items throughout their lifecycle. 4. **Storage and Inventory Management**: After data entry, items are stored in designated areas according to their categorization. Effective inventory management systems are implemented to keep track of stock levels, locations, and movement history. This ensures that items can be quickly located when needed and that inventory levels are always up-to-date. 5. **Processing and Handling**: Depending on the nature of the items, they may undergo various processing steps such as cleaning, packaging, labeling, or assembly. These tasks are performed by trained personnel using specialized equipment to maintain quality standards. 6. **Quality Control Checks**: Before items are dispatched or made available for use, they undergo rigorous quality control checks. These checks involve testing for functionality, inspecting for defects, and ensuring compliance with regulatory standards. 7. **Shipping and Distribution**: Once cleared by quality control, items are prepared for shipping or distribution. This involves packaging them appropriately, labeling them correctly, and arranging for transportation to their final destinations. 8. **Delivery and Receipt Confirmation**: The final step involves delivering the items to their intended recipients. Upon delivery, recipients confirm receipt of the items, which updates the tracking system and completes the processing cycle. By following this step-by-step breakdown, organizations can ensure that item processing is carried out systematically, reducing errors and enhancing overall efficiency. Each stage is interdependent, contributing to a seamless and reliable process that supports smooth operations across various industries. This meticulous approach not only improves productivity but also enhances customer satisfaction by delivering high-quality items in a timely manner.
Key Stakeholders Involved
In the intricate process of item processing, several key stakeholders play crucial roles to ensure efficiency, accuracy, and compliance. At the forefront are **Operations Managers**, who oversee the entire workflow, from receiving items to their final disposition. These managers coordinate with various teams to optimize processes, manage inventory levels, and implement quality control measures. **Inventory Specialists** are another vital group; they are responsible for tracking and maintaining accurate records of items as they move through different stages of processing. Their meticulous attention to detail helps in preventing stock discrepancies and ensures that items are properly accounted for. **Quality Control Inspectors** are essential stakeholders who verify the condition and authenticity of items. They conduct thorough inspections to identify any defects or irregularities, ensuring that only high-quality items proceed to the next stages of processing. This step is critical in maintaining customer satisfaction and upholding brand standards. **Logistics Coordinators** handle the transportation and storage aspects, arranging for the safe and timely movement of items between facilities or to customers. Their expertise in supply chain management helps in minimizing delays and reducing costs. **IT and Data Analysts** also play a significant role by developing and maintaining the software systems that support item processing. They ensure that data is accurately captured, processed, and reported, providing valuable insights that help in decision-making. **Customer Service Representatives** are often the face of the organization, interacting directly with customers to address queries, resolve issues, and provide updates on item status. Their ability to communicate effectively enhances customer experience and builds trust. Additionally, **Regulatory Compliance Officers** ensure that all processes adhere to relevant laws and regulations. They monitor changes in legislation and industry standards, implementing necessary adjustments to maintain compliance. This is particularly important in industries such as healthcare or finance, where strict regulations govern item processing. **Suppliers and Vendors** are external stakeholders who provide the raw materials or finished goods that undergo processing. Building strong relationships with these partners is crucial for securing reliable supply chains and maintaining consistent quality. Lastly, **End Users or Customers** are the ultimate stakeholders whose needs drive the entire process. Understanding their expectations and preferences helps in tailoring item processing to meet their demands efficiently. By engaging with these diverse stakeholders, organizations can streamline their item processing operations, enhance productivity, and deliver superior value to their customers. Each stakeholder brings unique expertise and perspectives that collectively contribute to a seamless and effective item processing system.
Technological Tools and Systems
In the realm of item processing, technological tools and systems play a pivotal role in enhancing efficiency, accuracy, and speed. At the heart of this process lies a sophisticated array of technologies designed to streamline every stage from receipt to delivery. **Barcode Scanning and RFID Technology** are fundamental components, allowing for quick identification and tracking of items. These tools enable real-time monitoring, reducing errors and ensuring that each item is correctly categorized and routed through the system. **Automated Sorting Systems**, powered by advanced algorithms and machine learning, further optimize the sorting process by rapidly categorizing items based on predefined criteria such as size, weight, and destination. **Inventory Management Software** is another crucial element, providing a centralized platform for tracking stock levels, managing orders, and predicting demand. This software integrates seamlessly with other systems to ensure that inventory is always up-to-date and that supply chains are optimized. **Robotic Process Automation (RPA)** has also become increasingly prevalent, automating repetitive tasks such as data entry and order processing, thereby freeing human resources for more complex and value-added activities. Moreover, **Internet of Things (IoT) Devices** contribute significantly by providing real-time data on item conditions during transit. Sensors embedded in packaging can monitor temperature, humidity, and other environmental factors, ensuring that perishable items are handled appropriately. **Artificial Intelligence (AI) and Machine Learning (ML)** technologies are being leveraged to predict potential bottlenecks in the processing pipeline and to optimize workflows dynamically. These intelligent systems analyze historical data to identify patterns and make informed decisions that improve overall efficiency. Additionally, **Cloud Computing** platforms support the scalability and flexibility needed for item processing operations. By hosting data and applications in the cloud, businesses can easily scale their operations to meet fluctuating demand without significant capital expenditures. **Blockchain Technology** is also being explored for its potential to enhance transparency and security in supply chains by creating immutable records of transactions. In summary, the integration of these technological tools and systems transforms the item processing landscape by introducing unprecedented levels of automation, precision, and transparency. By leveraging these technologies, businesses can significantly reduce processing times, minimize errors, and enhance customer satisfaction—ultimately driving operational excellence and competitive advantage in a rapidly evolving market.
Implications and Benefits of Item Processing
In today's fast-paced and highly competitive business environment, the efficient processing of items is crucial for maintaining operational excellence. Item processing, a cornerstone of various industries including manufacturing, logistics, and retail, encompasses a range of activities from receiving and inspecting goods to packaging and shipping. This intricate process has far-reaching implications that significantly impact an organization's overall performance. By delving into the efficiency and productivity gains that item processing offers, we can understand how streamlined operations lead to reduced costs and enhanced output. Additionally, the role of quality control and assurance in item processing ensures that products meet stringent standards, safeguarding brand reputation and customer trust. Ultimately, these aspects collectively contribute to heightened customer satisfaction and experience, as timely and accurate delivery of high-quality items fosters loyalty and drives business growth. Understanding the concept of "item processed" is essential for grasping these multifaceted benefits, and this article will explore these critical dimensions in detail.
Efficiency and Productivity Gains
Efficiency and productivity gains are pivotal implications of item processing, significantly enhancing operational performance across various industries. By streamlining the handling, tracking, and management of items, businesses can achieve substantial reductions in processing time and costs. Automated item processing systems, for instance, leverage advanced technologies such as barcode scanning, RFID tags, and machine learning algorithms to expedite tasks that were previously manual and time-consuming. This automation not only minimizes human error but also frees up personnel to focus on higher-value activities, thereby boosting overall productivity. Moreover, item processing facilitates better inventory management. Real-time tracking and updates enable companies to maintain accurate stock levels, reduce stockouts and overstocking, and optimize storage space. This precision in inventory control leads to improved supply chain efficiency, allowing for quicker response times to customer demands and more effective resource allocation. Additionally, advanced analytics derived from item processing data provide valuable insights into consumption patterns, helping businesses make informed decisions about production planning, procurement strategies, and demand forecasting. The benefits extend beyond operational efficiency to include enhanced customer satisfaction. With faster and more accurate item processing, orders are fulfilled promptly, reducing lead times and improving delivery reliability. This translates into higher customer satisfaction rates, as clients receive their products in a timely manner without errors. Furthermore, the data collected through item processing can be used to personalize customer experiences by offering tailored recommendations based on purchase history and preferences. From a financial perspective, the efficiency and productivity gains from item processing can lead to significant cost savings. Reduced labor costs, lower inventory holding costs, and minimized waste due to improved tracking all contribute to a healthier bottom line. Moreover, by optimizing processes and reducing errors, businesses can avoid costly rework and returns, further enhancing profitability. In summary, the implications of item processing are far-reaching and multifaceted. By enhancing efficiency and productivity through automation, better inventory management, improved customer satisfaction, and financial savings, businesses can achieve a competitive edge in their respective markets. As technology continues to evolve, the potential for even greater gains in these areas is substantial, making item processing an indispensable component of modern business operations.
Quality Control and Assurance
Quality Control and Assurance are pivotal components in the item processing cycle, ensuring that products meet stringent standards and customer expectations. Quality Control (QC) involves the systematic monitoring and evaluation of processes to detect and correct defects or deviations from specifications. This is typically achieved through rigorous testing, inspection, and validation at various stages of production. For instance, in manufacturing, QC might include checking raw materials, monitoring production lines for consistency, and conducting final product inspections to identify any defects or irregularities. On the other hand, Quality Assurance (QA) is a broader concept that encompasses all activities designed to ensure that the processes used to design, develop, and deliver products are effective and reliable. QA focuses on preventing defects rather than detecting them after they occur. This includes establishing clear quality policies, training personnel, implementing robust quality management systems (such as ISO 9001), and continuously improving processes through feedback loops and data analysis. The implications of robust Quality Control and Assurance are multifaceted. Firstly, they significantly enhance customer satisfaction by ensuring that products are reliable, durable, and meet their intended use. This builds trust and loyalty, leading to repeat business and positive word-of-mouth. Secondly, effective QC and QA reduce the likelihood of product recalls, legal liabilities, and financial losses associated with defective products. By identifying and addressing issues early in the production process, companies can avoid costly rework or scrap materials. Additionally, a strong focus on quality can lead to operational efficiencies as streamlined processes reduce waste and improve productivity. From a competitive standpoint, organizations that prioritize quality gain a market advantage by differentiating themselves from competitors who may not adhere to such high standards. The benefits extend beyond immediate operational gains; they also contribute to long-term sustainability. Companies that invest in QA and QC are more likely to innovate and improve their products continuously, staying ahead of market trends and consumer demands. Moreover, a culture of quality fosters employee engagement and morale as workers take pride in producing high-quality products. This can lead to lower turnover rates and higher job satisfaction. In summary, integrating Quality Control and Assurance into item processing is essential for delivering superior products that meet customer needs while driving business success through enhanced reputation, operational efficiency, and innovation. By embedding these practices deeply within their operations, organizations can ensure consistent excellence across all stages of production, ultimately leading to sustained growth and market leadership.
Customer Satisfaction and Experience
Customer satisfaction and experience are pivotal components in the broader context of item processing, as they directly influence the perceived value and loyalty of customers. When items are processed efficiently, it translates into faster delivery times, accurate order fulfillment, and reduced errors. This seamless execution enhances customer satisfaction by meeting or exceeding their expectations. For instance, in e-commerce, timely and accurate order processing ensures that customers receive their products quickly and in the correct condition, fostering trust and encouraging repeat business. Moreover, a well-optimized item processing system allows businesses to gather valuable feedback and insights from customer interactions. By analyzing these data points, companies can identify areas for improvement and implement changes that further enhance the customer experience. For example, if a pattern of delays or errors is detected during the processing stage, corrective measures can be taken to streamline operations and improve overall service quality. The implications of this are multifaceted. Firstly, satisfied customers are more likely to become brand advocates, sharing positive experiences with others through reviews and word-of-mouth recommendations. This organic marketing can significantly boost a company's reputation and attract new customers. Secondly, improved customer satisfaction leads to higher retention rates, reducing the costs associated with acquiring new customers and increasing long-term revenue. From a benefits perspective, efficient item processing also enables businesses to scale more effectively. As demand increases, a robust processing system ensures that operations can expand without compromising on quality or speed. This scalability is crucial for maintaining high levels of customer satisfaction even during peak periods or times of rapid growth. In addition, advanced item processing technologies such as automation and AI can provide real-time updates and tracking information to customers, enhancing transparency and reducing anxiety related to order status. This proactive communication builds trust and reinforces the notion that the company values its customers' time and satisfaction. In conclusion, the implications and benefits of item processing are deeply intertwined with customer satisfaction and experience. By ensuring that items are processed efficiently, accurately, and transparently, businesses can significantly enhance their customers' overall experience. This not only leads to higher satisfaction levels but also fosters loyalty, drives positive word-of-mouth, and supports sustainable business growth. As such, investing in robust item processing systems is essential for any organization aiming to deliver exceptional customer experiences in today's competitive market landscape.