What Is A Dcs

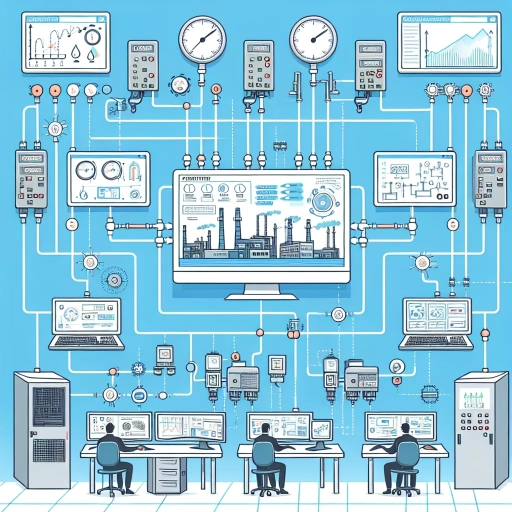
A Distributed Control System (DCS) is a sophisticated technology that plays a crucial role in modern industrial processes. At its core, a DCS is designed to manage and control various aspects of production, ensuring efficiency, reliability, and safety. This article delves into the multifaceted world of DCS, starting with **Understanding the Basics of DCS**, where we explore the fundamental components and operational principles that underpin these systems. We then examine **Applications and Industries Using DCS**, highlighting how diverse sectors such as power generation, chemical processing, and oil refining leverage DCS to optimize their operations. Finally, we discuss **Advantages and Future Trends of DCS**, outlining the benefits these systems offer and the innovations that are shaping their future. By grasping these key aspects, readers will gain a comprehensive understanding of what a DCS is and its significance in contemporary industrial environments. Let's begin by understanding the basics of DCS.
Understanding the Basics of DCS
Understanding the basics of Distributed Control Systems (DCS) is crucial for anyone involved in industrial automation and process control. A DCS is a sophisticated system that integrates various components to manage and monitor complex processes in real-time. To grasp the fundamentals of DCS, it is essential to delve into three key areas: **Definition and History**, **Key Components and Architecture**, and **Primary Functions and Objectives**. Starting with **Definition and History**, we explore how DCS evolved from earlier control systems, such as centralized control systems, to become the robust and decentralized solutions we see today. This historical context provides a solid foundation for understanding the development and significance of DCS in modern industrial settings. Next, examining **Key Components and Architecture** reveals the intricate structure of a DCS, including its hardware and software elements, communication networks, and user interfaces. This section highlights how these components work together seamlessly to ensure efficient process control. Finally, understanding **Primary Functions and Objectives** clarifies the role of DCS in optimizing process performance, enhancing safety, and improving overall plant efficiency. By focusing on these core aspects, one can appreciate the critical role DCS plays in contemporary industrial operations. To begin our journey into the world of DCS, let's first explore its **Definition and History**.
Definition and History
**Definition and History** A Distributed Control System (DCS) is a sophisticated control system that integrates various components and subsystems to manage and monitor industrial processes. At its core, a DCS is designed to distribute control functions across multiple nodes or stations, enhancing reliability, flexibility, and scalability. This system architecture allows for real-time data acquisition, processing, and control, making it indispensable in modern industrial environments. Historically, the evolution of DCS began in the 1970s as a response to the limitations of earlier control systems such as Programmable Logic Controllers (PLCs) and Supervisory Control and Data Acquisition (SCADA) systems. The first DCS systems were introduced by companies like Honeywell and Yokogawa, who recognized the need for more comprehensive and integrated control solutions. These early systems were primarily used in the oil and gas, chemical, and power generation industries where complex processes required precise control. The advent of microprocessors and advancements in communication technologies significantly enhanced the capabilities of DCS. By the 1980s, DCS had become more widespread, offering improved performance, better user interfaces, and enhanced diagnostic capabilities. The integration of Human-Machine Interfaces (HMIs) allowed operators to interact more effectively with the system, while advanced networking enabled seamless communication between different parts of the system. In the 1990s and 2000s, DCS continued to evolve with the incorporation of open standards and protocols such as Fieldbus and Ethernet. This shift towards open architectures facilitated greater interoperability among different vendors' equipment, reducing costs and increasing system flexibility. Modern DCS systems now leverage advanced technologies like cloud computing, big data analytics, and artificial intelligence to optimize process control, predict maintenance needs, and enhance overall plant efficiency. Today, DCS is a cornerstone of industrial automation, playing a critical role in ensuring the smooth operation of complex processes across various sectors. Its ability to integrate with other systems such as Enterprise Resource Planning (ERP) and Manufacturing Execution Systems (MES) further underscores its importance in modern industrial landscapes. Understanding the basics of DCS is essential for anyone involved in industrial automation, as it provides a foundational knowledge that can be applied to optimize process control, improve productivity, and ensure operational safety.
Key Components and Architecture
In the context of Distributed Control Systems (DCS), understanding the key components and architecture is crucial for grasping the fundamental principles of how these systems operate. A DCS is designed to control and monitor industrial processes, ensuring efficiency, reliability, and safety. The primary components include **Control Units**, **Input/Output (I/O) Modules**, **Communication Networks**, **Operator Stations**, and **Engineering Workstations**. - **Control Units**: These are the brain of the DCS, responsible for executing control algorithms and logic. They process data from various sensors and actuators to maintain optimal process conditions. - **Input/Output (I/O) Modules**: These modules interface with field devices such as sensors, valves, and motors. They convert analog signals from sensors into digital data for the control units and vice versa for actuators. - **Communication Networks**: DCS relies on robust communication networks to facilitate data exchange between different components. Common protocols include Ethernet, Fieldbus, and proprietary networks like Profibus or Modbus. - **Operator Stations**: These are human-machine interfaces (HMIs) where operators monitor and control the process in real-time. They display process data, alarms, and trends, allowing operators to make informed decisions. - **Engineering Workstations**: These stations are used by engineers to configure, program, and maintain the DCS. They provide tools for designing control strategies, tuning parameters, and troubleshooting issues. The architecture of a DCS is typically hierarchical and distributed. At the top level, there are **Central Control Rooms** where operator stations are located. Below this level are **Control Rooms** or **Local Control Stations** that manage specific sections of the process. The next layer consists of **Field Control Stations** which are closer to the process equipment and house control units and I/O modules. Finally, at the field level, there are **Field Devices** such as sensors and actuators that interact directly with the process. This hierarchical structure allows for decentralized control while maintaining centralized supervision and coordination. It ensures that critical functions can continue even if one part of the system fails, enhancing overall system reliability and redundancy. Additionally, modern DCS architectures often incorporate advanced technologies like cloud connectivity, big data analytics, and cybersecurity measures to enhance performance and security. Understanding these components and their interconnections is essential for designing, implementing, and maintaining an effective DCS. It enables users to leverage the full potential of these systems in optimizing industrial processes, improving productivity, and ensuring operational safety.
Primary Functions and Objectives
In the context of Distributed Control Systems (DCS), understanding the primary functions and objectives is crucial for grasping the fundamental principles of these systems. A DCS is designed to manage and control industrial processes, ensuring efficiency, reliability, and safety. The primary functions of a DCS include **data acquisition**, where sensors and input devices collect real-time data from the process; **control**, where the system interprets this data and makes decisions based on predefined algorithms and setpoints; **monitoring**, where operators are provided with real-time information through user interfaces such as HMIs (Human-Machine Interfaces); and **reporting**, where historical data is stored and analyzed for future improvements. The objectives of a DCS are multifaceted. **Optimization** is a key objective, aiming to maximize process efficiency by minimizing waste, reducing energy consumption, and enhancing product quality. **Reliability** is another critical objective, ensuring that the system operates continuously without downtime, thereby maintaining production levels and reducing maintenance costs. **Safety** is paramount, as DCS systems are designed to detect anomalies and prevent hazardous conditions from arising. Additionally, **scalability** and **flexibility** are important objectives, allowing the system to adapt to changes in production demands or process modifications without significant reconfiguration. Furthermore, DCS systems aim to enhance **operator efficiency** by providing intuitive interfaces that simplify complex operations, reduce human error, and facilitate quick response times to process deviations. **Integration** with other systems such as SCADA (Supervisory Control and Data Acquisition) and ERP (Enterprise Resource Planning) is also a key objective, enabling seamless communication across different levels of the organization. By achieving these objectives, a DCS ensures that industrial processes operate at peak performance, contributing to overall business success and sustainability. Understanding these primary functions and objectives is essential for anyone looking to implement or manage a DCS effectively.
Applications and Industries Using DCS
The integration of Distributed Control Systems (DCS) has revolutionized various industries by enhancing efficiency, reliability, and safety. In the realm of industrial automation, DCS plays a pivotal role in manufacturing processes, ensuring precise control over production lines and optimizing resource allocation. Additionally, DCS is crucial in power generation and distribution, where it monitors and controls the flow of electricity to meet demand while minimizing downtime. Furthermore, in chemical and petrochemical processes, DCS ensures that complex reactions are managed accurately, adhering to stringent safety standards. These applications highlight the versatility and importance of DCS across different sectors. Transitioning to the specifics of industrial automation in manufacturing, it is evident that DCS has become an indispensable tool for modern factories, enabling real-time monitoring and control that significantly improves productivity and product quality. This article will delve into these applications, starting with the transformative impact of DCS on industrial automation in manufacturing.
Industrial Automation in Manufacturing
Industrial automation in manufacturing has revolutionized the production process by integrating advanced technologies to enhance efficiency, precision, and productivity. At the heart of this transformation is the Distributed Control System (DCS), which plays a crucial role in managing and optimizing various industrial processes. DCS systems are widely adopted across diverse manufacturing sectors due to their ability to centralize control, monitor operations in real-time, and automate complex tasks. In the chemical processing industry, DCS is used to control and monitor reactions, manage batch processes, and ensure safety by adhering to strict regulatory standards. For instance, in petrochemical plants, DCS systems regulate temperature, pressure, and flow rates to maintain optimal conditions for chemical reactions. Similarly, in pharmaceutical manufacturing, DCS ensures that production adheres to Good Manufacturing Practices (GMP) by maintaining precise control over temperature, humidity, and other critical parameters. In the power generation sector, DCS is essential for managing power plants efficiently. It monitors and controls boiler operations, turbine performance, and cooling systems to optimize energy output while minimizing downtime. For example, in nuclear power plants, DCS systems are critical for ensuring safety by continuously monitoring radiation levels and other vital parameters. The oil and gas industry also heavily relies on DCS for upstream and downstream operations. In refineries, DCS controls crude oil processing, distillation, and product blending. Offshore platforms use DCS to manage drilling operations, well control, and production monitoring. This ensures that operations are conducted safely and efficiently. In addition to these industries, DCS is integral in food and beverage manufacturing where it ensures consistent product quality. It controls fermentation processes in breweries, pasteurization in dairy plants, and packaging lines to maintain hygiene standards. Automotive manufacturing also benefits from DCS as it automates assembly lines, welds components precisely, and monitors quality control checks. Furthermore, DCS is crucial in water treatment plants where it manages water purification processes such as filtration, disinfection, and wastewater treatment. This ensures that water quality meets or exceeds regulatory standards. The adoption of DCS in manufacturing has led to significant improvements in operational efficiency, reduced energy consumption, enhanced product quality, and improved safety standards. By providing real-time data analytics and predictive maintenance capabilities, DCS systems help manufacturers anticipate and prevent potential issues before they occur. This proactive approach minimizes downtime and maximizes overall plant performance. In summary, the application of DCS in various manufacturing industries underscores its versatility and importance. From chemical processing to power generation and from oil and gas to food and beverage production, DCS systems are indispensable tools that drive modern industrial automation forward. Their ability to integrate multiple functions into a single platform makes them an essential component of any modern manufacturing setup aiming for excellence in efficiency and quality.
Power Generation and Distribution
Power generation and distribution are critical components of modern infrastructure, ensuring the reliable supply of electricity to various industries and households. The process begins with power generation, where electrical energy is produced from diverse sources such as fossil fuels, nuclear reactions, and renewable sources like solar, wind, and hydroelectric power. These power plants utilize sophisticated control systems, including Distributed Control Systems (DCS), to optimize efficiency, safety, and output. DCS plays a pivotal role in monitoring and controlling the entire generation process, from fuel intake to energy output, allowing for real-time adjustments and predictive maintenance. Once generated, the electricity is transmitted over long distances through high-voltage transmission lines to substations, where the voltage is stepped down for distribution. This distribution network involves a complex web of medium-voltage lines, substations, and transformers that deliver electricity to consumers. Here again, DCS is instrumental in managing the distribution grid by monitoring voltage levels, detecting faults, and automatically rerouting power to minimize outages. Advanced DCS systems integrate with smart grid technologies, enabling real-time monitoring and control of the distribution network, enhancing grid resilience and efficiency. In the context of applications and industries using DCS, power generation and distribution stand out as prime examples. Utilities and power companies rely heavily on DCS to manage their operations from generation to distribution. For instance, in thermal power plants, DCS controls the combustion process, steam generation, and turbine operation to maximize efficiency. In renewable energy facilities like wind farms or solar parks, DCS ensures optimal performance by adjusting parameters such as blade angles or panel orientations based on environmental conditions. Moreover, DCS in power distribution helps utilities manage peak demand periods effectively by dynamically adjusting power flow and load shedding strategies. This not only prevents grid overload but also ensures a stable supply of electricity to critical infrastructure such as hospitals, data centers, and emergency services. The integration of DCS with other technologies like SCADA (Supervisory Control and Data Acquisition) systems further enhances the operational efficiency of power generation and distribution networks. In summary, the role of DCS in power generation and distribution is indispensable. It ensures efficient operation, enhances safety, and improves the reliability of the electrical supply chain. As industries continue to evolve with technological advancements, the importance of robust control systems like DCS will only grow, making them a cornerstone of modern power infrastructure.
Chemical and Petrochemical Processes
Chemical and petrochemical processes are complex, highly regulated, and safety-critical operations that rely heavily on advanced control systems to ensure efficiency, quality, and safety. These processes involve the transformation of raw materials into various chemical products through reactions, separations, and other unit operations. In these environments, Distributed Control Systems (DCS) play a crucial role by providing real-time monitoring, precise control, and data analytics to optimize production. DCS systems in chemical and petrochemical plants integrate various components such as sensors, actuators, controllers, and human-machine interfaces to manage the entire production process. They enable operators to monitor and control multiple parameters simultaneously, including temperature, pressure, flow rates, and chemical composition. This comprehensive oversight allows for quick response to any deviations from setpoints or anomalies, thereby preventing accidents and ensuring product quality. One of the key applications of DCS in these industries is process optimization. By analyzing real-time data from various sensors and historical trends, DCS can adjust process conditions to maximize yield while minimizing energy consumption and waste generation. For instance, in a refinery, DCS can optimize the cracking process to produce the desired mix of petroleum products efficiently. Another critical aspect is safety. Chemical and petrochemical processes often involve hazardous materials and high-energy operations, making safety paramount. DCS systems incorporate safety protocols such as alarm management and emergency shutdown procedures to mitigate risks. For example, if a sensor detects an abnormal rise in temperature or pressure beyond safe limits, the DCS can automatically initiate corrective actions or shut down the process to prevent an accident. Additionally, DCS supports regulatory compliance by maintaining detailed records of all process activities. This is particularly important in industries subject to stringent regulations like OSHA and EPA standards. The ability to generate reports and logs helps facilities demonstrate adherence to these regulations during audits. In terms of specific industries, DCS is widely used in refineries, petrochemical plants, fertilizer production facilities, and pharmaceutical manufacturing. For example, in ethylene production plants, DCS controls the complex sequence of reactions and separations required to produce ethylene from natural gas or naphtha. Similarly, in pharmaceutical manufacturing, DCS ensures that batch processes adhere strictly to Good Manufacturing Practices (GMP) standards. Overall, the integration of DCS into chemical and petrochemical processes enhances operational efficiency, improves product quality, ensures safety, and supports regulatory compliance. As these industries continue to evolve with advancements in technology and increasing demands for sustainability and efficiency, the role of DCS will remain vital in driving innovation and excellence.
Advantages and Future Trends of DCS
The advent of Distributed Control Systems (DCS) has revolutionized industrial operations, offering a multitude of advantages that are set to shape the future of various sectors. At the heart of these benefits are three key areas: Improved Efficiency and Productivity, Enhanced Safety and Reliability, and Integration with Emerging Technologies. By leveraging DCS, industries can significantly boost their operational efficiency, reducing downtime and increasing overall productivity. This is achieved through real-time monitoring and control, allowing for swift adjustments and optimizations. Additionally, DCS enhances safety by providing robust fail-safe mechanisms and redundant systems, ensuring continuous operation even in adverse conditions. The integration of DCS with emerging technologies such as IoT, AI, and cloud computing further amplifies its potential, enabling predictive maintenance, data-driven decision-making, and seamless scalability. As we delve into the specifics, it becomes clear that one of the most compelling advantages of DCS is its ability to improve efficiency and productivity, which we will explore in greater detail next.
Improved Efficiency and Productivity
Improved efficiency and productivity are cornerstone advantages of Distributed Control Systems (DCS), significantly enhancing the operational performance of various industries. By integrating multiple control functions into a single, cohesive system, DCS streamlines processes, reduces manual intervention, and optimizes resource allocation. This integration allows for real-time monitoring and control, enabling swift responses to changes in production conditions. Automated workflows minimize human error, while advanced algorithms and predictive analytics help in anticipating and mitigating potential issues before they arise. Additionally, DCS facilitates seamless communication between different departments and stakeholders, fostering a more collaborative environment that drives innovation and continuous improvement. The scalability of DCS systems ensures that they can adapt to growing demands without compromising performance, making them an invaluable asset for future-proofing industrial operations. As technology continues to evolve, the integration of IoT, AI, and machine learning into DCS will further amplify efficiency gains, enabling more precise control, enhanced predictive maintenance, and smarter decision-making. This synergy between advanced technologies and DCS will redefine industry standards for productivity and efficiency, positioning organizations for sustained success in an increasingly competitive landscape.
Enhanced Safety and Reliability
Enhanced safety and reliability are cornerstone advantages of Distributed Control Systems (DCS) in modern industrial settings. A DCS ensures that all components of a process are monitored and controlled in real-time, significantly reducing the risk of human error and system failures. By decentralizing control functions across various nodes, DCS systems distribute the workload, making them less susceptible to single-point failures. This redundancy ensures continuous operation even if one node fails, thereby maintaining overall system integrity. Advanced diagnostic tools integrated into DCS systems enable early detection of potential issues, allowing for proactive maintenance and minimizing downtime. Real-time data analytics provide insights into system performance, helping operators identify trends and anomalies that could indicate impending problems. This predictive maintenance capability not only enhances safety by preventing unexpected shutdowns but also optimizes operational efficiency. Moreover, DCS systems are designed with robust security protocols to protect against cyber threats. Secure communication protocols and encryption methods safeguard sensitive data, ensuring that critical control functions remain uncompromised. Compliance with industry standards such as IEC 62443 for industrial automation and control systems further reinforces the reliability and security of DCS. In terms of future trends, the integration of Artificial Intelligence (AI) and Machine Learning (ML) algorithms is set to revolutionize DCS capabilities. AI-driven predictive analytics will enhance fault detection and predictive maintenance, while ML will optimize control strategies based on historical data and real-time inputs. The advent of IoT (Internet of Things) technologies will also expand the scope of DCS by enabling seamless communication between diverse devices and systems, fostering a more interconnected and intelligent industrial ecosystem. Additionally, advancements in cloud computing and edge computing will allow for greater flexibility in data processing and storage, enabling real-time analytics and faster decision-making. These technological advancements will further enhance the safety and reliability of DCS, making them an indispensable component of future industrial automation landscapes. Overall, the enhanced safety and reliability offered by DCS systems make them a critical element in ensuring the smooth, efficient, and secure operation of modern industrial processes.
Integration with Emerging Technologies
Integration with emerging technologies is a pivotal aspect of Distributed Control Systems (DCS) that significantly enhances their capabilities and future prospects. As DCS continues to evolve, it is increasingly being integrated with cutting-edge technologies such as Artificial Intelligence (AI), Internet of Things (IoT), and Industrial Internet of Things (IIoT). These integrations enable real-time data analytics, predictive maintenance, and optimized process control, thereby improving operational efficiency and reducing downtime. For instance, AI algorithms can analyze vast amounts of data generated by DCS to predict potential failures and schedule maintenance, while IoT sensors provide real-time feedback on equipment performance. Additionally, advancements in cloud computing allow for remote monitoring and control, facilitating more agile and responsive management of industrial processes. The integration of these technologies also paves the way for Industry 4.0 initiatives, where smart factories leverage interconnected systems to achieve higher levels of automation and productivity. Furthermore, cybersecurity enhancements are crucial in this context to protect sensitive data and ensure the integrity of the control system. Overall, the integration of emerging technologies with DCS not only amplifies its advantages but also sets the stage for future trends that will redefine the landscape of industrial automation. This synergy is expected to drive innovation, improve reliability, and unlock new opportunities for industries relying on DCS, making it an indispensable component of modern industrial infrastructure.