What Is A Dead Load

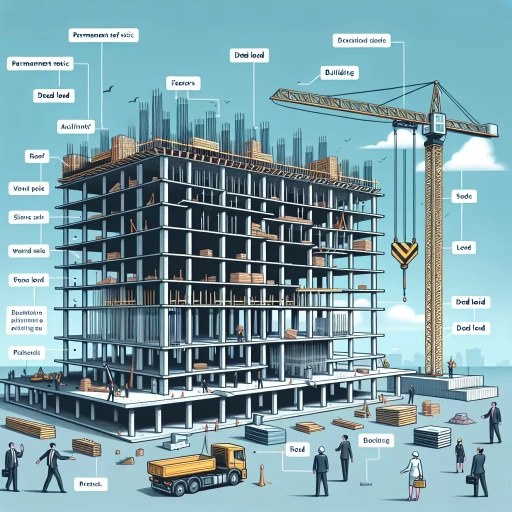
In the realm of structural engineering and architecture, understanding the various loads that act upon a building is crucial for ensuring safety, stability, and longevity. Among these loads, the dead load stands out as a fundamental concept that engineers must grasp to design and construct robust structures. A dead load refers to the permanent weight of a building's components, including walls, floors, roofs, and other structural elements. This article delves into the intricacies of dead loads, beginning with **Understanding the Concept of Dead Load**, where we explore the definition and significance of dead loads in building design. We then examine **Components and Types of Dead Loads**, detailing the different elements that contribute to this weight. Finally, we discuss **Calculation and Considerations for Dead Loads**, highlighting the methods and factors involved in accurately determining these loads. By understanding these aspects, engineers can better design structures that withstand the constant stresses imposed by their own weight, ensuring the integrity and durability of the building. Let's start by **Understanding the Concept of Dead Load**.
Understanding the Concept of Dead Load
Understanding the concept of dead load is crucial for anyone involved in structural engineering, as it forms the foundation of safe and efficient building design. This article delves into three key aspects that provide a comprehensive understanding of dead load: its definition and explanation, historical context and development, and its importance in structural engineering. First, we will explore the definition and explanation of dead load, which refers to the permanent weight of a structure itself, including all its components such as walls, floors, and roofs. This understanding is essential for calculating the total load that a structure must support. Next, we will examine the historical context and development of dead load calculations, tracing how our understanding has evolved over time with advancements in materials and construction techniques. Finally, we will discuss the importance of dead load in structural engineering, highlighting how accurate calculations ensure the stability and longevity of buildings. By grasping these elements, engineers can design structures that are both functional and safe. Let us begin by defining and explaining what dead load is, laying the groundwork for a deeper exploration of its significance.
Definition and Explanation
**Understanding the Concept of Dead Load** In the realm of structural engineering, the term "dead load" is a fundamental concept that plays a crucial role in designing and constructing buildings, bridges, and other infrastructure. **Definition and Explanation**: Dead load refers to the permanent weight of a structure itself, including all its components such as walls, floors, roofs, beams, columns, and any other permanent fixtures. This load is constant over time and does not vary with the use or occupancy of the structure. Unlike live loads which are temporary and can change (e.g., people, furniture, vehicles), dead loads are static and predictable. For instance, in a residential building, the dead load would include the weight of the concrete foundation, brick walls, wooden floors, roofing materials, and any built-in fixtures like plumbing and electrical systems. Understanding dead load is essential because it directly influences the structural integrity and safety of a building. Engineers must accurately calculate dead loads to ensure that the structure can support its own weight without collapsing or suffering from excessive deformation. This calculation involves summing up the weights of all permanent elements based on their material densities and dimensions. For example, if a building has a concrete slab floor with a thickness of 10 cm and an area of 100 square meters, the dead load contributed by this slab would be calculated by multiplying the volume of the slab by the density of concrete. The significance of dead load extends beyond mere structural stability; it also impacts other critical aspects such as foundation design and soil bearing capacity. A structure's foundation must be able to transfer its dead load safely to the ground without causing settlement or failure. Therefore, engineers often conduct soil tests to determine the soil's bearing capacity before finalizing foundation designs. Moreover, dead loads are integral to compliance with building codes and standards which mandate minimum load-carrying capacities for various types of structures. These codes typically provide guidelines for estimating dead loads based on common building materials and configurations. In summary, dead load is a critical component in structural analysis that represents the permanent weight of a structure's components. Accurate estimation and consideration of dead loads are vital for ensuring the safety, durability, and compliance of buildings with regulatory standards. By understanding what constitutes dead load and how it affects structural design, engineers can create robust and reliable infrastructure that withstands the test of time.
Historical Context and Development
The concept of dead load, a fundamental principle in structural engineering, has its roots deeply embedded in the historical context of building design and construction. The understanding and calculation of dead loads have evolved significantly over centuries, reflecting advancements in materials, architectural styles, and engineering techniques. In ancient civilizations such as Egypt, Greece, and Rome, builders recognized the importance of considering the weight of structures themselves when designing monumental architecture. For instance, the construction of the Great Pyramid of Giza required meticulous planning to ensure that the massive stone blocks could support their own weight without collapsing. Similarly, Greek and Roman architects developed sophisticated methods to distribute loads evenly across their structures, often using arches and vaults to manage weight effectively. The Middle Ages saw the rise of Gothic architecture, where intricate stone carvings and soaring vaults necessitated a deeper understanding of load distribution. Builders began to use empirical methods to estimate the weight of their structures, often relying on trial and error to achieve stability. The Renaissance period brought about a resurgence in classical knowledge, leading to more systematic approaches to structural analysis. The Industrial Revolution marked a significant turning point in the development of dead load calculations. With the introduction of new materials like steel and concrete, engineers needed precise methods to determine the loads these materials could withstand. The work of pioneers such as Leonhard Euler and Claude-Louis Navier laid the groundwork for modern structural analysis by introducing mathematical models that could predict how structures would behave under various loads. In the 20th century, the advent of computer-aided design (CAD) and finite element analysis (FEA) revolutionized the field by enabling engineers to simulate complex load scenarios with unprecedented accuracy. This allowed for more efficient and safer designs, particularly in high-rise buildings and large-scale infrastructure projects. Today, understanding dead loads is crucial for ensuring the safety and durability of structures. Engineers use detailed calculations that account for every component of a building's weight, from the foundation to the roofing material. This includes not only the permanent elements but also any permanent fixtures such as plumbing and electrical systems. The accuracy of these calculations is paramount; miscalculations can lead to catastrophic failures, as seen in historical examples like the collapse of the Tacoma Narrows Bridge in 1940. In summary, the concept of dead load has evolved from empirical observations in ancient times to sophisticated mathematical models and computational simulations today. This historical context underscores the importance of precise calculations in modern engineering practices, ensuring that structures are designed to safely support their own weight and endure over time. Understanding this concept is essential for anyone involved in the design, construction, or maintenance of buildings and infrastructure.
Importance in Structural Engineering
**Importance in Structural Engineering** Understanding the concept of dead load is crucial in structural engineering, as it directly impacts the safety, durability, and overall performance of buildings and infrastructure. Dead load, which includes the weight of the structure itself along with permanent fixtures such as walls, floors, and roofing materials, forms a significant portion of the total load that a structure must support. Accurate calculation and consideration of dead load are essential for several reasons. Firstly, dead load affects the structural integrity of a building. If the dead load is underestimated or miscalculated, it can lead to inadequate design and construction, potentially resulting in structural failures. This could compromise the safety of occupants and users, making it a critical factor in ensuring compliance with building codes and standards. For instance, underestimating the weight of roofing materials during a design phase might result in insufficient support from beams and columns, leading to catastrophic failures during extreme weather conditions. Secondly, dead load influences the long-term durability of structures. Properly accounting for dead load helps engineers design structures that can withstand various environmental conditions over time. For example, in regions prone to earthquakes or high winds, accurately calculating dead load ensures that the structure can resist these forces without suffering significant damage. This not only extends the lifespan of the structure but also reduces maintenance costs by minimizing the need for frequent repairs. Thirdly, understanding dead load is vital for optimizing structural design and resource allocation. By precisely determining the dead load, engineers can optimize material usage without compromising safety. This leads to more efficient use of resources, reducing construction costs while maintaining structural integrity. For instance, in high-rise buildings where every kilogram of material adds to the overall weight and cost, accurate dead load calculations can help in selecting appropriate materials that balance between strength and weight. Furthermore, dead load plays a significant role in sustainability and energy efficiency. Buildings designed with accurate dead load considerations can be more energy-efficient as they require less material for support, which in turn reduces the carbon footprint associated with material production and transportation. Additionally, structures that are well-designed to handle their dead load can incorporate more sustainable features such as green roofs or solar panels without compromising their stability. In conclusion, the importance of understanding dead load in structural engineering cannot be overstated. It is a fundamental aspect that ensures safety, durability, efficiency, and sustainability in building design and construction. By accurately calculating and considering dead load, engineers can create structures that are not only safe but also cost-effective and environmentally friendly, ultimately contributing to better infrastructure development.
Components and Types of Dead Loads
When discussing the components and types of dead loads, it is crucial to understand the various elements that contribute to the overall weight of a structure. Dead loads are the permanent weights that a building must support, and they can be categorized into several key components. First, there are the permanent structural elements, such as beams, columns, and foundations, which form the backbone of the structure. These elements are essential for the stability and integrity of the building. Additionally, non-structural elements and finishes, including walls, floors, ceilings, and roofing materials, also contribute significantly to the dead load. These components, while not part of the primary structural framework, are vital for the functionality and aesthetic appeal of the building. Lastly, specialized dead loads in unique structures, such as those found in industrial facilities or historic buildings, require special consideration due to their unique characteristics. Understanding these different types of dead loads is fundamental for engineers and architects to ensure that structures are designed and constructed safely and efficiently. By delving into each of these categories, we can gain a comprehensive insight into the complexities of dead loads, starting with the foundational aspect of permanent structural elements.
Permanent Structural Elements
When discussing the components and types of dead loads, it is crucial to delve into the realm of permanent structural elements. These elements are integral to the overall stability and integrity of a building, contributing significantly to the dead load that the structure must bear. Permanent structural elements include walls, floors, roofs, beams, columns, and foundations. Each of these components plays a vital role in distributing and supporting the weight of the building itself as well as any additional loads such as live loads (people, furniture) and environmental loads (wind, snow). **Walls**, for instance, are a primary structural component that not only provide enclosure but also bear the weight of floors and roofs. They can be made from various materials such as concrete, masonry, steel studs with drywall, or even wood framing. The choice of material influences the dead load significantly; for example, concrete walls are heavier than those made from wood framing. **Floors** and **roofs** are another critical set of permanent structural elements. Floors support the weight of occupants and their activities while roofs protect against environmental elements like rain and snow. These surfaces are typically composed of materials such as concrete slabs, wooden joists with decking, or steel beams with metal decking. The dead load from these components includes not just the material weight but also any finishes like flooring materials or roofing tiles. **Beams** and **columns** form the skeletal framework of a building's structure. Beams span between columns to support floors and roofs while columns transfer these loads down to the foundation. These elements are often made from steel or reinforced concrete and contribute substantially to the dead load due to their material density. The **foundation** is perhaps the most critical permanent structural element as it transfers all loads from the building to the ground. Foundations can be shallow (like spread footings) or deep (like piles), depending on soil conditions and load requirements. The weight of the foundation itself adds to the dead load, ensuring that it can adequately support the entire structure above it. Understanding these permanent structural elements is essential for engineers and architects when designing buildings because they directly impact the overall dead load calculation. Accurate estimation of dead loads ensures that structures are designed with sufficient strength and stability to withstand various types of loads without compromising safety or performance. In summary, permanent structural elements are fundamental in defining a building's dead load profile, and their careful selection and design are pivotal in ensuring structural integrity over time.
Non-Structural Elements and Finishes
Non-structural elements and finishes play a crucial role in the overall design, functionality, and aesthetic appeal of a building, while also contributing to the dead load that structural engineers must account for. Dead loads are the permanent weights of the building itself, including all components that are not part of the structural system but are integral to its completion. Non-structural elements such as walls, partitions, doors, windows, and finishes like flooring, ceilings, and interior cladding are essential for creating a habitable space but do not bear loads or transfer forces to the structural system. ### Types of Non-Structural Elements 1. **Walls and Partitions**: These are critical for dividing spaces within a building and providing privacy. Exterior walls may be load-bearing or non-load-bearing, but interior partitions are typically non-structural. Materials used can range from drywall to glass or metal studs with various finishes. 2. **Doors and Windows**: These elements allow for entry, exit, and natural light. While they do not contribute to the structural integrity of the building, their weight must be included in dead load calculations. 3. **Finishes**: This category includes flooring (such as hardwood, carpet, tile), ceilings (like drop ceilings or suspended ceilings), and interior cladding (such as paint, wallpaper, or paneling). Each type of finish has its own weight per square foot that needs to be factored into the overall dead load. ### Importance in Dead Load Calculations When calculating dead loads, engineers must consider the weight of all non-structural elements because they contribute significantly to the total weight of the building. For instance: - **Flooring**: Different types of flooring have varying weights; for example, ceramic tile is heavier than carpet. - **Ceilings**: Suspended ceilings with acoustic tiles can add substantial weight compared to drywall ceilings. - **Walls**: The material used for walls—whether it's drywall, brick veneer, or glass—significantly impacts the dead load. ### Impact on Building Design The selection of non-structural elements and finishes not only affects aesthetics but also influences structural design decisions. For example: - **Material Selection**: Choosing lighter materials for finishes can reduce the overall dead load on a structure, potentially allowing for smaller structural members. - **Load Distribution**: Ensuring that non-structural elements are evenly distributed across floors helps in maintaining uniform loading conditions which are crucial for structural stability. ### Best Practices To ensure accurate dead load calculations: 1. **Detailed Specifications**: Engineers should have detailed specifications of all materials used in non-structural elements. 2. **Weight Estimations**: Use standardized weights for common materials but also consider specific product weights where available. 3. **Regular Updates**: Keep calculations updated as design changes occur during the construction process. In summary, non-structural elements and finishes are vital components of a building that contribute to its functionality and appearance while adding to its dead load. Accurate accounting for these elements is essential for ensuring the structural integrity and safety of the building. By understanding their types, importance in dead load calculations, and impact on building design, engineers can make informed decisions that balance aesthetics with structural requirements.
Specialized Dead Loads in Unique Structures
In the realm of structural engineering, dead loads are a critical consideration, and certain unique structures require special attention due to their specialized dead loads. These loads are not just limited to the weight of the building materials but also include other permanent elements that contribute to the overall weight of the structure. For instance, in high-rise buildings, the dead load includes not only the weight of the walls, floors, and roof but also the weight of elevators, staircases, and even the plumbing and HVAC systems. In bridges, specialized dead loads can include the weight of the bridge deck, railings, and any integrated lighting or surveillance systems. In historic buildings or those with unique architectural features, such as grand chandeliers or intricate stone carvings, these elements add significant dead load that must be accounted for during design and construction. Similarly, in industrial facilities like power plants or chemical processing units, heavy machinery and equipment contribute substantial dead loads that need careful consideration to ensure structural integrity. Theaters and concert halls present another example where specialized dead loads are crucial. Here, the weight of stage equipment, lighting rigs, and seating areas must be precisely calculated to avoid any structural compromise. In addition, structures like museums with heavy exhibits or libraries with extensive book collections also have unique dead load requirements that engineers must address. Moreover, modern green buildings with extensive green roofs or solar panel installations introduce additional dead loads due to the weight of soil, plants, and solar panels. These loads are not only static but can also vary with weather conditions, such as snow accumulation on roofs in colder climates. Understanding and accurately calculating these specialized dead loads are essential for ensuring the safety and longevity of unique structures. Engineers use advanced software and meticulous calculations to account for every component that contributes to the dead load, ensuring that the structure can withstand its own weight without compromising its stability or integrity. This meticulous approach not only safeguards against structural failures but also optimizes the use of materials, reducing unnecessary costs while maintaining the aesthetic and functional integrity of the building. In summary, specialized dead loads in unique structures demand a detailed and nuanced approach to ensure that all permanent elements are considered in the design process. By recognizing and accurately accounting for these loads, engineers can create structures that are both safe and functional, meeting the specific needs of their intended use while adhering to stringent safety standards. This attention to detail is paramount in ensuring that these unique structures stand the test of time without compromising on performance or safety.
Calculation and Considerations for Dead Loads
When it comes to structural engineering, the calculation and consideration of dead loads are paramount for ensuring the safety and integrity of buildings and other structures. Dead loads, which include the weight of the structure itself along with permanent fixtures and materials, must be accurately assessed to prevent structural failures. This article delves into the critical aspects of dead load calculations, beginning with **Methods for Estimating Dead Load**, where we explore various techniques and tools used to determine these loads. We also examine **Factors Influencing Dead Load Calculations**, highlighting how different materials, design choices, and environmental conditions can impact these calculations. Additionally, we discuss **Best Practices for Accurate Assessment**, providing insights into how engineers can ensure their calculations are precise and reliable. By understanding these key components, engineers can make informed decisions that safeguard against potential risks. Let's start by exploring the various methods available for estimating dead loads, a foundational step in any structural analysis.
Methods for Estimating Dead Load
When calculating dead loads, engineers and architects employ several methods to ensure accuracy and compliance with structural integrity standards. One of the primary methods is the **Weight Density Method**, where the dead load is estimated by multiplying the volume of the material by its unit weight. This approach is particularly useful for homogeneous materials such as concrete, steel, and wood. For instance, if a concrete slab has a thickness of 0.15 meters and covers an area of 100 square meters, and knowing that the unit weight of concrete is approximately 2400 kg/m³, the dead load can be calculated as 0.15 m * 100 m² * 2400 kg/m³ = 36,000 kg or 36 tons. Another method is the **Component Weight Method**, which involves summing up the weights of individual components such as beams, columns, floors, and walls. This method is more detailed and often used in complex structures where different materials are involved. For example, in a multi-story building, the dead load would include the weight of each floor slab, beams, columns, walls, and any permanent fixtures like staircases and elevators. Each component's weight is calculated separately and then summed to obtain the total dead load. The **Load Factor Method** is also commonly used, especially in design codes like ASCE 7 and Eurocode. This method involves applying load factors to account for uncertainties in material properties and construction practices. For instance, a load factor might be applied to the calculated dead load to ensure that the structure can withstand potential variations in material densities or construction tolerances. In addition to these methods, **Computer-Aided Design (CAD) Software** and **Building Information Modeling (BIM)** tools are increasingly being used to estimate dead loads with high precision. These tools allow for detailed modeling of structures and automatic calculation of volumes and weights based on material properties inputted into the system. This not only streamlines the process but also reduces errors associated with manual calculations. Furthermore, **Standard Tables and Charts** provided by various engineering societies and building codes can be a quick reference for estimating dead loads. These tables typically list the average unit weights of common building materials, making it easier to perform preliminary calculations during the design phase. It is crucial to consider several factors when estimating dead loads, including the moisture content of materials, which can affect their weight over time. For example, wood and soil can absorb moisture, increasing their weight. Additionally, the presence of finishes such as flooring, roofing materials, and ceilings must be accounted for as they contribute significantly to the overall dead load. In summary, estimating dead loads involves a combination of precise calculations using various methods tailored to the specific structure being designed. By leveraging these methods—whether through traditional weight density and component weight calculations or advanced CAD/BIM tools—and considering all relevant factors, engineers can ensure that structures are designed to safely support their permanent loads over their lifespan.
Factors Influencing Dead Load Calculations
When calculating dead loads, several critical factors must be considered to ensure the structural integrity and safety of a building. **Material Density** is a primary factor, as it directly influences the weight of the structure. Different materials such as concrete, steel, wood, and masonry have varying densities, which must be accurately accounted for in calculations. For instance, reinforced concrete has a higher density compared to wood, significantly impacting the overall dead load. **Geometric Dimensions** of the structure are another crucial aspect. The size and shape of beams, columns, floors, and walls all contribute to the total dead load. Precise measurements are essential to avoid underestimation or overestimation of loads, which could lead to structural failures or unnecessary costs. Additionally, **Thickness and Depth** of structural elements like slabs and walls must be accurately determined to calculate their weight correctly. **Finishing Elements** such as roofing materials, flooring systems, and wall finishes also play a significant role. The weight of roofing materials like asphalt shingles, metal roofing, or clay tiles varies widely and must be included in dead load calculations. Similarly, flooring systems including concrete slabs, wooden floors, or ceramic tiles add to the overall weight. Wall finishes like drywall, plaster, or brick veneer further contribute to the dead load. **Partition Walls and Permanent Fixtures** are often overlooked but are important components of dead loads. Partition walls used to divide spaces within a building can be made from various materials and contribute significantly to the total weight. Permanent fixtures such as built-in cabinets, shelving units, and plumbing fixtures also need to be considered in these calculations. **Soil and Foundation Conditions** can indirectly affect dead load calculations by influencing the design of the foundation system. For example, in areas with poor soil conditions, deeper or more robust foundations may be required, increasing the overall dead load. Understanding these conditions helps engineers design foundations that can support both the dead load and any additional loads without compromising structural stability. **Building Codes and Standards** provide guidelines for minimum load requirements but may not cover all specific scenarios. Engineers must adhere to these standards while also considering local regulations and environmental factors that could impact the structure's weight distribution. For instance, areas prone to high winds or seismic activity may require additional structural elements that add to the dead load. In summary, accurate dead load calculations depend on a comprehensive understanding of material properties, geometric dimensions, finishing elements, partition walls, permanent fixtures, soil conditions, and adherence to building codes. Each factor contributes uniquely to the total weight of a structure, and meticulous consideration of these elements ensures that buildings are designed with safety and durability in mind. By integrating these factors into the calculation process, engineers can provide reliable and efficient structural designs that meet both functional and safety requirements.
Best Practices for Accurate Assessment
When it comes to the accurate assessment of dead loads in structural engineering, adhering to best practices is paramount to ensure the integrity and safety of buildings. Dead loads, which include the weight of the structure itself along with permanent fixtures such as walls, floors, and roofing materials, must be calculated with precision. Here are some key best practices to consider: 1. **Detailed Documentation**: Maintain meticulous records of all materials used in construction, including their densities and dimensions. This documentation should be readily accessible for future reference and updates. 2. **Material Specifications**: Ensure that all materials meet or exceed the specifications outlined in relevant building codes and standards. This includes verifying the density of materials through testing if necessary. 3. **Load Distribution**: Understand how dead loads are distributed across the structure. For instance, the weight of a roof may not be evenly distributed due to variations in material thickness or the presence of skylights and vents. 4. **Component Weight**: Break down the structure into its constituent parts and calculate the weight of each component separately. This includes not only the primary structural elements but also secondary components like finishes and fixtures. 5. **Consideration of Connections**: The connections between different structural elements can affect how loads are transferred and distributed. Ensure that these connections are accounted for in your calculations. 6. **Use of Standardized Tables**: Utilize standardized tables and charts provided by professional organizations such as the American Society of Civil Engineers (ASCE) or the International Code Council (ICC) to streamline calculations and ensure accuracy. 7. **Software Tools**: Leverage advanced software tools designed for structural analysis to perform complex calculations efficiently and accurately. These tools can help in simulating various load scenarios and identifying potential stress points. 8. **Peer Review**: Have your calculations reviewed by a peer or a senior engineer to catch any potential errors or oversights. This step is crucial in ensuring that all aspects have been considered. 9. **Regular Updates**: Keep your knowledge and methods up-to-date with the latest research, technologies, and code revisions. This ensures that your assessments remain accurate and compliant with current standards. 10. **Field Verification**: Whenever possible, conduct field measurements to verify the actual weights of materials used in construction against theoretical values. This step helps in validating the accuracy of your initial assessments. By following these best practices, engineers can ensure that their assessments of dead loads are accurate, comprehensive, and reliable, thereby safeguarding the structural integrity of buildings and protecting public safety. Accurate dead load calculations form the foundation upon which all other load calculations are built; hence, their precision is indispensable in the design process.