What Is Dtf Printing

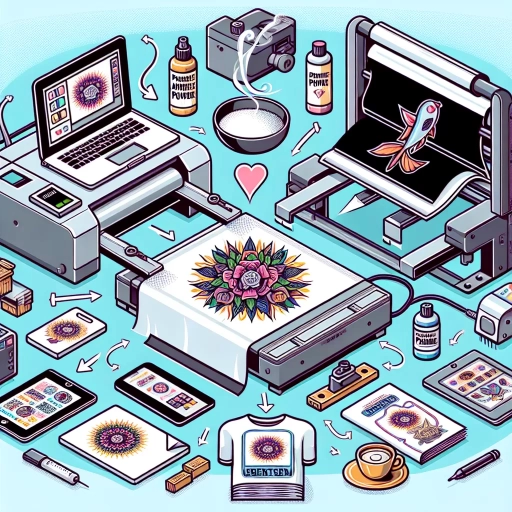
In the ever-evolving world of textile printing, Direct-to-Film (DTF) printing has emerged as a revolutionary technology that is transforming the way we produce custom apparel and accessories. This innovative method offers a versatile and efficient solution for businesses and individuals looking to create high-quality, personalized prints. In this article, we will delve into the intricacies of DTF printing, starting with an **Introduction to DTF Printing**, where we will explore its origins, key components, and how it differs from other printing techniques. We will then examine **How DTF Printing Works**, detailing the step-by-step process involved in creating these prints. Finally, we will discuss the **Applications and Benefits of DTF Printing**, highlighting its uses across various industries and the advantages it offers over traditional methods. By understanding these aspects, you will gain a comprehensive insight into why DTF printing is becoming a preferred choice for many in the textile industry. Let's begin by diving into the **Introduction to DTF Printing**.
Introduction to DTF Printing
In the ever-evolving landscape of printing technologies, Direct-to-Film (DTF) printing has emerged as a versatile and highly efficient method for producing high-quality prints. This innovative technique has garnered significant attention due to its unique advantages and broad applications. To fully understand the potential of DTF printing, it is essential to delve into its core principles, historical development, and how it distinguishes itself from other printing methods. Firstly, grasping the **Definition and Basics of DTF Printing** is crucial for appreciating its operational mechanics and benefits. This foundational knowledge will provide insight into how DTF printing works, its key components, and the process involved in creating prints. Secondly, exploring the **History and Evolution of DTF Technology** offers a deeper understanding of how this method has developed over time, influenced by technological advancements and market demands. This historical context helps in recognizing the milestones that have shaped DTF printing into what it is today. Lastly, understanding the **Key Differences from Other Printing Methods** highlights why DTF printing stands out in terms of flexibility, durability, and cost-effectiveness. By comparing it with other popular printing techniques, we can identify its unique strengths and limitations. With these aspects in mind, let's begin by examining the **Definition and Basics of DTF Printing**, which will serve as our starting point for a comprehensive exploration of this cutting-edge technology.
Definition and Basics of DTF Printing
**Definition and Basics of DTF Printing** DTF (Direct-to-Film) printing is a versatile and innovative method of textile decoration that has revolutionized the way custom designs are applied to fabrics. Unlike traditional screen printing or heat transfer methods, DTF printing involves directly printing designs onto a special film, which is then transferred to the fabric using heat and pressure. This process eliminates the need for pre-treating fabrics, making it highly adaptable for various types of materials including cotton, polyester, and blends. At its core, DTF printing involves three primary components: a special DTF film, a printer loaded with DTF ink, and a heat press. The DTF film is coated with a layer of adhesive that allows it to bond securely with the fabric during the heat transfer process. The printer uses specialized ink that adheres well to this film, ensuring vibrant and durable prints. Once the design is printed onto the film, it is cut to size and placed on the fabric. The heat press then applies high temperatures and pressure to melt the adhesive, bonding the film to the fabric. One of the key advantages of DTF printing is its flexibility and ease of use. It allows for full-color prints with intricate details and gradients, making it ideal for custom apparel, promotional products, and even small batch production. Unlike screen printing, which requires a minimum order quantity due to setup costs, DTF printing can be done in small quantities without significant additional costs. This makes it particularly appealing for businesses looking to offer personalized products or for individuals seeking unique custom designs. Moreover, DTF printing offers excellent durability and wash resistance. The adhesive used in the film ensures that the print remains intact even after multiple washes, making it suitable for everyday wear. This durability combined with its versatility in fabric compatibility has made DTF printing a preferred choice in various industries such as fashion, sports apparel, and promotional merchandise. In summary, DTF printing is a cutting-edge technique that simplifies the process of applying custom designs to fabrics while maintaining high quality and durability. Its ability to handle small orders, diverse fabric types, and intricate designs makes it an indispensable tool for both commercial and personal use. As technology continues to evolve, DTF printing is poised to become an even more integral part of the textile decoration landscape.
History and Evolution of DTF Technology
The history and evolution of Direct-to-Film (DTF) technology are deeply intertwined with advancements in digital printing and textile manufacturing. Emerging in the early 2000s, DTF printing was initially a response to the limitations of traditional screen printing and direct-to-garment (DTG) printing. The first iterations of DTF involved printing designs onto a special film using inkjet printers, which were then transferred onto fabrics using heat and pressure. This method offered greater flexibility and reduced setup times compared to screen printing, making it an attractive option for small to medium-sized print shops. As the technology progressed, significant improvements were made in ink formulations, printer hardware, and transfer processes. By the mid-2010s, DTF had become more mainstream, particularly among custom apparel manufacturers and promotional product suppliers. The introduction of high-quality, water-based inks that adhered well to various fabric types further expanded its applications. These inks were not only durable but also provided vibrant colors and soft finishes, enhancing the overall aesthetic appeal of printed garments. The COVID-19 pandemic accelerated the adoption of DTF technology as businesses sought more agile and cost-effective printing solutions. With many industries experiencing supply chain disruptions and increased demand for personalized products, DTF's ability to produce high-quality prints with minimal setup costs became a critical advantage. Modern DTF printers now integrate advanced features such as automatic ink circulation systems, improved printhead technology, and enhanced software for better color management and print optimization. Today, DTF printing is recognized for its versatility, allowing for prints on a wide range of fabrics including cotton, polyester, and blends. The process involves several key steps: printing the design onto the film, applying a hot melt adhesive powder, and then transferring the image onto the fabric using heat and pressure. This method ensures durable prints that withstand washing and wear without compromising fabric softness or breathability. The evolution of DTF technology has also been driven by environmental considerations. Eco-friendly ink options and recyclable films have become increasingly popular, aligning with consumer demands for sustainable products. Additionally, the reduced waste and lower energy consumption associated with DTF compared to traditional methods have made it an attractive choice for businesses aiming to minimize their environmental footprint. In summary, the history and evolution of DTF technology reflect a continuous pursuit of innovation in response to industry needs and consumer preferences. From its humble beginnings as a niche alternative to traditional printing methods to its current status as a versatile and sustainable solution, DTF printing has transformed the landscape of custom apparel and promotional products manufacturing. Its adaptability, cost-effectiveness, and high-quality output have solidified its position as a preferred choice for businesses seeking to produce personalized items efficiently and sustainably.
Key Differences from Other Printing Methods
When exploring the realm of printing technologies, it is crucial to understand the distinct advantages and characteristics that set Direct-to-Film (DTF) printing apart from other methods. Unlike traditional screen printing, which requires a significant setup process and is often limited to large quantities, DTF printing offers a more flexible and cost-effective solution for small to medium-sized orders. This method eliminates the need for pre-treatment or curing processes, making it a streamlined option for businesses looking to produce custom apparel quickly. In contrast to Direct-to-Garment (DTG) printing, which prints directly onto fabric using inkjet technology, DTF printing involves printing designs onto a special film that is then applied to the garment using heat and pressure. This approach allows for greater versatility in terms of fabric compatibility; while DTG is generally limited to cotton and blended fabrics, DTF can be applied to a wide range of materials including polyester, nylon, and even leather. Additionally, DTF prints tend to be more durable and less prone to fading over time compared to DTG prints. Another key difference lies in the comparison with sublimation printing. Sublimation requires specific polyester-based fabrics and involves a chemical reaction that embeds the dye into the fabric's fibers. In contrast, DTF does not require any specific fabric type and does not involve such a chemical process, making it safer and more environmentally friendly. Furthermore, sublimation often results in a softer finish but may lack the vibrant colors and detailed designs achievable with DTF. Heat transfer vinyl (HTV) is another common method used for custom apparel production. However, HTV typically involves cutting out individual designs from vinyl sheets and applying them manually or using a heat press. This process can be time-consuming and labor-intensive, especially for intricate designs. DTF printing simplifies this process by allowing for full-color prints with complex designs to be applied in one step without the need for cutting or weeding. Lastly, when compared to embroidery or appliqué techniques, DTF stands out for its ability to produce detailed, full-color designs without the high costs associated with thread or fabric usage. Embroidery and appliqué are often more expensive due to the manual labor involved and the materials required. In contrast, DTF offers an economical solution that maintains high-quality visual appeal. In summary, DTF printing distinguishes itself through its flexibility in fabric compatibility, streamlined production process, durability of prints, and cost-effectiveness compared to other printing methods. These advantages make it an attractive option for businesses and individuals seeking to produce high-quality custom apparel efficiently and economically.
How DTF Printing Works
Direct-to-film (DTF) printing has revolutionized the textile industry by offering a versatile and efficient method for customizing apparel and other fabric items. This innovative technique involves several key components and processes that ensure high-quality, durable prints. To fully understand how DTF printing works, it is essential to delve into the step-by-step process, the materials and supplies needed, and the crucial role of adhesive and transfer film. The DTF printing process itself is a meticulous sequence of steps that transform digital designs into tangible prints. Understanding each stage, from preparing the design to applying the print onto the fabric, is vital for achieving optimal results. Additionally, having the right materials and supplies is paramount; this includes specialized printers, ink, transfer films, and adhesives. The adhesive and transfer film play a pivotal role in ensuring that the print adheres smoothly and lasts long, making them integral to the overall success of the DTF printing process. By grasping these fundamental aspects, one can appreciate the complexity and precision involved in DTF printing. To begin, let's break down **The DTF Printing Process Step-by-Step**, where we will explore each critical stage in detail.
The DTF Printing Process Step-by-Step
**The DTF Printing Process Step-by-Step** The Direct-to-Film (DTF) printing process is a versatile and efficient method for creating custom designs on various fabrics, particularly popular in the apparel and textile industry. Here’s a detailed, step-by-step guide on how DTF printing works: 1. **Design Creation**: The journey begins with designing the artwork using specialized software. This involves creating or importing the design, adjusting colors, and ensuring it is mirrored since it will be printed in reverse. 2. **Printing**: The design is then printed onto a special heat transfer film using a DTF printer. These printers typically use CMYK ink sets, sometimes with additional white ink to ensure vibrant colors and opacity on dark fabrics. 3. **Curing**: After printing, the ink needs to be cured. This involves passing the printed film through a curing oven or using an infrared dryer to fix the ink onto the film. This step is crucial for ensuring durability and preventing smudging. 4. **Powder Application**: Once cured, a hot melt powder is applied evenly over the printed design. This powder acts as an adhesive that helps the design stick to the fabric during the heat press process. 5. **Shaking Off Excess Powder**: Excess powder is gently shaken off, leaving only the powder adhered to the inked areas of the design. This step ensures that only the necessary amount of adhesive remains. 6. **Heat Pressing**: The film with the design and powder is then placed on the fabric, and a heat press is applied. The heat press melts the powder, bonding it to both the fabric and the ink, thereby transferring the design onto the fabric. 7. **Peeling**: After the heat press cycle is complete, the film is carefully peeled away from the fabric. If done correctly, this leaves behind a vibrant, durable design that is resistant to fading and cracking. 8. **Finishing Touches**: Finally, any excess powder or residue can be brushed off, and the garment is ready for use. Some manufacturers may also apply additional treatments to enhance wash durability and softness. This step-by-step process highlights the precision and care required in DTF printing to achieve high-quality results. By understanding each stage, businesses and individuals can better appreciate the technology behind this innovative printing method and leverage it effectively for their custom apparel needs.
Materials and Supplies Needed for DTF Printing
To delve into the intricacies of DTF (Direct-to-Film) printing, it is crucial to understand the materials and supplies necessary for this process. DTF printing, a versatile method for customizing apparel and other textiles, requires a specific set of components to ensure high-quality results. At the core of DTF printing are the films themselves, which come in various types such as polyester or polyurethane-based films. These films are coated with a special adhesive that allows them to bond well with fabrics. In addition to the films, a key component is the DTF ink, which is specifically formulated to adhere to the film without compromising its adhesive properties. This ink is typically applied using an inkjet printer designed for DTF printing, ensuring precise and vibrant color reproduction. The printer itself must be compatible with the DTF ink and capable of handling the unique demands of this printing process. Another essential supply is the powder, often referred to as DTF powder or hot melt powder. This powder is applied over the printed film to enhance the adhesive properties and ensure a strong bond between the film and the fabric. The quality of the powder can significantly impact the durability and wash resistance of the final product. Furthermore, a heat press is indispensable for curing the printed film and bonding it to the fabric. The heat press applies the necessary pressure and temperature to melt the powder and fuse it with both the film and fabric, creating a durable and long-lasting finish. Proper calibration of the heat press is critical to avoid overheating or underheating, which can affect the quality of the bond. Other supporting materials include transfer tapes, which help in aligning and securing the printed film during the heat pressing process, and cleaning solutions to maintain the printer and other equipment. Additionally, protective gloves and a well-ventilated workspace are recommended to ensure safety while handling chemicals and inks. Understanding these materials and supplies is fundamental to mastering DTF printing. Each component plays a vital role in achieving professional-grade results, making it imperative to select high-quality products from reputable suppliers. By investing in the right materials and supplies, individuals can unlock the full potential of DTF printing, enabling them to produce custom designs that are both visually appealing and durable. This comprehensive approach ensures that every step of the DTF printing process contributes to a flawless final product, whether it's for personal projects or commercial applications.
Role of Adhesive and Transfer Film in DTF
In the realm of Direct-to-Film (DTF) printing, adhesives and transfer films play pivotal roles that are both complementary and crucial. DTF printing, a method gaining popularity for its versatility and ease of use, involves printing designs directly onto a special film that is then transferred to various substrates such as fabrics, plastics, and metals. Here, the adhesive and transfer film are the linchpins that ensure a successful transfer process. The transfer film in DTF printing is a thin, flexible sheet coated with a heat-activated adhesive. This adhesive is specifically formulated to bond well with a wide range of materials without leaving residue or damaging the substrate. When the printed design is applied to the transfer film, it adheres securely, allowing for precise alignment and smooth transfer. The quality of the transfer film directly impacts the final appearance of the print; high-quality films ensure vibrant colors, sharp details, and a durable finish. The adhesive layer on the transfer film is designed to be heat-activated, meaning it becomes tacky and adheres to the substrate when exposed to heat and pressure. This activation process is typically achieved using a heat press, which applies consistent heat and pressure to ensure a strong bond between the film and the substrate. The adhesive's properties are engineered to provide a strong initial bond while also allowing for some flexibility, which is essential for applications on fabrics that may stretch or move. Moreover, the adhesive used in DTF transfer films must balance adhesion strength with removability. For applications where the design needs to be temporary or removable without damaging the substrate, the adhesive must be formulated to release cleanly. This balance is particularly important in industries such as apparel and promotional products, where designs may need to be changed frequently. In addition to their technical roles, adhesives and transfer films contribute significantly to the user experience of DTF printing. They simplify the process by eliminating the need for additional steps like weeding or masking, which are common in other types of heat transfer methods. This streamlined process makes DTF printing more accessible to hobbyists and small businesses, as well as large-scale commercial operations. Overall, the synergy between adhesives and transfer films in DTF printing is what makes this technology so effective and versatile. By combining advanced adhesive chemistry with high-quality transfer films, DTF printing offers a reliable, efficient, and visually appealing way to decorate a variety of materials. This integration underscores why DTF has become a preferred method for many in the printing industry, offering a robust solution that meets both aesthetic and functional requirements.
Applications and Benefits of DTF Printing
Direct-to-Film (DTF) printing has revolutionized the world of textile decoration, offering a versatile, efficient, and cost-effective solution for various industries. This innovative technique stands out due to its wide range of applications, significant advantages over traditional screen printing methods, and its ability to streamline production processes. In this article, we will delve into the common uses of DTF printing across different sectors, highlighting its adaptability and utility. We will also explore the advantages DTF printing holds over traditional screen printing, including its flexibility, reduced setup times, and higher quality outputs. Additionally, we will discuss the cost-effectiveness and time efficiency of DTF printing, which make it an attractive option for businesses seeking to optimize their production workflows. By understanding these aspects, it becomes clear why DTF printing is gaining traction in multiple industries. Let's begin by examining the common uses of DTF printing in various industries, where its impact is most pronounced.
Common Uses of DTF Printing in Various Industries
**Common Uses of DTF Printing in Various Industries** Direct-to-Film (DTF) printing has revolutionized the way various industries approach customization and branding, offering a versatile and efficient solution for producing high-quality, durable prints. In the **apparel industry**, DTF printing is widely used for creating custom t-shirts, hoodies, and other clothing items. Unlike traditional screen printing or heat transfer methods, DTF allows for intricate designs and vibrant colors on a variety of fabrics without the need for pre-treatment or post-treatment processes. This makes it ideal for small to medium-sized orders and on-demand printing services. In **promotional products**, DTF printing is utilized to personalize items such as tote bags, mugs, and phone cases. The ability to print detailed graphics and text on non-traditional surfaces makes it a go-to method for businesses looking to create unique promotional materials. For **event marketing**, DTF printing enables the quick production of branded merchandise like banners, stickers, and custom signs that can be easily applied and removed without damaging the surface. The **automotive industry** also benefits from DTF printing by using it to create custom decals, logos, and graphics for vehicles. These prints are resistant to weather conditions and can withstand the wear and tear associated with outdoor use. Additionally, in **sports and fitness**, DTF printing is used to customize athletic wear, water bottles, and other equipment with team logos or personal messages. In **retail and e-commerce**, DTF printing allows businesses to offer personalized products such as custom phone cases, laptop skins, and other accessories. This personalization option enhances customer engagement and satisfaction while providing a competitive edge in the market. Furthermore, **educational institutions** use DTF printing for creating branded materials like school uniforms, water bottles, and notebooks. The **healthcare sector** also leverages DTF printing for producing custom labels for medical equipment and supplies. These labels are durable and can withstand various environmental conditions, ensuring clear identification even in high-stress environments. Lastly, in **art and design**, artists and designers use DTF printing to create unique pieces on various substrates such as canvas, wood, or metal, offering endless possibilities for artistic expression. Overall, the versatility of DTF printing makes it an indispensable tool across multiple industries, providing a cost-effective and efficient way to produce high-quality prints that meet diverse needs and applications. Its ability to handle complex designs on various surfaces without extensive setup or post-processing steps has made it a preferred choice for businesses seeking to enhance their branding efforts and customer engagement strategies.
Advantages Over Traditional Screen Printing Methods
**Advantages Over Traditional Screen Printing Methods** Direct-to-Film (DTF) printing offers several compelling advantages over traditional screen printing methods, making it a preferred choice for many in the textile industry. One of the most significant benefits is its versatility and flexibility. Unlike screen printing, which requires a separate screen for each color and design, DTF printing allows for full-color prints with intricate details and gradients without the need for multiple screens. This reduces setup time and costs, making it more economical for small to medium-sized orders. Another advantage of DTF printing is its ability to produce high-quality images with fine details and vibrant colors. The process involves printing directly onto a special film that is then applied to the fabric using heat and pressure, ensuring a crisp and durable finish. This results in prints that are resistant to fading and wear, maintaining their quality even after multiple washes. In contrast to traditional screen printing, which often requires a minimum order quantity due to the high setup costs, DTF printing can handle both large and small orders efficiently. This makes it ideal for custom orders, promotional products, and niche markets where smaller quantities are needed. Additionally, the absence of minimum order requirements allows businesses to test new designs without committing to large quantities. The environmental impact is also a significant factor. Traditional screen printing involves the use of chemicals and inks that can be harmful to the environment. DTF printing, on the other hand, uses eco-friendly inks and a water-based adhesive, reducing the ecological footprint of the printing process. Furthermore, DTF printing offers greater ease of use compared to screen printing. The process does not require specialized training or equipment beyond a standard heat press and printer, making it accessible to a wider range of users. This simplicity also translates into faster turnaround times, as there is no need for the lengthy setup and drying times associated with screen printing. In terms of material compatibility, DTF printing excels by allowing prints on a variety of fabrics including cotton, polyester, and blends. This versatility is particularly beneficial for businesses that need to print on different types of materials without compromising on quality. Overall, DTF printing stands out as a superior alternative to traditional screen printing due to its cost-effectiveness, high-quality output, environmental sustainability, ease of use, and flexibility in handling diverse fabric types and order sizes. These advantages make it an indispensable tool for businesses looking to enhance their textile printing capabilities while maintaining efficiency and quality.
Cost-Effectiveness and Time Efficiency of DTF Printing
**Cost-Effectiveness and Time Efficiency of DTF Printing** Direct-to-Film (DTF) printing stands out as a highly cost-effective and time-efficient method in the realm of textile printing. One of the primary advantages of DTF printing is its ability to minimize upfront costs. Unlike traditional screen printing, which requires significant investment in screens and setup fees, DTF printing allows for on-demand production without the need for expensive equipment or large minimum order quantities. This makes it an ideal choice for small businesses, startups, and individuals looking to produce custom apparel without breaking the bank. In terms of time efficiency, DTF printing excels by offering a streamlined process that reduces turnaround times significantly. The technology allows for rapid production of high-quality prints, enabling businesses to meet tight deadlines and capitalize on timely marketing opportunities. Unlike other methods that may require days or even weeks for preparation and production, DTF printing can produce finished products in a matter of hours. This speed is particularly beneficial for promotional events, seasonal sales, or any situation where quick turnaround is crucial. Moreover, the versatility of DTF printing contributes to its cost-effectiveness. The process allows for printing on a wide range of fabrics, including cotton, polyester, and blends, without the need for pre-treatment or post-treatment processes. This flexibility eliminates additional costs associated with fabric preparation and ensures that businesses can offer a diverse product line without incurring extra expenses. Another key aspect is the reduction in waste and errors. With DTF printing, each print is produced individually, which means there is no risk of large batches being ruined due to errors. This precision not only saves resources but also reduces the environmental impact by minimizing waste. Additionally, the digital nature of DTF printing allows for precise color matching and high-resolution images, ensuring that every print meets the desired quality standards. From a labor perspective, DTF printing is also highly efficient. The automated process requires minimal manual intervention, reducing labor costs and the potential for human error. This automation also enables continuous production, allowing businesses to operate around the clock without significant increases in labor expenses. In summary, the cost-effectiveness and time efficiency of DTF printing make it an attractive option for businesses seeking to produce high-quality custom apparel quickly and affordably. By eliminating high upfront costs, reducing turnaround times, offering versatility in fabric options, minimizing waste and errors, and optimizing labor efficiency, DTF printing provides a competitive edge in the textile industry. Whether you are a small business owner or a large enterprise, DTF printing offers a reliable and efficient solution for your custom printing needs.