What Are Bullets Made Of

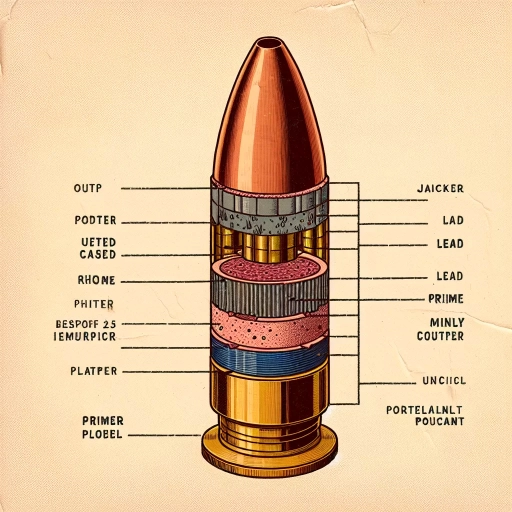
Bullets, a crucial component of firearms, have undergone significant transformations in their composition over the centuries. From their early beginnings to the present day, the materials used in bullet manufacturing have evolved to meet various demands such as performance, safety, and environmental considerations. This article delves into the multifaceted world of bullet materials, exploring their historical development, current usage, and future trends. We will examine how bullets transitioned from primitive lead projectiles to sophisticated modern designs, highlighting key milestones in their historical development. Additionally, we will discuss the current materials employed in bullet manufacturing, including lead, copper, and alternative metals, and their respective advantages and drawbacks. Finally, we will look at technological advancements and emerging trends that are shaping the future of bullet production. By understanding these aspects, readers will gain a comprehensive insight into the complex and evolving nature of bullet materials. Let us begin by tracing the historical development of bullet materials, which laid the foundation for the sophisticated projectiles we use today.
Historical Development of Bullet Materials
The development of bullet materials has been a pivotal aspect of military and technological history, reflecting the ingenuity and necessity driven by warfare and technological advancements. From the earliest days of projectile warfare, the materials used in bullets have evolved significantly, influenced by both practical needs and innovative breakthroughs. Initially, early bullet materials such as lead and stone were utilized due to their availability and basic effectiveness. However, as warfare tactics and technologies advanced, so did the materials used in bullet construction. The transition to modern metals like copper and brass marked a significant milestone, offering improved durability and performance. Furthermore, the pressures of warfare have consistently driven innovation in bullet material development, pushing the boundaries of what is possible and necessary for military effectiveness. This article delves into the historical development of bullet materials, exploring these key phases: Early Bullet Materials: Lead and Stone, Evolution to Modern Metals: Copper and Brass, and the Influence of Warfare on Bullet Material Innovation, providing a comprehensive look at how these advancements have shaped the course of history.
Early Bullet Materials: Lead and Stone
The early history of bullet materials is marked by the use of two primary substances: lead and stone. In the earliest days of firearms, bullets were often made from stone, particularly during the 14th to 16th centuries. Stone bullets, such as those made from limestone or granite, were used in primitive firearms like the hand cannon. These early projectiles were crude and inconsistent in shape and size, leading to variable performance and accuracy. However, as technology advanced and metalworking techniques improved, lead became the material of choice for bullet production. Lead's malleability, density, and relatively low melting point made it an ideal material for bullets. It could be easily molded into spherical shapes and was dense enough to maintain kinetic energy over long distances. The use of lead bullets became widespread during the 17th and 18th centuries, particularly with the development of rifled barrels which required more precise and consistent ammunition. Lead bullets were cast in molds to achieve uniformity, significantly enhancing the accuracy and range of firearms. Additionally, lead's softness allowed it to expand upon firing, engaging the rifling of the barrel and improving stability in flight. Despite its advantages, lead had its drawbacks. It was prone to deformation upon impact, which could affect penetration and expansion characteristics. Moreover, the use of lead posed health risks due to its toxicity; soldiers and hunters were exposed to lead dust and shavings during the loading process. However, these issues did not deter its widespread adoption until later centuries when alternative materials were developed. The transition from stone to lead marked a significant milestone in the historical development of bullet materials. It paved the way for further innovations such as the introduction of copper jackets in the late 19th century, which addressed some of the limitations associated with pure lead bullets. The evolution from stone to lead set a precedent for ongoing research into better, more efficient materials that would eventually lead to modern bullet designs made from a variety of metals and alloys. This early shift underscores the continuous quest for improved performance and safety in ammunition technology, a theme that remains central to the development of bullets today.
Evolution to Modern Metals: Copper and Brass
The evolution of metals from ancient times to modern applications is a fascinating narrative, particularly when it comes to materials like copper and brass, which have played pivotal roles in the development of bullet materials. Copper, one of the earliest metals to be extracted and used by humans, has a history dating back over 8,000 years. Its malleability, ductility, and excellent thermal and electrical conductivity made it an ideal material for various tools and weapons. As civilizations advanced, so did the techniques for alloying copper with other metals. The discovery of brass, an alloy of copper and zinc, marked a significant milestone. Brass was first produced around 3000 BCE in the ancient Near East and quickly became valued for its strength, durability, and resistance to corrosion. In the context of bullet materials, copper and brass have been integral components. During the early days of firearms, bullets were often made from lead due to its low melting point and high density. However, lead bullets had several drawbacks, including a tendency to deform upon firing and the potential for lead poisoning. The introduction of copper and brass jackets revolutionized bullet design. By encasing a lead core in a copper or brass jacket, bullets became more stable in flight and less prone to deformation. This innovation significantly improved accuracy and range. The use of copper and brass in modern bullet manufacturing continues to evolve. Modern bullets often feature a copper jacket over a lead core, which not only enhances performance but also reduces the environmental impact associated with lead exposure. Additionally, some bullets are now made entirely from copper or brass, eliminating the need for lead altogether. These all-metal bullets offer superior penetration and expansion characteristics while being more environmentally friendly. The historical development of bullet materials is closely tied to advancements in metallurgy and materials science. The transition from pure lead to copper-jacketed and brass-cased bullets reflects a broader trend towards more sophisticated and performance-driven materials. Today, researchers continue to explore new alloys and composite materials that can further enhance bullet performance while addressing safety and environmental concerns. The journey from ancient copper tools to modern brass-cased ammunition underscores the dynamic interplay between technological innovation and material science, highlighting how historical developments have shaped the present and will continue to influence future advancements in bullet technology.
Influence of Warfare on Bullet Material Innovation
The influence of warfare on bullet material innovation has been a driving force in the historical development of ammunition. Throughout history, the demands of conflict have consistently pushed the boundaries of technological advancements in bullet design and materials. In the early days of firearms, bullets were made from lead, which offered a good balance between weight and malleability but had significant drawbacks such as softness and tendency to deform upon impact. The advent of rifled barrels in the 19th century necessitated more robust materials to withstand the rifling process without deforming, leading to the introduction of copper jackets around lead cores. This innovation significantly improved accuracy and penetration. The World War I era saw further advancements with the introduction of full-metal jacket bullets, primarily made from copper or brass, which reduced lead exposure to soldiers and improved bullet performance in machine guns. The high-volume production needs during this period also spurred mass production techniques that made bullets more consistent and reliable. World War II brought about additional innovations, including the development of armor-piercing bullets with hardened steel cores encased in copper jackets, designed to penetrate armored vehicles and fortifications. The Cold War and subsequent conflicts led to the exploration of new materials such as tungsten carbide and depleted uranium for armor-piercing rounds due to their exceptional hardness and density. These materials allowed for smaller, lighter bullets that could achieve greater penetration than their predecessors. Modern warfare has also seen the rise of specialized bullets like those made from polymer or ceramic materials for specific applications such as hunting or law enforcement, where reduced ricochet risk is a priority. Moreover, advancements in materials science have enabled the creation of bullets with enhanced ballistic performance. For instance, the use of advanced composites and nanomaterials has led to the development of lighter yet stronger bullets that maintain their shape better upon impact. The ongoing quest for improved lethality, accuracy, and safety continues to drive innovation in bullet materials, reflecting the dynamic interplay between technological advancements and the evolving needs of warfare. In summary, the evolution of bullet materials has been intricately linked with the demands of warfare throughout history. Each major conflict has catalyzed significant improvements in design and material selection, ultimately leading to more effective, reliable, and specialized ammunition. This continuous cycle of innovation underscores the critical role that warfare plays in pushing the boundaries of technological development in the field of ammunition.
Current Materials Used in Bullet Manufacturing
The evolution of bullet manufacturing has been marked by significant advancements in materials science, reflecting a continuous quest for improved performance, durability, and lethality. From traditional choices to modern alternatives and cutting-edge innovations, the selection of materials has played a crucial role in shaping the history of ammunition. Historically, lead has been the traditional choice for bullet cores due to its density and malleability, but concerns over environmental impact and performance have led to the exploration of other materials. Copper and brass have emerged as modern alternatives, offering enhanced penetration and expansion characteristics while reducing lead exposure. Meanwhile, advanced materials such as tungsten and steel are being integrated into bullet design, providing superior hardness and penetration capabilities. This article delves into these three key areas—lead as the traditional choice, copper and brass as modern alternatives, and tungsten and steel as advanced materials—to provide a comprehensive understanding of current trends in bullet manufacturing. By examining these developments, we can better appreciate the historical development of bullet materials and how they have transformed over time.
Lead: The Traditional Choice
**Lead: The Traditional Choice** For centuries, lead has been the material of choice for bullet manufacturing due to its unique combination of properties that make it highly suitable for this application. Lead's primary advantage lies in its high density, which allows bullets to achieve significant kinetic energy and penetration upon impact. This density, coupled with its relatively low melting point, makes lead easy to cast into precise shapes and forms, a crucial factor in the mass production of bullets. Additionally, lead is malleable and can be easily shaped without breaking, which helps in maintaining the bullet's integrity during the manufacturing process and upon firing. Another significant benefit of lead is its cost-effectiveness. Compared to other metals, lead is relatively inexpensive, making it an economical choice for both small-scale and large-scale bullet production. This affordability has contributed to its widespread use across various types of ammunition, from hunting rounds to target practice bullets. Moreover, lead's chemical properties make it resistant to corrosion, which extends the shelf life of ammunition. When stored properly, lead bullets can remain viable for extended periods without degrading, ensuring consistent performance over time. However, it's worth noting that while lead offers many advantages, it also poses environmental and health concerns due to its toxicity. As a result, there has been a growing trend towards developing alternative materials that can mimic the performance of lead while mitigating its negative impacts. Despite these concerns, lead remains a traditional and widely used material in bullet manufacturing. Its well-understood properties and long history of use have established it as a reliable choice for many ammunition manufacturers. The familiarity with lead among gunsmiths and shooters also contributes to its enduring popularity. As technology continues to evolve and new materials are developed, it is likely that lead will remain a significant component in the production of bullets for the foreseeable future, albeit potentially in combination with other materials designed to enhance performance and safety.
Copper and Brass: Modern Alternatives
In the realm of bullet manufacturing, traditional materials like lead and copper have long been staples due to their durability and performance. However, with increasing concerns over environmental impact and the need for more sustainable options, modern alternatives such as copper and brass are gaining prominence. Copper, known for its excellent thermal conductivity and malleability, is being used in various forms to replace lead in bullets. For instance, copper-plated bullets offer a non-toxic alternative that maintains the ballistic performance of traditional lead bullets while reducing the risk of lead contamination in hunting grounds and shooting ranges. Additionally, solid copper bullets are becoming popular for their ability to expand upon impact, ensuring effective stopping power without the environmental drawbacks associated with lead. Brass, another versatile material, is also being leveraged in bullet manufacturing. Brass cartridges have been a standard component in ammunition for decades due to their strength, corrosion resistance, and recyclability. Modern advancements have led to the development of brass-cased bullets that combine the benefits of brass with the performance of copper or other metals. These hybrid bullets not only provide consistent ignition and reliable feeding but also offer a more eco-friendly solution compared to traditional lead-based ammunition. The use of brass further extends to the production of bullet casings, which can be recycled multiple times, reducing waste and the demand for raw materials. The shift towards copper and brass is driven by both regulatory pressures and consumer demand for greener products. In many regions, laws are being enacted to phase out lead-based ammunition in hunting and recreational shooting due to its harmful effects on wildlife and human health. As a result, manufacturers are investing heavily in research and development to perfect these alternative materials. The adoption of copper and brass in bullet manufacturing not only aligns with environmental sustainability but also ensures that the performance standards of ammunition are maintained or even improved. This dual focus on sustainability and performance underscores the evolving landscape of bullet manufacturing, where innovation meets necessity to create safer, more responsible ammunition options for the future.
Advanced Materials: Tungsten and Steel
In the realm of bullet manufacturing, advanced materials such as tungsten and steel play pivotal roles due to their unique properties and performance characteristics. Tungsten, known for its exceptional hardness and density, is often used in the production of armor-piercing rounds. Its high melting point and resistance to wear make it an ideal choice for penetrating hardened targets. When combined with other metals like copper or nickel, tungsten forms a composite that enhances the bullet's kinetic energy and penetration capabilities without compromising its structural integrity. This makes tungsten-based bullets highly effective in military applications where deep penetration is crucial. Steel, on the other hand, offers a balance of strength, durability, and cost-effectiveness, making it a versatile material in bullet manufacturing. Steel bullets are commonly used in full metal jacket (FMJ) rounds where the steel core is encased in a softer metal jacket. This design ensures that the bullet maintains its shape upon impact while minimizing the risk of fragmentation. The use of steel also allows for the production of bullets with precise dimensions and consistent performance, which is essential for achieving reliable accuracy and range. Additionally, steel's lower cost compared to tungsten makes it a preferred choice for mass production, particularly in civilian markets where cost efficiency is a significant factor. The integration of these advanced materials into bullet design has significantly enhanced the performance and reliability of ammunition across various applications. For instance, tungsten-tipped bullets are favored by military forces for their ability to penetrate armor effectively, while steel-cored bullets are popular among civilian shooters due to their affordability and consistent performance. The ongoing research and development in these materials continue to push the boundaries of what is possible in bullet technology, ensuring that modern ammunition meets the evolving demands of both military and civilian users. Moreover, the combination of tungsten and steel with other materials such as lead, copper, and brass has led to the creation of hybrid bullets that leverage the strengths of multiple components. These hybrid designs offer improved ballistic performance, reduced environmental impact, and enhanced safety features. For example, bullets with a steel core and a copper jacket can provide better expansion upon impact while minimizing lead exposure—a critical consideration in hunting and target shooting scenarios. In summary, the use of advanced materials like tungsten and steel in bullet manufacturing has revolutionized the field by offering superior performance, enhanced durability, and improved cost efficiency. These materials continue to be at the forefront of ammunition technology, driving innovation and ensuring that bullets meet the stringent requirements of various applications with precision and reliability. As research continues to advance, it is likely that these materials will remain integral to the development of next-generation ammunition.
Technological Advancements and Future Trends
In the ever-evolving landscape of technological advancements, the development of bullet materials has undergone significant transformations, driven by environmental considerations, performance enhancements, and innovative research. This article delves into the future trends shaping the industry, highlighting three pivotal areas: the development of non-toxic bullets to mitigate environmental impact, the creation of enhanced performance materials such as polymer and composite bullets, and cutting-edge research into new materials like nanomaterials and smart bullets. These advancements not only reflect a commitment to sustainability and improved functionality but also underscore the dynamic nature of technological innovation. As we explore these contemporary developments, it is essential to appreciate the historical context that has led us to this point. Understanding the historical development of bullet materials provides a rich backdrop against which we can fully appreciate the strides made and the future possibilities that lie ahead. By examining these trends and their historical roots, we gain a comprehensive view of how technology continues to redefine the boundaries of what is possible in bullet design and production.
Development of Non-Toxic Bullets: Environmental Considerations
The development of non-toxic bullets represents a significant stride in addressing the environmental and health concerns associated with traditional ammunition. Traditional bullets, often made from lead, pose substantial risks to both human health and the environment. Lead, a toxic heavy metal, can contaminate soil, water, and air when bullets are fired or when they decompose. This contamination can have devastating effects on wildlife, particularly birds and other scavengers that ingest lead fragments while feeding on carcasses. Moreover, hunters and shooters are also at risk of lead exposure through inhalation of lead dust or ingestion of contaminated game meat. In response to these issues, technological advancements have led to the creation of non-toxic bullets made from alternative materials such as copper, zinc, and tungsten. These materials are chosen for their high density and ability to maintain the ballistic performance of traditional lead bullets while eliminating the toxic risks. Copper bullets, for instance, are becoming increasingly popular due to their excellent expansion properties and minimal fragmentation upon impact, which reduces the likelihood of toxic residues being left behind. Zinc and tungsten bullets offer similar advantages, with tungsten being particularly effective due to its high density and hardness. The environmental benefits of non-toxic bullets are multifaceted. By reducing lead contamination in ecosystems, these bullets help protect biodiversity and maintain ecological balance. Additionally, non-toxic bullets support sustainable hunting practices by ensuring that game meat remains safe for consumption without the risk of lead poisoning. This shift towards eco-friendly ammunition also aligns with broader environmental policies aimed at minimizing pollution and promoting public health. From a technological standpoint, the development of non-toxic bullets involves sophisticated manufacturing processes that ensure consistent quality and performance. Advanced machining techniques and precise material selection are crucial in producing bullets that meet stringent standards for accuracy and reliability. Furthermore, ongoing research is focused on improving the design and composition of these bullets to enhance their effectiveness across various shooting applications. As we look to future trends in ammunition technology, it is clear that non-toxic bullets will play a pivotal role. Regulatory bodies are increasingly mandating the use of non-lead ammunition in certain areas, driving demand for these products. This regulatory push, combined with growing consumer awareness about environmental impacts, is likely to accelerate innovation in this field. As a result, we can expect even more advanced and efficient non-toxic bullet designs that not only mitigate environmental harm but also offer superior performance characteristics. The integration of these eco-friendly bullets into mainstream shooting practices will be a significant step towards a more sustainable future for both recreational and professional shooters alike.
Enhanced Performance Materials: Polymer and Composite Bullets
In the realm of technological advancements, the development of enhanced performance materials has significantly impacted the manufacturing of bullets, particularly with the introduction of polymer and composite materials. These innovative materials are transforming the traditional metal-centric bullet design, offering superior performance, reduced environmental impact, and enhanced safety features. Polymer bullets, for instance, are made from advanced synthetic polymers that provide consistent and reliable performance. These bullets are lighter, which can result in reduced recoil and improved accuracy for shooters. Additionally, polymer bullets are less likely to fragment upon impact, reducing the risk of collateral damage and making them safer for use in urban environments. Composite bullets take this innovation a step further by combining different materials to achieve specific properties. For example, a composite bullet might have a polymer core encased in a thin metal jacket, offering the best of both worlds: the lightness and consistency of polymers coupled with the penetration capabilities of metals. This hybrid approach allows for tailored performance characteristics such as controlled expansion upon impact, which is crucial for hunting and self-defense applications. Furthermore, composite materials can be engineered to be non-toxic and lead-free, addressing environmental concerns associated with traditional lead-based ammunition. The future trends in bullet technology are heavily influenced by these advancements. As research continues to push the boundaries of material science, we can expect even more sophisticated bullet designs that balance performance with sustainability. For instance, biodegradable polymers are being explored for use in bullets that could decompose over time, reducing the long-term environmental footprint of ammunition. Moreover, advancements in 3D printing are enabling the rapid prototyping and production of complex bullet geometries that were previously impossible to manufacture using traditional methods. The integration of smart materials and nanotechnology into bullet design is another promising area of research. These materials can be engineered to respond dynamically to different conditions, such as temperature or impact velocity, allowing for real-time adjustments in performance. This could lead to bullets that adapt their expansion or penetration characteristics based on the target, enhancing both effectiveness and safety. In conclusion, the evolution of polymer and composite bullets represents a significant leap forward in ammunition technology. These enhanced performance materials not only improve the functional aspects of bullets but also address critical issues related to safety and environmental sustainability. As technological advancements continue to drive innovation in this field, we can anticipate even more groundbreaking developments that will redefine the future of ammunition manufacturing.
Research into New Materials: Nanomaterials and Smart Bullets
Research into new materials, particularly nanomaterials and smart bullets, represents a significant frontier in technological advancements within the field of ammunition. Nanomaterials, characterized by their dimensions on the nanoscale, offer unique properties such as enhanced strength, reduced weight, and improved thermal conductivity. These attributes make them ideal for developing next-generation bullets that can penetrate armor more effectively while minimizing collateral damage. For instance, nanocrystalline metals and nanoceramics are being explored for their potential to create lighter yet stronger bullet casings and cores. This innovation could lead to ammunition that maintains its lethality at longer ranges without the need for heavier, more cumbersome rounds. Smart bullets, on the other hand, integrate advanced technologies such as microelectronics and sensors to enhance their performance and accuracy. These bullets can be programmed to adjust their trajectory mid-flight, ensuring a higher hit probability even against moving targets. The integration of GPS and inertial measurement units allows smart bullets to self-correct their path, making them highly effective in complex combat scenarios. Additionally, smart bullets can be designed with various mission profiles, such as detonating upon impact or after a specified delay, which adds a layer of tactical flexibility. The convergence of nanomaterials and smart technologies in bullet design also opens up possibilities for environmentally friendly ammunition. For example, bullets made from biodegradable nanomaterials could reduce the environmental impact of spent rounds by decomposing naturally over time. This dual focus on performance and sustainability underscores the multifaceted nature of current research into new materials for bullets. Moreover, the development of these advanced materials and technologies is not isolated but rather part of a broader trend towards more sophisticated weaponry. As military and law enforcement agencies seek to leverage cutting-edge science to gain strategic advantages, the demand for innovative ammunition solutions continues to drive research and development. The future of bullets is likely to be shaped by these advancements, leading to more precise, effective, and sustainable ammunition that aligns with evolving operational needs and ethical considerations. In summary, the research into nanomaterials and smart bullets epitomizes the dynamic interplay between technological innovation and practical application in the field of ammunition. By harnessing the unique properties of nanomaterials and integrating advanced sensor technologies, scientists are paving the way for a new generation of bullets that are not only more lethal but also more precise and environmentally conscious. This ongoing research underscores the relentless pursuit of excellence in technological advancements and future trends within the realm of ammunition.