What Is Instrumentation

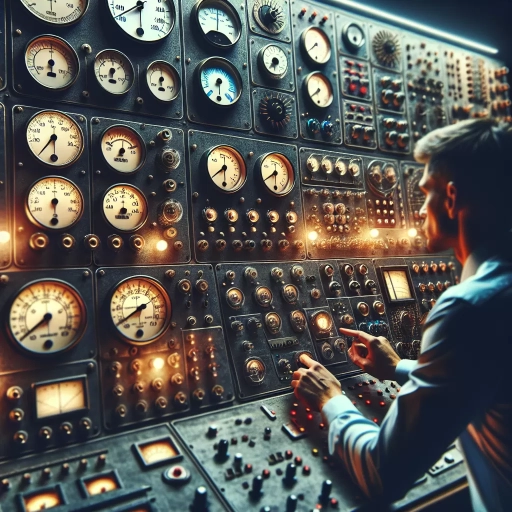
Instrumentation is a cornerstone of modern technology, playing a pivotal role in various industries such as healthcare, manufacturing, and environmental monitoring. At its core, instrumentation involves the use of devices and systems to measure, control, and analyze physical parameters. This field has evolved significantly over the years, offering a wide range of applications that cater to diverse needs. In this article, we will delve into the world of instrumentation, starting with an **Introduction to Instrumentation**, where we will explore the fundamental principles and historical development of this critical discipline. We will then examine the **Types and Applications of Instrumentation**, highlighting how different types of instruments are utilized across various sectors. Finally, we will discuss **Modern Trends and Future Directions in Instrumentation**, shedding light on the latest advancements and potential future developments that are set to shape the landscape of this field. By understanding these aspects, readers will gain a comprehensive insight into the significance and evolving nature of instrumentation. Let us begin our journey with an **Introduction to Instrumentation**.
Introduction to Instrumentation
Instrumentation is a fundamental aspect of modern technology, playing a crucial role in various industries by enabling precise measurement, control, and automation. This article provides a comprehensive introduction to instrumentation, delving into its definition and scope, historical development, and importance across different sectors. To begin, it is essential to understand the **Definition and Scope of Instrumentation**, which encompasses the principles, devices, and systems used to measure and control physical parameters such as temperature, pressure, flow rate, and more. This foundational knowledge sets the stage for exploring how instrumentation has evolved over time. The **Historical Development of Instrumentation** highlights key milestones and innovations that have transformed the field from simple mechanical devices to sophisticated digital systems. Finally, the **Importance in Various Industries** underscores how instrumentation impacts fields like manufacturing, healthcare, aerospace, and energy by ensuring safety, efficiency, and accuracy. By grasping these core concepts, readers will gain a deeper appreciation for the significance of instrumentation in today's technological landscape. Let us start by examining the **Definition and Scope of Instrumentation** to lay the groundwork for this exploration.
Definition and Scope of Instrumentation
Instrumentation, a cornerstone of modern technology, is the science and practice of measuring, controlling, and transmitting variables within a system. At its core, instrumentation involves the use of instruments to monitor and regulate physical parameters such as temperature, pressure, flow rate, and level. The definition of instrumentation encompasses not only the hardware components like sensors, transducers, and actuators but also the software and algorithms that interpret and act upon the data collected. The scope of instrumentation is vast and multifaceted, extending across various industries including manufacturing, healthcare, aerospace, and energy. In industrial settings, instrumentation plays a critical role in process control, ensuring that production processes operate within specified limits to maintain quality and safety standards. For instance, in chemical plants, instrumentation systems monitor and control variables like pH levels, temperature, and pressure to prevent accidents and optimize production efficiency. In healthcare, medical instrumentation is essential for diagnosing diseases and monitoring patient health. Devices such as electrocardiograms (ECGs), blood glucose meters, and ultrasound machines rely on sophisticated instrumentation to provide accurate readings that aid in medical decision-making. The precision and reliability of these instruments are crucial for patient care and treatment outcomes. Aerospace engineering also heavily relies on advanced instrumentation for navigation, communication, and system monitoring. Aircraft and spacecraft are equipped with complex systems that measure parameters such as altitude, velocity, and engine performance in real-time, ensuring safe and efficient operation. Furthermore, the energy sector benefits significantly from instrumentation in power generation and distribution. Smart grids utilize advanced instrumentation to monitor energy consumption patterns, detect anomalies, and optimize energy distribution networks. This not only improves efficiency but also enhances the reliability of power supply systems. The technological advancements in fields like IoT (Internet of Things) and AI (Artificial Intelligence) have further expanded the scope of instrumentation. Modern instruments are increasingly interconnected, allowing for real-time data analysis and automated decision-making processes. This integration enables more precise control over complex systems and enhances predictive maintenance capabilities. In summary, the definition and scope of instrumentation are broad and dynamic, reflecting its integral role across diverse sectors. From ensuring industrial safety to advancing medical diagnostics and optimizing energy distribution, instrumentation is a vital component that underpins many aspects of modern life. Its continuous evolution with technological advancements promises even greater efficiencies and innovations in the future.
Historical Development of Instrumentation
The historical development of instrumentation is a rich and dynamic narrative that spans centuries, reflecting human ingenuity and the relentless pursuit of precision and accuracy. The journey begins with ancient civilizations, where simple yet effective tools were crafted to measure basic physical quantities such as length, weight, and time. The Babylonians, for instance, used the sexagesimal system to divide the circle into 360 degrees, laying the groundwork for modern angular measurements. In ancient Greece, philosophers like Archimedes developed sophisticated instruments like the odometer and the astrolabe, which were pivotal in navigation and astronomy. The Middle Ages saw significant advancements with the invention of mechanical clocks, which revolutionized timekeeping and introduced the concept of precision timing. The Renaissance period brought forth a flurry of innovative devices, including Galileo Galilei's thermoscope—a precursor to the thermometer—and the invention of the telescope by Hans Lippershey and Zacharias Janssen. These instruments not only expanded our understanding of the physical world but also laid the foundation for scientific inquiry. The Industrial Revolution marked a critical turning point in the history of instrumentation. The development of steam engines by James Watt necessitated precise measurements of pressure and temperature, leading to the creation of more sophisticated gauges and thermometers. The invention of the telegraph by Samuel Morse introduced electrical signaling, paving the way for modern electrical instrumentation. The late 19th and early 20th centuries witnessed the emergence of electronic instruments, such as the oscilloscope and the voltmeter, which were crucial in understanding and harnessing electrical phenomena. The 20th century saw an explosion in technological advancements, driven by World War II and the subsequent Cold War. Radar technology, developed during World War II, utilized complex instrumentation to detect and track objects at a distance. Post-war innovations included the development of computers, which transformed data acquisition and processing. The advent of microprocessors in the 1970s further miniaturized instrumentation, enabling real-time data analysis and control. Modern instrumentation now includes advanced sensors, digital signal processing, and software-driven systems that integrate seamlessly into various fields such as medicine, aerospace, and industrial automation. Today, instrumentation continues to evolve with advancements in nanotechnology, artificial intelligence, and the Internet of Things (IoT). High-precision instruments like atomic force microscopes and quantum sensors are pushing the boundaries of measurement science. The integration of AI algorithms with instrumentation has enhanced data interpretation and predictive analytics, while IoT connectivity has enabled remote monitoring and real-time feedback loops. This ongoing evolution underscores the critical role that instrumentation plays in driving scientific discovery, technological innovation, and industrial progress. As we move forward, it is clear that the historical development of instrumentation will continue to shape our future, enabling us to measure, analyze, and understand the world around us with ever greater precision and accuracy.
Importance in Various Industries
Instrumentation plays a pivotal role across various industries, driving efficiency, safety, and innovation. In the **energy sector**, instrumentation is crucial for monitoring and controlling power generation, transmission, and distribution. Advanced sensors and control systems ensure optimal performance of power plants, reduce energy losses, and enhance grid stability. For instance, in nuclear power plants, precise instrumentation is essential for maintaining safe operating conditions and preventing accidents. In **manufacturing**, instrumentation is vital for process control and quality assurance. Sensors and actuators enable real-time monitoring of production lines, allowing for immediate adjustments to maintain product quality and reduce waste. This not only improves productivity but also ensures compliance with regulatory standards. Additionally, predictive maintenance facilitated by instrumentation helps in preventing equipment failures, thereby minimizing downtime. The **healthcare industry** heavily relies on instrumentation for diagnostic and therapeutic purposes. Medical devices such as ECGs, MRI machines, and ventilators are sophisticated instruments that provide critical data for patient care. These devices help in early diagnosis, accurate treatment planning, and continuous patient monitoring, significantly improving healthcare outcomes. In **aerospace and defense**, instrumentation is indispensable for the development, testing, and operation of aircraft and spacecraft. Advanced sensors and data acquisition systems are used to monitor flight dynamics, engine performance, and environmental conditions. This data is crucial for ensuring safety during flight operations and for conducting thorough post-flight analyses to improve future missions. The **chemical industry** also benefits significantly from instrumentation. Process control instruments monitor chemical reactions, temperatures, pressures, and flow rates to ensure safe and efficient production processes. This helps in maintaining product quality, reducing the risk of accidents, and complying with environmental regulations. Furthermore, in **agriculture**, precision farming techniques rely heavily on instrumentation. Sensors and drones equipped with GPS and other technologies help farmers monitor soil moisture levels, crop health, and weather conditions. This data enables farmers to make informed decisions about irrigation, fertilization, and pest control, leading to higher yields and more sustainable farming practices. In **environmental monitoring**, instrumentation is used to track air and water quality, detect pollutants, and monitor climate changes. Advanced sensors can detect even trace amounts of harmful substances, providing valuable data for policy makers to implement effective environmental protection measures. Overall, instrumentation is a cornerstone in modern industries, enhancing performance, safety, and sustainability. Its applications span from ensuring the reliability of critical infrastructure to improving the quality of life through better healthcare and environmental stewardship. As technology continues to evolve, the importance of instrumentation will only grow, driving further innovation and efficiency across diverse sectors.
Types and Applications of Instrumentation
Instrumentation plays a pivotal role in various industries, including manufacturing, healthcare, and environmental monitoring, by providing precise and reliable data. The types and applications of instrumentation are diverse and can be broadly categorized into three key areas: Measurement Instruments, Control Instruments, and Specialized Instruments. Measurement Instruments, such as sensors and transducers, are crucial for converting physical parameters into measurable signals. These instruments are the foundation of data collection and are used in a wide range of applications from industrial process control to medical diagnostics. Control Instruments, including regulators and actuators, are essential for maintaining and adjusting system parameters to desired levels. They ensure that processes operate within specified limits, enhancing efficiency and safety. Specialized Instruments, such as analytical and diagnostic tools, offer advanced capabilities for detailed analysis and diagnosis in fields like chemistry, biology, and medicine. Understanding these different types of instrumentation is vital for optimizing performance, ensuring accuracy, and driving innovation across various sectors. By delving into each category, we can appreciate the complexity and importance of instrumentation in modern technology. Let's begin by exploring the fundamental role of Measurement Instruments: Sensors and Transducers.
Measurement Instruments: Sensors and Transducers
Measurement instruments, particularly sensors and transducers, form the backbone of modern instrumentation, enabling the precise and reliable conversion of physical parameters into measurable signals. **Sensors** are specialized devices designed to detect changes in their environment, such as temperature, pressure, light, or motion. These devices convert the detected physical quantity into an electrical signal that can be processed and analyzed. For instance, thermocouples and thermistors are types of temperature sensors that measure heat levels by generating a voltage or resistance change proportional to the temperature variation. Similarly, photodiodes and phototransistors serve as light sensors, converting light intensity into electrical currents. **Transducers**, on the other hand, are more versatile and can convert energy from one form to another. They are crucial in instrumentation as they facilitate the transformation of non-electrical signals into electrical signals that can be easily measured and processed. Examples include piezoelectric transducers that convert mechanical stress into electrical charges, and strain gauges that measure deformation by altering their electrical resistance in response to mechanical strain. The versatility of transducers allows them to be used in a wide range of applications, from industrial automation to medical diagnostics. The applications of these measurement instruments are diverse and pervasive. In industrial settings, sensors and transducers are used for process control, monitoring parameters such as pressure, flow rate, and temperature to ensure optimal operation and safety. In healthcare, biosensors and medical transducers play critical roles in diagnosing diseases and monitoring patient health; for example, electrocardiogram (ECG) machines use transducers to convert heart muscle activity into electrical signals that are then displayed on a monitor. Additionally, in automotive systems, various sensors like oxygen sensors and pressure sensors help in engine management and safety features such as airbag deployment. The accuracy and reliability of these measurement instruments are paramount. Advances in technology have led to the development of more sophisticated sensors and transducers with higher precision and durability. For instance, MEMS (Micro-Electro-Mechanical Systems) technology has enabled the creation of miniaturized sensors that offer improved performance and reduced power consumption. Furthermore, advancements in materials science have introduced new types of sensors and transducers with enhanced sensitivity and stability. In conclusion, sensors and transducers are fundamental components of instrumentation systems, enabling the accurate measurement and conversion of physical parameters into usable data. Their widespread applications across various industries underscore their importance in modern technology. As technology continues to evolve, we can expect even more innovative and efficient measurement instruments that will further enhance our ability to monitor and control complex systems with precision and reliability.
Control Instruments: Regulators and Actuators
Control instruments, specifically regulators and actuators, play a crucial role in the realm of instrumentation by ensuring precise control and regulation of various processes across different industries. **Regulators** are devices designed to maintain a consistent level of a particular parameter, such as pressure, temperature, or flow rate, within a system. These instruments are essential for maintaining stability and efficiency in industrial processes. For instance, pressure regulators are used in gas supply systems to ensure that the pressure remains within safe and operational limits, preventing over-pressurization which could lead to equipment failure or safety hazards. Similarly, temperature regulators are vital in chemical processing and HVAC systems to maintain optimal operating conditions. **Actuators**, on the other hand, are the components that convert the control signal from a controller into physical action. They are the "muscles" of the control system, executing the commands to adjust valves, pumps, or other devices to achieve the desired state. Actuators can be powered by various sources including electricity, pneumatics, or hydraulics. In industrial automation, electric actuators are commonly used for precise control over valves and dampers, while pneumatic actuators are preferred in applications where high force is required but space is limited. Hydraulic actuators offer even greater force capabilities and are often used in heavy-duty applications such as oil and gas extraction. The types and applications of these control instruments are diverse and widespread. For example, in the oil and gas industry, regulators and actuators work together to manage the flow of fluids through pipelines, ensuring that pressures and flow rates are maintained within safe limits. In the pharmaceutical industry, these instruments are critical for maintaining sterile conditions and precise temperature control during manufacturing processes. In HVAC systems, regulators and actuators help in maintaining optimal indoor air quality and temperature by controlling airflow and heating/cooling elements. The integration of advanced technologies such as smart sensors and IoT capabilities has further enhanced the functionality of regulators and actuators. These advancements allow for real-time monitoring and remote control, enabling more efficient and responsive process management. Additionally, the use of materials like stainless steel and corrosion-resistant coatings has improved the durability and reliability of these instruments in harsh environments. In summary, regulators and actuators are indispensable components of modern instrumentation systems. Their ability to maintain precise control over various parameters ensures operational efficiency, safety, and product quality across a wide range of industries. As technology continues to evolve, these control instruments will remain at the forefront of industrial automation and process control, driving innovation and excellence in manufacturing and operations.
Specialized Instruments: Analytical and Diagnostic Tools
Specialized instruments, particularly analytical and diagnostic tools, play a pivotal role in various scientific, medical, and industrial fields. These instruments are designed to provide precise and detailed information about the composition, structure, and properties of substances or systems. In the realm of analytical instrumentation, tools such as mass spectrometers, nuclear magnetic resonance (NMR) spectrometers, and gas chromatographs are indispensable. Mass spectrometers, for instance, analyze the mass-to-charge ratio of ions to identify and quantify chemical compounds, while NMR spectrometers use magnetic fields and radio waves to determine the structure of organic molecules. Gas chromatographs separate and analyze volatile compounds based on their boiling points and affinity for a stationary phase. Diagnostic instruments, on the other hand, are crucial in healthcare for diagnosing diseases and monitoring patient health. Imaging technologies like MRI (Magnetic Resonance Imaging) and CT (Computed Tomography) scans provide detailed images of internal body structures, enabling doctors to diagnose conditions such as tumors, fractures, and vascular diseases. Other diagnostic tools include ultrasound machines, which use high-frequency sound waves to create images of internal organs, and electroencephalographs (EEGs), which measure electrical activity in the brain to diagnose neurological disorders. In industrial settings, specialized instruments ensure quality control and process optimization. For example, spectrophotometers measure the interaction between light and matter to analyze the concentration of substances in solutions, while particle size analyzers determine the size distribution of particles in suspensions or powders. These instruments are essential for maintaining product consistency and adhering to regulatory standards. The applications of these specialized instruments are diverse and far-reaching. In environmental science, they help monitor air and water quality by detecting pollutants and contaminants. In pharmaceutical research, they facilitate drug development by analyzing the chemical composition and efficacy of new compounds. In forensic science, they aid in crime scene investigation by analyzing evidence such as DNA samples and chemical residues. The precision and reliability of these instruments are critical for making informed decisions across various disciplines. Continuous advancements in technology have led to more sophisticated and user-friendly versions of these tools, enhancing their accuracy and efficiency. For instance, the integration of artificial intelligence and machine learning algorithms into analytical instruments has improved data interpretation and reduced human error. In conclusion, specialized analytical and diagnostic instruments are vital components of modern scientific inquiry and industrial practice. Their ability to provide detailed insights into complex systems and substances underpins many of the advancements we see today in fields ranging from medicine to environmental science. As technology continues to evolve, these instruments will remain at the forefront of innovation, driving progress and improving outcomes in numerous sectors.
Modern Trends and Future Directions in Instrumentation
The landscape of instrumentation is undergoing a significant transformation, driven by several key trends that are shaping its future. Modern trends in instrumentation are characterized by advancements in digital and smart instrumentation, which are revolutionizing the way we measure, monitor, and control various processes. These advancements are not isolated; they are deeply intertwined with the integration of IoT (Internet of Things) and AI (Artificial Intelligence) technologies, enabling real-time data analysis and predictive maintenance. Additionally, there is a growing emphasis on sustainability and environmental impact considerations, as industries strive to reduce their ecological footprint while maintaining operational efficiency. As we delve into these trends, it becomes clear that the evolution of instrumentation is multifaceted and interconnected. Let us begin by exploring the foundational aspect of these changes: the advancements in digital and smart instrumentation, which form the backbone of this technological shift.
Advancements in Digital and Smart Instrumentation
Advancements in digital and smart instrumentation have revolutionized the field of measurement and control, transforming traditional analog systems into sophisticated, high-precision tools. At the heart of these advancements is the integration of advanced technologies such as microprocessors, communication protocols, and artificial intelligence. Digital instrumentation now offers unparalleled accuracy, reliability, and flexibility compared to its analog counterparts. For instance, digital multimeters and oscilloscopes can perform complex measurements with higher precision and speed, while also providing real-time data logging and analysis capabilities. Smart instrumentation takes this a step further by incorporating intelligent sensors and actuators that can self-calibrate, diagnose issues, and adapt to changing conditions. These devices are often equipped with wireless communication capabilities, enabling seamless integration into IoT (Internet of Things) networks. This allows for remote monitoring and control, enhancing operational efficiency and reducing downtime. Additionally, smart instruments can leverage machine learning algorithms to predict maintenance needs, detect anomalies, and optimize performance in real-time. The adoption of Industry 4.0 principles has further accelerated the development of smart instrumentation. Technologies like edge computing and cloud analytics enable the processing of vast amounts of data generated by these instruments, providing insights that were previously unattainable. This data-driven approach not only improves process control but also fosters a culture of continuous improvement and innovation. Moreover, advancements in materials science have led to the development of novel sensors that can operate in extreme environments, such as high-temperature or high-pressure conditions. These sensors are crucial for industries like aerospace, oil and gas, and power generation, where accurate measurements are critical for safety and efficiency. The future of digital and smart instrumentation looks promising with ongoing research in areas such as nanotechnology and quantum sensing. These emerging technologies hold the potential to create ultra-sensitive sensors capable of detecting minute changes in physical parameters, opening up new possibilities for fields like healthcare and environmental monitoring. In conclusion, the evolution of digital and smart instrumentation represents a significant leap forward in modern trends and future directions in instrumentation. By combining cutting-edge technologies with innovative design principles, these advancements are redefining the boundaries of measurement accuracy, operational efficiency, and data-driven decision-making across various industries. As technology continues to advance, we can expect even more sophisticated and intelligent instrumentation solutions that will drive further innovation and progress.
Integration with IoT and AI Technologies
The integration of IoT (Internet of Things) and AI (Artificial Intelligence) technologies represents a pivotal trend in modern instrumentation, revolutionizing the way data is collected, analyzed, and utilized. This synergy enables the creation of intelligent, interconnected systems that can autonomously monitor, predict, and respond to various environmental and operational conditions. In instrumentation, IoT devices equipped with sensors and actuators can gather vast amounts of data from diverse sources, such as temperature, pressure, vibration, and other physical parameters. This data is then transmitted to centralized platforms or edge devices where AI algorithms process it in real-time, extracting valuable insights and patterns that would be impossible for human analysts to discern. AI technologies, including machine learning and deep learning, play a crucial role in enhancing the capabilities of IoT systems. By applying predictive analytics, AI can forecast potential failures or anomalies in industrial equipment, allowing for proactive maintenance and reducing downtime. For instance, in industrial automation, AI-driven predictive maintenance can analyze sensor data from machinery to predict when a component is likely to fail, enabling scheduled maintenance before an actual failure occurs. This not only improves operational efficiency but also enhances safety by mitigating the risk of sudden equipment failures. Moreover, the integration of IoT and AI facilitates the development of smart instrumentation systems that can adapt to changing conditions. For example, in smart buildings, IoT sensors can monitor energy consumption, air quality, and other parameters, while AI algorithms optimize energy usage and indoor conditions in real-time. This dynamic optimization ensures a more comfortable and sustainable environment while reducing energy costs. The future directions of this integration are promising and multifaceted. As 5G networks become more widespread, they will provide the high-speed, low-latency connectivity necessary for real-time data transmission and processing, further enhancing the capabilities of IoT-AI systems. Additionally, advancements in edge computing will allow more complex AI models to be deployed closer to the data source, reducing latency and improving response times. In the realm of healthcare instrumentation, the combination of IoT and AI is transforming patient care. Wearable devices equipped with sensors can continuously monitor vital signs and other health metrics, sending this data to healthcare providers who can use AI to identify early warning signs of health issues. This proactive approach enables timely interventions and personalized care plans, significantly improving patient outcomes. In conclusion, the integration of IoT and AI technologies is a cornerstone of modern trends in instrumentation. By leveraging these technologies together, industries can achieve unprecedented levels of efficiency, safety, and innovation. As these technologies continue to evolve, we can expect even more sophisticated applications across various sectors, driving forward the future directions in instrumentation with unparalleled potential.
Sustainability and Environmental Impact Considerations
As we navigate the complexities of modern trends and future directions in instrumentation, it is imperative to integrate sustainability and environmental impact considerations into our technological advancements. Instrumentation, which encompasses the development and application of measuring instruments to monitor and control physical parameters, must now be designed with a holistic approach that balances innovation with environmental stewardship. The increasing awareness of climate change, resource depletion, and pollution has necessitated a shift towards sustainable practices across all sectors, including instrumentation. Sustainable instrumentation involves the use of eco-friendly materials, energy-efficient designs, and minimal waste generation during both the manufacturing process and the product's lifecycle. For instance, modern instruments are being developed with recyclable components and biodegradable packaging to reduce electronic waste. Additionally, advancements in sensor technology and IoT (Internet of Things) enable real-time monitoring and optimization of resource usage, thereby reducing energy consumption and emissions. The environmental impact of instrumentation extends beyond the physical product itself; it also includes the broader ecosystem it operates within. For example, in industrial settings, instruments can be designed to monitor and control processes that minimize water usage, reduce chemical emissions, and optimize energy consumption. In agricultural contexts, precision farming instruments equipped with sensors can help farmers adopt more sustainable practices by optimizing water and fertilizer application, thereby reducing runoff and pollution. Moreover, future directions in instrumentation are likely to be influenced by emerging technologies such as artificial intelligence (AI) and machine learning (ML). These technologies can enhance the predictive capabilities of instruments, allowing for proactive maintenance and reducing downtime, which in turn minimizes the need for frequent replacements and associated environmental impacts. AI-driven analytics can also help in identifying patterns that indicate potential environmental hazards, enabling timely interventions. Incorporating sustainability into instrumentation also involves considering the end-of-life phase of these devices. Manufacturers are increasingly adopting circular economy principles by designing instruments that are easy to disassemble, repair, and recycle. This not only reduces electronic waste but also conserves valuable resources by reusing components. In conclusion, as we move forward with modern trends and future directions in instrumentation, integrating sustainability and environmental impact considerations is no longer an option but a necessity. By leveraging cutting-edge technologies while adhering to sustainable practices, we can ensure that our advancements contribute positively to both technological progress and environmental well-being. This dual focus will be crucial in creating a resilient and sustainable future where innovation and nature coexist harmoniously.