What Is Toilet Paper Made Of

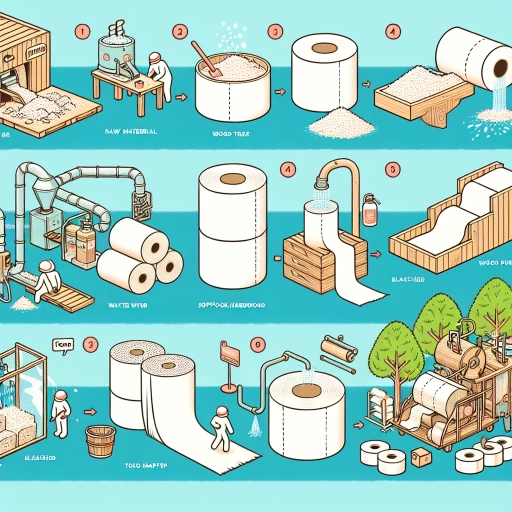
Raw Materials Used in Toilet Paper Production
The production of toilet paper, a staple in modern hygiene, relies on a variety of raw materials that contribute to its quality, sustainability, and functionality. At the heart of this process are three key components: wood pulp and cellulose, recycled fibers, and other natural fibers. Wood pulp and cellulose form the foundational material for most toilet paper products, providing the necessary strength and texture. Recycled fibers play a crucial role in reducing environmental impact by reusing post-consumer waste, thereby conserving natural resources. Additionally, other natural fibers such as bamboo and cotton offer alternative sustainable options that can enhance the product's eco-friendly profile. Understanding these raw materials is essential for appreciating the complexity and innovation involved in toilet paper production. By examining each of these components, we can gain insights into how they are sourced, processed, and integrated to create a product that meets both consumer needs and environmental standards. Let's begin by delving into the primary source of toilet paper: wood pulp and cellulose.
Wood Pulp and Cellulose
Wood pulp and cellulose are the primary raw materials in the production of toilet paper, playing a crucial role in its texture, strength, and overall quality. Wood pulp is derived from wood logs or recycled paper products, which are processed to break down the lignin and extract the cellulose fibers. This process involves mechanical or chemical pulping, where mechanical pulping retains more of the wood's natural lignin, resulting in a coarser texture, while chemical pulping removes most of the lignin, producing a finer and stronger fiber. Cellulose, the main component of wood pulp, is a polysaccharide that provides the structural framework for plant cell walls. In toilet paper production, cellulose fibers are refined and bleached to enhance their purity and whiteness. The refining process involves beating the fibers to make them more flexible and able to bond better when formed into a sheet. Bleaching, which can be done using various methods including chlorine dioxide or oxygen, not only whitens the pulp but also improves its strength and hygiene. The combination of wood pulp and cellulose allows for the creation of toilet paper with desired properties such as softness, absorbency, and durability. Softwood trees like spruce and pine are often used because their longer fibers contribute to greater strength and tear resistance in the final product. Hardwood trees like eucalyptus and birch can also be used, especially when blended with softwood fibers, to achieve a balance between softness and strength. In addition to these natural sources, recycled fibers from post-consumer waste are increasingly being incorporated into toilet paper production. This not only reduces the demand on virgin wood resources but also helps in conserving water and energy while minimizing waste. The use of recycled fibers can also result in a more sustainable product with lower environmental impact. The processing of wood pulp and cellulose into toilet paper involves several stages including forming, pressing, drying, and cutting. During the forming stage, the pulp is mixed with water and other additives such as fillers or wet strength agents before being spread onto a wire mesh screen. The water is drained off, leaving a thin layer of fibers that are then pressed to remove excess moisture and flatten the sheet. Drying involves passing the sheet through heated rollers to evaporate any remaining moisture before it is cut into individual sheets. In summary, wood pulp and cellulose are essential raw materials in toilet paper production due to their unique properties that contribute to the final product's quality. The careful selection and processing of these materials ensure that toilet paper meets consumer expectations for comfort, durability, and hygiene while also considering environmental sustainability through the use of recycled fibers and responsible forestry practices.
Recycled Fibers
Recycled fibers play a crucial role in the production of toilet paper, offering a sustainable and environmentally friendly alternative to virgin wood pulp. These fibers are derived from post-consumer waste, such as old newspapers, cardboard, and other paper products that have been collected, sorted, and processed. The recycling process involves several steps: collection, sorting, de-inking (to remove ink and other contaminants), pulping (to break down the fibers), and bleaching or de-coloring to achieve the desired whiteness and purity. Recycled fibers can significantly reduce the demand on natural resources, lower greenhouse gas emissions, and conserve water compared to traditional wood pulp production. Moreover, using recycled fibers helps in reducing landfill waste and supports a circular economy by reusing materials that would otherwise be discarded. In terms of quality, recycled fibers can produce toilet paper that is just as soft and durable as products made from virgin pulp. Many manufacturers now incorporate a blend of recycled and virgin fibers to balance sustainability with performance. This approach not only appeals to environmentally conscious consumers but also helps in maintaining consistent product quality. Additionally, some brands are pushing the boundaries by using 100% recycled content in their toilet paper products, further emphasizing the potential for sustainable practices in this industry. Overall, the integration of recycled fibers into toilet paper production is a key strategy for reducing environmental impact while meeting consumer demands for quality and sustainability.
Other Natural Fibers
In addition to wood pulp and cotton, other natural fibers play a significant role in the production of toilet paper, enhancing its quality, sustainability, and performance. One such fiber is bamboo, which has gained popularity due to its rapid growth rate and low environmental impact. Bamboo fibers are known for their softness, durability, and resistance to bacterial growth, making them an ideal alternative to traditional wood-based products. Another natural fiber is hemp, which boasts exceptional strength and absorbency. Hemp fibers are also biodegradable and require less water and pesticides compared to many other crops, contributing to a more sustainable production process. Sisal and jute fibers, derived from agave plants and jute plants respectively, are also used in some toilet paper products. These fibers offer good tensile strength and can be blended with other materials to improve the overall texture and durability of the final product. Flax fibers, commonly used in linen production, can also be incorporated into toilet paper for added strength and a softer feel. The use of these diverse natural fibers not only expands the raw material base but also helps in reducing the dependency on wood pulp, thereby supporting reforestation efforts and promoting biodiversity. Moreover, some manufacturers are exploring the use of agricultural by-products such as sugarcane bagasse and wheat straw. These residues would otherwise be discarded but can be converted into valuable cellulose fibers suitable for toilet paper production. This approach not only reduces waste but also provides an additional income stream for farmers, fostering a more circular economy. The integration of these various natural fibers into toilet paper production underscores the industry's commitment to sustainability and innovation, ensuring that consumers have access to high-quality, eco-friendly products that meet their needs without compromising the environment. By leveraging these diverse natural resources, manufacturers can create toilet paper that is not only effective but also environmentally responsible.
Manufacturing Process of Toilet Paper
The manufacturing process of toilet paper is a complex and multifaceted operation that involves several critical stages to produce a high-quality product. At its core, the process can be broken down into three key phases: Pulping and Screening, Forming and Pressing, and Drying and Cutting. Each of these stages plays a crucial role in transforming raw materials into the finished product that consumers rely on daily. Starting with Pulping and Screening, this initial phase involves breaking down wood chips or recycled fibers into a pulp, which is then filtered to remove impurities. This step is essential for creating a uniform consistency that will later contribute to the strength and softness of the toilet paper. Following the pulping process, the mixture is then subjected to Forming and Pressing, where it is molded into sheets and pressed to remove excess water. This stage is vital for achieving the desired texture and thickness of the final product. Finally, the sheets undergo Drying and Cutting, where they are dried to remove any remaining moisture and then cut into individual rolls. This final step ensures that the toilet paper is both durable and convenient for use. Understanding these three stages provides a comprehensive insight into how toilet paper is manufactured, highlighting the precision and care required at each step. Let's delve deeper into the first stage: Pulping and Screening.
Pulping and Screening
In the manufacturing process of toilet paper, pulping and screening are crucial steps that transform raw materials into the soft, absorbent sheets we use daily. **Pulping** involves breaking down wood chips or recycled fibers into a pulp, which is essentially a mixture of individual fibers suspended in water. This process can be mechanical or chemical. Mechanical pulping uses grinders to break down the wood, while chemical pulping employs solvents to dissolve lignin, the natural glue that holds wood fibers together. The choice between these methods depends on the desired quality and type of toilet paper being produced. For instance, chemical pulping yields a stronger and more durable product, often used for premium toilet paper brands. Following pulping, **screening** ensures that the pulp is free from contaminants and impurities. This step is vital for maintaining consistency and quality in the final product. The pulp is passed through a series of screens with varying mesh sizes to filter out dirt, bark, and other unwanted particles. Additionally, screening helps to remove any lumps or clumps that could affect the uniformity of the paper. This meticulous process ensures that only clean, individual fibers proceed to the next stages of production. The combination of pulping and screening sets the foundation for subsequent processes such as bleaching, refining, and forming. Bleaching may be applied to enhance brightness and hygiene, while refining involves beating the fibers to make them more pliable and flexible. These treated fibers are then formed into a sheet using a machine called a Fourdrinier, where water is drained through a wire mesh screen, leaving behind a thin layer of fibers. This sheet is then pressed, dried, and cut into rolls of toilet paper. The precision and care taken during pulping and screening are reflective of the overall attention to detail required in toilet paper production. These initial steps not only determine the strength and texture of the final product but also influence its environmental impact. For example, using recycled fibers in the pulping process can significantly reduce the demand on virgin wood resources and lower the carbon footprint of toilet paper production. In summary, pulping and screening are fundamental components of the toilet paper manufacturing process. They ensure that raw materials are transformed into high-quality fibers that meet consumer expectations for softness, strength, and cleanliness. As consumers become increasingly aware of environmental issues, these steps also play a critical role in sustainable practices within the industry. By understanding these processes, we gain a deeper appreciation for the complexity and care involved in producing something as seemingly simple as toilet paper.
Forming and Pressing
In the manufacturing process of toilet paper, the stages of forming and pressing are crucial for transforming raw materials into the final product. After the pulping process, where wood chips or recycled fibers are broken down into a pulp, the mixture is then formed into a sheet. This is achieved through a process known as wire drawing, where the pulp is poured onto a wire mesh screen and water is drained through the screen, leaving a thin layer of fibers. The fibers are then pressed together to form a uniform sheet. The forming stage involves several key steps. First, the pulp is mixed with various additives such as softeners, dyes, and strength enhancers to improve the quality and appearance of the toilet paper. This mixture is then spread evenly across the wire mesh screen, allowing excess water to drain off. The remaining fibers begin to bond together as they dry, creating a fragile sheet known as the "web." Following the forming stage, the web enters the pressing section of the manufacturing line. Here, it undergoes a series of rollers designed to remove excess moisture and flatten the sheet further. The first set of rollers, known as the "wet press," applies significant pressure to squeeze out more water from the web, reducing its thickness and increasing its density. Subsequent rollers continue this process, gradually increasing the pressure and heat to dry and smooth out the sheet. The pressing process also involves the application of heat through steam-heated rollers or hot air blowers. This heat helps to evaporate any remaining moisture, making the toilet paper more durable and less prone to tearing. Additionally, some manufacturers may use embossing rollers during this stage to create patterns or textures on the surface of the toilet paper, enhancing its softness and aesthetic appeal. Throughout these stages, quality control measures are implemented to ensure that the toilet paper meets the desired standards. Parameters such as thickness, strength, and softness are closely monitored to guarantee a consistent product. The final pressed sheet is then wound onto large rolls called "parent rolls," which are later cut into individual sheets or rolls of toilet paper ready for packaging and distribution. In summary, the forming and pressing stages in toilet paper manufacturing are pivotal in transforming raw pulp into a usable product. These processes involve careful manipulation of fibers, additives, and mechanical forces to produce a sheet that is both durable and comfortable for use. By understanding these steps, consumers can appreciate the complexity and precision involved in creating something as seemingly simple as toilet paper.
Drying and Cutting
In the manufacturing process of toilet paper, the stages of drying and cutting are crucial for transforming raw pulp into the final product. After the pulp has been formed into a sheet through the wire mesh screen, it undergoes a series of drying processes to remove excess moisture. The first step involves passing the wet sheet through a series of heated rollers, known as Yankee dryers, which use high temperatures to evaporate water content. This process not only dries the sheet but also presses it to achieve the desired thickness and smoothness. The heat from these dryers also helps in bonding the fibers together, enhancing the strength and durability of the toilet paper. Once dried, the sheet is then wound onto large rolls called parent rolls. These rolls can weigh up to several tons and are typically several feet in diameter. The next critical step is cutting, where these massive rolls are unwound and cut into smaller, manageable sheets. This is done using high-speed cutting machines that can precision-cut the sheets to exact dimensions. The cutting process involves both longitudinal and transverse cuts; longitudinal cuts divide the roll into narrower strips, while transverse cuts split these strips into individual sheets of toilet paper. To ensure uniformity and quality, manufacturers often use advanced cutting technologies such as laser cutting or precision shearing. These methods allow for precise control over sheet length and width, minimizing waste and ensuring consistent product quality. Additionally, some manufacturers may apply additional treatments during this stage, such as embossing or perforation, to enhance user experience and functionality. The final step in the cutting process involves packaging the individual sheets into rolls or multi-roll packs. This is typically done on automated packaging lines where the sheets are wound onto cardboard tubes and wrapped in plastic or paper covers. Quality control checks are performed throughout this stage to ensure that each roll meets the specified standards for softness, strength, and sheet count. In summary, the drying and cutting stages are pivotal in transforming raw pulp into usable toilet paper. The combination of advanced drying technologies and precise cutting methods ensures that the final product is both durable and comfortable to use. These processes underscore the complexity and attention to detail involved in manufacturing toilet paper, highlighting why it remains an essential commodity in modern hygiene practices.
Chemicals and Additives in Toilet Paper
Toilet paper, a staple in modern hygiene, often contains a variety of chemicals and additives that enhance its functionality and user experience. These additives can be broadly categorized into three key areas: softening agents and lotions, colorants and dyes, and preservatives and antimicrobial agents. Softening agents and lotions are crucial for improving the tactile comfort of toilet paper, making it gentler on skin. Colorants and dyes, on the other hand, are used to achieve the desired aesthetic appeal, whether it's a pure white or a subtle pastel hue. Preservatives and antimicrobial agents play a vital role in extending the shelf life of toilet paper by preventing the growth of bacteria and mold. Understanding these components is essential for consumers who seek to make informed choices about their personal care products. By delving into each of these categories, we can gain a deeper appreciation for the science behind toilet paper production. Let's start by exploring the role of softening agents and lotions, which are instrumental in creating a comfortable and soothing experience for users.
Softening Agents and Lotions
Softening agents and lotions play a crucial role in enhancing the comfort and usability of toilet paper, making it a staple in modern hygiene. These additives are designed to improve the tactile experience, ensuring that the toilet paper feels gentle against the skin. Softening agents, such as quaternary ammonium compounds and cationic surfactants, work by reducing the surface tension of water, allowing the fibers to become more pliable and less abrasive. This results in a softer, more absorbent product that minimizes irritation and discomfort. Lotions, on the other hand, are applied to the toilet paper during the manufacturing process to provide an additional layer of comfort. These lotions typically contain moisturizing ingredients like aloe vera, chamomile, and vitamin E, which help to soothe and protect the skin. By incorporating these lotions, toilet paper manufacturers can offer products that not only clean effectively but also provide a calming and nourishing experience. The application of lotions can be done through various methods, including spraying or coating the paper with a thin layer of the moisturizing substance. The inclusion of softening agents and lotions in toilet paper is particularly beneficial for individuals with sensitive skin or those who experience frequent irritation from using standard toilet paper. For instance, people suffering from conditions like hemorrhoids or anal fissures can find significant relief by using toilet paper enriched with these additives. Additionally, parents often prefer toilet paper with softening agents and lotions for their children to prevent skin irritation and discomfort. From a manufacturing perspective, incorporating softening agents and lotions requires careful consideration to ensure that the final product maintains its structural integrity while providing the desired comfort. Manufacturers must balance the amount of additives to avoid compromising the strength and durability of the toilet paper. Advanced technologies in paper production have made it possible to integrate these additives seamlessly, resulting in high-quality products that meet consumer expectations for both comfort and performance. In conclusion, softening agents and lotions are essential components in the production of premium toilet paper. They enhance user experience by providing a softer, more gentle product that is less likely to cause irritation. As consumer preferences continue to evolve towards greater comfort and hygiene, the role of these additives will remain pivotal in the development of superior toilet paper products. By understanding how these chemicals work and their benefits, consumers can make informed choices about their personal care products, ultimately leading to a more comfortable and healthy lifestyle.
Colorants and Dyes
Colorants and dyes play a crucial role in the manufacturing of toilet paper, particularly when it comes to enhancing the aesthetic appeal and functionality of the product. These additives are part of the broader category of chemicals and additives used in toilet paper production. Colorants can be divided into two main types: dyes and pigments. Dyes are dissolved in the pulp during the manufacturing process, imparting color to the entire sheet, while pigments are insoluble particles that adhere to the fibers, providing a more vibrant and durable color. The use of colorants in toilet paper is not merely for visual appeal; it also serves functional purposes. For instance, colored toilet paper can be used to indicate different scents or to differentiate between various product lines. Additionally, some colorants are designed to be pH-sensitive, changing color in response to changes in the user's body chemistry, which can be useful for health monitoring. From an environmental perspective, the choice of colorants is critical. Many traditional dyes and pigments are derived from synthetic chemicals that can have adverse effects on waterways and ecosystems when released during the manufacturing or disposal process. In response to these concerns, there has been a shift towards using eco-friendly and biodegradable colorants. These alternatives are often derived from natural sources such as plants, minerals, or microorganisms, ensuring that they are less harmful to the environment. The selection of colorants must also consider consumer safety. Some synthetic dyes have been linked to skin irritation and allergic reactions in sensitive individuals. Therefore, manufacturers often opt for hypoallergenic and dermatologically tested colorants to ensure that their products are safe for use on sensitive skin. In terms of regulatory compliance, the use of colorants in toilet paper is subject to strict guidelines. For example, the FDA in the United States has specific regulations regarding the types of dyes that can be used in products that come into contact with human skin. Similarly, the European Union has its own set of directives that dictate the permissible levels and types of colorants allowed in consumer goods. Technological advancements have also influenced the development of colorants for toilet paper. Modern manufacturing processes allow for precise control over the application of dyes and pigments, enabling consistent coloration and minimizing waste. Furthermore, innovations in nanotechnology have led to the creation of nano-pigments that offer superior lightfastness and durability compared to traditional colorants. In conclusion, colorants and dyes are integral components in the production of toilet paper, enhancing both its appearance and functionality while adhering to stringent safety and environmental standards. As consumer preferences continue to lean towards sustainable and safe products, the development of eco-friendly and hypoallergenic colorants will remain a key focus area for manufacturers in this industry.
Preservatives and Antimicrobial Agents
In the realm of toilet paper production, preservatives and antimicrobial agents play a crucial role in ensuring the product remains safe and hygienic for consumer use. These additives are essential components that help extend the shelf life of toilet paper by preventing the growth of microorganisms such as bacteria, fungi, and mold. Preservatives, in particular, are chemicals that inhibit the degradation of materials, thereby maintaining the integrity and freshness of the product. For instance, parabens and formaldehyde-releasing agents are commonly used preservatives that effectively combat microbial growth. However, due to growing consumer concerns about potential health risks associated with these chemicals, manufacturers are increasingly turning to alternative preservatives like phenoxyethanol and ethylhexylglycerin, which are considered safer and more environmentally friendly. Antimicrobial agents, on the other hand, are specifically designed to target and eliminate microorganisms. These agents can be incorporated into the pulp during the manufacturing process or applied as a coating on the finished product. Triclosan, for example, has been widely used as an antimicrobial agent in various consumer products, including toilet paper. However, its use has been scrutinized due to environmental and health concerns, leading many manufacturers to seek out alternative antimicrobial compounds such as silver nanoparticles or plant-derived extracts like tea tree oil. The inclusion of preservatives and antimicrobial agents in toilet paper is not merely a matter of product longevity but also consumer safety. These additives help prevent the spread of infections and maintain a clean environment around the bathroom area. Moreover, they contribute to a better user experience by ensuring that the toilet paper remains odor-free and free from visible signs of microbial growth. Despite their benefits, it is important for consumers to be aware of the potential risks associated with certain preservatives and antimicrobial agents. Some studies have suggested links between long-term exposure to certain chemicals and health issues such as skin irritation or hormonal disruptions. As a result, there is a growing trend towards using natural preservatives and antimicrobial agents that are gentler on both human skin and the environment. In conclusion, preservatives and antimicrobial agents are vital components in the production of toilet paper, enhancing both its shelf life and safety profile. While traditional chemicals have been effective in this role, the industry is shifting towards more sustainable and consumer-friendly alternatives. This evolution reflects a broader commitment to health, safety, and environmental responsibility in consumer goods manufacturing. As consumers become more informed about what goes into their everyday products, manufacturers must adapt by incorporating safer yet effective preservatives and antimicrobial agents into their formulations. This balance ensures that toilet paper remains a hygienic and reliable product for daily use while aligning with contemporary values of sustainability and health consciousness.