What Is The Strongest Glue To Use On Plastic

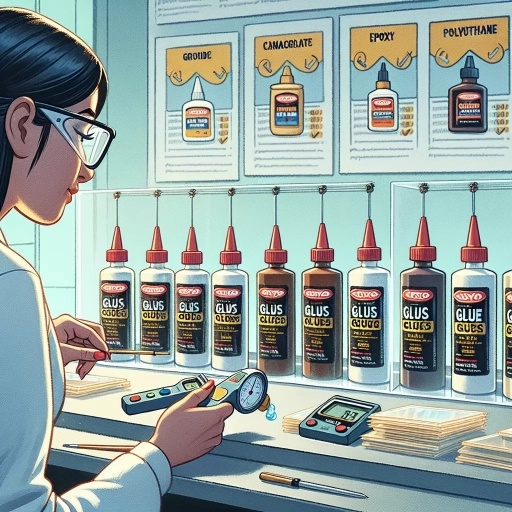
When it comes to bonding plastic, selecting the right adhesive is crucial for achieving a strong and durable bond. With the vast array of plastics and adhesives available, making an informed decision can be daunting. This article aims to guide you through the process by first understanding the different types of plastics, as each type has unique properties that affect adhesion. We will then evaluate various adhesives specifically designed for plastic, highlighting their strengths and limitations. Finally, we will discuss application considerations and best practices to ensure a successful bonding process. By grasping these key aspects, you will be better equipped to choose the strongest glue for your specific plastic application. Let's begin by delving into the diverse world of plastics and how their characteristics influence adhesive performance in our first section: **Understanding the Types of Plastics**.
Understanding the Types of Plastics
Understanding the types of plastics is crucial for various industries, from manufacturing to healthcare, as it directly influences the performance, durability, and safety of products. This article delves into the complexities of plastic materials, beginning with a comparison of thermoplastics and thermosets. These two categories are fundamental in understanding the broader spectrum of plastics, as they differ significantly in terms of their molecular structure and reusability. Additionally, we will explore common plastic materials and their unique properties, which are essential for selecting the right material for specific applications. Finally, we will discuss how the type of plastic impacts the choice of adhesives, a critical consideration in product assembly and repair. By grasping these concepts, readers will gain a comprehensive understanding of plastics and their diverse uses. Let's start by examining the key differences between thermoplastics and thermosets, which form the foundation of plastic classification and usage.
Thermoplastics vs. Thermosets
When delving into the world of plastics, it is crucial to understand the fundamental differences between thermoplastics and thermosets, as these distinctions significantly impact their applications, properties, and uses. Thermoplastics and thermosets are two broad categories of plastics that exhibit unique characteristics due to their molecular structures and processing methods. **Thermoplastics** are versatile and widely used materials that can be melted and reformed multiple times without undergoing any significant chemical change. This property makes them highly recyclable and reusable. Thermoplastics are typically linear or branched polymers, which allow them to be molded, extruded, or 3D printed into various shapes. Examples of thermoplastics include polyethylene (PE), polypropylene (PP), polyvinyl chloride (PVC), and polycarbonate (PC). These materials are commonly found in everyday items such as plastic bags, water bottles, and automotive parts. The ability of thermoplastics to be melted and reshaped makes them ideal for applications requiring flexibility and durability. On the other hand, **thermosets** undergo a chemical change when they are exposed to heat, resulting in a rigid structure that cannot be melted or reshaped once it has been set. This irreversible process is known as curing, which transforms the material into a three-dimensional network of molecules. Thermosets are often used in applications where high strength, dimensional stability, and resistance to heat and chemicals are required. Examples of thermosets include epoxy resins, polyurethane (PU), and phenolic resins. These materials are frequently used in adhesives, coatings, and composite materials such as fiberglass and carbon fiber reinforced polymers (CFRP). The rigidity and stability of thermosets make them suitable for demanding environments like aerospace, automotive, and construction industries. The choice between thermoplastics and thermosets depends on the specific requirements of the application. For instance, if the plastic needs to be flexible and recyclable, a thermoplastic would be the better option. However, if the application demands high strength, stability, and resistance to heat or chemicals, a thermoset would be more appropriate. Understanding these differences is essential for selecting the right type of plastic for various projects and ensuring optimal performance. In the context of using glue on plastic, knowing whether you are working with a thermoplastic or thermoset can guide your choice of adhesive. For thermoplastics, adhesives that can bond well with the specific type of plastic are often necessary; for example, cyanoacrylate (super glue) works well with many types of thermoplastics. For thermosets, the adhesive must be compatible with the cured material's properties; epoxy-based adhesives are commonly used due to their strong bonding capabilities. In conclusion, the distinction between thermoplastics and thermosets is pivotal in understanding their applications and selecting the appropriate type of plastic for a given task. This knowledge not only aids in material selection but also ensures that the chosen adhesive will effectively bond with the plastic, thereby enhancing the overall performance and longevity of the product.
Common Plastic Materials and Their Properties
When delving into the realm of plastics, understanding the various types and their properties is crucial for selecting the appropriate material for specific applications. Common plastic materials are diverse, each with unique characteristics that make them suitable for different uses. **Polyethylene (PE)**, for instance, is one of the most widely used plastics due to its flexibility, chemical resistance, and low cost. It is often found in packaging materials like plastic bags and containers. **Polypropylene (PP)**, another versatile plastic, offers high impact resistance and is commonly used in automotive parts, medical devices, and consumer products such as containers and fibers. **Polyvinyl Chloride (PVC)** is known for its rigidity and resistance to chemicals, making it ideal for pipes, vinyl records, and window frames. Its versatility also extends to flexible forms used in flooring and clothing. **Polyethylene Terephthalate (PET)** is renowned for its clarity and strength, which is why it is frequently used in water bottles, food packaging, and textile fibers like polyester. **Polycarbonate (PC)** stands out for its exceptional impact resistance and transparency, making it a favorite for safety glasses, bulletproof glass, and electronic components. **Acrylonitrile Butadiene Styrene (ABS)** combines the benefits of impact resistance, toughness, and affordability, making it a popular choice for consumer products such as toys, appliances, and automotive parts. **Nylon**, a polyamide, is valued for its high strength-to-weight ratio, abrasion resistance, and ability to withstand high temperatures. It is commonly used in textiles, gears, bearings, and other mechanical components. **Polystyrene (PS)**, known for its lightweight and insulating properties, is widely used in foam cups, packaging materials, and insulation. Understanding these properties is essential when considering the strongest glue to use on plastic. Different adhesives bond better with specific types of plastics due to their chemical composition. For example, cyanoacrylate (super glue) works well with many plastics but may not adhere as strongly to polyethylene or polypropylene due to their non-polar nature. In contrast, adhesives like epoxy or polyurethane may offer better bonding with these materials due to their ability to form strong chemical bonds. In summary, recognizing the distinct properties of common plastic materials such as polyethylene, polypropylene, PVC, PET, polycarbonate, ABS, nylon, and polystyrene is vital for choosing the right adhesive for your application. This knowledge ensures that the bond between the plastic and the adhesive is strong and durable, thereby enhancing the overall performance and longevity of the product. By understanding these types of plastics and their characteristics, you can make informed decisions about which glue will provide the best results for your specific needs.
Impact of Plastic Type on Adhesive Choice
When it comes to selecting the right adhesive for bonding plastic, the type of plastic in question plays a crucial role. Different plastics have unique surface properties, chemical compositions, and physical characteristics that can significantly impact the performance of adhesives. For instance, polyethylene and polypropylene, known as olefin plastics, are notoriously difficult to bond due to their low surface energy and non-polar nature. These plastics often require specialized adhesives or surface treatments such as corona or flame treatment to enhance their bondability. On the other hand, plastics like polycarbonate and ABS (Acrylonitrile Butadiene Styrene) have higher surface energies and can be bonded effectively with a wider range of adhesives, including cyanoacrylates, epoxies, and acrylics. Polyvinyl chloride (PVC) and polyurethane (PU) present another set of challenges due to their potential for plasticizer migration and moisture absorption, which can weaken the adhesive bond over time. In such cases, choosing an adhesive that is resistant to these factors is essential. For example, silicone-based adhesives are often preferred for bonding PVC and PU because they offer good flexibility and resistance to environmental factors. In contrast, engineering plastics like nylon and polycarbonate can be bonded using high-strength adhesives such as epoxies and polyurethanes. These adhesives provide strong mechanical properties and excellent durability, making them suitable for applications where high stress and impact resistance are required. Understanding the specific type of plastic you are working with allows you to make an informed decision about the most appropriate adhesive. For example, if you are working with a plastic that has a high degree of flexibility, such as TPU (Thermoplastic Polyurethane), you would need an adhesive that maintains its flexibility without compromising on strength. Conversely, rigid plastics like polycarbonate might require adhesives that offer high tensile strength and impact resistance. Moreover, environmental factors such as temperature, humidity, and exposure to chemicals must also be considered when selecting an adhesive for plastic bonding. Some adhesives may degrade under certain conditions, leading to a weakened bond or even complete failure. Therefore, it is critical to choose an adhesive that not only bonds well with the specific type of plastic but also withstands the environmental conditions in which the bonded assembly will operate. In summary, the impact of plastic type on adhesive choice cannot be overstated. Each type of plastic presents unique challenges and opportunities for bonding, and selecting the right adhesive requires a thorough understanding of these differences. By matching the adhesive to the specific properties and requirements of the plastic, you can ensure a strong, durable bond that meets your application needs effectively. This careful consideration is key to achieving successful outcomes in various industries ranging from automotive and aerospace to consumer goods and medical devices.
Evaluating Different Adhesives for Plastic
When evaluating different adhesives for plastic, it is crucial to consider the specific requirements of your application, including the need for quick bonds, high strength, and versatility. In this article, we delve into three prominent types of adhesives that cater to various needs. Cyanoacrylate, commonly known as Super Glue, excels in forming quick bonds, making it ideal for applications where speed is paramount. Epoxy adhesives, on the other hand, offer high strength and durability, making them suitable for heavy-duty applications. Acrylic adhesives provide a balance of versatility and flexibility, allowing them to adapt to a wide range of materials and conditions. Each of these adhesives has unique characteristics that make them stand out in different scenarios. By understanding the strengths and weaknesses of each, you can make informed decisions to ensure the best possible outcome for your project. Let's start by examining Cyanoacrylate (Super Glue) for Quick Bonds, a staple in many industries due to its rapid bonding capabilities.
Cyanoacrylate (Super Glue) for Quick Bonds
When evaluating different adhesives for plastic, Cyanoacrylate, commonly known as Super Glue, stands out for its exceptional bonding capabilities and rapid curing time. This versatile adhesive is particularly effective on a wide range of plastic materials, including ABS, PVC, and polycarbonate. Cyanoacrylate works by polymerizing in the presence of moisture, forming a strong and durable bond almost instantly. Its fast-acting nature makes it ideal for applications where time is of the essence, such as in industrial manufacturing, DIY projects, and emergency repairs. One of the key advantages of Cyanoacrylate is its ability to create high-strength bonds with minimal surface preparation. Unlike some other adhesives that require extensive cleaning or priming, Super Glue can often be applied directly to the plastic surfaces without any special treatment. This convenience, combined with its low viscosity, allows for precise application and penetration into small gaps and intricate details. However, it's important to note that Cyanoacrylate's performance can be influenced by environmental factors. For instance, high humidity can accelerate the curing process but may also lead to a weaker bond if the adhesive dries too quickly. Additionally, Cyanoacrylate is not suitable for all types of plastics; it may not adhere well to certain types like polyethylene or polypropylene due to their non-polar nature. Despite these limitations, Cyanoacrylate remains a top choice for many plastic bonding applications due to its ease of use and rapid results. It is also available in various formulations tailored to specific needs—such as flexible versions for impact resistance or low-odor variants for use in confined spaces. When used correctly and under appropriate conditions, Cyanoacrylate can provide bonds that are both strong and long-lasting, making it an indispensable tool in any adhesive arsenal. In summary, while evaluating different adhesives for plastic, Cyanoacrylate's unique combination of speed, strength, and ease of application makes it a compelling option. Its ability to form quick bonds on various plastic materials without extensive preparation underscores its value in both professional and amateur contexts. However, understanding its limitations and optimal usage conditions is crucial to achieving the best possible results with this powerful adhesive.
Epoxy Adhesives for High Strength and Durability
When evaluating different adhesives for plastic, epoxy adhesives stand out for their exceptional strength and durability. Epoxy adhesives are a class of two-part adhesives that consist of a resin and a hardener, which when mixed together, form a strong and rigid bond. This chemical reaction, known as curing, results in a highly cross-linked polymer structure that provides superior mechanical properties. Unlike other types of adhesives, epoxy adhesives offer excellent resistance to chemicals, heat, and impact, making them ideal for applications where high performance is critical. One of the key advantages of epoxy adhesives is their versatility. They can be formulated to bond a wide range of materials, including various types of plastics, metals, glass, and even ceramics. For plastic bonding specifically, epoxy adhesives can effectively join different types of plastics such as polyethylene, polypropylene, and polycarbonate. Their ability to wet the surface of these materials and form strong intermolecular bonds ensures a durable and long-lasting connection. The high strength of epoxy adhesives is due to their excellent tensile and shear strength. These properties make them suitable for load-bearing applications where the bonded parts are subjected to significant stress. Additionally, epoxy adhesives exhibit minimal shrinkage during curing, which reduces the risk of internal stresses that could compromise the integrity of the bond. In terms of durability, epoxy adhesives are highly resistant to environmental factors such as moisture, UV light, and extreme temperatures. This resistance helps maintain the bond's integrity over time, even in harsh conditions. Furthermore, epoxy adhesives are less prone to degradation from chemicals and solvents compared to other adhesive types, making them a reliable choice for industrial and automotive applications. Another significant benefit of epoxy adhesives is their ease of use. While they require mixing before application, modern formulations often include pre-measured kits or automated dispensing systems that simplify the process. Some epoxy adhesives also offer adjustable curing times, allowing users to tailor the application process to their specific needs. However, it's important to note that epoxy adhesives may have some limitations. They typically require a clean and dry surface for optimal bonding, which can be challenging in certain environments. Additionally, the curing process can be time-consuming compared to other fast-drying adhesives like cyanoacrylates or hot melts. In conclusion, epoxy adhesives are a top choice for applications requiring high strength and durability when bonding plastics. Their superior mechanical properties, versatility in material compatibility, and resistance to environmental factors make them an excellent option for demanding applications. While they may require more preparation and curing time than other adhesives, their performance and reliability justify the extra effort. For those seeking the strongest glue to use on plastic, epoxy adhesives are certainly worth considering due to their unparalleled strength and long-lasting bonds.
Acrylic Adhesives for Versatility and Flexibility
When evaluating different adhesives for plastic, acrylic adhesives stand out for their versatility and flexibility, making them a top choice for various applications. Acrylic adhesives are known for their excellent bonding strength, durability, and resistance to environmental factors such as temperature, humidity, and chemicals. These adhesives are formulated from a mixture of acrylic polymers and monomers, which cure quickly upon exposure to air or through the application of heat or UV light. This rapid curing process allows for efficient production and assembly in industrial settings. One of the key advantages of acrylic adhesives is their ability to bond a wide range of materials, including plastics, metals, glass, and even some elastomers. This versatility makes them particularly useful in industries where diverse materials are used in the same product or assembly. For instance, in automotive manufacturing, acrylic adhesives can be used to bond plastic components to metal frames or other materials, ensuring a strong and lasting bond. Acrylic adhesives also offer superior flexibility compared to other types of adhesives. They can absorb vibrations and stresses without compromising the bond, which is crucial in applications where the bonded parts may be subject to movement or impact. This flexibility is particularly beneficial in consumer electronics, where devices are often handled roughly and exposed to various environmental conditions. In addition to their mechanical properties, acrylic adhesives are often formulated to meet specific performance criteria. Some versions are designed with high impact resistance, while others may have enhanced UV stability or chemical resistance. This customization allows users to select an adhesive that precisely matches their application requirements. Another significant benefit of acrylic adhesives is their ease of use. They are available in various forms, including liquid, gel, and tape formats, making them suitable for different application methods. The liquid form can be applied using automated dispensing systems, while the tape format provides a convenient solution for manual applications. This adaptability ensures that users can choose the most appropriate form based on their production needs. From a safety and health perspective, many acrylic adhesives are formulated to be low in volatile organic compounds (VOCs) and free from hazardous materials like solvents and heavy metals. This makes them a safer choice for workers and aligns with increasingly stringent environmental regulations. In summary, acrylic adhesives offer a compelling combination of strength, versatility, and flexibility that makes them an ideal choice for bonding plastics and other materials. Their rapid curing times, excellent bonding capabilities across diverse materials, and adaptability to various application methods make them a go-to solution in many industries. Whether you are working in manufacturing, construction, or consumer goods production, acrylic adhesives provide a reliable and efficient bonding solution that meets high performance standards while ensuring safety and compliance with environmental regulations.
Application Considerations and Best Practices
When considering the application of adhesives, several critical factors must be taken into account to ensure optimal performance and longevity. The success of an adhesive bond is heavily influenced by three key areas: surface preparation, environmental factors, and the avoidance of common mistakes. Proper **Surface Preparation for Optimal Bonding** is essential as it directly impacts the strength and durability of the bond. Additionally, **Environmental Factors Affecting Adhesive Performance** must be carefully considered, as temperature, humidity, and exposure to chemicals can significantly alter the adhesive's properties. Lastly, understanding **Common Mistakes to Avoid When Using Adhesives on Plastic** can help prevent failures that might arise from incorrect application techniques or material incompatibilities. By addressing these considerations, users can ensure that their adhesive applications are both effective and reliable. To begin, it is crucial to focus on the foundational aspect of any successful adhesive application: **Surface Preparation for Optimal Bonding**.
Surface Preparation for Optimal Bonding
**Surface Preparation for Optimal Bonding** When it comes to achieving the strongest bond on plastic surfaces, surface preparation is paramount. The quality of the bond directly correlates with the cleanliness and condition of the surface. Here are some key considerations and best practices to ensure optimal bonding. First, **cleanliness** is crucial. Any contaminants such as dirt, oil, grease, or mold release agents can significantly weaken the bond. Use a mild detergent and water to clean the surface, followed by a solvent like acetone or isopropyl alcohol to remove any residual impurities. Ensure the surface is completely dry before proceeding. Next, **surface roughening** can enhance the bonding area. Lightly sanding the plastic surface with a fine-grit sandpaper (around 220-320 grit) increases the surface area available for bonding, allowing for a stronger mechanical interlock between the adhesive and the substrate. However, avoid over-sanding as it can create micro-scratches that may trap air bubbles or contaminants. **Chemical treatment** can also be beneficial for certain types of plastics. For example, polyethylene and polypropylene often require surface activation through methods like corona treatment or plasma treatment to introduce polar functional groups that improve adhesion. Additionally, **primers** can be used to further enhance adhesion. These specialized coatings create a strong chemical bond between the plastic surface and the adhesive, particularly useful for plastics that are inherently difficult to bond such as polyolefins. Another critical aspect is **environmental conditions** during bonding. Ensure that both the adhesive and the plastic surface are at room temperature and humidity levels recommended by the manufacturer. Extreme temperatures or high humidity can affect the curing process and overall strength of the bond. Finally, **handling techniques** play a significant role in maintaining surface integrity. Avoid touching the cleaned and prepared surfaces with bare hands as oils from skin can contaminate them. Use gloves or handle parts by edges to minimize contact. By meticulously following these steps—cleaning, roughening, chemically treating (if necessary), applying primers (if required), controlling environmental conditions, and careful handling—you can significantly improve the strength and durability of your plastic bonds. This thorough preparation ensures that your chosen adhesive performs optimally, leading to a robust and reliable bond that withstands various stresses and environmental factors.
Environmental Factors Affecting Adhesive Performance
When considering the application of adhesives on plastic surfaces, it is crucial to understand the environmental factors that can significantly impact adhesive performance. Temperature, humidity, exposure to UV light, and chemical contaminants are among the key environmental variables that can affect the bonding strength and durability of adhesives. **Temperature** plays a critical role in adhesive performance. Most adhesives have optimal temperature ranges for application and curing. Operating outside these ranges can lead to reduced bond strength or even adhesive failure. For instance, high temperatures can accelerate the curing process but may also cause the adhesive to degrade prematurely, while low temperatures can slow down curing, potentially resulting in a weaker bond. **Humidity** is another significant factor. High humidity levels can interfere with the curing process of certain adhesives, such as cyanoacrylates and epoxies, by introducing moisture that reacts with the adhesive components. This can lead to a weaker bond or the formation of bubbles within the adhesive layer. Conversely, very dry conditions may slow down the curing process of adhesives that rely on moisture for polymerization. **UV Light Exposure** can also degrade adhesives over time. Many adhesives are susceptible to ultraviolet radiation, which can break down their molecular structure, leading to a loss of bonding strength and flexibility. This is particularly relevant for outdoor applications where the adhesive may be exposed to direct sunlight. **Chemical Contaminants** present in the environment can also compromise adhesive performance. Solvents, oils, and other chemicals can weaken or dissolve certain types of adhesives. For example, exposure to fuels or cleaning agents can degrade the bond strength of some plastic adhesives. To mitigate these environmental impacts and ensure optimal adhesive performance on plastic surfaces, several best practices should be followed: 1. **Pre-treatment of Surfaces**: Cleaning and preparing the surfaces before applying the adhesive is essential to remove contaminants that could interfere with bonding. 2. **Selection of Adhesive**: Choose an adhesive that is specifically formulated for the environmental conditions in which it will be used. For example, select UV-resistant adhesives for outdoor applications. 3. **Controlled Application Conditions**: Apply adhesives within the recommended temperature and humidity ranges specified by the manufacturer. 4. **Proper Curing**: Ensure that the adhesive is allowed to cure under optimal conditions to achieve maximum bond strength. 5. **Regular Inspection**: Periodically inspect bonded areas for signs of degradation or failure due to environmental factors. By understanding and addressing these environmental factors, users can significantly enhance the reliability and longevity of adhesive bonds on plastic surfaces, ensuring that their applications meet the required standards of performance and durability.
Common Mistakes to Avoid When Using Adhesives on Plastic
When working with adhesives on plastic, it is crucial to avoid common mistakes that can compromise the strength and durability of the bond. One of the most significant errors is failing to properly prepare the surface. Plastic surfaces often have a low surface energy, which can hinder the adhesive's ability to form a strong bond. To mitigate this, ensure that the plastic is thoroughly cleaned and degreased to remove any contaminants or oils. Additionally, lightly abrading the surface can increase the surface area and improve adhesion. Another critical mistake is selecting the wrong type of adhesive for the specific plastic material. Different plastics have unique properties that require specific adhesives. For example, polyethylene and polypropylene are notoriously difficult to bond and may require specialized adhesives such as cyanoacrylate or two-component epoxies. On the other hand, plastics like ABS and PVC can often be bonded effectively with acrylic adhesives or hot melt adhesives. Always consult the manufacturer's recommendations and conduct compatibility tests before proceeding. Incorrect application techniques can also lead to suboptimal results. Applying too little adhesive may result in a weak bond, while applying too much can lead to excess adhesive oozing out and creating a mess. It is essential to follow the manufacturer's guidelines for application amounts and techniques. Furthermore, ensuring that the parts are properly aligned and clamped during the curing process is vital for achieving a strong and even bond. Temperature and environmental conditions also play a significant role in adhesive performance. Many adhesives have optimal temperature ranges for application and curing. Applying adhesives in extreme temperatures or exposing them to moisture before they are fully cured can significantly reduce their effectiveness. It is important to work in a controlled environment and allow the adhesive sufficient time to cure according to the manufacturer's instructions. Finally, neglecting to test the adhesive on a small, inconspicuous area first can lead to unexpected failures. This step helps ensure that the adhesive does not degrade the plastic or cause discoloration. By conducting a small-scale test, you can identify any potential issues before proceeding with the full application. By avoiding these common mistakes—proper surface preparation, selecting the right adhesive for the plastic type, correct application techniques, optimal environmental conditions, and preliminary testing—you can significantly enhance the strength and reliability of your plastic bonds. This attention to detail is crucial for achieving successful outcomes in various applications, from industrial manufacturing to DIY projects. By adhering to these best practices, you can ensure that your adhesive bonds are strong, durable, and long-lasting.