What Is A Stator

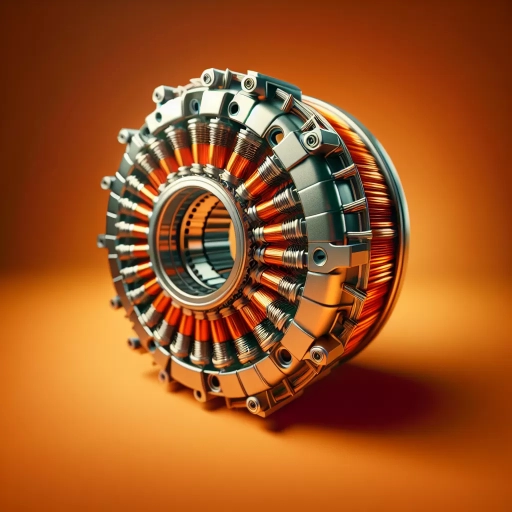
Understanding the Basics of a Stator
Understanding the basics of a stator is crucial for anyone interested in electrical engineering, particularly in the context of motors and generators. At its core, a stator is a fundamental component that plays a pivotal role in the operation of these devices. To grasp the intricacies of a stator, it is essential to delve into three key aspects: its definition and function, its components and structure, and the various types that exist. Firstly, understanding the definition and function of a stator sets the foundation for further exploration. This involves recognizing how the stator interacts with other parts of the motor or generator to produce or utilize electrical energy. Secondly, examining the components and structure of a stator reveals the intricate design elements that contribute to its functionality. This includes the materials used, the arrangement of windings, and other critical features. Lastly, familiarizing oneself with the different types of stators highlights their versatility and adaptability across various applications. From simple AC motors to complex industrial generators, each type of stator has unique characteristics that make it suitable for specific uses. By exploring these three dimensions—definition and function, components and structure, and types of stators—we can gain a comprehensive understanding of this vital component. Let's begin by defining what a stator is and how it functions within electrical systems.
Definition and Function
A stator, a fundamental component in electrical machinery, is defined as the stationary part of an electric motor or generator that surrounds the rotor. Its primary function is to provide a magnetic field necessary for the operation of the machine. The stator consists of a cylindrical frame with slots where windings are placed, which carry alternating current (AC) or direct current (DC) depending on the type of machine. When an electric current flows through these windings, it generates a magnetic field that interacts with the magnetic field produced by the rotor, enabling the conversion of electrical energy into mechanical energy in motors or vice versa in generators. The design and construction of the stator are crucial for efficient operation. It typically includes laminated steel sheets to reduce eddy current losses and improve magnetic permeability. The windings are carefully arranged to ensure uniform distribution of the magnetic field, which enhances the overall performance and efficiency of the machine. In motors, the stator's magnetic field induces rotation in the rotor, while in generators, it helps in converting mechanical energy from the rotor into electrical energy. Understanding the basics of a stator is essential for appreciating how electric motors and generators work. For instance, in an induction motor, the stator's AC current creates a rotating magnetic field that induces an electromotive force (EMF) in the rotor, causing it to rotate. In synchronous motors and generators, the stator's magnetic field synchronizes with the rotor's magnetic field to maintain a constant speed. This synchronization is critical for maintaining grid stability in power generation systems. Moreover, advancements in stator design have led to improvements in machine efficiency and reliability. Modern stators often incorporate advanced materials and technologies such as high-temperature superconductors and optimized winding configurations to minimize energy losses and maximize output. These innovations are particularly significant in applications requiring high power density and efficiency, such as in electric vehicles and renewable energy systems. In summary, the stator plays a pivotal role in the functioning of electric motors and generators by providing the necessary magnetic field for energy conversion. Its design and construction are tailored to optimize performance, efficiency, and reliability. As technology continues to evolve, understanding the basics of a stator remains fundamental for developing more efficient and sustainable electrical machinery. This foundational knowledge not only aids in the maintenance and troubleshooting of existing machines but also drives innovation in new applications across various industries.
Components and Structure
When delving into the intricacies of a stator, it is crucial to understand its components and structure, as these elements are fundamental to its operation and efficiency. A stator, the stationary part of an electric motor or generator, consists of several key components that work in harmony to facilitate the conversion of electrical energy into mechanical energy or vice versa. At its core, the stator includes a **stator core**, typically made from laminated steel sheets to minimize eddy current losses. This core is designed to provide a magnetic path for the flux generated by the stator windings. The **stator windings** are another critical component, comprising insulated copper wires wound around the stator core in a specific pattern. These windings are arranged in slots within the stator core and are connected in a way that creates a magnetic field when an alternating current (AC) flows through them. The configuration of these windings can vary depending on the type of motor or generator, with common arrangements including star (Y) and delta (∆) connections. In addition to the core and windings, the stator often includes **end rings** or **end caps** which serve to secure the windings in place and protect them from mechanical stress. These components ensure that the windings remain tightly packed and aligned, maintaining the integrity of the magnetic field. The **housing** or **frame** of the stator provides structural support and protection from environmental factors. It is typically made from durable materials such as cast iron or steel and is designed to house the stator core and windings securely. Understanding the interplay between these components is essential for optimizing stator performance. For instance, the design of the stator core and windings must be carefully balanced to achieve efficient energy transfer while minimizing losses due to heat and friction. Moreover, advancements in materials science have led to the development of more efficient stator designs, such as those using rare-earth magnets or advanced insulation materials. In summary, the components and structure of a stator are meticulously engineered to ensure reliable and efficient operation. By grasping the roles of each component—from the stator core and windings to the end rings and housing—one can better appreciate the complex dynamics at play within these critical electrical machines. This foundational knowledge is vital for anyone seeking to understand the basics of a stator and its integral role in modern electrical systems.
Types of Stators
### Types of Stators Understanding the various types of stators is crucial for appreciating their diverse applications and functionalities. A stator, the stationary part of an electric motor or generator, plays a pivotal role in converting electrical energy into mechanical energy or vice versa. There are several key types of stators, each designed to meet specific requirements and performance criteria. **1. Squirrel Cage Stator:** The most common type, the squirrel cage stator, is characterized by its simplicity and robustness. It consists of a cylindrical core with slots that house conductive bars connected at both ends by short-circuiting rings. This design allows for high starting torque and reliability, making it ideal for industrial applications such as pumps, fans, and conveyor belts. **2. Wound Rotor Stator:** In contrast to the squirrel cage stator, the wound rotor stator features a rotor with windings that can be connected to an external circuit. This allows for greater control over the motor's speed and torque by adjusting the resistance in the rotor circuit. Wound rotor stators are often used in applications requiring variable speed control, such as in cranes and hoists. **3. Permanent Magnet Stator:** Permanent magnet stators use permanent magnets instead of electromagnets, eliminating the need for a DC power supply to generate the magnetic field. These stators are lightweight, efficient, and offer high power density, making them suitable for electric vehicles, wind turbines, and other high-performance applications. **4. Axial Flux Stator:** Axial flux stators have their magnetic flux oriented axially rather than radially. This unique configuration allows for a more compact design and higher power-to-weight ratio, making them ideal for applications where space is limited, such as in electric bicycles and small wind turbines. **5. Transverse Flux Stator:** Transverse flux stators feature a magnetic flux that is perpendicular to both the rotor and stator surfaces. This design offers high torque density and is particularly useful in direct drive systems like those found in some wind turbines and electric vehicles. **6. Claw Pole Stator:** Claw pole stators are used in alternators and feature a unique claw-like pole piece design that enhances magnetic flux density. These stators are known for their high efficiency and reliability, making them a preferred choice for automotive alternators. Each type of stator is engineered to optimize performance under different operating conditions. By selecting the appropriate stator design, engineers can ensure that their electrical machines operate efficiently, reliably, and effectively in various industrial, automotive, and renewable energy applications. Understanding these differences is essential for designing and maintaining complex electrical systems that power our modern world.
The Role of a Stator in Electrical Systems
In electrical systems, the stator plays a pivotal role in the functioning of motors and generators. This stationary component is integral to the operation of these devices, and its performance directly impacts the overall efficiency and reliability of the system. The stator's interaction with the rotor is fundamental, as it sets the stage for the electromagnetic induction process that converts mechanical energy into electrical energy or vice versa. Understanding how the stator interacts with the rotor is crucial, as it determines the efficiency and performance of the entire system. The electromagnetic induction process, facilitated by the stator's magnetic field, is the core mechanism behind energy conversion. Finally, the efficiency and performance of the stator are critical factors that influence the system's overall output and longevity. By examining these aspects, we can gain a comprehensive understanding of the stator's role and its significance in electrical systems. Let's delve into the first of these key areas: the interaction between the stator and the rotor.
Interaction with the Rotor
Interaction with the Rotor is a crucial aspect of understanding the role of a stator in electrical systems. The stator, which is the stationary part of an electric motor or generator, interacts dynamically with the rotor, the moving component. This interaction is fundamental to the operation of these devices. In an electric motor, the stator generates a magnetic field when an alternating current (AC) flows through its windings. This magnetic field induces a torque on the rotor, causing it to rotate. The design and alignment of the stator's magnetic poles relative to those of the rotor ensure efficient energy transfer and smooth operation. For instance, in a three-phase induction motor, the stator's three-phase windings create a rotating magnetic field that interacts with the rotor's conductive bars, inducing currents and subsequent magnetic fields in the rotor, which then interact back with the stator's field to produce rotation. In generators, the process is reversed; the rotor's movement generates a magnetic field that induces voltage in the stator windings. Here, the interaction between the rotor and stator is critical for efficient power generation. The speed and strength of the rotor's magnetic field determine the voltage and frequency of the output electricity. Proper alignment and synchronization between the rotor and stator are essential to maintain optimal performance and prevent overheating or mechanical stress. The materials used in both components also play a significant role in their interaction. High-quality magnetic materials in both the stator and rotor enhance the magnetic field strength, reducing energy losses and improving efficiency. Additionally, advanced designs such as laminated cores in the stator help reduce eddy currents, further optimizing performance. In summary, the interaction between the stator and rotor is at the heart of electrical machine operation. Understanding this interaction is key to designing and maintaining efficient motors and generators. It highlights the importance of precise engineering and material selection to ensure that these critical components work harmoniously together, enabling reliable and efficient electrical power conversion. This synergy underscores why the stator's role is so pivotal in electrical systems, making it an indispensable component for various industrial and domestic applications.
Electromagnetic Induction Process
Electromagnetic induction is a fundamental process that underpins the operation of many electrical systems, including those involving stators. This phenomenon, discovered by Michael Faraday in 1831, describes how an electric current is generated in a conductor by changing the magnetic field around it. In the context of a stator, which is the stationary part of an electric motor or generator, electromagnetic induction plays a crucial role in converting mechanical energy into electrical energy or vice versa. When a magnetic field moves relative to a conductor, such as the coils of wire in a stator, it induces an electromotive force (EMF) in the conductor. This EMF drives an electric current through the circuit. The direction of the induced current is determined by Lenz's law, which states that the induced current will flow in such a way as to oppose the change in the magnetic field that caused it. In an electrical generator, for example, the stator's coils are stationary while the rotor (the moving part) carries magnets that rotate within the stator. As the rotor spins, it creates a changing magnetic field around the stator coils, inducing an EMF and thus generating electricity. In an electric motor, the process is reversed. Here, the stator coils carry an alternating current (AC) that generates a rotating magnetic field. This field interacts with the magnets on the rotor, causing it to rotate. The efficiency and performance of both motors and generators depend significantly on the design of the stator and its ability to effectively induce or respond to electromagnetic fields. The design of the stator involves careful consideration of factors such as coil configuration, material selection, and thermal management to ensure optimal performance. For instance, laminated steel cores are often used in stators to reduce eddy currents and improve efficiency. Additionally, advanced materials like permanent magnets and high-temperature superconductors are being integrated into stator designs to enhance power density and efficiency. In summary, electromagnetic induction is the heart of stator functionality in electrical systems. It enables the conversion between mechanical and electrical energy, making it possible for motors to drive mechanical loads and for generators to produce electricity. Understanding this process is essential for designing and optimizing stators for various applications, from industrial machinery to consumer electronics. By leveraging the principles of electromagnetic induction, engineers can create more efficient, reliable, and powerful electrical systems that meet the demands of modern technology.
Efficiency and Performance
Efficiency and performance are critical components in the operation of electrical systems, particularly when it comes to the role of a stator. The stator, a stationary part of an electric motor or generator, plays a pivotal role in converting electrical energy into mechanical energy or vice versa. Its design and construction significantly influence the overall efficiency and performance of the system. For instance, in an electric motor, the stator's magnetic field interacts with the rotor's magnetic field to produce torque. The efficiency of this interaction is heavily dependent on factors such as the stator's winding configuration, material quality, and thermal management. High-quality materials with low electrical resistance and high magnetic permeability can enhance the stator's ability to generate a strong, consistent magnetic field, thereby increasing the motor's efficiency. Additionally, advanced cooling systems can help manage heat dissipation, which is crucial for maintaining optimal performance over extended periods. In generators, the stator's efficiency directly impacts the output voltage and current stability. A well-designed stator ensures that the magnetic flux is evenly distributed, minimizing energy losses and maximizing power output. This is particularly important in applications where consistent power supply is essential, such as in industrial processes or renewable energy systems. Moreover, advancements in technology have led to the development of more efficient stator designs. For example, the use of permanent magnets in some stators eliminates the need for electrical excitation currents, reducing energy consumption and increasing overall system efficiency. Similarly, innovative materials like rare-earth magnets and high-temperature superconductors are being integrated into stator designs to enhance performance under various operating conditions. The integration of smart technologies also enhances the efficiency and performance of stators. Real-time monitoring and control systems can optimize stator operation by adjusting parameters such as voltage and frequency based on load demands. This not only improves efficiency but also extends the lifespan of the stator by preventing overheating and other forms of wear. In conclusion, the efficiency and performance of electrical systems are intricately linked to the design and operation of the stator. By leveraging advanced materials, innovative designs, and smart technologies, engineers can significantly improve the overall efficiency and reliability of these systems. This underscores the critical role that a stator plays in ensuring optimal performance in a wide range of electrical applications.
Applications and Uses of Stators
Stators, a crucial component in various electrical and mechanical systems, play a pivotal role in transforming electrical energy into mechanical energy or vice versa. Their applications span across multiple industries, each leveraging their unique properties to enhance efficiency and performance. In the industrial and commercial sectors, stators are integral to motors and generators, driving machinery and powering facilities. In automotive and aerospace applications, they are essential for electric vehicles and aircraft, contributing to the development of sustainable transportation solutions. Additionally, stators are vital in renewable energy systems, particularly in wind turbines and hydroelectric power plants, where they help convert kinetic energy into electrical power. Understanding the diverse uses of stators is crucial for appreciating their impact on modern technology. This article will delve into these applications, starting with the industrial and commercial uses of stators, where their presence is felt in everyday operations and industrial processes.
Industrial and Commercial Uses
In the realm of industrial and commercial applications, stators play a pivotal role in various sectors due to their versatility and efficiency. A stator, the stationary component of an electric motor or generator, is crucial for converting electrical energy into mechanical energy and vice versa. In industrial settings, stators are integral to the operation of large machinery such as pumps, fans, and conveyor systems. For instance, in manufacturing plants, stators power the motors that drive assembly lines, ensuring continuous production with minimal downtime. Similarly, in power generation facilities, stators are key components of generators that produce electricity on a massive scale, meeting the energy demands of entire cities. In commercial environments, stators are equally essential. They power HVAC systems in office buildings and shopping malls, maintaining comfortable temperatures and air quality. In the automotive industry, stators are used in electric vehicles and hybrid cars, contributing to the growing trend of sustainable transportation. Additionally, stators find applications in renewable energy systems such as wind turbines and hydroelectric power plants, where they help convert kinetic energy into electrical power. The reliability and durability of stators make them indispensable in critical infrastructure like water treatment plants and sewage systems. Here, they ensure that pumps operate consistently to maintain water quality and public health standards. Furthermore, in the agricultural sector, stators power irrigation systems and farm machinery, enhancing crop yields and efficiency. The design and construction of stators also cater to specific industrial needs. For example, explosion-proof stators are used in hazardous environments such as chemical plants and oil refineries to prevent accidents. High-temperature stators are employed in steel mills and foundries where extreme conditions prevail. The customization of stators to meet unique operational requirements underscores their adaptability and importance across diverse industries. Moreover, advancements in technology have led to the development of more efficient and compact stator designs. These innovations enable better performance, reduced energy consumption, and lower maintenance costs. For instance, permanent magnet stators used in high-efficiency motors offer superior torque-to-weight ratios, making them ideal for applications requiring high power density. In summary, the industrial and commercial uses of stators are multifaceted and critical. From powering heavy machinery in manufacturing plants to driving renewable energy systems, stators are fundamental components that ensure smooth operations and efficiency across various sectors. Their reliability, adaptability, and continuous technological improvements make them an indispensable part of modern industrial and commercial infrastructure.
Automotive and Aerospace Applications
In the realms of automotive and aerospace engineering, stators play a pivotal role in the performance and efficiency of various critical systems. Within the automotive sector, stators are integral components of electric motors and generators, such as those found in hybrid and electric vehicles. Here, they work in tandem with rotors to convert electrical energy into mechanical energy, enabling smooth acceleration and efficient power transmission. For instance, in regenerative braking systems, the stator helps capture kinetic energy and convert it back into electrical energy, which is then stored in the vehicle's battery. This not only enhances fuel efficiency but also reduces wear on traditional braking components. In aerospace applications, stators are equally crucial, particularly in the context of aircraft electrical systems. They are used in generators and motors that power essential onboard systems such as navigation, communication, and lighting. The reliability and durability of these stators are paramount due to the harsh operating conditions encountered during flight, including extreme temperatures and vibrations. Additionally, stators are employed in the electric motors of modern electric and hybrid-electric propulsion systems being developed for future aircraft. These systems aim to reduce emissions and noise while improving overall efficiency, making stators a key technological component in the evolution of sustainable aviation. Moreover, in both industries, the design and materials used for stators are continually being advanced to meet stringent performance requirements. For example, the use of high-temperature superconducting materials in stators can significantly enhance their efficiency and power density. Similarly, advancements in magnetic materials and coil designs have led to more compact and lightweight stators, which are particularly beneficial in aerospace where weight reduction is critical for fuel efficiency and payload capacity. The integration of advanced technologies such as sensor feedback systems and real-time monitoring also ensures that stators operate optimally under various conditions. This not only extends their lifespan but also allows for predictive maintenance, reducing downtime and improving overall system reliability. In summary, the role of stators in automotive and aerospace applications is multifaceted and indispensable, driving innovation and efficiency in these industries while paving the way for future technological advancements.
Renewable Energy Systems
Renewable energy systems, a cornerstone of modern sustainability, are increasingly reliant on advanced technologies to maximize efficiency and reliability. Among these technologies, stators play a pivotal role in various applications. In the context of renewable energy, stators are integral components of electrical generators and motors, particularly in wind turbines and hydroelectric power plants. In wind turbines, stators are part of the generator system that converts mechanical energy from the rotating blades into electrical energy. The stator's stationary magnetic field interacts with the rotor's moving magnetic field, inducing an electrical current. This process is crucial for harnessing wind energy efficiently, as it ensures a stable and consistent power output despite varying wind speeds. The design and material of the stator can significantly impact the overall performance of the turbine, with advancements in materials like permanent magnets and high-temperature superconductors enhancing efficiency and reducing maintenance costs. Similarly, in hydroelectric power plants, stators are essential for converting the kinetic energy of water into electrical energy. Here, the stator is part of a synchronous generator that works in tandem with the turbine's rotor to produce electricity. The stator's design must withstand the high pressures and flow rates associated with hydroelectric systems, making durability and reliability paramount. Innovations in stator design have led to more efficient energy conversion, allowing hydroelectric plants to generate power with minimal environmental impact. Beyond these traditional applications, stators are also being integrated into emerging renewable energy technologies such as tidal and wave power systems. These systems harness the predictable and consistent energy from ocean tides and waves, converting it into electricity through advanced generator designs that include sophisticated stators. The unique challenges posed by marine environments necessitate specialized stator materials and designs that can withstand corrosion and extreme conditions. Furthermore, stators are vital in the development of smart grids and energy storage solutions. As renewable energy sources become more prevalent, the need for efficient energy storage and distribution systems grows. Stators in motor-generators used in battery storage systems help stabilize grid frequency and provide backup power during outages, ensuring a reliable supply of renewable energy. In conclusion, the applications and uses of stators in renewable energy systems are diverse and critical. From wind turbines to hydroelectric power plants, and from traditional to emerging technologies, stators are at the forefront of efficient energy conversion and reliability. As the world continues to transition towards a more sustainable future, advancements in stator technology will remain essential for optimizing the performance of renewable energy systems.