What Is A Static Load

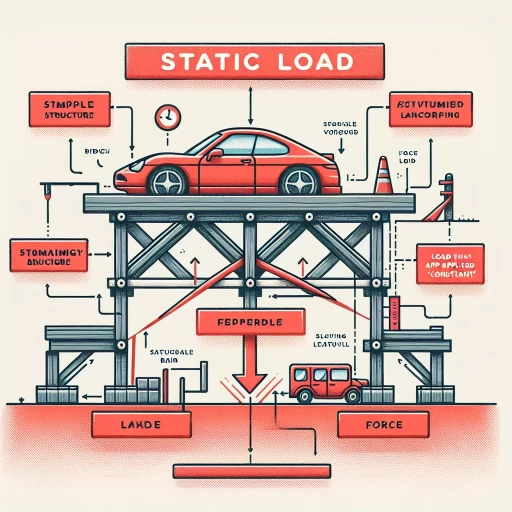
In the realm of engineering and structural analysis, understanding the concept of static load is crucial for ensuring the safety and integrity of buildings, bridges, and other infrastructure. A static load refers to a constant force applied to a structure over time, which can significantly impact its design, construction, and long-term durability. This article delves into the intricacies of static loads, beginning with **Understanding Static Load Basics**, where we explore the fundamental principles and types of static loads. We then examine **Factors Influencing Static Load**, discussing how various environmental and structural elements can affect the load's impact. Finally, we provide insights into **Calculating and Managing Static Load**, highlighting the methods and strategies engineers use to mitigate potential risks. By grasping these key aspects, professionals can better design and maintain structures that withstand the stresses imposed by static loads. Let's start by understanding the basics of static loads and how they form the foundation of structural integrity.
Understanding Static Load Basics
Understanding static load basics is crucial for engineers, architects, and anyone involved in the design and construction of structures. Static loads, which are non-dynamic forces applied to a system, play a pivotal role in determining the stability and integrity of buildings, bridges, and other infrastructure. To grasp this concept fully, it is essential to delve into three key areas: the definition and explanation of static loads, the various types of static loads that can be encountered, and their common applications in real-world scenarios. First, defining and explaining what static loads are sets the foundation for further understanding. This involves understanding the nature of these forces and how they differ from dynamic loads. Next, recognizing the different types of static loads—such as dead loads, live loads, and environmental loads—is vital for accurate structural analysis. Finally, exploring common applications where these principles are applied helps to illustrate their practical significance. By starting with a clear definition and explanation of static loads, we can then transition seamlessly into the nuances of their types and applications, providing a comprehensive overview that is both informative and engaging. This structured approach ensures that readers gain a thorough understanding of static load basics, equipping them with the knowledge necessary to tackle complex engineering challenges effectively.
Definition and Explanation
**Understanding Static Load Basics: Definition and Explanation** A static load is a type of load that remains constant over time and does not change in magnitude or direction. This concept is fundamental in various fields such as engineering, physics, and construction, where understanding the behavior of static loads is crucial for designing and analyzing structures, machines, and other systems. To delve into the definition and explanation of static loads, it's essential to differentiate them from dynamic loads, which vary over time due to factors like vibration or movement. Static loads can be further categorized into several types, each with distinct characteristics. **Dead loads**, for instance, are the weights of the permanent components of a structure, including the building itself and any fixed equipment. These loads are constant and predictable, making them easier to account for in structural design. On the other hand, **live loads** are temporary and can vary depending on the usage of the structure. While live loads are dynamic in nature because they change over time, their maximum expected values are often treated as static loads for design purposes to ensure safety and structural integrity. The analysis of static loads involves determining the distribution and impact of these forces on a structure. Engineers use various methods such as free-body diagrams and equilibrium equations to calculate the stresses and strains caused by static loads. This process helps in ensuring that the structure can withstand the applied forces without failing or deforming excessively. For example, in bridge design, engineers must consider both dead loads (the weight of the bridge itself) and live loads (the weight of vehicles crossing the bridge) to ensure that the bridge can support these forces without compromising safety. In addition to structural integrity, understanding static loads is also critical for material selection and durability assessment. Different materials have varying capacities to withstand static forces; some materials may exhibit creep or fatigue under prolonged exposure to constant loads. Therefore, selecting materials that are appropriate for the expected static load conditions is vital for maintaining the longevity of a structure. Moreover, static loads play a significant role in safety standards and regulations. Building codes and industry standards often specify minimum requirements for structures to resist static loads, ensuring public safety and preventing catastrophic failures. Compliance with these standards involves thorough analysis and testing to validate that structures can handle anticipated static loads. In summary, static loads are constant forces that do not change over time and are a critical aspect of structural design and analysis. Understanding the different types of static loads, such as dead and live loads, and their impact on structures is essential for ensuring safety, durability, and compliance with regulatory standards. By accurately calculating and managing static loads, engineers can design robust structures that withstand the forces they are subjected to, thereby safeguarding public safety and maintaining structural integrity. This foundational knowledge is indispensable for anyone involved in the design, construction, or maintenance of buildings, bridges, and other engineered systems.
Types of Static Loads
**Types of Static Loads** Understanding the various types of static loads is crucial for engineers, architects, and construction professionals to ensure the structural integrity and safety of buildings, bridges, and other infrastructure. Static loads are forces that act on a structure without changing over time, and they can be categorized into several distinct types based on their nature and application. 1. **Dead Loads**: These are the permanent weights of the structure itself, including the weight of the building materials such as concrete, steel, wood, and roofing materials. Dead loads are constant and do not change over time unless there is a modification to the structure. 2. **Live Loads**: Unlike dead loads, live loads are temporary and can vary in magnitude and location. They include the weight of people, furniture, vehicles, and any other movable objects that may be present on or within the structure. Live loads can be further divided into residential, commercial, and industrial categories depending on the intended use of the building. 3. **Snow Loads**: These loads are caused by the accumulation of snow on roofs and other horizontal surfaces. Snow loads vary significantly depending on geographical location, climate conditions, and roof design. They are particularly important in regions with heavy snowfall to prevent structural collapse. 4. **Wind Loads**: Wind exerts horizontal forces on structures that can cause bending, torsion, and uplift. The magnitude of wind loads depends on factors such as wind speed, direction, and the shape and height of the structure. Proper design considerations for wind loads are essential to prevent damage from high winds and storms. 5. **Soil and Hydrostatic Loads**: These loads arise from the pressure exerted by soil and water against foundation walls and basement walls. Soil loads depend on the density of the soil, while hydrostatic loads are influenced by groundwater levels and soil permeability. 6. **Seismic Loads**: Although seismic activity is dynamic in nature, the design process often involves static analysis to determine the maximum forces that a structure might experience during an earthquake. Seismic loads are critical in earthquake-prone areas to ensure that structures can withstand seismic forces without collapse. 7. **Impact Loads**: These are sudden forces that occur due to impacts such as those from vehicles or falling objects. While not strictly static, impact loads are often treated as static forces in design calculations because they are typically short-lived but can have significant effects on structural integrity. Each type of static load requires careful consideration during the design phase to ensure that structures are built to withstand these forces safely and efficiently. By understanding these different types of loads, engineers can design structures that are resilient, durable, and compliant with safety standards. This comprehensive approach not only enhances structural integrity but also protects human life and property by mitigating the risk of failure under various loading conditions.
Common Applications
Understanding static load basics is crucial for various engineering and construction applications, where the stability and integrity of structures are paramount. One of the most common applications of static load principles is in the design and analysis of buildings. Architects and structural engineers must ensure that buildings can withstand the weight of their own components, including walls, floors, roofs, and any permanent fixtures. This involves calculating the dead load, which is the total weight of all permanent elements of the structure. Additionally, they must consider live loads, such as the weight of occupants, furniture, and other movable items that can vary over time. By accurately determining these loads, engineers can specify appropriate materials and design elements to ensure the building's safety and longevity. Another significant application is in bridge construction. Bridges are subjected to a variety of static loads, including their own dead weight and the weight of vehicles or pedestrians using them. Engineers use static load analysis to determine the maximum stresses that different parts of the bridge will experience under various loading conditions. This helps in selecting suitable materials and designing the bridge's structural components to withstand these stresses without failing. In mechanical engineering, static loads are critical in the design of machinery and equipment. For instance, in the development of engines or gearboxes, engineers need to calculate the static loads on bearings and other components to ensure they can support the weight and forces involved without premature wear or failure. Similarly, in aerospace engineering, understanding static loads is essential for designing aircraft structures that can handle the weight of the aircraft itself as well as any cargo or passengers it may carry. Civil engineers also rely heavily on static load analysis when designing infrastructure such as dams and retaining walls. These structures must be able to resist the static forces exerted by water pressure or soil weight without compromising their stability. Incorrect calculations could lead to catastrophic failures with severe consequences. Furthermore, static load principles are applied in automotive engineering to ensure vehicle safety and performance. Car manufacturers need to consider the distribution of weight within a vehicle to optimize its stability during various driving conditions. This includes understanding how different components like engines, transmissions, and batteries contribute to the overall static load on the vehicle's chassis. In addition to these examples, static load analysis plays a vital role in offshore engineering where platforms and rigs must withstand extreme environmental conditions such as wind and wave forces. Here again, accurate calculation of static loads helps engineers design robust structures capable of withstanding these forces over long periods. In conclusion, understanding static load basics is fundamental across a wide range of engineering disciplines because it directly impacts the safety, efficiency, and durability of structures and machines. By meticulously calculating and managing static loads during the design phase, engineers can prevent potential failures and ensure that their creations perform optimally under expected conditions. This underscores the importance of thorough education and training in static load analysis for aspiring engineers across various fields.
Factors Influencing Static Load
When analyzing the factors that influence static load, it is crucial to consider a multifaceted approach that encompasses various critical elements. Static load, which refers to the weight or force exerted on a structure without any movement or vibration, is significantly affected by three primary factors: material properties, structural design, and environmental conditions. Each of these components plays a vital role in determining the overall stability and integrity of a structure under static load. Material properties, for instance, dictate how well a structure can withstand and distribute the applied load. The strength, elasticity, and durability of the materials used are fundamental in ensuring that the structure remains stable and intact. Structural design, on the other hand, involves the architectural and engineering aspects that influence how loads are transferred and distributed throughout the structure. This includes considerations such as beam configurations, support systems, and load paths. Environmental conditions, including temperature, humidity, and exposure to natural elements like wind and earthquakes, also significantly impact the performance of a structure under static load. Understanding these interrelated factors is essential for engineers and architects to design and build structures that can safely support the intended loads. By delving into each of these areas, we can gain a comprehensive insight into how static loads are managed and mitigated. Let's begin by examining the role of material properties in more detail.
Material Properties
Material properties play a crucial role in determining how a structure or component behaves under static load. These properties are intrinsic characteristics of the material that influence its strength, durability, and overall performance. Key material properties include **tensile strength**, which is the maximum stress a material can withstand while being stretched before failing; **compressive strength**, which measures the material's ability to resist compression forces; and **shear strength**, indicating the material's resistance to shear forces that cause deformation by sliding along a plane parallel to the direction of the force. **Young's Modulus**, or elastic modulus, is another critical property that describes a material's stiffness and its ability to return to its original shape after the load is removed. Materials with high Young's Modulus are stiffer and less prone to deformation under load. **Poisson's Ratio** complements this by describing how much a material will laterally deform when subjected to longitudinal tensile loading. Understanding these elastic properties is essential for predicting how materials will behave under static loads without failing. In addition to these mechanical properties, **density** and **thermal expansion** are also significant. Density affects the weight and structural integrity of the material, while thermal expansion influences how materials respond to temperature changes, which can induce additional stresses when subjected to static loads. For instance, materials with high thermal expansion coefficients may experience significant dimensional changes with temperature variations, potentially leading to structural issues if not properly accounted for. The **yield strength** of a material is another vital property, as it marks the point at which the material begins to deform plastically rather than elastically. Beyond this point, the material will not return to its original shape even if the load is removed. Knowing the yield strength helps engineers design structures that can safely withstand static loads without entering into the plastic deformation range. Furthermore, **fracture toughness** and **fatigue strength** are important considerations for materials under repeated or cyclic loading conditions that may arise from static loads over time. Fracture toughness measures a material's resistance to crack propagation and failure, while fatigue strength indicates how well a material can withstand repeated loading cycles without failing. In summary, understanding material properties such as tensile strength, compressive strength, shear strength, Young's Modulus, Poisson's Ratio, density, thermal expansion, yield strength, fracture toughness, and fatigue strength is crucial for designing and analyzing structures subjected to static loads. These properties collectively determine how materials will respond to various types of forces and ensure that structures are safe and durable over their intended lifespan. By carefully selecting materials based on their properties relative to the anticipated loading conditions, engineers can optimize structural performance and prevent failures due to static loads.
Structural Design
When delving into the realm of structural design, understanding the factors that influence static loads is paramount. Static loads, which are constant and unchanging over time, play a crucial role in determining the integrity and stability of any structure. In structural design, engineers must meticulously consider several key factors to ensure that the structure can withstand these loads without compromising its safety or functionality. First and foremost, **material properties** are a critical consideration. The strength, stiffness, and durability of the materials used in construction directly affect how well a structure can resist static loads. For instance, steel beams are often preferred for their high tensile strength and ability to distribute loads evenly, while concrete is valued for its compressive strength. The selection of materials must align with the anticipated load conditions to prevent material failure. Another significant factor is **geometric configuration**. The shape and layout of a structure influence how loads are distributed across its components. Engineers use principles of geometry to optimize the design, ensuring that loads are transferred efficiently from one element to another. For example, arches and domes are designed to distribute loads uniformly, reducing stress concentrations that could lead to structural failure. **Environmental conditions** also significantly impact static load calculations. Factors such as soil type, groundwater levels, and climate can affect the foundation's stability and the overall structural integrity. In areas prone to earthquakes or high winds, additional design considerations must be made to account for these dynamic forces that can impose static-like loads on the structure during extreme events. Furthermore, **dead loads**—the weight of the structure itself—and **live loads**—the weight of occupants, furniture, and other movable items—must be accurately estimated. Dead loads are generally easier to predict since they are constant, but live loads can vary widely depending on the intended use of the structure. For example, a residential building will have different live load requirements compared to a commercial office space or a warehouse. Additionally, **foundation design** is essential in managing static loads. The foundation must be capable of transferring the weight of the structure to the ground without settling or shifting excessively. Different types of foundations—such as shallow foundations like footings or deep foundations like piles—are chosen based on soil conditions and the magnitude of expected loads. Lastly, **regulatory standards** and **building codes** provide guidelines that ensure structures meet minimum safety requirements. These standards often dictate specific load calculations and design methodologies that engineers must adhere to. Compliance with these regulations helps safeguard against potential failures by ensuring that all relevant factors influencing static loads have been adequately addressed. In summary, structural design involves a comprehensive analysis of various factors influencing static loads. By carefully considering material properties, geometric configurations, environmental conditions, load types, foundation design, and regulatory standards, engineers can create structures that are both safe and functional. This meticulous approach ensures that buildings and bridges can withstand the constant forces acting upon them, providing reliable service over their lifespan.
Environmental Conditions
Environmental conditions play a crucial role in influencing static loads, as they can significantly impact the structural integrity and performance of materials and structures. Temperature, humidity, and exposure to weather elements are key factors that must be considered. For instance, extreme temperatures can cause materials to expand or contract, leading to potential stress and strain on structures. In cold climates, materials may become brittle and more susceptible to cracking under load, while high temperatures can lead to softening and reduced strength. Humidity levels also affect the durability of materials; high humidity can accelerate corrosion in metals and degrade the integrity of composite materials. Additionally, environmental conditions such as wind, rain, and sunlight exposure can impose additional static loads on structures. Wind loads, for example, can exert significant pressure on buildings and bridges, necessitating robust design considerations to ensure stability. Rain and snow can add weight to roofs and other surfaces, increasing the static load that these structures must withstand. Sunlight exposure can cause thermal gradients within materials, leading to uneven expansion and contraction that may compromise structural stability. Moreover, environmental conditions can influence the long-term performance of materials through processes like weathering and degradation. Outdoor structures are often subjected to cycles of wetting and drying, freezing and thawing, which can lead to material fatigue over time. This degradation can reduce the load-bearing capacity of structures, making them more vulnerable to failure under static loads. Understanding these environmental factors is essential for engineers and architects who design structures intended to withstand various climatic conditions. By incorporating these considerations into the design process, they can ensure that structures are resilient and capable of supporting static loads safely and efficiently over their lifespan. This involves selecting appropriate materials that are resistant to environmental degradation, designing structures with adequate redundancy to handle unexpected loads, and implementing maintenance strategies to mitigate the effects of environmental conditions on structural integrity. In summary, environmental conditions are a critical component in assessing static loads because they directly impact the behavior and durability of materials and structures. By accounting for these factors during the design phase and through ongoing maintenance, it is possible to build structures that are robust, reliable, and capable of withstanding the stresses imposed by both static loads and environmental influences. This holistic approach ensures that structures remain safe and functional over their intended lifespan, even in challenging environmental conditions.
Calculating and Managing Static Load
Calculating and managing static load is a critical aspect of engineering and construction, ensuring the structural integrity and safety of buildings, bridges, and other infrastructure. This complex process involves several key components that must be meticulously considered to avoid catastrophic failures. At the heart of static load calculation lies the application of **Mathematical Formulas and Equations**, which provide the foundational tools for engineers to predict and analyze the stresses and strains on structures. These formulas, derived from principles of physics and mechanics, are essential for determining the load-bearing capacity of materials and designing structures that can withstand various types of static loads. In addition to mathematical rigor, **Engineering Standards and Guidelines** play a crucial role in ensuring that structures meet minimum safety requirements. These standards, often developed by professional organizations and regulatory bodies, outline best practices and specifications that engineers must adhere to. By following these guidelines, engineers can ensure that their designs are not only mathematically sound but also compliant with industry norms. Real-world examples and case studies further illustrate the importance of accurate static load calculations. These examples highlight both successful implementations and failures, providing valuable lessons for engineers. By examining how static loads have been managed in various projects, engineers can gain practical insights into the application of mathematical formulas and adherence to engineering standards. Understanding these elements is paramount for effective static load management, and it begins with a deep grasp of **Mathematical Formulas and Equations**.
Mathematical Formulas and Equations
When it comes to calculating and managing static loads, mathematical formulas and equations play a crucial role in ensuring structural integrity and safety. At the heart of these calculations are fundamental principles from mechanics and physics, which provide the necessary tools to analyze and predict the behavior of structures under various loads. One of the most essential formulas in this context is the equation for stress, given by \(\sigma = \frac{F}{A}\), where \(\sigma\) represents stress, \(F\) is the force applied, and \(A\) is the cross-sectional area of the material. This formula helps engineers determine whether a structure can withstand the forces acting upon it without failing. Another critical equation is Hooke's Law, which describes the relationship between stress and strain in elastic materials: \(\sigma = E \epsilon\), where \(E\) is the modulus of elasticity and \(\epsilon\) is the strain. This law is vital for understanding how materials deform under load and is used extensively in the design of beams, columns, and other structural elements. The moment of a force, calculated using \(M = F \times d\), where \(M\) is the moment, \(F\) is the force, and \(d\) is the distance from the axis of rotation to the point where the force is applied, is also crucial. Moments are essential in determining the bending and torsional stresses in beams and other structural members. For more complex structures, such as those involving multiple loads or distributed loads, integral calculus comes into play. The formula for the bending moment in a beam under a uniformly distributed load, for example, involves integrating the load function over the length of the beam: \(M(x) = \int_{0}^{x} w(x) (x - x') dx'\), where \(w(x)\) is the load per unit length and \(x'\) is a dummy variable. In addition to these specific formulas, vector analysis is often necessary to handle three-dimensional loads and complex geometries. The resultant force vector, given by \(\mathbf{R} = \mathbf{F_1} + \mathbf{F_2} + \cdots + \mathbf{F_n}\), allows engineers to combine multiple forces acting on a structure and determine their overall effect. Finally, statistical methods and probability theory are increasingly important in modern engineering practice, particularly when dealing with uncertainties in material properties or load conditions. The use of reliability-based design methods involves calculating probabilities of failure using statistical distributions and Monte Carlo simulations, ensuring that structures meet safety standards even under uncertain conditions. In summary, mathematical formulas and equations form the backbone of static load calculations, enabling engineers to predict and manage the stresses and strains on structures with precision. From basic stress calculations to complex integrals and vector analyses, these mathematical tools are indispensable for ensuring the safety and durability of buildings, bridges, and other engineered structures. By mastering these formulas and applying them rigorously, engineers can confidently design structures that withstand static loads and perform as intended over their lifespan.
Engineering Standards and Guidelines
Engineering standards and guidelines are crucial components in the calculation and management of static loads, ensuring that structures and systems are designed, constructed, and maintained to withstand various types of loads safely and efficiently. These standards, often developed by reputable organizations such as the American Society of Civil Engineers (ASCE), the American Society of Mechanical Engineers (ASME), and the International Organization for Standardization (ISO), provide a framework for engineers to follow. They cover a wide range of aspects including material properties, structural integrity, safety factors, and environmental considerations. For instance, when calculating static loads on a building, engineers must adhere to standards like ASCE 7-16, which outlines minimum design loads for buildings and other structures. This standard includes detailed guidelines on how to determine dead loads (the weight of the structure itself), live loads (the weight of occupants and movable objects), and environmental loads such as wind and snow. Similarly, in mechanical engineering, ASME standards like ASME B31.1 for power piping and ASME B31.3 for process piping provide specific requirements for designing and constructing piping systems to handle static pressures and stresses. These guidelines not only ensure compliance with regulatory requirements but also help in optimizing design and construction processes. By following established standards, engineers can minimize risks associated with structural failures and ensure that their designs are robust and reliable. For example, in bridge construction, adhering to standards such as AASHTO LRFD Bridge Design Specifications helps in ensuring that bridges can support both dead loads (the weight of the bridge itself) and live loads (the weight of vehicles). Moreover, engineering standards often include best practices for material selection, fabrication techniques, and inspection methods. This ensures that materials used are appropriate for the intended application and that fabrication processes do not introduce defects that could compromise structural integrity under static loads. Regular inspections based on these guidelines help in identifying potential issues early on, allowing for timely maintenance or repairs. In addition to technical specifications, these standards also address safety and environmental concerns. For example, standards may dictate minimum safety factors to be applied during design to account for uncertainties in load calculations or material properties. Environmental considerations might include guidelines for designing structures that can withstand natural disasters or extreme weather conditions without failing under static loads. In summary, engineering standards and guidelines are indispensable tools for calculating and managing static loads. They provide a structured approach to design, construction, and maintenance, ensuring that structures are safe, efficient, and compliant with regulatory requirements. By adhering to these standards, engineers can mitigate risks, optimize designs, and contribute to the overall reliability and longevity of engineered systems.
Real-World Examples and Case Studies
When it comes to calculating and managing static loads, real-world examples and case studies provide invaluable insights into the practical applications and challenges of this critical engineering task. For instance, consider the construction of the Burj Khalifa, the tallest building in the world. Engineers had to meticulously calculate the static loads imposed by the structure's weight, as well as external forces such as wind and seismic activity. This involved detailed analysis of the building's design, materials, and foundation to ensure that it could withstand these loads without compromising structural integrity. The success of this project highlights the importance of accurate static load calculations in ensuring safety and durability. Another compelling example is the Golden Gate Bridge in San Francisco. Here, engineers faced the challenge of managing static loads from the bridge's own weight, as well as dynamic loads from traffic and environmental factors like wind and earthquakes. The bridge's suspension design was carefully optimized to distribute these loads efficiently, demonstrating how innovative engineering solutions can mitigate the effects of static loads. Additionally, regular maintenance and inspections are crucial for managing static loads over time, as seen in the periodic checks and repairs conducted on the bridge to ensure its continued stability. In industrial settings, managing static loads is equally critical. For example, in the design of large storage tanks for chemicals or petroleum products, engineers must calculate the static loads from the weight of the tank itself and its contents. This involves considering factors such as soil conditions, tank geometry, and material properties to prevent failures that could have catastrophic consequences. The case study of a major oil storage facility in Texas illustrates this point; after a series of failures due to inadequate load calculations, a comprehensive redesign was undertaken to ensure that all static loads were properly managed, resulting in significant improvements in safety and operational reliability. Furthermore, in aerospace engineering, managing static loads is essential for ensuring the structural integrity of aircraft and spacecraft. The development of NASA's Space Shuttle program provides a notable example where precise calculations of static loads were necessary to guarantee that the vehicle could withstand launch stresses and orbital conditions. This involved sophisticated modeling and testing to validate load assumptions, underscoring the importance of rigorous analysis in managing static loads. These examples collectively emphasize that calculating and managing static loads is not merely a theoretical exercise but a practical necessity across various engineering disciplines. By studying these real-world cases, engineers can gain valuable lessons on how to approach similar challenges effectively, ensuring that structures and systems are designed to safely and efficiently handle the static loads they will encounter throughout their lifespan. This not only enhances safety but also optimizes performance and extends the operational life of critical infrastructure and equipment.