What Is Rtd

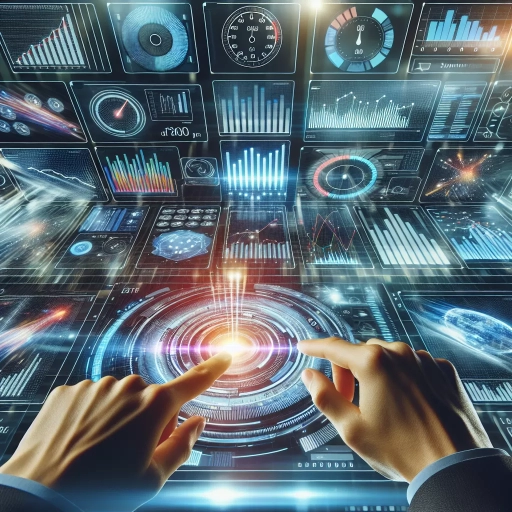
In the realm of industrial measurement and control, the Resistance Temperature Detector (RTD) stands as a crucial component, offering precise temperature readings that are essential for various applications. This article delves into the world of RTD, providing a comprehensive overview of its definition and basic principles, technical aspects, and its advantages and limitations in modern industries. First, we will explore the fundamental definition and basics of RTD, understanding how it operates and its core components. Next, we will delve into the technical aspects of RTD, examining how it works and the underlying physics that make it reliable. Finally, we will discuss the advantages and limitations of RTD in modern industries, highlighting its applications and potential drawbacks. By understanding these facets, readers will gain a thorough insight into the role and significance of RTD in contemporary industrial settings. Let's begin by understanding RTD: Definition and Basics.
Understanding RTD: Definition and Basics
Understanding RTD (Resistance Temperature Detector) is crucial for anyone involved in temperature measurement and control. RTDs are high-quality, informative, and engaging tools that have been integral in various industries for decades. To fully grasp the concept of RTD, it is essential to delve into its historical context, key components, and common applications. Historically, RTDs have evolved significantly since their inception, adapting to technological advancements and industrial needs. The key components of RTD include the sensing element, lead wires, and protective sheath, each playing a critical role in accurate temperature measurement. These components work together to provide precise readings across a wide range of temperatures. RTDs are commonly applied in various sectors such as aerospace, automotive, and chemical processing due to their reliability and accuracy. By understanding these aspects, one can appreciate the significance of RTD in modern industrial practices. Let's begin by exploring the historical context of RTD to see how it has developed over time.
Historical Context of RTD
The historical context of Ready-to-Drink (RTD) beverages is deeply intertwined with the evolution of consumer preferences, technological advancements, and market dynamics. The concept of RTD drinks has its roots in the early 20th century, but it wasn't until the latter half of the century that these beverages began to gain significant traction. In the 1960s and 1970s, the rise of convenience foods and drinks became a cultural phenomenon, driven by increasing urbanization and a growing demand for quick, easy-to-consume products. This period saw the introduction of early RTD formats such as canned and bottled juices, which laid the groundwork for future innovations. The 1980s marked a pivotal moment with the emergence of single-serve packaging and the development of more sophisticated manufacturing processes. This era witnessed the launch of popular RTD brands like Capri Sun and Hi-C, which catered to children and families seeking convenient beverage options. The success of these products underscored the potential for RTD beverages to capture a broader market share. In the 1990s and early 2000s, health-conscious consumers began to drive demand for low-calorie, low-sugar alternatives. This shift led to the proliferation of RTD teas, coffees, and sports drinks. Brands like Snapple and Arizona Iced Tea capitalized on this trend by offering a range of flavors and health benefits that appealed to a more discerning consumer base. The modern RTD landscape has been significantly shaped by recent trends in wellness, sustainability, and premiumization. The rise of hard seltzers and canned cocktails in the late 2010s exemplifies how RTD beverages have adapted to changing consumer preferences for low-carb, low-calorie alcoholic drinks. Brands such as White Claw and Truly have dominated this segment, leveraging innovative packaging and marketing strategies to appeal to a younger demographic. Additionally, advancements in technology have enabled better preservation methods, improved flavor profiles, and more eco-friendly packaging options. This has allowed RTD manufacturers to offer a wider variety of products that meet both taste and sustainability criteria. For instance, the use of aseptic packaging has extended shelf life without compromising nutritional content or flavor. Today, the RTD market is characterized by its diversity and dynamism. Consumers can choose from a vast array of beverages tailored to specific dietary needs, lifestyle preferences, and taste profiles. The historical context of RTD beverages highlights how this industry has continuously evolved in response to consumer demands, technological innovations, and broader societal trends. Understanding this historical backdrop is crucial for grasping the current state and future potential of the RTD market.
Key Components of RTD
When delving into the realm of RTD (Ready-to-Drink) beverages, several key components come to the forefront that define their appeal, functionality, and market presence. **Formulation** is a critical aspect, as it involves the precise blending of ingredients to achieve a consistent taste, texture, and nutritional profile. This includes the selection of high-quality raw materials such as natural sweeteners, flavor enhancers, and preservatives that ensure the product remains fresh and palatable over its shelf life. **Packaging** plays a pivotal role in RTD beverages, influencing both consumer convenience and environmental impact. Modern RTD packaging often features eco-friendly materials like recyclable plastics, cartons, or cans that are designed to be lightweight yet durable. The design of the packaging also impacts consumer perception, with visually appealing labels and ergonomic shapes contributing to the overall brand experience. **Shelf Stability** is another crucial factor, as RTD beverages must remain safe for consumption without refrigeration for an extended period. This is achieved through a combination of pasteurization, sterilization, or aseptic processing techniques that eliminate pathogens while preserving the product's nutritional value and flavor profile. **Regulatory Compliance** is essential for any RTD product entering the market. Manufacturers must adhere to strict guidelines set by food safety authorities regarding ingredient usage, labeling requirements, and manufacturing practices. Compliance ensures that the product meets health standards and avoids potential legal issues. **Marketing and Distribution** strategies are vital for the success of RTD beverages. Effective marketing campaigns often focus on highlighting the convenience, health benefits, and unique selling points of the product. Distribution channels must be robust to ensure widespread availability in retail stores, online platforms, and other sales outlets. **Consumer Trends** also significantly influence the development and positioning of RTD beverages. With increasing demand for healthier options, low-calorie drinks, and sustainable products, manufacturers are compelled to innovate and adapt their offerings accordingly. Understanding consumer preferences helps in tailoring products that meet evolving needs and tastes. Finally, **Innovation** remains a driving force in the RTD market. Continuous research and development lead to new flavors, ingredients, and technologies that enhance the product's appeal and functionality. Innovations such as functional ingredients (e.g., probiotics, vitamins), unique flavor profiles, and advanced packaging solutions keep the market dynamic and competitive. In summary, the key components of RTD beverages—formulation, packaging, shelf stability, regulatory compliance, marketing and distribution, consumer trends, and innovation—collectively contribute to their success in a rapidly evolving market landscape. Each component must be carefully considered to ensure that the final product meets consumer expectations while maintaining high standards of quality and safety.
Common Applications of RTD
Resistance Temperature Detectors (RTDs) are widely used in various industries due to their high accuracy, stability, and reliability in temperature measurement. One of the most common applications of RTDs is in **process control**, where precise temperature monitoring is crucial. For instance, in chemical processing plants, RTDs are used to monitor and control reaction temperatures, ensuring optimal conditions for chemical reactions and product quality. Similarly, in **power generation**, RTDs are employed to measure temperatures in boilers, turbines, and other critical components, helping to maintain efficient operation and prevent overheating. In the **food and beverage industry**, RTDs ensure that products are processed at the correct temperatures to meet safety standards and quality requirements. They are often used in pasteurization processes, cooking, and refrigeration systems. **Aerospace and defense** also rely heavily on RTDs for monitoring temperatures in aircraft engines, fuel systems, and other critical components where precise temperature control is vital for safety and performance. **Automotive applications** include using RTDs to monitor engine temperatures, transmission temperatures, and exhaust gas temperatures, which helps in optimizing engine performance and reducing emissions. In **medical devices**, RTDs are used in patient monitoring systems, such as thermometers, and in medical equipment like incubators and sterilizers where accurate temperature control is essential. Additionally, RTDs are integral in **HVAC systems** for heating, ventilation, and air conditioning. They help in maintaining optimal indoor air quality by accurately measuring temperatures in heating and cooling units. In **research and development**, RTDs are used in laboratory settings for precise temperature measurements in experiments involving materials science, chemistry, and physics. Overall, the versatility of RTDs makes them a preferred choice across diverse industries where accurate temperature measurement is critical for safety, efficiency, and product quality. Their reliability and long-term stability ensure consistent performance over time, making them an indispensable tool in modern industrial processes.
How RTD Works: Technical Aspects
Understanding how Resistance Temperature Detectors (RTDs) work is crucial for leveraging their full potential in various industrial and scientific applications. At the heart of RTD technology lies a fundamental principle: the relationship between temperature and electrical resistance. This article delves into the technical aspects of RTDs, starting with the **Principle of Operation**, which explains how these devices convert temperature changes into measurable resistance variations. Additionally, we will explore **Types of RTD Sensors**, highlighting the different materials and configurations that cater to diverse operational requirements. Finally, we will discuss **Accuracy and Precision in RTD Measurements**, addressing the factors that influence the reliability and accuracy of temperature readings. By grasping these key concepts, users can better select, implement, and maintain RTD systems. Let's begin by examining the **Principle of Operation**, which forms the basis of RTD functionality.
Principle of Operation
The Principle of Operation for a Resistance Temperature Detector (RTD) is rooted in the fundamental property of metals to change electrical resistance in response to temperature variations. Here’s how it works: An RTD typically consists of a thin wire or film of a pure metal, such as platinum, nickel, or copper, which is carefully wound or deposited onto a substrate. When the temperature around the RTD changes, the metal's resistance also changes. This change in resistance is directly proportional to the change in temperature, following a predictable and linear relationship over a wide range of temperatures. The most common type of RTD is the platinum RTD (Pt100 or Pt1000), which has a resistance of 100 ohms at 0°C and increases by approximately 0.385 ohms per degree Celsius. This precise and repeatable relationship allows for accurate temperature measurement. In operation, the RTD is connected to a measurement circuit that applies a small current through the sensor. The resulting voltage drop across the RTD is then measured, and using Ohm's Law, the resistance can be calculated. This resistance value is then correlated to a specific temperature using calibration data or tables. To enhance accuracy and reliability, RTDs often employ three- or four-wire configurations. The three-wire setup compensates for lead wire resistance by using one wire to carry the current and two wires to measure the voltage drop across the RTD. The four-wire setup further improves accuracy by allowing separate wires for current and voltage measurement, effectively eliminating lead wire resistance from the measurement. RTDs are widely used in industrial applications due to their high precision, stability, and durability. They offer advantages over other temperature sensors like thermocouples in terms of accuracy and linearity, making them ideal for applications requiring precise temperature control and monitoring. However, they generally have slower response times compared to thermocouples and are more expensive. In summary, the principle of operation for an RTD hinges on the predictable change in electrical resistance of a metal with temperature, allowing for precise and reliable temperature measurement across various industrial and scientific applications.
Types of RTD Sensors
RTD (Resistance Temperature Detector) sensors are versatile and widely used for precise temperature measurement across various industries. There are several types of RTD sensors, each with its own unique characteristics and applications. 1. **Pt100 and Pt1000 RTDs**: These are the most common types, named for their resistance at 0°C (Pt100 = 100 ohms, Pt1000 = 1000 ohms). Pt100 RTDs are more accurate and stable but less sensitive than Pt1000 RTDs. They are often used in industrial processes, laboratory settings, and HVAC systems. 2. **Pt50 and Pt200 RTDs**: These have lower base resistances (50 ohms and 200 ohms at 0°C) and are less common. They offer higher sensitivity but lower accuracy compared to Pt100 and Pt1000 models. 3. **Copper RTDs**: Although less common due to their lower accuracy and stability, copper RTDs have a higher temperature coefficient of resistance compared to platinum RTDs. They are sometimes used in specific applications where cost is a significant factor. 4. **Nickel RTDs**: Known for their high temperature coefficient of resistance, nickel RTDs are used in applications requiring high sensitivity but are less accurate and stable than platinum RTDs. 5. **Thin-Film RTDs**: These are made by depositing a thin layer of metal onto a substrate. They offer fast response times and are often used in applications requiring quick temperature changes detection, such as in automotive and aerospace industries. 6. **Wire-Wound RTDs**: Constructed by winding a wire around a core, these RTDs provide high accuracy and stability. They are commonly used in laboratory equipment and precision measurement instruments. 7. **Film-Deposited RTDs**: Similar to thin-film RTDs but with improved durability and stability. They are widely used in industrial automation and process control. 8. **Bare Element RTDs**: These consist of a bare platinum wire or film without any protective coating or housing. They offer the fastest response times but require careful handling due to their fragility. 9. **Sheathed RTDs**: Encased in a protective sheath, these RTDs provide better durability and resistance to environmental factors like moisture and chemicals. They are commonly used in harsh industrial environments. 10. **Sanitary RTDs**: Designed for use in food processing and pharmaceutical industries where hygiene is critical, these RTDs are made from materials that meet sanitary standards and are easy to clean. Each type of RTD sensor has its specific advantages and disadvantages, making them suitable for different applications based on factors such as accuracy, sensitivity, durability, and cost. Understanding these differences is crucial for selecting the right RTD sensor for precise temperature measurement in various technical contexts.
Accuracy and Precision in RTD Measurements
Accuracy and precision are crucial in Resistance Temperature Detector (RTD) measurements, as they directly impact the reliability and usefulness of the temperature data obtained. **Accuracy** refers to how close the measured temperature is to the actual temperature, while **precision** pertains to the consistency of repeated measurements under the same conditions. In RTD measurements, achieving high accuracy involves ensuring that the sensor is calibrated correctly and that any potential sources of error, such as lead wire resistance or environmental factors, are minimized. For instance, using a four-wire configuration can help eliminate lead wire resistance errors, thereby enhancing accuracy. **Precision**, on the other hand, is influenced by factors such as sensor quality, measurement technique, and data acquisition system. High-quality RTDs made from materials like platinum (Pt100 or Pt1000) offer better precision due to their stable and predictable resistance-temperature relationship. Additionally, employing advanced measurement techniques like ratiometric measurement methods can improve precision by reducing noise and increasing signal-to-noise ratio. Environmental conditions also play a significant role in maintaining both accuracy and precision. Factors such as ambient temperature fluctuations, humidity, and physical stress on the sensor can introduce errors. Proper insulation and shielding of the RTD can mitigate these effects. Furthermore, regular calibration checks against a known standard ensure that the RTD remains accurate over time. In practical applications, the choice of RTD type (e.g., Pt100 vs. Pt1000) and configuration (e.g., two-wire vs. four-wire) should be based on the required level of accuracy and precision. For example, in industrial processes where high precision is critical but the environment is relatively stable, a four-wire Pt100 RTD might be ideal. Conversely, in less demanding applications where cost is a factor, a two-wire Pt1000 RTD could suffice. In summary, achieving high accuracy and precision in RTD measurements involves careful selection of the sensor type, proper calibration, use of appropriate measurement techniques, and consideration of environmental factors. By understanding these technical aspects, users can ensure reliable temperature data that meet their specific needs. This attention to detail is essential for maintaining the integrity of temperature measurements across various industries, from manufacturing to scientific research.
Advantages and Limitations of RTD in Modern Industries
In modern industries, Resistance Temperature Detectors (RTDs) have emerged as a crucial tool for precise temperature measurement, offering a balance of advantages and limitations. This article delves into the multifaceted role of RTDs, exploring their benefits over other temperature measurement methods, their widespread industrial applications and case studies, and the potential drawbacks and challenges associated with their use. By understanding these aspects, industries can make informed decisions about integrating RTDs into their operations. The benefits of RTDs, such as higher accuracy and stability compared to thermocouples, make them a preferred choice in many applications. This article will first examine the benefits of RTDs over other temperature measurement methods, highlighting their superior performance and reliability. This will set the stage for a deeper exploration of their industrial applications and case studies, as well as a discussion on the potential drawbacks and challenges that need to be addressed. By transitioning from the general advantages to the specific benefits over other methods, we can appreciate the unique value RTDs bring to modern industrial processes.
Benefits Over Other Temperature Measurement Methods
When comparing RTDs (Resistance Temperature Detectors) to other temperature measurement methods, several key benefits emerge that make RTDs a preferred choice in modern industries. **Accuracy and Precision**: RTDs offer high accuracy and precision, often surpassing other methods like thermocouples and thermistors. This is crucial in applications where even slight deviations can have significant consequences, such as in chemical processing, pharmaceutical manufacturing, and aerospace engineering. **Stability and Reliability**: Unlike thermocouples, which can drift over time due to oxidation or contamination, RTDs are known for their long-term stability. This reliability ensures consistent readings without the need for frequent recalibration, making them ideal for continuous monitoring in industrial settings. **Linearity**: RTDs exhibit a linear relationship between resistance and temperature, which simplifies calibration and data interpretation. This linearity contrasts with the non-linear responses of thermocouples and thermistors, reducing the complexity of temperature measurement systems. **Low Noise and High Signal-to-Noise Ratio**: RTDs generate a strong, noise-resistant signal that is less susceptible to electromagnetic interference (EMI) compared to thermocouples. This results in more reliable data transmission and fewer errors in measurement. **Wide Range of Applications**: RTDs can be used across a broad temperature range, from very low temperatures (e.g., cryogenic applications) to high temperatures (e.g., in power generation). Their versatility makes them suitable for diverse industrial environments. **Ease of Use and Maintenance**: While RTDs may require more complex wiring compared to thermocouples, their overall ease of use and maintenance is enhanced by their robust construction and minimal drift over time. This reduces the need for frequent maintenance checks and replacements, saving both time and resources. **Compatibility with Digital Systems**: Modern RTDs are easily integrated with digital systems due to their straightforward electrical interface, facilitating seamless data acquisition and processing. This compatibility is particularly advantageous in automated industrial processes where real-time monitoring is essential. In summary, the advantages of RTDs over other temperature measurement methods lie in their superior accuracy, stability, linearity, low noise, wide applicability, ease of use, and compatibility with digital systems, making them an indispensable tool in modern industries.
Industrial Applications and Case Studies
In modern industries, Resistance Temperature Detectors (RTDs) find widespread application due to their precision, reliability, and durability. One of the primary industrial applications of RTDs is in process control systems, where accurate temperature measurement is crucial for maintaining optimal operating conditions. For instance, in the chemical processing industry, RTDs are used to monitor and control reaction temperatures, ensuring consistent product quality and safety. In the oil and gas sector, RTDs are employed in pipelines and refineries to measure temperature variations that can affect fluid viscosity and flow rates, thereby optimizing energy efficiency and reducing the risk of equipment failure. A notable case study involves a major automotive manufacturer that integrated RTDs into their engine testing facilities. By accurately measuring engine block temperatures, the manufacturer was able to fine-tune engine performance, reduce emissions, and enhance overall vehicle reliability. Another example is in the food processing industry, where RTDs are used to monitor temperatures during pasteurization and sterilization processes, ensuring compliance with food safety regulations and extending product shelf life. In aerospace engineering, RTDs play a critical role in monitoring the extreme temperatures experienced by aircraft components during flight. This data is essential for material selection and design optimization to ensure structural integrity and safety. Additionally, in HVAC systems, RTDs help maintain precise indoor climate conditions by accurately measuring air and water temperatures, leading to improved energy efficiency and comfort. Despite these advantages, RTDs also have limitations. For example, they are generally more expensive than thermocouples and may require additional wiring and signal conditioning. Moreover, their response time can be slower compared to other temperature sensors, which might be a drawback in applications requiring rapid temperature changes. However, these limitations are often outweighed by the high accuracy and long-term stability that RTDs offer, making them a preferred choice in many industrial settings where precision is paramount. Overall, the industrial applications of RTDs are diverse and critical, underscoring their importance in maintaining operational efficiency, product quality, and safety across various sectors.
Potential Drawbacks and Challenges
Despite the numerous advantages of Resistance Temperature Detectors (RTDs) in modern industries, there are several potential drawbacks and challenges that need to be considered. One significant limitation is the higher cost compared to other temperature measurement devices, such as thermocouples. This increased expense can be a barrier for budget-conscious operations. Additionally, RTDs generally have slower response times than thermocouples, which can be critical in applications requiring rapid temperature changes detection. The fragility of RTD elements, particularly when exposed to mechanical stress or vibration, is another concern. This fragility necessitates careful handling and installation to ensure longevity and accuracy. Moreover, RTDs are typically less robust in extreme environments. For instance, they may not perform well in very high or very low temperatures, limiting their applicability in certain industrial settings. The requirement for precise calibration and maintenance also adds to the operational complexity and cost. Furthermore, the wiring and connections of RTDs can be prone to errors or damage, which can lead to inaccurate readings or complete system failure. In some cases, the self-heating effect of RTDs—where the current used for measurement heats the sensor itself—can introduce measurement errors, especially at low temperatures. Another challenge is the compatibility issue with existing systems. Integrating RTDs into legacy systems or those designed for other types of sensors can be challenging and may require significant modifications or additional hardware. This compatibility issue can delay implementation and increase overall costs. Lastly, while RTDs offer high precision and stability, they are not immune to environmental factors such as moisture, corrosion, or electromagnetic interference (EMI), which can affect their performance and lifespan. In summary, while RTDs offer many advantages in terms of accuracy and reliability, their higher cost, slower response times, fragility, limited extreme temperature range, calibration requirements, wiring issues, self-heating effects, compatibility challenges with existing systems, and susceptibility to environmental factors are all potential drawbacks that must be carefully evaluated when considering their use in modern industrial applications.