What Is The Strongest Glue For Metal To Metal

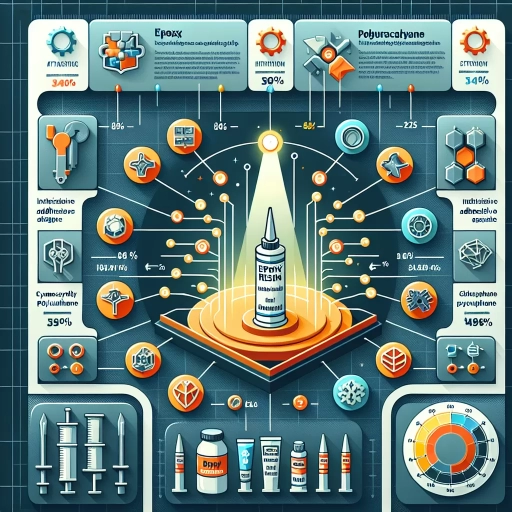
When it comes to bonding metal to metal, selecting the strongest adhesive is crucial for ensuring durability and reliability. The choice of adhesive can significantly impact the performance and longevity of the bond, making it essential to understand the various types of metal-to-metal adhesives available. In this article, we will delve into the key factors that influence the strength of these adhesives, such as surface preparation, environmental conditions, and chemical properties. We will also provide top recommendations for the strongest metal-to-metal glues on the market. To begin, it is vital to understand the different types of metal-to-metal adhesives, each with its unique characteristics and applications. By grasping these distinctions, you can make informed decisions about which adhesive best suits your needs. Let's start by exploring the various types of metal-to-metal adhesives.
Understanding the Types of Metal-to-Metal Adhesives
Understanding the types of metal-to-metal adhesives is crucial for various industrial and engineering applications, as these adhesives play a pivotal role in bonding metals securely and efficiently. There are several key types of metal-to-metal adhesives, each with its unique properties and advantages. Epoxy-based adhesives, known for their high strength and durability, are widely used in structural applications. Acrylic-based adhesives offer rapid curing times and excellent impact resistance, making them ideal for high-volume production. Polyurethane-based adhesives provide flexibility and resistance to environmental factors, making them suitable for dynamic load conditions. By understanding the characteristics of these adhesives, engineers and manufacturers can select the most appropriate type for their specific needs. Let's delve into the first of these: epoxy-based adhesives, which are renowned for their exceptional bonding strength and versatility in various metal bonding applications.
1. Epoxy-Based Adhesives
Epoxy-based adhesives are a robust and versatile option for metal-to-metal bonding, renowned for their exceptional strength, durability, and versatility. These adhesives are composed of two primary components: a resin and a hardener, which when mixed together, undergo a chemical reaction that results in a strong, rigid bond. The epoxy resin provides excellent mechanical properties, including high tensile strength and resistance to impact, while the hardener ensures the adhesive cures properly to achieve optimal bonding. One of the key advantages of epoxy-based adhesives is their ability to bond a wide range of metals, including aluminum, steel, copper, and titanium. They are particularly effective in applications where high structural integrity is required, such as in aerospace, automotive, and industrial manufacturing. Epoxy adhesives also offer excellent resistance to environmental factors like moisture, chemicals, and extreme temperatures, making them suitable for use in harsh conditions. The curing process of epoxy adhesives can be tailored to meet specific application needs. Room temperature curing epoxies are convenient for many applications, while heat-cured epoxies can provide even higher strength and faster curing times. Additionally, some epoxy formulations are designed to be flexible, which can help absorb vibrations and stresses that might otherwise compromise the bond. In terms of preparation and application, epoxy-based adhesives generally require a clean and dry surface for optimal bonding. Surface preparation may involve degreasing, sanding, or applying a primer to ensure a strong bond. Once applied, the mixed adhesive is typically allowed to cure for a specified period, which can range from a few minutes to several hours depending on the formulation. Overall, epoxy-based adhesives offer a reliable and powerful solution for metal-to-metal bonding due to their high strength, versatility, and resistance to environmental factors. Their ability to be tailored for various applications makes them a preferred choice in many industries where strong and durable bonds are critical.
2. Acrylic-Based Adhesives
Acrylic-based adhesives are a versatile and widely used option for metal-to-metal bonding, offering a balance of strength, flexibility, and ease of use. These adhesives are typically two-component systems, consisting of a resin and a hardener, which when mixed together, form a strong and durable bond. Here are the key characteristics and advantages of acrylic-based adhesives: 1. **Rapid Cure Time**: Acrylic adhesives are known for their fast curing times, often setting within minutes to hours, depending on the specific formulation. This rapid curing makes them ideal for high-volume production environments where quick turnaround times are crucial. 2. **High Strength**: Acrylic adhesives provide excellent tensile strength and shear strength, making them suitable for a wide range of metal bonding applications. They can withstand significant stress and are often used in structural bonding where high mechanical performance is required. 3. **Flexibility**: Unlike some other types of adhesives, acrylics offer a degree of flexibility, which helps absorb vibrations and impacts without compromising the bond. This flexibility is particularly beneficial in applications where the bonded parts may be subject to thermal expansion or mechanical stress. 4. **Chemical Resistance**: Many acrylic adhesives exhibit good resistance to chemicals, oils, and fuels, making them suitable for use in harsh environments. However, it's important to select an adhesive that is specifically formulated to withstand the chemicals present in your application. 5. **Ease of Use**: Acrylic adhesives are generally easy to apply and mix, with some formulations available in pre-mixed cartridges that simplify the application process. They also have a relatively low odor compared to other types of adhesives, enhancing workplace safety. 6. **Surface Preparation**: While acrylic adhesives can bond well to a variety of metals, proper surface preparation is still essential for achieving optimal bond strength. Cleaning the surfaces to remove oils, greases, and other contaminants is crucial before applying the adhesive. 7. **Temperature Range**: Acrylic adhesives typically operate well within a moderate temperature range, usually between -20°C to 80°C (-4°F to 176°F), although some specialized formulations can handle more extreme temperatures. 8. **Environmental Considerations**: Some acrylic adhesives are formulated to be more environmentally friendly than others, with lower VOCs (volatile organic compounds) and safer handling characteristics. When choosing an adhesive, consider these factors if environmental impact is a concern. In summary, acrylic-based adhesives offer a robust combination of fast curing times, high mechanical strength, flexibility, and ease of use, making them a popular choice for metal-to-metal bonding applications across various industries. Their versatility and performance characteristics ensure they remain a strong contender in the selection of the strongest glue for metal-to-metal bonding.
3. Polyurethane-Based Adhesives
Polyurethane-based adhesives are a versatile and widely used option for metal-to-metal bonding, offering a balance of strength, flexibility, and durability. These adhesives are formulated from the reaction of isocyanates with polyols, resulting in a robust polymer network that adheres well to various metal surfaces. One of the key advantages of polyurethane adhesives is their ability to absorb vibrations and impacts, making them ideal for applications where the bonded parts are subject to dynamic stresses. This flexibility also allows them to accommodate slight movements between the bonded surfaces without compromising the integrity of the bond. In terms of strength, polyurethane adhesives can achieve tensile strengths ranging from 1,000 to 3,000 psi (pounds per square inch), which is sufficient for many industrial and automotive applications. They also exhibit good resistance to chemicals and environmental factors such as moisture and temperature fluctuations, although their performance can vary depending on the specific formulation and curing conditions. The curing process for polyurethane adhesives typically involves a chemical reaction that can be accelerated by heat or catalysts, allowing for faster production cycles. Another significant benefit of polyurethane-based adhesives is their ease of application. They are available in various forms, including one-component (1K) and two-component (2K) systems. One-component systems are simpler to apply as they do not require mixing, while two-component systems offer greater control over the curing process and often result in stronger bonds. Additionally, polyurethane adhesives can be formulated to meet specific requirements such as low viscosity for easy spreading or high viscosity for better gap-filling capabilities. Despite their many advantages, polyurethane adhesives do have some limitations. They generally require surface preparation to ensure optimal adhesion, which can include cleaning and applying a primer. Furthermore, they may not be suitable for high-temperature applications above 200°F (93°C) due to potential degradation of the polymer matrix. However, for a wide range of metal-to-metal bonding needs where flexibility and moderate to high strength are required, polyurethane-based adhesives are an excellent choice. Their versatility, combined with their robust performance characteristics, makes them a popular selection across various industries including automotive, aerospace, and construction.
Key Factors Influencing the Strength of Metal Adhesives
The strength of metal adhesives is a critical factor in various industrial applications, and several key factors influence their performance. Surface preparation and cleanliness, environmental conditions and durability, and application techniques and curing times are the primary elements that determine the efficacy of metal adhesives. Proper surface preparation ensures a strong bond by removing contaminants and enhancing the surface energy of the metal, which is essential for achieving optimal adhesion. Environmental conditions, such as temperature and humidity, can significantly impact the durability of the adhesive bond, necessitating careful consideration to ensure long-term stability. Additionally, the application techniques and curing times must be precisely controlled to maximize the adhesive's mechanical properties. By understanding and optimizing these factors, manufacturers can ensure that metal adhesives meet the stringent requirements of their applications. Let's delve into the first of these crucial factors: surface preparation and cleanliness.
1. Surface Preparation and Cleanliness
Surface preparation and cleanliness are crucial factors influencing the strength of metal adhesives. The integrity of the bond between metal surfaces depends significantly on how well these surfaces are prepared before applying the adhesive. Any contaminants, such as dirt, oil, grease, or moisture, can weaken the adhesive bond by creating a barrier that prevents the adhesive from forming a strong chemical or mechanical bond with the metal. Therefore, thorough cleaning of the metal surfaces is essential. This typically involves degreasing with solvents to remove oils and greases, followed by mechanical cleaning methods like sanding or grit blasting to remove any oxide layers and roughen the surface for better adhesion. Additionally, chemical treatments such as etching or priming may be necessary to enhance surface energy and create a more receptive surface for bonding. Ensuring that the surfaces are free from dust and other particles after cleaning is also vital; this can be achieved through the use of compressed air or vacuum cleaning. Proper surface preparation not only enhances the initial bond strength but also ensures long-term durability and resistance to environmental factors such as temperature changes and exposure to chemicals. In summary, meticulous surface preparation and cleanliness are foundational steps in achieving strong and reliable metal-to-metal bonds with adhesives.
2. Environmental Conditions and Durability
Environmental conditions play a crucial role in determining the durability and strength of metal adhesives. Temperature, humidity, exposure to chemicals, and mechanical stress are key factors that can significantly impact the performance of these adhesives. High temperatures can cause the adhesive to degrade, leading to a loss of bond strength over time. Conversely, low temperatures may slow down the curing process or affect the adhesive's flexibility, making it more prone to cracking under stress. Humidity levels are also critical; excessive moisture can lead to hydrolysis, which breaks down the adhesive's molecular structure, compromising its integrity. Chemical exposure is another significant environmental factor. Metals often come into contact with various substances such as fuels, oils, and cleaning agents, which can react with the adhesive and weaken its bond. For instance, certain adhesives may not be compatible with solvents or acids, leading to a rapid deterioration of the bond when exposed to these substances. Mechanical stress, including vibrations and impacts, can also affect the durability of metal adhesives. The adhesive must be able to withstand these stresses without failing or degrading over time. To ensure optimal performance under various environmental conditions, it is essential to select an adhesive that is specifically formulated for the anticipated exposure. For example, epoxy-based adhesives are known for their high temperature resistance and chemical stability, making them suitable for applications in harsh environments. Polyurethane adhesives offer good flexibility and resistance to mechanical stress, making them ideal for dynamic loading conditions. Acrylic adhesives, on the other hand, provide fast curing times and are often used in applications where rapid assembly is required. In addition to selecting the right type of adhesive, proper surface preparation is crucial for ensuring durability. Cleanliness and surface roughness can significantly affect the bond strength. Contaminants such as oils or greases must be removed to ensure a strong bond, while surface roughening can enhance mechanical interlocking between the metal and adhesive. Ultimately, understanding and addressing these environmental factors is vital for achieving the strongest possible bond between metal surfaces. By choosing an appropriate adhesive based on anticipated environmental conditions and ensuring proper surface preparation, engineers and manufacturers can maximize the strength and durability of metal adhesives, thereby enhancing the overall performance and lifespan of their products. This careful consideration of environmental conditions not only ensures that the adhesive meets its intended specifications but also contributes to the reliability and safety of the final product.
3. Application Techniques and Curing Times
When it comes to achieving the strongest bond in metal-to-metal adhesion, application techniques and curing times are crucial factors that cannot be overlooked. The method of applying the adhesive can significantly impact the final strength of the bond. For instance, ensuring a uniform and thin layer of adhesive is applied can help in maximizing the surface area contact between the metals, thereby enhancing the bond strength. This can be achieved through techniques such as brushing, spraying, or using automated dispensing systems. Additionally, proper surface preparation is essential; cleaning the metal surfaces to remove any contaminants or oils and roughening them slightly can improve the adhesive's ability to bond effectively. Curing times also play a critical role in determining the ultimate strength of the adhesive bond. Different types of metal adhesives have varying curing times, which can range from a few minutes for some epoxy-based adhesives to several hours or even days for others like polyurethane or acrylic adhesives. It is vital to adhere strictly to the recommended curing times specified by the manufacturer to ensure that the adhesive fully cures and reaches its maximum bonding potential. Premature handling or loading of the bonded parts before the adhesive has fully cured can lead to weakened bonds and reduced overall strength. Moreover, environmental conditions such as temperature and humidity during the curing process can influence the final bond strength. Some adhesives may require elevated temperatures to accelerate curing, while others may be sensitive to moisture levels. Ensuring that these conditions are controlled and optimized according to the adhesive's specifications is key to achieving a strong and durable bond. In summary, precise application techniques and adherence to recommended curing times are essential for maximizing the strength of metal adhesives. By ensuring uniform application, proper surface preparation, and optimal curing conditions, users can significantly enhance the bonding performance and achieve the strongest possible bond between metal components. This attention to detail is critical in applications where high reliability and durability are paramount, such as in aerospace, automotive, and industrial manufacturing sectors.
Top Recommendations for Strong Metal-to-Metal Glues
When it comes to selecting the best metal-to-metal glues, several top-tier options stand out for their exceptional strength, durability, and ease of use. Among these, Loctite Epoxy Instant Mix, 3M Scotch-Weld DP100 Plus, and J-B Weld KwikWeld are highly recommended for various applications. Each of these products offers unique advantages that cater to different needs. Loctite Epoxy Instant Mix is renowned for its rapid curing time and high bonding strength, making it ideal for projects requiring quick results. 3M Scotch-Weld DP100 Plus is celebrated for its versatility and ability to bond a wide range of metals, including aluminum and steel. J-B Weld KwikWeld, on the other hand, is praised for its fast-setting properties and high temperature resistance. Whether you are working on a small DIY project or a large industrial application, these glues provide reliable solutions. In this article, we will delve into the specifics of each product, starting with the benefits and applications of Loctite Epoxy Instant Mix.
1. Loctite Epoxy Instant Mix
**Loctite Epoxy Instant Mix** stands out as a top recommendation for strong metal-to-metal glues due to its exceptional bonding strength and ease of use. This two-part epoxy adhesive is designed to provide a robust and durable bond between metal surfaces, making it ideal for a wide range of applications, from industrial repairs to DIY projects. The instant mix formula ensures that the epoxy hardens quickly, typically within 5 minutes, allowing for rapid assembly and minimizing downtime. This fast-setting characteristic is particularly beneficial in situations where time is of the essence or where parts need to be handled soon after application. The Loctite Epoxy Instant Mix boasts a high tensile strength, often exceeding 3,000 psi, which is significantly higher than many other adhesives on the market. This superior strength ensures that the bond can withstand significant stress and impact without compromising its integrity. Additionally, the epoxy is resistant to various environmental factors such as moisture, chemicals, and extreme temperatures, making it suitable for use in harsh conditions. One of the key advantages of Loctite Epoxy Instant Mix is its simplicity in application. The adhesive comes in a convenient syringe format with a built-in mixing nozzle, eliminating the need for separate mixing containers and reducing the risk of contamination. This design also ensures a precise 1:1 mix ratio, which is crucial for achieving optimal bonding performance. Furthermore, the epoxy is versatile and can be used on a variety of metal substrates including steel, aluminum, and brass. In terms of safety and handling, Loctite Epoxy Instant Mix is formulated to be user-friendly. It has low odor and is free from solvents, making it safer to use in confined spaces or indoor environments. However, it is still important to follow standard safety precautions such as wearing gloves and working in a well-ventilated area. Overall, Loctite Epoxy Instant Mix is an excellent choice for anyone seeking a reliable and powerful metal-to-metal adhesive. Its combination of rapid curing time, high tensile strength, environmental resistance, and ease of application makes it an indispensable tool for both professionals and hobbyists alike. Whether you are repairing machinery, fabricating parts, or simply need a strong bond for a metal project, Loctite Epoxy Instant Mix delivers consistent results that meet the highest standards of quality and performance.
2. 3M Scotch-Weld DP100 Plus
For those seeking a reliable and robust metal-to-metal adhesive, the 3M Scotch-Weld DP100 Plus stands out as a top recommendation. This epoxy-based adhesive is engineered to deliver exceptional strength and durability, making it an ideal choice for various industrial and DIY applications. The DP100 Plus boasts a high tensile strength of up to 3,000 psi, ensuring that it can withstand significant stress and load without compromising the bond. Its excellent shear strength further enhances its performance in demanding environments. One of the key advantages of the 3M Scotch-Weld DP100 Plus is its versatility. It can effectively bond a wide range of metals, including aluminum, steel, and stainless steel, as well as other materials such as glass and ceramics. This versatility makes it a go-to solution for diverse projects, from automotive repairs to construction and manufacturing. The adhesive also features a moderate viscosity, which allows for easy application and ensures that it flows smoothly into tight spaces. This characteristic is particularly beneficial for bonding complex geometries or small parts where precision is crucial. Additionally, the DP100 Plus has a relatively short working time of about 4-6 minutes, allowing users to quickly assemble parts before the adhesive sets. Another significant benefit of this adhesive is its resistance to environmental factors. It exhibits excellent chemical resistance and can withstand exposure to various solvents, fuels, and oils. This makes it particularly suitable for applications in harsh environments where other adhesives might fail. Furthermore, the DP100 Plus is resistant to high temperatures up to 250°F (121°C), ensuring that the bond remains strong even under thermal stress. In terms of safety and ease of use, the 3M Scotch-Weld DP100 Plus is formulated with low odor and low VOCs (volatile organic compounds), making it safer for users compared to other epoxy adhesives. It also comes in convenient packaging options, including dual cartridges and bulk containers, which cater to different project scales and user preferences. Overall, the 3M Scotch-Weld DP100 Plus is a superior choice for metal-to-metal bonding due to its exceptional strength, versatility, ease of application, and environmental resistance. Whether you are a professional or a DIY enthusiast, this adhesive offers the reliability and performance needed to ensure strong and lasting bonds in a variety of challenging applications.
3. J-B Weld KwikWeld
J-B Weld KwikWeld is a standout choice among metal-to-metal adhesives, renowned for its exceptional strength and versatility. This two-part epoxy-based adhesive is designed to provide a robust bond between metal surfaces, making it an ideal solution for various applications, from automotive repairs to industrial manufacturing. Unlike many other adhesives, KwikWeld sets quickly, typically within 4-6 minutes, allowing for rapid assembly and minimizing downtime. Once fully cured, which usually takes about 4-6 hours, KwikWeld achieves a tensile strength of up to 3,960 psi, ensuring a durable and long-lasting bond that can withstand significant stress and environmental conditions. Its high temperature resistance, up to 240°F (115°C), makes it suitable for use in demanding environments. Additionally, KwikWeld is resistant to chemicals and fuels, further enhancing its reliability in harsh settings. The ease of application—simply mix the two components together and apply—combined with its impressive bonding capabilities, makes J-B Weld KwikWeld a top recommendation for anyone seeking a strong and reliable metal-to-metal adhesive. Whether you're a professional mechanic or a DIY enthusiast, KwikWeld's performance and convenience make it an indispensable tool in your arsenal.