What Is Casting

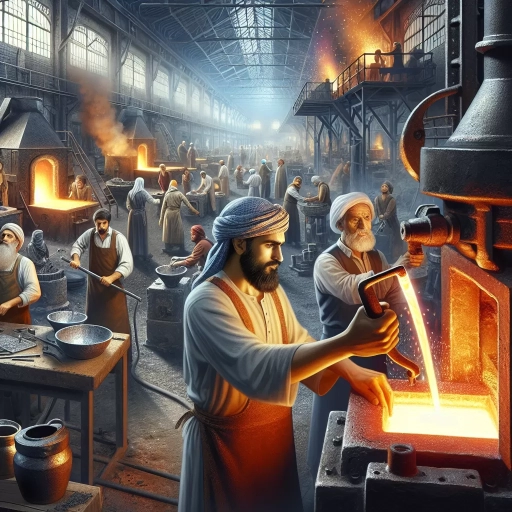
Casting, a fundamental process in manufacturing, involves shaping molten material into a desired form. This versatile technique has been integral to human innovation for centuries, from ancient artifacts to modern industrial components. In this article, we will delve into the multifaceted world of casting, exploring its core principles, the intricate steps involved in the casting process, and its widespread applications across various industries. First, we will **Understand the Basics of Casting**, examining the essential materials, tools, and methodologies that underpin this craft. Next, we will navigate **The Casting Process: From Design to Completion**, detailing how designs are transformed into tangible products through a series of meticulous steps. Finally, we will explore **Applications and Industries Utilizing Casting**, highlighting the diverse sectors that rely on casting for their operations. By grasping these foundational elements, readers will gain a comprehensive understanding of casting's significance and its role in shaping our modern world. Let's begin by **Understanding the Basics of Casting**.
Understanding the Basics of Casting
Understanding the basics of casting is a multifaceted journey that encompasses various aspects, each contributing to a comprehensive grasp of this ancient yet evolving craft. At its core, casting involves the process of creating objects by pouring molten material into a mold, but its significance extends far beyond this simple definition. To delve into the world of casting, it is essential to explore three key areas: the definition and purpose of casting, the diverse types of casting processes, and the historical development of casting techniques. Firstly, understanding the definition and purpose of casting sets the foundation for appreciating its role in manufacturing and art. This involves recognizing how casting serves as a versatile method for producing intricate shapes and designs that might be challenging or impossible to achieve through other means. Secondly, examining the various types of casting processes reveals the adaptability and innovation within the field, from sand casting to investment casting, each with its unique advantages and applications. Lastly, tracing the historical development of casting techniques highlights the evolution from primitive methods to sophisticated modern practices, showcasing human ingenuity and technological advancements. By exploring these dimensions, one can gain a profound understanding of casting's significance and its enduring relevance in contemporary industries. Let us begin by defining and understanding the purpose of casting, which serves as the bedrock for all subsequent discussions on this fascinating subject.
Definition and Purpose of Casting
Casting, a fundamental process in various industries including manufacturing, art, and entertainment, involves the creation of objects by pouring molten material into a mold. The definition of casting encompasses a broad range of techniques and materials, but its core purpose remains consistent: to produce a desired shape or form with precise dimensions and characteristics. In the context of manufacturing, casting is crucial for producing complex parts that cannot be easily fabricated through other methods such as machining or forging. For instance, engine blocks, cylinder heads, and other automotive components are often cast to achieve the intricate geometries required for optimal performance. In the realm of art, casting allows artists to create intricate sculptures and statues with detailed textures and designs. Techniques like bronze casting have been used for centuries to produce iconic works of art that stand the test of time. The process involves creating a mold from a master model, which is then filled with molten metal to replicate the original design. This method enables artists to achieve high levels of detail and precision that would be difficult or impossible to attain through other sculpting methods. The purpose of casting extends beyond mere replication; it also offers significant advantages in terms of cost, efficiency, and material properties. In industrial settings, casting can reduce production costs by minimizing the need for subsequent machining operations. Additionally, casting allows for the use of a wide range of materials, each with its own unique properties such as strength, durability, and resistance to corrosion. This versatility makes casting an indispensable tool across various sectors, from aerospace to medical devices. Moreover, casting enables the creation of parts with internal cavities or hollow sections that would be challenging to produce using other manufacturing techniques. This capability is particularly valuable in industries where weight reduction is critical, such as in aerospace engineering where lighter components can significantly improve fuel efficiency and overall performance. Understanding the basics of casting is essential for anyone involved in these fields because it underpins the production processes that drive innovation and efficiency. By grasping the principles of mold design, material selection, and casting techniques, professionals can optimize their workflows, enhance product quality, and push the boundaries of what is possible. Whether in manufacturing complex machinery parts or crafting exquisite works of art, the art and science of casting play a pivotal role in transforming raw materials into functional or aesthetic masterpieces. In summary, casting is a multifaceted process that serves as a cornerstone in diverse industries by enabling the precise creation of complex shapes and forms. Its purpose is not only to replicate designs but also to leverage material properties and manufacturing efficiencies that are unparalleled by other production methods. As technology continues to evolve, the importance of casting will only grow, making it an essential skill set for anyone seeking to excel in fields where precision, innovation, and quality are paramount.
Types of Casting Processes
Casting, a fundamental process in manufacturing, involves shaping molten material into desired forms. There are several types of casting processes, each with its unique characteristics and applications. **Sand Casting** is one of the oldest and most widely used methods, where molten metal is poured into a mold made of sand. This process is versatile and can produce complex shapes, making it ideal for large-scale production of parts such as engine blocks and cylinder heads. **Investment Casting**, also known as lost-wax casting, involves creating a wax pattern which is then coated with a refractory material. When the wax is melted out, the resulting cavity is filled with molten metal, producing intricate and precise parts like turbine blades and dental implants. **Die Casting** uses a permanent mold made of metal, allowing for high production rates and excellent surface finish. This method is commonly used for producing components such as gearboxes, engine parts, and consumer electronics. **Continuous Casting** involves continuously pouring molten metal into a mold, which solidifies and is then cut into desired lengths. This process is particularly efficient for producing long, uniform products like steel beams and aluminum rods. **Centrifugal Casting** utilizes centrifugal force to distribute molten metal evenly within a rotating mold, resulting in symmetrical parts such as pipes and tubes. **Squeeze Casting** combines the benefits of die casting and forging by applying high pressure to force molten metal into a mold, enhancing mechanical properties and reducing porosity. This method is often used for producing high-strength components like aircraft parts. **Plaster Casting** involves using a mold made of plaster of Paris, which is suitable for casting non-ferrous metals and alloys. It offers good dimensional accuracy but is generally slower than other methods due to the fragile nature of the mold. **Shell Molding** uses a resin-bonded sand mixture to create a shell-like mold, offering better surface finish compared to traditional sand casting. This process is particularly useful for casting small to medium-sized parts with complex geometries. **Gravity Die Casting**, also known as permanent mold casting, uses a reusable metal mold that relies on gravity to fill the mold cavity. It is known for producing parts with good dimensional accuracy and surface finish, making it suitable for automotive and aerospace applications. Each type of casting process has its own set of advantages and limitations, making them suitable for different materials, part complexities, and production volumes. Understanding these various techniques is crucial for selecting the most appropriate method based on specific manufacturing requirements, ensuring optimal quality and efficiency in the production of cast parts. By leveraging the unique benefits of each casting process, manufacturers can achieve high precision, durability, and cost-effectiveness in their products.
Historical Development of Casting Techniques
The historical development of casting techniques is a rich and evolving narrative that spans thousands of years, reflecting human ingenuity and the quest for precision in metalworking. The earliest evidence of casting dates back to around 3200 BCE, during the Bronze Age, where archaeologists have discovered cast bronze artifacts in ancient civilizations such as the Indus Valley and Mesopotamia. These early castings were typically made using the lost-wax method, also known as investment casting, where a wax model was encased in clay and then melted out to create a mold into which molten metal was poured. As civilizations advanced, so did the sophistication of casting techniques. In ancient Egypt around 2000 BCE, craftsmen developed more intricate methods for casting gold and bronze, often using sand molds to produce detailed sculptures and jewelry. The ancient Greeks further refined these techniques, employing them to create iconic works of art such as statues and coins. The Romans expanded upon these methods, introducing new alloys and improving furnace designs to achieve higher temperatures necessary for casting iron. The Middle Ages saw a decline in casting technology due to the loss of knowledge from ancient times, but the Renaissance period brought about a resurgence. During this time, artists like Benvenuto Cellini perfected the art of bronze casting, producing masterpieces that showcased exceptional skill and detail. The Industrial Revolution marked a significant turning point with the introduction of new materials and machinery. The development of the cupola furnace in the late 18th century allowed for mass production of cast iron, revolutionizing industries such as construction and manufacturing. In the 20th century, advancements in materials science led to the development of new casting techniques. The introduction of aluminum alloys expanded the range of applications for castings, while the invention of die casting enabled the production of complex shapes with high precision and speed. Modern casting techniques also include sand casting, investment casting, and continuous casting, each tailored to specific needs and materials. Today, casting techniques are more advanced than ever before. Computer-aided design (CAD) and 3D printing technologies have transformed the field by allowing for rapid prototyping and highly accurate mold creation. Additionally, advancements in materials such as titanium alloys and composites have opened up new possibilities for aerospace and medical applications. The integration of automation and robotics has further increased efficiency and reduced costs in mass production settings. Understanding these historical developments is crucial for appreciating the complexity and versatility of modern casting techniques. From ancient civilizations to contemporary industries, the evolution of casting has been driven by human innovation and the relentless pursuit of precision and quality. This rich history underpins our current capabilities in metalworking, enabling us to produce everything from intricate jewelry to critical components for advanced technologies. By grasping these foundational principles, we can better appreciate the art and science behind casting and its indispensable role in shaping our world.
The Casting Process: From Design to Completion
The casting process is a multifaceted and intricate journey that transforms raw materials into precise, functional, and aesthetically pleasing products. This complex procedure involves several critical stages, each contributing to the final outcome. The journey begins with **Design and Pattern Making**, where the initial blueprint of the product is created, laying the foundation for all subsequent steps. Following this, **Mold Preparation and Material Selection** ensures that the right materials are chosen and molds are prepared to accurately replicate the design. Finally, **Pouring, Solidification, and Finishing** bring the product to life through the careful pouring of molten material, its solidification, and the final touches that enhance its quality. Understanding these stages is essential for appreciating the craftsmanship and technology involved in casting. By delving into each of these phases, we can gain a deeper insight into how designs are transformed into tangible, high-quality products. Let's start by exploring the initial stage: **Design and Pattern Making**.
Design and Pattern Making
In the intricate journey of the casting process, design and pattern making serve as the foundational pillars that bridge the conceptual phase with the tangible reality of a finished product. This critical stage involves translating an idea into a detailed blueprint, ensuring that every aspect of the design is meticulously considered and executed. Design begins with sketching and prototyping, where artists and engineers collaborate to visualize the final product. This initial step is crucial as it sets the tone for all subsequent processes, including material selection, structural integrity, and aesthetic appeal. Once the design is finalized, pattern making takes over. Pattern making involves creating a precise template or model of the desired shape and form. This can be done using traditional methods such as hand-drawn patterns or modern technologies like computer-aided design (CAD) software. CAD systems offer unparalleled accuracy and flexibility, allowing for rapid iterations and simulations that can significantly reduce production time and costs. The patterns created during this phase are then used to generate molds or dies, which are essential for casting. These molds must be highly accurate to ensure that the cast product meets the required specifications. The material used for pattern making can vary depending on the intended application; for instance, wood, metal, or even 3D printed materials may be employed. A key aspect of pattern making is considering the shrinkage factor of the material being cast. Different materials shrink at varying rates as they cool, so patterns must be designed with this in mind to achieve the desired dimensions in the finished product. Additionally, allowances for draft angles and parting lines are made to facilitate easy removal from the mold after casting. The interplay between design and pattern making is symbiotic; each informs and enhances the other. Effective communication between designers, pattern makers, and casting engineers is vital to ensure that all elements align seamlessly. This collaborative effort ensures that the final product not only meets but exceeds expectations in terms of quality, functionality, and aesthetics. In summary, design and pattern making are indispensable components of the casting process. They transform abstract ideas into concrete realities through meticulous planning, precise execution, and innovative use of technology. By combining artistic vision with technical expertise, these stages lay the groundwork for successful casting outcomes that are both functional and visually appealing. As such, they play a pivotal role in transforming raw materials into finished products that meet or exceed industry standards.
Mold Preparation and Material Selection
In the intricate process of casting, mold preparation and material selection are crucial steps that significantly influence the final product's quality and integrity. The casting process, which transforms raw materials into precise, detailed shapes, relies heavily on the meticulous preparation of molds and the judicious selection of materials. Mold preparation begins with designing and creating the mold itself. This involves several key considerations: the type of casting process (such as sand casting, die casting, or investment casting), the desired shape and dimensions of the final product, and the properties required for the mold material. For instance, in sand casting, molds are typically made from compacted sand mixed with binders to enhance strength and durability. In contrast, die casting uses metal molds (dies) that can withstand high pressures and temperatures. The mold's surface finish and dimensional accuracy are also critical as they directly impact the quality of the cast part. Material selection is another vital aspect of mold preparation. The choice of mold material must align with the specific casting process and the properties of the metal or alloy being cast. For example, in investment casting, a refractory material like silica or zirconia is often used because it can withstand high temperatures without deforming or reacting with the molten metal. In addition to the mold material, the selection of core materials is equally important. Cores are used to create internal cavities within the cast part and must be made from materials that can be easily removed after casting without damaging the part. The properties of the mold material also play a significant role in determining the casting's surface finish and dimensional accuracy. For instance, molds made from high-strength materials can produce parts with finer details and smoother surfaces. Moreover, the thermal conductivity of the mold material affects how evenly heat is dissipated during solidification, which in turn influences the microstructure and mechanical properties of the cast part. Furthermore, considerations such as cost, availability, and environmental impact are essential in material selection. Different mold materials vary significantly in cost; for example, metal dies are more expensive than sand molds but offer longer lifetimes and higher precision. Similarly, some materials may have environmental or health implications that need to be addressed. In summary, mold preparation and material selection are foundational elements in the casting process. By carefully designing and selecting appropriate mold materials and considering factors such as process type, desired properties, cost, and environmental impact, manufacturers can ensure that their cast parts meet stringent quality standards and perform optimally in their intended applications. This attention to detail at the outset of the casting process sets the stage for successful production from design to completion.
Pouring, Solidification, and Finishing
In the intricate journey of the casting process, the stages of pouring, solidification, and finishing are pivotal in transforming raw materials into a final, functional product. **Pouring** marks the beginning of this critical phase, where molten metal is carefully introduced into a mold that has been meticulously prepared to capture the desired shape and details. The pouring technique must be precise to avoid defects such as porosity or inclusions, which can compromise the structural integrity of the cast part. This step requires careful control over temperature, flow rate, and mold design to ensure that the molten metal fills the mold cavity uniformly. As the molten metal cools and undergoes **solidification**, it transforms from a liquid state into a solid. This process is highly dependent on factors such as the type of metal being cast, the mold material, and the cooling rate. Proper solidification is crucial for achieving the desired microstructure and mechanical properties of the cast part. For instance, rapid cooling can result in a finer grain structure, while slower cooling may lead to coarser grains. The solidification process also involves shrinkage, which must be accounted for in the mold design to prevent defects like shrinkage cavities. Once solidification is complete, the cast part undergoes **finishing** to remove any imperfections and achieve the required surface finish. This stage involves several steps, including cleaning to remove any residual sand or debris from the mold, deburring to eliminate sharp edges, and machining to refine dimensions and surface quality. Additional treatments such as heat treatment or surface coating may also be applied to enhance the mechanical properties or corrosion resistance of the cast part. The finishing process is tailored to meet specific application requirements, ensuring that the final product meets stringent quality standards and is ready for use in various industries ranging from automotive to aerospace. Throughout these stages, quality control measures are essential to ensure that the cast part meets specifications. Inspections are conducted at various points to detect any defects or irregularities, allowing for prompt corrective actions. Advanced technologies such as computer-aided design (CAD) and computer-aided manufacturing (CAM) are increasingly being integrated into these processes to enhance precision and efficiency. By meticulously managing each step from pouring through solidification to finishing, manufacturers can produce high-quality castings that are reliable, durable, and meet the exacting demands of modern engineering applications. This attention to detail underscores the complexity and sophistication of the casting process, transforming raw materials into precision-engineered components that form the backbone of modern industry.
Applications and Industries Utilizing Casting
Casting, a versatile and ancient manufacturing technique, has evolved to play a crucial role in various industries, each leveraging its unique benefits to produce high-quality, precision components. This article delves into the diverse applications of casting, highlighting its significance in three key sectors: Automotive and Aerospace Industries, Medical and Dental Applications, and Artistic and Architectural Uses. In the automotive and aerospace industries, casting enables the production of complex engine parts, aircraft components, and other critical structural elements that require precision and durability. The medical and dental fields benefit from casting's ability to create intricate instruments and implants with exacting standards. Meanwhile, artistic and architectural endeavors utilize casting to bring creative visions to life, from sculptures to ornate building features. By exploring these applications, we gain insight into how casting continues to innovate and support modern industries. Let us begin by examining the pivotal role casting plays in the Automotive and Aerospace Industries.
Automotive and Aerospace Industries
The automotive and aerospace industries are pivotal sectors that heavily rely on casting processes to produce critical components. In the automotive industry, casting is essential for manufacturing engine blocks, cylinder heads, crankshafts, and gearboxes. These components require high strength, durability, and precision to ensure the reliability and performance of vehicles. For instance, aluminum alloy castings are widely used in engine blocks and cylinder heads due to their lightweight properties and excellent thermal conductivity, which enhance fuel efficiency and reduce emissions. Additionally, iron castings are utilized for engine blocks and crankshafts because of their high strength-to-weight ratio and resistance to wear and tear. The precision and complexity of these castings are crucial for maintaining the integrity and efficiency of modern vehicles. In the aerospace industry, casting plays a vital role in producing components that must withstand extreme conditions such as high temperatures, stresses, and corrosive environments. Titanium alloys are frequently cast for aerospace applications due to their exceptional strength-to-weight ratio, corrosion resistance, and ability to maintain structural integrity at high temperatures. Components like turbine blades, engine components, and structural parts are cast using advanced techniques such as investment casting or sand casting. These processes allow for the creation of intricate geometries and complex shapes that are necessary for the performance and safety of aircraft and spacecraft. Furthermore, the use of advanced materials like superalloys in casting enables the production of parts that can operate in extreme conditions without compromising on performance or safety. Both industries also benefit from advancements in casting technologies such as 3D printing (additive manufacturing) and simulation software. These tools enable the design and production of complex geometries that were previously impossible to achieve with traditional casting methods. This not only improves the efficiency of production but also enhances the performance characteristics of the final products. For example, 3D printing allows for the creation of lightweight structures with internal cavities that cannot be produced through conventional methods, leading to significant weight reductions in aerospace applications. Moreover, the integration of casting with other manufacturing processes like machining and surface treatment further enhances the quality and functionality of automotive and aerospace components. Post-casting treatments such as heat treatment and surface coating can improve the mechanical properties and resistance to wear and corrosion of these components. This holistic approach ensures that cast parts meet stringent industry standards while contributing to overall system efficiency. In summary, casting is a cornerstone technology in both the automotive and aerospace industries, enabling the production of high-performance components that are critical to vehicle and aircraft safety, efficiency, and reliability. The versatility of casting processes combined with advancements in materials science and manufacturing technologies continues to drive innovation in these sectors, ensuring that they remain at the forefront of technological advancement.
Medical and Dental Applications
Casting plays a pivotal role in the medical and dental industries, where precision, durability, and biocompatibility are paramount. In medical applications, casting techniques are used to produce a wide range of critical components, from surgical instruments to implantable devices. For instance, orthopedic implants such as hip and knee replacements are often cast from titanium alloys due to their strength, corrosion resistance, and compatibility with human tissue. These implants must be crafted with exacting precision to ensure proper fit and function, making casting an ideal method for their production. Additionally, casting is employed in the manufacture of surgical tools like forceps, scalpels, and retractors, which require high strength and resistance to wear and tear. In dental applications, casting is equally essential. Dental restorations such as crowns, bridges, and dentures are frequently produced using casting techniques. These restorations are typically made from gold alloys or other biocompatible materials that can withstand the harsh environment of the mouth while maintaining their shape and function. The process involves creating a precise mold of the patient's teeth, which is then used to cast the final restoration. This method ensures a snug fit and natural appearance, enhancing patient comfort and satisfaction. Furthermore, casting is used in the production of dental implants, which involve anchoring artificial teeth into the jawbone. The precision required for these implants makes casting an indispensable tool in modern dentistry. The use of advanced casting techniques such as investment casting and 3D printing has further revolutionized medical and dental manufacturing. Investment casting allows for the creation of intricate shapes with high accuracy, which is particularly beneficial for producing complex medical devices like stents and pacemaker components. On the other hand, 3D printing enables rapid prototyping and production of customized implants and dental restorations, significantly reducing turnaround times and improving patient outcomes. Moreover, the materials used in medical and dental casting are subject to stringent regulatory standards to ensure safety and efficacy. For example, materials must be non-toxic and hypoallergenic to prevent adverse reactions in patients. This necessitates careful selection of alloys and other materials that meet these criteria while also providing the necessary mechanical properties. In summary, casting is a critical technology in the medical and dental fields, enabling the production of precise, durable, and biocompatible devices that improve patient care and outcomes. Its versatility in creating complex shapes with high accuracy makes it an indispensable tool for both industries, driving innovation and excellence in healthcare.
Artistic and Architectural Uses
Casting, a versatile and ancient technique, has been a cornerstone in both artistic and architectural endeavors for centuries. Its applications in these fields are as diverse as they are impressive, showcasing the medium's ability to transform raw materials into intricate, durable, and aesthetically pleasing creations. In the realm of art, casting allows artists to bring their visions to life with precision and detail. Sculptors, for instance, use casting to create complex three-dimensional pieces that can range from delicate figurines to monumental installations. Techniques such as bronze casting, known for its durability and expressive qualities, have been favored by artists like Auguste Rodin and Michelangelo. The process involves creating a mold from which the final piece is cast, allowing for multiple iterations and variations of the same design. This flexibility has made casting a preferred method for producing limited edition art pieces and replicas of historical works. In architecture, casting plays a crucial role in the creation of structural elements and decorative features. Cast iron, with its strength and malleability, was a key material during the Industrial Revolution, enabling the construction of grand buildings like the Crystal Palace in London and the Eiffel Tower in Paris. Today, architects continue to utilize casting for producing custom architectural details such as ornate railings, intricate facades, and ornamental fixtures. The use of advanced materials like aluminum and stainless steel has further expanded the possibilities of architectural casting, allowing for lighter yet stronger structures that can withstand various environmental conditions. Additionally, modern casting techniques such as 3D printing have opened up new avenues for innovative architectural designs that were previously impossible to achieve through traditional methods. The synergy between art and architecture is particularly evident in historical landmarks where casting has been used to create both functional and decorative elements. For example, Gothic cathedrals feature intricate stone carvings that were often cast in place to achieve the desired level of detail and precision. Similarly, in contemporary urban design, public art installations frequently incorporate cast elements that blend seamlessly into their surroundings while adding a touch of elegance and character to public spaces. Moreover, the preservation of cultural heritage relies heavily on casting techniques. Restoration projects often involve creating exact replicas of damaged or missing parts using original molds or reverse-engineered designs. This ensures that historical buildings maintain their authenticity while ensuring structural integrity. The use of advanced casting materials also allows for the creation of durable replicas that can withstand harsh weather conditions without compromising on aesthetic appeal. In summary, casting's artistic and architectural applications are multifaceted and profound. From enabling artists to create intricate sculptures to facilitating the construction of iconic buildings and preserving historical landmarks, casting continues to be an indispensable tool across various creative and functional disciplines. Its ability to marry form with function makes it an enduring medium that will continue to shape our cultural landscape for generations to come.