What Is Interfacing In Sewing

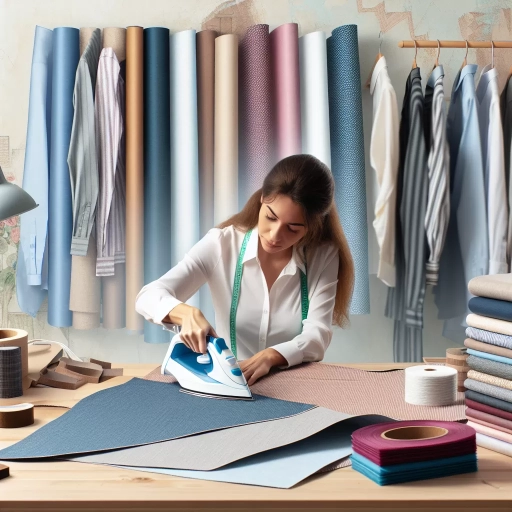
Interfacing is a crucial component in sewing, often overlooked but essential for achieving professional-grade results. It provides stability, structure, and sometimes even additional texture to your fabric, making it indispensable for various sewing projects. To fully appreciate the role of interfacing, it's important to understand its basics, including what it is, how it works, and why it's necessary. This article will delve into the fundamentals of interfacing, guiding you through the process of choosing the right type for your specific project. Additionally, it will cover techniques for applying interfacing effectively to ensure your finished product looks and feels its best. By grasping these key aspects, you'll be well-equipped to enhance your sewing skills and create high-quality garments and crafts. Let's start by understanding the basics of interfacing in sewing.
Understanding the Basics of Interfacing in Sewing
Understanding the basics of interfacing in sewing is crucial for any sewer looking to enhance the quality and durability of their garments. Interfacing, a layer of fabric placed between two other layers, serves multiple purposes that are essential for garment construction. This article will delve into three key aspects: the definition and purpose of interfacing, the various types of interfacing materials available, and their common uses in garment construction. By grasping these fundamentals, sewers can ensure their projects have the necessary stability, structure, and finish. Starting with the definition and purpose of interfacing, we will explore how it provides support and shape to fabrics, making it an indispensable tool in sewing. This foundational understanding will set the stage for a deeper look into the diverse types of interfacing materials and their specific applications, ultimately guiding readers to make informed choices in their sewing projects. Let's begin by examining the definition and purpose of interfacing.
Definition and Purpose of Interfacing
Interfacing in sewing is a crucial component that serves to enhance the stability, structure, and durability of various fabric projects. **Definition:** Interfacing is a layer of fabric, usually made from cotton, polyester, or a blend, that is placed between two layers of fabric to provide additional support and stability. It can be fusible (adheres to fabric with heat) or sew-in (requires stitching to secure). **Purpose:** The primary purpose of interfacing is to add body and shape to fabrics that are too thin or flimsy to hold their form on their own. This is particularly important for items like collars, waistbands, and buttonholes, where structural integrity is essential. Interfacing helps maintain the shape of these elements over time, preventing them from stretching or sagging. It also provides a smooth surface for sewing, making it easier to work with delicate or slippery fabrics. In addition to structural support, interfacing can improve the overall appearance of a garment by giving it a more polished finish. For instance, in bag-making, interfacing helps keep the bag's shape and prevents it from becoming misshapen when filled with items. In home decor projects like quilting and upholstery, interfacing can add stability to the fabric, ensuring that it does not pucker or distort during the sewing process. Moreover, interfacing can be used to add weight and texture to fabrics, which is beneficial for creating dimensional effects in crafts such as appliqué or embroidery. It also helps in reducing fraying and stretching at seams, thereby extending the lifespan of the finished product. Understanding the basics of interfacing is fundamental for any sewer because it allows them to choose the right type of interfacing for their specific project needs. By selecting an appropriate interfacing material—whether it's lightweight for delicate fabrics or heavy-duty for robust projects—sewers can ensure that their creations maintain their intended shape and functionality over time. This knowledge empowers them to produce high-quality, professional-looking results that stand up to wear and tear. In summary, interfacing is an indispensable tool in sewing that enhances both the functionality and aesthetics of various fabric projects by providing necessary support and stability.
Types of Interfacing Materials
Interfacing materials are crucial components in sewing, providing stability, structure, and shape to various garments and crafts. There are several types of interfacing materials, each designed for specific applications and fabric types. **Fusible Interfacing** is one of the most common types, featuring a heat-activated adhesive on one side that allows it to be ironed onto the fabric. This type is ideal for projects like collars, waistbands, and bag linings where a strong bond is needed. **Sew-in Interfacing**, on the other hand, does not have an adhesive and must be sewn into place. It is often preferred for more durable projects or when a permanent bond is not desired. **Knit Interfacing** is specifically designed for stretchy fabrics such as knits and spandex blends. It maintains the flexibility of the fabric while providing necessary support. **Woven Interfacing** is suitable for woven fabrics like cotton, linen, and silk. It comes in various weights and is commonly used in garments such as jackets, pants, and skirts. **Non-woven Interfacing** is made from fibers that are bonded together using heat, moisture, or chemicals rather than being woven or knitted. This type is lightweight and easy to work with but may lack the durability of woven or knit interfacings. **Stabilizer Interfacing** serves a different purpose; it provides temporary support during the sewing process rather than permanent structure. It is often used in quilting, embroidery, and other precision sewing tasks where fabric stability is crucial but the interfacing will be removed after completion. **Water-soluble Interfacing** dissolves in water and is used primarily in appliqué and other decorative techniques where the interfacing needs to be easily removable. **Specialty Interfacings** include options like **Fusible Web**, which is used for appliqué and quilting; **Shirt Interfacing**, designed specifically for collars and cuffs; and **Tailor's Interfacing**, a heavier weight interfacing used in tailoring for jackets and coats. Each type of interfacing material has its unique characteristics and applications, making it essential for sewists to choose the right one based on their project requirements to achieve professional-looking results. Understanding these different types of interfacing materials is key to mastering the basics of interfacing in sewing.
Common Uses in Garment Construction
In garment construction, interfacing plays a crucial role in enhancing the stability, shape, and durability of various components. It is commonly used to support and stabilize areas that need extra structure, such as collars, waistbands, buttonholes, and pockets. For collars, interfacing helps maintain their shape and prevents them from sagging or losing their form over time. In waistbands, it provides additional stability and prevents stretching or distortion, ensuring a consistent fit. When creating buttonholes, interfacing reinforces the fabric around the holes to prevent fraying and tearing. Pockets also benefit from interfacing as it gives them a more defined shape and prevents the fabric from stretching excessively. Interfacing is also essential for stabilizing seams in areas subject to high stress, like shoulder seams or side seams in garments that require extra support. It can be used to add body to lightweight fabrics, making them more suitable for structured garments such as jackets or coats. Additionally, interfacing can be used to create crisp folds in items like cuffs or hemlines, ensuring a professional finish. In the construction of bags and accessories, interfacing is vital for providing the necessary rigidity and shape retention. Furthermore, different types of interfacing cater to various fabric types and garment needs. Fusible interfacing is convenient for beginners as it adheres to the fabric with heat and pressure, while sew-in interfacing requires sewing but offers more flexibility in terms of fabric choice and durability. Knit interfacing is ideal for stretchy fabrics like knits, ensuring that the garment retains its elasticity while still providing support. Overall, understanding the appropriate use of interfacing in garment construction is fundamental for achieving professional results and ensuring that garments maintain their shape and integrity over time. By selecting the right type of interfacing for each component of a garment, sewists can enhance both the functionality and aesthetic appeal of their creations. This knowledge is particularly important for those looking to elevate their sewing skills beyond basic projects and into more complex and structured garments.
Choosing the Right Interfacing for Your Project
When embarking on a sewing or crafting project, selecting the right interfacing is crucial for achieving the desired texture, stability, and overall quality of the final product. Interfacing serves as a hidden layer between the fabric and the outer surface, providing structure and support that can make or break the success of your project. To ensure you choose the correct interfacing, it is essential to consider several key factors. First, you must match the interfacing to the type of fabric you are using, as different fabrics require different types of interfacing to achieve optimal results. Additionally, the weight and stability requirements of your project must be taken into account, as these will dictate the thickness and rigidity of the interfacing needed. By carefully evaluating these aspects, you can make an informed decision that enhances your project's durability and aesthetic appeal. Let's delve into the first critical step: **Factors to Consider When Selecting Interfacing**.
Factors to Consider When Selecting Interfacing
When selecting interfacing for your sewing project, several key factors must be considered to ensure the best results. **Fabric Type** is crucial; different fabrics require different types of interfacing. For example, delicate fabrics like silk or cotton voile need lightweight, fusible interfacings to avoid bulk and distortion, while heavier fabrics such as denim or canvas can handle thicker, more robust interfacings. **Project Purpose** also plays a significant role; if you're making a structured item like a bag or a jacket, you'll need interfacing that provides stability and shape retention, whereas for garments that require drape, such as dresses or blouses, a lighter interfacing is more appropriate. **Weight and Thickness** of the interfacing are vital considerations. Thicker interfacings offer more stability but can add bulk, while thinner ones provide less structure but are more flexible. **Fusible vs. Non-Fusible** is another important decision; fusible interfacings have a heat-activated adhesive and are easier to apply but may not be suitable for all fabrics or projects, whereas non-fusible interfacings require sewing in place and offer more versatility. **Stretch and Recovery** are essential for projects that need flexibility, such as knit garments or activewear. Interfacings with stretch properties will help maintain the fabric's natural movement without restricting it. **Care Instructions** should also be taken into account; some interfacings may not be machine washable or dryable, which could limit their use in certain projects. Additionally, **Color and Texture** can affect the appearance of your finished project. Matching the color of the interfacing to the fabric can help it blend in, especially if it will be visible from the outside. Texture-wise, smooth interfacings work well with smooth fabrics, while textured interfacings can complement more rugged or patterned fabrics. Lastly, **Brand and Quality** should not be overlooked. High-quality interfacings from reputable brands tend to perform better and last longer than cheaper alternatives. They often have better adhesion, stability, and durability, making them worth the investment for professional-looking results. By carefully considering these factors—fabric type, project purpose, weight and thickness, fusible vs. non-fusible, stretch and recovery, care instructions, color and texture, and brand and quality—you can choose the right interfacing for your project, ensuring it turns out as intended with the desired look and functionality.
Matching Interfacing to Fabric Types
When selecting the right interfacing for your sewing project, it is crucial to match the interfacing type to the fabric you are using. Different fabrics have unique properties such as weight, drape, and texture, and choosing an interfacing that complements these characteristics ensures a professional finish and optimal performance. For lightweight fabrics like cotton lawn, voile, or silk, a lightweight interfacing such as fusible cotton or silk interfacing is ideal. These interfacings add stability without overwhelming the delicate fabric. For medium-weight fabrics like quilting cotton, linen, or denim, a medium-weight interfacing is appropriate. Fusible cotton interfacing or woven interfacing works well here, providing the necessary structure without adding too much bulk. Heavyweight fabrics such as canvas, burlap, or thick denim require a more robust interfacing. Here, you can use a heavier fusible interfacing or even a stabilizer like Pellon Peltex, which offers substantial support and stability. Stretchy fabrics like knits and spandex blends demand a specialized interfacing that accommodates their elasticity. Knit interfacing or stretch fusible interfacing is designed to move with the fabric, preventing distortion and maintaining the garment's shape. For projects requiring additional structure and stability, such as bags or home decor items, interfacing options like ByAnnie's Soft and Stable or Bosal In-R-Form can be used. These interfacings provide excellent support while maintaining a soft, pliable feel. In addition to fabric weight and stretch, consider the intended use of your project. For instance, if you're making a garment that will be subject to heavy wear or frequent washing, choose an interfacing that is durable and resistant to shrinkage. Similarly, if you're working on a project that requires a crisp finish, such as collars or waistbands, opt for a fusible interfacing that can be easily pressed into place. Ultimately, matching the right interfacing to your fabric type ensures that your project turns out as intended—stable, durable, and visually appealing. By understanding the different types of interfacings available and their specific uses, you can enhance your sewing skills and achieve professional results in all your projects. Whether you're a beginner or an experienced sewer, selecting the correct interfacing is a critical step in ensuring that your finished product meets your expectations.
Weight and Stability Requirements
When choosing the right interfacing for your sewing project, it is crucial to consider the weight and stability requirements of the fabric and the intended use of the final product. Interfacing serves as a layer between the fabric and the lining or backing, providing structure, stability, and sometimes additional texture or support. The weight of the interfacing should be compatible with the weight of your fabric to ensure that it does not overwhelm or distort it. For example, lightweight fabrics such as silk or cotton voile require lightweight interfacing to maintain their drape and flexibility, while heavier fabrics like denim or canvas can handle heavier interfacing for added stability. Stability is another key factor; projects that need to hold their shape, such as collars, waistbands, or home decor items like table runners and placemats, require interfacing with high stability. Fusible interfacing is often preferred for these applications because it adheres well to the fabric and provides consistent support. On the other hand, projects that require flexibility and movement, such as garments with sleeves or skirts, may benefit from non-fusible interfacing which allows for more give without compromising the overall structure. The type of interfacing also depends on the desired finish and functionality of the project. For instance, if you are making a bag or purse that needs to stand upright and maintain its shape, a heavier interfacing like canvas or buckram would be appropriate. Conversely, if you are working on a delicate blouse that requires minimal support but needs some stability around buttonholes or seams, a lightweight fusible interfacing would be more suitable. Additionally, consider the care instructions for your project when selecting an interfacing. Some interfacings are designed to be washable and dryable while others may not withstand machine washing or drying. Ensuring that your interfacing choice aligns with how you intend to care for the finished product is essential for its longevity. In summary, selecting the right interfacing involves a careful balance of weight and stability tailored to your specific project needs. By understanding these requirements and choosing an appropriate interfacing type—whether fusible or non-fusible—you can ensure that your finished project maintains its intended shape, structure, and functionality while also meeting your aesthetic and practical goals. This thoughtful approach will enhance the overall quality and durability of your sewing projects.
Techniques for Applying Interfacing Effectively
When it comes to enhancing the structure and stability of your sewing projects, interfacing is a crucial component. However, its effectiveness depends on several key techniques. To apply interfacing successfully, you must first understand the importance of proper preparation and cutting. This involves selecting the right type of interfacing for your fabric, accurately measuring and cutting it to fit your pattern pieces, and ensuring it is aligned correctly. Once you have prepared your interfacing, you need to know the best methods for attaching it to your fabric, whether that involves fusing, sewing, or using a combination of both. Finally, being aware of common mistakes and how to avoid them can save you time and frustration. By mastering these techniques—preparation and cutting of interfacing, methods for attaching interfacing to fabric, and tips for avoiding common mistakes—you can achieve professional results in your sewing projects. Let's start by diving into the critical step of preparation and cutting of interfacing.
Preparation and Cutting of Interfacing
When it comes to the preparation and cutting of interfacing, precision and attention to detail are crucial for achieving professional results in your sewing projects. Interfacing is a layer of fabric that is fused or sewn between two layers of fabric to add stability, shape, and structure. Here’s how you can prepare and cut interfacing effectively: 1. **Choose the Right Interfacing**: Select an interfacing that matches the weight and type of your main fabric. There are various types, including fusible, sew-in, and knit interfacing, each suited for different applications. 2. **Read Instructions**: Always read the manufacturer's instructions on the interfacing package. Some interfacings have specific requirements for temperature, steam, and pressure when fusing. 3. **Pre-wash Your Fabric**: If you're using a sew-in interfacing or if your main fabric is prone to shrinkage, pre-wash both the fabric and the interfacing to ensure they shrink equally. 4. **Cut Accurately**: Use your pattern pieces to cut out the interfacing. For fusible interfacings, cut on the wrong side of the interfacing to avoid any adhesive residue on your cutting tools or work surface. 5. **Match Grain Lines**: Ensure that the grain lines of your interfacing align with those of your main fabric. This prevents distortion and ensures stability in your finished project. 6. **Cut Seam Allowances**: If you're using a sew-in interfacing, cut it slightly smaller than your main fabric pieces to avoid bulk in seams. For fusible interfacings, cut it exactly to size or slightly larger if necessary. 7. **Label Pieces**: Label each piece of interfacing with its corresponding pattern piece number or description to avoid confusion during assembly. 8. **Fusible Application Tips**: When applying fusible interfacing, place it on the wrong side of your fabric with the adhesive side down. Use a hot iron with steam (if recommended) and apply gentle pressure, moving the iron slowly over the area to ensure even bonding. By following these steps meticulously, you can ensure that your interfacing is prepared and cut correctly, which is essential for applying it effectively and achieving a professional finish in your sewing projects. Proper preparation sets the stage for successful application and enhances the overall quality of your work.
Methods for Attaching Interfacing to Fabric
When it comes to attaching interfacing to fabric, several methods can ensure a secure and professional finish. The choice of method often depends on the type of interfacing and fabric being used, as well as the desired outcome. **Fusible Interfacing** is one of the most common types and is attached using heat and pressure. To apply fusible interfacing, start by placing the interfacing with its fusible side down onto the wrong side of your fabric. Use a hot iron set to the appropriate temperature for your fabric type, applying gentle to moderate pressure while moving the iron slowly over the area. It is crucial to follow the manufacturer's instructions for temperature and time to avoid damaging either the interfacing or the fabric. For **Non-Fusible Interfacing**, which does not have a heat-activated adhesive, you will need to use a sewing method. This can be done by basting the interfacing to the fabric using a simple running stitch or by using a serger to attach it. Another effective technique is to use a walking foot or Teflon foot on your sewing machine, which helps guide the fabric smoothly and prevents bunching. When sewing non-fusible interfacing, it is important to match the grain lines of both the interfacing and fabric to maintain stability and prevent distortion. **Adhesive-Backed Interfacing** offers a hybrid approach, combining elements of both fusible and non-fusible methods. These interfacings have a light adhesive that allows for temporary placement before being sewn in place. This method is particularly useful for projects where precision is key, such as in bag making or home decor items. Simply peel off the backing paper and place the interfacing on your fabric, smoothing out any air bubbles before sewing along the edges. Regardless of the method chosen, it is essential to pre-wash and dry both your fabric and interfacing if they are prone to shrinkage. This step ensures that any shrinkage occurs before the interfacing is attached, preventing unwanted distortions in your final project. Additionally, always read and follow the specific instructions provided by the manufacturer for each type of interfacing, as different brands may have unique application requirements. In summary, attaching interfacing to fabric involves selecting the appropriate method based on the type of interfacing and fabric in use. Whether using heat for fusible interfacings, sewing for non-fusible ones, or a combination approach for adhesive-backed interfacings, careful attention to detail and adherence to manufacturer guidelines are key to achieving a professional and durable finish. By mastering these techniques, you can effectively apply interfacing to enhance the stability, shape, and overall quality of your sewing projects.
Tips for Avoiding Common Mistakes
When applying interfacing effectively in sewing, it is crucial to avoid common mistakes that can compromise the quality and durability of your project. Here are some key tips to help you steer clear of these pitfalls: 1. **Choose the Right Interfacing**: Select an interfacing that matches the weight and type of fabric you are using. For instance, use a lightweight interfacing for delicate fabrics and a heavier one for thicker materials. This ensures that the interfacing does not overpower or distort the fabric. 2. **Follow Manufacturer Instructions**: Always read and follow the manufacturer's instructions for the specific interfacing you are using. Different interfacings may have unique application methods, such as fusible or sew-in types, which require different handling. 3. **Pre-wash Your Fabric**: Pre-washing your fabric before applying interfacing can help prevent shrinkage issues later on. This step ensures that any shrinkage occurs before the interfacing is applied, maintaining the integrity of your project. 4. **Cut Accurately**: Cut your interfacing pieces accurately to match your fabric pieces. Inaccurate cutting can lead to misaligned seams and poor fit. Use a rotary cutter and mat for precise cuts. 5. **Apply Even Pressure**: When applying fusible interfacing, use even pressure to avoid bubbles or wrinkles. Use a pressing cloth if necessary to distribute heat evenly and prevent scorching the fabric. 6. **Avoid Over-ironing**: Do not over-iron the interfacing as this can cause it to become brittle or distort the fabric. Follow the recommended ironing time and temperature to ensure a smooth application. 7. **Test on Scrap Fabric**: Always test the interfacing on a scrap piece of fabric before applying it to your actual project. This helps you identify any potential issues with compatibility or application technique. 8. **Use the Correct Grain**: Ensure that both your fabric and interfacing are cut on the correct grain to prevent distortion or stretching during sewing. Cutting off-grain can lead to uneven seams and poor stability in your finished project. 9. **Sew Through Interfacing Carefully**: When sewing through interfaced fabric, use a sharp needle and appropriate thread to avoid breaking threads or damaging the fabric. A walking foot or Teflon foot can also help guide the fabric smoothly under the needle. 10. **Consider Layering Order**: Pay attention to the layering order when working with multiple layers of fabric and interfacing. Typically, place the interfacing between two layers of fabric to ensure it is fully enclosed and does not show on the outside of your finished project. By adhering to these tips, you can avoid common mistakes and ensure that your interfacing is applied effectively, enhancing the stability, structure, and overall quality of your sewing projects.