What Is Rope Made Of

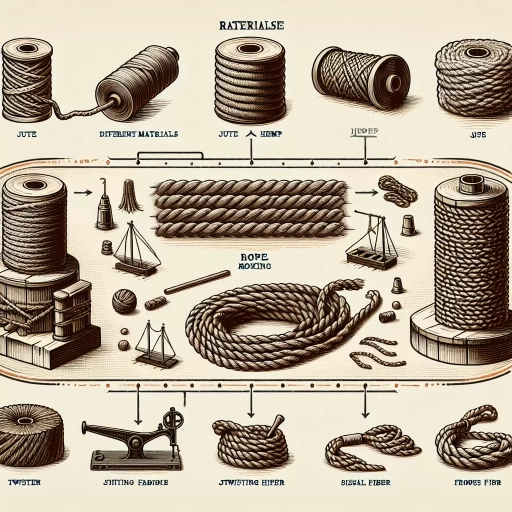
Historical Development of Rope Materials
The historical development of rope materials is a rich and multifaceted narrative that spans thousands of years, reflecting human ingenuity and the quest for durability and efficiency. From the earliest natural fibers to the introduction of synthetic materials, and through significant advancements in manufacturing techniques, the evolution of rope has been pivotal in various aspects of human civilization. This journey begins with **Early Natural Fibers**, where ancient societies harnessed plant and animal resources to create robust and versatile ropes. The transition from these natural materials to **Introduction of Synthetic Materials** marked a significant turning point, offering enhanced strength, durability, and resistance to environmental factors. Furthermore, **Evolution in Manufacturing Techniques** has continuously refined the production process, enabling mass production and customization of ropes for diverse applications. Understanding these developments provides a comprehensive insight into how rope materials have adapted to meet the changing needs of humanity over time. Let us delve into the origins of this story, starting with the use of **Early Natural Fibers**.
Early Natural Fibers
Early natural fibers played a pivotal role in the historical development of rope materials, laying the foundation for modern rope manufacturing. These fibers, derived from plants and animals, were the primary resources for creating durable and versatile ropes that served various purposes across ancient civilizations. One of the earliest and most widely used natural fibers was flax, from which linen was produced. Flax fibers were valued for their strength, durability, and resistance to decay, making them ideal for maritime applications such as ship rigging and sails. Another significant fiber was hemp, known for its exceptional tensile strength and resistance to water. Hemp ropes were commonly used in agriculture, construction, and even as a material for early textiles. Cotton, though softer than flax or hemp, was also utilized in rope production, particularly in regions where it was abundantly available. Cotton ropes were lighter and easier to handle but lacked the strength of other natural fibers. In addition to plant-based fibers, animal-derived materials like wool and silk were occasionally used for rope-making, especially for specialized applications requiring flexibility and elasticity. Wool ropes, for instance, were used in ancient Greece and Rome for tasks that required a degree of give, such as securing loads on carts. The use of these early natural fibers was not limited to Western civilizations; in Asia, fibers like jute and sisal were integral to local economies. Jute, native to India and Bangladesh, was highly valued for its affordability and versatility. Sisal, derived from the agave plant, was another tropical fiber that found widespread use in Africa and South America. These fibers were often combined with other materials to enhance their properties; for example, blending hemp with flax could create a rope that balanced strength with durability. The processing of these natural fibers involved labor-intensive techniques such as retting (soaking in water to break down pectins), breaking (separating the fibers), and spinning (twisting the fibers into yarn). The yarns were then twisted together to form strands, which were finally braided or laid to create the rope. This meticulous process ensured that the ropes were robust enough to withstand various environmental conditions and heavy use. The historical significance of early natural fibers extends beyond their practical applications; they also influenced trade routes and cultural exchanges. The demand for high-quality fibers drove commerce between regions, fostering economic growth and technological advancements. For instance, the Silk Road facilitated the exchange of silk between China and Europe, while the maritime trade routes connected Europe with Africa and Asia through the exchange of flax and hemp. In conclusion, early natural fibers were the cornerstone of rope-making throughout history. Their unique properties and widespread availability made them indispensable for various tasks across different cultures. As technology evolved and new materials were discovered, these natural fibers continued to play a significant role in the development of rope materials, setting the stage for modern synthetic fibers that would eventually complement and sometimes replace them. Understanding the history of these early natural fibers provides valuable insights into the evolution of rope-making techniques and their enduring impact on human civilization.
Introduction of Synthetic Materials
The introduction of synthetic materials marked a significant turning point in the historical development of rope materials, revolutionizing the industry with unparalleled durability, versatility, and performance. Prior to the mid-20th century, ropes were primarily made from natural fibers such as cotton, hemp, and sisal, which, although robust, had inherent limitations including susceptibility to moisture, UV degradation, and lower tensile strength. The advent of synthetic materials like nylon, polyester, and polypropylene transformed this landscape. Nylon, first synthesized in 1935 by Wallace Carothers at DuPont, was the first commercially viable synthetic fiber. Its introduction in the 1940s brought about ropes that were stronger, lighter, and more resistant to abrasion and chemicals compared to their natural counterparts. Polyester followed suit in the 1950s, offering even greater resistance to UV light and improved dimensional stability. Polypropylene, introduced in the 1960s, added another dimension with its buoyancy and resistance to marine environments, making it ideal for maritime applications. These synthetic fibers not only enhanced the physical properties of ropes but also expanded their range of applications. For instance, nylon ropes became indispensable in mountaineering and rescue operations due to their high strength-to-weight ratio and elasticity. Polyester ropes found widespread use in industrial settings where high durability and resistance to wear were critical. Polypropylene ropes, with their unique buoyancy, became essential for fishing nets and other aquatic uses. The versatility of these materials allowed for the development of specialized rope types tailored to specific needs—such as arborist ropes for tree climbing, climbing ropes for rock climbing, and tow lines for heavy-duty hauling. The manufacturing process of synthetic ropes also underwent significant advancements. Modern extrusion techniques allow for precise control over fiber diameter and texture, enabling the production of ropes with consistent quality and performance. Additionally, advancements in braiding and twisting technologies have enabled the creation of complex rope constructions that combine different fibers to achieve optimal performance characteristics. This has led to the development of hybrid ropes that leverage the strengths of multiple materials—such as combining nylon's elasticity with polyester's UV resistance. Moreover, synthetic materials have driven innovation in rope design and functionality. For example, the introduction of Dyneema—a high-modulus polyethylene fiber—has led to the creation of ultra-high molecular weight polyethylene (UHMWPE) ropes that are significantly stronger than steel on a weight-for-weight basis. These advanced ropes are now used in critical applications such as offshore mooring lines and search and rescue operations. In conclusion, the introduction of synthetic materials has been a game-changer in the evolution of rope technology. By offering superior strength, durability, and versatility compared to natural fibers, synthetic ropes have expanded the scope of applications across various industries. As technology continues to advance, it is likely that synthetic materials will remain at the forefront of rope innovation, driving further improvements in performance and functionality. This shift underscores the dynamic nature of rope development and highlights how historical advancements have paved the way for modern-day innovations in this field.
Evolution in Manufacturing Techniques
The evolution in manufacturing techniques has significantly impacted the historical development of rope materials, transforming the industry from traditional, labor-intensive methods to modern, high-efficiency processes. Historically, rope production involved manual twisting and braiding of natural fibers such as hemp, cotton, and flax. This laborious process limited production capacity and quality consistency. The Industrial Revolution marked a pivotal shift with the introduction of mechanized spinning and weaving machinery, enabling mass production and standardization of rope materials. The invention of the power loom and spinning jenny in the 18th century allowed for faster and more uniform production, making ropes more accessible and affordable. The 20th century saw further advancements with the advent of synthetic materials like nylon, polyester, and polypropylene. These materials offered superior strength, durability, and resistance to environmental factors compared to their natural counterparts. Modern manufacturing techniques such as extrusion, where molten plastic is forced through a die to create fibers, have streamlined the production process. Additionally, advancements in textile technology have introduced new methods like braiding and twisting machines that can handle both natural and synthetic fibers with precision. Today, advanced manufacturing techniques include computer-aided design (CAD) and computer-aided manufacturing (CAM), which allow for precise engineering and customization of rope structures. These technologies enable the creation of specialized ropes tailored for specific applications, such as climbing ropes with built-in safety features or marine ropes designed to withstand harsh marine environments. Furthermore, the integration of automation and robotics in manufacturing has increased efficiency and reduced human error, ensuring consistent quality across large production runs. Sustainability has also become a key driver in the evolution of manufacturing techniques for rope materials. Eco-friendly production methods and the use of recycled materials are gaining traction. For instance, some manufacturers are now producing ropes from recycled plastics, reducing waste and promoting environmental stewardship. This shift towards sustainable practices not only aligns with global environmental goals but also appeals to consumers increasingly conscious of the ecological impact of their purchases. In conclusion, the evolution in manufacturing techniques has revolutionized the production of rope materials from traditional manual processes to sophisticated, high-tech methods. This transformation has enhanced product quality, increased efficiency, and expanded the range of available materials and applications. As technology continues to advance, it is likely that future innovations will further refine and diversify the manufacturing landscape for rope materials, ensuring they remain a vital component in various industries ranging from construction to recreation.
Types of Natural Fibers Used in Rope Making
Natural fibers have been the cornerstone of rope making for centuries, offering a blend of strength, durability, and sustainability. The diversity in natural fibers allows for a wide range of applications, each with its unique characteristics and advantages. This article delves into three primary categories of natural fibers used in rope making: Cotton and Hemp, Jute and Sisal, and Coconut and Manila. Cotton and Hemp are renowned for their versatility and robustness. Cotton ropes are often preferred for their softness and resistance to abrasion, making them ideal for applications where a high degree of flexibility is required. Hemp, on the other hand, stands out for its exceptional tensile strength and resistance to rot, making it a popular choice for marine and industrial uses. Jute and Sisal fibers are celebrated for their eco-friendly nature and cost-effectiveness. Jute ropes are known for their biodegradability and are commonly used in agricultural settings due to their affordability and ease of production. Sisal fibers, derived from the agave plant, offer a high level of durability and are frequently used in landscaping and gardening. Coconut and Manila fibers round out the spectrum with their unique properties. Coconut coir ropes are highly resistant to saltwater and are often used in coastal environments, while Manila ropes, made from abaca fibers, are prized for their strength and resistance to decay. Transitioning to the first category, Cotton and Hemp fibers have been staples in rope making due to their balanced blend of strength, durability, and versatility. These fibers have been used across various industries, from maritime to agricultural, and their popularity endures due to their proven performance and adaptability. In the following section, we will explore the specific attributes and applications of Cotton and Hemp in greater detail.
Cotton and Hemp
When it comes to natural fibers used in rope making, two of the most versatile and widely utilized materials are cotton and hemp. These fibers have been integral to various industries for centuries, offering unique properties that make them ideal for different applications. **Cotton** is one of the most common natural fibers used globally. Known for its softness, breathability, and durability, cotton is a staple in textile production. In rope making, cotton ropes are often preferred for their flexibility and resistance to abrasion. Cotton ropes are typically used in applications where a softer, more pliable rope is required, such as in sailing, camping, and general-purpose utility ropes. However, cotton has some limitations; it absorbs water, which can lead to swelling and reduced strength when wet. This makes it less suitable for marine or heavy-duty industrial use. **Hemp**, on the other hand, is renowned for its exceptional strength and durability. Hemp fibers are significantly stronger than cotton and have a higher tensile strength, making them ideal for heavy-duty applications. Hemp ropes are resistant to UV light, moisture, and abrasion, which makes them a preferred choice for marine and industrial uses. Unlike cotton, hemp does not swell when exposed to water; instead, it becomes even stronger when wet. This property, combined with its resistance to rot and mildew, makes hemp an excellent material for ropes used in harsh environments. Additionally, hemp is more sustainable than many other natural fibers due to its fast growth rate and low water requirements. The choice between cotton and hemp often depends on the specific needs of the application. For instance, if a rope needs to be soft and flexible but does not require extreme strength or resistance to water, cotton might be the better option. However, if a rope needs to withstand heavy loads, harsh weather conditions, or prolonged exposure to water, hemp is generally the superior choice. In summary, both cotton and hemp offer distinct advantages that make them valuable in rope making. While cotton provides flexibility and softness suitable for lighter applications, hemp's unparalleled strength and durability make it a go-to material for more demanding uses. Understanding these differences allows manufacturers and users to select the most appropriate natural fiber for their specific needs, ensuring the creation of high-quality ropes that meet various performance standards.
Jute and Sisal
Jute and sisal are two of the most significant natural fibers used in rope making, each offering unique properties that make them invaluable in various applications. **Jute**, derived from the Corchorus capsularis and Corchorus olitorius plants, is one of the most widely cultivated natural fibers globally. Known for its strength, durability, and affordability, jute is a popular choice for rope production. The fiber has a high tensile strength and is resistant to abrasion, making it suitable for heavy-duty ropes used in construction, agriculture, and marine industries. Additionally, jute ropes are biodegradable and compostable, aligning with sustainable practices. However, jute's moisture absorption can lead to swelling and reduced strength when exposed to water, limiting its use in wet environments. **Sisal**, on the other hand, is extracted from the leaves of the Agave sisalana plant, primarily grown in tropical regions. Sisal fibers are known for their exceptional tensile strength and resistance to saltwater corrosion, making them ideal for marine applications such as mooring lines and fishing nets. Unlike jute, sisal has better resistance to moisture and UV light, enhancing its durability in harsh conditions. Sisal ropes also exhibit good elasticity, allowing them to absorb shocks without breaking. While sisal is more expensive than jute due to the labor-intensive harvesting process, its superior performance in demanding environments justifies the cost. Furthermore, sisal's natural resistance to pests and fungi reduces the need for chemical treatments, contributing to its eco-friendly profile. Both jute and sisal fibers can be blended with other materials to enhance their performance. For instance, combining jute with synthetic fibers can improve its water resistance, while blending sisal with other natural fibers can optimize its cost-effectiveness without compromising on quality. The versatility of these fibers allows rope manufacturers to tailor their products to meet specific industry requirements, from the rugged demands of maritime use to the sustainability needs of modern consumers. In summary, jute and sisal are cornerstone natural fibers in rope making due to their robust mechanical properties and environmental benefits. While jute excels in terms of cost and general-purpose applications, sisal stands out for its superior performance in harsh environments. Together, these fibers provide a range of options for industries seeking reliable, sustainable, and high-quality ropes tailored to their unique needs.
Coconut and Manila
Coconut and Manila fibers are two of the most significant natural materials used in rope making, each offering unique properties that make them ideal for various applications. **Coconut fibers**, derived from the husks of coconuts, are known for their durability and resistance to saltwater and UV light. These fibers are extracted through a process that involves soaking the husks in water, followed by retting and decortication. The resulting fibers are coarse yet flexible, making them perfect for ropes intended for marine use or outdoor applications where exposure to harsh conditions is inevitable. Coconut fiber ropes are also biodegradable and non-toxic, adding an environmental benefit to their practical advantages. **Manila fibers**, on the other hand, come from the abacá plant (Musa textilis), native to the Philippines. These fibers are renowned for their exceptional strength, elasticity, and resistance to decay. The extraction process involves stripping the plant's leaf sheaths and then separating the fibers through a combination of mechanical and manual techniques. Manila fiber ropes are highly valued for their tensile strength and are often used in heavy-duty applications such as shipping, construction, and even in the manufacture of high-quality paper products. Unlike coconut fibers, Manila fibers have a smoother texture and can be dyed easily, making them versatile for both functional and aesthetic purposes. Both coconut and Manila fibers have been integral to rope making for centuries due to their natural resilience and adaptability. While coconut fibers excel in marine environments and offer eco-friendly benefits, Manila fibers stand out for their superior strength and versatility. Together, these natural fibers provide a robust and sustainable alternative to synthetic materials, ensuring that ropes made from them can withstand rigorous use while maintaining environmental integrity. This dual capability underscores the importance of these natural resources in modern rope manufacturing, highlighting their enduring relevance in a world increasingly conscious of sustainability and performance.
Modern Synthetic Materials in Rope Production
The evolution of rope production has been significantly influenced by the advent of modern synthetic materials, which offer superior strength, durability, and versatility compared to traditional natural fibers. This transformation is evident in three key areas: the widespread use of polypropylene and polyethylene, the integration of nylon and polyester, and the development of advanced composites and blends. Polypropylene and polyethylene ropes are renowned for their resistance to abrasion, UV degradation, and chemical corrosion, making them ideal for marine and industrial applications. Nylon and polyester ropes, on the other hand, are celebrated for their high tensile strength and elasticity, often used in climbing, rescue operations, and heavy-duty lifting. Meanwhile, advanced composites and blends push the boundaries further by combining different materials to achieve unique properties tailored to specific needs. As we delve into these advancements, it becomes clear that the foundation of modern rope production lies in the robust characteristics of polypropylene and polyethylene, which set the stage for the broader spectrum of synthetic materials in use today. Therefore, our exploration begins with a detailed look at polypropylene and polyethylene.
Polypropylene and Polyethylene
Polypropylene and polyethylene are two of the most widely used synthetic materials in modern rope production, offering a blend of durability, versatility, and cost-effectiveness that has revolutionized the industry. **Polypropylene**, often abbreviated as PP, is a thermoplastic polymer known for its high tensile strength, resistance to abrasion, and excellent resistance to chemicals and UV light. This makes it an ideal choice for ropes that need to withstand harsh environmental conditions such as marine ropes, mooring lines, and industrial lifting equipment. Polypropylene ropes are also lightweight and buoyant, which is particularly advantageous in aquatic applications where weight and floatation are critical factors. Additionally, polypropylene can be easily colored and textured to meet specific requirements, enhancing its aesthetic appeal and functionality. **Polyethylene**, on the other hand, is another versatile thermoplastic polymer that comes in various forms including low-density polyethylene (LDPE) and high-density polyethylene (HDPE). HDPE is particularly popular in rope production due to its exceptional strength-to-weight ratio, making it suitable for heavy-duty applications such as climbing ropes, tow lines, and cargo nets. Polyethylene ropes exhibit superior resistance to abrasion and chemicals, similar to polypropylene but with added benefits like higher impact resistance and flexibility. This makes them highly adaptable for use in diverse environments ranging from construction sites to recreational activities. Furthermore, polyethylene can be formulated to have different levels of stiffness or flexibility depending on the specific needs of the application. Both polypropylene and polyethylene offer significant advantages over traditional natural fibers like cotton or hemp. They are more resistant to rot, mildew, and insect damage, ensuring a longer lifespan for the rope. These synthetic materials also exhibit consistent performance across various temperatures and humidity levels, reducing the risk of sudden failures. The manufacturing process for these polymers allows for precise control over their properties, enabling the production of ropes with tailored characteristics such as elasticity, tensile strength, and color. In modern rope production, the combination of polypropylene and polyethylene has opened up new possibilities for innovation. For instance, hybrid ropes that blend these materials can leverage the strengths of each to create products with enhanced performance profiles. This synergy allows manufacturers to design ropes that are not only stronger but also more durable and resistant to environmental degradation. Additionally, advancements in extrusion technology have made it possible to produce these synthetic fibers with intricate textures and patterns that improve grip and reduce slippage. In conclusion, polypropylene and polyethylene are cornerstone materials in contemporary rope manufacturing due to their robust mechanical properties, chemical resistance, and adaptability. These synthetic polymers have transformed the rope industry by offering reliable solutions for a wide range of applications from industrial to recreational use. As technology continues to evolve, it is likely that these materials will remain at the forefront of rope production innovation, driving further improvements in performance and functionality.
Nylon and Polyester
In the realm of modern synthetic materials, Nylon and Polyester stand out as pivotal components in rope production, offering a blend of durability, versatility, and performance that has revolutionized various industries. **Nylon**, first introduced in the 1930s, is renowned for its exceptional strength, elasticity, and resistance to abrasion. This polyamide polymer is often used in applications where high tensile strength and flexibility are crucial, such as in climbing ropes, marine ropes, and industrial lifting equipment. One of the key advantages of Nylon is its ability to absorb shock loads without breaking, making it an ideal choice for dynamic applications. However, it does have a tendency to stretch under load and can be affected by UV light and chemicals, which necessitates careful selection and treatment. **Polyester**, on the other hand, offers a different set of benefits that complement those of Nylon. Known for its high resistance to UV degradation, chemicals, and abrasion, Polyester is frequently used in outdoor and marine environments where exposure to harsh conditions is common. Polyester ropes exhibit minimal stretch compared to Nylon, providing a more stable and predictable performance under load. This characteristic makes Polyester particularly suitable for static applications such as mooring lines, tow lines, and safety nets. Additionally, Polyester's resistance to water absorption reduces its weight gain when wet, enhancing its overall efficiency in aquatic settings. The combination of these synthetic materials allows manufacturers to tailor rope specifications to meet specific needs. For instance, ropes made from a blend of Nylon and Polyester can leverage the strengths of both materials—Nylon's elasticity and Polyester's stability—to create a product that is both durable and reliable. This synergy is particularly evident in the production of composite ropes where different fibers are combined to achieve optimal performance characteristics. In modern rope production, advancements in manufacturing techniques have further enhanced the properties of Nylon and Polyester. Techniques such as braiding and twisting allow for the creation of complex rope structures that maximize strength while minimizing weight. Moreover, surface treatments and coatings can be applied to improve resistance against abrasion and environmental degradation. The widespread adoption of Nylon and Polyester in rope production is also driven by their cost-effectiveness compared to natural fibers like cotton or hemp. Synthetic fibers offer consistent quality, longer lifespan, and easier maintenance, making them a preferred choice across various sectors including construction, maritime, and recreational activities. In conclusion, the integration of Nylon and Polyester into modern synthetic materials has significantly elevated the standards of rope production. These polymers not only provide superior mechanical properties but also offer the flexibility to be engineered for specific applications. As technology continues to evolve, it is likely that these materials will remain at the forefront of innovation in the field of rope manufacturing, ensuring that ropes continue to meet and exceed the demands of an increasingly complex world.
Advanced Composites and Blends
Advanced composites and blends have revolutionized the field of rope production, offering unparalleled strength, durability, and versatility. These modern synthetic materials are engineered to combine the best properties of different components, resulting in ropes that outperform traditional natural fibers and single-component synthetics. At the heart of these advancements are high-performance polymers such as ultra-high molecular weight polyethylene (UHMWPE), polyaramid (e.g., Kevlar), and polypropylene, which are often blended with other materials to enhance specific attributes. For instance, UHMWPE fibers, known for their exceptional tensile strength and resistance to abrasion, are frequently combined with polypropylene or polyester to improve UV resistance and reduce costs. This blend not only maintains the superior mechanical properties of UHMWPE but also adds the benefits of increased chemical stability and easier handling. Similarly, polyaramid fibers, renowned for their high strength-to-weight ratio and thermal stability, are often integrated into composite ropes to provide enhanced resistance to heat and chemicals. The manufacturing process for these advanced composites involves sophisticated techniques such as extrusion, spinning, and braiding. Extrusion allows for the precise control of fiber dimensions and molecular alignment, while spinning ensures uniformity in fiber thickness and texture. Braiding or twisting these fibers into rope configurations further enhances their mechanical properties by distributing loads more evenly across the structure. One of the key advantages of advanced composites in rope production is their ability to be tailored for specific applications. For example, ropes designed for offshore oil rigs or marine environments can be formulated with additives that resist seawater corrosion and biological degradation. Similarly, ropes intended for rescue operations or climbing can be engineered with enhanced elasticity and shock absorption to ensure safety and reliability. Moreover, these modern synthetic ropes exhibit superior resistance to environmental factors such as UV radiation, moisture, and extreme temperatures compared to natural fibers like cotton or hemp. This makes them ideal for use in harsh conditions where traditional materials would degrade quickly. Additionally, their lightweight nature reduces fatigue during handling while maintaining or even exceeding the strength of heavier counterparts. In conclusion, advanced composites and blends represent a significant leap forward in rope production technology. By leveraging the strengths of various synthetic materials through innovative blending and manufacturing techniques, these ropes offer unprecedented performance characteristics that cater to a wide range of industrial and recreational applications. As research continues to push the boundaries of material science, it is clear that these advanced composites will remain at the forefront of modern synthetic materials in rope production for years to come.