What Is A Pump Cover

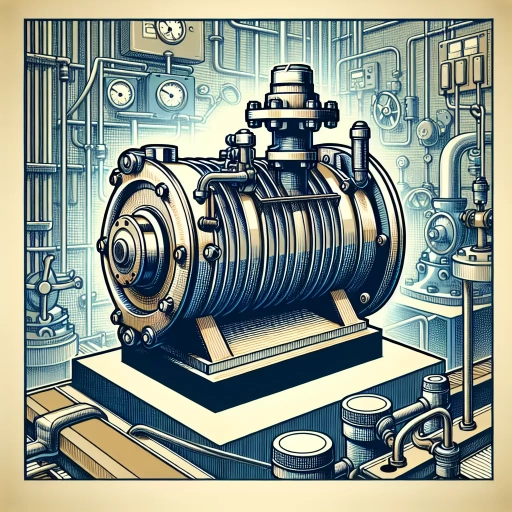
In the realm of industrial and mechanical engineering, pump covers play a crucial role in ensuring the efficient and safe operation of pumps. These protective enclosures are designed to shield pumps from environmental elements, reduce noise pollution, and enhance overall system performance. Understanding what a pump cover is and its significance involves delving into several key aspects. First, it is essential to introduce the concept of pump covers, exploring their purpose and how they integrate into various systems. This introduction sets the stage for a deeper examination of their design and construction, which highlights the materials, engineering principles, and manufacturing processes involved. Additionally, the applications and benefits of pump covers will be discussed, revealing how these components contribute to improved durability, reduced maintenance needs, and enhanced operational efficiency across diverse industries. By grasping these fundamental elements, readers can appreciate the multifaceted importance of pump covers. Let us begin by introducing the basics of pump covers and understanding their foundational role in modern engineering.
Introduction to Pump Covers
In the realm of industrial machinery, pump covers play a crucial role in ensuring the efficiency, safety, and longevity of pumps. These protective enclosures are more than just a peripheral component; they are essential for maintaining optimal performance and preventing potential hazards. This article delves into the world of pump covers, providing a comprehensive overview that includes their definition and purpose, the various types available, and their importance in industrial settings. Understanding the definition and purpose of pump covers is fundamental to appreciating their significance. These covers are designed to shield pumps from environmental factors such as dust, moisture, and extreme temperatures, thereby extending their lifespan. Additionally, they help in noise reduction and provide a layer of protection against physical damage. The diversity in types of pump covers caters to different industrial needs. From simple protective covers to more complex designs that incorporate cooling systems or monitoring devices, each type is tailored to meet specific requirements. This variety ensures that industries can select the most appropriate cover to enhance their pump operations. In industrial settings, the importance of pump covers cannot be overstated. They contribute to maintaining a safe working environment by preventing accidents and ensuring that pumps operate within optimal parameters. This not only enhances productivity but also reduces maintenance costs in the long run. To begin our exploration, let's first define what pump covers are and why they are indispensable in modern industrial practices. **Definition and Purpose** of pump covers set the stage for understanding their broader impact and applications.
Definition and Purpose
In the realm of industrial and mechanical engineering, the term "pump cover" refers to a critical component designed to protect and enhance the functionality of pumps. A pump cover, often made from durable materials such as stainless steel, cast iron, or advanced polymers, serves as an outer casing that encloses the pump's internal mechanisms. The primary purpose of a pump cover is multifaceted: it provides structural integrity by supporting the pump's moving parts and ensuring proper alignment, thereby maintaining optimal performance and efficiency. Moreover, the pump cover acts as a protective barrier against environmental factors such as dust, moisture, and extreme temperatures, which could otherwise compromise the pump's operation. This shielding is particularly crucial in harsh industrial settings where pumps are exposed to corrosive substances or high-pressure conditions. By safeguarding the internal components from these external threats, the pump cover significantly extends the lifespan of the pump and reduces maintenance costs. Additionally, pump covers often feature design elements that facilitate ease of use and maintenance. For instance, they may include access panels or removable sections that allow technicians to inspect and service the pump without having to disassemble the entire unit. This accessibility not only speeds up routine maintenance but also enables quicker diagnosis and repair of any issues that may arise, minimizing downtime and ensuring continuous operation. From a safety perspective, pump covers play a vital role in preventing accidents. By encasing moving parts and electrical components, they protect operators from potential hazards such as entanglement or electrical shock. This safety aspect is particularly important in industries where human safety is paramount, such as in chemical processing plants or water treatment facilities. In summary, the definition and purpose of a pump cover are deeply intertwined with the overall performance, longevity, and safety of the pump. By providing structural support, environmental protection, ease of maintenance, and enhanced safety features, pump covers are indispensable components in various industrial applications. Understanding the significance of pump covers is essential for anyone involved in the selection, installation, and operation of pumps, as it directly impacts the efficiency and reliability of these critical machines.
Types of Pump Covers
Pump covers are essential components in various industrial and residential applications, serving to protect pumps from environmental factors, enhance safety, and improve operational efficiency. There are several types of pump covers, each designed to meet specific needs and conditions. 1. **Weatherproof Pump Covers**: These covers are designed to shield pumps from harsh weather conditions such as rain, snow, and extreme temperatures. Made from durable materials like stainless steel or heavy-duty plastics, they ensure the pump remains dry and functional even in outdoor settings. 2. **Sound-Reducing Pump Covers**: For applications where noise reduction is crucial, sound-reducing pump covers are ideal. These covers are typically made from sound-absorbing materials and are often used in residential areas or noise-sensitive environments to minimize the operational noise of the pump. 3. **Explosion-Proof Pump Covers**: In hazardous environments where flammable gases or vapors are present, explosion-proof pump covers are necessary. These covers are engineered to prevent sparks or electrical discharges that could ignite explosive atmospheres, ensuring safety in high-risk settings. 4. **Insulated Pump Covers**: Insulated pump covers are used to maintain optimal operating temperatures for the pump. They are particularly useful in cold climates where freezing temperatures could damage the pump or in hot environments where overheating might occur. These covers help in conserving energy by reducing heat loss or gain. 5. **Security Pump Covers**: Designed with security in mind, these covers protect pumps from unauthorized access and tampering. Often used in public spaces or sensitive installations, they feature locking mechanisms and robust construction to deter vandalism and theft. 6. **Custom Pump Covers**: For unique or specialized applications, custom pump covers can be tailored to fit specific requirements. These covers can be made from a variety of materials and can include additional features such as ventilation systems, monitoring ports, or specialized coatings for corrosive environments. 7. **Aesthetic Pump Covers**: In scenarios where the pump's appearance is a concern, aesthetic pump covers offer a solution. These covers come in various designs and colors to blend with the surrounding architecture, making them suitable for installations in visible areas such as commercial buildings or residential landscapes. Each type of pump cover addresses different challenges and needs, ensuring that the pump operates efficiently and safely under various conditions. By selecting the appropriate cover, users can extend the lifespan of their pumps, reduce maintenance costs, and enhance overall system performance. Understanding the different types of pump covers is essential for making informed decisions about which cover best suits a particular application.
Importance in Industrial Settings
In industrial settings, the importance of pump covers cannot be overstated. These protective enclosures play a crucial role in ensuring the optimal performance, longevity, and safety of pumps, which are often the heart of various industrial processes. Firstly, pump covers shield the pump from environmental elements such as dust, moisture, and extreme temperatures, thereby reducing the risk of corrosion and mechanical failure. This protection is particularly vital in harsh industrial environments where exposure to these elements can significantly shorten the lifespan of equipment. Moreover, pump covers enhance operational efficiency by maintaining a consistent operating environment. By insulating the pump, these covers help regulate temperature fluctuations, which can affect the viscosity of fluids being pumped and the overall efficiency of the system. This consistency is essential for maintaining precise control over industrial processes, such as chemical processing, oil refining, and water treatment. Safety is another paramount consideration where pump covers excel. They prevent accidental contact with moving parts, reducing the risk of injuries to personnel. Additionally, they contain potential leaks or spills, minimizing the risk of environmental contamination and ensuring compliance with stringent safety regulations. This containment also helps in quick identification and isolation of issues, facilitating faster maintenance and reducing downtime. From a maintenance perspective, pump covers simplify routine inspections and repairs. By providing easy access to the pump while protecting it from external factors, these covers enable technicians to perform necessary checks and maintenance tasks more efficiently. This accessibility can lead to early detection of potential issues, preventing costly repairs down the line. Furthermore, pump covers contribute to noise reduction, which is a significant factor in industrial settings where noise levels can be hazardous to workers' health. By encasing the pump, these covers help dampen operational noise, creating a safer working environment that adheres to occupational health standards. In summary, pump covers are indispensable components in industrial settings due to their multifaceted benefits. They protect equipment from environmental damage, enhance operational efficiency, ensure safety, facilitate maintenance, and reduce noise pollution. As such, incorporating high-quality pump covers into industrial systems is essential for optimizing performance, extending equipment lifespan, and maintaining a safe and efficient working environment.
Design and Construction of Pump Covers
The design and construction of pump covers are critical components in ensuring the efficient and safe operation of pumping systems across various industries. These covers not only protect the machinery from environmental elements but also play a significant role in maintaining structural integrity, enhancing durability, and offering customization options to meet specific needs. When it comes to materials used, the choice can significantly impact the performance and longevity of the pump cover. High-quality materials such as stainless steel, aluminum, and durable plastics are often preferred due to their resistance to corrosion and ability to withstand harsh conditions. The structural integrity of pump covers is another crucial aspect, as it ensures that the cover can support its own weight and any external forces without compromising the safety of the pumping system. Additionally, customization options allow for tailored designs that can fit specific applications, enhancing both functionality and aesthetics. By understanding these key factors, engineers and manufacturers can create pump covers that are not only functional but also durable and adaptable. Let's delve into the first of these critical aspects: **Materials Used**.
Materials Used
In the design and construction of pump covers, the selection of materials is a critical factor that influences both the functionality and durability of the cover. The primary goal is to ensure that the material chosen can withstand the operational conditions and environmental factors associated with the pump's application. For instance, stainless steel and aluminum are popular choices due to their corrosion resistance and strength. Stainless steel, in particular, is favored for its ability to resist chemical corrosion, making it ideal for pumps handling corrosive fluids. Aluminum, on the other hand, offers a lightweight yet robust solution that is often used in applications where weight is a concern. Fiberglass-reinforced polymers (FRP) are another material of choice, especially in harsh environments. FRP combines the benefits of high strength-to-weight ratio with excellent resistance to corrosion and chemical attack, making it suitable for use in chemical plants, wastewater treatment facilities, and other industrial settings. Additionally, FRP can be molded into complex shapes, allowing for customized designs that fit specific pump configurations. For more budget-friendly options, galvanized steel or carbon steel may be considered. These materials are cost-effective and can provide adequate protection when properly coated or treated to resist corrosion. However, they may require more maintenance compared to other materials like stainless steel or FRP. In certain applications, such as in food processing or pharmaceutical industries, materials must also meet stringent hygiene standards. Here, materials like 304 or 316 stainless steel are preferred due to their non-reactive properties and ease of cleaning. These grades of stainless steel are resistant to bacterial growth and can withstand frequent sanitizing processes. Furthermore, the choice of material may also depend on the aesthetic requirements of the pump cover. For example, in architectural or residential settings where the pump cover will be visible, materials such as powder-coated aluminum or fiberglass can offer a visually appealing finish while maintaining functional integrity. Ultimately, the selection of materials for pump covers must balance factors such as cost, durability, corrosion resistance, and compliance with industry standards. By carefully considering these aspects, engineers and designers can ensure that the pump cover not only protects the pump but also enhances its overall performance and lifespan. This meticulous approach to material selection underscores the importance of a well-designed and constructed pump cover in maintaining efficient and reliable pump operation across various industries.
Structural Integrity and Durability
**Structural Integrity and Durability** When it comes to the design and construction of pump covers, ensuring structural integrity and durability is paramount. A pump cover serves as a protective barrier against environmental elements, mechanical stress, and potential hazards, making its robustness crucial for the overall performance and longevity of the pumping system. The structural integrity of a pump cover hinges on several key factors: material selection, design geometry, and manufacturing quality. Firstly, the choice of material is critical. Materials such as stainless steel, aluminum, or high-density polymers are often preferred due to their resistance to corrosion, strength-to-weight ratio, and ability to withstand harsh conditions. For instance, stainless steel offers excellent corrosion resistance and can endure extreme temperatures, making it an ideal choice for environments where chemical exposure is a concern. Similarly, aluminum provides a lightweight yet robust solution that can be easily machined and finished to meet specific design requirements. The design geometry of the pump cover also plays a significant role in maintaining structural integrity. Engineers must consider factors such as load distribution, stress concentrations, and potential failure points. Finite Element Analysis (FEA) and computational fluid dynamics (CFD) are commonly used tools to simulate various operating conditions and predict how the cover will behave under different loads. This allows for the optimization of the design to ensure that it can withstand both static and dynamic stresses without compromising its integrity. Manufacturing quality is another vital aspect that directly impacts the durability of the pump cover. Precision machining and fabrication techniques are essential to ensure that the cover meets the specified dimensions and tolerances. Surface treatments like anodizing or powder coating can enhance the cover's resistance to corrosion and wear, further extending its lifespan. Additionally, quality control measures such as inspection and testing protocols must be rigorously implemented to detect any defects or anomalies before the cover is deployed in service. In terms of durability, a well-designed pump cover should be able to endure the rigors of continuous operation over an extended period. This involves considering aspects such as fatigue life, impact resistance, and thermal stability. For example, in applications where the pump is subjected to cyclic loading or vibration, the cover must be designed to absorb these stresses without suffering from material fatigue. Similarly, in high-temperature environments, the cover material should exhibit stable thermal properties to prevent deformation or degradation. Moreover, maintenance accessibility is a key consideration for ensuring long-term durability. A design that allows for easy disassembly and inspection can significantly reduce downtime and maintenance costs. This includes features such as quick-release fasteners, modular components, and clear access points for routine checks and repairs. In conclusion, achieving structural integrity and durability in pump covers is a multifaceted challenge that requires careful attention to material selection, design optimization, manufacturing quality, and maintenance considerations. By integrating these elements effectively, engineers can create pump covers that not only protect the pumping system but also contribute to its overall efficiency and reliability. This holistic approach ensures that the pump cover remains a robust and reliable component throughout its service life, thereby enhancing the performance and lifespan of the entire pumping system.
Customization Options
When it comes to the design and construction of pump covers, customization options play a crucial role in ensuring that these protective enclosures meet the specific needs of various applications. Customization allows for tailored solutions that can enhance performance, safety, and durability. For instance, material selection can be customized based on the environmental conditions in which the pump will operate. Stainless steel or fiberglass might be chosen for corrosive environments, while aluminum or galvanized steel could be more suitable for general industrial use. Additionally, the design of the cover can be adjusted to accommodate different pump sizes and shapes, ensuring a snug fit that maximizes protection without hindering accessibility for maintenance. Customization also extends to the features and accessories of the pump cover. Ventilation systems can be integrated to manage heat and moisture, preventing overheating and condensation buildup. Electrical components such as lighting, sensors, and control panels can be incorporated to enhance operational efficiency and safety. Furthermore, customization can include the addition of access panels, latches, and hinges that facilitate easy maintenance and inspection. These features not only streamline routine tasks but also contribute to the overall longevity of the pump by reducing wear and tear. Another significant aspect of customization is the aesthetic and branding considerations. Companies may opt for specific colors or logos to align with their corporate identity, making the pump cover an integral part of their visual brand presence. This level of personalization can also extend to the finish and texture of the cover, allowing for a seamless integration with existing equipment and surroundings. In terms of regulatory compliance, customization ensures that pump covers adhere to industry standards and local regulations. For example, in hazardous locations, the cover might need to be designed with explosion-proof features or meet specific fire resistance ratings. Customization enables manufacturers to address these requirements effectively, ensuring that the pump cover not only protects the equipment but also complies with all relevant safety standards. Moreover, customization can cater to unique operational requirements such as noise reduction or soundproofing. Specialized materials and design elements can be used to minimize noise levels, making the pump cover suitable for use in residential areas or noise-sensitive environments. This flexibility in design underscores the importance of customization in creating pump covers that are both functional and adaptable. In conclusion, the ability to customize pump covers is essential for optimizing their performance, safety, and longevity. By offering a range of materials, features, and design options, manufacturers can provide solutions that are precisely tailored to the needs of different industries and applications. This level of customization not only enhances the operational efficiency of pumps but also ensures that they are well-integrated into their working environments, contributing to a more streamlined and effective overall system.
Applications and Benefits of Pump Covers
Pump covers are a crucial component in the operation and maintenance of industrial pumps, offering a multitude of benefits that enhance their performance, safety, and longevity. These covers protect pumps from various environmental factors, ensuring they remain functional even in harsh conditions. Additionally, they play a significant role in enhancing safety and security by preventing accidental starts and protecting personnel from moving parts. Furthermore, pump covers contribute to operational efficiency and maintenance by reducing wear and tear, thereby extending the lifespan of the pump and minimizing downtime. By understanding these applications, users can better appreciate the comprehensive value that pump covers bring to their operations. In this article, we will delve into each of these aspects, starting with the critical role of protection from environmental factors.
Protection from Environmental Factors
Protection from environmental factors is a critical aspect of maintaining the efficiency and longevity of industrial equipment, particularly pumps. Pump covers play a pivotal role in safeguarding these essential components against various environmental hazards. By encasing the pump, these covers shield it from direct exposure to harsh weather conditions such as heavy rainfall, snow, and extreme temperatures. This protection prevents water ingress, which can lead to corrosion and electrical malfunctions, ensuring that the pump operates reliably even in adverse weather conditions. Additionally, pump covers protect against dust and debris accumulation, which can clog the pump's moving parts and reduce its performance over time. In coastal or marine environments, these covers also guard against salt spray and other corrosive substances that could degrade the pump's materials. Furthermore, they offer a barrier against physical damage from accidental impacts or vandalism, thereby enhancing the overall durability of the pump. The use of pump covers also facilitates easier maintenance by providing a clean and dry environment for routine inspections and repairs. This not only extends the lifespan of the pump but also reduces downtime and maintenance costs. In summary, pump covers are indispensable for protecting pumps from a wide range of environmental factors, ensuring optimal performance, reliability, and longevity in diverse operational settings.
Enhanced Safety and Security
Enhanced safety and security are paramount when it comes to the operation and maintenance of industrial equipment, particularly pumps. Pump covers play a crucial role in this regard by providing several layers of protection that mitigate risks and ensure a safer working environment. Firstly, pump covers shield the machinery from environmental elements such as dust, moisture, and extreme temperatures, which can lead to premature wear and tear or even catastrophic failures. This not only extends the lifespan of the pump but also reduces downtime due to maintenance or repairs, thereby enhancing operational reliability. Moreover, pump covers act as a physical barrier that prevents unauthorized access to the pump's internal components. This is especially important in industries where tampering could have serious consequences, such as in chemical processing or water treatment plants. By limiting access, pump covers help maintain the integrity of the system and prevent potential sabotage or accidental damage. In addition to physical security, pump covers also contribute to workplace safety by reducing noise levels and preventing accidental contact with moving parts. Industrial pumps can generate significant noise pollution, which can be detrimental to workers' hearing health over time. By encasing the pump, covers help dampen noise levels, creating a more comfortable and safer working environment. Furthermore, the covers protect workers from coming into contact with rotating parts or other hazardous components of the pump, thereby reducing the risk of injuries. From an operational standpoint, pump covers also facilitate easier maintenance and inspection processes. Many modern pump covers are designed with quick-release mechanisms or transparent panels that allow technicians to monitor the pump's condition without having to remove the cover entirely. This streamlined approach to maintenance enhances safety by minimizing the time spent on potentially hazardous tasks and ensures that any issues are identified and addressed promptly. In summary, enhanced safety and security are key benefits of using pump covers in industrial settings. By protecting equipment from environmental factors, preventing unauthorized access, reducing noise pollution, safeguarding against accidental injuries, and facilitating easier maintenance, pump covers significantly contribute to a safer and more secure operational environment. These advantages underscore the importance of incorporating pump covers into any comprehensive safety and security strategy for industrial facilities.
Operational Efficiency and Maintenance
Operational efficiency and maintenance are crucial components in the overall performance and longevity of industrial equipment, particularly pumps. In the context of pump covers, these aspects play a significant role in ensuring that the pumping system operates at its optimal level. Pump covers, designed to protect the pump from environmental elements and potential hazards, contribute significantly to maintaining operational efficiency. By shielding the pump from dust, moisture, and other contaminants, pump covers prevent premature wear and tear on moving parts, thereby reducing the likelihood of mechanical failures. This protection not only extends the lifespan of the pump but also minimizes downtime due to repairs, which is essential for maintaining continuous production processes. Moreover, pump covers facilitate easier maintenance routines. With a cover in place, technicians can perform routine inspections and maintenance tasks without exposing themselves to hazardous conditions such as electrical components or moving parts. The cover also helps in organizing cables and connections neatly, making it easier to identify any issues quickly. Regular maintenance becomes more efficient as technicians can focus on specific areas without the need for extensive disassembly or exposure to potential risks. Additionally, pump covers can be designed with features that enhance operational efficiency. For instance, some covers come with built-in cooling systems or ventilation to regulate temperature around the pump, ensuring optimal operating conditions even in extreme environments. This not only improves the performance of the pump but also reduces energy consumption by preventing overheating and subsequent inefficiencies. From a cost perspective, investing in high-quality pump covers can yield significant long-term savings. By reducing the frequency of repairs and replacements, companies can lower their maintenance costs. Furthermore, the extended lifespan of pumps means fewer capital expenditures over time. The reduction in downtime also translates into higher productivity levels, as operations are less likely to be interrupted by equipment failures. In summary, pump covers are more than just protective devices; they are integral components that enhance operational efficiency and simplify maintenance processes. By protecting pumps from environmental hazards, facilitating easier maintenance, and potentially incorporating features that optimize performance, pump covers contribute to a more reliable and efficient pumping system. This underscores their importance as a critical accessory in various industrial applications where pumps are essential for continuous operation.