What Is Cmc

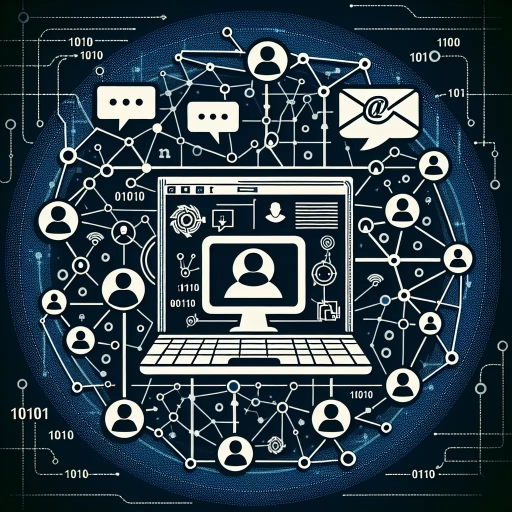
In today's interconnected world, the concept of Critical Micelle Concentration (CMC) plays a pivotal role in various scientific and industrial applications. CMC is a crucial parameter that defines the concentration at which surfactant molecules in a solution begin to form micelles, significantly altering the solution's properties. Understanding CMC is essential for grasping its multifaceted implications. This article delves into the intricacies of CMC, starting with **Understanding the Concept of CMC**, where we explore the fundamental principles and mechanisms behind micelle formation. We then examine **Applications and Uses of CMC**, highlighting how this concept is utilized in diverse fields such as pharmaceuticals, cosmetics, and environmental science. Finally, we discuss **Benefits and Challenges of CMC**, outlining the advantages and potential drawbacks associated with its application. By navigating these aspects, readers will gain a comprehensive insight into the significance and practical relevance of CMC. Let us begin by **Understanding the Concept of CMC**, the foundation upon which all other discussions are built.
Understanding the Concept of CMC
Understanding the Concept of Critical Mass Communication (CMC) is a multifaceted topic that requires a comprehensive exploration of its various dimensions. At its core, CMC involves the study of how communication technologies and media influence social interactions and collective behavior. To delve into this concept effectively, it is essential to examine three key aspects: the definition and origins of CMC, its key components and characteristics, and its historical development and evolution. Firstly, understanding the definition and origins of CMC provides a foundational grasp of the concept. This involves tracing back to the early theories and models that laid the groundwork for modern CMC studies. Secondly, identifying the key components and characteristics helps in recognizing how different elements of communication technology shape our interactions. This includes examining the role of media, networks, and user behaviors. Lastly, exploring the historical development and evolution of CMC reveals how this field has adapted over time, influenced by technological advancements and societal changes. By examining these three facets, readers can gain a holistic understanding of CMC, from its theoretical roots to its practical applications in today's digital age. Let us begin by exploring the definition and origins of CMC, which will set the stage for a deeper dive into its components and historical trajectory.
Definition and Origins
**Understanding the Concept of CMC** ### Definition and Origins The concept of Critical Micelle Concentration (CMC) is a cornerstone in the study of surfactants and their behavior in solutions. At its core, CMC is defined as the concentration of surfactants in a solution at which micelles start to form. Below this concentration, surfactants exist as monomers, but once the CMC is reached, these monomers aggregate into micelles—complex structures composed of hydrophobic tails shielded by hydrophilic heads. This transition marks a significant change in the physical and chemical properties of the solution, such as surface tension, solubility, and conductivity. The origins of CMC can be traced back to early 20th-century research on colloidal solutions. Scientists like McBain and his collaborators in the 1910s began observing that certain substances, now known as surfactants, exhibited unique properties when dissolved in water. These observations led to the realization that these substances could form aggregates or micelles above a certain concentration threshold. The term "micelle" itself was coined by McBain in 1913, derived from the Latin word "mica," meaning crumb or morsel, reflecting the small, particulate nature of these aggregates. Understanding CMC is crucial because it influences various applications across different fields. In pharmaceuticals, knowing the CMC helps in formulating drugs that require solubilization of hydrophobic compounds. In industrial processes, such as cleaning and emulsification, CMC determines the effectiveness and efficiency of surfactant-based products. Moreover, in biological systems, CMC plays a role in membrane structure and function, as well as in drug delivery mechanisms. The measurement of CMC typically involves observing changes in physical properties such as surface tension, conductivity, or light scattering as surfactant concentration increases. These methods provide a quantitative way to determine the exact concentration at which micelle formation begins. The value of CMC varies widely among different surfactants and is influenced by factors such as temperature, pH, and ionic strength of the solution. In summary, the concept of CMC is rooted in early research on colloidal solutions and has evolved into a fundamental principle guiding various scientific and industrial applications. Its definition and measurement are essential for understanding how surfactants behave in solutions and how they can be effectively utilized across diverse fields. As research continues to advance our understanding of micelle formation and behavior, the significance of CMC remains a pivotal aspect in both theoretical and practical contexts.
Key Components and Characteristics
Understanding the concept of Critical Micelle Concentration (CMC) is pivotal in various scientific and industrial contexts, and it hinges on several key components and characteristics. At its core, CMC is the concentration of surfactants in a solution at which micelles start to form. This phenomenon is crucial because it marks a significant change in the physical and chemical properties of the solution. **Key Components:** 1. **Surfactants:** These are amphiphilic molecules, meaning they have both hydrophilic (water-attracting) and hydrophobic (water-repelling) parts. This dual nature allows them to interact with both water and oil, making them essential in processes like emulsification and solubilization. 2. **Micelles:** These are spherical structures formed by surfactant molecules when their concentration exceeds the CMC. In a micelle, the hydrophobic tails of the surfactants cluster together in the center, while the hydrophilic heads face outward, interacting with water. 3. **Solvent:** Typically water, but it can be any polar solvent that allows surfactants to dissolve and form micelles. **Characteristics:** 1. **Concentration Dependency:** The formation of micelles is highly dependent on the concentration of surfactants. Below the CMC, surfactants exist as monomers; above it, they aggregate into micelles. 2. **Thermodynamic Stability:** Micelle formation is a spontaneous process driven by thermodynamic forces. It minimizes the free energy of the system by reducing the contact between hydrophobic tails and water. 3. **Surface Tension Reduction:** Surfactants reduce the surface tension of water, which is a key characteristic that makes them useful in applications such as detergents and emulsifiers. 4. **Solubilization Capacity:** Micelles can solubilize substances that are otherwise insoluble in water by encapsulating them within their hydrophobic core. 5. **Dynamic Equilibrium:** Micelles are in dynamic equilibrium with monomeric surfactants, meaning that surfactant molecules are constantly exchanging between the micellar and monomeric states. **Implications and Applications:** - **Detergency:** Understanding CMC is crucial for developing effective detergents, as it determines the optimal concentration for cleaning. - **Pharmaceuticals:** Micelles can be used as drug delivery vehicles, encapsulating drugs to enhance their solubility and bioavailability. - **Food Industry:** Emulsifiers used in food products rely on the principles of CMC to stabilize mixtures of oil and water. - **Environmental Science:** Surfactants play a role in environmental remediation by solubilizing pollutants, making them easier to remove from contaminated sites. In summary, the concept of CMC is underpinned by the unique properties of surfactants and their ability to form micelles. Understanding these key components and characteristics is essential for leveraging the benefits of surfactants in various applications across different industries.
Historical Development and Evolution
The historical development and evolution of Computer-Mediated Communication (CMC) are deeply intertwined with the advancements in technology and societal needs. The journey began in the 1960s with the inception of the first network, ARPANET, which laid the groundwork for modern-day internet communication. This early form of CMC was primarily used by government and academic institutions for sharing information and resources. As technology progressed, the 1980s saw the rise of Bulletin Board Systems (BBS), allowing users to access and share information via dial-up connections. This marked a significant shift towards more accessible and user-friendly forms of CMC. The advent of the World Wide Web in the 1990s revolutionized CMC, making it more mainstream and accessible to a broader audience. The introduction of email, chat rooms, and online forums enabled real-time communication across geographical boundaries. This period also witnessed the emergence of instant messaging services like ICQ and AOL Instant Messenger, further enhancing real-time interaction capabilities. The early 2000s brought about a new era with the proliferation of social media platforms such as MySpace, Facebook, and Twitter. These platforms transformed CMC by integrating multimedia content, facilitating social networking, and enabling mass communication. The rise of smartphones and mobile internet access in the late 2000s and 2010s further accelerated this trend, making CMC an integral part of daily life. Recent years have seen significant advancements with the integration of artificial intelligence, machine learning, and blockchain technology into CMC. Video conferencing tools like Zoom and Skype have become indispensable for remote work and virtual meetings. Social media platforms continue to evolve with features like live streaming, voice messages, and augmented reality interactions. Additionally, the growth of virtual reality (VR) and augmented reality (AR) technologies promises to redefine the future landscape of CMC by offering immersive communication experiences. Throughout its evolution, CMC has not only reflected technological advancements but also adapted to changing societal needs and behaviors. It has transformed from a tool primarily used by professionals to a ubiquitous medium that permeates all aspects of life. Understanding this historical development is crucial for grasping the concept of CMC fully, as it highlights how technology has continuously reshaped how we communicate, interact, and connect with each other. This understanding also underscores the importance of CMC in modern society, where it plays a pivotal role in facilitating global communication, collaboration, and community building.
Applications and Uses of CMC
Carboxymethyl cellulose (CMC) is a versatile and widely used derivative of cellulose, offering a multitude of applications across various industries. Its unique properties, such as high viscosity, stability, and biocompatibility, make it an indispensable component in industrial and manufacturing processes, medical and pharmaceutical applications, and environmental sustainability roles. In industrial settings, CMC enhances the performance of products by improving their texture, stability, and shelf life. It is commonly used as a thickening agent in food products, a binder in paper production, and a stabilizer in paints and coatings. In the medical and pharmaceutical sectors, CMC serves as an excipient in drug formulations, aiding in the controlled release of active ingredients and improving the bioavailability of medications. Additionally, its role in environmental sustainability is significant, as it is used in wastewater treatment to remove contaminants and in agriculture to improve soil structure and water retention. Understanding these diverse applications of CMC is crucial for optimizing its use and exploring new avenues for innovation. This article will delve into these three key areas, starting with the critical role of CMC in industrial and manufacturing processes.
Industrial and Manufacturing Processes
In the realm of industrial and manufacturing processes, Ceramic Matrix Composites (CMCs) have emerged as a transformative material, offering unparalleled performance and durability. These advanced composites, which combine ceramic fibers or particles within a ceramic matrix, are engineered to withstand extreme temperatures, corrosion, and mechanical stress. This makes them ideal for applications in high-temperature environments such as aerospace and defense, where traditional materials often fail. For instance, CMCs are used in the production of jet engine components and heat shields due to their ability to maintain structural integrity at temperatures exceeding 1000°C. In the automotive sector, CMCs are utilized in brake discs and other friction components, enhancing braking performance and reducing wear. The manufacturing process for CMCs involves sophisticated techniques such as chemical vapor infiltration (CVI) and melt infiltration (MI), which ensure uniform distribution of the ceramic fibers within the matrix. These processes require precise control over temperature, pressure, and chemical composition to achieve optimal material properties. Additionally, CMCs are finding increasing use in energy applications, particularly in gas turbines and nuclear reactors, where their resistance to radiation damage and high-temperature stability are crucial. The integration of CMCs into these industrial processes not only enhances the efficiency and lifespan of equipment but also contributes to significant reductions in maintenance costs and environmental impact. As research continues to advance the properties and manufacturing techniques of CMCs, their potential applications are expected to expand further into fields such as biomedical devices and advanced electronics, solidifying their position as a cornerstone material in modern industrial and manufacturing processes.
Medical and Pharmaceutical Applications
In the realm of medical and pharmaceutical applications, Carboxymethyl Cellulose (CMC) plays a pivotal role due to its unique properties and versatility. As a derivative of cellulose, CMC is widely recognized for its ability to form stable, non-toxic, and biocompatible solutions, making it an ideal component in various healthcare products. One of the primary uses of CMC in pharmaceuticals is as an excipient in tablet formulations. Here, it serves multiple functions: as a binder to hold the tablet together, as a disintegrant to facilitate the breakdown of the tablet in the digestive system, and as a thickening agent to control the release of active ingredients. This multifunctionality ensures that medications are delivered effectively and consistently, enhancing patient compliance and therapeutic outcomes. CMC is also integral in the production of ophthalmic solutions and eye drops. Its ability to form a protective film on the eye surface helps in soothing and lubricating dry eyes, making it a common ingredient in artificial tears. Additionally, CMC's viscosity-enhancing properties make it suitable for use in topical creams and gels, where it helps maintain the desired consistency and ensures even distribution of active ingredients on the skin. In wound care, CMC-based dressings are gaining prominence due to their hydrophilic nature, which promotes moisture retention and accelerates the healing process. These dressings create a conducive environment for wound healing by maintaining a moist interface between the dressing and the wound, thereby facilitating tissue regeneration and reducing the risk of infection. Moreover, CMC is used in drug delivery systems, particularly in controlled-release formulations. Its hydrophilic nature allows it to swell in aqueous environments, which can be leveraged to design matrices that release drugs at a controlled rate. This technology is crucial for managing chronic conditions where sustained drug release is necessary to maintain therapeutic levels over an extended period. Furthermore, CMC's biocompatibility and non-toxicity make it an excellent candidate for use in implantable devices such as drug-eluting stents and biodegradable scaffolds. These applications require materials that are not only effective but also safe for long-term use within the body, and CMC meets these stringent criteria. In addition to its direct medical applications, CMC is also utilized in the manufacturing process of various pharmaceutical products. For instance, it is used as a stabilizer in emulsions and suspensions, ensuring that these formulations remain stable over their shelf life. This stability is critical for maintaining the efficacy and safety of medications. In summary, the versatility of CMC in medical and pharmaceutical applications underscores its importance as a multifaceted material. From enhancing drug delivery systems to providing comfort in ophthalmic care, CMC's unique properties make it an indispensable component in the development of numerous healthcare products. Its role in ensuring the stability, efficacy, and safety of medications highlights why it remains a cornerstone in the pharmaceutical industry.
Environmental and Sustainability Roles
In the realm of environmental and sustainability roles, carboxymethyl cellulose (CMC) plays a multifaceted and critical part. As a versatile derivative of cellulose, CMC is widely recognized for its ability to enhance the performance of various products while contributing to sustainable practices. One of the key applications of CMC is in water treatment processes. Here, it acts as a flocculant and coagulant, helping to remove impurities and contaminants from water, thereby improving water quality and making it safer for consumption. This role is particularly significant in regions where access to clean water is limited, as it supports public health and environmental hygiene. CMC also finds extensive use in agriculture, where it serves as a soil conditioner. By improving soil structure and water retention, CMC helps in reducing soil erosion and enhancing crop yields. This not only supports sustainable agricultural practices but also aids in conserving water resources, which is crucial in areas prone to drought. Additionally, CMC's role in biodegradable packaging materials is gaining prominence. As companies shift towards more eco-friendly packaging solutions, CMC's biodegradable nature makes it an ideal component for replacing traditional plastics. This transition helps in reducing plastic waste and mitigating the environmental impact associated with non-biodegradable materials. In the construction industry, CMC is used as an additive in cement and concrete mixtures. It improves the workability of these mixtures, allowing for better flow and application properties. This enhances the efficiency of construction processes while ensuring that the final products have improved durability and strength. Moreover, CMC's use in drilling fluids for oil and gas operations helps in reducing the environmental footprint of these activities. By stabilizing borehole walls and preventing fluid loss, CMC minimizes the risk of environmental contamination and supports safer drilling practices. The pharmaceutical industry also benefits from CMC's sustainability attributes. As an excipient in drug formulations, CMC aids in controlled drug release, ensuring that medications are delivered effectively while minimizing waste. Its use in tablet coatings further reduces the need for additional packaging materials, aligning with broader sustainability goals. Furthermore, CMC's application in personal care products such as toothpaste and cosmetics underscores its commitment to environmental stewardship. By acting as a thickening agent and stabilizer, CMC helps in creating products that are not only effective but also environmentally friendly. In summary, the environmental and sustainability roles of CMC are diverse and impactful. From water treatment and agricultural soil conditioning to biodegradable packaging and construction additives, CMC consistently demonstrates its value in supporting sustainable practices across various industries. Its ability to enhance product performance while reducing environmental impact makes it a crucial component in the quest for a more sustainable future. As industries continue to evolve and prioritize environmental responsibility, the applications and uses of CMC are likely to expand, further solidifying its position as a key player in sustainability initiatives.
Benefits and Challenges of CMC
The integration of Composite Materials (CMCs) into various industries has ushered in a new era of innovation, offering a multitude of benefits while also presenting several challenges. This article delves into the multifaceted advantages and complexities associated with CMCs, exploring three key areas: Economic and Efficiency Advantages, Technical and Performance Benefits, and Environmental Impact and Regulatory Considerations. On the economic front, CMCs offer significant reductions in production costs and enhanced efficiency due to their lightweight yet robust nature, which can lead to substantial savings in fuel consumption and maintenance. Technically, these materials boast superior strength-to-weight ratios, thermal resistance, and durability, making them ideal for high-performance applications. However, the environmental impact of CMCs, including their production processes and end-of-life disposal, must be carefully managed to comply with stringent regulatory standards. By understanding these aspects, industries can harness the full potential of CMCs while mitigating their drawbacks. Let us first examine the Economic and Efficiency Advantages that make CMCs an attractive choice for modern manufacturing.
Economic and Efficiency Advantages
The integration of Computer-Mediated Communication (CMC) into various aspects of modern life offers significant economic and efficiency advantages, making it a cornerstone of contemporary communication. Economically, CMC reduces the need for physical meetings and travel, thereby saving on transportation costs, accommodation expenses, and other logistical expenditures. For instance, businesses can conduct virtual meetings and conferences, enabling global teams to collaborate seamlessly without the financial burden of frequent travel. This not only enhances cost-efficiency but also promotes sustainability by reducing carbon footprints associated with air travel. In terms of efficiency, CMC streamlines communication processes by providing instant connectivity and real-time feedback. Email, instant messaging, and video conferencing tools allow for rapid exchange of information, facilitating quicker decision-making and project execution. Additionally, CMC platforms often include features such as file sharing, collaborative document editing, and task management tools, which further enhance productivity by centralizing workflows and minimizing the risk of miscommunication. Moreover, CMC enables organizations to operate on a 24/7 basis, transcending geographical and temporal constraints. This round-the-clock availability allows for continuous customer support, improved customer satisfaction, and enhanced market reach. For example, e-commerce websites can process transactions and respond to customer inquiries at any time, ensuring that business operations are always active and responsive. From an educational perspective, CMC has revolutionized the way learning is delivered. Online courses and virtual classrooms provide access to education for a broader audience, including those in remote or underserved areas. This democratization of education not only increases educational opportunities but also reduces the economic barriers associated with traditional brick-and-mortar institutions. Furthermore, CMC fosters a more flexible work environment, supporting remote work arrangements that can lead to higher employee satisfaction and retention rates. By allowing employees to work from anywhere, organizations can attract and retain top talent from a global pool rather than being limited to a specific geographic area. This flexibility also contributes to better work-life balance, which can result in increased productivity and overall well-being. In conclusion, the economic and efficiency advantages of CMC are multifaceted and profound. By reducing costs, enhancing productivity, and providing round-the-clock connectivity, CMC has transformed the way businesses operate, how education is delivered, and how people communicate. As technology continues to evolve, these benefits are likely to expand further, solidifying CMC's role as a critical component of modern communication systems.
Technical and Performance Benefits
The integration of Ceramic Matrix Composites (CMCs) into various industrial and technological applications offers a multitude of technical and performance benefits, significantly enhancing the capabilities and efficiency of systems across different sectors. One of the primary advantages of CMCs is their exceptional thermal resistance, allowing them to operate effectively in extreme temperature environments where traditional materials would fail. This property makes CMCs ideal for aerospace and defense applications, such as rocket nozzles, heat shields, and turbine components, where high thermal stability is crucial. Additionally, CMCs exhibit superior mechanical properties, including high strength-to-weight ratios and excellent resistance to fatigue and corrosion. These characteristics enable the development of lightweight yet robust structures that can withstand harsh conditions, thereby improving the overall performance and lifespan of critical components. Another significant benefit of CMCs is their ability to reduce maintenance costs and downtime. Unlike metallic materials that can degrade over time due to oxidation or other forms of corrosion, CMCs maintain their integrity even in aggressive environments. This durability translates into longer service lives for components, reducing the need for frequent replacements and minimizing operational interruptions. Furthermore, the low thermal expansion coefficients of CMCs make them suitable for applications requiring dimensional stability under varying thermal conditions, such as in advanced electronics and precision engineering. In terms of performance, CMCs also offer enhanced friction and wear resistance, which is particularly beneficial in tribological applications like brake pads and seals. The reduced frictional forces and wear rates contribute to smoother operation, increased efficiency, and prolonged component life. Moreover, the electrical insulation properties of certain CMCs make them valuable in high-voltage applications, such as in the automotive and renewable energy sectors. The versatility of CMCs extends to their potential for customization through various manufacturing techniques. Advanced processes like chemical vapor infiltration (CVI) and polymer impregnation and pyrolysis (PIP) allow for the precise control of material properties, enabling the creation of tailored composites that meet specific application requirements. This flexibility is particularly advantageous in fields like biomedical engineering, where implants and prosthetics need to mimic the natural properties of human tissues while providing enhanced durability. In conclusion, the technical and performance benefits of CMCs are multifaceted and far-reaching. Their unique combination of thermal resistance, mechanical strength, durability, and customizable properties makes them an indispensable material in cutting-edge technologies. As research continues to advance the manufacturing processes and material science behind CMCs, their potential applications are likely to expand further, driving innovation across diverse industries and contributing significantly to technological progress.
Environmental Impact and Regulatory Considerations
When considering the benefits and challenges of Cellulose Microcrystalline (CMC), it is crucial to delve into the environmental impact and regulatory considerations associated with its production and use. CMC, derived from wood pulp or cotton linters, is a versatile polymer widely used in various industries including food, pharmaceuticals, and cosmetics. However, its lifecycle from raw material sourcing to end-use and disposal has significant environmental implications. The production process of CMC involves chemical treatments that can lead to the release of harmful by-products and effluents, potentially contaminating water bodies and soil. Additionally, the sourcing of raw materials such as wood pulp can contribute to deforestation if not managed sustainably. This underscores the need for stringent environmental regulations to ensure that CMC manufacturers adhere to sustainable forestry practices and implement effective waste management systems. Regulatory bodies around the world have established guidelines to mitigate these environmental impacts. For instance, the U.S. Environmental Protection Agency (EPA) and the European Union's REACH (Registration, Evaluation, Authorization, and Restriction of Chemicals) regulation mandate thorough assessments of chemical substances, including those used in CMC production, to ensure they do not pose undue risks to human health or the environment. Compliance with these regulations not only helps in reducing the ecological footprint but also enhances the reputation of companies committed to sustainability. Moreover, certifications such as ISO 14001 for Environmental Management Systems encourage companies to adopt best practices in environmental stewardship. This includes implementing recycling programs for CMC waste, using renewable energy sources in manufacturing processes, and conducting regular audits to monitor environmental performance. Despite these regulatory frameworks, challenges persist. The cost of compliance can be prohibitive for smaller manufacturers, potentially leading to a competitive disadvantage. Furthermore, the complexity of global supply chains can make it difficult to ensure that all raw materials are sourced responsibly. Therefore, it is essential for companies to invest in robust supply chain management and transparency to address these challenges effectively. In conclusion, while CMC offers numerous benefits across various industries, its environmental impact and regulatory considerations must be carefully managed. By adhering to stringent environmental regulations and adopting sustainable practices, manufacturers can minimize the ecological footprint of CMC production while ensuring compliance with legal standards. This balanced approach not only safeguards the environment but also contributes to long-term business sustainability and ethical corporate governance.