What Are The Three Components Of Whmis

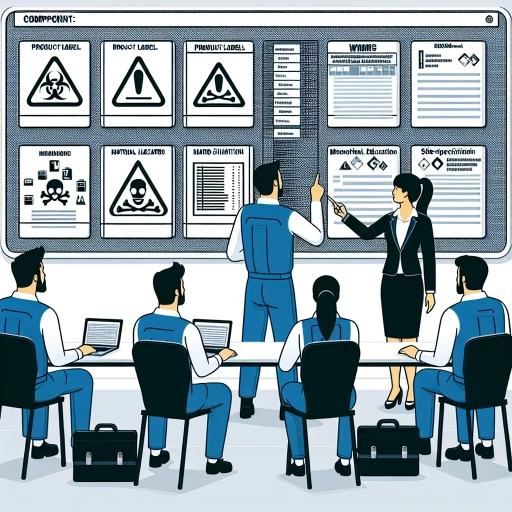
The Workplace Hazardous Materials Information System (WHMIS) is a critical framework designed to protect workers from the hazards associated with chemical substances in the workplace. This comprehensive system ensures that employers and employees are well-informed about the dangers of various chemicals, enabling them to handle them safely. WHMIS is composed of three essential components: Hazard Classification, Safety Data Sheets (SDS), and Labels and Pictograms. Each component plays a vital role in ensuring workplace safety. The Hazard Classification component categorizes chemicals based on their physical and health hazards, providing a clear understanding of the risks they pose. Safety Data Sheets (SDS) offer detailed information about the safe handling, use, storage, and emergency procedures for each chemical. Labels and Pictograms serve as visual warnings that immediately convey the hazards of a substance. Understanding these components is crucial for maintaining a safe work environment. In this article, we will delve into each of these components, starting with the foundational aspect of Hazard Classification, which sets the stage for effective chemical management and risk mitigation.
Component 1: Hazard Classification
Hazard classification is a critical component in ensuring the safe handling, storage, and use of substances. It involves a systematic approach to identify and categorize the potential dangers associated with various chemicals and materials. This process is multifaceted, encompassing several key areas that are essential for comprehensive risk assessment. First, **Chemical Classification Criteria** provide the foundational framework for determining the inherent hazards of a substance based on its chemical properties. This includes evaluating factors such as reactivity, flammability, and toxicity. Additionally, **Physical and Health Hazards** must be considered, as these can pose immediate risks to human health and safety, including explosions, fires, and exposure to harmful substances. Lastly, **Environmental Hazards** are crucial, as they address the potential impact of substances on ecosystems and the environment. Understanding these different aspects is vital for developing effective safety protocols and regulatory standards. By starting with a thorough examination of **Chemical Classification Criteria**, we can establish a robust foundation for hazard classification that informs all subsequent evaluations.
1.1 Chemical Classification Criteria
### 1.1 Chemical Classification Criteria The classification of chemicals under the Workplace Hazardous Materials Information System (WHMIS) is a critical component in ensuring workplace safety and compliance with regulatory standards. This process is guided by specific criteria that help categorize substances based on their potential hazards. The primary goal of chemical classification is to identify and communicate the risks associated with a particular substance, enabling employers and workers to take appropriate precautions. WHMIS classifies chemicals into two main categories: physical hazards and health hazards. **Physical hazards** include substances that can cause immediate harm due to their physical properties, such as flammability, explosiveness, or reactivity. For instance, flammable liquids are classified based on their flash points and boiling points, while gases are categorized according to their flammability limits. Explosives are evaluated for their potential to cause rapid release of gas and pressure, while oxidizing substances are identified for their ability to support combustion. On the other hand, **health hazards** encompass substances that can cause adverse health effects through exposure. These include toxic substances, biohazardous agents, and substances that can cause skin or eye irritation, sensitization, or other systemic effects. For example, toxic substances are classified based on their acute toxicity (LD50 or LC50 values), while carcinogens are identified if they have the potential to cause cancer. Reproductive toxins are categorized if they can affect fertility or fetal development. The classification process involves a thorough evaluation of available data from various sources including scientific literature, experimental studies, and manufacturer information. This data is then compared against established criteria set forth by regulatory bodies such as Health Canada and the Globally Harmonized System of Classification and Labelling of Chemicals (GHS). The GHS provides a framework for classifying chemicals based on standardized hazard categories and criteria, ensuring consistency across different regions. Once a chemical is classified, it must be labeled accordingly with specific hazard statements, precautionary statements, and pictograms that convey the nature of the hazard. This labeling system ensures that workers can quickly identify potential dangers and take necessary precautions to mitigate risks. Additionally, Safety Data Sheets (SDSs) must be prepared for each classified substance, providing detailed information on safe handling practices, emergency procedures, and first aid measures. In summary, the chemical classification criteria under WHMIS are designed to systematically evaluate and categorize substances based on their physical and health hazards. By adhering to these criteria and using standardized classification systems like GHS, employers can ensure a safer working environment by providing clear communication about chemical hazards through labels and SDSs. This proactive approach not only complies with regulatory requirements but also fosters a culture of safety awareness among workers handling hazardous materials.
1.2 Physical and Health Hazards
### 1.2 Physical and Health Hazards Physical and health hazards are critical components of the Workplace Hazardous Materials Information System (WHMIS), which is designed to protect workers from the dangers associated with hazardous materials. Physical hazards refer to the potential of a substance to cause harm through physical means, such as explosions, fires, or chemical reactions. These hazards can be particularly dangerous because they often involve immediate and severe consequences. For instance, flammable liquids and gases can ignite easily, leading to fires or explosions that can result in serious injury or death. Similarly, reactive substances can undergo violent chemical reactions when exposed to certain conditions, releasing harmful gases or generating intense heat. Health hazards, on the other hand, pertain to the potential of a substance to cause adverse health effects through exposure. These effects can range from acute symptoms like skin irritation or respiratory distress to chronic conditions such as cancer or neurological damage. Health hazards are often more insidious because their impacts may not be immediately apparent; prolonged exposure over time can lead to severe health issues. For example, carcinogenic substances can increase the risk of cancer after years of exposure, while neurotoxic substances can impair cognitive function and motor skills. Understanding these hazards is crucial for effective hazard classification under WHMIS. The classification process involves identifying the specific physical and health hazards associated with a substance and categorizing them according to their severity. This information is then communicated through Safety Data Sheets (SDSs) and labels on the product, ensuring that workers are aware of the risks and can take appropriate precautions to mitigate them. In practice, this means that workers handling hazardous materials must be trained to recognize the signs of physical hazards such as flammability or reactivity and take steps to prevent accidents, such as using proper storage facilities and following strict handling protocols. For health hazards, personal protective equipment (PPE) like gloves, masks, and eye protection may be necessary to prevent exposure. Additionally, employers must ensure that workplace environments are designed to minimize exposure risks through ventilation systems and other safety measures. The accurate classification of physical and health hazards under WHMIS also facilitates compliance with regulatory requirements and industry standards. It ensures that manufacturers, distributors, and employers are held accountable for providing safe working conditions and that workers have access to the information they need to protect themselves from harm. By integrating this knowledge into everyday workplace practices, organizations can significantly reduce the risk of accidents and promote a safer, healthier work environment for all employees. In summary, recognizing and classifying physical and health hazards are essential steps in the WHMIS framework. These classifications enable workers to understand the risks associated with hazardous materials and take necessary precautions to avoid harm. By prioritizing this aspect of hazard management, workplaces can enhance safety protocols, reduce the incidence of accidents, and foster a culture of safety and well-being.
1.3 Environmental Hazards
### 1.3 Environmental Hazards Environmental hazards are a critical component of the Workplace Hazardous Materials Information System (WHMIS) classification, emphasizing the potential impact of substances on the environment. These hazards are particularly relevant in industrial settings where chemicals and materials can inadvertently or intentionally be released into the environment, posing significant risks to ecosystems, wildlife, and human health. Under WHMIS, environmental hazards are categorized based on their potential to cause harm to aquatic life, persistence in the environment, and bioaccumulation potential. **Aquatic Toxicity:** Substances that are toxic to aquatic organisms can have devastating effects on aquatic ecosystems. For instance, chemicals like certain pesticides and heavy metals can be lethal to fish and other aquatic life even at low concentrations. The classification under WHMIS ensures that such substances are handled with caution and disposed of properly to prevent contamination of water bodies. **Persistence:** Persistent substances do not break down easily in the environment and can remain for extended periods, accumulating over time. Examples include certain plastics and polychlorinated biphenyls (PCBs). These substances can bioaccumulate in organisms and biomagnify through the food chain, leading to long-term ecological damage. **Bioaccumulation:** Bioaccumulative substances tend to accumulate in living organisms over time, often reaching toxic levels that can harm both the organism itself and those that consume it. Mercury, for example, is a bioaccumulative substance that can accumulate in fish and other seafood, posing health risks to humans who consume them. The classification of environmental hazards under WHMIS involves rigorous testing and evaluation to determine the potential environmental impact of a substance. This includes laboratory tests to assess aquatic toxicity, field studies to evaluate persistence and bioaccumulation, and risk assessments to predict the likelihood of environmental harm. Manufacturers and suppliers must provide detailed safety data sheets (SDSs) that include information on environmental hazards, ensuring that users are aware of the risks associated with handling these substances. Effective management of environmental hazards requires a multi-faceted approach involving proper storage, handling, and disposal practices. Employers must ensure that workers are trained on safe handling procedures and that facilities are equipped with appropriate spill response measures. Regulatory compliance is also crucial; adherence to environmental regulations helps prevent unauthorized releases into the environment. In summary, the classification of environmental hazards under WHMIS is essential for protecting both human health and the environment from the adverse effects of hazardous substances. By understanding these hazards and implementing stringent safety protocols, industries can mitigate their environmental footprint and contribute to a more sustainable future. This component of WHMIS underscores the importance of responsible chemical management and highlights the interconnectedness between workplace safety and environmental stewardship.
Component 2: Safety Data Sheets (SDS)
Safety Data Sheets (SDS) are crucial documents that provide essential information about the safe handling, use, storage, and disposal of chemical substances. These documents are a cornerstone of workplace safety, ensuring that employees, employers, and emergency responders have the necessary knowledge to manage chemical hazards effectively. This article delves into the critical aspects of SDS, starting with the **Required Sections of an SDS**, which outline the mandatory content that must be included in these sheets. We will then explore **Information Provided in Each Section**, detailing the specific data that each section contains and why it is vital for safe chemical management. Finally, we will discuss **The Importance of SDS in Workplace Safety**, highlighting how these documents contribute to a safer working environment and compliance with regulatory standards. Understanding these elements is essential for anyone working with chemicals, as it ensures that all stakeholders are well-informed and equipped to handle potential risks. Let us begin by examining the **Required Sections of an SDS**, which form the foundation of these critical safety documents.
2.1 Required Sections of an SDS
When it comes to the Safety Data Sheets (SDS) component of the Workplace Hazardous Materials Information System (WHMIS), understanding the required sections is crucial for ensuring workplace safety and compliance. An SDS is a comprehensive document that provides detailed information about a hazardous product, and it must include 16 specific sections as outlined by regulatory standards. The first section, **Identification**, provides essential details such as the product identifier, manufacturer's name, address, and contact information. This section sets the stage for all subsequent information. The **Hazard Identification** section (Section 2) is critical as it outlines the classification of the substance or mixture according to the Globally Harmonized System of Classification and Labelling of Chemicals (GHS), including hazard statements, precautionary statements, and pictograms. **Composition/Information on Ingredients** (Section 3) lists the chemical identity and concentration of all ingredients in the product, which is vital for understanding potential hazards. **First Aid Measures** (Section 4) provides immediate response actions in case of exposure, including procedures for skin and eye contact, inhalation, and ingestion. **Fire-Fighting Measures** (Section 5) details how to extinguish fires involving the product, including suitable extinguishing media and special fire-fighting procedures. **Accidental Release Measures** (Section 6) outlines steps to take in case of spills or leaks, such as containment and cleanup methods. **Handling and Storage** (Section 7) offers guidelines on safe handling practices and storage conditions to minimize risks. **Exposure Controls/Personal Protection** (Section 8) specifies recommended exposure limits, engineering controls, and personal protective equipment (PPE) necessary to prevent exposure. **Physical and Chemical Properties** (Section 9) describes the physical and chemical characteristics of the substance or mixture, such as melting point, boiling point, and solubility. **Stability and Reactivity** (Section 10) discusses the stability of the product under normal conditions and potential reactivity with other substances. **Toxicological Information** (Section 11) provides data on the toxicological effects of the substance or mixture, including acute toxicity, skin and eye irritation, and sensitization. **Ecological Information** (Section 12) addresses potential environmental impacts if the product is released into the environment. **Disposal Considerations** (Section 13) outlines safe disposal practices to prevent environmental harm. **Transport Information** (Section 14) includes details necessary for safe transportation, such as classification codes and packaging requirements. **Regulatory Information** (Section 15) summarizes relevant regulatory information not covered in other sections. Finally, **Other Information** (Section 16) includes any additional information that might be useful but is not covered elsewhere in the SDS. Each of these sections plays a vital role in ensuring that workers can handle hazardous materials safely and responsibly. By adhering strictly to these required sections, employers can help prevent accidents, reduce risks, and comply with WHMIS regulations effectively. This structured approach ensures that all necessary safety information is readily available and easily accessible when needed most.
2.2 Information Provided in Each Section
In the context of the Workplace Hazardous Materials Information System (WHMIS), Safety Data Sheets (SDS) are a crucial component that provides essential information to ensure the safe handling, use, and disposal of hazardous materials. Each section of an SDS is meticulously designed to offer comprehensive details that help workers, employers, and emergency responders understand the risks associated with a particular substance. The SDS is divided into 16 sections, each serving a specific purpose. **Section 1: Identification** includes the product identifier, manufacturer's name, address, and phone number, as well as emergency contact information. This section sets the foundation for identifying the substance and who to contact in case of an emergency. **Section 2: Hazard Identification** outlines the classification of the substance according to WHMIS criteria, including hazard statements and precautionary statements that highlight potential risks. **Section 3: Composition/Information on Ingredients** details the chemical composition of the substance, including the concentration of each ingredient. This information is vital for understanding potential health and environmental hazards. **Section 4: First Aid Measures** provides critical instructions on how to respond to exposure through various routes (skin, eyes, inhalation, ingestion), ensuring prompt and appropriate medical treatment. **Section 5: Fire-Fighting Measures** offers guidance on extinguishing media, special fire-fighting procedures, and protective equipment needed for firefighters. This section is crucial for preventing fires and mitigating their impact. **Section 6: Accidental Release Measures** outlines procedures for spills, leaks, or releases, including containment and cleanup methods to minimize environmental and health impacts. **Section 7: Handling and Storage** advises on safe handling practices and storage conditions to prevent accidents. This includes recommendations for ventilation, incompatible materials, and specific storage requirements. **Section 8: Exposure Controls/Personal Protection** specifies exposure limits, personal protective equipment (PPE), and engineering controls necessary to protect workers from hazardous substances. **Section 9: Physical and Chemical Properties** lists physical and chemical properties such as appearance, odor, pH, melting point, boiling point, and solubility. These properties are essential for understanding how the substance behaves under different conditions. **Section 10: Stability and Reactivity** discusses the stability of the substance and potential reactivity with other materials or under specific conditions. **Section 11: Toxicological Information** provides data on the toxicological effects of the substance, including acute and chronic health effects. This section is critical for understanding potential health risks associated with exposure. **Section 12: Ecological Information** addresses the environmental impact of the substance, including its persistence, bioaccumulation potential, mobility in soil, and effects on aquatic and terrestrial organisms. **Section 13: Disposal Considerations** offers guidelines on safe disposal practices to prevent environmental contamination. This includes recommendations for waste treatment methods and disposal facilities. **Section 14: Transport Information** provides details necessary for safe transportation of hazardous materials, including UN numbers, proper shipping names, and transport categories. **Section 15: Regulatory Information** summarizes relevant national and international regulations that apply to the substance. This ensures compliance with legal requirements across different jurisdictions. Finally, **Section 16: Other Information** includes any additional information that might be relevant but does not fit into the other sections. In summary, each section of an SDS is carefully crafted to provide a comprehensive understanding of a hazardous substance's properties, risks, and safe handling practices. By adhering to the information provided in these sections, workers can minimize risks and ensure a safer working environment. The detailed structure of SDSs underscores their importance as a critical component of WHMIS, enabling informed decision-making and effective risk management in workplaces where hazardous materials are present.
2.3 Importance of SDS in Workplace Safety
The importance of Safety Data Sheets (SDS) in workplace safety cannot be overstated. As a critical component of the Workplace Hazardous Materials Information System (WHMIS), SDSs serve as comprehensive guides that provide essential information about the safe handling, use, storage, and disposal of hazardous materials. These documents are pivotal in ensuring that workers are adequately informed and equipped to manage potential risks associated with chemical substances. An SDS typically includes detailed sections on the identification of the substance, its composition, first aid measures, fire-fighting measures, accidental release measures, handling and storage, exposure controls/personal protection, physical and chemical properties, stability and reactivity, toxicological information, ecological information, disposal considerations, transport information, regulatory information, and other relevant data. This structured format ensures that all necessary information is readily available and easily accessible to workers. One of the primary benefits of SDSs is their role in preventing accidents and injuries. By providing clear instructions on how to handle hazardous materials safely, SDSs help workers avoid exposure to harmful substances. For instance, if a chemical spill occurs, the SDS will outline the appropriate procedures for containment and cleanup, reducing the risk of further harm. Additionally, SDSs highlight potential health hazards associated with each substance, enabling workers to take preventive measures such as wearing personal protective equipment (PPE) or following specific ventilation guidelines. SDSs also play a crucial role in emergency preparedness. In the event of an accident or spill, having immediate access to an SDS can be lifesaving. Emergency responders rely on this information to make informed decisions about how to respond safely and effectively. Furthermore, SDSs are often required by regulatory bodies and are a key component of compliance with workplace safety standards. From a training perspective, SDSs are invaluable tools for educating workers about workplace hazards. They provide a standardized format for communicating critical safety information, which helps ensure consistency in training programs across different departments or locations within an organization. This consistency is particularly important in industries where workers may be exposed to multiple hazardous substances on a daily basis. In summary, the importance of SDSs in workplace safety is multifaceted. They provide essential information for safe handling practices, prevent accidents through clear guidelines, support emergency preparedness efforts, and serve as a cornerstone for comprehensive training programs. By ensuring that SDSs are readily available and understood by all workers who handle hazardous materials, organizations can significantly enhance their overall safety culture and reduce the risk of workplace injuries and illnesses. This underscores why SDSs remain a fundamental component of WHMIS and a critical element in maintaining a safe and healthy work environment.
Component 3: Labels and Pictograms
When it comes to ensuring safety and compliance in various industries, the use of labels and pictograms is paramount. Component 3 of safety regulations delves into the critical aspects of labeling, which are essential for clear communication and hazard identification. This component is divided into three key areas: Standard Label Elements, GHS Pictograms and Their Meanings, and Labeling Requirements for Different Products. Understanding these elements is crucial for manufacturers, distributors, and users alike. Standard Label Elements provide a framework for consistency in labeling, ensuring that all necessary information is clearly and uniformly presented. GHS Pictograms and Their Meanings offer a visual language that transcends linguistic barriers, immediately conveying potential hazards. Lastly, Labeling Requirements for Different Products address the specific needs of various product categories, ensuring that each type of product is labeled appropriately to mitigate risks. By exploring these aspects, we can ensure that labels are not only informative but also effective in preventing accidents and ensuring compliance with international standards. Let's begin by examining the foundational aspect of this component: Standard Label Elements.
3.1 Standard Label Elements
### 3.1 Standard Label Elements In the context of the Workplace Hazardous Materials Information System (WHMIS), standard label elements are crucial for ensuring that workers can quickly and accurately identify the hazards associated with a chemical product. These elements are designed to be consistent and easy to understand, making them an essential component of workplace safety. A standard WHMIS label typically includes several key pieces of information. First, there is the **Supplier Identifier**, which provides contact information for the supplier or manufacturer of the product. This is vital in case workers need to obtain additional safety information or report any issues related to the product. Next, there is the **Product Identifier**, which clearly states the name or identifier of the hazardous product. This ensures that workers can easily identify the substance they are handling. Another critical element is the **Hazard Classification**, which categorizes the product based on its physical, health, and environmental hazards. This classification is often represented through pictograms—visual symbols that convey specific types of hazards such as flammability, toxicity, or reactivity. For instance, a flame pictogram indicates a flammable substance, while a skull and crossbones pictogram signifies a toxic substance. **Hazard Statements** provide brief descriptions of the nature of the hazard(s) associated with the product. These statements are standardized and help workers understand what specific risks they might face when handling the substance. For example, "Flammable liquid and vapor" or "Toxic if inhaled." **Precautionary Statements** offer advice on how to minimize or prevent adverse effects resulting from exposure to or improper handling of the hazardous product. These statements might include instructions such as "Keep away from heat/sparks/open flames/hot surfaces," "Use explosion-proof electrical/ventilating/lighting equipment," or "Wear protective gloves/protective clothing/eye protection/face protection." Finally, **Pictograms** serve as visual alerts that quickly convey hazard information without needing to read text. These pictograms are standardized under the Globally Harmonized System of Classification and Labelling of Chemicals (GHS) and include symbols for various types of hazards such as explosive, corrosive, toxic, and more. The inclusion of these standard label elements ensures that workers have immediate access to critical safety information at all times when handling hazardous materials. This not only enhances workplace safety but also complies with regulatory requirements aimed at protecting workers' health and well-being. By understanding these elements, workers can take necessary precautions to mitigate risks and ensure a safer working environment.
3.2 GHS Pictograms and Their Meanings
In the context of the Workplace Hazardous Materials Information System (WHMIS), Component 3: Labels and Pictograms plays a crucial role in ensuring the safe handling and use of hazardous materials. A key element within this component is the use of 3.2 GHS Pictograms, which are standardized symbols designed to convey specific hazard information quickly and universally. These pictograms are part of the Globally Harmonized System of Classification and Labelling of Chemicals (GHS), adopted by WHMIS to enhance clarity and consistency in hazard communication. There are nine GHS pictograms, each representing a distinct category of hazards. The **Explosive** pictogram, depicted by an exploding bomb, indicates substances that may explode or be highly reactive. The **Flammable** pictogram, showing a flame, warns of substances that can catch fire easily. The **Oxidizing** pictogram, represented by a flame over a circle, signifies substances that can cause or intensify fires. The **Corrosive** pictogram, featuring a hand and surface being corroded, alerts users to substances that can cause severe skin burns or eye damage. The **Toxic** and **Toxic (Acute)** pictograms, both showing a skull and crossbones, indicate substances that are highly toxic and can cause death or serious health effects upon short-term exposure. The **Harmful/Irritant** pictogram, depicted by an exclamation mark, signals substances that are less severe but still pose health risks such as skin or eye irritation. The **Health Hazard** pictogram, showing a silhouette of a person with a red circle around it, warns of substances that can cause long-term health effects like cancer or reproductive issues. The **Environmental Hazard** pictogram, represented by a dead fish and tree, indicates substances that are hazardous to aquatic life or the environment. Finally, the **Gas Under Pressure** pictogram, showing a gas cylinder, alerts users to substances that are gases under pressure. These pictograms are essential because they provide immediate visual cues about the hazards associated with a chemical, allowing workers to take necessary precautions without needing to read detailed text. This visual communication is particularly important in workplaces where multiple languages are spoken or where time is critical in responding to emergencies. By understanding these pictograms, workers can better protect themselves and their environment from potential dangers, making the workplace safer and more compliant with regulatory standards. Overall, the integration of GHS pictograms into WHMIS labels ensures a consistent and effective method for communicating critical hazard information, enhancing workplace safety and reducing the risk of accidents involving hazardous materials.
3.3 Labeling Requirements for Different Products
When it comes to the Workplace Hazardous Materials Information System (WHMIS), labeling requirements are a critical component for ensuring the safe handling and use of hazardous products. Under Component 3: Labels and Pictograms, specific guidelines are outlined to ensure that different types of products are labeled accurately and consistently. For instance, **Supplier Labels** are mandatory for all hazardous products sold or imported into Canada. These labels must include essential information such as the product identifier, hazard statements, precautionary statements, and pictograms that visually represent the hazards associated with the product. The pictograms are standardized symbols that quickly convey the nature of the hazard, making it easier for workers to understand potential risks at a glance. **Workplace Labels**, on the other hand, are used when hazardous products are decanted or transferred into different containers within the workplace. These labels must also include the product identifier and at least one hazard statement or pictogram that reflects the primary hazard of the product. This ensures that workers are aware of the hazards even when products are not in their original packaging. Additionally, **Imported Products** must comply with WHMIS labeling requirements before they can be sold or used in Canada. This involves ensuring that all necessary information is translated into English and French and that the labels meet Canadian standards. For **Consumer Products**, which are typically sold through retail channels, labeling requirements may differ slightly but still adhere to WHMIS standards. These products often have more detailed instructions for safe use and may include additional information such as first aid measures and disposal instructions. However, they must still display the required pictograms and hazard statements to alert consumers to potential dangers. In summary, the labeling requirements under WHMIS are designed to provide clear and consistent information about hazardous products across different contexts—whether they are supplier labels, workplace labels, imported products, or consumer products. By adhering to these guidelines, employers and suppliers can help ensure a safer work environment and protect workers from potential hazards associated with the handling and use of hazardous materials. This comprehensive approach to labeling is a cornerstone of WHMIS, enabling effective communication of critical safety information and contributing significantly to workplace safety and compliance.