What Is Crank

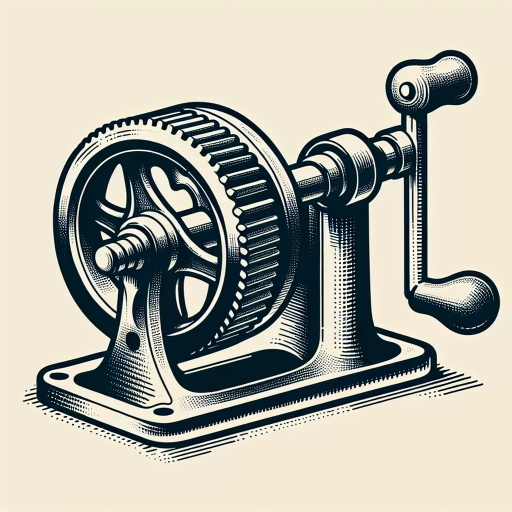
In the realm of mechanical engineering and industrial applications, the term "crank" is synonymous with efficiency and precision. A crank is a fundamental component that converts linear motion into rotational motion, playing a pivotal role in various industries such as automotive, aerospace, and manufacturing. This article delves into the multifaceted world of cranks, starting with an in-depth exploration of **Understanding the Concept of Crank**, where we will dissect the basic principles and mechanisms behind this essential part. We will then examine **The Role of Crank in Various Industries**, highlighting its critical functions and applications across different sectors. Finally, we will discuss **Design, Materials, and Maintenance of Cranks**, providing insights into the engineering aspects and best practices for ensuring optimal performance and longevity. By understanding these facets, readers will gain a comprehensive appreciation for the significance and versatility of cranks in modern technology. Let us begin by **Understanding the Concept of Crank**, the foundation upon which all other aspects are built.
Understanding the Concept of Crank
In the realm of mechanical engineering, few components are as fundamental yet versatile as the crank. This simple yet powerful mechanism has been a cornerstone of machinery for centuries, driving innovation and efficiency across various industries. To fully appreciate the significance of the crank, it is essential to delve into its definition and historical context, understanding how it has evolved over time to become an integral part of modern machinery. Additionally, grasping the mechanical principles and functionality of the crank is crucial for appreciating its role in converting linear motion into rotational motion, a transformation that underpins many mechanical systems. Finally, exploring the common applications of the crank in engineering highlights its widespread utility, from automotive engines to industrial machinery. By examining these facets, we can gain a comprehensive understanding of the concept of the crank and its enduring importance in engineering. This article will guide you through these key aspects, leading to a deeper understanding of the concept of the crank.
Definition and Historical Context
The concept of a crank, often misunderstood or trivialized, has a rich and complex history that underscores its significance in both mechanical engineering and broader cultural contexts. Historically, the term "crank" originated from the Old English word "cranc," meaning "bend" or "crook," which aptly describes the physical shape of this mechanical component. In its most basic form, a crank is a lever with a pivot at one end and a rotating member at the other, converting linear motion into rotational motion or vice versa. This fundamental principle has been crucial in the development of various machines and engines throughout history. The earliest recorded use of cranks dates back to ancient China during the Han Dynasty (206 BCE – 220 CE), where they were employed in grain mills and water pumps. However, it was during the Middle Ages in Europe that cranks became integral to machinery such as windmills and bellows, significantly enhancing productivity in agriculture and industry. The Industrial Revolution further amplified the importance of cranks as they were incorporated into steam engines, textile machinery, and other mechanized systems, driving technological advancements and economic growth. Beyond its mechanical applications, the term "crank" has also evolved to encompass broader cultural connotations. In the late 19th and early 20th centuries, "crank" began to be used colloquially to describe eccentric or unconventional individuals who often championed unorthodox ideas or causes. This usage reflects a societal perception of innovation and progress being driven by those who challenge conventional norms. Understanding the concept of a crank is essential not only for appreciating its role in modern machinery but also for recognizing its historical impact on technological development and societal change. The crank's ability to transform motion has been pivotal in human progress, from ancient agricultural tools to contemporary automotive engines. Moreover, its cultural significance highlights the interplay between technological innovation and societal attitudes towards change and progress. By examining the definition and historical context of the crank, we gain a deeper appreciation for how this seemingly simple mechanism has shaped our world in profound ways.
Mechanical Principles and Functionality
Mechanical principles and functionality are the cornerstone of understanding how a crank operates. At its core, a crank is a simple machine that converts linear motion into rotational motion or vice versa, leveraging the fundamental principles of mechanics such as torque, leverage, and kinematics. The functionality of a crank can be broken down into several key components: the crankshaft, connecting rods, and pistons or other load-bearing elements. The crankshaft, typically a rod with offset crankpins, serves as the central axis around which the entire mechanism revolves. When a force is applied to the crankpin in a linear direction, it translates into rotational motion due to the offset position of the crankpin from the axis of rotation. This conversion is crucial in engines where pistons move up and down in cylinders but need to drive a rotating shaft for power transmission. Connecting rods play a vital role in linking the pistons or other moving parts to the crankshaft. These rods transfer the linear motion of the pistons to the crankpins, ensuring that every up-and-down movement is converted into a smooth rotational motion. The design and material of these rods are critical for durability and efficiency, as they must withstand significant stresses and strains without compromising performance. In addition to these mechanical components, understanding the concept of torque is essential for grasping how a crank functions. Torque, or rotational force, is generated when the linear force applied to the crankpin is multiplied by the radius of the crank. This torque is what ultimately drives the rotational motion, making it possible for engines to produce power or for bicycles to convert pedaling into forward motion. Furthermore, kinematic principles come into play when analyzing the motion of a crank. The path traced by the connecting rod and piston forms an ellipse rather than a perfect circle due to the offset nature of the crankpin. This elliptical path ensures that even though the motion at one end (e.g., piston) is linear, it translates into smooth rotational motion at the other end (e.g., crankshaft). In summary, the functionality of a crank relies heavily on mechanical principles such as torque generation, leverage through offset crankpins, and kinematic analysis of motion paths. By understanding these principles and how they interact within a crank mechanism, one can appreciate the intricate yet efficient design that underpins many modern machines and engines. This foundational knowledge not only enhances comprehension but also fosters innovation in mechanical engineering and design.
Common Applications in Engineering
In the realm of engineering, the crank is a fundamental component that plays a crucial role in converting linear motion into rotational motion, and vice versa. This versatile mechanism is integral to various applications across different fields, showcasing its importance in modern technology. One of the most common and iconic applications of the crank is in internal combustion engines, where it connects the pistons to the camshaft, enabling the transformation of the up-and-down motion of pistons into the rotational energy needed to power vehicles. Similarly, in mechanical engineering, cranks are used in bicycles and motorcycles to convert the linear motion of pedals into rotational energy that propels the vehicle forward. In industrial settings, cranks are essential components of machinery such as pumps, compressors, and generators. For instance, in a reciprocating pump, the crank converts the rotational motion of an electric motor or engine into the linear motion required to move fluids or gases. This application is critical in industries like oil and gas, where precise control over fluid movement is necessary. Additionally, cranks are used in textile machinery to drive looms and spinning machines, ensuring consistent and efficient production processes. The aerospace industry also relies heavily on cranks, particularly in aircraft engines and landing gear systems. Here, the precision and reliability of crank mechanisms are paramount for ensuring safe and efficient operation. Furthermore, in renewable energy systems like wind turbines, cranks can be used to convert the linear motion of blades into rotational energy that drives generators to produce electricity. Beyond these industrial applications, cranks find their way into everyday life through consumer products such as hand-cranked tools and generators. For example, hand-cranked flashlights and radios are invaluable during power outages or in remote areas without access to electricity. These devices leverage the mechanical advantage provided by cranks to generate power through manual effort. The versatility of the crank extends into medical devices as well. In orthopedic rehabilitation equipment, cranks are used to provide controlled resistance for patients undergoing physical therapy, helping them regain strength and mobility. This application highlights the adaptability of crank mechanisms beyond traditional mechanical systems. In summary, the crank is an indispensable element in engineering due to its ability to convert motion types efficiently. Its widespread use across various sectors underscores its significance in modern technology and daily life. Whether in high-performance engines or simple hand tools, the crank remains a cornerstone of mechanical design and innovation. Understanding the concept of the crank is essential for appreciating its multifaceted role in engineering applications and its continued relevance in advancing technological capabilities.
The Role of Crank in Various Industries
In the intricate web of modern industries, the humble crank plays a pivotal role, often unseen but always crucial. From the high-speed engines of automotive and aerospace applications to the robust machinery in industrial manufacturing, and even the complex systems of marine and naval engineering, the crank's versatility and functionality are indispensable. In automotive and aerospace industries, cranks convert linear motion into rotational energy, driving vehicles and aircraft forward with precision and power. In industrial machinery and manufacturing, cranks facilitate the operation of heavy-duty equipment, ensuring smooth and efficient production processes. Meanwhile, in marine and naval engineering, cranks are integral to the propulsion systems of ships and submarines, enabling them to traverse vast distances with reliability. Understanding the multifaceted role of the crank across these diverse sectors is essential for appreciating its significance in modern technology. As we delve into the specifics of each industry, it becomes clear that grasping the concept of the crank is fundamental to comprehending how these industries operate effectively. Therefore, this article aims to explore **Understanding the Concept of Crank** in depth, shedding light on its critical contributions to various industrial domains.
Automotive and Aerospace Applications
In the realms of automotive and aerospace engineering, the crank plays a pivotal role that is both fundamental and multifaceted. In automotive applications, the crankshaft is a critical component of the internal combustion engine, converting the up-and-down motion of pistons into rotational energy that ultimately powers the vehicle. This conversion is essential for transforming the linear motion generated by combustion into the rotational energy needed to drive the wheels. The crankshaft's design, including its offset crankpins and counterweights, ensures smooth operation and minimizes vibrations, contributing to engine efficiency and durability. Additionally, in modern vehicles, advanced materials and manufacturing techniques have allowed for lighter yet stronger crankshafts, enhancing fuel efficiency and performance. In aerospace, the concept of a crank extends beyond traditional mechanical applications. Here, it often manifests in more sophisticated forms such as camshafts and other precision-engineered components within aircraft engines. These components are crucial for controlling valve timing and ensuring optimal engine performance under varying flight conditions. The precision required in aerospace engineering means that these cranks must be crafted with extreme accuracy to withstand high stresses and temperatures while maintaining reliability over thousands of hours of operation. Furthermore, advancements in materials science have led to the development of lightweight yet incredibly strong alloys that are used in these critical components, contributing to improved fuel efficiency and overall aircraft performance. Beyond traditional engine components, the principle of the crank is also applied in other aerospace systems such as landing gear mechanisms and control surfaces. For instance, hydraulic systems that operate landing gear often rely on crank-like mechanisms to convert fluid pressure into mechanical motion, ensuring safe and reliable deployment and retraction of landing gear. Similarly, control surfaces like flaps and ailerons may use crank-based linkages to translate pilot inputs into precise movements that control aircraft attitude and direction. The integration of advanced technologies such as 3D printing and computer-aided design (CAD) has further revolutionized the development of crank-based components in both automotive and aerospace industries. These technologies allow for complex geometries that enhance performance while reducing weight, thereby improving overall efficiency and safety. In summary, the crank's role in automotive and aerospace applications is indispensable, driving innovation and performance in these industries through its versatility, precision engineering, and continuous technological advancements.
Industrial Machinery and Manufacturing
Industrial machinery and manufacturing form the backbone of modern industry, driving innovation and efficiency across various sectors. At the heart of this complex machinery lies the humble yet crucial component known as the crank. The crank, a simple yet ingenious device, converts linear motion into rotational motion or vice versa, making it an indispensable part of many industrial processes. In manufacturing, cranks are integral to engines, pumps, and other machinery that require precise mechanical movements. For instance, in automotive manufacturing, cranks are essential components of internal combustion engines, where they convert the up-and-down motion of pistons into rotational energy that powers vehicles. Similarly, in textile manufacturing, cranks are used in looms and spinning machines to facilitate the intricate movements necessary for weaving and yarn production. The versatility of cranks extends beyond these industries; they are also pivotal in aerospace, where they are used in aircraft engines and other critical systems requiring precise mechanical control. In the oil and gas sector, cranks play a vital role in drilling equipment, enabling the efficient extraction of resources from deep within the earth. Additionally, in food processing and packaging, cranks are used in machinery that requires consistent and reliable motion to handle products with precision. The role of cranks in industrial machinery is not limited to their mechanical function; they also contribute significantly to safety and reliability. By ensuring smooth and predictable motion, cranks help prevent mechanical failures that could lead to downtime or accidents. Furthermore, advancements in materials science have led to the development of more durable and efficient cranks, enhancing overall performance and longevity of industrial equipment. In recent years, the integration of technology such as computer-aided design (CAD) and 3D printing has revolutionized the design and production of cranks. These technologies allow for the creation of complex geometries and customized designs that optimize performance for specific applications. This innovation has enabled industries to achieve higher levels of precision and efficiency, further solidifying the importance of cranks in modern manufacturing. In conclusion, the crank is more than just a simple mechanical component; it is a cornerstone of industrial machinery and manufacturing. Its ability to convert motion types makes it indispensable across a wide range of industries, from automotive and aerospace to textiles and food processing. As technology continues to evolve, the role of cranks will only become more critical, driving innovation and efficiency in the ever-advancing landscape of industrial production.
Marine and Naval Engineering Uses
Marine and naval engineering are critical fields that rely heavily on precise mechanical components to ensure the efficient operation of ships, submarines, and other maritime vessels. Among these components, the crank plays a pivotal role. In marine and naval engineering, cranks are integral to the propulsion systems of ships. They convert the linear motion of pistons in diesel or gasoline engines into rotational motion, which is then transmitted to the propeller shaft. This rotational motion propels the vessel through water, making cranks essential for both speed and maneuverability. The design and material selection of cranks in marine applications are highly specialized due to the harsh marine environment. Cranks must withstand high stresses, corrosive seawater, and extreme temperatures. Engineers often use high-strength alloys and advanced coatings to protect against corrosion and wear. Additionally, the crankshaft's geometry and balance are meticulously optimized to minimize vibrations and ensure smooth engine operation, which is crucial for maintaining stability and reducing noise levels on board. Beyond propulsion, cranks are also used in various auxiliary systems such as generators, pumps, and compressors that support the vessel's operations. For instance, cranks in generator sets provide the necessary power for onboard electrical systems, while those in pumps facilitate the movement of fluids essential for cooling, lubrication, and other critical functions. In submarines, cranks play a dual role; they are part of both the main propulsion system and the auxiliary power units that support life support systems and other vital operations when the submarine is submerged. The role of cranks extends beyond traditional mechanical systems; they are also integral to modern advancements in marine technology. For example, in hybrid propulsion systems that combine traditional fossil fuels with electric motors or diesel-electric configurations, cranks continue to play a central role in converting energy efficiently. Moreover, as the industry moves towards more sustainable solutions like wind-assisted propulsion or hydrogen fuel cells, the adaptability and reliability of crank mechanisms remain indispensable. In summary, the crank is a fundamental component in marine and naval engineering, driving the heart of propulsion systems and supporting various auxiliary functions. Its robust design and precise engineering ensure the reliability and efficiency of maritime operations, making it an indispensable element in the complex machinery that keeps ships and submarines operational. As technology evolves, the versatility and importance of the crank will continue to be a cornerstone of marine engineering innovation.
Design, Materials, and Maintenance of Cranks
In the realm of mechanical engineering and industrial design, cranks play a pivotal role in converting linear motion into rotational motion, a fundamental principle in various machinery and vehicles. The efficiency, durability, and performance of a crank are heavily influenced by three critical aspects: design considerations and optimization, materials used for construction, and maintenance and troubleshooting techniques. Effective design involves careful optimization to ensure smooth operation, minimal wear, and maximum efficiency. The choice of materials is equally crucial, as it directly impacts the crank's strength, durability, and resistance to wear and tear. Additionally, regular maintenance and troubleshooting are essential to prevent failures and extend the lifespan of the crank. Understanding these elements is vital for engineers, technicians, and anyone involved in the development or operation of machinery that relies on cranks. By delving into these key areas, we can gain a comprehensive understanding of the concept of cranks and their integral role in modern machinery. This article will explore these critical facets in detail, providing a thorough insight into the design, materials, and maintenance of cranks, ultimately leading to a deeper understanding of the concept of cranks.
Design Considerations and Optimization
When designing cranks, several critical considerations must be taken into account to ensure optimal performance, durability, and safety. **Design Considerations** play a pivotal role in this process. Firstly, the geometry of the crank must be carefully planned to align with the intended application. For instance, in bicycle cranks, the length and offset of the crank arms significantly affect pedaling efficiency and comfort. In industrial settings, such as in engines or machinery, the crank's design must accommodate the specific load and stress requirements to prevent premature wear or failure. **Materials Selection** is another crucial aspect. The choice of material can significantly impact the crank's strength, weight, and resistance to corrosion. High-strength alloys like steel or titanium are often preferred for their durability and ability to withstand high stresses. However, considerations such as cost, manufacturing complexity, and environmental impact also need to be balanced. For example, aluminum cranks are lighter and more cost-effective but may not offer the same level of strength as steel. **Optimization** involves refining the design to achieve maximum efficiency while minimizing potential drawbacks. This can include optimizing the crank's shape for better stress distribution, using advanced manufacturing techniques like 3D printing to create complex geometries that reduce weight without compromising strength, or incorporating surface treatments to enhance wear resistance. Additionally, dynamic balancing is essential to ensure smooth operation and reduce vibration, which can lead to fatigue and failure over time. **Maintenance** is also a key consideration in the design phase. Easy maintenance can extend the lifespan of the crank and reduce downtime. Design features such as easy access points for lubrication or inspection can make routine maintenance more efficient. Furthermore, designing components with interchangeability in mind allows for quicker replacement of worn parts, reducing overall maintenance costs. Incorporating these design considerations, material selections, optimization strategies, and maintenance-friendly features into the development process ensures that cranks perform optimally under various conditions. By balancing these factors effectively, engineers can create cranks that are not only functional but also reliable and cost-effective, whether they are used in high-performance sports equipment or heavy-duty industrial machinery. This holistic approach to design underscores the importance of meticulous planning and execution in producing high-quality cranks that meet or exceed performance expectations.
Materials Used for Crank Construction
When it comes to the construction of cranks, the choice of materials is crucial for ensuring durability, performance, and longevity. Cranks are a critical component in various mechanical systems, including engines, bicycles, and machinery, where they convert linear motion into rotational motion or vice versa. The materials used for crank construction must withstand high stresses, fatigue, and wear while maintaining precision and reliability. **Steel** is one of the most common materials used for crankshafts due to its high strength-to-weight ratio, toughness, and affordability. Specifically, alloy steels such as 4130 and 4140 are popular choices because they offer excellent mechanical properties that can be further enhanced through heat treatment processes like quenching and tempering. These treatments improve the hardness and yield strength of the steel, making it more resistant to wear and fatigue. **Aluminum** alloys are another option for crank construction, particularly in applications where weight reduction is a priority, such as in high-performance engines or lightweight bicycles. Aluminum alloys like 7075-T6 offer a good balance of strength, corrosion resistance, and light weight. However, they generally have lower fatigue strength compared to steel and may require additional surface treatments to enhance durability. **Titanium** alloys are used in specialized applications where both high strength and low weight are essential. Titanium's unique combination of properties makes it ideal for aerospace and high-performance automotive cranks. It has a higher strength-to-weight ratio than many steel alloys and excellent corrosion resistance. However, titanium is more expensive than steel or aluminum, limiting its widespread use. **Cast Iron** is sometimes used for crankshafts in heavy-duty applications such as diesel engines due to its high compressive strength, good vibration damping properties, and cost-effectiveness. However, cast iron has lower tensile strength compared to steel and may not be suitable for high-speed or high-stress environments. In addition to these primary materials, surface treatments play a significant role in enhancing the performance of cranks. Techniques such as nitriding, chrome plating, or applying ceramic coatings can improve wear resistance and reduce friction. These treatments help extend the lifespan of the crank by protecting it from corrosion and mechanical wear. In summary, the selection of materials for crank construction depends on the specific requirements of the application, including factors such as weight, strength, durability, and cost. By choosing the right material and applying appropriate surface treatments, engineers can design cranks that meet stringent performance criteria while ensuring reliability and longevity. This careful consideration of materials is a cornerstone in the design, materials selection, and maintenance of cranks across various industries.
Maintenance and Troubleshooting Techniques
**Maintenance and Troubleshooting Techniques** Effective maintenance and troubleshooting are crucial for the longevity and performance of cranks, whether they are part of a bicycle, engine, or any other mechanical system. Regular maintenance involves several key steps. First, inspect the crank for any signs of wear or damage, such as cracks, rust, or excessive play in the bearings. Lubrication is also essential; applying the appropriate lubricant to moving parts can significantly reduce friction and prevent wear. For bicycle cranks, this often involves greasing the pedal threads and ensuring that the bottom bracket bearings are well-lubricated. In engines, oil changes and filter replacements are critical to keep the crankshaft and its bearings in good condition. Troubleshooting begins with identifying symptoms. Common issues include unusual noises, vibrations, or a decrease in performance. For instance, a clicking sound from a bicycle crank might indicate loose bolts or worn-out bearings, while a grinding noise from an engine crankshaft could signal worn-out bearings or misaligned components. Visual inspections and diagnostic tests can help pinpoint the problem. In some cases, specialized tools may be necessary to measure tolerances and clearances accurately. When repairing or replacing cranks, it's important to follow precise procedures to avoid further damage. For example, when replacing a bicycle crankset, ensure that the new cranks are compatible with the existing bottom bracket and that all bolts are tightened according to the manufacturer's specifications. In engines, replacing a crankshaft requires careful alignment and torque specifications to prevent damage to other components. Preventive maintenance can also include periodic cleaning and degreasing to remove dirt and grime that can accumulate over time. Additionally, keeping records of maintenance activities helps in tracking the history of the crank and identifying potential issues before they become major problems. In summary, maintaining and troubleshooting cranks involves regular inspections, proper lubrication, timely repairs, and adherence to manufacturer guidelines. By adopting these practices, users can extend the lifespan of their cranks, ensure optimal performance, and prevent costly repairs down the line. Whether in high-performance applications like racing bicycles or in heavy-duty machinery like industrial engines, meticulous maintenance is key to reliability and efficiency.