What Are Hockey Pucks Made Of

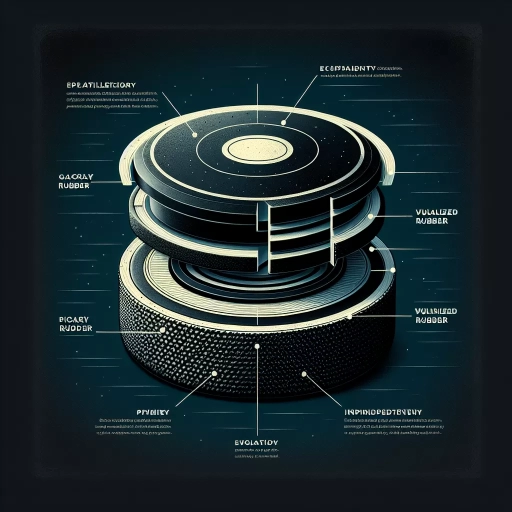
Hockey pucks are a crucial component of the fast-paced and physically demanding sport of ice hockey, known for their durability and precision. But what exactly are these pucks made of? The composition of hockey pucks is a fascinating blend of materials that ensure they can withstand the high-speed impacts and cold temperatures of the game. To delve into this, we will explore three key aspects: the materials used in their construction, the manufacturing process that shapes them, and the standards and regulations that govern their production. Understanding these elements is essential for appreciating the science and craftsmanship behind these seemingly simple objects. Let's begin by examining the materials used in hockey pucks, which form the foundation of their performance and longevity.
Materials Used in Hockey Pucks
Hockey pucks, a crucial component of the game, are crafted from a blend of materials that ensure durability, performance, and safety. The primary components of hockey pucks are rubber and carbon black, which provide the necessary hardness and resilience. However, these pucks also incorporate secondary materials such as additives and fillers to enhance their properties. Additionally, there is a growing focus on sustainability and eco-friendly alternatives in the production of hockey pucks, reflecting broader trends in sports equipment manufacturing. Understanding these elements is essential for appreciating the complexity and innovation behind hockey pucks. Let's delve into the primary components first: rubber and carbon black, which form the foundation of these critical game pieces.
Primary Components: Rubber and Carbon Black
The primary components of hockey pucks are rubber and carbon black, each playing a crucial role in the puck's performance and durability. **Rubber** is the foundational material, providing the necessary elasticity and resilience to withstand the high-speed impacts and collisions inherent in hockey. Natural rubber, derived from the sap of the rubber tree (Hevea brasiliensis), is often used due to its superior elasticity and ability to absorb shock. This natural rubber is mixed with various additives to enhance its properties, such as vulcanization agents that cross-link the polymer chains, thereby increasing the rubber's strength and resistance to wear. **Carbon black**, on the other hand, serves as a reinforcing filler that significantly enhances the mechanical properties of the rubber. It is added to the rubber compound to improve its tensile strength, abrasion resistance, and thermal stability. Carbon black particles distribute evenly throughout the rubber matrix, acting as tiny reinforcing agents that help maintain the puck's shape and integrity under extreme conditions. This combination ensures that hockey pucks can endure the intense forces generated during games without deforming or breaking apart. The precise formulation of rubber and carbon black is critical for achieving the desired puck characteristics. The International Ice Hockey Federation (IIHF) and the National Hockey League (NHL) have specific standards for hockey pucks, including dimensions, weight, and material composition. These standards ensure consistency across different manufacturers and games, which is essential for maintaining fair play and player safety. In addition to their mechanical benefits, rubber and carbon black contribute to the puck's surface texture and frictional properties. The smooth, even surface of a well-manufactured puck allows it to glide smoothly over ice while maintaining sufficient grip to prevent slipping out of control. This balance is crucial for players' accuracy and control during passes and shots. Manufacturers carefully control the mixing process of these components to achieve optimal performance. The vulcanization process, which involves heating the rubber compound under pressure, is particularly important as it cross-links the polymer chains in the rubber, further enhancing its durability. Quality control measures are also in place to ensure that each puck meets the required specifications before being approved for use in professional and amateur games. In summary, the combination of rubber and carbon black in hockey pucks is a testament to the importance of material science in sports equipment. These components work synergistically to provide a durable, consistent, and high-performance product that meets the demands of one of the world's fastest and most physically demanding sports. Their precise formulation and manufacturing process are key factors in ensuring that hockey pucks perform reliably and safely, contributing to the overall enjoyment and competitiveness of the game.
Secondary Materials: Additives and Fillers
In the context of hockey pucks, secondary materials such as additives and fillers play a crucial role in enhancing the performance, durability, and cost-effectiveness of the final product. Additives are substances added to the primary material—typically rubber—to improve specific properties. For instance, antioxidants are used to prevent degradation from exposure to air and light, ensuring the puck maintains its integrity over time. UV stabilizers help protect the rubber from ultraviolet radiation, which can cause it to become brittle or discolored. Additionally, plasticizers may be included to improve flexibility and reduce brittleness, making the puck less prone to cracking under impact. Fillers, on the other hand, are inert materials that are mixed with the rubber to increase its volume and reduce costs without significantly affecting its primary properties. Common fillers include silica (silicon dioxide), calcium carbonate, and carbon black. Silica adds strength and abrasion resistance, while calcium carbonate helps in reducing the cost of production by bulking up the material without compromising on performance. Carbon black is particularly important as it enhances the rubber's tensile strength and resistance to wear and tear. The combination of these additives and fillers allows manufacturers to achieve a balance between performance and cost. For example, by incorporating silica and carbon black, hockey pucks gain improved durability and resistance to wear, which is essential for withstanding high-speed impacts during games. Meanwhile, antioxidants and UV stabilizers ensure that the pucks remain consistent in their performance over their lifespan. In summary, additives and fillers are essential secondary materials in the production of hockey pucks. They enhance the physical properties of the rubber, improve durability, and help control production costs. These materials work synergistically to create a puck that is both resilient and consistent, meeting the stringent requirements of professional and amateur hockey games alike.
Sustainability and Eco-Friendly Alternatives
In the pursuit of sustainability and eco-friendly alternatives, the materials used in hockey pucks are undergoing significant transformations. Traditionally, hockey pucks have been made from rubber, which is derived from non-renewable resources and contributes to environmental degradation. However, innovative companies are now exploring sustainable materials to reduce the ecological footprint of this essential hockey equipment. One promising alternative is the use of recycled rubber, which not only reduces waste but also conserves natural resources. Additionally, some manufacturers are experimenting with plant-based bioplastics, such as those derived from corn starch or sugarcane, which offer a biodegradable and renewable option. Another approach involves using composite materials that combine recycled plastics with natural fibers, enhancing durability while minimizing environmental impact. These eco-friendly alternatives not only align with global sustainability goals but also ensure that hockey pucks remain high-quality and performance-driven, making them a win-win for both the environment and the sport. By adopting these sustainable materials, the hockey industry can significantly reduce its carbon footprint and contribute to a more environmentally conscious future.
Manufacturing Process of Hockey Pucks
The manufacturing process of hockey pucks is a meticulous and multi-step procedure that ensures the production of high-quality, durable, and consistent pucks. This process can be broken down into three critical stages: mixing and compounding raw materials, molding and shaping the puck, and quality control and testing. Each stage is essential to the final product's integrity and performance. The journey begins with the careful selection and blending of raw materials, which sets the foundation for the puck's density, hardness, and overall durability. This initial step is crucial as it determines the puck's ability to withstand the high-speed impacts and harsh conditions of the game. Once the raw materials are properly mixed and compounded, they are then molded and shaped into the iconic disk form of a hockey puck. Finally, rigorous quality control and testing ensure that every puck meets the stringent standards required for professional and amateur play. By understanding these stages, one can appreciate the complexity and precision involved in creating a simple yet vital component of the game. Let's delve deeper into the first stage: mixing and compounding raw materials.
Mixing and Compounding Raw Materials
In the manufacturing process of hockey pucks, the initial and crucial step involves mixing and compounding raw materials. This phase is essential for achieving the desired physical properties and durability of the pucks. The primary raw materials used are rubber and carbon black, along with various additives such as sulfur, zinc oxide, and stearic acid. Rubber, typically a blend of natural and synthetic types, provides the necessary elasticity and resilience. Carbon black enhances the hardness and abrasion resistance of the pucks, while sulfur acts as a vulcanizing agent to cross-link the rubber molecules, improving overall strength and stability. Zinc oxide and stearic acid are added to facilitate the vulcanization process and to reduce the friction between the rubber and other materials during mixing. The mixing process begins with the weighing and measuring of each raw material according to precise formulations. These ingredients are then combined in a specific order to ensure uniform distribution. The rubber is first masticated to break down its molecular structure, making it more receptive to other additives. Carbon black, sulfur, zinc oxide, and stearic acid are subsequently added in a controlled sequence, ensuring thorough dispersion. This mixture is then subjected to high shear mixing in an internal mixer or a two-roll mill to achieve a homogeneous blend. The compounding stage involves further processing to ensure that all components are fully integrated. The mixture is heated and cooled under controlled conditions to optimize the vulcanization reaction. This step is critical as it determines the final hardness, density, and performance characteristics of the hockey pucks. After compounding, the material is formed into sheets or blocks, which are then cut into cylindrical shapes that will eventually become hockey pucks. Throughout this process, quality control measures are implemented to ensure consistency and adherence to specifications. The mixed and compounded material is tested for its physical properties, such as hardness, tensile strength, and impact resistance, to guarantee that it meets the standards required for professional hockey use. This meticulous attention to detail in mixing and compounding raw materials is what sets high-quality hockey pucks apart from inferior alternatives, ensuring they can withstand the rigors of the game without compromising performance or safety.
Molding and Shaping the Puck
In the manufacturing process of hockey pucks, molding and shaping are critical steps that transform raw materials into the precise, durable, and consistent pucks required for the game. This phase involves several key stages. First, a mixture of rubber and other additives such as carbon black, silica, and calcium carbonate is prepared. This blend is then heated and mixed thoroughly to ensure uniformity. The mixture is subsequently poured into molds that are specifically designed to produce pucks with the exact dimensions and weight specified by hockey governing bodies. Once the mixture is in the mold, it undergoes a vulcanization process where it is subjected to high pressure and temperature. This chemical reaction cross-links the rubber molecules, enhancing the puck's hardness, elasticity, and overall durability. After vulcanization, the pucks are removed from the molds and undergo a series of inspections to ensure they meet the required standards. Any excess material is trimmed off, and the pucks are polished to achieve a smooth surface. To achieve the precise weight and balance, pucks may undergo additional processes such as grinding or sanding. Finally, they are painted with the official colors and logos as per regulations. The entire molding and shaping process is highly controlled to ensure consistency across all pucks, which is crucial for fair play in hockey games. The precision in this stage guarantees that each puck will behave predictably on the ice, making it an essential part of the overall manufacturing process.
Quality Control and Testing
Quality control and testing are crucial components of the manufacturing process for hockey pucks, ensuring that each puck meets the stringent standards required for safe and consistent performance on the ice. The process begins with raw material inspection, where rubber compounds and other additives are checked for purity and consistency. Once the raw materials are verified, they are mixed and formulated according to precise recipes to achieve the desired hardness, elasticity, and durability. The mixture is then molded into puck shapes using high-pressure injection molding machines. After molding, pucks undergo a series of tests to ensure they meet the specifications set by governing bodies such as the National Hockey League (NHL) and the International Ice Hockey Federation (IIHF). These tests include weight checks to ensure pucks are within the 5.5 to 6 ounce range, dimensional checks to verify they are 1 inch thick and 3 inches in diameter, and hardness tests using durometers to ensure they have the correct level of hardness. Additionally, pucks are subjected to impact tests where they are dropped from a height to assess their resilience and resistance to cracking or breaking. Visual inspections are also conducted to check for any defects or irregularities in the surface finish. To further guarantee quality, random samples are selected for more rigorous testing, including freeze-thaw cycles to simulate the extreme temperatures pucks may encounter during games. Manufacturers also conduct performance tests such as sliding tests on ice surfaces to ensure pucks glide smoothly and consistently. These comprehensive quality control measures not only enhance player safety but also contribute to a more enjoyable and competitive game by maintaining uniform puck behavior. In summary, quality control and testing in hockey puck manufacturing involve meticulous raw material inspection, precise molding processes, and rigorous testing protocols. These steps collectively ensure that every hockey puck produced adheres to the highest standards of quality, safety, and performance required in professional and recreational hockey games.
Standards and Regulations for Hockey Pucks
Hockey pucks are a crucial component of the game, and their standards and regulations are meticulously defined to ensure consistency, safety, and fair play. The dimensions and weight specifications of hockey pucks are strictly adhered to, ensuring that every puck used in professional and amateur games meets the same criteria. Additionally, material standards and safety guidelines are in place to guarantee that pucks are made from durable, non-toxic materials that minimize the risk of injury to players. Furthermore, certification and compliance with various leagues, such as the National Hockey League (NHL) and the International Ice Hockey Federation (IIHF), ensure that all pucks meet the highest standards of quality and performance. Understanding these aspects is essential for maintaining the integrity of the game. Let's start by examining the precise dimensions and weight specifications that define a standard hockey puck.
Dimensions and Weight Specifications
When it comes to the standards and regulations for hockey pucks, dimensions and weight specifications are crucial to ensure consistency and fairness in the game. According to the National Hockey League (NHL) and the International Ice Hockey Federation (IIHF), hockey pucks must adhere to precise measurements. Each puck must be 1 inch (2.54 cm) thick and 3 inches (7.62 cm) in diameter. The weight of a hockey puck is equally important; it must weigh between 5.5 and 6 ounces (156 to 170 grams). These dimensions and weight specifications are rigorously enforced to maintain the integrity of the game, ensuring that all players compete under the same conditions. The material used to make hockey pucks, typically rubber, is also subject to strict standards to ensure uniformity in performance and durability. The rubber composition must be dense enough to withstand the high-speed impacts and cold temperatures of an ice hockey game without deforming or breaking apart. Compliance with these dimensions and weight specifications is essential for maintaining player safety and the overall quality of the game, making them a cornerstone of hockey regulations.
Material Standards and Safety Guidelines
Material standards and safety guidelines are crucial components in the manufacturing of hockey pucks, ensuring that these essential pieces of equipment meet the necessary criteria for both performance and player safety. The primary material used in hockey pucks is rubber, specifically a dense, vulcanized rubber that provides the required durability and consistency. According to the International Ice Hockey Federation (IIHF) and the National Hockey League (NHL), hockey pucks must adhere to strict specifications: they must be made from a non-abrasive, dense rubber compound, weigh between 5.5 and 6 ounces (156-170 grams), and measure 1 inch (2.54 cm) in thickness and 3 inches (7.62 cm) in diameter. Safety guidelines dictate that the rubber used should be free from any harmful substances and must not cause any adverse reactions when coming into contact with players' skin or equipment. The manufacturing process involves rigorous quality control checks to ensure that each puck meets these standards. For instance, pucks are tested for their weight, size, and hardness to guarantee uniformity and prevent any potential hazards during gameplay. Additionally, the surface finish of the puck is critical; it must be smooth and even to prevent any irregularities that could affect its glide on the ice or cause injuries. The color of the puck is also standardized—official pucks are black to provide high visibility against the white ice surface. Compliance with these material standards and safety guidelines is enforced through regular inspections by governing bodies such as the IIHF and NHL, ensuring that all hockey pucks used in professional and amateur games meet the highest safety and performance standards. In summary, the strict adherence to material standards and safety guidelines in hockey puck manufacturing is paramount for maintaining the integrity of the game while prioritizing player safety. These regulations ensure that every puck used in competitive hockey is consistent, reliable, and safe for all participants involved.
Certification and Compliance with Leagues
Certification and compliance with leagues are crucial aspects of ensuring the quality and safety of hockey pucks. In professional and amateur hockey, pucks must adhere to strict standards set by governing bodies such as the National Hockey League (NHL) and the International Ice Hockey Federation (IIHF). These organizations mandate that pucks meet specific dimensions, weight, and material requirements to ensure consistent performance and player safety. For instance, NHL regulations stipulate that pucks must be made from dense, vulcanized rubber, weigh between 5.5 and 6 ounces, and measure 1 inch thick and 3 inches in diameter. Compliance is verified through rigorous testing procedures, including checks for size, weight, and hardness. Manufacturers must obtain certification from these leagues before their pucks can be used in official games. This certification process involves submitting samples for inspection and passing tests that simulate game conditions. By adhering to these standards, leagues ensure that all players compete with pucks that are uniform in quality, reducing the risk of injury and maintaining the integrity of the game. Additionally, compliance helps in maintaining consistency across different levels of play, from youth leagues to professional tournaments, thereby enhancing the overall experience for players and spectators alike. Overall, the stringent certification and compliance measures in place for hockey pucks are essential for upholding the standards of the sport and ensuring a fair and safe game environment.