A Very Toxic Chemical Is Being Used In Your Work What Is The Best Way To Control The Hazard

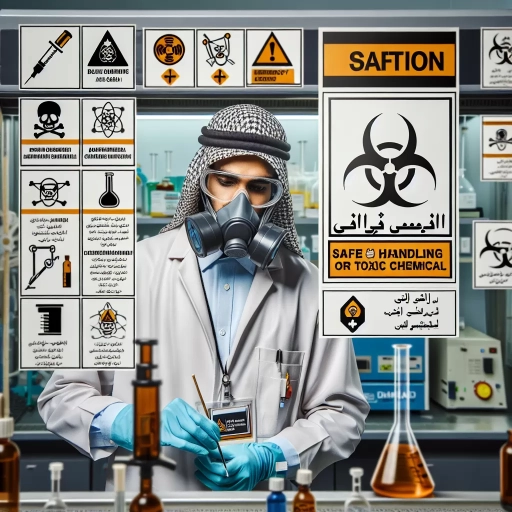
In many industrial settings, workers are exposed to highly toxic chemicals that pose significant health risks. One such chemical, known for its severe health implications, is frequently used in various industries. To mitigate the hazards associated with this chemical, it is crucial to adopt a multi-faceted approach. This involves understanding the chemical hazard in detail, implementing engineering controls to reduce exposure, and adopting personal protective equipment (PPE) along with administrative measures to ensure safety protocols are followed. By comprehensively addressing these aspects, workplaces can significantly reduce the risks associated with handling toxic chemicals. In this article, we will delve into each of these strategies, starting with a thorough understanding of the chemical hazard itself. Understanding the Chemical Hazard is the first step in developing effective safety measures and will be explored in the next section.
Understanding the Chemical Hazard
Understanding the chemical hazards associated with various substances is crucial for ensuring safety in both industrial and everyday environments. To effectively manage these risks, it is essential to follow a structured approach that encompasses several key steps. First, one must identify the chemical's properties and risks, which involves understanding its physical and chemical characteristics as well as its potential to cause harm. This foundational knowledge sets the stage for recognizing exposure routes and symptoms, allowing individuals to anticipate and mitigate potential health impacts. Additionally, reviewing Safety Data Sheets (SDS) provides critical information on handling, storage, and emergency procedures. By integrating these elements, individuals can develop a comprehensive understanding of chemical hazards. Let's begin by delving into the first critical step: identifying the chemical's properties and risks.
Identifying the Chemical's Properties and Risks
To effectively control the hazard posed by a very toxic chemical in your workplace, it is crucial to start by identifying its properties and risks. This involves a thorough understanding of the chemical's physical and chemical characteristics, such as its boiling point, vapor pressure, solubility, and reactivity. Knowing these properties helps in predicting how the chemical will behave under different conditions and what safety measures are necessary. For instance, if the chemical is highly volatile or reactive, special storage and handling procedures must be implemented to prevent accidents. Next, you need to assess the health and environmental risks associated with the chemical. This includes reviewing Material Safety Data Sheets (MSDS) or Safety Data Sheets (SDS), which provide detailed information on the chemical's toxicity, potential health effects, and recommended safety precautions. Understanding whether the chemical is carcinogenic, neurotoxic, or can cause other adverse health effects is essential for developing appropriate protective measures. Identifying exposure routes is also critical. Determine if the chemical can be absorbed through the skin, inhaled as a gas or vapor, or ingested accidentally. This knowledge will guide the selection of personal protective equipment (PPE) such as gloves, respirators, and eye protection. Additionally, understanding the chemical's environmental impact helps in preventing spills and ensuring proper disposal methods are in place. Implementing engineering controls is another key step. This may include using fume hoods, ventilation systems, or enclosed processes to minimize exposure. Administrative controls such as training programs for employees, strict adherence to safety protocols, and regular monitoring of chemical levels in the workplace are also vital. Finally, having emergency response plans in place is essential. This includes knowing how to handle spills, having first aid kits available, and ensuring that all employees are trained in emergency procedures. Regular audits and inspections should be conducted to ensure compliance with safety regulations and to identify any gaps in the hazard control measures. By meticulously identifying the properties and risks of a toxic chemical and implementing comprehensive control measures, you can significantly reduce the hazards associated with its use in your workplace. This proactive approach not only protects employees but also ensures compliance with regulatory standards and maintains a safe working environment.
Recognizing Exposure Routes and Symptoms
Recognizing exposure routes and symptoms is crucial when dealing with highly toxic chemicals in the workplace. The primary exposure routes include inhalation, skin contact, and ingestion. Inhalation occurs when toxic vapors or particles are breathed in, often through inadequate ventilation or improper use of personal protective equipment (PPE). Skin contact can happen through direct exposure to the chemical, which can lead to absorption through the skin or cause severe burns. Ingestion, though less common, can occur if the chemical is ingested accidentally, such as through contaminated food or water. Symptoms of exposure can vary widely depending on the specific chemical and the route of exposure. For inhalation, common symptoms include respiratory distress, coughing, wheezing, and shortness of breath. Skin exposure may result in redness, irritation, blistering, or burns. Ingestion can lead to nausea, vomiting, abdominal pain, and in severe cases, organ damage. To control these hazards effectively, it is essential to implement robust safety measures. First, ensure proper ventilation in the work area to prevent the accumulation of toxic vapors. Use of PPE such as respirators, gloves, and protective clothing is mandatory when handling toxic chemicals. Regular training on safe handling practices and emergency procedures should be provided to all employees. Labeling and signage must clearly indicate areas where hazardous chemicals are used or stored. Additionally, conducting regular health monitoring and medical surveillance can help identify early signs of exposure. This includes pre-employment screenings, periodic health checks, and immediate medical evaluation if symptoms arise. Implementing a spill response plan and having emergency showers and eyewash stations readily available are also critical for prompt action in case of accidents. Finally, adherence to strict protocols for handling, storing, and disposing of hazardous chemicals is paramount. This includes following Material Safety Data Sheets (MSDS) guidelines and ensuring that all containers are properly sealed and labeled. By recognizing potential exposure routes and symptoms, and by implementing these control measures, workplaces can significantly reduce the risks associated with highly toxic chemicals.
Reviewing Safety Data Sheets (SDS)
When dealing with highly toxic chemicals in the workplace, reviewing Safety Data Sheets (SDS) is a crucial step in understanding and controlling the associated hazards. An SDS provides comprehensive information about the chemical's properties, hazards, safe handling practices, and emergency procedures. Here’s how to effectively review an SDS to ensure safety: 1. **Identify the Chemical**: Start by verifying the chemical name and its synonyms to ensure you are reviewing the correct SDS. 2. **Hazard Identification**: Section 2 of the SDS details the chemical's hazards, including its classification, label elements, and any pictograms. This section helps you understand the potential risks such as toxicity, flammability, and reactivity. 3. **Composition/Information on Ingredients**: Section 3 lists the chemical composition and concentration of ingredients. This information is vital for understanding potential interactions and synergistic effects. 4. **First Aid Measures**: Section 4 outlines first aid procedures in case of exposure. Knowing these measures can help in responding quickly and effectively during emergencies. 5. **Fire-Fighting Measures**: Section 5 provides guidance on how to extinguish fires involving the chemical, including suitable extinguishing agents and those that should not be used. 6. **Accidental Release Measures**: Section 6 describes how to handle spills or leaks, including containment and cleanup procedures. 7. **Handling and Storage**: Section 7 offers advice on safe handling practices and storage conditions to minimize risks. 8. **Exposure Controls/Personal Protection**: Section 8 specifies exposure limits, personal protective equipment (PPE), and engineering controls necessary to prevent exposure. 9. **Physical and Chemical Properties**: Section 9 details physical and chemical properties such as melting point, boiling point, and solubility which can affect handling and storage. 10. **Stability and Reactivity**: Section 10 discusses the chemical's stability and potential reactivity with other substances or under different conditions. 11. **Toxicological Information**: Section 11 provides toxicological data including LD50 values (lethal dose for 50% of test subjects), which helps in assessing the severity of potential exposure. 12. **Ecological Information**: Section 12 covers ecological data such as environmental fate and toxicity to aquatic organisms. 13. **Disposal Considerations**: Section 13 outlines proper disposal methods to prevent environmental contamination. 14. **Transport Information**: Section 14 provides transportation classifications and regulations for safe transport of the chemical. 15. **Regulatory Information**: Section 15 lists relevant regulatory information including laws and standards that apply to the chemical. By meticulously reviewing these sections of an SDS, you can gain a thorough understanding of the hazards associated with a toxic chemical and implement appropriate control measures such as using PPE, following safe handling practices, and having emergency response plans in place. This proactive approach ensures a safer working environment for everyone involved in handling these chemicals. In summary, reviewing an SDS is not just a compliance requirement but a critical tool for understanding chemical hazards and implementing effective control measures to mitigate risks in the workplace.
Implementing Engineering Controls
Implementing engineering controls is a crucial step in ensuring a safe and efficient work environment, particularly in industries where hazardous materials are involved. These controls not only protect workers from potential health risks but also enhance productivity and compliance with regulatory standards. There are several key strategies that can be employed to achieve these goals. Firstly, **Using Ventilation Systems and Fume Hoods** helps to remove airborne contaminants, providing a cleaner air environment for workers. Secondly, **Installing Containment Barriers and Enclosures** prevents the spread of hazardous substances, isolating them from the general workspace. Lastly, **Utilizing Automated Handling Systems** reduces manual exposure to dangerous materials by automating tasks that would otherwise be performed by humans. By integrating these engineering controls, workplaces can significantly mitigate risks and improve overall safety. Let's delve into the specifics of how **Using Ventilation Systems and Fume Hoods** can be an effective first line of defense against airborne hazards.
Using Ventilation Systems and Fume Hoods
When dealing with highly toxic chemicals in the workplace, implementing effective engineering controls is crucial for ensuring the safety and health of employees. Among these controls, ventilation systems and fume hoods play a pivotal role in mitigating hazards. Ventilation systems are designed to remove airborne contaminants from the work environment, thereby reducing exposure to harmful substances. These systems can be categorized into two main types: general ventilation and local exhaust ventilation. General ventilation involves circulating and exchanging air throughout the entire workspace to maintain a safe atmosphere, while local exhaust ventilation targets specific areas where hazardous substances are released, capturing and removing them at the source. Fume hoods, a type of local exhaust ventilation, are particularly effective in laboratories and industrial settings where chemicals are frequently used. These hoods create a negative pressure environment that draws fumes and particles away from the worker's breathing zone, directing them into a duct system for safe disposal. Properly installed and maintained fume hoods can significantly reduce the risk of inhalation exposure to toxic chemicals. It is essential to ensure that fume hoods are used correctly; this includes keeping the sash at the recommended height, avoiding overcrowding the hood with equipment, and regularly inspecting the system for any malfunctions. Additionally, regular maintenance of both ventilation systems and fume hoods is critical. This includes checking airflow rates, inspecting ducts for blockages or damage, and ensuring that filters are clean and functioning properly. Training employees on the correct use and maintenance of these systems is also vital to maximize their effectiveness. By combining these measures—proper installation, regular maintenance, and employee training—ventilation systems and fume hoods can significantly minimize the risks associated with working with toxic chemicals, creating a safer and healthier work environment. This proactive approach not only protects workers but also enhances overall operational efficiency and compliance with safety regulations.
Installing Containment Barriers and Enclosures
When dealing with highly toxic chemicals in the workplace, one of the most effective ways to control the hazard is by implementing engineering controls, specifically through the installation of containment barriers and enclosures. These physical barriers are designed to isolate the hazardous substance from the work environment, significantly reducing exposure risks for employees. Here’s how they can be effectively installed: 1. **Assessment and Planning**: Begin by conducting a thorough risk assessment to identify areas where toxic chemicals are used and potential pathways for exposure. This involves mapping out workflows, identifying potential leak points, and determining the most effective placement for barriers. 2. **Material Selection**: Choose materials that are compatible with the chemical being used. For example, if the chemical is corrosive or reactive, select materials that are resistant to these properties. Common materials include stainless steel, PVC, or specialized polymers. 3. **Design Considerations**: The design of containment barriers should ensure complete isolation of the hazardous area. This may involve creating sealed enclosures around equipment or processes that involve toxic chemicals. Ensure that all connections and joints are leak-proof and that there are no gaps or openings that could allow the chemical to escape. 4. **Installation**: Install barriers in a way that minimizes disruption to workflow while maximizing safety. This might involve installing permanent structures like walls or partitions, or using more flexible solutions such as curtains or screens made from appropriate materials. 5. **Ventilation Systems**: Integrate ventilation systems within these enclosures to remove any airborne contaminants. This could include local exhaust ventilation (LEV) systems or fume hoods that capture and filter out hazardous vapors before they can spread to other areas. 6. **Maintenance and Inspection**: Regularly inspect and maintain containment barriers to ensure they remain effective. This includes checking for any signs of wear, damage, or degradation that could compromise their integrity. 7. **Training and Compliance**: Ensure all employees are trained on the proper use and maintenance of these barriers. Adhere strictly to relevant safety standards and regulations to guarantee compliance and optimal safety performance. By meticulously installing containment barriers and enclosures, you can significantly reduce the risk of exposure to toxic chemicals in the workplace, creating a safer environment for all employees involved in handling these substances. This proactive approach not only protects health but also enhances operational efficiency by minimizing downtime due to accidents or health issues related to chemical exposure.
Utilizing Automated Handling Systems
When dealing with highly toxic chemicals in the workplace, one of the most effective strategies for controlling hazards is implementing engineering controls. Among these, utilizing automated handling systems stands out as a crucial measure to minimize exposure and enhance safety. Automated handling systems involve the use of machinery and technology to manage, transport, and process hazardous materials without direct human intervention. This approach significantly reduces the risk of accidental spills, leaks, and inhalation of toxic substances. By automating tasks such as material transfer, mixing, and packaging, these systems ensure that workers are not exposed to dangerous chemicals during routine operations. For instance, robotic arms can be programmed to handle containers of toxic substances with precision, eliminating the need for manual handling which often leads to accidents. Additionally, automated systems can be equipped with sensors and alarms that detect any anomalies or potential leaks, allowing for immediate intervention before a hazardous situation develops. Moreover, automated handling systems can be integrated with other safety measures such as ventilation systems and containment enclosures to further mitigate risks. These enclosures can capture any emissions or spills, preventing them from spreading into the work environment. The integration of these technologies ensures a comprehensive safety net that protects workers from multiple angles. Another significant benefit of automated handling systems is their ability to maintain consistency and precision in handling hazardous materials. Unlike human operators who may vary in their techniques and attention levels, automated systems perform tasks uniformly and reliably. This consistency is particularly important when dealing with highly toxic chemicals where even minor deviations can have severe consequences. Implementing automated handling systems also contributes to a more efficient and productive work environment. By automating repetitive and dangerous tasks, workers can focus on higher-value activities that require human expertise and judgment. This not only enhances overall productivity but also improves job satisfaction as workers are relieved from hazardous duties. In conclusion, utilizing automated handling systems is a best practice for controlling hazards associated with highly toxic chemicals in the workplace. These systems offer a robust solution by reducing direct exposure, enhancing precision and consistency, and integrating seamlessly with other safety measures. By leveraging technology to manage hazardous materials, organizations can create a safer and more efficient work environment that protects both their employees and their operations.
Adopting Personal Protective Equipment and Administrative Measures
Adopting personal protective equipment (PPE) and administrative measures is crucial for ensuring workplace safety and preventing injuries. This comprehensive approach involves several key components that work together to create a safe and healthy environment. First, **selecting and using appropriate PPE** is essential to protect workers from specific hazards. This includes choosing the right type of equipment based on the nature of the job and ensuring it is used correctly. Second, **developing and enforcing safety protocols** helps in establishing clear guidelines and procedures that everyone must follow, thereby reducing the risk of accidents. Lastly, **conducting regular training and monitoring** ensures that employees are well-informed about safety practices and that compliance is consistently maintained. By focusing on these three areas, organizations can significantly enhance their safety standards. To begin with, the importance of selecting and using appropriate PPE cannot be overstated, as it forms the first line of defense against workplace hazards.
Selecting and Using Appropriate PPE
When dealing with highly toxic chemicals in the workplace, selecting and using appropriate Personal Protective Equipment (PPE) is crucial for ensuring the safety and health of workers. The best way to control the hazard involves a systematic approach to PPE selection and use. First, conduct a thorough risk assessment to identify potential exposure routes such as inhalation, skin contact, or eye exposure. Based on this assessment, choose PPE that aligns with the specific hazards present. For example, if the chemical is highly volatile, respirators with organic vapor cartridges or supplied air systems may be necessary. If skin contact is a risk, impermeable gloves and protective clothing like coveralls or lab coats should be worn. Eye protection is also vital; goggles or face shields can prevent chemical splashes from reaching the eyes. Ensure that all PPE meets relevant standards and regulations, such as those set by OSHA or EN standards in Europe. Proper fitting of PPE is essential; ill-fitting equipment can compromise its effectiveness. Regular maintenance and inspection of PPE are critical to ensure it remains in good condition. Training employees on how to correctly don, doff, and maintain their PPE is equally important to prevent contamination and exposure during these processes. Administrative measures complement PPE by reducing the need for it through engineering controls and safe work practices. Implementing engineering controls like fume hoods or ventilation systems can significantly reduce airborne concentrations of toxic chemicals. Safe work practices include following established protocols for handling chemicals, minimizing the amount of chemical used, and ensuring adequate ventilation in work areas. Additionally, enforcing strict hygiene practices such as washing hands thoroughly after handling chemicals and before eating or smoking can further mitigate risks. Regular monitoring of chemical levels in the workplace helps in adjusting PPE and administrative measures accordingly. This may involve air sampling to determine if respirators are needed or if current ventilation systems are adequate. Finally, having an emergency response plan in place that includes procedures for spills, leaks, or other accidents ensures prompt action can be taken to minimize exposure and mitigate harm. By combining robust PPE selection with effective administrative measures and safe work practices, workplaces can significantly reduce the risks associated with handling highly toxic chemicals.
Developing and Enforcing Safety Protocols
Developing and enforcing safety protocols is crucial when working with highly toxic chemicals. The best way to control the hazard involves a multi-faceted approach that integrates both personal protective equipment (PPE) and administrative measures. First, conduct a thorough risk assessment to identify potential exposure points and the severity of the hazard. Based on this assessment, develop comprehensive safety protocols that outline specific procedures for handling, storing, and disposing of the chemical. Ensure all employees are trained on these protocols and understand the importance of adhering to them. Implementing administrative measures such as limiting access to areas where the chemical is used, enforcing strict hygiene practices, and scheduling regular breaks to minimize prolonged exposure are essential. Establish clear communication channels so that any incidents or near-misses are reported immediately and investigated thoroughly to prevent future occurrences. Personal Protective Equipment (PPE) must be selected based on the specific hazards identified during the risk assessment. This may include respirators, gloves, goggles, and protective clothing that are designed to prevent skin contact and inhalation of the chemical. Regular inspections of PPE should be conducted to ensure it remains in good condition and is properly maintained. Additionally, enforce strict adherence to PPE use through regular monitoring and disciplinary actions for non-compliance. Administrative controls like job rotation, engineering controls such as ventilation systems, and emergency response plans should also be part of the overall safety strategy. Regular audits and reviews of safety protocols will help in identifying gaps and areas for improvement, ensuring that the workplace remains safe and compliant with regulatory standards. By combining these measures—thorough risk assessment, comprehensive training, strict administrative controls, and proper use of PPE—you can significantly reduce the risks associated with working with highly toxic chemicals. This integrated approach not only protects employees but also ensures compliance with legal requirements and maintains a safe working environment.
Conducting Regular Training and Monitoring
Conducting regular training and monitoring is a crucial component of effectively controlling hazards associated with the use of very toxic chemicals in the workplace. This approach ensures that all employees are well-equipped with the knowledge and skills necessary to handle these substances safely. Training programs should be comprehensive, covering topics such as the proper use of personal protective equipment (PPE), safe handling procedures, emergency response protocols, and the importance of adhering to administrative measures. These sessions should be conducted by qualified trainers who can provide hands-on demonstrations and address any questions or concerns raised by employees. Regular refresher courses are also essential to reinforce previously learned information and update employees on any new procedures or regulations. Monitoring involves continuous observation and evaluation of workplace practices to ensure compliance with safety standards. Supervisors and safety officers should regularly inspect work areas to identify potential hazards and enforce the use of PPE and adherence to administrative controls. This includes checking for proper ventilation, ensuring that chemical storage areas are secure, and verifying that employees are following established safety protocols. Additionally, monitoring should involve reviewing incident reports and near-miss incidents to identify patterns or areas for improvement. Feedback from employees is also valuable; it can highlight gaps in training or areas where additional support is needed. Technology can also play a significant role in monitoring. Advanced safety management software can track training completion rates, monitor compliance with safety protocols, and provide real-time alerts for potential hazards. Wearable devices can monitor exposure levels to toxic chemicals, providing immediate alerts if safe limits are exceeded. By integrating these tools into the monitoring process, organizations can enhance their ability to protect employees from chemical hazards. Moreover, regular audits and inspections by external agencies or internal teams can provide an objective assessment of the effectiveness of training and monitoring programs. These audits help in identifying any lapses in compliance and provide recommendations for improvement. They also serve as a mechanism to ensure that the organization is adhering to regulatory requirements and industry standards. In summary, conducting regular training and monitoring is pivotal in controlling the hazards associated with very toxic chemicals. It ensures that employees are knowledgeable about safety procedures, that workplace practices are compliant with safety standards, and that any potential risks are promptly identified and mitigated. By combining robust training programs with rigorous monitoring practices, organizations can significantly reduce the risk of chemical exposure and create a safer working environment for all employees.