What Is A Knock Sensor

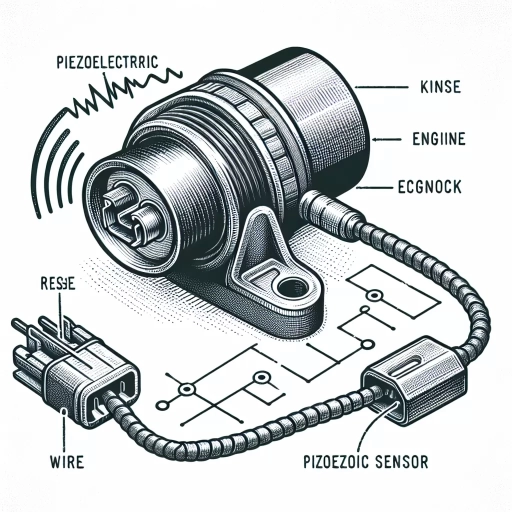
In the realm of automotive technology, one crucial component that ensures the optimal performance and longevity of modern engines is the knock sensor. This sophisticated device plays a pivotal role in preventing engine damage by detecting abnormal combustion patterns, commonly known as engine knock or pinging. To fully appreciate the significance of knock sensors, it is essential to delve into their fundamental principles, operational mechanisms, and the broader implications they have on vehicle maintenance and safety. This article will explore these aspects in detail, starting with **Understanding the Basics of a Knock Sensor**, where we will examine the core concepts behind this critical engine component. Subsequent sections will delve into **How Knock Sensors Work**, explaining the intricate processes involved in detecting engine knock, and **Importance and Applications of Knock Sensors**, highlighting their role in maintaining engine health and their various applications across different vehicle types. By understanding these key aspects, readers will gain a comprehensive insight into the vital function of knock sensors in modern automotive engineering.
Understanding the Basics of a Knock Sensor
Understanding the basics of a knock sensor is crucial for maintaining the health and performance of modern engines. This critical component plays a pivotal role in preventing engine damage by detecting abnormal combustion patterns, commonly known as engine knock or pinging. To delve into the intricacies of knock sensors, it is essential to explore three key aspects: their definition and purpose, historical development, and key components. Firstly, understanding the **definition and purpose** of knock sensors provides a foundational grasp of how they function within an engine. These sensors are designed to monitor the engine's combustion process, alerting the engine control unit (ECU) to any irregularities that could lead to potential damage. This immediate feedback allows the ECU to adjust fuel injection timing and other parameters to prevent engine knock. Secondly, examining the **historical development** of knock sensors reveals how advancements in automotive technology have led to their integration into modern vehicles. From early mechanical solutions to sophisticated electronic sensors, this evolution highlights the importance of continuous innovation in engine management systems. Lastly, identifying the **key components** of a knock sensor helps in comprehending its operational mechanics. These components typically include a piezoelectric element, wiring, and a mounting system, all working in harmony to detect and transmit critical data to the ECU. By understanding these facets, one can appreciate the significance of knock sensors in ensuring optimal engine performance and longevity. Let's begin by exploring the **definition and purpose** of knock sensors in more detail.
Definition and Purpose
A knock sensor, also known as a detonation sensor, is a critical component in modern vehicle engines designed to detect and prevent engine knock or pinging, which can lead to serious engine damage. **Definition and Purpose** of a knock sensor are intertwined with its role in maintaining optimal engine performance and longevity. The knock sensor is essentially an electronic device that listens for the distinctive sound waves produced by engine knock, a condition where the fuel-air mixture in the engine ignites prematurely, causing a knocking or pinging noise. This premature ignition can lead to overheating, reduced fuel efficiency, and potentially catastrophic engine failure if left unchecked. The primary purpose of a knock sensor is to monitor the engine's combustion process in real-time. When it detects the characteristic vibrations associated with engine knock, it sends a signal to the engine control unit (ECU). The ECU then adjusts the ignition timing to prevent further knocking by retarding the spark timing, thereby ensuring that the fuel-air mixture ignites at the correct moment. This adjustment helps in maintaining smooth engine operation, reducing wear and tear on engine components, and preventing potential damage. In addition to preventing engine knock, the knock sensor plays a crucial role in optimizing engine performance. By continuously monitoring and adjusting ignition timing based on real-time data, it helps in achieving better fuel efficiency and reducing emissions. This is particularly important in modern vehicles equipped with advanced fuel injection systems and turbochargers, where precise control over combustion is essential for optimal performance. Moreover, the knock sensor contributes to the overall reliability and durability of the vehicle. By preventing engine knock, it reduces the risk of costly repairs down the line. Regular functioning of the knock sensor also ensures that other critical components such as pistons, cylinders, and valves are protected from damage caused by abnormal combustion patterns. In summary, the definition and purpose of a knock sensor are centered around its ability to detect and mitigate engine knock through real-time monitoring and adjustments to ignition timing. This not only safeguards the engine from potential damage but also enhances overall vehicle performance, fuel efficiency, and reliability. Understanding how a knock sensor works is fundamental to appreciating its vital role in maintaining a healthy and efficient engine.
Historical Development
The historical development of the knock sensor is a fascinating narrative that underscores the evolution of automotive technology in response to the demands of engine performance and efficiency. The concept of knock sensors emerged in the early 20th century, as internal combustion engines became more sophisticated and the need to prevent engine damage from pinging or knocking grew more pressing. Initially, engine knock was managed through manual adjustments by mechanics, who would tune engines to run on lower octane fuel or adjust ignition timing to mitigate the problem. However, these methods were time-consuming and often ineffective. The first significant breakthrough came in the 1980s with the introduction of electronic knock sensors. These early sensors were piezoelectric devices that detected the high-frequency vibrations generated by engine knock. By integrating these sensors into engine management systems, car manufacturers could dynamically adjust ignition timing to prevent knock, thereby improving fuel efficiency and reducing engine wear. This innovation marked a critical shift from manual tuning to automated control, significantly enhancing engine reliability and performance. Throughout the 1990s and 2000s, advancements in sensor technology and computing power further refined knock detection systems. Modern knock sensors are highly sensitive and can detect even slight variations in engine vibrations, allowing for precise real-time adjustments. The integration of these sensors with sophisticated engine control units (ECUs) has enabled vehicles to optimize their performance under various driving conditions, including different altitudes, temperatures, and fuel types. Moreover, contemporary knock sensors are often part of broader engine management systems that incorporate multiple sensors and advanced algorithms. This holistic approach ensures that engines operate within optimal parameters, balancing power output with fuel efficiency and minimizing emissions. The development of knock sensors has also been influenced by regulatory pressures to reduce emissions and improve fuel economy, driving continuous innovation in sensor technology. In recent years, the advent of advanced materials and manufacturing techniques has led to more durable and reliable knock sensors. These improvements have extended sensor lifespan and reduced maintenance costs, making them an indispensable component of modern vehicles. Additionally, the integration of knock sensors with other vehicle systems such as turbocharging and direct fuel injection has further enhanced engine performance and efficiency. In summary, the historical development of knock sensors reflects a trajectory of technological advancement driven by the need for better engine performance, efficiency, and reliability. From their humble beginnings as simple piezoelectric devices to their current status as integral components of sophisticated engine management systems, knock sensors have played a crucial role in shaping the modern automotive landscape. Understanding this history provides a deeper appreciation for the complex interplay between technology, regulation, and innovation that underpins the operation of a knock sensor in today's vehicles.
Key Components
When delving into the intricacies of a knock sensor, it is crucial to understand its key components, as these elements collectively ensure the sensor's optimal performance and reliability. At the heart of a knock sensor lies the **piezoelectric element**, which is responsible for converting mechanical stress (vibrations) into electrical signals. This element, typically made from materials like quartz or ceramic, is highly sensitive and capable of detecting even the slightest variations in engine knock or pinging. The **housing and mounting system** is another vital component, designed to securely fasten the sensor to the engine block. This housing must be robust enough to withstand the harsh conditions of an engine environment, including high temperatures and vibrations, while also ensuring precise placement and alignment of the piezoelectric element. Proper mounting is essential for accurate signal transmission and to prevent damage to the sensor. The **electrical connector** plays a critical role in transmitting the electrical signals generated by the piezoelectric element to the engine control module (ECM). This connector must be durable and resistant to corrosion to maintain a reliable connection over time. The quality of this connection directly impacts the sensor's ability to provide accurate feedback, which is essential for the ECM to adjust fuel timing and prevent engine damage. Additionally, **signal conditioning circuits** are often integrated within or near the knock sensor to enhance signal quality. These circuits help filter out noise and amplify the weak signals produced by the piezoelectric element, ensuring that only relevant data reaches the ECM. This preprocessing step is vital for improving the sensor's accuracy and reducing false positives that could lead to unnecessary adjustments in engine performance. Finally, **thermal compensation mechanisms** are included to account for temperature variations that could affect the sensor's performance. As engine temperatures fluctuate, these mechanisms help stabilize the sensor's output, ensuring consistent and reliable data regardless of operating conditions. This feature is particularly important since engine knock can be influenced by temperature changes, and accurate detection is crucial for maintaining optimal engine performance and longevity. Understanding these key components provides a comprehensive insight into how a knock sensor operates and highlights their importance in maintaining engine health. By recognizing the roles of each component, one can better appreciate the sophisticated technology behind this critical automotive system and its contribution to efficient and safe engine operation.
How Knock Sensors Work
Knock sensors are crucial components in modern automotive engines, playing a vital role in maintaining engine performance and preventing damage. These sensors detect the knocking or pinging sounds that occur when fuel ignites prematurely in the engine, a phenomenon known as engine knock or pinging. Understanding how knock sensors work involves delving into three key areas: the principle of operation, sensor types and technologies, and signal processing and interpretation. The **principle of operation** explains how knock sensors convert mechanical vibrations into electrical signals, which are then used to adjust engine timing. This fundamental concept is the backbone of knock sensor functionality. Different **sensor types and technologies** exist, each with its own strengths and weaknesses. These variations can significantly impact the accuracy and reliability of knock detection. Finally, **signal processing and interpretation** are essential for translating raw data from the sensor into actionable information that the engine control unit (ECU) can use to make necessary adjustments. By grasping these elements, one can fully appreciate the sophisticated mechanisms behind knock sensors and their critical role in ensuring optimal engine performance. Let's start by exploring the **principle of operation** to understand the foundational mechanics that make knock sensors effective.
Principle of Operation
The principle of operation for knock sensors is rooted in the detection of abnormal engine combustion patterns, specifically those that indicate engine knocking or pinging. Engine knocking occurs when the fuel-air mixture in the combustion chamber ignites prematurely, before the spark plug fires, leading to a knocking or pinging sound. This phenomenon can cause significant damage to the engine over time, including piston damage and cylinder wall wear. Knock sensors are designed to monitor these vibrations and alert the engine control unit (ECU) to take corrective action. Typically, knock sensors are piezoelectric devices that convert mechanical stress into an electrical signal. They are usually mounted on the engine block or cylinder head, where they can best detect the vibrations caused by engine knocking. When engine knocking occurs, it generates a specific frequency of vibration that is different from the normal engine operation. The knock sensor detects these vibrations and sends an electrical signal to the ECU. The ECU then interprets this signal and adjusts the ignition timing to prevent further knocking. This adjustment typically involves retarding the ignition timing slightly to ensure that the fuel-air mixture ignites at the correct time, thus preventing premature ignition. The sensitivity of knock sensors is crucial for their effectiveness. Modern knock sensors are highly sensitive and can detect even slight deviations from normal engine operation. This sensitivity allows for real-time adjustments to be made, ensuring that the engine runs smoothly and efficiently while minimizing the risk of damage from knocking. In addition to their role in preventing engine damage, knock sensors also contribute to optimizing engine performance. By continuously monitoring engine vibrations and adjusting ignition timing accordingly, knock sensors help maintain optimal combustion conditions. This not only enhances fuel efficiency but also reduces emissions by ensuring that the combustion process is as efficient as possible. Overall, the principle of operation for knock sensors hinges on their ability to detect and respond to abnormal engine vibrations in real-time. Through their integration with the ECU, knock sensors play a critical role in maintaining engine health, optimizing performance, and ensuring that vehicles operate safely and efficiently.
Sensor Types and Technologies
In the realm of automotive diagnostics and engine performance, knock sensors play a crucial role in preventing engine damage by detecting abnormal combustion patterns. However, to fully appreciate the functionality of knock sensors, it is essential to understand the broader spectrum of sensor types and technologies that underpin modern automotive systems. **Sensor Types and Technologies** Modern vehicles are equipped with a myriad of sensors designed to monitor various parameters such as temperature, pressure, speed, and vibration. These sensors can be broadly categorized into several types based on their functionality and technology. 1. **Piezoelectric Sensors**: These are commonly used in knock sensors due to their ability to detect vibrations and convert mechanical stress into electrical signals. Piezoelectric materials like quartz or ceramic generate an electric charge when subjected to mechanical stress, making them ideal for detecting the high-frequency vibrations associated with engine knock or pinging. 2. **Thermocouples**: These sensors measure temperature differences by generating a small voltage proportional to the temperature gradient between two dissimilar metals. Thermocouples are widely used in exhaust gas temperature monitoring and engine cooling systems. 3. **Hall Effect Sensors**: Utilizing the Hall effect principle, these sensors detect magnetic fields and are often used in crankshaft and camshaft position sensors. They provide critical data for engine timing and fuel injection systems. 4. **Optical Sensors**: These employ light to measure parameters such as speed, position, and level. Optical sensors are used in applications like wheel speed sensors for anti-lock braking systems (ABS) and level sensors for fuel tanks. 5. **MEMS (Micro-Electro-Mechanical Systems) Sensors**: These miniaturized sensors integrate mechanical and electrical components on a single chip, offering high precision and reliability. MEMS sensors are used in airbag deployment systems, tire pressure monitoring systems (TPMS), and inertial measurement units. 6. **Capacitive Sensors**: These measure changes in capacitance to detect parameters such as pressure, humidity, and proximity. Capacitive sensors are used in applications like fuel level sensors and climate control systems. 7. **Inductive Sensors**: Based on the principle of electromagnetic induction, these sensors detect metal objects and are commonly used in proximity sensing applications such as parking sensors and gear position indicators. The integration of these diverse sensor technologies enables modern vehicles to operate efficiently, safely, and with optimal performance. For instance, knock sensors specifically leverage piezoelectric technology to detect the high-frequency vibrations indicative of engine knock or pinging. This detection allows the engine control unit (ECU) to adjust ignition timing and fuel mixture to prevent engine damage. Understanding the various sensor types and their underlying technologies provides a comprehensive insight into how knock sensors function within the broader context of automotive diagnostics and performance optimization. By combining data from multiple sensors, vehicles can achieve better fuel efficiency, reduced emissions, and enhanced overall performance while ensuring the longevity of critical engine components.
Signal Processing and Interpretation
Signal processing and interpretation are crucial components in understanding how knock sensors work, as these sensors rely on sophisticated algorithms to detect and analyze the subtle vibrations that indicate engine knock or pinging. At the heart of a knock sensor system lies a piezoelectric sensor, which converts mechanical stress (vibrations) into electrical signals. These signals are then transmitted to an engine control unit (ECU) where they undergo rigorous processing. The ECU employs advanced signal processing techniques such as filtering, amplification, and noise reduction to isolate the specific frequency range associated with engine knock. This involves applying band-pass filters to focus on the frequency spectrum where knock typically occurs, usually between 5 kHz to 15 kHz. Additionally, adaptive algorithms may be used to adjust the sensitivity of the sensor based on engine operating conditions, ensuring that false positives are minimized while maintaining high accuracy. Once the raw signal is filtered and amplified, it is interpreted by sophisticated software within the ECU. This interpretation involves comparing the processed signal against predefined thresholds and patterns known to indicate engine knock. The software can also account for various factors such as engine speed, load, and temperature to provide a more accurate diagnosis. In real-time, this data is used to adjust engine parameters like ignition timing and fuel injection to prevent or mitigate knock. For instance, if knock is detected, the ECU may retard ignition timing slightly to reduce pressure inside the combustion chamber and prevent damage to engine components. Moreover, modern knock sensor systems often integrate machine learning algorithms that learn from historical data and adapt over time. These algorithms can refine their detection capabilities based on the specific characteristics of the engine and its operating environment, leading to more precise and reliable knock detection. In summary, signal processing and interpretation in knock sensors involve a combination of hardware and software technologies working in tandem to detect and analyze engine vibrations accurately. By leveraging advanced filtering techniques, adaptive algorithms, and real-time data analysis, these systems play a critical role in maintaining optimal engine performance while preventing potential damage from engine knock. This sophisticated approach ensures that knock sensors remain an essential component in modern automotive engineering.
Importance and Applications of Knock Sensors
Knock sensors play a crucial role in modern automotive technology, contributing significantly to engine performance, safety, and overall vehicle reliability. These sensors are designed to detect the slightest irregularities in engine combustion, known as engine knock or pinging, which can lead to severe engine damage if left unchecked. By optimizing engine performance, knock sensors ensure that the engine operates within its optimal parameters, enhancing fuel efficiency and power output. Additionally, they prevent engine damage by alerting the engine control unit (ECU) to adjust ignition timing and fuel injection accordingly, thereby protecting the engine from potential harm. Furthermore, knock sensors are integral to modern automotive systems integration, enabling seamless communication between various components to maintain optimal vehicle operation. In this article, we will delve into the importance and applications of knock sensors, starting with their critical role in **Engine Performance Optimization**.
Engine Performance Optimization
Engine performance optimization is a critical aspect of modern automotive engineering, aimed at enhancing the efficiency, power output, and reliability of internal combustion engines. This multifaceted process involves several key components and technologies, one of which is the knock sensor. The knock sensor plays a pivotal role in preventing engine damage by detecting the onset of engine knock or pinging, a condition that occurs when the fuel-air mixture in the engine ignites prematurely. This premature ignition can lead to significant engine damage over time, including piston damage, cylinder wall scoring, and even engine failure. Optimizing engine performance begins with careful tuning of the ignition timing, fuel injection, and air-fuel mixture. However, these parameters must be balanced against the risk of engine knock. Here, the knock sensor acts as a crucial feedback mechanism. By monitoring the engine's vibrations and detecting the characteristic sound waves produced by knocking, the sensor sends signals to the engine control unit (ECU). The ECU then adjusts the ignition timing to prevent further knocking, ensuring that the engine operates within safe parameters. Beyond its role in preventing damage, the knock sensor also enables more aggressive engine tuning. By allowing the ECU to dynamically adjust ignition timing based on real-time data from the knock sensor, engineers can push the limits of engine performance without compromising reliability. This dynamic adjustment is particularly beneficial in turbocharged and supercharged engines, where higher boost pressures increase the risk of knocking. Moreover, advancements in knock sensor technology have led to more accurate and rapid detection of knocking. Modern knock sensors often use piezoelectric materials that convert mechanical stress into electrical signals, providing high sensitivity and fast response times. These improvements allow for finer control over engine operation, enabling better fuel efficiency and reduced emissions. In addition to its technical benefits, the knock sensor has significant practical applications. For instance, in high-performance vehicles, the ability to optimize engine performance without risking damage is paramount. In everyday driving conditions, the knock sensor helps maintain fuel efficiency by ensuring that the engine operates at its optimal settings. Furthermore, in regions where fuel quality varies significantly, the knock sensor can adapt to different fuel types, preventing potential damage from lower-octane fuels. In conclusion, engine performance optimization is a complex process that relies on multiple technologies working in harmony. The knock sensor stands out as a vital component in this ecosystem, providing real-time feedback that allows for precise control over engine operation. By preventing engine knock and enabling more aggressive tuning, the knock sensor contributes significantly to enhanced engine performance, efficiency, and longevity. Its importance underscores the critical role of advanced sensors in modern automotive engineering, highlighting how these technologies drive innovation and improvement in vehicle design.
Prevention of Engine Damage
Preventing engine damage is a critical aspect of maintaining vehicle performance and longevity, and knock sensors play a pivotal role in this process. Engine knock, also known as pinging or pinking, occurs when the fuel-air mixture in the engine ignites too quickly, causing a knocking or pinging sound. This premature ignition can lead to severe engine damage, including piston damage, cylinder wall scoring, and even engine failure. To mitigate these risks, modern engines are equipped with knock sensors that detect the vibrations caused by engine knock. These sensors are typically piezoelectric devices mounted on the engine block or cylinder head, designed to capture the unique frequency of engine knock vibrations. When a knock sensor detects abnormal vibrations indicative of engine knock, it sends a signal to the engine control module (ECM). The ECM then adjusts the ignition timing to prevent further knocking. This adjustment ensures that the fuel-air mixture ignites at the optimal time, thereby preventing the harmful effects of premature ignition. By continuously monitoring engine performance and making real-time adjustments, knock sensors help maintain optimal engine operation, reduce wear and tear, and prevent costly repairs. Moreover, knock sensors are essential for engines that operate under varying conditions such as different fuel types, temperatures, and driving styles. For instance, using lower-octane fuel can increase the likelihood of engine knock, but with a knock sensor, the ECM can compensate by retarding the ignition timing. This adaptability ensures that the engine runs smoothly and efficiently regardless of external factors. In addition to preventing immediate damage, knock sensors contribute to long-term engine health. By minimizing the occurrence of engine knock, these sensors help reduce stress on engine components such as pistons, rings, and cylinder walls. This reduced stress translates into extended component life and lower maintenance costs over time. Furthermore, knock sensors support the use of advanced engine technologies like turbocharging and direct fuel injection, which often operate at higher compression ratios where engine knock is more likely to occur. In summary, the prevention of engine damage through the use of knock sensors is crucial for maintaining vehicle reliability and performance. These sensors provide real-time monitoring and feedback that allow the ECM to make necessary adjustments to prevent harmful engine knock. By doing so, they protect against immediate damage and contribute to the long-term health of the engine, ensuring that vehicles run efficiently and reliably under various operating conditions. The importance of knock sensors cannot be overstated; they are a vital component in modern engine management systems, safeguarding against potential damage while optimizing engine performance.
Modern Automotive Systems Integration
Modern automotive systems integration represents a significant leap forward in vehicle technology, enhancing performance, efficiency, and safety. At the heart of this integration are sophisticated sensors and advanced computer systems that work in harmony to optimize engine operation. One crucial component in this ecosystem is the knock sensor, which plays a pivotal role in preventing engine damage from pinging or knocking. In contemporary vehicles, knock sensors are integrated into the engine management system to detect abnormal combustion patterns. These sensors use piezoelectric materials to convert mechanical stress into electrical signals, allowing the engine control unit (ECU) to monitor and adjust fuel ignition timing in real-time. This integration ensures that the engine operates within optimal parameters, preventing premature wear and potential catastrophic failure. The importance of knock sensors extends beyond mere engine protection; they are integral to maintaining fuel efficiency and reducing emissions. By continuously monitoring combustion conditions, knock sensors enable the ECU to fine-tune fuel injection and ignition timing, resulting in improved fuel economy and lower emissions. This synergy between knock sensors and other automotive systems like oxygen sensors, mass airflow sensors, and exhaust gas recirculation (EGR) systems creates a holistic approach to engine management. Moreover, modern automotive systems integration leverages advanced data analytics and machine learning algorithms to enhance the functionality of knock sensors. Real-time data from various sensors is processed to predict potential issues before they occur, enabling proactive maintenance and reducing downtime. This predictive maintenance capability not only extends the lifespan of critical components but also enhances overall vehicle reliability. The applications of knock sensors are diverse and far-reaching. In high-performance vehicles, they allow for more aggressive tuning without compromising engine integrity. In hybrid and electric vehicles, knock sensors contribute to optimizing the combustion process in hybrid powertrains, ensuring seamless transitions between electric and gasoline modes. Additionally, in autonomous vehicles, the data from knock sensors can be used to adjust driving patterns and maintain optimal engine performance under varying conditions. In summary, the integration of knock sensors into modern automotive systems underscores the evolving complexity and sophistication of vehicle technology. By ensuring optimal engine performance, enhancing fuel efficiency, reducing emissions, and supporting predictive maintenance, knock sensors are a critical component in the broader landscape of automotive innovation. Their importance highlights the interconnected nature of modern automotive systems and the continuous pursuit of better, safer, and more efficient vehicles.