What Is A Scissor Lift

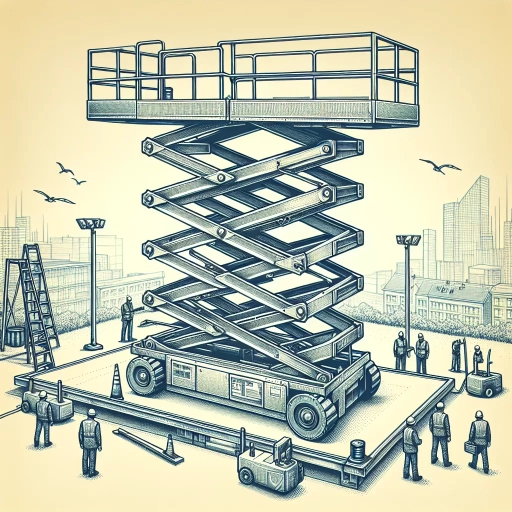
A scissor lift is a versatile and essential piece of equipment in various industries, including construction, maintenance, and warehousing. These lifts are designed to elevate workers and materials to high places safely and efficiently. Understanding what a scissor lift is and its purpose is crucial for effective use. This article will delve into the definition and purpose of a scissor lift, explore the different types and variations available, and discuss critical safety considerations and best practices. By grasping these key aspects, users can maximize the benefits of scissor lifts while ensuring a safe working environment. Let's begin by examining the definition and purpose of a scissor lift, which forms the foundation of its utility and application.
Definition and Purpose of a Scissor Lift
A scissor lift is a versatile piece of equipment designed to elevate workers and materials to various heights, making it an indispensable tool across multiple industries. Understanding its definition and purpose is crucial for optimizing its use. At its core, a scissor lift operates through a basic mechanism and design that involves interconnected metal arms which expand and contract to raise or lower the platform. This fundamental principle allows for stable and controlled vertical movement. The primary uses of scissor lifts span various industries, including construction, manufacturing, and maintenance, where access to high areas is essential. Key features such as safety mechanisms, adjustable height settings, and robust construction contribute to their widespread adoption. By delving into the basic mechanism and design of scissor lifts, we can appreciate how these elements come together to provide a reliable and efficient solution for height access needs. This understanding sets the stage for exploring the broader applications and benefits of scissor lifts in different sectors. Transitioning to the basic mechanism and design, it is essential to grasp how the scissor-like structure enables smooth elevation and stability, ensuring safe and effective operation.
Basic Mechanism and Design
A scissor lift's basic mechanism and design are crucial to its functionality and safety. At its core, a scissor lift operates on the principle of linked, folding supports that resemble the blades of scissors. These supports, typically made of steel or aluminum, are connected in a crisscross pattern and extend when the lift is raised, allowing the platform to ascend vertically. The lifting action is usually achieved through hydraulic or electric motors that drive the scissor mechanism. The design of a scissor lift includes several key components: the base, the scissor arms, the platform, and the control system. The base provides stability and houses the power source and control mechanisms. The scissor arms are the primary structural elements that support the platform and facilitate vertical movement. The platform itself is where workers or materials are placed and is often equipped with safety features such as railings and non-slip surfaces. The control system, which can be manual or automated, allows operators to safely raise and lower the lift. In terms of safety, scissor lifts are designed with multiple features to prevent accidents. These include load sensors to prevent overloading, emergency descent systems in case of power failure, and interlocks to ensure the platform is secure before movement. Additionally, many modern scissor lifts come with advanced features like tilt sensors and automatic leveling systems to maintain stability on uneven surfaces. The design also considers ease of use and maintenance. Scissor lifts are often built with durable materials to withstand heavy use and harsh environments, and they typically have accessible components for routine maintenance. This ensures that the equipment remains operational over its lifespan and minimizes downtime. Overall, the basic mechanism and design of a scissor lift are engineered to provide reliable, safe, and efficient vertical access for various applications, making them an indispensable tool in industries such as construction, warehousing, and maintenance.
Primary Uses in Various Industries
Scissor lifts are versatile pieces of equipment that find primary uses across various industries due to their ability to safely and efficiently elevate workers to high areas. In the **construction industry**, scissor lifts are essential for tasks such as painting, installing drywall, and performing electrical work. They provide a stable platform that allows workers to reach heights without the need for scaffolding, thereby enhancing productivity and reducing the risk of accidents. In **warehousing and logistics**, scissor lifts are used for inventory management, stock retrieval, and maintenance tasks. They enable warehouse staff to access high shelves quickly and safely, streamlining operations and improving overall efficiency. The **aviation industry** also relies on scissor lifts for aircraft maintenance. These lifts allow technicians to work on aircraft components at various heights, facilitating routine inspections and repairs without compromising safety standards. In **retail and commercial settings**, scissor lifts are often used for tasks like changing light bulbs, cleaning windows, and performing other maintenance activities that require access to elevated areas. This ensures that these tasks can be completed swiftly without disrupting business operations. Additionally, **event management** and **entertainment industries** utilize scissor lifts for setting up stages, lighting rigs, and other equipment during concerts, festivals, and theatrical productions. These lifts provide a secure way to reach high areas quickly, ensuring that events are set up efficiently and safely. In **industrial manufacturing**, scissor lifts support maintenance activities such as inspecting machinery, replacing parts, and performing routine upkeep. They offer a reliable means of accessing hard-to-reach areas within factories and plants. Lastly, in **emergency services**, scissor lifts may be employed by fire departments or rescue teams to access high-rise buildings during emergencies or for rescue operations where vertical access is critical. Overall, the primary use of scissor lifts across these diverse industries is to provide a safe, efficient, and reliable method for workers to access elevated areas, thereby enhancing productivity while minimizing the risk of accidents.
Key Features and Benefits
A scissor lift, also known as a scissor jack or scissor table, is a type of aerial work platform that offers several key features and benefits, making it an indispensable tool in various industries such as construction, maintenance, and warehousing. **Key Features:** 1. **Mechanical Advantage:** The scissor lift's unique design, which resembles a pair of scissors, allows for vertical movement by expanding and contracting the cross-beams. This mechanism provides a stable and secure platform. 2. **Height Range:** Scissor lifts can reach heights ranging from a few feet to over 50 feet, catering to different job requirements. 3. **Platform Size:** The platforms come in various sizes to accommodate different numbers of workers and equipment. 4. **Power Options:** They are available in electric, diesel, and hybrid models, offering flexibility based on the work environment and power availability. 5. **Safety Features:** Modern scissor lifts often include safety features such as railings, non-slip surfaces, and emergency descent systems. **Benefits:** 1. **Enhanced Safety:** By providing a stable working platform at elevated heights, scissor lifts reduce the risk of falls and other accidents associated with ladders or scaffolding. 2. **Increased Productivity:** Workers can access high areas quickly and efficiently, allowing them to complete tasks faster without the need for cumbersome setup or teardown. 3. **Versatility:** Scissor lifts are versatile and can be used indoors and outdoors for various tasks such as painting, electrical work, maintenance, and construction. 4. **Ease of Use:** They are generally easy to operate with minimal training required, making them accessible to a wide range of users. 5. **Cost-Effective:** Compared to other aerial lifts like boom lifts or cherry pickers, scissor lifts are often more cost-effective in terms of purchase price and maintenance costs. 6. **Compact Design:** Many scissor lifts are designed to be compact, allowing them to fit into tight spaces and navigate through narrow aisles or doorways. Overall, the combination of mechanical advantage, height range, platform size options, power flexibility, and robust safety features makes scissor lifts an essential piece of equipment for any industry requiring elevated work platforms. Their benefits in terms of safety, productivity, versatility, ease of use, cost-effectiveness, and compact design further solidify their importance in modern workplaces.
Types and Variations of Scissor Lifts
Scissor lifts are versatile and essential tools in various industries, including construction, maintenance, and warehousing. These lifts come in a range of types and variations, each designed to meet specific needs and environments. Understanding the differences between these types is crucial for selecting the right equipment for your tasks. This article delves into three key areas: the comparison between electric and hydraulic scissor lifts, the distinction between portable and fixed scissor lifts, and the specialized scissor lifts tailored for specific tasks. Each of these categories offers unique advantages and limitations that can significantly impact efficiency and safety. For instance, electric scissor lifts are ideal for indoor use due to their quiet operation and zero emissions, while hydraulic lifts provide greater lifting capacity and are often preferred for heavy-duty outdoor applications. By exploring these variations, you can make informed decisions about which scissor lift best suits your operational requirements. Let's start by examining the critical differences between electric and hydraulic scissor lifts.
Electric vs. Hydraulic Scissor Lifts
When it comes to scissor lifts, two primary types stand out: electric and hydraulic. Each has its own set of advantages and disadvantages, making them suitable for different applications and environments. **Electric Scissor Lifts:** Electric scissor lifts are powered by electric motors and batteries, making them ideal for indoor use where noise and emissions are a concern. These lifts are generally quieter and produce zero emissions, which is crucial in confined spaces such as warehouses, shopping malls, and construction sites within urban areas. They are also more energy-efficient and require less maintenance compared to their hydraulic counterparts. However, electric scissor lifts typically have lower lifting capacities and may not be as robust for heavy-duty tasks. Their battery life can also limit their continuous operation time, necessitating regular recharging. **Hydraulic Scissor Lifts:** Hydraulic scissor lifts, on the other hand, are powered by hydraulic systems that rely on fluid pressure to lift the platform. These lifts offer higher lifting capacities and are more suitable for heavy-duty applications such as outdoor construction sites, industrial settings, and tasks that require significant load-bearing capabilities. Hydraulic systems provide greater force and stability, making them more reliable in demanding conditions. However, they are generally noisier and produce emissions due to the combustion engine required to power the hydraulic pump. This makes them less suitable for indoor use or areas with strict environmental regulations. Additionally, hydraulic lifts require more frequent maintenance due to the complexity of their systems and the potential for fluid leaks. **Comparison and Application:** In summary, electric scissor lifts are best suited for indoor, low-to-medium duty tasks where noise and emissions need to be minimized. They offer a cleaner, quieter operation with lower maintenance costs but may lack the heavy-duty capabilities needed for more robust applications. Hydraulic scissor lifts excel in outdoor and heavy-duty scenarios where high lifting capacities are essential. While they are more powerful and reliable in demanding conditions, they come with higher maintenance needs and environmental drawbacks. Understanding these differences is crucial for selecting the right type of scissor lift for your specific needs, ensuring both safety and efficiency in your operations. Whether you prioritize environmental considerations or require the brute force of hydraulic power, choosing between electric and hydraulic scissor lifts will depend on the unique demands of your project or workplace environment.
Portable vs. Fixed Scissor Lifts
When it comes to scissor lifts, two primary types stand out: portable and fixed. Each has its own set of advantages and applications, making them suitable for different scenarios. **Portable Scissor Lifts** are designed for versatility and mobility. These lifts are typically lightweight, compact, and easy to transport, allowing them to be moved from one location to another with minimal effort. They often come with wheels or casters that enable smooth movement across various surfaces. Portable scissor lifts are ideal for indoor and outdoor tasks where the lift needs to be relocated frequently, such as in construction sites, warehouses, and retail environments. Their ease of use and portability make them a favorite among contractors and maintenance personnel who need to access different areas quickly. On the other hand, **Fixed Scissor Lifts** are installed in a permanent location and are not intended for frequent relocation. These lifts are often more robust and can handle heavier loads compared to their portable counterparts. Fixed scissor lifts are commonly used in settings where consistent access to a specific area is required, such as in manufacturing plants, theaters, and high-rise buildings. They provide a stable and reliable means of vertical access, ensuring safety and efficiency in operations that demand regular use. Additionally, fixed scissor lifts can be customized with additional features like extended platforms or specialized controls to meet specific needs. In terms of safety, both types must adhere to stringent standards. However, fixed scissor lifts may offer an added layer of security due to their permanent installation, which can include anchoring systems that prevent movement during operation. Portable lifts, while safe when used correctly, require more careful handling and setup to ensure stability. The choice between a portable and fixed scissor lift ultimately depends on the nature of the task at hand. For projects that require flexibility and frequent repositioning, portable lifts are the better option. For permanent installations where consistent access is necessary, fixed scissor lifts provide reliability and durability. Understanding these differences helps users select the right tool for their specific needs, enhancing productivity and safety in various working environments.
Specialized Scissor Lifts for Specific Tasks
Specialized scissor lifts are designed to cater to specific tasks that require unique capabilities beyond the standard features of general-purpose scissor lifts. These lifts are engineered to meet the demands of various industries, ensuring safety, efficiency, and precision. For instance, **narrow aisle scissor lifts** are ideal for confined spaces such as warehouses and retail environments where traditional lifts cannot fit. These models offer a slim profile while maintaining the necessary height and stability for tasks like inventory management and shelving. **Heavy-duty scissor lifts** are built for rugged applications, such as construction sites and heavy industries, where they need to support substantial weights and withstand harsh conditions. These lifts often feature reinforced structures, enhanced stability systems, and robust motors to handle heavy loads and frequent use. In contrast, **electric scissor lifts** are preferred in indoor settings like offices, hospitals, and shopping malls due to their quiet operation and zero emissions. They are perfect for maintenance tasks that require minimal disruption to daily activities. **Trailer-mounted scissor lifts** offer mobility and versatility, allowing them to be transported easily between job sites. These lifts are particularly useful for outdoor projects such as landscaping, event setup, and utility maintenance where access to different areas is crucial. **Rough terrain scissor lifts**, on the other hand, are equipped with four-wheel drive and large tires to navigate uneven ground, making them essential for outdoor construction projects in challenging terrains. **Bi-level scissor lifts** provide two separate working platforms at different heights, which can be raised independently. This feature is beneficial in scenarios where multiple tasks need to be performed simultaneously at varying elevations. Additionally, **articulating scissor lifts** combine the functionality of a traditional scissor lift with the flexibility of an articulating boom lift, allowing for greater reach and maneuverability in tight spaces. Each type of specialized scissor lift is designed with specific safety features tailored to its intended use. For example, some models come with advanced stabilization systems to prevent tipping on uneven surfaces, while others may include safety sensors to detect obstacles or overloading. By selecting the right specialized scissor lift for the task at hand, users can ensure optimal performance, enhanced safety, and increased productivity. These tailored solutions underscore the versatility and adaptability of scissor lifts in meeting diverse operational needs across various industries.
Safety Considerations and Best Practices
Ensuring safety in any operational environment is paramount, and it involves a multifaceted approach that encompasses several key considerations. At the heart of effective safety practices are three critical components: Pre-Operation Checks and Maintenance, Operator Training and Certification, and On-Site Safety Protocols and Regulations. Each of these elements plays a vital role in mitigating risks and preventing accidents. Pre-Operation Checks and Maintenance are essential for guaranteeing that equipment is in optimal working condition, thereby reducing the likelihood of mechanical failures. Operator Training and Certification ensure that personnel have the necessary skills and knowledge to operate equipment safely and efficiently. Meanwhile, On-Site Safety Protocols and Regulations provide a structured framework for managing risks and responding to emergencies. By integrating these practices, organizations can create a robust safety culture that protects both personnel and assets. To delve deeper into these critical safety measures, we begin by examining the importance of Pre-Operation Checks and Maintenance.
Pre-Operation Checks and Maintenance
Pre-operation checks and maintenance are crucial components of ensuring the safe and efficient use of scissor lifts. Before each use, operators must conduct a thorough inspection to identify any potential hazards or malfunctions. This includes checking the lift's hydraulic system for leaks, inspecting the electrical components for damage, and verifying that all safety features such as guardrails and toe boards are securely in place. The tires or wheels should be inspected for wear and proper inflation, and the platform should be free from debris and obstructions. Additionally, operators must ensure that all controls are functioning correctly and that warning lights and alarms are operational. Regular maintenance is also essential to extend the lifespan of the scissor lift and prevent unexpected failures. This involves adhering to the manufacturer's maintenance schedule, which typically includes tasks such as lubricating moving parts, replacing worn-out components, and performing routine inspections. Battery maintenance is particularly important for electric scissor lifts, as it involves checking the battery's state of charge, cleaning terminals, and ensuring proper charging procedures are followed. Operators should also be trained to recognize signs of wear and tear that may indicate the need for more extensive maintenance or repair. For instance, unusual noises, excessive vibration, or erratic movement could signal underlying issues that need immediate attention. Keeping detailed records of maintenance activities can help track the history of the equipment and ensure compliance with safety regulations. Moreover, pre-operation checks and maintenance should be integrated into a broader safety culture that emphasizes best practices. This includes ensuring that operators are properly trained and certified to use scissor lifts, following established safety protocols during operation, and conducting regular safety audits to identify potential risks. By combining rigorous pre-operation checks with regular maintenance and a commitment to safety, users can significantly reduce the risk of accidents and ensure a safe working environment for all personnel involved.
Operator Training and Certification
Operator training and certification are crucial components of ensuring safety when using scissor lifts. These aerial lifts are designed to elevate workers to high places, but they can be hazardous if not operated correctly. Here are the key points to consider: 1. **Comprehensive Training**: Operators must undergo thorough training that includes both classroom instruction and hands-on practice. This training should cover the safe operation of the scissor lift, pre-operational checks, load capacity limits, and emergency procedures. 2. **Certification Programs**: Many organizations offer certification programs for scissor lift operators. These programs typically include a written exam and a practical test to ensure the operator has the necessary knowledge and skills. 3. **Manufacturer Guidelines**: Operators should be familiar with the manufacturer's guidelines and recommendations for the specific model of scissor lift they are using. This includes understanding the lift's capabilities, limitations, and any unique features. 4. **Regular Refresher Courses**: To maintain proficiency, operators should participate in regular refresher courses. This helps reinforce safe operating practices and updates them on any new regulations or technologies. 5. **Supervisory Oversight**: Supervisors play a critical role in ensuring that operators are trained and certified. They must also conduct regular inspections to ensure that the scissor lift is in good working condition and that operators are following safety protocols. 6. **Site-Specific Training**: Training should also include site-specific hazards such as uneven terrain, overhead obstacles, and weather conditions. This helps operators anticipate and mitigate risks associated with their particular work environment. 7. **Documentation**: All training and certification activities should be well-documented. This includes records of training sessions, certification dates, and any refresher courses attended by the operators. 8. **Regulatory Compliance**: Operators and employers must comply with relevant regulations such as those set by OSHA (Occupational Safety and Health Administration) in the United States or similar bodies in other countries. These regulations often mandate specific training requirements for aerial lift operators. By emphasizing operator training and certification, workplaces can significantly reduce the risk of accidents involving scissor lifts, ensuring a safer environment for all employees. This approach not only protects workers but also enhances operational efficiency and compliance with safety standards.
On-Site Safety Protocols and Regulations
**On-Site Safety Protocols and Regulations** When operating a scissor lift on-site, adhering to stringent safety protocols and regulations is paramount to ensure the well-being of operators, bystanders, and the overall work environment. The Occupational Safety and Health Administration (OSHA) mandates specific guidelines for aerial lift operations, including scissor lifts. First, all operators must undergo comprehensive training that includes both theoretical knowledge and practical experience. This training should cover topics such as equipment inspection, safe operation procedures, and emergency response protocols. Before each use, a thorough pre-operational inspection of the scissor lift is essential to identify any potential hazards or malfunctions. This includes checking for proper function of all controls, ensuring that all safety features like guardrails and toeboards are in place, and verifying that the lift is on a firm, level surface. Operators must also be aware of their surroundings, avoiding overhead obstructions and maintaining a safe distance from power lines. Personal Protective Equipment (PPE) is another critical aspect of on-site safety. Operators should wear hard hats, safety glasses, and fall protection gear when necessary. Additionally, the use of harnesses and lanyards can prevent falls from elevated positions. It is also important to follow load capacity guidelines strictly; overloading can lead to instability and accidents. Weather conditions also play a significant role in safe operation. Scissor lifts should not be used during strong winds, thunderstorms, or icy conditions as these can compromise stability and control. Furthermore, regular maintenance of the equipment is crucial; this includes routine checks by certified technicians to ensure that all components are functioning correctly. Compliance with local regulations and industry standards such as ANSI A92.22 (American National Standards Institute) is mandatory. These standards provide detailed guidelines on safe usage practices, maintenance requirements, and operator training. In addition to these technical aspects, effective communication among team members is vital for preventing accidents. Clear signage indicating work areas where scissor lifts are in operation can alert other workers and visitors to potential hazards. Supervisors should also conduct regular safety audits to ensure that all protocols are being followed diligently. By strictly adhering to these on-site safety protocols and regulations, workplaces can significantly reduce the risk of accidents involving scissor lifts, thereby protecting both human lives and property. This holistic approach ensures that safety considerations are integrated into every aspect of scissor lift operation from training through to daily use and maintenance.