What Is Cc Engine

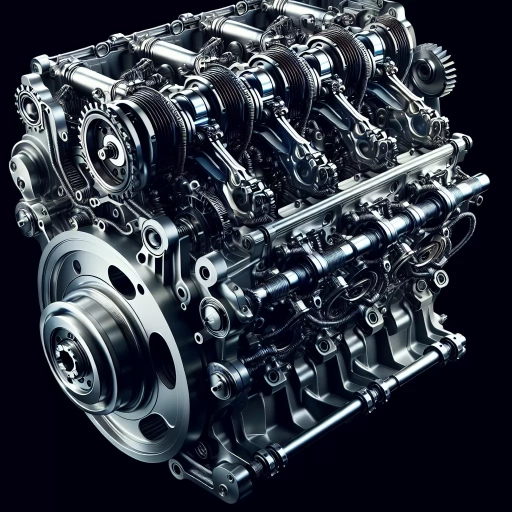
In the world of automotive and mechanical engineering, the term "CC engine" is often encountered, but its intricacies are not always fully understood. A CC engine, short for cubic centimeter engine, refers to the displacement volume of an engine's cylinders. This metric is crucial for determining an engine's power output and efficiency. To delve into the complexities of CC engines, it is essential to first understand their basic principles. This article will explore three key aspects: **Understanding the Basics of CC Engines**, which will cover the fundamental concepts and terminology associated with these engines; **How CC Engines Work**, which will explain the operational mechanics behind them; and **Applications and Types of CC Engines**, which will discuss their various uses and classifications. By grasping these elements, readers will gain a comprehensive insight into what makes CC engines tick. Let's begin by **Understanding the Basics of CC Engines**.
Understanding the Basics of CC Engines
Understanding the basics of CC (Cubic Centimeter) engines is crucial for anyone interested in automotive mechanics or engineering. This article delves into the fundamental aspects of CC engines, providing a comprehensive overview that is both informative and engaging. To grasp the intricacies of these engines, it is essential to start with a clear understanding of the definition and terminology associated with them. This includes familiarizing oneself with key terms such as displacement, horsepower, and torque. Historical development is another critical aspect, as it sheds light on how CC engines have evolved over time, from their early beginnings to the sophisticated designs of today. This historical context helps in appreciating the advancements and innovations that have shaped modern engine technology. Lastly, understanding the key components and structure of CC engines is vital for any mechanic or enthusiast. This involves knowing the roles of pistons, cylinders, crankshafts, and other critical parts that work together to convert fuel into mechanical energy. By exploring these three foundational areas—definition and terminology, historical development, and key components and structure—readers will gain a solid foundation in the basics of CC engines. Let's begin by examining the definition and terminology that form the bedrock of this knowledge.
Definition and Terminology
Understanding the basics of CC (Cubic Centimeter) engines begins with a clear grasp of key definitions and terminology. A CC engine, also known as a cubic centimeter engine or more commonly referred to in terms of its displacement in liters, is fundamentally defined by its engine displacement. Engine displacement is the total volume of air and fuel that all the pistons in an engine's cylinders can push through in one complete cycle. This volume is measured in cubic centimeters (cc) or liters (L), where 1 liter equals 1,000 cubic centimeters. **Key Terms:** - **Engine Displacement:** The total volume swept by all the pistons in an engine's cylinders. - **Cubic Centimeter (cc):** A unit of volume measurement for engine displacement. - **Liter (L):** Another unit of volume measurement, where 1 liter = 1,000 cc. - **Piston Stroke:** The distance a piston travels from the top of its stroke to the bottom. - **Bore:** The diameter of the cylinder. - **Cylinder Head:** The component that sits on top of the engine block and contains the valves and combustion chamber. - **Combustion Chamber:** The space where fuel is ignited to produce power. **How It Works:** The engine displacement is calculated by multiplying the number of cylinders by the volume swept by one cylinder. This volume is determined by the formula: π/4 * (bore)^2 * stroke * number of cylinders. For instance, if an engine has four cylinders with a bore of 80 mm and a stroke of 90 mm, its displacement would be calculated as follows: π/4 * (80 mm)^2 * 90 mm * 4 = approximately 1,814 cc or 1.814 liters. **Importance:** Understanding these terms is crucial because they directly influence an engine's performance characteristics such as power output, fuel efficiency, and overall size. A higher displacement generally means more power but often at the cost of increased fuel consumption and larger engine size. In summary, grasping the definitions and terminology related to CC engines provides a foundational understanding necessary for appreciating how these engines operate and their various applications in vehicles and machinery. This knowledge helps in making informed decisions about engine selection based on specific needs and requirements.
Historical Development
The historical development of internal combustion engines, particularly those measured in cubic centimeters (cc), is a narrative of innovation and continuous improvement. The journey began in the late 19th century with the invention of the first practical internal combustion engine by Nikolaus August Otto in 1876. Otto's four-stroke cycle—intake, compression, power, and exhaust—became the foundational principle for modern engines. In the early 20th century, engineers like Gottlieb Daimler and Wilhelm Maybach adapted these principles to create smaller, more efficient engines suitable for automotive use. The term "cc" refers to the displacement volume of an engine's cylinders, measured in cubic centimeters. This metric became crucial as manufacturers sought to standardize engine sizes and performance. By the 1920s, car manufacturers were producing engines with displacements ranging from a few hundred to several thousand cubic centimeters. The development of motorcycles in the early 20th century further accelerated the demand for smaller, lighter engines, often in the range of 50 to 500 cc. Post-World War II saw significant advancements in engine technology, driven by the need for more efficient and powerful engines. The introduction of overhead camshafts, fuel injection systems, and improved materials like aluminum and titanium allowed for lighter yet stronger engines. This period also saw the rise of two-stroke engines, particularly in the motorcycle industry, which offered higher power-to-weight ratios but were eventually phased out due to environmental concerns. In the latter half of the 20th century, emissions regulations became a major driver of engine development. Manufacturers had to balance performance with environmental compliance, leading to innovations such as catalytic converters and fuel injection systems that could optimize fuel efficiency while reducing emissions. Modern engines continue this trend with advancements in computer-controlled fuel management, turbocharging, and hybrid technologies. Today, cc engines are found in a wide range of applications from small generators and lawn mowers to high-performance sports cars and motorcycles. The diversity in engine sizes reflects the varied needs of different industries and consumers. For instance, small cc engines (50-125 cc) are common in scooters and mopeds due to their fuel efficiency and ease of handling, while larger cc engines (1000-2000 cc) are used in high-performance vehicles where power and torque are paramount. Understanding the historical development of cc engines provides a deeper appreciation for the engineering challenges and innovations that have shaped the industry. From humble beginnings with Otto's four-stroke cycle to the sophisticated, computer-controlled engines of today, each step has contributed to more efficient, powerful, and environmentally friendly engines that power our modern world. This evolution underscores the importance of continuous innovation in meeting the changing demands of society while adhering to stringent performance and environmental standards.
Key Components and Structure
When delving into the basics of CC (Cubic Centimeter) engines, understanding the key components and structure is paramount. At the heart of any CC engine lies the **cylinder block**, which houses the cylinders where combustion occurs. The number of cylinders can vary, but common configurations include inline-4, V6, and V8. Each cylinder contains a **piston** that moves up and down, driven by explosive forces generated during combustion. These pistons are connected to **connecting rods**, which in turn are linked to the **crankshaft**. The crankshaft converts the linear motion of the pistons into rotational energy, which is then transmitted to the **camshaft** via a timing belt or chain. The **camshaft** operates the **valves** (intake and exhaust) that allow air and fuel into the cylinders and exhaust gases out. The **valve train**, comprising components like valve springs, retainers, and lifters, ensures precise valve operation. Above the cylinders, the **cylinder head** seals the combustion chamber and houses the valves, spark plugs (in gasoline engines), or fuel injectors (in diesel engines). The **engine block** and **cylinder head** are sealed by a **head gasket** to prevent leaks. The **crankcase** encloses the crankshaft and connecting rods, protecting them from debris and maintaining oil circulation. **Engine oil** lubricates moving parts, while the **cooling system** (radiator, water pump, hoses) regulates engine temperature. The **fuel system**, including fuel injectors or carburetors, delivers fuel to the cylinders. In modern engines, electronic control units (ECUs) manage fuel injection, ignition timing, and other critical functions. Additionally, key structural elements include the **engine mounts** that secure the engine to the vehicle's chassis and **accessories** such as alternators, power steering pumps, and air conditioning compressors. Understanding these components and their interplay is essential for diagnosing issues, performing maintenance, and optimizing engine performance. By grasping the fundamental structure and operation of a CC engine, one can better appreciate its complexity and importance in powering vehicles efficiently.
How CC Engines Work
Understanding how CC (Cubic Centimeter) engines work is crucial for appreciating the intricate mechanics behind modern vehicles. At the heart of these engines lies a complex interplay of processes that convert chemical energy into mechanical power. This article delves into three key aspects: the Four-Stroke Cycle Process, the Role of Fuel and Air Mixture, and the Ignition and Combustion Process. The Four-Stroke Cycle Process, which includes intake, compression, power, and exhaust strokes, forms the foundational mechanism by which engines operate. The Role of Fuel and Air Mixture highlights the critical balance required for efficient combustion, while the Ignition and Combustion Process explains how this mixture is ignited to produce power. By examining these components, readers will gain a comprehensive understanding of how CC engines function. Let's begin by exploring the Four-Stroke Cycle Process, which sets the stage for the entire engine operation.
Four-Stroke Cycle Process
The Four-Stroke Cycle Process is a fundamental mechanism in the operation of internal combustion engines, particularly those classified as CC (Cubic Centimeter) engines. This process involves four distinct phases that occur within the engine's cylinders, ensuring efficient combustion and power generation. Here’s a detailed breakdown: 1. **Intake Stroke**: During this initial phase, the piston moves downward, creating a vacuum in the cylinder. The intake valve opens, allowing a mixture of air and fuel to enter the cylinder through the intake manifold. This mixture is precisely metered by the fuel injection system or carburetor to ensure optimal combustion. 2. **Compression Stroke**: As the intake valve closes, the piston begins to move upward, compressing the air-fuel mixture within the cylinder. This compression increases the temperature and pressure of the mixture, preparing it for ignition. 3. **Power Stroke**: At the top of the compression stroke, the spark plug ignites the compressed air-fuel mixture (in a gasoline engine) or fuel injection occurs (in a diesel engine), causing a small explosion that pushes the piston downward. This downward motion is what ultimately drives the crankshaft and converts chemical energy into mechanical energy. 4. **Exhaust Stroke**: Finally, as the piston moves upward again, it pushes the exhaust gases out of the cylinder through the exhaust valve, which is open during this phase. Once the exhaust gases are expelled, the exhaust valve closes, and the cycle repeats with the intake stroke. Each stroke is precisely timed and coordinated by the engine's camshaft and valve train system, ensuring smooth operation and maximizing efficiency. The Four-Stroke Cycle Process is crucial for maintaining engine performance, fuel efficiency, and overall reliability in CC engines. Understanding this cycle is essential for appreciating how these engines generate power and why they are widely used in various applications, from automotive vehicles to industrial machinery.
Role of Fuel and Air Mixture
The role of the fuel and air mixture is crucial in the operation of a combustion chamber (CC) engine. This mixture, often referred to as the air-fuel mixture, is the blend of air and fuel that is ignited within the engine's combustion chamber to produce power. Here’s how it works: 1. **Air Intake**: Air is drawn into the engine through the intake manifold, which is typically controlled by a throttle valve that regulates airflow based on driver input. 2. **Fuel Injection**: Fuel is injected into the intake manifold by fuel injectors, which spray a precise amount of fuel into the airflow. The amount of fuel injected is determined by the engine control unit (ECU) based on various parameters such as engine speed, load, and temperature. 3. **Mixing**: The air and fuel mix in the intake manifold before entering the combustion chamber. The ideal air-fuel ratio varies depending on engine design and operating conditions but is generally around 14.7:1 for gasoline engines. 4. **Ignition**: Once inside the combustion chamber, this air-fuel mixture is compressed by the piston and then ignited by a spark plug (in a spark-ignition engine) or by heat generated during compression (in a compression-ignition engine). 5. **Combustion**: The ignition of this mixture causes a small explosion that pushes the piston down, which in turn rotates the crankshaft and ultimately powers the vehicle. ### Importance of Proper Mixture - **Efficiency**: A proper air-fuel mixture ensures optimal combustion efficiency, maximizing power output while minimizing fuel consumption. - **Emissions**: A well-balanced mixture helps in reducing harmful emissions such as carbon monoxide (CO), hydrocarbons (HC), and nitrogen oxides (NOx). - **Engine Health**: Incorrect mixtures can lead to engine problems like knocking or pinging in spark-ignition engines and soot buildup in compression-ignition engines. ### Factors Influencing Mixture - **Engine Load**: The amount of fuel injected changes with engine load to maintain an optimal air-fuel ratio. - **Engine Speed**: The ECU adjusts the fuel injection timing and quantity based on engine speed. - **Temperature**: Cold engines require richer mixtures for easier starting, while hot engines may require leaner mixtures to prevent overheating. In summary, the precise control over the fuel and air mixture is essential for efficient operation, reduced emissions, and prolonged engine life in CC engines. The ECU plays a critical role in ensuring that this delicate balance is maintained under various operating conditions.
Ignition and Combustion Process
In the context of internal combustion (IC) engines, particularly those categorized as CC (cubic centimeter) engines, the ignition and combustion process is a critical phase that converts chemical energy into mechanical energy. This process occurs within the engine's cylinders and is fundamental to the engine's operation. Here’s a detailed overview: 1. **Air-Fuel Mixture Preparation**: The journey begins with the intake stroke where air and fuel are drawn into the cylinder through the intake valves. The air-fuel mixture is precisely metered by the fuel injection system or carburetor to achieve an optimal ratio, typically around 14.7:1 for gasoline engines. 2. **Compression Stroke**: As the intake valves close, the piston moves upward, compressing the air-fuel mixture in the cylinder. This compression increases the temperature and pressure of the mixture, preparing it for ignition. 3. **Ignition**: At the top dead center (TDC) of the compression stroke, a spark plug ignites the compressed air-fuel mixture in a gasoline engine. In diesel engines, the high compression ratio generates enough heat to ignite the fuel without a spark plug. 4. **Combustion**: The ignition of the air-fuel mixture leads to a rapid expansion of gases due to combustion. This expansion forces the piston downward, which in turn rotates the crankshaft. The rotational energy of the crankshaft is what ultimately powers the vehicle or machine. 5. **Power Stroke**: The downward motion of the piston during combustion is known as the power stroke. It is this stroke that generates the torque and power output of the engine. 6. **Exhaust Stroke**: After the power stroke, the exhaust valves open, and the piston moves upward again, pushing the exhaust gases out of the cylinder and into the exhaust system. 7. **Cycle Completion**: The four-stroke cycle (intake, compression, power, exhaust) repeats continuously in each cylinder, ensuring a smooth and efficient operation of the engine. The efficiency and performance of an IC engine are heavily dependent on the precise timing and control of these ignition and combustion processes. Modern engines employ sophisticated technologies such as fuel injection systems, ignition timing control, and turbocharging to optimize these processes, thereby enhancing fuel efficiency, power output, and reducing emissions. Understanding these mechanisms is crucial for appreciating how CC engines work and their role in powering various vehicles and machinery.
Applications and Types of CC Engines
The applications and types of combustion chamber (CC) engines are diverse and pivotal in various sectors, making them a cornerstone of modern technology. This article delves into the multifaceted world of CC engines, exploring their widespread use in both automotive and industrial contexts. We will examine how these engines power vehicles and machinery, highlighting their critical role in transportation and manufacturing. Additionally, the article will detail the different types of CC engines, such as inline, V-type, and rotary configurations, each with its unique advantages and applications. Finally, we will discuss modern innovations and variants that have enhanced efficiency, performance, and environmental sustainability. By understanding these aspects, readers will gain a comprehensive insight into the versatility and importance of CC engines. Transitioning to their practical applications, we begin by exploring their significant impact on automotive and industrial uses.
Automotive and Industrial Uses
In the realm of automotive and industrial applications, CC (Cubic Centimeter) engines play a pivotal role due to their versatility, efficiency, and reliability. Within the automotive sector, CC engines are widely used in various types of vehicles, including motorcycles, scooters, cars, and trucks. For instance, motorcycles often employ smaller CC engines ranging from 50cc to 1000cc, which provide a balance between power and fuel efficiency. In contrast, cars typically use larger CC engines, often between 1000cc to 3000cc or more, to deliver the necessary torque and horsepower for both urban and highway driving. These engines are designed to optimize performance while adhering to stringent emissions standards. In industrial settings, CC engines are utilized in a variety of equipment such as generators, pumps, and machinery. For example, portable generators used in construction sites or emergency power backup systems often rely on smaller CC engines (typically between 200cc to 500cc) for their compact size and high power output relative to their size. Similarly, agricultural machinery like tractors and lawn mowers also depend on robust CC engines that can handle heavy loads and demanding conditions. The choice of engine size in these applications is critical as it must balance power requirements with fuel consumption and maintenance costs. Moreover, the type of CC engine used can significantly impact the performance and longevity of the equipment. For instance, two-stroke engines are commonly found in smaller industrial tools due to their lightweight and high power-to-weight ratio, although they may require more frequent maintenance compared to four-stroke engines. On the other hand, four-stroke engines are preferred in heavier machinery due to their durability and lower emissions. The application-specific design of CC engines also extends to marine vehicles where they must withstand harsh environments such as saltwater and varying temperatures. Here, larger CC engines (often above 2000cc) are used in boats and yachts to provide the necessary propulsion while ensuring reliability and efficiency. In summary, the diverse range of CC engines caters to a broad spectrum of automotive and industrial needs by offering tailored solutions that balance power output with operational efficiency and environmental considerations. Whether it's a high-performance sports car or a rugged industrial generator, the right CC engine is crucial for optimal performance and longevity. This adaptability underscores the significance of understanding the different types and applications of CC engines in various sectors.
Different Types (e.g., Inline, V-Type, Rotary)
In the realm of internal combustion engines, particularly those categorized by their displacement in cubic centimeters (cc), various types of engine configurations play crucial roles in different applications. Among these, inline, V-type, and rotary engines stand out for their unique characteristics and uses. **Inline Engines**: These engines feature cylinders arranged in a straight line along the crankshaft. They are known for their simplicity, balance, and smooth operation. Inline engines can be further divided into inline-4, inline-6, and inline-8 configurations. The inline-4 is the most common due to its compact size and lower production costs, making it ideal for smaller vehicles like sedans and hatchbacks. The inline-6 offers better balance and smoother operation, often used in higher-end vehicles where refinement is paramount. The inline-8, though less common, provides even greater smoothness but is typically found in larger, heavier vehicles due to its length. **V-Type Engines**: V-type engines have cylinders arranged in a V shape around the crankshaft. This configuration allows for a shorter overall length compared to inline engines of similar displacement, making them suitable for larger vehicles where space is limited. Common configurations include V6, V8, and V12. The V6 is widely used in mid-size vehicles for its balance between power and efficiency. The V8 is iconic in American muscle cars and trucks, offering significant power output. The V12 is often found in luxury and high-performance vehicles, providing exceptional smoothness and power. **Rotary Engines**: Unlike traditional piston engines, rotary engines use a rotor instead of a piston to generate power. Developed by Felix Wankel, these engines are known for their high power-to-weight ratio, compact size, and unique sound. Rotary engines are typically found in sports cars like the Mazda RX-7 and RX-8 due to their ability to deliver high performance from a relatively small displacement. However, they are less fuel-efficient and have higher emissions compared to traditional engines. Each type of engine has its own set of advantages and disadvantages, making them suitable for different applications. Inline engines offer simplicity and smooth operation but may lack the compactness of V-type engines. V-type engines provide a balance between power and space efficiency but can be more complex and heavier. Rotary engines excel in performance but struggle with efficiency and emissions. Understanding these differences is crucial for selecting the right engine type for specific needs, whether it's for everyday driving, high-performance applications, or specialized uses such as racing or heavy-duty work.
Modern Innovations and Variants
Modern innovations in combustion chamber (CC) engines have led to significant advancements in efficiency, performance, and environmental sustainability. One notable innovation is the development of direct fuel injection systems, which enhance fuel efficiency by injecting fuel directly into the combustion chamber, allowing for better control over the air-fuel mixture. Another key advancement is the use of turbocharging and supercharging, which increase power output by forcing more air into the combustion chamber, thereby improving engine performance without increasing engine size. Variable Valve Timing (VVT) technology has also become prevalent, enabling engines to optimize valve timing based on driving conditions, resulting in improved fuel efficiency and reduced emissions. Additionally, hybrid and electric-assisted technologies are being integrated into CC engines to reduce emissions and enhance fuel economy. For instance, mild hybrid systems use an electric motor to assist the engine during acceleration, while full hybrid systems can operate the vehicle solely on electric power at low speeds. Advanced materials and manufacturing techniques have further optimized engine design. The use of lightweight materials such as aluminum and magnesium reduces overall engine weight, improving power-to-weight ratios and enhancing fuel efficiency. Moreover, 3D printing and other advanced manufacturing methods allow for the creation of complex engine components with improved thermal management and reduced friction. In terms of variants, modern CC engines come in various configurations tailored to specific applications. For example, inline-four and V6 engines are common in passenger vehicles due to their balance of power and efficiency. Larger V8 engines are often used in heavy-duty trucks and performance vehicles where raw power is a priority. Rotary engines, though less common, offer unique advantages in terms of compactness and smooth operation, making them suitable for certain niche applications. Furthermore, the development of alternative fuel engines has expanded the types of CC engines available. Biofuel-compatible engines can run on renewable fuels such as ethanol or biodiesel, reducing dependence on fossil fuels. Hydrogen fuel cell engines represent another frontier, offering zero-emission operation by converting chemical energy from hydrogen into electrical energy. Overall, these modern innovations and variants of CC engines reflect a continuous effort to improve performance, efficiency, and environmental impact, ensuring that combustion chamber technology remains relevant and competitive in the evolving automotive landscape.