What Is Grease

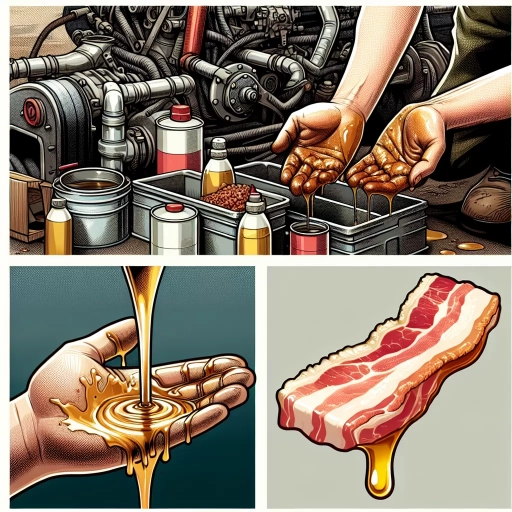
Grease is a ubiquitous substance that plays a critical role in various industrial, automotive, and everyday applications. Its importance cannot be overstated, as it serves as a vital lubricant, reducing friction and wear on moving parts. To fully understand the significance of grease, it is essential to delve into its definition and composition, which will be explored in the following section. Beyond its fundamental nature, grease has a wide range of applications and uses, from machinery maintenance to food processing, each highlighting its versatility and necessity. Additionally, the benefits of using grease, such as extended equipment life and reduced energy consumption, are substantial. However, these benefits are contingent upon proper maintenance practices, which will also be discussed. By examining the definition and composition of grease, we set the foundation for understanding its broader applications and the importance of its maintenance. This article will provide a comprehensive overview, starting with the core aspects of what constitutes grease.
Definition and Composition of Grease
Grease, a vital lubricant in various industrial and mechanical applications, is often misunderstood due to its complex composition and diverse types. To fully grasp the essence of grease, it is crucial to delve into its definition, chemical structure, and key properties. At its core, grease is a semi-solid lubricant composed of a thickener dispersed in a lubricating fluid, typically oil. This article will explore three critical aspects of grease: its chemical structure and components, the different types based on thickeners, and its key properties and characteristics. Understanding the chemical structure and components of grease is foundational, as it reveals the intricate balance between the thickener and the lubricating oil. This knowledge sets the stage for comprehending the various types of greases, each tailored for specific uses based on their thickeners. Finally, recognizing the key properties and characteristics of grease ensures optimal selection and application in diverse settings. By examining these facets, we can appreciate the versatility and importance of grease in modern technology. Let us begin by dissecting the chemical structure and components that underpin this essential lubricant.
Chemical Structure and Components
Chemical structure and components are crucial in understanding the definition and composition of grease. Grease, a semi-solid lubricant, is primarily composed of a base oil, thickener, and additives. The base oil, which can be mineral, synthetic, or bio-based, constitutes the majority of the grease and provides the primary lubricating properties. The thickener, typically a soap or non-soap material, is dispersed in the base oil to create a stable matrix that maintains the grease's semi-solid consistency. Common thickeners include lithium, calcium, and sodium soaps, as well as non-soap thickeners like polyurea and silica. The chemical structure of these components significantly influences the performance characteristics of the grease. For instance, lithium-based greases have a balanced combination of high and low temperature performance, making them versatile for various applications. Calcium-based greases are often used in water-resistant applications due to their hydrophilic nature. Sodium-based greases are typically used in high-temperature applications due to their excellent thermal stability. Additives play a critical role in enhancing specific properties of the grease. Anti-wear additives reduce friction and wear on moving parts, while extreme pressure (EP) additives protect against heavy loads and high pressures. Corrosion inhibitors prevent rust and corrosion, especially in environments exposed to moisture. Oxidation inhibitors extend the service life of the grease by preventing degradation from exposure to air and heat. Understanding the chemical structure and components of grease is essential for selecting the right type for specific applications. For example, in automotive applications, greases with high viscosity index and good low-temperature properties are preferred to ensure consistent lubrication across a wide range of temperatures. In industrial settings, greases with high load-carrying capacity and resistance to water and corrosion are often required. In summary, the chemical structure and components of grease—base oil, thickener, and additives—determine its physical and performance characteristics. These elements work together to provide the necessary lubrication, stability, and protection for various mechanical systems, making grease an indispensable material in both everyday and industrial contexts.
Types of Greases Based on Thickeners
Greases are semi-solid lubricants that consist of a lubricating fluid, typically oil, mixed with a thickener. The type of thickener used significantly influences the properties and applications of the grease. Here are the primary types of greases based on their thickeners: 1. **Lithium Grease**: This is one of the most common types, using lithium salts as thickeners. Lithium greases offer excellent balance between high and low temperature performance, making them versatile for various industrial and automotive applications. 2. **Calcium Grease**: Thickeners in calcium greases are calcium soaps. These greases are known for their water resistance and are often used in applications where moisture is present, such as in marine environments or construction equipment. 3. **Sodium Grease**: Sodium soaps serve as thickeners in sodium greases. They have high melting points and are typically used in high-temperature applications like in the textile and paper industries. 4. **Aluminum Complex Grease**: These greases use aluminum complex soaps as thickeners. They offer superior high-temperature stability and are often used in severe operating conditions, such as in aerospace and military applications. 5. **Polyurea Grease**: Polyurea greases are thickeners made from polyurea polymers. They provide excellent mechanical stability, resistance to water and chemicals, and are commonly used in heavy-duty industrial machinery and automotive components. 6. **Silicone Grease**: Silicone oils combined with silica or other thickeners form silicone greases. These are known for their extreme temperature stability and are used in applications requiring non-reactive lubrication, such as in electrical and aerospace industries. 7. **Bentonite Grease**: Bentonite clays act as thickeners in these greases. They are often used in applications where the grease needs to be non-melting and have good low-temperature properties, such as in some automotive and industrial bearings. 8. **Polyethylene Grease**: Polyethylene waxes or polymers are used as thickeners in these greases. They offer good mechanical stability and are used in specialized applications where other types of greases may not perform adequately. Each type of grease has its unique characteristics, advantages, and specific uses, making the choice of grease dependent on the operational conditions and requirements of the application. Understanding the different types of thickeners and their properties is crucial for selecting the right grease to ensure optimal performance and longevity of machinery and equipment.
Key Properties and Characteristics
Grease, a semi-solid lubricant, exhibits several key properties and characteristics that make it an essential component in various industrial and mechanical applications. **Viscosity** is one of the most critical properties, as it determines the grease's ability to flow and lubricate effectively. Greases are typically classified into different grades based on their viscosity, with higher viscosity greases being thicker and more resistant to flow, making them suitable for heavy-duty applications. **Thickener Type** is another crucial characteristic; common thickeners include soaps (such as lithium, calcium, and sodium), polyureas, and clays. Each type of thickener influences the grease's performance under different conditions, such as temperature, load, and moisture. **Temperature Range** is a vital property, as greases have specific operating temperatures beyond which they may degrade or lose their lubricating properties. For instance, lithium-based greases generally have a wider temperature range compared to calcium-based greases. **Water Resistance** is also an important characteristic, especially in applications where the grease may be exposed to moisture or water. Some greases, like those thickened with polyurea or lithium, offer better water resistance than others. **Load-Carrying Capacity** refers to the grease's ability to withstand pressure and load without breaking down. This property is crucial in high-stress applications such as gears and bearings. **Corrosion Protection** is another significant characteristic; many greases contain additives that help protect metal surfaces from corrosion. **Oxidation Stability** ensures that the grease does not degrade over time due to exposure to air, which can lead to the formation of harmful by-products. In addition, **Drop Point** is a key indicator of a grease's thermal stability; it is the temperature at which the grease begins to melt and lose its shape. A higher drop point generally indicates better performance at elevated temperatures. **Worked Penetration** measures how much the grease softens when it is worked or agitated, which affects its consistency and usability in different scenarios. The **Base Oil** used in the composition of grease also plays a significant role in determining its overall performance. Common base oils include mineral oils, synthetic oils, and bio-based oils, each offering different levels of lubricity, viscosity index, and compatibility with various materials. The choice of base oil can significantly impact the grease's performance in terms of low-temperature flowability, high-temperature stability, and compatibility with seals and other materials. Understanding these key properties and characteristics allows users to select the appropriate grease for specific applications, ensuring optimal performance, longevity, and reliability of machinery and equipment. By matching the grease's properties with the operational conditions, users can prevent premature wear, reduce maintenance costs, and enhance overall system efficiency.
Applications and Uses of Grease
Grease, a semi-solid lubricant, plays a crucial role in various industries due to its unique properties and versatility. This article delves into the diverse applications and uses of grease, highlighting its significance in three key sectors. First, we explore the industrial applications of grease in machinery and equipment, where it ensures smooth operation and longevity of mechanical components. Next, we examine the automotive uses of grease in vehicles and parts, focusing on how it enhances performance and durability. Finally, we discuss the specialized uses of grease in aerospace and marine industries, where its high-performance characteristics are essential for critical operations. By understanding these applications, we can appreciate the multifaceted role of grease in maintaining efficiency and reliability across different fields. Let's begin by examining the industrial applications of grease in machinery and equipment, a cornerstone of modern manufacturing and production processes.
Industrial Applications in Machinery and Equipment
Industrial applications in machinery and equipment are pivotal in ensuring the smooth operation, longevity, and efficiency of various mechanical systems. Grease, a semi-solid lubricant, plays a crucial role in these applications due to its unique properties. In industrial settings, grease is used to lubricate bearings, gears, and other moving parts that are subject to high loads, temperatures, and vibrations. For instance, in the manufacturing sector, grease is applied to conveyor belts and machinery to reduce friction and wear, thereby increasing productivity and minimizing downtime. In the automotive industry, grease is essential for lubricating wheel bearings, universal joints, and other components that require consistent lubrication under varying conditions. Additionally, in construction equipment such as cranes and excavators, grease helps to protect against corrosion and wear on critical components like pivot pins and bushings. The use of grease also extends to the food processing industry where it must meet stringent hygiene standards; here, food-grade greases are used to ensure compliance with safety regulations while maintaining equipment performance. Furthermore, in the aerospace sector, specialized greases are formulated to withstand extreme temperatures and pressures, ensuring the reliability of aircraft components. Overall, the versatility and performance of grease make it an indispensable component in maintaining the integrity and functionality of industrial machinery and equipment across diverse sectors.
Automotive Uses in Vehicles and Parts
In the automotive industry, grease plays a crucial role in maintaining the performance and longevity of vehicles. It is extensively used in various components to reduce friction, prevent wear and tear, and protect against corrosion. One of the primary applications of grease is in the lubrication of moving parts such as bearings, joints, and hinges. For instance, wheel bearings and suspension components rely on grease to ensure smooth operation and durability. Grease also finds its way into the chassis and steering systems, where it helps in reducing friction between metal surfaces, thereby enhancing the overall driving experience. Additionally, grease is used in the lubrication of engine components like valve train mechanisms and timing chains. It provides a protective barrier against extreme temperatures and contaminants, which can otherwise lead to premature wear. In transmissions and gearboxes, grease helps in reducing noise and vibration while ensuring efficient gear shifting. Furthermore, it is applied to door hinges, locks, and other mechanical parts to maintain their functionality over time. The use of grease extends beyond mechanical components; it also plays a significant role in protecting electrical connections from moisture and corrosion. Battery terminals, for example, are often treated with a specialized type of grease to prevent rust and ensure reliable electrical conductivity. Moreover, some types of grease are designed for specific applications such as high-temperature environments or extreme weather conditions, making them versatile tools for vehicle maintenance. In terms of vehicle parts, grease is an essential component in the manufacturing process. It is used as a release agent during the production of rubber seals and gaskets, ensuring they do not stick to molds. Grease also serves as a protective coating for metal parts during storage and transportation, preventing rust and damage. Overall, the automotive industry relies heavily on grease for its multifaceted benefits. From enhancing performance and longevity to providing protection against environmental factors, grease is an indispensable element in both the maintenance and manufacturing of vehicles and their parts. Its widespread use underscores its importance as a critical component in ensuring the smooth operation and extended lifespan of automotive systems.
Specialized Uses in Aerospace and Marine Industries
In the aerospace and marine industries, specialized greases play a critical role in ensuring the reliability and longevity of equipment under extreme conditions. In aerospace, these greases are formulated to withstand the harsh environments encountered during flight, such as high temperatures, low pressures, and exposure to fuels and other chemicals. For instance, synthetic greases like polyalphaolefin (PAO) and perfluoropolyether (PFPE) are commonly used due to their excellent thermal stability and resistance to degradation. These greases lubricate critical components like bearings, gears, and actuators in aircraft engines, landing gear systems, and control surfaces, thereby maintaining smooth operation and preventing wear and tear. In the marine industry, specialized greases are designed to combat the corrosive effects of seawater and the high loads associated with marine equipment. Here, greases with high water resistance and anti-corrosion properties are essential. For example, lithium-based greases with additives that inhibit rust and corrosion are widely used on ship propellers, rudder bearings, and other submerged components. Additionally, silicone-based greases offer excellent resistance to seawater and are often applied in stern tubes and other areas where conventional greases might fail. These marine-specific greases help in reducing maintenance costs by extending the service life of equipment and minimizing downtime due to corrosion or mechanical failure. Both industries also benefit from the use of biodegradable greases, which are becoming increasingly important due to environmental regulations. These eco-friendly greases are made from renewable resources and are designed to break down naturally without harming aquatic life or ecosystems. This is particularly significant for marine applications where accidental spills or leaks could have detrimental environmental impacts. Overall, the specialized uses of grease in aerospace and marine industries highlight their versatility and critical importance in maintaining operational efficiency and safety in these demanding sectors. By selecting the right type of grease for specific applications, these industries can ensure optimal performance, reduce maintenance needs, and comply with stringent environmental standards.
Benefits and Maintenance of Grease
Grease is a versatile and essential component in various mechanical systems, offering a range of benefits that enhance performance, longevity, and overall efficiency. This article delves into the key advantages and maintenance practices associated with grease, focusing on three critical aspects: lubrication and wear protection, sealing and corrosion prevention, and proper application and maintenance techniques. By understanding these elements, users can optimize the use of grease to reduce friction, protect against wear and tear, and prevent corrosion. Effective lubrication is crucial for minimizing mechanical wear, which in turn extends the lifespan of machinery. Additionally, grease acts as a sealant to prevent contaminants from entering sensitive areas, while also providing a protective barrier against corrosive elements. Proper application and maintenance are equally important to ensure these benefits are fully realized. In the following sections, we will explore each of these aspects in detail, starting with the fundamental role of grease in providing lubrication and wear protection.
Lubrication and Wear Protection Benefits
Lubrication and wear protection are paramount benefits of grease, significantly enhancing the performance and longevity of mechanical systems. Grease acts as a barrier between moving parts, reducing friction and preventing direct metal-to-metal contact. This minimizes wear and tear on components, thereby extending their lifespan and reducing the need for frequent replacements. By maintaining a consistent film of lubricant, grease ensures smooth operation even under extreme temperatures and pressures, which is crucial for machinery in harsh environments. Additionally, grease helps to seal out contaminants such as dust and moisture, protecting the system from corrosion and damage caused by external factors. This sealing effect also aids in maintaining the integrity of the lubricant itself, preventing it from being washed away or degraded over time. Furthermore, many greases contain additives that provide additional benefits like anti-wear properties, corrosion inhibitors, and extreme pressure (EP) protection, making them highly versatile for various applications. Regular maintenance involving the application of grease can significantly reduce downtime due to mechanical failures, lower maintenance costs, and improve overall system efficiency. In summary, the lubrication and wear protection provided by grease are essential for maintaining optimal performance, extending equipment life, and ensuring reliable operation across diverse industrial and automotive applications.
Sealing and Corrosion Prevention
Sealing and corrosion prevention are critical aspects of maintaining equipment and machinery, and grease plays a pivotal role in these processes. Grease, a semi-solid lubricant, acts as a barrier between moving parts and the environment, preventing the ingress of contaminants such as dust, water, and chemicals. This sealing action not only reduces friction but also shields components from corrosive substances that could degrade metal surfaces. By forming a protective film on metal surfaces, grease inhibits the reaction between metals and corrosive agents like moisture and acids, thereby extending the lifespan of equipment. In environments where machinery is exposed to harsh conditions such as high humidity, saltwater, or chemical exposure, the use of grease with corrosion-inhibiting properties is particularly beneficial. These specialized greases contain additives that enhance their protective capabilities, ensuring that even in adverse conditions, the metal surfaces remain intact. For instance, in marine applications where equipment is frequently exposed to seawater, using a grease with anti-corrosion additives helps prevent rust and pitting on metal components. Regular maintenance involving the application of grease is essential for maintaining this protective barrier. Over time, grease can break down due to heat, load, or contamination, losing its effectiveness. Therefore, periodic reapplication ensures that the sealing and corrosion-preventing properties are consistently maintained. This proactive approach not only prevents premature wear but also reduces downtime and maintenance costs associated with repairing or replacing damaged components. Moreover, selecting the right type of grease for specific applications is crucial for optimal sealing and corrosion prevention. Different greases have varying viscosities, temperature ranges, and additive packages tailored for different environments and loads. For example, in high-temperature applications such as industrial bearings or automotive engines, a high-temperature grease with excellent thermal stability is necessary to maintain its protective film without degrading. In summary, grease is an indispensable tool in sealing and corrosion prevention due to its ability to form a protective barrier on metal surfaces. Regular maintenance involving the application of appropriate greases ensures that equipment remains in good condition even under harsh operating conditions. By understanding the benefits of grease in these contexts and adhering to proper maintenance schedules, operators can significantly extend the lifespan of their machinery while minimizing maintenance costs.
Proper Application and Maintenance Techniques
Proper application and maintenance techniques are crucial for maximizing the benefits of grease in various industrial and mechanical applications. To ensure optimal performance, it is essential to select the right type of grease for the specific task at hand. This involves considering factors such as operating temperature, load conditions, and environmental exposure. For instance, high-temperature greases are formulated to maintain their lubricating properties in extreme heat, while water-resistant greases are ideal for applications where moisture is present. Once the appropriate grease is chosen, correct application methods must be followed. This typically involves cleaning the surface thoroughly to remove any dirt or old lubricant residue, which can contaminate the new grease and reduce its effectiveness. The recommended amount of grease should be applied evenly, avoiding over-greasing which can lead to waste and potential contamination of surrounding components. In some cases, specialized tools like grease guns or pumps may be necessary to ensure precise application. Regular maintenance is also vital to extend the life of both the grease and the equipment it lubricates. This includes periodic inspections to check for signs of wear or degradation, such as discoloration or separation of the grease. Re-lubrication schedules should be adhered to, taking into account factors like usage intensity and environmental conditions. Additionally, keeping equipment clean and free from debris helps prevent contamination of the grease, thereby maintaining its lubricating properties. Proper storage and handling of grease are also important aspects of maintenance. Grease should be stored in a cool, dry place away from direct sunlight and moisture to prevent degradation. Containers should be tightly sealed when not in use to prevent contamination and spoilage. Following these guidelines ensures that the grease remains effective over its intended lifespan, providing consistent lubrication and protection against wear and tear. In summary, proper application and maintenance techniques are essential for leveraging the full benefits of grease. By selecting the right type of grease, applying it correctly, performing regular maintenance checks, and storing it properly, users can optimize equipment performance, extend component life, and reduce downtime due to lubrication-related issues. These practices not only enhance operational efficiency but also contribute to cost savings by minimizing the need for frequent repairs and replacements.