What Are Alloy Wheels

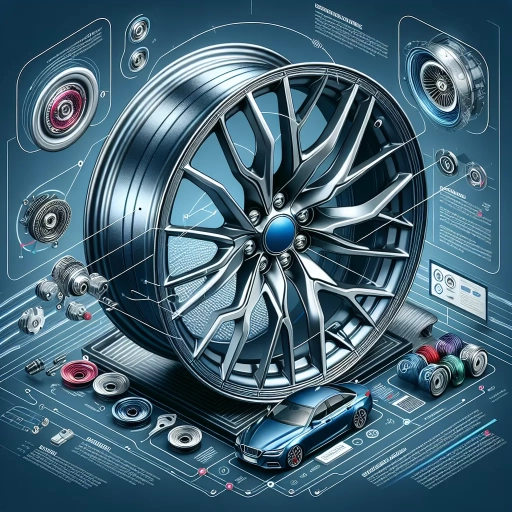
Alloy wheels have become a staple in the automotive industry, offering a blend of style, performance, and durability that traditional steel wheels cannot match. These high-quality components are crafted from a combination of metals, each chosen for its unique properties, which together enhance the overall driving experience. In this article, we will delve into the world of alloy wheels, starting with an **Introduction to Alloy Wheels**, where we explore their history, design, and how they differ from other types of wheels. We will then examine the **Materials and Manufacturing Process**, highlighting the specific metals used and the intricate steps involved in their production. Finally, we will discuss the **Benefits and Applications of Alloy Wheels**, detailing how they improve vehicle performance, safety, and aesthetics. By understanding these aspects, readers will gain a comprehensive insight into why alloy wheels are a preferred choice for many car enthusiasts and manufacturers alike. Let's begin by diving into the **Introduction to Alloy Wheels**.
Introduction to Alloy Wheels
Alloy wheels have become a staple in the automotive industry, offering a blend of performance, aesthetics, and durability that traditional steel wheels cannot match. This article delves into the world of alloy wheels, providing a comprehensive introduction that covers their definition and history, a comparison with steel wheels, and an analysis of their popularity and market demand. First, we will explore the **Definition and History of Alloy Wheels**, tracing their evolution from early experiments with lightweight materials to their current widespread use. Understanding the origins and development of alloy wheels sets the stage for appreciating their technological advancements and the reasons behind their adoption. Next, we will conduct a **Comparison with Steel Wheels**, highlighting the key differences in terms of weight, strength, heat dissipation, and overall driving experience. This comparison will help readers understand why alloy wheels have become the preferred choice for many car enthusiasts and manufacturers. Finally, we will examine the **Popularity and Market Demand** for alloy wheels, discussing how their appeal extends beyond functional benefits to include significant aesthetic and status-related factors. This section will reveal why alloy wheels continue to dominate the aftermarket and OEM markets. By understanding these aspects, readers will gain a thorough insight into the significance and impact of alloy wheels in modern automotive culture. Let's begin by exploring the **Definition and History of Alloy Wheels**.
Definition and History of Alloy Wheels
Alloy wheels, a staple in modern automotive design, have a rich history that underscores their evolution from humble beginnings to the sleek, high-performance components we see today. The term "alloy" refers to a mixture of two or more elements, at least one of which is a metal, where the resultant mixture has properties different from those of its individual components. In the context of wheels, alloy wheels are typically made from a combination of aluminum and other metals such as magnesium, silicon, and copper. The history of alloy wheels dates back to the early 20th century when aluminum began to be used in automotive applications due to its lightweight yet strong properties. However, it wasn't until the 1960s that alloy wheels started gaining popularity as a performance-enhancing feature. The first mass-produced alloy wheels were introduced by the Italian company Campagnolo, known for its high-quality bicycle components, which later expanded into the automotive sector. These early alloy wheels were primarily used in racing and sports cars due to their ability to reduce unsprung weight, thereby improving handling and braking performance. The 1970s and 1980s saw a significant rise in the adoption of alloy wheels across various segments of the automotive industry. This period marked the introduction of new manufacturing techniques such as casting and forging, which allowed for more complex designs and improved durability. Companies like BBS (Bauart, Bremmer, Sinsheim) in Germany and Enkei in Japan became synonymous with high-quality alloy wheels, catering to both aftermarket enthusiasts and original equipment manufacturers (OEMs). In recent decades, advancements in technology have further refined the production process of alloy wheels. Modern manufacturing techniques include flow forming and rotary forging, which enhance strength while maintaining lightness. Additionally, the use of advanced materials like titanium and magnesium alloys has become more prevalent, offering even greater weight reduction without compromising on strength. Today, alloy wheels are not just about performance; they also play a crucial role in aesthetics. With a wide range of designs available—from simple and elegant to complex and aggressive—alloy wheels have become an integral part of a vehicle's visual appeal. Many car manufacturers now offer alloy wheels as standard or optional equipment across their model lines, reflecting their importance in both functionality and design. In conclusion, the definition and history of alloy wheels highlight their transformation from a niche performance component to a ubiquitous feature in modern vehicles. From their early adoption in racing to their widespread use today, alloy wheels have evolved significantly, combining technological innovation with aesthetic appeal to enhance both the performance and appearance of cars. As automotive technology continues to advance, it is likely that alloy wheels will remain a key component in the ongoing quest for better vehicle dynamics and design.
Comparison with Steel Wheels
When comparing alloy wheels to their steel counterparts, several key differences emerge that highlight the distinct advantages of alloy wheels. **Durability and Strength**: Alloy wheels, typically made from a combination of aluminum and magnesium, offer superior strength-to-weight ratios compared to steel wheels. This means they are lighter yet more robust, enhancing vehicle performance and fuel efficiency. In contrast, steel wheels are heavier and more prone to bending or cracking under stress. **Corrosion Resistance**: Alloy wheels exhibit better resistance to corrosion due to their inherent properties and the protective coatings often applied. This makes them more durable over time, especially in harsh weather conditions where steel wheels might rust or degrade. Steel wheels, on the other hand, require additional protective measures such as galvanizing or painting to combat corrosion. **Heat Dissipation**: The thermal conductivity of alloy materials is significantly higher than that of steel, allowing for better heat dissipation from the brakes. This is crucial for maintaining optimal braking performance and extending the lifespan of brake components. Steel wheels tend to retain heat longer, which can lead to reduced braking efficiency and increased wear on brake pads. **Aesthetics**: Alloy wheels are renowned for their sleek designs and polished finishes, which can significantly enhance the visual appeal of a vehicle. They come in a wide range of styles and colors, offering drivers greater customization options. Steel wheels, while functional, often lack the aesthetic appeal of alloy wheels and may appear more utilitarian. **Performance**: The lighter weight of alloy wheels reduces unsprung mass, which improves handling and suspension response. This results in a smoother ride and better overall vehicle dynamics. Additionally, the reduced weight contributes to improved acceleration and braking performance. Steel wheels, being heavier, can negatively impact these aspects of vehicle performance. **Maintenance**: While alloy wheels generally require less maintenance than steel wheels due to their corrosion resistance, they do need periodic cleaning to maintain their appearance. Steel wheels, however, may require more frequent maintenance to prevent rust and ensure longevity. In summary, alloy wheels outperform steel wheels in terms of durability, corrosion resistance, heat dissipation, aesthetics, performance, and maintenance requirements. These advantages make alloy wheels a preferred choice for many vehicle owners seeking both functional and cosmetic enhancements for their vehicles. As an integral part of modern automotive design, alloy wheels continue to evolve with advancements in materials science and manufacturing technologies, further solidifying their position as a superior alternative to traditional steel wheels.
Popularity and Market Demand
The popularity and market demand for alloy wheels have skyrocketed in recent years, driven by a combination of aesthetic appeal, performance enhancements, and technological advancements. Alloy wheels, made from a mixture of aluminum and other metals, offer significant advantages over traditional steel wheels. Their lighter weight contributes to improved fuel efficiency, better handling, and enhanced braking performance, making them a favorite among car enthusiasts and everyday drivers alike. The visual appeal of alloy wheels is another major factor in their widespread adoption; they come in a variety of styles, finishes, and sizes, allowing vehicle owners to personalize their vehicles and enhance their overall appearance. This versatility has led to a thriving aftermarket industry where consumers can choose from a wide range of designs to match their vehicle's make, model, and personal taste. Moreover, the durability of alloy wheels is a key selling point. Unlike steel wheels, which can rust and corrode over time, alloy wheels are resistant to corrosion and can withstand harsh weather conditions. This durability not only extends the lifespan of the wheels but also reduces maintenance costs in the long run. Additionally, advancements in manufacturing technology have made alloy wheels more affordable and accessible to a broader market segment. The use of advanced materials and manufacturing processes such as casting and forging has improved the strength-to-weight ratio of alloy wheels, making them safer and more reliable. The automotive industry's shift towards performance and luxury has further fueled the demand for alloy wheels. High-performance vehicles often come equipped with alloy wheels as standard, highlighting their importance in enhancing vehicle dynamics. Furthermore, the rise of electric vehicles (EVs) has introduced new challenges and opportunities for alloy wheel manufacturers. EVs require lighter yet stronger wheels to optimize their range and efficiency, making alloy wheels an essential component in this emerging market. In conclusion, the popularity and market demand for alloy wheels are driven by their multifaceted benefits—ranging from improved performance and aesthetics to durability and cost-effectiveness. As automotive technology continues to evolve, it is likely that alloy wheels will remain a staple in the industry, catering to both the practical needs of everyday drivers and the performance aspirations of car enthusiasts. Their widespread adoption underscores their importance as a critical component in modern vehicles, enhancing both functionality and style.
Materials and Manufacturing Process
The production of alloy wheels is a complex process that involves several critical stages, each contributing to the final product's quality, durability, and performance. At the heart of this process are the materials used, which dictate the wheel's strength, weight, and aesthetic appeal. Common materials such as aluminum, magnesium, and titanium alloys are favored for their unique properties that enhance vehicle performance and safety. However, the choice of material is just the beginning. Advanced manufacturing techniques and technologies play a pivotal role in shaping these materials into precise and functional components. Techniques like casting, forging, and machining are employed to achieve the desired form and structure. Additionally, quality control and testing methods are essential to ensure that the final product meets stringent standards. These methods involve rigorous inspections and tests to verify the wheel's integrity, balance, and resistance to various environmental conditions. By understanding these three key aspects—common materials used in alloy wheels, manufacturing techniques and technologies, and quality control and testing methods—we can appreciate the meticulous craftsmanship and technological advancements that go into creating high-quality alloy wheels. Let's start by exploring the common materials used in alloy wheels.
Common Materials Used in Alloy Wheels
Alloy wheels are crafted from a variety of materials, each chosen for its unique properties that contribute to the overall performance, durability, and aesthetic appeal of the wheel. The most common materials used in alloy wheels are aluminum and magnesium, often combined in various alloys to optimize their characteristics. **Aluminum Alloys:** Aluminum is the most prevalent material in alloy wheels due to its lightweight nature, high strength-to-weight ratio, and excellent corrosion resistance. Aluminum alloys, such as 6061 and 7075, are widely used because they offer a balance between strength and ductility. These alloys can be further enhanced through processes like forging or casting, which allow for intricate designs and improved mechanical properties. Forged aluminum wheels, in particular, are prized for their exceptional strength and reduced weight, making them ideal for high-performance vehicles. **Magnesium Alloys:** Magnesium is another key material used in alloy wheels, particularly for high-end applications where weight reduction is critical. Magnesium alloys are even lighter than aluminum, providing a significant advantage in terms of unsprung weight reduction, which can improve handling and fuel efficiency. However, magnesium has a lower melting point and is more prone to corrosion compared to aluminum, necessitating additional protective coatings to ensure longevity. **Other Materials:** While aluminum and magnesium dominate the market, other materials like titanium and carbon fiber are also being explored for their potential in creating ultra-lightweight and high-strength alloy wheels. Titanium alloys offer superior strength-to-weight ratios but are more expensive and less commonly used due to their higher production costs. Carbon fiber, known for its exceptional stiffness and lightness, is sometimes integrated into wheel designs to enhance performance, although it remains a niche option due to cost and manufacturing complexities. **Manufacturing Processes:** The choice of material is closely tied to the manufacturing process. Forging, casting, and flow-forming are among the most common methods used to produce alloy wheels. Forging involves shaping the metal under high pressure and heat to create a strong and dense structure. Casting allows for more intricate designs but may result in a slightly heavier wheel. Flow-forming combines elements of both processes, offering a balance between strength and weight while allowing for complex geometries. In summary, the selection of materials for alloy wheels is driven by the need for a combination of light weight, high strength, and corrosion resistance. Aluminum alloys remain the standard due to their well-balanced properties, while magnesium alloys offer additional weight savings for specialized applications. The integration of other materials like titanium and carbon fiber represents ongoing innovation in the field, aimed at pushing the boundaries of performance and efficiency in alloy wheel design. Understanding these materials and their associated manufacturing processes is crucial for appreciating the engineering and craftsmanship that go into creating high-quality alloy wheels.
Manufacturing Techniques and Technologies
Manufacturing techniques and technologies play a pivotal role in the production of alloy wheels, ensuring they meet stringent standards of quality, durability, and aesthetic appeal. The process begins with the selection of high-quality raw materials, typically aluminum or magnesium alloys, which are chosen for their lightweight properties, strength, and corrosion resistance. These materials are then subjected to various manufacturing techniques. **Casting** is one of the most common methods used in alloy wheel production. This involves melting the alloy and pouring it into a mold to achieve the desired shape. There are several casting techniques, including gravity casting, low-pressure casting, and high-pressure casting. Each method has its own advantages; for instance, high-pressure casting allows for more precise control over the final product's dimensions and surface finish. **Forging** is another critical technique that enhances the mechanical properties of alloy wheels. In this process, the alloy is heated and then shaped using a die under high pressure. Forging increases the strength and toughness of the material by aligning the grain structure in the direction of stress, making it ideal for high-performance applications. **Machining** follows casting or forging to refine the wheel's shape and add detailed features such as bolt holes and valve stem holes. Advanced machining technologies like CNC (Computer Numerical Control) machining ensure precision and consistency in every wheel produced. **Finishing** processes are equally important as they enhance both the appearance and durability of alloy wheels. Techniques such as polishing, anodizing, and powder coating are employed to protect the surface from corrosion and add a visually appealing finish. Anodizing, for example, involves an electrochemical process that forms a protective oxide layer on the surface of the aluminum alloy. In recent years, **3D printing** has emerged as an innovative technology in manufacturing alloy wheels. This method allows for complex geometries that cannot be achieved through traditional casting or forging methods. It also enables rapid prototyping and customization, making it particularly useful for niche or bespoke wheel designs. **Quality Control** is an integral part of the manufacturing process to ensure that every alloy wheel meets safety and performance standards. Advanced inspection technologies such as X-ray computed tomography (CT) scans and ultrasonic testing are used to detect any internal defects or irregularities. In addition to these techniques, **sustainability** has become a growing concern in the manufacturing sector. Efforts are being made to reduce energy consumption and waste generation during the production process. Recycling programs for aluminum alloys are also being implemented to minimize environmental impact. Overall, the combination of traditional manufacturing techniques with cutting-edge technologies ensures that alloy wheels are not only aesthetically pleasing but also robust and reliable. These advancements continue to drive innovation in the automotive industry, enabling the creation of high-performance wheels that meet the demands of modern vehicles.
Quality Control and Testing Methods
Quality control and testing methods are pivotal components in the production of alloy wheels, ensuring these critical automotive components meet stringent safety, performance, and aesthetic standards. Within the context of materials and manufacturing processes, quality control begins at the raw material stage. Suppliers of aluminum or magnesium alloys must adhere to strict specifications regarding chemical composition, purity, and physical properties. Once these materials are received, they undergo rigorous inspection for any defects or impurities that could compromise the integrity of the final product. The manufacturing process itself involves several key stages where quality control is paramount. For instance, during the casting phase, molten metal is poured into molds under controlled conditions to prevent porosity or other defects. Post-casting, wheels are inspected for any visible imperfections before proceeding to machining operations. Here, precise cutting tools and CNC machines are used to achieve the desired shape and finish, with continuous monitoring to ensure dimensional accuracy and surface quality. Mechanical testing is another crucial aspect of quality control in alloy wheel production. Tensile strength, impact resistance, and fatigue tests are conducted to verify that the wheels can withstand various loads and stresses encountered on the road. These tests simulate real-world conditions such as cornering forces, braking loads, and impact from road hazards. Additionally, wheels are subjected to dynamic testing on specialized equipment like radial fatigue machines and impact testers to ensure they comply with international standards such as those set by the Society of Automotive Engineers (SAE) or the European Tyre and Rim Technical Organisation (ETRTO). Aesthetic quality is also a significant factor, particularly since alloy wheels are often considered a styling element for vehicles. Visual inspections are performed to check for any surface blemishes or irregularities in finish. Advanced techniques like X-ray fluorescence (XRF) may be employed to verify the chemical composition of coatings and ensure they meet regulatory requirements regarding heavy metal content. Furthermore, environmental testing is essential to guarantee that alloy wheels can endure diverse climatic conditions without degradation. This includes exposure to extreme temperatures, humidity, and salt spray to simulate corrosion resistance. Such comprehensive testing ensures that alloy wheels not only perform optimally but also maintain their appearance over time. In conclusion, the integration of robust quality control and testing methods throughout the materials selection and manufacturing process of alloy wheels is indispensable. These measures collectively ensure that alloy wheels are safe, durable, and visually appealing, thereby enhancing overall vehicle performance and customer satisfaction. By adhering to these stringent standards, manufacturers can produce high-quality alloy wheels that meet or exceed industry benchmarks, ultimately contributing to a safer and more reliable driving experience.
Benefits and Applications of Alloy Wheels
Alloy wheels have revolutionized the automotive industry by offering a multitude of benefits that enhance both the performance and aesthetic appeal of vehicles. These high-quality wheels are crafted from a blend of metals, typically aluminum or magnesium, which provides significant advantages over traditional steel wheels. One of the primary benefits of alloy wheels is their ability to improve performance and handling. By being lighter and stronger, they reduce unsprung weight, leading to better acceleration, braking, and cornering capabilities. Additionally, alloy wheels offer unparalleled aesthetic appeal, allowing for a wide range of customization options that can transform the look of any vehicle. Their sleek designs and various finishes make them a popular choice for car enthusiasts seeking to personalize their vehicles. However, it is also important to consider the durability and maintenance aspects of alloy wheels, as they require specific care to maintain their longevity. By understanding these facets, drivers can fully appreciate the comprehensive benefits that alloy wheels bring to their driving experience. Let's delve into how alloy wheels specifically enhance performance and handling improvements.
Performance and Handling Improvements
Performance and handling improvements are among the most significant benefits of alloy wheels, making them a preferred choice for both everyday drivers and performance enthusiasts. Unlike traditional steel wheels, alloy wheels are crafted from a combination of metals such as aluminum and magnesium, which offer superior strength-to-weight ratios. This lighter yet stronger construction reduces the overall weight of the vehicle, leading to enhanced acceleration and braking performance. The reduced unsprung mass of alloy wheels also improves suspension dynamics, allowing for better shock absorption and more precise handling. This results in a smoother ride and improved stability, particularly during cornering and braking maneuvers. Moreover, alloy wheels are designed to dissipate heat more efficiently than steel wheels. This is crucial for high-performance driving where excessive heat can lead to brake fade and reduced tire performance. The enhanced heat dissipation capabilities of alloy wheels help maintain optimal brake and tire temperatures, ensuring consistent performance even under demanding conditions. Additionally, the aerodynamic design of many alloy wheels can improve airflow around the wheel and brake components, further contributing to better cooling and reduced drag. The improved handling characteristics of alloy wheels are also attributed to their ability to maintain precise contact with the road surface. The lighter and more responsive nature of these wheels allows for quicker steering response and better traction, making them ideal for both urban driving and high-speed cruising. Furthermore, the aesthetic appeal of alloy wheels often includes intricate designs that not only enhance the visual appeal of a vehicle but also contribute to improved aerodynamics. In practical terms, these performance and handling improvements translate into a more enjoyable and safer driving experience. For instance, the enhanced braking capabilities provided by alloy wheels can significantly reduce stopping distances, which is particularly important in emergency situations. Similarly, the improved handling and stability offered by these wheels can help drivers navigate challenging road conditions with greater confidence and control. Overall, the performance and handling benefits of alloy wheels make them an attractive option for anyone seeking to enhance their vehicle's capabilities. Whether you are a casual driver looking for improved everyday performance or a performance enthusiast pushing the limits of your vehicle, alloy wheels offer a compelling combination of strength, lightness, and design that can elevate your driving experience to new heights.
Aesthetic Appeal and Customization Options
Aesthetic appeal and customization options are pivotal benefits of alloy wheels, significantly enhancing the overall look and personalization of a vehicle. Unlike traditional steel wheels, alloy wheels offer a sleek, modern design that can instantly elevate the visual appeal of any car. The diverse range of styles, from sleek and minimalist to bold and aggressive, allows car owners to choose wheels that perfectly align with their personal taste and the vehicle's design. For instance, alloy wheels can be finished in various colors and textures, such as chrome, matte black, or polished silver, providing endless possibilities for customization. This versatility ensures that drivers can match their wheels to their car's exterior color scheme or contrast them for a striking visual effect. Moreover, alloy wheels are often lighter than their steel counterparts, which not only improves fuel efficiency but also enhances handling and performance. This lightweight construction allows for better heat dissipation, reducing the risk of brake overheating during high-performance driving. Additionally, the reduced unsprung weight of alloy wheels improves suspension dynamics, leading to a smoother ride and more responsive steering. Customization extends beyond aesthetics; it also includes functional enhancements. For example, alloy wheels can be designed with specific offsets and bolt patterns to accommodate different tire sizes and types. This flexibility is particularly beneficial for car enthusiasts who may want to upgrade their tires for improved traction or performance. Furthermore, some alloy wheels are engineered with advanced materials and technologies that enhance durability and strength, making them suitable for various driving conditions. The ability to personalize alloy wheels also reflects in their compatibility with various vehicle models. Whether you own a sports car, an SUV, or a sedan, there are alloy wheels designed to fit your vehicle's specifications. This universality makes alloy wheels an attractive option for car owners looking to upgrade their vehicle's appearance without compromising on functionality. In conclusion, the aesthetic appeal and customization options of alloy wheels make them a highly desirable upgrade for any vehicle. By offering a wide range of styles, finishes, and functional enhancements, alloy wheels allow car owners to tailor their vehicle's appearance and performance to their unique preferences. This blend of form and function underscores why alloy wheels are a popular choice among car enthusiasts and everyday drivers alike, enhancing both the visual appeal and driving experience of their vehicles.
Durability and Maintenance Considerations
When considering the benefits and applications of alloy wheels, durability and maintenance are crucial factors that should not be overlooked. Alloy wheels, known for their lightweight yet robust construction, offer significant advantages over traditional steel wheels in terms of performance and aesthetics. However, to fully leverage these benefits, it is essential to understand the durability and maintenance requirements associated with alloy wheels. ### Durability Considerations Alloy wheels are generally more durable than steel wheels due to their higher strength-to-weight ratio. This means they can withstand the rigors of daily driving, including potholes and minor impacts, without sustaining significant damage. The materials used in alloy wheels, such as aluminum or magnesium alloys, are resistant to corrosion and can maintain their structural integrity over time. However, it is important to note that while alloy wheels are durable, they are not indestructible. Severe impacts or improper handling can lead to damage such as cracks or bends, which may necessitate costly repairs or replacement. ### Maintenance Considerations Proper maintenance is key to extending the lifespan of alloy wheels. Regular cleaning is essential to prevent the buildup of brake dust and road grime, which can cause pitting and discoloration if left unchecked. A mild soap solution and a soft cloth are recommended for cleaning alloy wheels to avoid scratching the surface. Additionally, avoiding harsh chemicals and abrasive cleaners is crucial as they can damage the finish and compromise the wheel's integrity. Another critical aspect of maintenance involves checking tire pressure regularly. Properly inflated tires distribute weight evenly across the wheel, reducing the risk of uneven wear and potential damage to the wheel itself. It is also important to ensure that the vehicle's suspension system is in good condition, as misaligned or worn-out components can put undue stress on the wheels. ### Protective Measures To further enhance durability and reduce maintenance needs, several protective measures can be taken. Applying a wheel sealant or wax can provide an additional layer of protection against environmental elements and road debris. These coatings help repel dirt and grime, making cleaning easier and reducing the risk of corrosion. Moreover, using wheel spacers or hub rings can help distribute stress more evenly across the wheel, particularly in vehicles that are subject to heavy loads or extreme driving conditions. These accessories can also improve handling and stability by ensuring proper alignment between the wheel and hub. ### Conclusion In conclusion, while alloy wheels offer numerous benefits in terms of performance and aesthetics, their durability and maintenance requirements should not be underestimated. By understanding these considerations and implementing proper maintenance practices, vehicle owners can ensure that their alloy wheels remain in excellent condition for years to come. Regular cleaning, proper tire inflation, and protective measures such as wheel sealants all contribute to extending the lifespan of alloy wheels. By taking these steps, drivers can fully appreciate the advantages of alloy wheels while minimizing potential drawbacks. This holistic approach to durability and maintenance underscores the value of alloy wheels as a superior choice for modern vehicles.