What Does Permanent Press Mean

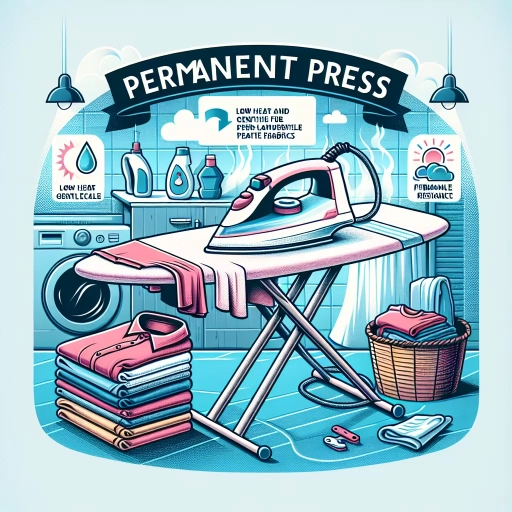
In the realm of textile technology, the term "permanent press" has become synonymous with convenience and durability. This innovative fabric treatment revolutionizes the way we care for our clothing, reducing the need for ironing and enhancing the overall lifespan of garments. But what exactly does permanent press mean? To delve into this concept, it is essential to understand the underlying principles, mechanisms, and benefits associated with it. This article will explore the concept of permanent press in depth, starting with **Understanding the Concept of Permanent Press**, where we will define and explain the origins of this technology. We will then examine **How Permanent Press Works**, detailing the chemical processes and treatments involved. Finally, we will discuss **Benefits and Applications of Permanent Press**, highlighting its practical advantages and widespread use in various industries. By grasping these key aspects, readers will gain a comprehensive understanding of how permanent press transforms everyday fabrics into low-maintenance, high-performance textiles. Let's begin by **Understanding the Concept of Permanent Press**.
Understanding the Concept of Permanent Press
Understanding the concept of permanent press involves delving into its multifaceted nature, which encompasses its definition and origin, the chemical treatments involved, and its historical context and development. Permanent press, a term often associated with wrinkle-resistant fabrics, is more than just a modern convenience; it represents a significant advancement in textile technology. To grasp this concept fully, one must first explore its definition and origin, tracing back to the early innovations that led to the creation of these durable fabrics. This foundational understanding sets the stage for examining the chemical treatments that make permanent press possible, revealing the intricate processes that alter fabric properties. Additionally, considering the historical context and development of permanent press fabrics provides insight into how societal needs and technological advancements have shaped this industry over time. By exploring these three key aspects, we can appreciate the complexity and importance of permanent press in our daily lives. Let us begin by defining what permanent press is and where it originated.
Definition and Origin
**Understanding the Concept of Permanent Press** ### Definition and Origin The term "permanent press" refers to a fabric treatment process designed to reduce wrinkles and make ironing easier. This innovative textile technology emerged in the mid-20th century, revolutionizing the way people maintained their clothing. The concept of permanent press was first introduced in the 1950s by chemists at the DuPont company, who developed a chemical treatment known as "wrinkle-resistant" or "easy-care" fabric. This breakthrough involved applying a resin finish to fabrics, typically cotton or cotton blends, which altered their molecular structure. When treated fabrics were washed and dried, the resin helped maintain their shape, significantly reducing the need for ironing. The origin of permanent press can be traced back to the post-war era when there was a growing demand for convenience and efficiency in household chores. As women entered the workforce in greater numbers, there was less time available for traditional domestic tasks such as ironing. DuPont's innovation addressed this need by creating fabrics that could withstand multiple washes and wear without losing their smooth appearance. The process involved treating fabrics with chemicals like formaldehyde, which cross-linked the fibers to prevent them from wrinkling. The introduction of permanent press fabrics marked a significant shift in textile manufacturing and consumer behavior. It not only simplified laundry routines but also influenced fashion trends, enabling the mass production of wrinkle-resistant garments that were both stylish and practical. Today, permanent press fabrics are ubiquitous in various types of clothing, from business attire to casual wear, making them an integral part of modern textile technology. Despite some environmental and health concerns associated with the chemicals used in the treatment process, permanent press remains a cornerstone of contemporary fabric science, continuing to evolve with advancements in sustainable and eco-friendly treatments. This evolution underscores the enduring impact of permanent press on our daily lives, reflecting a broader societal trend towards convenience and ease in everyday tasks.
Chemical Treatments Involved
Chemical treatments play a crucial role in achieving the concept of permanent press, a textile finishing process designed to reduce wrinkles and maintain fabric shape. These treatments involve the application of specific chemicals to the fabric, which alter its molecular structure to enhance durability and ease of care. One of the primary chemicals used is formaldehyde, often in the form of dimethylol dihydroxyethyleneurea (DMDHEU). This resin is applied to the fabric and then cured under heat, causing cross-linking between the cellulose molecules in cotton fibers. This cross-linking process stiffens the fibers, making them less prone to wrinkling and more resistant to shrinkage. Another key chemical treatment involves the use of silicone-based finishes. These treatments impart a smooth, wrinkle-resistant surface to fabrics by forming a thin layer on the fiber surface. Silicones also improve fabric softness and reduce static cling, enhancing overall comfort and appearance. Additionally, some permanent press treatments include the use of fluoropolymers, which provide stain resistance and water repellency, further extending the benefits of permanent press beyond just wrinkle resistance. The process of applying these chemical treatments typically involves several steps. First, the fabric is treated with a solution containing the desired chemicals. This solution is then evenly distributed across the fabric using various methods such as padding, spraying, or immersion. After treatment, the fabric is dried and cured under controlled conditions to activate the chemicals and ensure they bond effectively with the fibers. It's important to note that while chemical treatments are effective in achieving permanent press properties, they can also have environmental and health implications. Formaldehyde, for instance, is a known irritant and potential carcinogen, prompting many manufacturers to seek alternative treatments that are safer and more sustainable. Recent advancements include the development of formaldehyde-free resins and eco-friendly finishing agents that offer similar benefits without the associated risks. In summary, chemical treatments are essential for creating fabrics with permanent press properties. By altering the molecular structure of fibers through cross-linking and surface modification, these treatments enhance fabric durability, reduce wrinkles, and improve overall performance. However, it is crucial to balance these benefits with considerations for safety and sustainability to ensure that permanent press fabrics meet both functional and ethical standards.
Historical Context and Development
The concept of permanent press, a term synonymous with wrinkle-resistant fabrics, has its roots deeply embedded in the historical context of textile innovation. The mid-20th century marked a significant turning point in the development of fabrics, particularly with the advent of synthetic fibers like polyester and nylon. These new materials offered durability and ease of care that natural fibers could not match. However, they also presented challenges such as wrinkling and lack of smoothness. In the 1950s and 1960s, textile manufacturers began exploring ways to enhance the performance of these synthetic fibers. One of the key breakthroughs came with the introduction of chemical treatments that could alter the fabric's molecular structure. This led to the development of permanent press fabrics, which retained their shape and smoothness even after washing and drying without ironing. The historical context of post-war consumer culture played a crucial role in the popularity of permanent press fabrics. As women entered the workforce in greater numbers, there was an increasing demand for clothing that was both stylish and low-maintenance. Permanent press fabrics filled this need perfectly, offering a solution that balanced aesthetics with practicality. Technological advancements in fabric finishing processes further solidified the position of permanent press fabrics in the market. The use of resins and other chemical treatments allowed manufacturers to create fabrics that were not only wrinkle-resistant but also resistant to shrinkage and fading. This made permanent press garments highly appealing to consumers who valued convenience without compromising on quality. The impact of permanent press on fashion and lifestyle cannot be overstated. It democratized access to stylish clothing by making it easier for people to maintain their wardrobe without the need for frequent ironing. This shift also influenced fashion trends, enabling designers to create garments with more complex designs and textures that would previously have been impractical due to maintenance requirements. Moreover, the environmental and economic implications of permanent press fabrics are noteworthy. By reducing the need for ironing, these fabrics contributed to energy savings and lower household utility bills. Additionally, the durability of permanent press fabrics extended the lifespan of garments, potentially reducing waste and the demand for new clothing. In summary, the development of permanent press fabrics is a testament to human ingenuity in response to changing societal needs. From its origins in post-war textile innovation to its widespread adoption in modern fashion, permanent press has revolutionized how we think about clothing maintenance and style. Understanding this historical context provides a deeper appreciation for the concept of permanent press and its enduring impact on our daily lives.
How Permanent Press Works
Understanding how permanent press works is crucial for appreciating the advancements in textile technology that have transformed the way we care for our clothing. Permanent press, a process that ensures fabrics retain their shape and smoothness without the need for frequent ironing, is a result of several key factors. First, **Textile Fabric Modifications** play a pivotal role in creating fabrics that are inherently resistant to wrinkling. This involves altering the molecular structure of fibers to enhance their resilience and stability. Second, the **Manufacturing Process Overview** highlights the steps involved in producing permanent press fabrics, including treatments and finishes that are applied during the manufacturing stage. Lastly, **Role of Finishing Agents** explains how specific chemicals and treatments are used to enhance fabric performance and durability. By delving into these aspects, we can gain a comprehensive understanding of how permanent press fabrics are created and maintained. Let's start by examining the critical **Textile Fabric Modifications** that lay the foundation for this innovative technology.
Textile Fabric Modifications
Textile fabric modifications are crucial in achieving the desired properties and performance of fabrics, particularly in the context of permanent press treatments. Permanent press, also known as wrinkle-resistant or easy-care fabric, relies on specific chemical and physical modifications to reduce the need for ironing and enhance fabric durability. One key modification involves the application of resins, such as formaldehyde-based finishes, which cross-link the molecular structure of the fabric. This cross-linking process stabilizes the fibers, preventing them from wrinkling and shrinking as easily as untreated fabrics. Additionally, fabric manufacturers may employ techniques like sanforization to pre-shrink fabrics, ensuring that they will not shrink further after treatment. Another significant modification is the use of fabric softeners and anti-wrinkle agents that are integrated into the fabric during the manufacturing process. These agents work by coating the fibers with a thin layer that reduces friction between them, making it easier for fabrics to smooth out wrinkles naturally. Furthermore, some fabrics undergo mechanical treatments like calendaring, where the fabric is passed through heated rollers to flatten and smooth out the fibers, enhancing its appearance and reducing wrinkles. The combination of these chemical and physical modifications results in fabrics that retain their shape and appearance even after repeated washing and drying cycles, making them ideal for garments that require minimal maintenance. By understanding these textile fabric modifications, consumers can better appreciate how permanent press works to provide convenience and longevity in their clothing.
Manufacturing Process Overview
The manufacturing process for permanent press fabrics involves a series of intricate steps that transform raw materials into durable, wrinkle-resistant textiles. It begins with the selection of high-quality fibers, often a blend of cotton and synthetic materials like polyester or nylon, which are chosen for their strength and ability to withstand the rigors of the manufacturing process. These fibers are then spun into yarns, which are subsequently woven or knitted into fabric using advanced machinery. The critical phase in creating permanent press fabric is the application of a chemical treatment known as a finish. This involves immersing the fabric in a solution containing resins such as formaldehyde-based compounds, which react with the fibers to create cross-links. These cross-links alter the molecular structure of the fabric, making it resistant to wrinkles and improving its overall durability. Following the chemical treatment, the fabric undergoes a process called curing, where it is exposed to high temperatures and pressures. This step ensures that the chemical finish penetrates deeply into the fabric, enhancing its performance characteristics. The fabric is then washed and dried to remove any excess chemicals and stabilize the fibers. To further enhance the fabric's properties, additional treatments may be applied. These can include softening agents to improve texture, stain resistors to enhance cleanliness, and UV protectants to prevent fading. The fabric is then inspected for quality and cut into desired dimensions for use in various applications such as clothing, upholstery, and bedding. Throughout this process, manufacturers must adhere to strict quality control measures to ensure consistency and reliability. Advanced technologies such as automated inspection systems and computer-controlled weaving machines help maintain high standards. Additionally, many manufacturers now incorporate sustainable practices into their processes, using eco-friendly chemicals and reducing waste to minimize environmental impact. In summary, the manufacturing process for permanent press fabrics is a complex interplay of material selection, chemical treatment, curing, and finishing steps designed to produce textiles that are both functional and aesthetically pleasing. This meticulous process underscores the science behind how permanent press works, transforming ordinary fabrics into resilient and low-maintenance materials that meet modern demands for convenience and durability.
Role of Finishing Agents
In the context of textile manufacturing, finishing agents play a crucial role in enhancing the performance and aesthetic appeal of fabrics, particularly in the process of creating permanent press garments. Permanent press, also known as wrinkle-resistant or easy-care fabric, relies heavily on these chemical treatments to achieve its signature properties. Finishing agents are specialized chemicals applied to fabrics during the manufacturing process to impart specific characteristics such as wrinkle resistance, smoothness, and durability. One of the primary types of finishing agents used in permanent press fabrics is fabric softeners and wrinkle resistors. These agents work by cross-linking the fibers within the fabric, creating a more stable structure that resists wrinkles and creases. For instance, formaldehyde-based resins like dimethylol dihydroxyethyleneurea (DMDHEU) are commonly used to treat cotton fabrics. When these resins are applied and cured under heat, they form covalent bonds between cellulose molecules, thereby reducing the fabric's tendency to wrinkle. Another category of finishing agents includes moisture-wicking and breathable treatments. These agents help in managing moisture levels within the fabric, ensuring that it remains dry and comfortable against the skin. Such treatments are particularly beneficial for active wear and work uniforms where moisture management is critical. For example, silicone-based treatments can enhance fabric smoothness while also improving its ability to wick away moisture. Additionally, finishing agents can be used to enhance fabric durability and resistance to wear and tear. Anti-pilling treatments, for instance, prevent the formation of unsightly pills on fabric surfaces by reducing fiber breakage and tangling. Similarly, stain-resistant treatments like Teflon or Scotchgard can be applied to make fabrics more resistant to spills and stains, making them easier to clean and maintain. The application of finishing agents also extends to improving the fabric's appearance and feel. Softening agents like quaternary ammonium compounds can make fabrics feel softer and more luxurious, while optical brighteners can enhance the fabric's color brightness by absorbing ultraviolet light and emitting blue light. In summary, the role of finishing agents in creating permanent press fabrics is multifaceted. They not only provide wrinkle resistance but also enhance fabric softness, durability, moisture management, and stain resistance. These treatments are integral to the manufacturing process, ensuring that permanent press garments retain their shape, look fresh after washing, and offer long-lasting comfort and performance. By understanding how these agents work, consumers can better appreciate the technology behind their easy-care clothing and make informed choices about their wardrobe needs.
Benefits and Applications of Permanent Press
The concept of Permanent Press has revolutionized the textile industry by offering a multitude of benefits that extend beyond mere aesthetics. At its core, Permanent Press technology ensures that fabrics maintain their shape and appearance without the need for frequent ironing, thereby enhancing convenience and ease of care. This innovation also contributes to the enhanced durability and longevity of garments, making them resistant to wear and tear over time. Furthermore, the widespread use of Permanent Press in various industries, from fashion to healthcare, underscores its versatility and practicality. By exploring these facets, it becomes clear that Permanent Press is not just a technological advancement but a game-changer in how we interact with and maintain our clothing. Let's delve into the first of these benefits: the convenience and ease of care that Permanent Press offers, transforming the way we handle our daily wardrobe.
Convenience and Ease of Care
Convenience and ease of care are among the most significant benefits of permanent press fabrics, making them a staple in modern wardrobes. Permanent press technology involves treating fabrics to reduce wrinkles and make them easier to maintain, thereby saving time and effort for the consumer. Unlike traditional fabrics that require frequent ironing, permanent press materials retain their shape and smooth finish even after multiple washes and wear cycles. This feature is particularly advantageous for busy individuals who value efficiency in their daily routines. For instance, professionals can enjoy the crisp appearance of their work attire without the hassle of daily ironing, while parents can appreciate the low-maintenance aspect when it comes to children's clothing. Additionally, travelers benefit from packing fewer items without worrying about wrinkles, as permanent press garments are less prone to creasing during transit. The ease of care extends beyond just ironing; these fabrics often require less drying time and can be machine washed and dried, further simplifying laundry tasks. This convenience translates into more free time for other activities, enhancing overall quality of life. Moreover, the durability of permanent press fabrics means they withstand repeated washing and wear better than untreated fabrics, ensuring that your wardrobe remains in good condition for longer. This combination of convenience, ease of care, and durability makes permanent press fabrics an indispensable choice for anyone seeking to streamline their daily routines while maintaining a polished appearance. By integrating permanent press technology into their wardrobe, individuals can enjoy the perfect blend of style, comfort, and practicality.
Enhanced Durability and Longevity
Enhanced durability and longevity are among the most significant benefits of permanent press fabrics, making them a preferred choice for various applications. Permanent press treatments involve chemical processes that alter the fabric's molecular structure, allowing it to retain its shape and resist wrinkles even after repeated washing and drying. This inherent durability translates into several key advantages. Firstly, permanent press fabrics require less maintenance compared to untreated materials; they do not need ironing, which saves time and effort. This convenience is particularly valuable in busy households and commercial settings where laundry efficiency is crucial. Moreover, the enhanced durability of permanent press fabrics extends their lifespan. These fabrics are less prone to wear and tear, such as fraying or fading, which means they can withstand the rigors of daily use without compromising their appearance or functionality. For instance, in the hospitality industry, permanent press linens and uniforms can endure multiple wash cycles without losing their crispness or color, thereby reducing the need for frequent replacements. Similarly, in healthcare settings, permanent press uniforms offer a hygienic and durable solution that can withstand rigorous cleaning protocols. The longevity of permanent press fabrics also has environmental benefits. By lasting longer, these fabrics reduce the need for frequent purchases and replacements, which in turn decreases textile waste. Additionally, the reduced need for ironing means lower energy consumption, contributing to a more sustainable lifestyle. In consumer goods, such as workwear and school uniforms, permanent press fabrics offer long-lasting performance that can withstand the demands of daily activities without showing signs of wear prematurely. From a practical standpoint, the enhanced durability of permanent press fabrics makes them ideal for a wide range of applications. For example, in outdoor gear like camping equipment and sportswear, these fabrics provide the necessary resilience to withstand harsh conditions while maintaining their integrity. In home furnishings, permanent press curtains and upholstery fabrics retain their shape and color over time, ensuring that they continue to look fresh and vibrant even after prolonged exposure to sunlight. In summary, the enhanced durability and longevity of permanent press fabrics are key factors that contribute to their widespread adoption across various sectors. By offering low maintenance, extended lifespan, and environmental benefits, these fabrics provide a practical solution for both personal and professional use. Whether in household textiles, work uniforms, or outdoor gear, permanent press treatments ensure that fabrics remain in excellent condition for an extended period, making them an invaluable asset in today's fast-paced world.
Widespread Use in Various Industries
The widespread use of permanent press technology spans across various industries, underscoring its versatility and value. In the **textile industry**, permanent press fabrics are a cornerstone for producing wrinkle-resistant garments, bedding, and upholstery. This treatment ensures that fabrics maintain their shape and appearance even after repeated washing and drying, making them ideal for busy lifestyles. For instance, business attire such as suits and dresses benefit from permanent press, as they remain crisp and professional without the need for frequent ironing. In **healthcare**, permanent press fabrics are used in hospital linens and uniforms due to their ease of maintenance and hygiene. These fabrics can withstand high-temperature washing cycles necessary for sterilization, ensuring that medical textiles remain clean and free from bacteria. This is particularly important in environments where infection control is paramount. The **hospitality industry** also leverages permanent press technology to enhance guest comfort and operational efficiency. Hotel linens, towels, and uniforms are often treated with permanent press to reduce laundry costs and improve the overall appearance of these items. This not only enhances the guest experience but also streamlines housekeeping operations. In **automotive manufacturing**, permanent press materials are utilized in car interiors such as seat covers, carpets, and other upholstery components. These materials are designed to withstand wear and tear while maintaining their aesthetic appeal over time. The durability and low maintenance requirements of permanent press fabrics make them an excellent choice for vehicles that are subject to heavy use. Furthermore, **furniture manufacturers** incorporate permanent press treatments into their products to ensure that fabrics used in sofas, chairs, and other upholstered items remain resilient against wrinkles and stains. This enhances the longevity of the furniture while maintaining its visual appeal. Additionally, **aviation** and **marine industries** benefit from permanent press textiles due to their resistance to wrinkles and creases under varying environmental conditions. Uniforms for flight attendants and crew members, as well as interior components of aircraft and boats, are often treated with permanent press to ensure they look professional and well-maintained even after prolonged use. In **outdoor gear**, such as camping equipment and sportswear, permanent press technology is applied to enhance durability and comfort. Tents, sleeping bags, and clothing made from these treated fabrics can withstand harsh weather conditions while requiring minimal care. Overall, the widespread adoption of permanent press technology across diverse industries highlights its practical benefits and broad applicability. By offering a combination of durability, ease of maintenance, and aesthetic appeal, permanent press fabrics have become an essential component in many sectors where functionality meets style.