What Does A Machinist Do

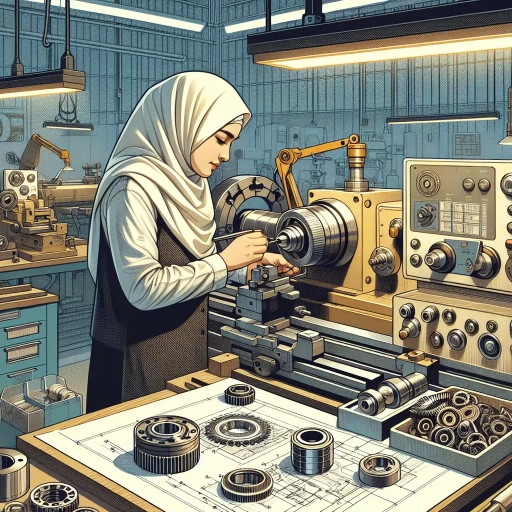
Overview of a Machinist's Role
A machinist plays a pivotal role in modern manufacturing, contributing significantly to the production and maintenance of machinery and equipment. This role is multifaceted, encompassing a broad scope of work that demands precision, technical skill, and attention to detail. To understand the machinist's role comprehensively, it is essential to delve into three key aspects: the definition and scope of their work, their key responsibilities and duties, and their importance across various industries. Firstly, defining the scope of a machinist's work sets the foundation for understanding their daily tasks and the skills required to perform them. This involves an examination of the types of machinery they operate, the materials they work with, and the environments in which they function. Secondly, outlining the key responsibilities and duties of a machinist highlights the specific activities they engage in, such as cutting, shaping, and assembling metal parts, as well as maintaining and repairing existing machinery. Lastly, exploring the importance of machinists in various industries underscores their critical role in sectors like aerospace, automotive, and healthcare, where precision engineering is paramount. By examining these facets, we can gain a deeper appreciation for the intricate and vital work that machinists undertake. Let us begin by defining the scope of their work to understand the breadth of their responsibilities and the impact they have on industrial processes.
Definition and Scope of Work
**Definition and Scope of Work** A machinist is a skilled craftsman who specializes in the fabrication, assembly, and repair of machinery and other precision parts. The definition of a machinist's role encompasses a broad range of responsibilities that are crucial to various industries, including manufacturing, aerospace, automotive, and construction. At its core, the scope of work for a machinist involves using advanced tools and machinery to create or modify metal parts with high precision. This includes operating computer numerical control (CNC) machines, lathes, milling machines, and grinders to cut, shape, and finish metal components according to detailed specifications. The scope of a machinist's work extends beyond mere machine operation; it requires a deep understanding of engineering principles, blueprint reading, and quality control. Machinists must interpret technical drawings and instructions to ensure that the parts they produce meet exacting standards. They also perform routine maintenance on their equipment to prevent malfunctions and optimize performance. Additionally, machinists are often involved in troubleshooting issues with machinery and developing solutions to improve production efficiency. In modern manufacturing environments, machinists frequently work with advanced technologies such as 3D printing and computer-aided design (CAD) software. These tools enable them to design complex parts and simulate their performance before actual production begins. The role also involves collaborating with other professionals like engineers and quality control specialists to ensure that the final products meet industry standards. The versatility of a machinist's role means they can work in various settings, from small workshops to large industrial facilities. In some cases, machinists may specialize in specific types of machinery or materials, such as aerospace components or precision medical instruments. Regardless of the setting or specialization, the fundamental skills required include attention to detail, problem-solving abilities, and a commitment to precision. Overall, the definition and scope of work for a machinist highlight the critical importance of this profession in maintaining and advancing industrial capabilities. By combining technical expertise with practical skills, machinists play a vital role in ensuring the quality and reliability of machinery across diverse sectors. Their work is not only about producing parts but also about contributing to the efficiency, safety, and innovation of modern manufacturing processes.
Key Responsibilities and Duties
As a crucial component of the manufacturing and engineering sectors, a machinist's role is multifaceted and demanding. The key responsibilities and duties of a machinist are centered around precision, skill, and attention to detail. Primarily, machinists are responsible for interpreting blueprints, technical drawings, and specifications to understand the requirements of the parts they need to fabricate. This involves analyzing dimensions, tolerances, and material specifications to ensure that the final product meets exacting standards. A significant portion of a machinist's day is spent operating various machine tools such as lathes, milling machines, grinders, and drill presses. These machines are used to cut, shape, and finish metal and other materials into precise components. Machinists must be adept at setting up these machines, selecting appropriate cutting tools, and adjusting parameters like speed and feed rates to achieve optimal results. Additionally, they are tasked with monitoring the machining process to detect any anomalies or defects early on, thereby ensuring quality control. Maintenance is another critical duty for machinists. They are responsible for performing routine maintenance on their equipment to prevent breakdowns and ensure continuous operation. This includes cleaning machines, lubricating parts, and replacing worn-out tools or components. Troubleshooting is also an essential skill; machinists must diagnose issues with machinery or parts and implement corrective actions promptly. Quality assurance is integral to the machinist's role. They conduct inspections using precision instruments like micrometers, calipers, and gauges to verify that the finished parts meet the required specifications. Any deviations from the standards are documented and addressed through rework or adjustments in the machining process. Collaboration with other departments is also a key responsibility. Machinists often work closely with engineers to provide feedback on design feasibility and suggest improvements based on their practical experience. They may also interact with quality control teams to resolve any issues related to part quality and with production managers to optimize workflow and meet production targets. In modern manufacturing environments, machinists are increasingly expected to be proficient in computer-aided manufacturing (CAM) software and computer numerical control (CNC) systems. These technologies enable them to program machines for automated operations, enhancing efficiency and accuracy. Staying updated with the latest technological advancements and best practices is therefore essential for a machinist to remain competitive. Finally, safety is paramount in this role. Machinists must adhere strictly to safety protocols when operating machinery, handling materials, and working in potentially hazardous environments. This includes wearing protective gear such as gloves, safety glasses, and ear protection as well as following established procedures for handling chemicals and disposing of waste materials. In summary, the role of a machinist is highly specialized and requires a blend of technical knowledge, practical skills, and attention to detail. By fulfilling their key responsibilities and duties diligently, machinists play a vital role in ensuring the production of high-quality components that are essential for various industries ranging from aerospace to automotive manufacturing.
Importance in Various Industries
The role of a machinist is pivotal across various industries, underscoring their importance in maintaining operational efficiency and product quality. In the **aerospace industry**, machinists are crucial for crafting precision components such as engine parts, landing gear, and other critical structural elements that demand exacting tolerances and high-quality finishes. Their expertise ensures the safety and reliability of aircraft, which is paramount given the stringent regulatory standards in this sector. In **automotive manufacturing**, machinists play a key role in producing engine blocks, cylinder heads, and other vital components that require precise machining to meet performance and fuel efficiency standards. Their work directly impacts vehicle reliability, fuel economy, and overall customer satisfaction. The **medical device industry** also heavily relies on machinists to fabricate intricate parts for medical equipment, implants, and surgical instruments. Here, precision is not just a preference but a necessity to ensure patient safety and the efficacy of medical treatments. In **energy production**, particularly in nuclear and renewable energy sectors, machinists are essential for creating components that withstand extreme conditions. For instance, in nuclear power plants, machined parts must be able to endure high temperatures and radiation levels without compromising safety or performance. Furthermore, **defense industries** depend on machinists to produce military hardware such as firearms, ammunition, and other specialized equipment where accuracy and durability are critical factors. The precision work of machinists in this field directly contributes to national security. Additionally, **consumer goods manufacturing** benefits from the skills of machinists who create molds and dies used in mass production processes. This ensures consistent quality in products ranging from household appliances to electronics. In **research and development**, machinists often collaborate with engineers to prototype new designs and test innovative materials. Their ability to translate conceptual designs into tangible prototypes is invaluable for advancing technological frontiers. Lastly, **industrial machinery** relies on machinists for maintenance and repair tasks that keep production lines running smoothly. By fabricating replacement parts or modifying existing machinery, they help minimize downtime and optimize operational efficiency. In summary, the versatility and precision of a machinist's role make them indispensable across a wide spectrum of industries. Their contributions are not limited to production but extend to ensuring safety, reliability, and innovation in various sectors. As technology continues to evolve, the demand for skilled machinists will only grow, highlighting their enduring importance in modern manufacturing processes.
Skills and Qualifications Required
In today's fast-paced and highly competitive job market, possessing the right skills and qualifications is crucial for success. An individual's ability to excel in their chosen profession hinges on a combination of technical skills, physical and mental demands, and the educational pathways they have pursued. Technical skills and knowledge form the foundation of any career, enabling professionals to perform their duties efficiently and effectively. However, these technical competencies must be complemented by the physical and mental stamina required to handle the demands of the job. Additionally, education and training pathways provide the necessary framework for acquiring these skills and staying updated with industry trends. Understanding these three key areas is essential for both employers seeking to hire top talent and individuals aiming to advance their careers. By delving into these aspects, we can better appreciate the multifaceted nature of professional development. Let us begin by exploring the critical role of **Technical Skills and Knowledge** in shaping a successful career.
Technical Skills and Knowledge
**Technical Skills and Knowledge** To excel as a machinist, one must possess a robust set of technical skills and knowledge that span multiple domains. At the core of these skills is a deep understanding of mechanical engineering principles, including kinematics, dynamics, and materials science. Machinists need to be proficient in reading and interpreting blueprints, technical drawings, and computer-aided design (CAD) files to accurately translate designs into physical components. Proficiency in computer numerical control (CNC) machining is crucial, as it involves operating sophisticated machinery that requires precise programming and monitoring. Familiarity with various machining tools and equipment such as lathes, milling machines, grinders, and drill presses is essential. Machinists must also have hands-on experience with metrology tools like micrometers, calipers, and dial indicators to ensure the precision and quality of their work. Knowledge of different materials—such as metals, plastics, and composites—and their properties is vital for selecting the appropriate material for each project. In addition to these foundational skills, modern machinists are increasingly expected to be adept in advanced technologies such as 3D printing, laser cutting, and robotic automation. Understanding software applications like CAM (Computer-Aided Manufacturing) and CAD/CAM integration can significantly enhance productivity and accuracy. Furthermore, familiarity with quality control processes and standards like ISO 9001 ensures that machined parts meet stringent industry requirements. Safety protocols are another critical aspect of a machinist's technical skillset. They must adhere to strict safety guidelines to prevent injuries from machinery and materials. This includes knowing how to properly use personal protective equipment (PPE) such as safety glasses, gloves, and ear protection. Moreover, problem-solving skills are indispensable in this field. Machinists often encounter unexpected issues during production that require quick analysis and resolution. The ability to troubleshoot mechanical problems efficiently can save time and resources while maintaining high-quality output. Finally, staying updated with industry trends and advancements is imperative for career longevity. Participating in continuous learning opportunities such as workshops, seminars, or online courses helps machinists adapt to new technologies and techniques that emerge in the field. By combining these technical skills with practical experience and a commitment to ongoing learning, machinists can deliver precise, high-quality components that meet or exceed customer expectations while contributing to the efficiency and innovation of their organizations.
Physical and Mental Demands
**Physical and Mental Demands** The role of a machinist is inherently demanding, requiring a blend of physical stamina and mental acuity. Physically, machinists must be capable of standing for extended periods, often in environments that are noisy and may involve exposure to hazardous materials. They frequently lift heavy tools and parts, which necessitates good physical strength and endurance. Additionally, the precision required in their work means they must have fine motor skills and dexterity to handle intricate machinery and tools accurately. The physical demands also include working in confined spaces or at heights, which can be challenging and requires a good sense of balance. Mentally, the job is equally taxing. Machinists need to possess strong problem-solving skills to troubleshoot issues with machinery and resolve complex technical problems. They must be detail-oriented to ensure that parts are manufactured to precise specifications, which can be mentally taxing due to the high level of concentration required. Furthermore, machinists often work under tight deadlines, managing multiple projects simultaneously while maintaining quality standards. This demands excellent organizational skills and the ability to manage stress effectively. The mental demands also extend to continuous learning; machinists need to stay updated with new technologies and techniques, which requires a commitment to ongoing education and professional development. In terms of cognitive abilities, machinists must have strong analytical skills to interpret blueprints, technical drawings, and instructions accurately. They need to be able to visualize the final product from raw materials and understand how different components interact within a larger system. This requires a high level of spatial reasoning and the ability to think critically about complex mechanical systems. Moreover, effective communication is crucial as machinists often collaborate with other professionals such as engineers, quality control specialists, and production managers to ensure smooth operations. Overall, the physical and mental demands of being a machinist are significant but rewarding for those who enjoy hands-on work combined with problem-solving challenges. It is essential for aspiring machinists to understand these demands thoroughly to prepare themselves adequately for this dynamic and demanding profession. By recognizing these requirements upfront, individuals can better align their skills and qualifications with the needs of the role, ensuring they are well-equipped to excel in this field.
Education and Training Pathways
Education and training pathways for machinists are multifaceted and designed to equip individuals with the necessary skills and knowledge to excel in this precision-driven field. Typically, aspiring machinists begin their journey with a strong foundation in mathematics and science during high school. Post-secondary education often involves enrolling in vocational or technical schools that offer programs specifically tailored for machinists. These programs, which can range from a few months to two years, provide hands-on training in areas such as blueprint reading, metalworking, and the operation of various machine tools like lathes, milling machines, and grinders. Many machinists also pursue apprenticeships, which combine on-the-job training with classroom instruction. These apprenticeships, usually lasting four years, offer invaluable practical experience under the guidance of experienced machinists. Additionally, some machinists choose to earn associate degrees or certificates in machining technology from community colleges or technical institutes. These programs often include coursework in computer-aided design (CAD), computer numerical control (CNC) machining, and quality control. Certification is another critical component of a machinist's education and training pathway. The National Institute for Metalworking Skills (NIMS) offers various certifications that validate a machinist's competence in specific areas such as CNC machining, grinding, and turning. These certifications not only enhance job prospects but also demonstrate a commitment to ongoing professional development. Continuous learning is essential in the field of machining due to the rapid evolution of technology. Many machinists participate in ongoing training and professional development courses to stay updated with advancements in machinery and manufacturing techniques. Employers often support this ongoing education through in-house training programs or by sponsoring attendance at industry workshops and conferences. In summary, the education and training pathways for machinists are structured to provide a comprehensive blend of theoretical knowledge and practical skills. By combining formal education with apprenticeships, certifications, and continuous learning, aspiring machinists can build a robust foundation that prepares them for successful careers in this demanding yet rewarding field. This well-rounded approach ensures that machinists possess the skills and qualifications required to meet the high standards of precision and quality demanded by modern manufacturing environments.
Day-to-Day Activities and Tools Used
In the realm of day-to-day activities, efficiency and precision are paramount. Whether in industrial settings, scientific laboratories, or even everyday tasks, the tools and techniques employed significantly impact the outcome. This article delves into three critical aspects that underpin successful operations: Machine Operation and Maintenance, Measurement and Quality Control, and the Use of Precision Tools and Equipment. Each of these components plays a vital role in ensuring that tasks are completed accurately and effectively. Machine Operation and Maintenance is essential for preventing downtime and optimizing performance, while Measurement and Quality Control guarantee that standards are met consistently. The Use of Precision Tools and Equipment further enhances accuracy and reliability. By understanding these elements, individuals can streamline their processes, improve productivity, and achieve higher quality results. Let's begin by examining the first of these crucial elements: Machine Operation and Maintenance.
Machine Operation and Maintenance
Machine operation and maintenance are crucial components of a machinist's day-to-day activities, ensuring that machinery runs efficiently and safely. Effective machine operation involves a deep understanding of the equipment's capabilities, limitations, and operational procedures. Machinists must be adept at reading technical manuals, interpreting blueprints, and following safety protocols to avoid accidents. They are responsible for setting up machines, calibrating tools, and performing routine checks to ensure optimal performance. This includes monitoring temperature, pressure, and vibration levels, as well as checking for any signs of wear or malfunction. Maintenance is equally important and involves both preventive and corrective measures. Preventive maintenance includes scheduled tasks such as lubricating moving parts, replacing worn-out components, and conducting regular inspections to identify potential issues before they become major problems. Corrective maintenance involves diagnosing and repairing faults when they occur, which requires troubleshooting skills and the ability to analyze data from sensors and monitoring systems. Machinists use a variety of tools for these tasks, including precision instruments like micrometers and calipers for measurements, as well as power tools such as drill presses and grinders for repairs. In addition to hands-on skills, modern machine operation often involves working with advanced technologies such as computer numerical control (CNC) systems. These systems require machinists to program and operate sophisticated software that controls the machining process with high precision. Understanding programming languages like G-code is essential for operating CNC machines effectively. Safety is another critical aspect of machine operation and maintenance. Machinists must adhere to strict safety guidelines to protect themselves and others from hazards such as sharp edges, moving parts, and chemical exposure. Personal protective equipment (PPE) such as gloves, safety glasses, and earplugs are standard tools in this environment. The integration of technology into machine operation has also led to the use of predictive maintenance techniques. These involve using sensors and data analytics to predict when maintenance will be needed based on real-time data from the machinery. This proactive approach helps in minimizing downtime and optimizing overall production efficiency. In summary, machine operation and maintenance are integral parts of a machinist's role, requiring a blend of technical knowledge, practical skills, and attention to detail. By combining traditional craftsmanship with modern technological advancements, machinists ensure that machinery operates at peak performance while maintaining a safe working environment. The tools used in these activities range from basic hand tools to sophisticated CNC systems and predictive maintenance software, all aimed at enhancing productivity and reliability in manufacturing processes.
Measurement and Quality Control
In the day-to-day activities of a machinist, measurement and quality control are paramount to ensuring precision and excellence in every piece produced. These processes are integral to the machinist's role, as they directly impact the final product's accuracy, reliability, and overall quality. Measurement involves the use of various tools and instruments to gauge dimensions, angles, and other critical specifications of parts and components. Machinists rely on calipers, micrometers, dial indicators, and coordinate measuring machines (CMMs) to take precise measurements that adhere to blueprint specifications. For instance, a machinist might use a digital caliper to measure the diameter of a shaft or the thickness of a plate, while a CMM could be employed for more complex geometries. Quality control is an ongoing process that begins with the initial inspection of raw materials and continues through each stage of production. Machinists conduct regular checks to ensure that parts meet the required standards, often using statistical process control (SPC) methods to monitor production trends and identify any deviations early. This proactive approach helps in maintaining consistency and preventing defects. Additionally, machinists may perform functional tests on completed parts to verify their performance under real-world conditions. For example, a machinist might assemble a gearbox and run it through a series of tests to ensure smooth operation and durability. The tools used in measurement and quality control are sophisticated and highly specialized. Precision gauges like go/no-go gauges are used to quickly determine if a part meets specific tolerances. Surface finish testers help in evaluating the texture and smoothness of surfaces, which is crucial for parts that require low friction or high wear resistance. Optical comparators and vision systems provide detailed visual inspections, allowing machinists to examine intricate features without physical contact. Moreover, modern machining shops increasingly incorporate advanced technologies such as computer-aided inspection (CAI) and machine learning algorithms to enhance quality control processes. CAI systems automate the inspection process by comparing part dimensions against digital models, significantly reducing human error and increasing efficiency. Machine learning algorithms can analyze historical data to predict potential issues before they occur, enabling preventive maintenance and optimizing production workflows. In summary, measurement and quality control are fundamental aspects of a machinist's daily activities. By leveraging a range of precision tools and advanced technologies, machinists can ensure that every part produced meets stringent quality standards, thereby contributing to the reliability and performance of the final product. This meticulous attention to detail not only enhances customer satisfaction but also supports the broader goals of manufacturing excellence and continuous improvement.
Use of Precision Tools and Equipment
In the daily life of a machinist, precision tools and equipment are indispensable for ensuring accuracy, efficiency, and quality in every task. These tools are meticulously designed to handle a wide range of operations, from cutting and shaping metal to measuring and inspecting finished products. At the heart of a machinist's toolkit lies the lathe, a versatile machine capable of turning, facing, and boring various materials with high precision. The milling machine is another crucial piece of equipment, allowing machinists to perform complex operations such as drilling, cutting, and shaping parts with intricate designs. Drill presses and grinders also play vital roles; drill presses provide precise control over drilling operations, while grinders are used for fine-tuning surfaces to exact specifications. Precision measuring tools are equally important in a machinist's arsenal. Calipers, micrometers, and dial indicators enable machinists to measure dimensions accurately down to fractions of a millimeter. These measurements are critical for ensuring that parts fit together seamlessly and function as intended. Additionally, surface finish testers help in evaluating the smoothness and quality of the finished surface, which is essential for applications where friction and wear resistance are key factors. Computer Numerical Control (CNC) machines have revolutionized the field by integrating advanced technology with traditional machining techniques. CNC machines allow for automated operations based on pre-programmed instructions, significantly reducing human error and increasing production speed. These machines can perform multiple tasks simultaneously, such as milling, turning, and drilling, making them highly efficient in modern manufacturing environments. Furthermore, precision cutting tools like end mills, drill bits, and taps are designed to withstand high speeds and pressures while maintaining their cutting edge. These tools are often made from high-strength materials such as tungsten carbide or high-speed steel to ensure durability and longevity. The use of these specialized tools not only enhances the quality of the final product but also extends the lifespan of the machinery itself. In addition to these physical tools, software plays a significant role in modern machining practices. Computer-Aided Design (CAD) software allows machinists to design parts with precise dimensions before they are manufactured. Computer-Aided Manufacturing (CAM) software then translates these designs into instructions that CNC machines can execute. This integration of technology ensures that every step of the machining process is optimized for precision and efficiency. Overall, the use of precision tools and equipment is fundamental to the work of a machinist. These tools enable machinists to produce high-quality parts consistently, meeting stringent industry standards. Whether it's traditional manual machinery or advanced CNC systems, precision is at the core of every operation, reflecting the meticulous attention to detail that defines the profession. By leveraging these tools effectively, machinists can achieve exceptional results in their day-to-day activities, contributing significantly to various industries such as aerospace, automotive, and medical device manufacturing.