What Is Flux In Soldering

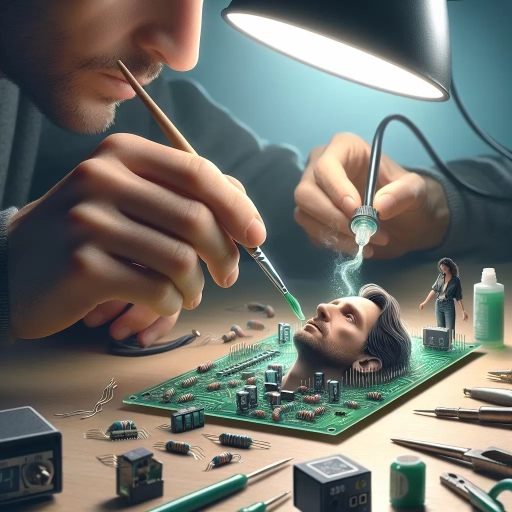
In the realm of soldering, flux plays a crucial role in ensuring successful and reliable joints. This article delves into the essential aspects of flux, starting with **Understanding the Basics of Flux in Soldering**, where we explore its fundamental properties and types. We then examine **The Role of Flux in the Soldering Process**, highlighting how it facilitates the removal of oxides, improves wetting, and enhances the overall quality of solder joints. Finally, **Practical Applications and Considerations of Flux** will discuss real-world scenarios, including the selection of appropriate fluxes for different materials and the importance of proper handling and safety measures. By grasping these key concepts, readers will gain a comprehensive understanding of flux's significance in soldering. Let's begin by understanding the basics of flux in soldering.
Understanding the Basics of Flux in Soldering
Understanding the basics of flux in soldering is crucial for achieving high-quality joints and ensuring the reliability of electronic and mechanical assemblies. Flux plays a pivotal role in the soldering process, and its proper use can significantly impact the outcome. This article delves into three key aspects of flux: its definition and purpose, the various types used in soldering, and its chemical composition. First, we will explore the definition and purpose of flux, which is essential for removing oxidation and promoting a clean, strong bond between the solder and the metal surfaces. Next, we will examine the different types of flux available, each with its own set of characteristics and applications. Finally, we will dissect the chemical composition of flux, understanding how its components contribute to its effectiveness. By grasping these fundamental concepts, individuals can better appreciate the importance of flux in soldering and make informed decisions about its use. Let's begin by defining what flux is and its critical role in the soldering process.
Definition and Purpose of Flux
**Definition and Purpose of Flux** In the context of soldering, flux is a substance applied to the surfaces of metals to be joined. Its primary purpose is to remove oxidation and other contaminants, ensuring a clean and smooth soldering process. Flux works by chemically reducing the oxides on metal surfaces, thereby preventing new oxides from forming during the heating process. This action facilitates better wetting and spreading of the solder, resulting in stronger and more reliable joints. The use of flux is crucial because metal oxides can significantly impede the soldering process. Oxides act as barriers that prevent the solder from adhering properly to the metal surfaces, leading to weak or incomplete joints. By removing these oxides, flux enables the solder to flow freely and bond securely with the metals being joined. There are different types of fluxes available, each suited for specific soldering applications. For example, rosin-based fluxes are commonly used in electronics due to their mild action and ease of removal after soldering. Acidic fluxes, on the other hand, are more aggressive and often used for soldering thicker materials like copper pipes. No-clean fluxes are designed to leave minimal residue, making them ideal for applications where cleaning is difficult or undesirable. In addition to its primary function of removing oxides, flux also helps in lowering the melting point of the solder by reducing surface tension. This makes it easier to achieve a uniform and consistent solder joint without overheating the components. Overall, the definition and purpose of flux in soldering revolve around ensuring a clean, efficient, and reliable joining process. By effectively removing contaminants and promoting good wetting and spreading of the solder, flux plays a vital role in achieving high-quality solder joints that are essential for the integrity and performance of electronic devices and other soldered assemblies.
Types of Flux Used in Soldering
In the realm of soldering, flux plays a crucial role in ensuring a strong and reliable bond between metal components. There are several types of flux, each designed to cater to specific soldering needs and environments. **Rosin-based flux**, one of the most traditional and widely used, is derived from pine sap and is known for its effectiveness in removing oxidation from metal surfaces. It is particularly suitable for hand soldering and is often used in electronics assembly due to its relatively low cost and ease of use. **No-clean flux** is another popular type, designed to leave minimal residue after soldering. This makes it ideal for applications where cleaning the soldered area is impractical or undesirable, such as in high-volume production lines. No-clean fluxes are formulated to be less active than rosin-based fluxes but still provide adequate protection against oxidation. **Water-soluble flux**, as the name suggests, can be easily cleaned with water after soldering. This type is often used in situations where cleanliness is paramount, such as in medical devices or aerospace applications. Water-soluble fluxes are more active than no-clean fluxes and offer better wetting properties but require thorough cleaning to prevent any residue from causing electrical issues. **Acid-core flux**, typically used in plumbing and other non-electronic soldering applications, contains strong acids that aggressively remove oxidation. However, due to its corrosive nature, it is not suitable for electronic components and requires careful handling. **Organic acid fluxes**, such as those based on citric or lactic acid, offer a balance between effectiveness and safety. They are less corrosive than acid-core fluxes but still provide good oxidation removal properties. These fluxes are often used in precision soldering tasks where a clean environment is necessary. **Inorganic fluxes**, including those based on zinc chloride or ammonium chloride, are highly active and used in specialized applications like brazing or welding. They are not commonly used in electronic soldering due to their high reactivity and potential for leaving harmful residues. Understanding the different types of flux available allows soldering professionals to select the most appropriate one for their specific task, ensuring optimal results and minimizing potential issues such as corrosion or electrical malfunctions. Each type of flux has its unique characteristics, advantages, and limitations, making it essential to choose the right one to achieve high-quality solder joints.
Chemical Composition of Flux
The chemical composition of flux is a critical aspect of its role in soldering, as it directly influences the effectiveness and quality of the soldering process. Fluxes are typically formulated from a combination of ingredients, each serving a specific purpose. The primary components include activators, solvents, and thickeners. **Activators** are the most crucial part of the flux composition. These are usually acidic or alkaline substances that help remove oxidation from the metal surfaces to be soldered. Common activators include rosin (a natural resin derived from pine trees), organic acids like citric acid or lactic acid, and inorganic acids such as hydrochloric acid or phosphoric acid. Rosin-based fluxes are widely used due to their mild action and effectiveness at relatively low temperatures. **Solvents** play a key role in dissolving and carrying the activators to the surface of the metals being soldered. These can be volatile organic compounds (VOCs) like isopropyl alcohol, acetone, or ethyl acetate. The solvent helps in spreading the flux evenly over the surface and evaporates during the heating process, leaving behind a residue that continues to protect the metal from re-oxidation until the soldering is complete. **Thickeners** are added to adjust the viscosity of the flux, making it easier to apply and maintain on vertical surfaces or in intricate joints. Thickeners can include polymers, waxes, or other inert materials that do not interfere with the chemical properties of the activators. In addition to these primary components, some fluxes may contain **fillers** or **inhibitors**. Fillers are inert materials that help in maintaining a consistent viscosity and improving the flux's shelf life. Inhibitors are substances that prevent the flux from reacting too aggressively with certain metals or components, thereby preventing damage to sensitive parts. The specific chemical composition of a flux can vary significantly depending on its intended application. For example, **no-clean fluxes** are designed to leave minimal residue after soldering and are often used in electronics where cleanliness is paramount. **Water-soluble fluxes**, on the other hand, are used when thorough cleaning is required post-soldering and typically contain more aggressive activators. Understanding the chemical composition of flux is essential for selecting the right type for a particular soldering task. The correct choice ensures optimal performance, minimizes defects, and maintains the integrity of the solder joint. By knowing what each component does, users can better manage their soldering processes and achieve high-quality results consistently.
The Role of Flux in the Soldering Process
In the soldering process, flux plays a crucial role that significantly impacts the quality and reliability of the joints formed. This article delves into the multifaceted contributions of flux, highlighting three key aspects: removing oxidation and contamination, improving wetting and flow of solder, and enhancing joint strength and reliability. By understanding these functions, one can appreciate the importance of flux in ensuring that soldered connections are robust and durable. Flux acts as a cleaning agent, removing oxidation and contamination from metal surfaces, which is essential for creating a strong bond. It also facilitates better wetting and flow of solder, allowing it to spread evenly and fill gaps effectively. Finally, flux helps in enhancing the strength and reliability of the joint by promoting a clean and stable environment for the soldering process. This article will explore each of these roles in detail, starting with the critical task of removing oxidation and contamination.
Removing Oxidation and Contamination
Removing oxidation and contamination is a critical step in the soldering process, and it is here that flux plays its most pivotal role. Oxidation occurs when metals react with oxygen, forming a layer of oxide that can prevent the formation of a strong bond between the solder and the metal surfaces. Contamination, whether from dirt, grease, or other substances, can also hinder the soldering process by creating barriers that prevent the solder from wetting and adhering properly to the metal surfaces. Flux, by its nature, is designed to address these issues directly. When applied to the metal surfaces, flux melts and spreads evenly, covering the areas where soldering will take place. As it melts, flux releases gases that help to displace oxygen from the immediate environment, thereby preventing further oxidation. Simultaneously, the flux chemically reacts with any existing oxides on the metal surfaces, breaking them down and removing them. This process is known as reduction and is essential for exposing clean metal surfaces that are ready for soldering. In addition to removing oxidation, flux also helps to clean the metal surfaces by dissolving and removing contaminants such as dirt, grease, and other impurities. This ensures that the solder can wet and adhere uniformly to the cleaned surfaces, resulting in a strong and reliable bond. The ability of flux to remove both oxidation and contamination makes it an indispensable component of the soldering process. Different types of fluxes are available, each with its own strengths and applications. For example, rosin-based fluxes are commonly used in electronics soldering due to their mild action and low residue left behind. Acidic fluxes, on the other hand, are more aggressive and are often used for soldering thicker materials or in situations where heavy oxidation is present. Regardless of the type, the primary function of flux remains consistent: to ensure that the metal surfaces are clean and free from oxidation and contamination, thereby facilitating a successful soldering operation. In summary, removing oxidation and contamination is crucial for achieving high-quality solder joints, and flux is the key tool in this process. By displacing oxygen, breaking down existing oxides, and cleaning metal surfaces of contaminants, flux enables the solder to form strong bonds with the metal surfaces. This underscores the importance of flux in ensuring reliable and durable solder joints in various applications ranging from electronics to heavy-duty industrial use.
Improving Wetting and Flow of Solder
Improving the wetting and flow of solder is crucial for achieving high-quality solder joints, and this is where flux plays a pivotal role. Flux is a substance applied to the surfaces to be soldered, which helps in removing oxidation and other contaminants, thereby enhancing the wetting properties of the solder. When flux is applied, it melts at a lower temperature than the solder, creating a protective atmosphere that prevents re-oxidation of the metal surfaces. This allows the solder to flow more smoothly and evenly, ensuring strong and reliable bonds. The effectiveness of flux in improving wetting and flow can be attributed to its ability to reduce surface tension and lower the melting point of the solder slightly. By breaking down oxides and other impurities, flux enables the solder to spread uniformly across the joint area, filling gaps and creating a robust mechanical connection. Additionally, flux helps in reducing the thermal energy required for soldering, which can prevent overheating and damage to sensitive components. Different types of fluxes are available, each tailored to specific soldering applications. For instance, rosin-based fluxes are commonly used in electronics due to their mild properties and effectiveness in removing light oxidation. However, for more challenging soldering tasks involving heavily oxidized or contaminated surfaces, stronger fluxes like acid-core or no-clean fluxes may be necessary. The choice of flux depends on the materials being soldered and the desired level of cleanliness post-soldering. In practice, proper application and removal of flux are essential for optimal results. Excessive flux can leave residues that may interfere with electrical performance or cause corrosion over time. Therefore, it is important to use the right amount of flux and ensure thorough cleaning after the soldering process is complete. Modern soldering techniques often incorporate fluxes that are designed to be residue-free or easily removable, making post-soldering cleaning more efficient. In summary, improving the wetting and flow of solder is fundamentally linked to the role of flux in the soldering process. By removing oxidation, reducing surface tension, and creating a conducive environment for solder flow, flux ensures that solder joints are strong, reliable, and free from defects. The appropriate selection and application of flux are critical steps in achieving high-quality soldering outcomes across various industries.
Enhancing Joint Strength and Reliability
Enhancing joint strength and reliability is a critical aspect of the soldering process, and flux plays a pivotal role in achieving this goal. Flux is a substance applied to the surfaces of metals to be joined, and its primary function is to remove oxidation and other contaminants, ensuring a clean and stable environment for the solder to flow smoothly. By eliminating these impurities, flux facilitates better wetting of the solder on the metal surfaces, which is essential for forming strong and reliable joints. The presence of flux significantly improves the mechanical properties of solder joints by promoting uniform heating and cooling, thereby reducing thermal stresses that could lead to joint failure. Additionally, flux helps in achieving a consistent solder flow, which minimizes the formation of voids or porosity within the joint. These voids can act as stress concentrators and weaken the joint over time. Moreover, flux aids in reducing the surface tension of the molten solder, allowing it to penetrate more easily into the gap between the components being joined. This enhanced penetration ensures a stronger bond between the solder and the base metals, resulting in higher joint strength and better electrical conductivity. In terms of reliability, flux also helps in preventing re-oxidation during the soldering process. By maintaining a protective layer over the metal surfaces until the solder solidifies, flux ensures that no new oxides form that could compromise the integrity of the joint. This is particularly important in applications where joints are subjected to environmental stresses such as temperature fluctuations or exposure to corrosive substances. Overall, the use of flux in soldering is indispensable for enhancing joint strength and reliability. It not only improves the quality of the solder joints but also ensures that they remain durable and functional over their intended lifespan. By understanding and leveraging the role of flux effectively, engineers and technicians can produce high-quality soldered connections that meet stringent performance standards across various industries.
Practical Applications and Considerations of Flux
When delving into the practical applications and considerations of flux, it is crucial to approach the subject with a comprehensive understanding of several key aspects. First, selecting the right flux for your project is paramount, as different types of fluxes are suited to various materials and processes. This involves understanding the chemical properties and compatibility of the flux with the materials being used. Second, mastering application methods and techniques is essential for achieving optimal results, whether you are working with soldering, brazing, or other joining processes. Finally, safety precautions and environmental impact must be carefully considered to ensure that the use of flux does not pose risks to health or the environment. By focusing on these critical areas, practitioners can ensure that their use of flux is both effective and responsible. In this article, we will explore each of these considerations in detail, starting with the fundamental step of selecting the right flux for your project. This initial decision sets the stage for successful application and safe handling, making it a critical component of any project involving flux.
Selecting the Right Flux for Your Project
Selecting the right flux for your soldering project is crucial for achieving high-quality joints and ensuring the longevity of your work. Here are the key considerations to guide your choice: 1. **Type of Flux**: There are several types of fluxes, including rosin-based, acid-core, no-clean, and water-soluble. Rosin-based fluxes are commonly used for general-purpose soldering and are suitable for most electronics. Acid-core fluxes are more aggressive and used for heavy-duty applications like plumbing or automotive work. No-clean fluxes leave minimal residue and are ideal for sensitive electronics where cleaning is not feasible. Water-soluble fluxes are easy to clean but may leave residues if not properly cleaned. 2. **Application Temperature**: The melting point of the solder and the temperature at which the flux becomes active are critical. Ensure the flux activates at a temperature lower than the solder's melting point to facilitate smooth solder flow. 3. **Surface Preparation**: The cleanliness of the surfaces to be soldered affects flux performance. A clean surface ensures better wetting and stronger bonds. Choose a flux that can handle minor oxidation or contamination if perfect cleanliness is not achievable. 4. **Material Compatibility**: Different materials react differently to various fluxes. For example, some fluxes may not be suitable for aluminum or stainless steel due to their reactivity. Always check compatibility before selecting a flux. 5. **Environmental Considerations**: If your project will be exposed to harsh environments (e.g., high humidity, extreme temperatures), choose a flux that provides good protection against corrosion and oxidation. 6. **Regulatory Compliance**: Ensure the flux you select complies with relevant regulations such as RoHS (Restriction of Hazardous Substances) or other local environmental standards. 7. **Ease of Use and Cleanup**: Consider the ease of application and cleanup when choosing a flux. No-clean and water-soluble fluxes offer different advantages in this regard, depending on your specific needs. 8. **Cost and Availability**: Balance the cost of the flux with its performance and availability. High-quality fluxes may be more expensive but offer better results and reliability. By carefully evaluating these factors, you can select the right flux for your project, ensuring strong, reliable solder joints and maintaining the integrity of your work over time. This thoughtful approach will help you avoid common pitfalls such as poor wetting, weak bonds, or unwanted residues that can compromise the quality of your soldering work.
Application Methods and Techniques
When it comes to the practical applications and considerations of flux in soldering, understanding the various application methods and techniques is crucial for achieving high-quality solder joints. Flux application methods can significantly impact the efficiency, reliability, and overall quality of the soldering process. Here are some key techniques: 1. **Manual Application**: This involves applying flux directly to the components or joints using a brush, swab, or syringe. It allows for precise control but can be time-consuming and labor-intensive, making it less suitable for high-volume production. 2. **Wave Soldering**: In this method, the printed circuit board (PCB) is passed over a wave of molten solder, and flux is applied before the board enters the solder wave. This technique is widely used in mass production due to its efficiency and consistency. 3. **Selective Soldering**: This method involves applying flux only to specific areas of the PCB where soldering is required. It is particularly useful for mixed-technology boards that combine through-hole and surface-mount components. 4. **Reflow Soldering**: Here, flux is often integrated into the solder paste or pre-forms used in surface-mount technology (SMT). The flux helps in removing oxidation during the reflow process, ensuring strong bonds between components and the PCB. 5. **Foam Fluxing**: This technique uses a foam applicator to apply flux to the PCB. It is effective for cleaning and preparing surfaces before soldering but may leave residues that need to be cleaned afterward. 6. **Spray Fluxing**: Flux can be sprayed onto the PCB using aerosol cans or automated systems. This method is quick and covers large areas efficiently but requires careful control to avoid over-application. 7. **No-Clean Fluxes**: These are designed to leave minimal residues after soldering, reducing the need for post-solder cleaning processes. However, they may not be as effective at removing oxidation as other types of fluxes. 8. **Automated Flux Application Systems**: These systems use precision dispensers or jets to apply flux exactly where needed, enhancing accuracy and reducing waste. They are ideal for high-volume manufacturing environments where consistency is paramount. Each application method has its own set of advantages and considerations. For instance, manual application offers precision but lacks scalability, while automated systems provide efficiency but require significant initial investment. The choice of technique depends on factors such as production volume, component type, and desired level of quality control. By selecting the appropriate flux application method, manufacturers can optimize their soldering processes to achieve reliable and durable joints, which are essential for the performance and longevity of electronic devices.
Safety Precautions and Environmental Impact
When discussing the practical applications and considerations of flux in soldering, it is crucial to emphasize the importance of safety precautions and environmental impact. Flux, a substance used to promote the flow of solder by removing oxidation from metal surfaces, can pose significant health and environmental risks if not handled properly. **Safety Precautions:** 1. **Personal Protective Equipment (PPE):** Always wear protective gear such as gloves, safety glasses, and a face mask to prevent skin contact and inhalation of fumes. 2. **Ventilation:** Ensure good ventilation in the workspace to avoid inhaling toxic fumes emitted during the soldering process. 3. **Fire Safety:** Keep flammable materials away from the soldering area, as flux can ignite at high temperatures. 4. **Chemical Handling:** Handle flux carefully to avoid spills and skin contact; wash hands thoroughly after use. **Environmental Impact:** 1. **Waste Disposal:** Dispose of used flux and soldering waste according to local regulations to prevent contamination of soil and water. 2. **Air Pollution:** Use fume extractors or ventilation systems to minimize the release of harmful fumes into the atmosphere. 3. **Chemical Usage:** Opt for environmentally friendly flux types, such as no-clean or water-soluble fluxes, which have lower environmental impact compared to rosin-based fluxes. 4. **Recycling:** Implement recycling practices for soldering materials where possible to reduce waste and conserve resources. By adhering to these safety precautions and environmental considerations, individuals can ensure a safer working environment while minimizing the ecological footprint associated with soldering activities. This holistic approach not only protects health but also contributes to sustainable practices in the industry.