What Is Dcs

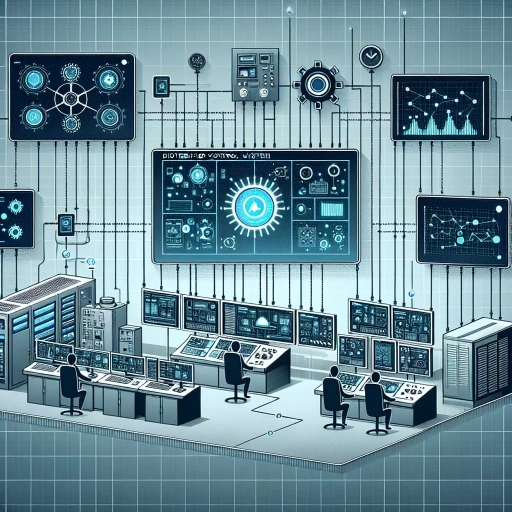
In the realm of industrial automation, Distributed Control Systems (DCS) play a pivotal role in enhancing efficiency, reliability, and scalability. A DCS is a sophisticated control system that integrates various components to manage and monitor industrial processes in real-time. This article delves into the multifaceted world of DCS, exploring its fundamental principles, diverse applications across various industries, and the significant advantages it offers. We will begin by **Understanding the Basics of DCS**, where we will dissect the core components and operational mechanisms that make DCS a cornerstone of modern industrial control. From there, we will examine **Applications and Industries Using DCS**, highlighting how different sectors leverage this technology to optimize their operations. Finally, we will discuss **Advantages and Future Trends of DCS**, shedding light on its benefits and the evolving landscape that promises even greater innovations. By grasping these aspects, readers will gain a comprehensive understanding of DCS and its transformative impact on industrial processes. Let's start with the foundation: **Understanding the Basics of DCS**.
Understanding the Basics of DCS
In the realm of industrial automation, Distributed Control Systems (DCS) play a pivotal role in managing and optimizing complex processes. To fully grasp the functionality and significance of DCS, it is essential to delve into its foundational aspects. This article aims to provide a comprehensive overview, starting with the **Definition and History of DCS**, which explores the evolution and core principles behind these systems. Next, we will examine the **Key Components and Architecture** that make up a DCS, highlighting the critical elements that enable seamless control and monitoring. Finally, we will discuss the **Types of DCS Systems**, shedding light on the various configurations and applications that cater to different industrial needs. By understanding these fundamental aspects, readers will gain a solid foundation in the basics of DCS, equipping them to navigate the intricacies of these sophisticated systems effectively. This knowledge is crucial for anyone seeking to leverage the full potential of DCS in their industrial operations. Understanding the Basics of DCS is not just about technical jargon; it's about mastering the tools that drive efficiency and innovation in modern industry.
Definition and History of DCS
**Definition and History of DCS** Distributed Control Systems (DCS) are sophisticated industrial control systems that integrate various components to monitor, control, and optimize processes in real-time. At its core, a DCS is designed to distribute control functions across multiple nodes or stations, each handling specific tasks within the overall system. This decentralized approach enhances reliability, flexibility, and scalability compared to traditional centralized control systems. The history of DCS dates back to the 1970s when the first generation of DCS emerged as a response to the limitations of earlier control systems. These early systems were primarily based on proprietary hardware and software, making them expensive and inflexible. However, they marked a significant shift from analog control systems by introducing digital technology, which allowed for greater precision and automation. In the 1980s, advancements in microprocessor technology led to the development of second-generation DCS. These systems were more robust and featured improved user interfaces, better diagnostics, and enhanced communication capabilities. This era saw the introduction of open architectures and standardized communication protocols, such as Modbus and Ethernet, which facilitated interoperability between different vendors' equipment. The 1990s witnessed the advent of third-generation DCS, characterized by the widespread adoption of commercial off-the-shelf (COTS) hardware and software. This transition enabled greater cost-effectiveness and easier integration with other enterprise systems. The use of Windows-based platforms and web technologies further enhanced user experience and remote access capabilities. In recent years, the evolution of DCS has been influenced by the Industrial Internet of Things (IIoT) and Industry 4.0 initiatives. Modern DCS systems leverage advanced technologies such as cloud computing, big data analytics, and artificial intelligence to provide real-time insights and predictive maintenance. These advancements have transformed DCS into a critical component of smart manufacturing, enabling industries to achieve higher levels of efficiency, productivity, and sustainability. Understanding the basics of DCS involves recognizing its historical development from proprietary systems to open architectures, as well as its current integration with cutting-edge technologies. This knowledge is essential for appreciating how DCS can be tailored to meet specific industrial needs, ensuring optimal performance and innovation in various sectors. By grasping the fundamentals of DCS, users can better navigate the complexities of modern industrial automation and capitalize on the benefits these systems offer.
Key Components and Architecture
Understanding the basics of Distributed Control Systems (DCS) hinges on grasping its key components and architecture. At the heart of a DCS lies a network of interconnected nodes that work in harmony to control and monitor industrial processes. The primary components include **Process Control Units (PCUs)**, **Input/Output (I/O) Modules**, **Human-Machine Interfaces (HMIs)**, and **Communication Networks**. **Process Control Units (PCUs)** are the brain of the DCS, executing control algorithms and logic to manage the process. These units are typically distributed across the plant, allowing for localized control and reducing the risk of system-wide failures. **I/O Modules** interface directly with field devices such as sensors, actuators, and valves, collecting data and implementing control actions. These modules are usually located near the process equipment to minimize signal transmission delays. **Human-Machine Interfaces (HMIs)** provide operators with real-time data visualization and control capabilities. HMIs can range from simple operator stations to complex control rooms, offering intuitive interfaces for monitoring process variables, setting parameters, and responding to alarms. They are crucial for ensuring that operators can make informed decisions quickly. The **Communication Networks** are the backbone of a DCS, facilitating data exchange between various components. These networks can be based on proprietary protocols or open standards like Ethernet or Fieldbus. They ensure that data is transmitted reliably and efficiently, supporting both real-time control and historical data logging. The architecture of a DCS is designed for redundancy and fault tolerance. It typically follows a hierarchical structure: at the top level, there are **Supervisory Control Systems** that oversee the entire process; below this, **Control Networks** manage specific sections of the plant; and at the lowest level, **Field Devices** interact directly with the process. This hierarchical approach allows for scalable and flexible system design, enabling easy integration of new components or expansion of existing systems. In addition to these core elements, modern DCS architectures often incorporate advanced features such as **Redundancy Systems** to ensure continuous operation even in the event of component failures, **Cybersecurity Measures** to protect against unauthorized access, and **Data Analytics Tools** to optimize process performance. Understanding these components and their interplay is essential for leveraging the full potential of a DCS in industrial automation, ensuring efficient, reliable, and safe operation of complex processes. By integrating these elements seamlessly, a well-designed DCS can significantly enhance productivity, reduce downtime, and improve overall plant performance.
Types of DCS Systems
**Types of DCS Systems** In the realm of Distributed Control Systems (DCS), various types cater to different industrial needs, each offering unique advantages and functionalities. **Centralized DCS** systems are the most traditional form, where control functions are concentrated in a central location. This setup is often used in smaller, more straightforward processes where simplicity and ease of management are paramount. However, it can be less flexible and more vulnerable to single-point failures. **Decentralized DCS** systems, on the other hand, distribute control functions across multiple nodes or controllers, each handling specific parts of the process. This architecture enhances redundancy and fault tolerance, making it ideal for complex and large-scale operations. Decentralized systems also facilitate easier expansion and modification as the process evolves. **Hybrid DCS** systems combine elements of both centralized and decentralized architectures. They leverage the strengths of each by centralizing higher-level control functions while decentralizing lower-level control tasks. This hybrid approach allows for greater flexibility and scalability, making it suitable for a wide range of industrial applications. Another significant category is **Open Architecture DCS**, which emphasizes interoperability and standardization. These systems use open communication protocols and modular designs, enabling seamless integration with various third-party devices and software. This openness facilitates easier maintenance, upgrades, and integration with other systems, reducing vendor lock-in and enhancing overall system longevity. **Redundant DCS** systems are designed with high availability in mind, featuring duplicate components that can take over immediately if a primary component fails. This redundancy is crucial in critical processes where downtime can have severe consequences, such as in power generation or chemical processing. **Wireless DCS** systems leverage wireless communication technologies to connect sensors, actuators, and controllers. This approach reduces cabling costs and complexity, making it easier to install and maintain systems in remote or hard-to-reach areas. However, wireless systems must address concerns related to security and reliability. Lastly, **Cloud-based DCS** systems integrate cloud computing capabilities into traditional DCS architectures. These systems offer enhanced data analytics, remote monitoring, and collaborative capabilities. Cloud-based DCS also provides scalability and cost savings by reducing the need for on-premise infrastructure. Each type of DCS system is tailored to meet specific operational requirements, ensuring that industries can select the most appropriate solution to optimize their processes efficiently. Understanding these different types is essential for making informed decisions about which DCS system best aligns with an organization's needs and goals.
Applications and Industries Using DCS
In the modern industrial landscape, Distributed Control Systems (DCS) play a pivotal role in enhancing efficiency, reliability, and safety across various sectors. These sophisticated systems integrate control and information across the entire plant, enabling real-time monitoring and precise control over complex processes. The applications of DCS are diverse and far-reaching, impacting industries such as manufacturing, energy and power generation, and water treatment and distribution. In manufacturing, DCS ensures seamless production processes by optimizing resource allocation and minimizing downtime. In the energy sector, DCS is crucial for managing power generation and distribution networks efficiently. Similarly, in water treatment and distribution, DCS helps maintain water quality and ensures consistent supply. Understanding the multifaceted role of DCS in these industries is essential for appreciating its broader impact on industrial operations. This article delves into the specific applications of DCS in these key sectors, providing insights into how these systems drive innovation and excellence. By exploring these examples, readers will gain a deeper understanding of the basics of DCS and its transformative potential in various industrial contexts.
Process Control in Manufacturing
Process control in manufacturing is a critical component that ensures the efficient and reliable operation of production systems. It involves the use of various technologies and strategies to monitor, control, and optimize industrial processes. At the heart of modern process control lies the Distributed Control System (DCS), which integrates multiple control elements into a unified system. DCS allows for real-time monitoring and control of process variables such as temperature, pressure, flow rate, and level, enabling precise adjustments to maintain optimal operating conditions. In manufacturing, process control is essential for maintaining product quality, reducing waste, and enhancing safety. For instance, in chemical processing plants, DCS systems can regulate the mixing of raw materials, monitor reaction temperatures, and adjust pH levels to ensure the production of high-quality chemicals. Similarly, in oil refineries, DCS helps in managing the distillation process, optimizing the yield of different petroleum products while adhering to stringent safety standards. The applications of process control extend across various industries. In the pharmaceutical sector, DCS ensures that drug manufacturing processes comply with regulatory standards by maintaining precise control over parameters such as temperature and humidity. In food processing, it helps in controlling cooking times, temperatures, and ingredient mixing ratios to ensure consistent product quality and safety. Additionally, in power generation plants, DCS systems manage the combustion process in boilers and turbines to optimize energy output while minimizing emissions. Advanced process control techniques, such as Model Predictive Control (MPC) and Advanced Process Control (APC), are increasingly being integrated into DCS systems to further enhance efficiency. These techniques use complex algorithms to predict future process behavior and make proactive adjustments, thereby improving overall plant performance. Moreover, the integration of Internet of Things (IoT) technologies with DCS allows for greater connectivity and data analytics, enabling real-time decision-making and predictive maintenance. The benefits of effective process control in manufacturing are multifaceted. It leads to improved product consistency, reduced energy consumption, lower maintenance costs due to predictive maintenance, and enhanced operational safety. Furthermore, by optimizing production processes, manufacturers can increase throughput while minimizing environmental impact. As industries continue to evolve with technological advancements, the role of DCS in process control will remain pivotal in driving efficiency, quality, and sustainability in manufacturing operations.
Energy and Power Generation
In the realm of energy and power generation, Distributed Control Systems (DCS) play a pivotal role in ensuring efficient, reliable, and safe operations. The energy sector, encompassing power plants, renewable energy sources, and transmission systems, relies heavily on DCS to manage complex processes. For instance, in thermal power plants, DCS systems monitor and control critical parameters such as temperature, pressure, and flow rates to optimize combustion efficiency and minimize emissions. This real-time data analysis enables operators to make informed decisions quickly, thereby enhancing plant performance and reducing downtime. In the context of renewable energy, DCS is equally vital. Solar farms and wind turbines require precise control over their operational parameters to maximize energy output. DCS systems integrate data from various sensors and actuators to adjust the angle of solar panels or the pitch of wind turbine blades in response to changing environmental conditions. This dynamic control ensures that these renewable sources operate at peak efficiency, contributing significantly to the global shift towards cleaner energy. Moreover, DCS is instrumental in managing the grid distribution network. By integrating with Supervisory Control and Data Acquisition (SCADA) systems, DCS helps utilities balance supply and demand in real-time, preventing power outages and ensuring stable voltage levels across the grid. This integration also facilitates predictive maintenance by analyzing historical data trends, allowing for proactive measures to be taken before potential issues arise. The application of DCS extends beyond traditional power generation to include emerging technologies like energy storage systems. Battery storage facilities, for example, use DCS to manage charge/discharge cycles, monitor state-of-charge levels, and optimize overall system health. This level of control is crucial for maintaining the longevity of battery cells and ensuring they perform optimally under varying load conditions. In summary, DCS is a cornerstone technology in the energy and power generation sector. Its ability to provide real-time monitoring, precise control, and data-driven insights makes it indispensable for optimizing performance across various types of power plants and grid management systems. As the world continues to transition towards more sustainable energy solutions, the role of DCS will only become more critical in ensuring that these systems operate efficiently and reliably.
Water Treatment and Distribution
Water treatment and distribution are critical processes that ensure the availability of safe and clean water for various applications, including residential, industrial, and agricultural use. These processes involve a series of complex steps, from raw water intake to final distribution, which can significantly benefit from the implementation of Distributed Control Systems (DCS). In water treatment plants, DCS systems play a pivotal role in monitoring and controlling various parameters such as pH levels, turbidity, and disinfection levels. By integrating sensors and actuators with advanced control algorithms, DCS enables real-time monitoring and precise control over treatment processes like coagulation, sedimentation, filtration, and disinfection. This ensures that the treated water meets stringent quality standards before it is distributed to consumers. For instance, DCS can automatically adjust chemical dosing based on real-time data from sensors, optimizing the treatment process while minimizing chemical usage and reducing operational costs. In addition to treatment, DCS is equally crucial in the distribution phase. It helps manage water supply networks by monitoring pressure, flow rates, and water quality at different points in the distribution system. This allows for quick detection of leaks or contamination, enabling prompt action to maintain water quality and prevent losses. Advanced DCS systems can also integrate with Geographic Information Systems (GIS) to provide spatially referenced data, facilitating better management of the distribution network. Moreover, DCS enhances operational efficiency by automating routine tasks such as pump control and valve operation. It also provides historical data analysis and predictive maintenance capabilities, helping operators anticipate potential issues before they occur. This proactive approach reduces downtime and ensures continuous supply of clean water to consumers. The use of DCS in water treatment and distribution also supports regulatory compliance by providing detailed records of treatment processes and water quality parameters. This documentation is essential for meeting standards set by regulatory bodies such as the Environmental Protection Agency (EPA) in the United States. In summary, the integration of DCS in water treatment and distribution systems significantly improves the efficiency, reliability, and safety of these critical processes. By leveraging advanced control technologies, water utilities can deliver high-quality water consistently while minimizing operational costs and environmental impact. As part of broader applications and industries using DCS, the role of these systems in ensuring clean and safe water supply underscores their importance in modern infrastructure management.
Advantages and Future Trends of DCS
In the realm of industrial automation, Distributed Control Systems (DCS) have emerged as a cornerstone of modern manufacturing, offering a plethora of advantages that transform operational landscapes. At the heart of these systems lies the potential for **Improved Efficiency and Productivity**, where real-time data and automated processes streamline operations, reducing downtime and enhancing overall performance. Additionally, DCS significantly **Enhance Safety and Reliability** by providing robust monitoring and control mechanisms that mitigate risks and ensure consistent output quality. As technology continues to evolve, DCS are also poised for **Integration with Emerging Technologies**, such as AI, IoT, and cloud computing, further amplifying their capabilities and future-proofing industrial operations. Understanding these key benefits is crucial for grasping the full impact of DCS. To delve deeper into these advantages and future trends, it is essential to start by **Understanding the Basics of DCS**, laying the groundwork for a comprehensive exploration of how these systems are revolutionizing the industrial sector.
Improved Efficiency and Productivity
Improved efficiency and productivity are cornerstone advantages of Distributed Control Systems (DCS), significantly enhancing the operational capabilities of various industries. By integrating multiple control functions into a unified system, DCS streamlines processes, reduces manual intervention, and optimizes resource allocation. This holistic approach allows for real-time monitoring and control, enabling swift responses to changes in production conditions. For instance, in manufacturing, DCS can automatically adjust parameters such as temperature, pressure, and flow rates to maintain optimal operating conditions, thereby increasing throughput and reducing downtime. Additionally, advanced analytics and predictive maintenance features embedded in modern DCS solutions help in identifying potential issues before they occur, minimizing unplanned shutdowns and extending the lifespan of equipment. This proactive maintenance not only saves costs but also ensures consistent product quality, further boosting overall efficiency. Moreover, the scalability and flexibility of DCS make it an ideal solution for evolving industrial needs. As industries grow or diversify, DCS can be easily expanded or reconfigured without significant disruptions to ongoing operations. This adaptability is particularly beneficial in sectors like oil and gas, where process conditions can vary widely depending on the site and the stage of production. The user-friendly interfaces and intuitive control systems of DCS also facilitate better operator training and reduced errors, as operators can quickly understand and respond to system alerts and status updates. Furthermore, the integration of DCS with other technologies such as IoT and AI enhances its capabilities, allowing for more sophisticated automation and data-driven decision-making. Looking ahead, future trends in DCS are expected to be driven by advancements in digital technologies. The increasing adoption of Industry 4.0 principles will see DCS becoming even more interconnected with other smart systems, enabling seamless communication between different layers of the industrial hierarchy. This will lead to more autonomous operations, where systems can self-optimize and adapt to changing conditions without human intervention. Additionally, the integration of cybersecurity measures will become more critical as DCS becomes more networked, ensuring that sensitive data and control systems are protected against potential threats. Overall, the future of DCS promises unprecedented levels of efficiency and productivity, setting new benchmarks for industrial performance and innovation.
Enhanced Safety and Reliability
Enhanced safety and reliability are paramount advantages of Distributed Control Systems (DCS) in modern industrial settings. A DCS ensures that all components of a process are monitored and controlled in real-time, significantly reducing the risk of human error and system failures. By decentralizing control functions across various nodes, DCS systems can maintain operational integrity even if one node fails, thereby ensuring continuous production with minimal downtime. This redundancy is crucial in critical applications such as power plants, chemical processing, and pharmaceutical manufacturing where safety and reliability are non-negotiable. The advanced diagnostic capabilities of DCS systems allow for early detection of potential issues, enabling proactive maintenance and preventing unexpected shutdowns. Real-time data analytics and predictive maintenance tools integrated into DCS platforms provide insights that help in optimizing system performance, extending equipment lifespan, and reducing maintenance costs. Additionally, DCS systems often include robust security measures to protect against cyber threats, ensuring the integrity of the control environment and safeguarding sensitive data. In terms of future trends, the integration of emerging technologies such as artificial intelligence (AI), Internet of Things (IoT), and cloud computing is set to further enhance the safety and reliability of DCS systems. AI-driven predictive analytics will become more prevalent, allowing for more accurate forecasting and proactive measures to prevent failures. The adoption of IoT devices will expand the scope of real-time monitoring, enabling more granular control over processes. Cloud-based solutions will offer greater flexibility and scalability, allowing for seamless updates and remote access without compromising system security. Moreover, advancements in cybersecurity will be critical as DCS systems become increasingly interconnected. Future DCS architectures will likely incorporate advanced threat detection mechanisms and secure communication protocols to mitigate risks associated with cyber-attacks. The convergence of these technologies will not only enhance operational safety but also drive efficiency and innovation in industrial processes, making DCS an indispensable tool for industries aiming to achieve high reliability and safety standards. As industries continue to evolve, the role of DCS in ensuring enhanced safety and reliability will remain pivotal, driving the future of industrial automation towards greater resilience and performance.
Integration with Emerging Technologies
**Integration with Emerging Technologies** The integration of Distributed Control Systems (DCS) with emerging technologies is a pivotal aspect that underscores the future trends and advantages of DCS. As industries evolve, the seamless incorporation of cutting-edge technologies such as Artificial Intelligence (AI), Internet of Things (IoT), and Cloud Computing becomes imperative. AI, for instance, enhances predictive maintenance by analyzing real-time data from sensors and equipment, allowing for proactive interventions that minimize downtime and optimize performance. IoT expands the scope of DCS by connecting a vast array of devices, enabling real-time monitoring and control across dispersed locations. This interconnectedness facilitates more precise and efficient operations, as well as better decision-making through data-driven insights. Cloud Computing further amplifies the capabilities of DCS by providing scalable storage and processing power. This allows for the handling of vast amounts of data generated by IoT devices, enabling advanced analytics and machine learning applications. The cloud also ensures greater flexibility and accessibility, as control systems can be managed remotely, reducing the need for on-site personnel and enhancing overall system reliability. Moreover, the integration of DCS with blockchain technology promises to enhance security and transparency. By creating an immutable ledger of transactions and data exchanges, blockchain ensures that all changes to the system are traceable and tamper-proof, thereby safeguarding against cyber threats and ensuring compliance with regulatory standards. In addition, advancements in 5G networks will significantly improve communication speeds and reduce latency, making real-time control and monitoring even more effective. This will be particularly beneficial in industries requiring high-speed data transfer, such as manufacturing and energy production. The future of DCS is also likely to be influenced by augmented reality (AR) and virtual reality (VR) technologies. These tools can enhance operator training, improve maintenance procedures, and provide immersive experiences for better system understanding and control. Overall, the integration of emerging technologies with DCS not only amplifies its existing advantages but also opens up new avenues for innovation and efficiency. As these technologies continue to evolve, they will play a crucial role in shaping the future landscape of industrial automation, driving smarter, more resilient, and highly interconnected systems. This synergy between DCS and emerging technologies will be a key driver in achieving operational excellence, sustainability, and competitive advantage in various industries.