What Are Magnets Made Of

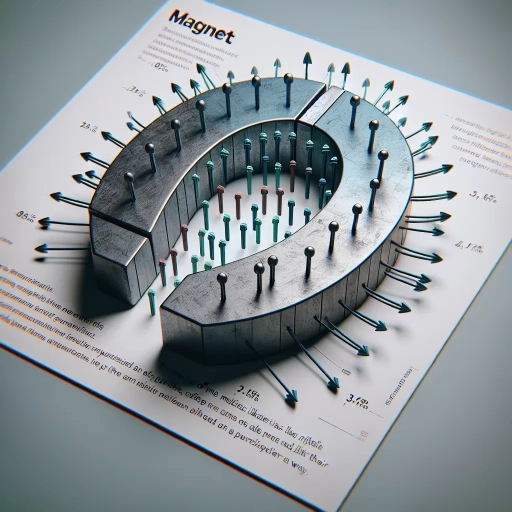
Magnets, ubiquitous in modern technology and everyday life, are fascinating objects that harness the power of magnetism to perform a wide range of functions. But what exactly are magnets made of? This question delves into the heart of magnetism, revealing the intricate materials and processes that bring these magnetic wonders to life. To understand magnets comprehensively, it is essential to explore three key aspects: the materials used in their production, the manufacturing processes that shape them, and the diverse applications and properties of different types of magnets. By examining the specific materials such as ferromagnetic metals and rare-earth elements, we can gain insight into why certain magnets are more powerful or durable than others. The manufacturing processes, which involve precise techniques like sintering and injection molding, play a crucial role in determining the final product's quality and performance. Finally, understanding the various applications and unique properties of magnets—from industrial machinery to consumer electronics—highlights their versatility and importance in our technological landscape. Let's begin by diving into the foundational aspect: the materials used in magnet production.
Materials Used in Magnet Production
Magnet production is a multifaceted field that relies on a diverse array of materials, each with its unique properties and applications. The journey to creating powerful magnets involves the use of various substances, ranging from naturally occurring minerals to sophisticated man-made compounds and advanced composite materials. Natural magnet materials, such as lodestone and magnetite, have been utilized for centuries due to their inherent magnetic properties. However, the advent of modern technology has led to the development of man-made magnet materials like neodymium iron boron (NdFeB) and samarium-cobalt (SmCo), which offer superior strength and durability. Furthermore, the integration of advanced composite materials has opened new avenues for magnet production, enabling the creation of tailored magnetic properties that cater to specific industrial needs. This article delves into the intricacies of these three categories—Natural Magnet Materials, Man-made Magnet Materials, and Advanced Composite Materials—providing a comprehensive overview of the materials used in magnet production.
Natural Magnet Materials
Natural magnet materials have been a cornerstone in the history of magnetism, providing the earliest sources of magnetic properties that have fascinated humans for centuries. The most well-known natural magnet material is magnetite, also known as lodestone, which is a naturally occurring iron oxide mineral (Fe₃O₄). Magnetite is one of the few minerals that are naturally magnetized, meaning it can be found in its magnetized state in nature. This unique property made magnetite a crucial discovery in ancient times, as it was used by early civilizations to create simple compasses and understand the fundamental principles of magnetism. Another significant natural magnet material is hematite (Fe₂O₃), although it is not naturally magnetized like magnetite. However, when subjected to certain conditions such as high pressure or temperature, hematite can exhibit magnetic properties. Other natural materials like goethite (FeO(OH)) and siderite (FeCO₃) also show magnetic behavior under specific conditions but are less commonly associated with strong magnetic properties compared to magnetite. The discovery and study of these natural magnet materials laid the groundwork for modern magnet production. Understanding the chemical and physical properties of these minerals allowed scientists to develop synthetic magnet materials with enhanced magnetic strengths and durability. For instance, the development of ferrites—a class of synthetic iron oxides—was directly influenced by the study of magnetite and other natural iron oxides. Ferrites are widely used today in various applications ranging from consumer electronics to industrial machinery due to their cost-effectiveness and robust magnetic performance. In addition to their historical significance, natural magnet materials continue to play a role in contemporary research. Scientists study these materials to understand the fundamental mechanisms behind magnetism at the atomic level, which can lead to breakthroughs in materials science and technology. For example, research on magnetite has contributed to advancements in spintronics—a field that leverages the spin of electrons to create new types of electronic devices. While synthetic magnet materials have largely supplanted natural ones in modern applications due to their superior performance and consistency, the study of natural magnet materials remains essential for advancing our understanding of magnetism. The intrinsic properties of these minerals continue to inspire innovation and drive technological progress, making them an integral part of both historical and contemporary discussions about magnet production.
Man-made Magnet Materials
Man-made magnet materials have revolutionized the field of magnetism, offering a wide range of properties and applications that natural magnets cannot match. These synthetic materials are engineered to possess specific magnetic characteristics, such as high coercivity, remanence, and energy product, which are crucial for various technological and industrial uses. One of the most significant categories of man-made magnet materials is the ferrites. Ferrites, composed of iron oxide combined with other metals like nickel, zinc, or manganese, are known for their low cost, high electrical resistance, and moderate magnetic strength. They are widely used in consumer electronics, such as radio antennas, transformers, and magnetic resonance imaging (MRI) machines due to their ability to operate efficiently at high frequencies. Another critical group is the rare-earth magnets, which include neodymium (NdFeB) and samarium-cobalt (SmCo) magnets. These materials exhibit exceptionally high magnetic strength and durability, making them indispensable in advanced technologies like electric motors, wind turbines, and magnetic resonance imaging (MRI) equipment. Neodymium magnets, in particular, are renowned for their high energy product and are used in everything from smartphones to electric vehicles. However, their production is often challenged by the scarcity and geopolitical complexities surrounding rare-earth elements. Alnico magnets, an alloy of aluminum, nickel, and cobalt, are another important class of man-made magnet materials. Known for their high temperature stability and resistance to demagnetization, Alnico magnets are frequently employed in applications requiring consistent performance over a wide temperature range, such as in automotive sensors and industrial machinery. Additionally, there are also composite magnets that combine different materials to achieve specific properties. For instance, bonded magnets made from a mixture of ferrite or rare-earth powders with a polymer binder offer flexibility in shape and size while maintaining good magnetic performance. The development of man-made magnet materials has also led to the creation of nanomagnets and thin-film magnets, which are pivotal in emerging technologies such as data storage devices and spintronics. These materials leverage the unique properties of nanoscale structures to enhance magnetic performance and reduce size, enabling advancements in fields like quantum computing and biomedical research. In summary, man-made magnet materials have transformed the landscape of magnetism by providing tailored magnetic properties that cater to diverse industrial and technological needs. From ferrites in consumer electronics to rare-earth magnets in high-performance applications, these synthetic materials continue to drive innovation and efficiency across various sectors. Their versatility, combined with ongoing research into new compositions and nanostructures, ensures that man-made magnet materials will remain a cornerstone of modern technology for years to come.
Advanced Composite Materials
Advanced composite materials play a pivotal role in the evolution of magnet production, offering unparalleled performance and versatility. These materials are engineered by combining two or more distinct components, such as fibers, polymers, and metals, to create a new material with superior properties that exceed those of its individual constituents. In the context of magnet production, advanced composites are particularly valuable due to their ability to enhance magnetic strength, durability, and thermal stability. One of the most significant advancements in composite materials for magnet applications is the development of fiber-reinforced polymers (FRPs). These composites integrate high-strength fibers like carbon or glass into a polymer matrix, resulting in materials that are lightweight yet incredibly robust. When used in magnet production, FRPs can provide structural support while minimizing weight, making them ideal for applications where both strength and portability are crucial. Additionally, these composites can be tailored to have specific thermal properties, ensuring that the magnets maintain their magnetic field even under extreme temperature conditions. Another critical area where advanced composites shine is in the creation of hybrid materials. By combining different types of materials—such as metals, ceramics, and polymers—engineers can design composites that optimize multiple properties simultaneously. For instance, a composite material might combine a ferromagnetic metal for high magnetic permeability with a ceramic component for enhanced thermal resistance. This hybrid approach allows for the creation of magnets that not only possess superior magnetic characteristics but also exhibit improved resistance to corrosion and wear. The integration of nanomaterials into composite structures further elevates the performance of magnets. Nanocomposites, which incorporate nanoparticles or nanofibers into the matrix material, can significantly enhance the magnetic properties of the final product. These nanoparticles can be engineered to have specific shapes and sizes that maximize their surface area, thereby increasing their magnetic moment and overall magnetic strength. Moreover, nanocomposites often exhibit better mechanical properties and higher thermal stability compared to traditional materials. In summary, advanced composite materials have revolutionized the field of magnet production by offering a wide range of benefits including enhanced magnetic strength, improved durability, and optimized thermal performance. Through the strategic combination of various components such as fibers, metals, ceramics, and nanoparticles, engineers can tailor these composites to meet the exacting demands of diverse applications. As research continues to advance in this field, it is likely that even more sophisticated composite materials will emerge, further expanding the capabilities and uses of magnets across various industries.
Manufacturing Processes for Magnets
The production of magnets involves a range of sophisticated manufacturing processes, each tailored to specific types of magnetic materials and applications. At the heart of magnet manufacturing are three key techniques: Casting and Sintering, Powder Metallurgy, and Injection Molding and Bonding. **Casting and Sintering Techniques** allow for the creation of complex shapes and high-performance magnets by fusing raw materials under controlled conditions. **Powder Metallurgy Methods** offer precision and versatility, enabling the production of magnets with unique properties through the compaction and sintering of metal powders. **Injection Molding and Bonding** processes, on the other hand, facilitate the mass production of magnets with consistent quality, often used in consumer electronics and automotive applications. Understanding these manufacturing processes is crucial for optimizing magnet performance and efficiency. As we delve into these techniques, it becomes clear that the choice of method is deeply intertwined with the **Materials Used in Magnet Production**, highlighting the importance of selecting the right materials to achieve desired magnetic properties. This article will explore these manufacturing processes in detail, providing insights into their applications and the critical role they play in producing high-quality magnets.
Casting and Sintering Techniques
Casting and sintering are pivotal techniques in the manufacturing of magnets, particularly for those made from ferromagnetic materials such as neodymium iron boron (NdFeB) and samarium-cobalt (SmCo). **Casting** involves the process of pouring molten metal into a mold to create the desired shape. For magnet production, this method is often used for simpler magnet geometries. The molten alloy is carefully poured into a mold, where it solidifies and takes the shape of the mold. This technique allows for the creation of complex shapes that would be difficult or impossible to achieve through other methods. However, casting can result in a less uniform microstructure compared to sintering, potentially affecting the magnetic properties. **Sintering**, on the other hand, is a more advanced and commonly used method for producing high-performance magnets. This process involves compacting fine powders of the magnetic material into a desired shape using high pressure. The compacted powder is then heated to a temperature below the melting point of the material but high enough to cause the particles to bond together through diffusion. This process enhances the microstructural uniformity and grain alignment, leading to superior magnetic properties. Sintering allows for the production of magnets with precise dimensions and complex geometries, making it ideal for applications requiring high magnetic strength and stability. In both techniques, **quality control** is crucial. For casting, ensuring the purity of the molten alloy and maintaining precise temperature control during solidification are essential. For sintering, careful selection of powder particle size and distribution, along with controlled heating and cooling cycles, is vital to achieve optimal magnetic performance. Additionally, post-processing steps such as machining and surface treatment may be necessary to meet specific application requirements. The choice between casting and sintering depends on the intended application of the magnet. Casting is often preferred for less demanding applications where cost-effectiveness is a priority, while sintering is chosen for high-performance applications requiring superior magnetic strength and durability. In summary, casting and sintering are complementary techniques that together enable the production of a wide range of magnets tailored to various industrial and consumer needs, each offering unique advantages in terms of cost, complexity, and performance. Understanding these processes is essential for appreciating the versatility and sophistication of modern magnet manufacturing.
Powder Metallurgy Methods
Powder metallurgy (PM) is a versatile and highly efficient method for manufacturing magnets, offering several advantages over traditional techniques. This process involves the production of parts from metal powders, which are compacted and then sintered to form the final product. In the context of magnet manufacturing, PM allows for the creation of complex geometries and precise control over material composition, which are crucial for achieving optimal magnetic properties. The PM process begins with the production of metal powders, typically through atomization or mechanical alloying. These powders are then mixed with other elements or additives to enhance magnetic performance. The powder blend is subsequently compacted using various techniques such as uniaxial pressing, isostatic pressing, or injection molding. This step ensures uniform density and shape retention. Following compaction, the green part undergoes sintering in a controlled atmosphere at high temperatures. Sintering fuses the powder particles together, enhancing the mechanical strength and magnetic properties of the material. For magnetic materials, additional steps like annealing or heat treatment may be necessary to align the magnetic domains and achieve the desired magnetic characteristics. One of the key benefits of PM in magnet manufacturing is its ability to produce near-net shapes, reducing the need for subsequent machining operations. This not only saves time but also minimizes material waste. Additionally, PM can handle a wide range of materials, including rare-earth alloys like neodymium iron boron (NdFeB) and samarium cobalt (SmCo), which are known for their exceptional magnetic strength. The precision and control offered by PM are particularly advantageous for producing high-performance magnets with specific properties tailored to various applications. For instance, in automotive and aerospace industries where weight and efficiency are critical, PM allows for the creation of lightweight yet powerful magnets. Similarly, in consumer electronics and medical devices, PM can produce small-scale magnets with precise dimensions and consistent quality. In summary, powder metallurgy is a sophisticated method that plays a pivotal role in the manufacturing of high-quality magnets. Its ability to control material composition, achieve complex geometries, and produce near-net shapes makes it an indispensable technique in modern magnet production. As technology continues to evolve, the role of PM in advancing magnet performance and efficiency will remain significant.
Injection Molding and Bonding
Injection molding and bonding are critical manufacturing processes in the production of magnets, particularly for those requiring complex geometries and high precision. **Injection Molding** involves the use of a machine to inject molten plastic into a mold, which is then cooled and ejected as a solid part. This process is often utilized for creating the housings or enclosures that hold magnetic components together. For instance, in the production of magnetic sensors or actuators, injection molding can produce the outer casing with precise dimensions and surface finishes, ensuring optimal performance and durability. The versatility of injection molding allows for the integration of various materials, including thermoplastics and thermosets, each offering unique properties such as strength, flexibility, or resistance to environmental factors. **Bonding**, on the other hand, is essential for assembling the magnetic components within these housings. There are several bonding techniques used depending on the specific requirements of the magnet. **Adhesive Bonding** involves applying a chemical adhesive to join two surfaces together. This method is particularly useful for bonding magnets to other materials like plastics or metals without compromising their magnetic properties. **Ultrasonic Welding** is another technique where high-frequency vibrations generate heat at the interface of two parts, causing them to fuse together. This method is advantageous for bonding thermoplastics and is commonly used in applications where hermetic seals are necessary. **Laser Welding** offers even greater precision and is often employed for bonding delicate or intricate parts, ensuring minimal thermal distortion and maintaining the integrity of the magnetic material. The combination of injection molding and bonding enables the creation of sophisticated magnetic devices with complex geometries and high reliability. For example, in the automotive industry, these processes are used to manufacture magnetic sensors for anti-lock braking systems (ABS) and electronic stability control (ESC), where precision and durability are paramount. Similarly, in consumer electronics, injection-molded housings and bonded magnetic components are integral to the functionality of devices such as smartphones and laptops. In summary, injection molding and bonding are indispensable in the manufacturing of magnets, allowing for the production of intricate designs with high accuracy and reliability. These processes not only enhance the structural integrity of magnetic devices but also ensure their optimal performance across various applications. By leveraging these advanced manufacturing techniques, industries can produce high-quality magnets that meet stringent specifications, driving innovation and efficiency in a wide range of technological fields.
Applications and Properties of Different Magnets
Magnets are fundamental components in a wide array of modern technologies, from consumer electronics and medical devices to industrial machinery and renewable energy systems. The diverse applications of magnets are underpinned by their varied properties, which are tailored to specific uses through different types of magnets. This article delves into the applications and properties of three primary types of magnets: permanent magnets, temporary magnets, and electromagnets. **Permanent Magnets: Uses and Characteristics** will explore the enduring magnetic fields of materials like neodymium and ferrite, highlighting their roles in devices such as motors, generators, and magnetic resonance imaging (MRI) machines. **Temporary Magnets: Uses and Characteristics** will discuss the transient magnetic properties of materials like iron and nickel, focusing on their utility in applications requiring temporary magnetization. **Electromagnets: Construction and Applications** will examine the construction and versatile uses of electromagnets, which are crucial in technologies ranging from electric motors to particle accelerators. Understanding these different types of magnets is essential for appreciating the broader context of materials used in magnet production, a topic that will be explored further in the section **Materials Used in Magnet Production**.
Permanent Magnets: Uses and Characteristics
**Permanent Magnets: Uses and Characteristics** Permanent magnets are a cornerstone in modern technology, renowned for their ability to retain magnetic field indefinitely without the need for an external power source. These magnets are fabricated from ferromagnetic materials such as neodymium iron boron (NdFeB), samarium-cobalt (SmCo), and ferrite, each offering distinct characteristics that cater to various applications. Neodymium iron boron magnets, for instance, are highly sought after due to their exceptional strength and durability, making them ideal for use in electric motors, generators, and wind turbines where high magnetic field strength is crucial. Samarium-cobalt magnets, on the other hand, excel in high-temperature environments and are often used in aerospace and automotive industries where reliability under extreme conditions is paramount. Ferrite magnets, though less powerful than their rare-earth counterparts, are cost-effective and widely used in consumer products such as refrigerator magnets, magnetic hooks, and audio speakers. The versatility of permanent magnets extends into medical devices like MRI machines and magnetic resonance imaging (MRI) systems, where precise and stable magnetic fields are essential for diagnostic imaging. In consumer electronics, permanent magnets play a vital role in the operation of hard disk drives and magnetic sensors. The characteristics of permanent magnets include their remanence (the ability to retain magnetic field), coercivity (resistance to demagnetization), and energy product (a measure of magnetic strength). These properties make them indispensable in industrial applications such as lifting and moving heavy metal objects in manufacturing processes. Additionally, permanent magnets are integral to renewable energy technologies like tidal power turbines and geothermal systems, contributing significantly to sustainable energy solutions. Innovations in material science have led to the development of advanced permanent magnets with enhanced properties. For example, dysprosium-alloyed neodymium iron boron magnets offer improved thermal stability and resistance to demagnetization. These advancements have expanded the scope of applications for permanent magnets, enabling their use in more demanding environments and contributing to technological advancements across various sectors. Overall, the unique combination of strength, durability, and cost-effectiveness makes permanent magnets an essential component in a wide range of modern technologies.
Temporary Magnets: Uses and Characteristics
Temporary magnets are a fascinating class of magnetic materials that exhibit magnetic properties only under specific conditions, making them versatile and highly useful in various applications. Unlike permanent magnets, which retain their magnetic field indefinitely, temporary magnets lose their magnetism once the external magnetic field is removed. This characteristic is primarily due to the material's ability to be magnetized by an external field but not to retain that magnetization once the field is gone. One of the most common types of temporary magnets is soft iron. Soft iron is an alloy of iron with a small amount of carbon and is known for its high magnetic permeability, which allows it to be easily magnetized and demagnetized. This property makes soft iron ideal for use in electromagnets, where a magnetic field needs to be turned on and off repeatedly. Electromagnets are crucial in applications such as electric motors, generators, and relays, where the ability to control the magnetic field is essential. Another significant use of temporary magnets is in the construction of magnetic cores for transformers and inductors. These components are vital in electrical circuits for stepping up or stepping down voltages and for filtering or storing electrical energy. The cores are typically made from materials like ferrite or silicon steel, which can be easily magnetized and demagnetized without retaining any residual magnetism. This ensures efficient energy transfer and minimizes energy losses due to hysteresis. Temporary magnets also play a critical role in medical imaging technologies such as Magnetic Resonance Imaging (MRI). In MRI machines, powerful electromagnets made from superconducting materials are used to create strong magnetic fields that align the spins of hydrogen nuclei in the body. These fields are temporary and can be adjusted precisely to generate detailed images of internal structures. In addition to these industrial and medical applications, temporary magnets find use in everyday life. For instance, the magnetic strips on credit cards and hotel key cards are made from temporary magnet materials. These strips can be magnetized during the manufacturing process but do not retain any permanent magnetism, ensuring they do not interfere with other magnetic devices. The characteristics of temporary magnets that make them so useful include their high magnetic permeability, low coercivity, and minimal hysteresis loss. These properties allow them to be easily magnetized and demagnetized without significant energy loss, making them efficient for applications requiring frequent changes in the magnetic field. Overall, temporary magnets are indispensable in modern technology due to their unique ability to be controlled and their wide range of practical applications.
Electromagnets: Construction and Applications
Electromagnets are a fascinating class of magnetic devices that leverage the principles of electromagnetism to generate powerful magnetic fields. Unlike permanent magnets, which retain their magnetic properties indefinitely, electromagnets derive their magnetism from the flow of electric current. The construction of an electromagnet typically involves a core material, often made of ferromagnetic substances like iron or nickel, around which one or more coils of wire are wound. When an electric current flows through these coils, it generates a magnetic field that can be controlled by adjusting the current's magnitude and direction. The versatility of electromagnets makes them indispensable in various applications. In industrial settings, electromagnets are used in cranes and lifting machines to handle heavy metal objects with precision and safety. They are also crucial in medical imaging technologies such as MRI (Magnetic Resonance Imaging) machines, where strong magnetic fields are necessary to align hydrogen nuclei for detailed imaging of the body's internal structures. Additionally, electromagnets play a vital role in consumer electronics; for instance, they are used in speakers and headphones to convert electrical signals into sound waves. In scientific research, electromagnets are employed in particle accelerators to steer and focus charged particles at incredibly high speeds. These devices are essential for experiments in particle physics that aim to uncover the fundamental nature of matter and energy. Furthermore, electromagnets are integral components of many household appliances, including refrigerators and air conditioners, where they facilitate the operation of compressors and fans. The ability to control the strength and polarity of an electromagnet's field makes it highly adaptable across different industries. For example, in transportation systems, electromagnets are used in magnetic levitation (maglev) trains to create frictionless motion by suspending the train above the track using magnetic forces. This technology significantly reduces wear and tear on the train's components while enabling smoother and faster travel. In summary, electromagnets offer unparalleled flexibility and power compared to permanent magnets due to their reliance on electric current for magnetization. Their widespread applications span from heavy industry and medical diagnostics to consumer electronics and cutting-edge scientific research. The unique properties of electromagnets make them an essential tool in modern technology, enabling innovations that transform various aspects of our lives.