What Do The Initials Whmis Stand For

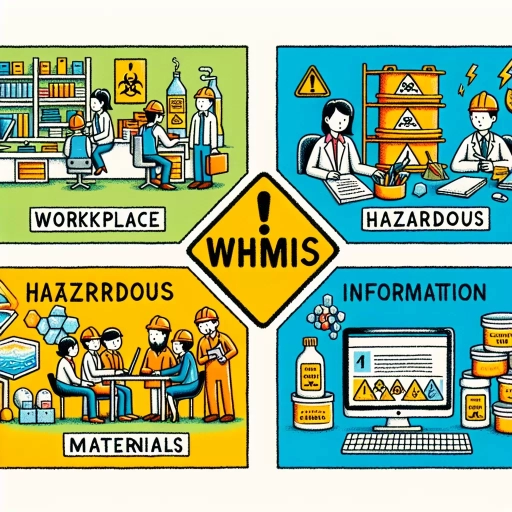
In the realm of workplace safety and chemical management, few acronyms are as crucial as WHMIS. Standing for Workplace Hazardous Materials Information System, WHMIS is a comprehensive framework designed to protect workers from the dangers associated with hazardous materials. This system is not just a set of regulations; it is a multifaceted approach that ensures the safe handling, use, and disposal of chemicals in various work environments. To fully grasp the significance of WHMIS, it is essential to delve into its core components. This article will provide an in-depth look at what WHMIS entails, starting with an **Understanding WHMIS: An Overview**, which sets the stage for a detailed exploration. We will then **Break Down the Acronym: What Each Letter Represents**, dissecting the meaning behind each letter to clarify its purpose. Finally, we will examine **Implementation and Compliance: How WHMIS Works**, highlighting the practical aspects of integrating WHMIS into daily operations. By the end of this journey, readers will have a thorough understanding of how WHMIS safeguards workplaces and why it is indispensable in modern industry. Let us begin with **Understanding WHMIS: An Overview** to lay the foundation for this critical discussion.
Understanding WHMIS: An Overview
Understanding WHMIS (Workplace Hazardous Materials Information System) is crucial for ensuring safety and compliance in workplaces that handle hazardous materials. This comprehensive system has evolved significantly since its inception, making it essential to grasp its historical context, key components, and importance in maintaining workplace safety. Historically, WHMIS was introduced to standardize the classification and communication of hazardous materials, addressing the need for a unified approach to safety protocols. The key components of WHMIS include hazard classification, safety data sheets (SDS), and labels, which provide critical information about the risks associated with various substances. These elements are vital for training employees and implementing safe handling practices. The importance of WHMIS in workplace safety cannot be overstated, as it directly impacts the health and well-being of workers by providing them with the necessary knowledge to handle hazardous materials safely. By delving into these aspects, we can better appreciate the significance of WHMIS. Let's begin by exploring the historical context of WHMIS, which laid the foundation for the robust safety standards we have today.
Historical Context of WHMIS
The Historical Context of WHMIS (Workplace Hazardous Materials Information System) is deeply rooted in the evolving landscape of occupational health and safety regulations in Canada. The inception of WHMIS can be traced back to the late 1970s and early 1980s, a period marked by growing public awareness and concern over the risks associated with hazardous materials in the workplace. Prior to WHMIS, there was a lack of standardized protocols for identifying, handling, and communicating the dangers of chemicals used in various industries. This void led to numerous workplace accidents and health issues, prompting the need for a comprehensive system to protect workers. In 1983, the Canadian government, in collaboration with provincial and territorial authorities, launched WHMIS as a national standard to ensure that workers were adequately informed about the hazards of materials they worked with. The system was designed to provide a consistent approach to classifying hazardous materials, labeling products, and providing safety data sheets (SDSs) that detailed essential safety information. This initiative was a significant step forward in aligning Canadian regulations with international standards, particularly those set by the United Nations. The implementation of WHMIS involved several key components: hazard classification, labeling, and safety data sheets. Hazard classification ensured that substances were categorized based on their physical and health hazards, while labeling provided immediate visual warnings about the dangers of a product. Safety data sheets offered detailed information on safe handling practices, emergency procedures, and first aid measures. These elements collectively aimed to empower workers with the knowledge necessary to handle hazardous materials safely. Over the years, WHMIS has undergone several revisions to keep pace with advancements in scientific understanding and changes in regulatory frameworks. One of the most significant updates came in 2015 with the alignment of WHMIS with the Globally Harmonized System of Classification and Labelling of Chemicals (GHS), an international standard developed by the United Nations. This alignment, known as WHMIS 2015, introduced new classification criteria, updated labeling requirements, and revised the format of safety data sheets to enhance clarity and consistency. Today, WHMIS remains a cornerstone of workplace safety in Canada, ensuring that employers and workers alike are equipped with the necessary tools to manage hazardous materials effectively. The system's evolution reflects a commitment to continuous improvement and adaptation to emerging challenges in occupational health and safety. As part of a broader framework that includes training programs, workplace policies, and enforcement mechanisms, WHMIS plays a critical role in safeguarding the well-being of workers across various sectors. Understanding the historical context of WHMIS underscores its importance as a proactive measure in preventing workplace injuries and illnesses, highlighting the collaborative efforts between government, industry, and labor that have shaped this essential safety standard.
Key Components of WHMIS
**Key Components of WHMIS** The Workplace Hazardous Materials Information System (WHMIS) is a comprehensive framework designed to ensure the safe handling, use, and disposal of hazardous materials in Canadian workplaces. At its core, WHMIS consists of several key components that work together to protect workers from chemical hazards. 1. **Classification**: This involves categorizing hazardous products based on their physical and health hazards. Products are classified into two main categories: physical hazards (such as flammable liquids or gases) and health hazards (such as toxic substances). This classification is crucial for identifying the risks associated with each product. 2. **Labels**: Hazardous products must be labeled with specific information to alert workers about the potential dangers. These labels include the product identifier, hazard statements, precautionary statements, and pictograms (symbols that convey specific hazards). The label serves as a quick reference guide for workers to understand the risks and necessary precautions. 3. **Safety Data Sheets (SDSs)**: These detailed documents provide comprehensive information about each hazardous product, including its composition, first aid measures, fire-fighting measures, accidental release measures, handling and storage, exposure controls/personal protection, physical and chemical properties, stability and reactivity, toxicological information, ecological information, disposal considerations, transport information, regulatory information, and any other relevant data. SDSs are essential for employers to develop safe work practices and for workers to understand how to handle products safely. 4. **Training**: Effective training is a critical component of WHMIS. Employers are required to educate workers on the safe handling of hazardous materials, including how to read labels and SDSs, understand hazard classifications, and follow safe work procedures. Training must be specific to the workplace and the types of hazardous products used. 5. **Program Implementation**: Employers must implement a WHMIS program that includes procedures for handling hazardous materials, emergency response plans, and regular updates to ensure compliance with current regulations. This program should be tailored to the specific needs of the workplace and should involve ongoing monitoring and evaluation. 6. **Regulatory Compliance**: WHMIS is governed by federal and provincial regulations. Employers must comply with these regulations to ensure that their workplace meets all legal requirements regarding the handling of hazardous materials. This includes adhering to standards for classification, labeling, SDSs, and training. By integrating these components—classification, labels, SDSs, training, program implementation, and regulatory compliance—WHMIS provides a robust system for managing chemical hazards in the workplace. This integrated approach ensures that workers are well-informed and equipped to handle hazardous materials safely, thereby reducing the risk of injuries and illnesses. Understanding these key components is essential for any organization seeking to create a safe and compliant work environment.
Importance of WHMIS in Workplace Safety
The importance of WHMIS (Workplace Hazardous Materials Information System) in workplace safety cannot be overstated. WHMIS is a comprehensive system designed to provide workers with the necessary information to safely handle hazardous materials in the workplace. The initials WHMIS stand for Workplace Hazardous Materials Information System, which is a Canadian standard for classifying and communicating the hazards of controlled products in the workplace. This system ensures that workers are well-informed about the potential dangers associated with the chemicals they use, thereby reducing the risk of accidents and health issues. At its core, WHMIS mandates that all hazardous materials be labeled with specific information, including the product identifier, hazard statements, precautionary statements, and pictograms. These labels serve as critical visual cues that alert workers to potential hazards. Additionally, WHMIS requires the provision of Safety Data Sheets (SDSs), which provide detailed information on the safe handling, use, storage, and disposal of hazardous products. This documentation is essential for training programs and emergency response planning. The implementation of WHMIS also includes rigorous training requirements to ensure that all employees understand the hazards associated with the materials they work with. This training covers how to read and interpret labels and SDSs, as well as how to handle spills and other emergencies safely. By equipping workers with this knowledge, employers can significantly reduce the incidence of workplace injuries and illnesses caused by chemical exposure. Moreover, WHMIS compliance is not just a matter of regulatory adherence; it also has significant economic benefits. Workplaces that adhere to WHMIS standards often experience lower rates of absenteeism due to work-related illnesses and injuries, which in turn can lead to increased productivity and reduced healthcare costs. Furthermore, a safe working environment fosters a positive workplace culture, enhancing employee morale and retention. In summary, WHMIS plays a pivotal role in maintaining a safe and healthy work environment by providing critical information about hazardous materials. Through its labeling and documentation requirements, along with mandatory training programs, WHMIS empowers workers to handle chemicals safely and effectively. By prioritizing WHMIS compliance, employers not only meet legal obligations but also contribute to a safer, more productive workplace. This underscores the importance of understanding and adhering to WHMIS guidelines as an integral part of any workplace safety strategy.
Breaking Down the Acronym: What Each Letter Represents
When delving into the intricacies of an acronym, it is crucial to understand the significance of each letter, as it often represents a critical component of a larger system. In this article, we will break down an acronym that encompasses three key elements: Workplace, Hazardous, and Materials Information System (MIS). Each of these components plays a vital role in ensuring safety, efficiency, and compliance in various industries. The "W" stands for Workplace, highlighting the environment where tasks are performed and where safety protocols are paramount. The "H" represents Hazardous, emphasizing the potential risks and dangers that must be mitigated to protect workers and the environment. Finally, "MIS" signifies the Materials Information System, which is essential for managing and tracking materials to ensure their safe handling and use. By understanding these individual components, we can better appreciate how they collectively contribute to a safe, efficient, and well-regulated workplace. Let's start by examining the first letter: W - Workplace.
W - Workplace
In the context of WHMIS (Workplace Hazardous Materials Information System), the letter "W" stands for "Workplace," emphasizing the critical importance of a safe and informed work environment. The workplace is where employees interact with hazardous materials on a daily basis, making it essential to ensure that all workers are adequately trained and equipped to handle these substances safely. WHMIS is designed to provide comprehensive information about the hazards associated with various chemicals and materials, enabling workers to take necessary precautions to protect themselves and their colleagues. This includes understanding the proper use, handling, storage, and disposal of hazardous substances, as well as recognizing the signs and symptoms of exposure. By focusing on the workplace, WHMIS aims to reduce the risk of accidents, injuries, and illnesses that can arise from the use of hazardous materials. Effective implementation of WHMIS involves not only providing detailed safety data sheets (SDS) and labels but also ensuring that all employees receive regular training and updates on new substances and procedures. This proactive approach helps foster a culture of safety within the workplace, where every individual is empowered to contribute to a healthier and safer working environment. Ultimately, the "W" in WHMIS underscores the commitment to safeguarding the well-being of workers and promoting a responsible and safe handling of hazardous materials in all workplaces.
H - Hazardous
In the context of WHMIS (Workplace Hazardous Materials Information System), the letter "H" stands for "Hazardous," a term that encapsulates the inherent dangers associated with certain materials. Hazardous substances are those that can cause harm to human health, the environment, or both. These substances can be classified into various categories based on their potential to cause physical or health hazards. For instance, physical hazards include flammable liquids, gases, and solids that can ignite or explode under certain conditions. Health hazards, on the other hand, encompass substances that can cause acute or chronic health effects such as carcinogens, mutagens, and reproductive toxins. Understanding the hazardous nature of a substance is crucial for ensuring workplace safety. Under WHMIS, employers are mandated to provide workers with comprehensive information about the hazards of the materials they handle. This includes labeling products with standardized symbols and providing Safety Data Sheets (SDSs) that detail the substance's properties, safe handling practices, and emergency procedures. By recognizing and respecting these hazards, workers can take necessary precautions to minimize risks and prevent accidents. The classification of hazardous substances under WHMIS is rigorous and based on scientific criteria. For example, substances are evaluated for their potential to cause skin irritation, respiratory problems, or other adverse health effects. This classification system ensures that workers are aware of the specific risks associated with each substance they encounter. Moreover, it facilitates the development of targeted safety protocols and training programs tailored to the unique hazards present in different workplaces. In addition to protecting workers, the identification of hazardous substances also plays a critical role in environmental protection. Many hazardous materials can contaminate soil, water, and air if not handled properly. Therefore, understanding their hazardous nature helps in implementing appropriate disposal methods and spill response strategies to mitigate environmental impacts. Overall, the "H" in WHMIS serves as a critical reminder of the importance of recognizing and managing hazards in the workplace. By understanding what makes a substance hazardous and taking appropriate measures to mitigate these risks, employers and workers alike can contribute to a safer and healthier work environment. This proactive approach not only safeguards human health but also helps in preserving the integrity of our environment for future generations.
MIS - Materials Information System
In the context of workplace safety and chemical management, the acronym WHMIS (Workplace Hazardous Materials Information System) is crucial, but it is also important to understand the broader framework that supports such systems. This is where the concept of a Materials Information System (MIS) comes into play. An MIS is a comprehensive database and management tool designed to store, retrieve, and analyze detailed information about various materials used within an organization. It serves as a central repository for material properties, safety data sheets (SDS), handling instructions, and other critical information necessary for ensuring compliance with regulations like WHMIS. An effective MIS integrates seamlessly with existing safety protocols, enhancing the ability of organizations to manage hazardous materials efficiently. Each component of the MIS is tailored to address specific needs: material properties databases provide detailed chemical and physical characteristics; SDS repositories ensure easy access to essential safety information; and inventory management modules track the quantity and location of materials. This holistic approach not only aids in compliance but also improves operational efficiency by streamlining processes related to procurement, storage, and disposal of materials. Moreover, an MIS often includes advanced features such as data analytics and reporting tools, which help in identifying trends and potential risks associated with material usage. These insights can be invaluable for risk assessment and mitigation strategies, allowing organizations to proactively address potential hazards before they become incidents. The system also facilitates training programs by providing easy access to relevant documentation and guidelines, ensuring that employees are well-informed about the safe handling of materials. From a regulatory standpoint, an MIS ensures that all necessary documentation is up-to-date and readily available for audits or inspections. This reduces the administrative burden on compliance officers and minimizes the risk of non-compliance penalties. Additionally, many modern MIS solutions are cloud-based, enabling real-time updates and access across multiple locations, which is particularly beneficial for large or distributed organizations. In summary, a Materials Information System is a powerful tool that complements initiatives like WHMIS by providing a structured framework for managing material-related data. By centralizing critical information and enhancing operational efficiency, an MIS plays a pivotal role in maintaining a safe and compliant work environment. Its ability to integrate with existing safety protocols, provide real-time updates, and offer advanced analytics makes it an indispensable asset for any organization dealing with hazardous materials. As such, understanding the role of an MIS is essential for breaking down the complexities of acronyms like WHMIS and appreciating the broader landscape of workplace safety and material management.
Implementation and Compliance: How WHMIS Works
The implementation and compliance of the Workplace Hazardous Materials Information System (WHMIS) are crucial for ensuring the safety of workers in environments where hazardous materials are present. WHMIS is a comprehensive system that encompasses several key components, each designed to mitigate risks associated with hazardous substances. At its core, WHMIS involves the classification and labeling of hazardous materials, which provides immediate visual warnings and detailed information about the dangers posed by specific substances. Additionally, Safety Data Sheets (SDS) play a pivotal role by offering in-depth information on the safe handling, storage, and emergency procedures for these materials. Furthermore, training and education for workers are essential to ensure that they understand the risks and know how to handle hazardous materials safely. By integrating these elements, WHMIS creates a robust framework for workplace safety. Understanding how these components work together begins with the fundamental step of classifying and labeling hazardous materials, which sets the stage for effective compliance and risk mitigation.
Classification and Labeling of Hazardous Materials
**Classification and Labeling of Hazardous Materials** The classification and labeling of hazardous materials are critical components of the Workplace Hazardous Materials Information System (WHMIS), which stands for **Workplace Hazardous Materials Information System**. WHMIS is a comprehensive system designed to provide workers with the information they need to safely handle hazardous materials in the workplace. At the heart of WHMIS lies the rigorous process of classifying and labeling these substances, ensuring that all stakeholders are aware of the potential dangers and necessary precautions. Classification under WHMIS involves categorizing hazardous materials into specific classes based on their physical and health hazards. This includes categories such as flammable gases, toxic substances, and corrosive materials. Each class has its own set of criteria that define the severity of the hazard, allowing for a standardized approach to risk assessment. For instance, flammable liquids are classified based on their flash points and boiling points, while toxic substances are categorized based on their acute toxicity and other adverse health effects. Once classified, these hazardous materials must be labeled with specific information that alerts workers to the potential risks. Labels are mandated to include key elements such as the product identifier, hazard statements, precautionary statements, and pictograms. Pictograms are visual symbols that quickly convey the nature of the hazard; for example, a flame symbol indicates flammability, while a skull and crossbones symbol indicates acute toxicity. This visual approach ensures that even workers who may not read or understand the written information can still recognize potential hazards. In addition to labels, Safety Data Sheets (SDSs) are also required for each hazardous material. SDSs provide detailed information about the substance, including its composition, first aid measures, fire-fighting measures, accidental release measures, handling and storage instructions, exposure controls/personal protection, physical and chemical properties, stability and reactivity, toxicological information, ecological information, disposal considerations, transport information, regulatory information, and other relevant data. This comprehensive documentation ensures that workers have access to all necessary information to handle hazardous materials safely. The implementation of these classification and labeling standards is enforced through regulations and compliance measures. Employers are responsible for ensuring that all hazardous materials in their workplace are properly classified and labeled according to WHMIS standards. They must also provide training to their employees on how to read and understand labels and SDSs, as well as how to handle these substances safely. Regular inspections and audits help ensure compliance with WHMIS regulations, protecting both workers and the environment from potential hazards. In summary, the classification and labeling of hazardous materials under WHMIS are essential steps in maintaining a safe working environment. By categorizing substances based on their hazards and providing clear, standardized labeling and documentation, WHMIS empowers workers with the knowledge they need to handle these materials safely. This systematic approach not only protects workers but also contributes to a broader culture of safety and compliance in the workplace.
SDS (Safety Data Sheets) and Their Role
**SDS (Safety Data Sheets) and Their Role** Safety Data Sheets (SDS) are a cornerstone of workplace safety, particularly within the framework of the Workplace Hazardous Materials Information System (WHMIS). WHMIS, which stands for Workplace Hazardous Materials Information System, is a Canadian regulation designed to protect workers from hazardous materials. At the heart of WHMIS compliance lies the SDS, a comprehensive document that provides critical information about the safe handling, use, storage, and disposal of chemical products. An SDS typically includes 16 sections, each addressing a specific aspect of the chemical's properties and hazards. These sections cover everything from the chemical's identity and composition to its first aid measures, fire-fighting measures, and environmental impact. This detailed information enables employers to develop effective safety protocols and ensure that workers are adequately trained to handle hazardous substances safely. The role of SDS extends beyond mere compliance; it serves as a vital tool for risk management. By providing detailed hazard information, SDS help employers assess the risks associated with specific chemicals and implement appropriate control measures. For instance, if an SDS indicates that a chemical is highly flammable, employers can take steps to ensure that it is stored in a well-ventilated area away from ignition sources. Moreover, SDS facilitate communication among various stakeholders involved in the handling of hazardous materials. Suppliers are required to provide SDS for each hazardous product they sell or import, ensuring that downstream users have access to essential safety information. This ensures a chain of responsibility where each party can make informed decisions about how to handle the chemical safely. In addition to their practical applications, SDS also play a crucial role in emergency response planning. In the event of an accident or spill, having immediate access to an SDS can be lifesaving. The information contained in these documents helps emergency responders understand the nature of the hazard and take appropriate actions to mitigate risks. Overall, SDS are indispensable for maintaining a safe and compliant workplace under WHMIS regulations. They empower employers and workers with the knowledge needed to handle hazardous materials responsibly, thereby reducing the risk of accidents and ensuring a healthier work environment. By understanding and adhering to the information provided in SDS, workplaces can foster a culture of safety that aligns with the broader objectives of WHMIS.
Training and Education for Workers
**Training and Education for Workers** Effective training and education are cornerstone elements in the implementation and compliance of the Workplace Hazardous Materials Information System (WHMIS). WHMIS, which stands for Workplace Hazardous Materials Information System, is a Canadian standard designed to provide workers with the necessary information to safely handle hazardous materials. To ensure that workers can identify, handle, and respond to hazardous substances safely, comprehensive training programs are essential. Training under WHMIS involves several key components. First, workers must be educated on the classification of hazardous products, which includes understanding the types of hazards (physical, health, and environmental) and how these hazards are categorized. This knowledge enables workers to recognize potential dangers and take appropriate precautions. Second, training includes learning how to read and interpret Safety Data Sheets (SDSs), which provide detailed information about the safe handling, use, storage, and disposal of hazardous products. Workers must also be familiar with the labels on hazardous products, which include pictograms, hazard statements, and precautionary statements that convey critical safety information. Hands-on training is also crucial as it allows workers to practice using personal protective equipment (PPE) and emergency response procedures. This practical training helps workers develop the skills needed to respond effectively in case of spills, leaks, or other emergencies involving hazardous materials. Additionally, ongoing training and refresher courses are necessary to keep workers up-to-date with any changes in WHMIS regulations or new hazardous products introduced into the workplace. Employers play a significant role in ensuring that their workers receive adequate training. They must provide regular training sessions, maintain records of training, and ensure that all new employees receive WHMIS training as part of their onboarding process. Employers should also conduct regular audits to assess the effectiveness of their training programs and make necessary adjustments. Moreover, worker participation is vital in the success of WHMIS training. Workers should be encouraged to ask questions and report any concerns or incidents related to hazardous materials. This active engagement fosters a culture of safety within the workplace, where everyone is committed to adhering to WHMIS standards. In summary, robust training and education programs are indispensable for the successful implementation and compliance with WHMIS. By equipping workers with the knowledge and skills to handle hazardous materials safely, employers not only protect their workforce but also contribute to a safer and more compliant work environment. This commitment to training underscores the importance of WHMIS in safeguarding health and safety in Canadian workplaces.