What Is Corra

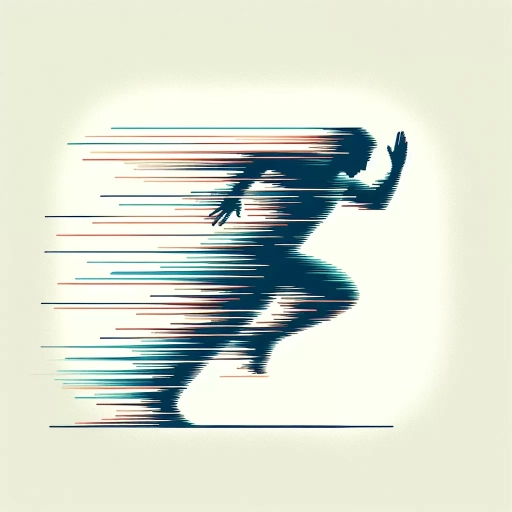
Corrosion is a pervasive and costly issue that affects various industries, from infrastructure and manufacturing to transportation and healthcare. It is a complex process that involves the degradation of materials, particularly metals, due to chemical or electrochemical reactions with their environment. Understanding corrosion is crucial for mitigating its detrimental effects, which can lead to significant economic losses and safety hazards. This article delves into the multifaceted nature of corrosion, starting with a foundational exploration of its definition and basic principles. We will then examine the various causes and factors that contribute to corrosion, highlighting the environmental, chemical, and physical elements that play a role. Finally, we will discuss effective prevention and mitigation strategies that can be employed to combat corrosion. By grasping these fundamental aspects, individuals can better appreciate the importance of addressing corrosion and take proactive steps to protect valuable assets. Let us begin by understanding the basics of corrosion, which forms the cornerstone of our comprehensive analysis.
Understanding Corrosion: Definition and Basics
Understanding corrosion is crucial for maintaining the integrity and longevity of various materials across different industries. Corrosion, a natural process that involves the degradation of materials due to chemical reactions with their environment, can have significant economic and safety implications. To grasp the complexities of corrosion, it is essential to delve into the chemical reactions involved, which fundamentally drive this process. Additionally, recognizing the different types of corrosion—such as uniform, pitting, and crevice corrosion—helps in identifying and mitigating specific risks. Furthermore, understanding which common materials are most affected by corrosion allows for targeted preventive measures. By exploring these aspects, we can better comprehend how corrosion occurs and how to effectively manage it. Let's begin by examining the chemical reactions involved in corrosion, as this foundational knowledge is pivotal in understanding the broader context of this phenomenon.
Chemical Reactions Involved in Corrosion
Corrosion is a complex process that involves various chemical reactions, which ultimately lead to the degradation of materials, particularly metals. At its core, corrosion is an electrochemical reaction that occurs when a metal interacts with its environment, often involving oxygen and moisture. The most common form of corrosion is rusting, which affects iron and its alloys. This process begins with the oxidation of iron in the presence of oxygen and water, resulting in the formation of iron oxide (rust). The reaction can be summarized as follows: iron (Fe) reacts with oxygen (O₂) and water (H₂O) to form iron(III) oxide (Fe₂O₃·H₂O), commonly known as rust. The electrochemical nature of corrosion involves two primary half-reactions: an anodic reaction where the metal loses electrons (oxidation), and a cathodic reaction where electrons are gained (reduction). In the case of rusting, the anodic reaction involves the oxidation of iron to form iron ions (Fe²⁺), while the cathodic reaction involves the reduction of oxygen to form hydroxide ions (OH⁻). These half-reactions occur simultaneously and are interconnected through an electrolyte, such as water or moisture, which facilitates the flow of electrons. Another significant type of corrosion is galvanic corrosion, which occurs when two dissimilar metals are in contact with each other in the presence of an electrolyte. This setup creates a galvanic cell where one metal acts as the anode and the other as the cathode, leading to accelerated corrosion of the more reactive metal. For instance, when copper and zinc are in contact, zinc tends to corrode more rapidly because it is more reactive. Pitting corrosion is another form that involves localized attacks on the metal surface, often resulting in small pits or holes. This type of corrosion can be particularly damaging because it can lead to sudden failure of the material without significant overall loss of mass. Pitting corrosion is often facilitated by the presence of chloride ions, which can penetrate protective oxide layers and initiate localized attacks. Understanding these chemical reactions is crucial for mitigating corrosion. Strategies such as applying protective coatings, using cathodic protection (where an external current is applied to drive the reaction in the opposite direction), and selecting materials that are inherently resistant to corrosion can significantly extend the lifespan of materials. Additionally, controlling environmental factors like humidity and exposure to corrosive substances can also help in preventing or slowing down the corrosion process. In summary, the chemical reactions involved in corrosion are multifaceted and depend on various factors including the type of metal, environmental conditions, and the presence of electrolytes. By grasping these underlying mechanisms, we can better design and implement measures to protect materials from degradation, ensuring their longevity and performance in diverse applications.
Types of Corrosion: Uniform, Pitting, Crevice
Corrosion, a pervasive and costly issue in various industries, manifests in several distinct forms, each with its own characteristics and consequences. Among the most common types are uniform corrosion, pitting corrosion, and crevice corrosion. **Uniform Corrosion** is the most straightforward and predictable form of corrosion. It occurs evenly over the surface of a material, leading to a uniform thinning of the metal. This type of corrosion is often seen in environments where the conditions are consistent across the surface, such as in atmospheric exposure or immersion in a uniform solution. Uniform corrosion can be managed through the application of protective coatings or the selection of materials that are inherently resistant to the corrosive environment. **Pitting Corrosion**, on the other hand, is localized and highly destructive. It involves the formation of small pits or holes on the surface of the material, which can penetrate deeply into the metal. Pitting corrosion often occurs in environments where there are localized differences in oxygen concentration or where there are small imperfections in protective coatings. This type of corrosion is particularly dangerous because it can lead to sudden failures without significant prior warning signs. Materials susceptible to pitting corrosion include stainless steels and aluminum alloys, especially when exposed to chloride ions. **Crevice Corrosion** is another localized form of corrosion that occurs within narrow gaps or crevices between two surfaces. These areas can trap moisture and corrosive substances, creating an environment conducive to corrosion while the surrounding areas remain unaffected. Crevice corrosion is common in marine environments and can be exacerbated by the presence of debris or poor design that creates tight spaces. To mitigate crevice corrosion, designers often use techniques such as increasing the size of gaps, using non-absorbent materials for gaskets, and ensuring good drainage. Understanding these types of corrosion is crucial for developing effective strategies for prevention and mitigation. By recognizing the specific conditions that lead to uniform, pitting, or crevice corrosion, engineers and maintenance professionals can select appropriate materials, design systems to minimize risk, and implement protective measures such as coatings or cathodic protection. This knowledge not only extends the lifespan of equipment but also enhances safety and reduces operational costs associated with premature failures due to corrosion. In summary, recognizing and addressing these different forms of corrosion is essential for maintaining integrity and performance across various industrial applications.
Common Materials Affected by Corrosion
Corrosion, a natural process that degrades materials, particularly metals, due to chemical or electrochemical reactions with their environment, affects a wide range of common materials. Understanding which materials are most susceptible to corrosion is crucial for preventing damage and extending the lifespan of structures and equipment. **Metals** are among the most commonly affected by corrosion. **Iron and steel**, for instance, are prone to rusting when exposed to moisture and oxygen, leading to significant structural weakening. **Aluminum**, while generally resistant due to its oxide layer, can corrode in acidic or alkaline environments. **Copper**, often used in plumbing and electrical wiring, can corrode when exposed to oxygen and moisture, forming green patina. **Zinc**, frequently used as a protective coating for steel (galvanization), itself corrodes in acidic conditions. **Non-metallic materials** are also vulnerable to various forms of degradation. **Concrete**, a composite material made from cement, water, and aggregate, can suffer from chemical corrosion when exposed to acidic substances or seawater, leading to the degradation of its reinforcing steel. **Wood**, though not typically associated with corrosion in the same way as metals, can be affected by biological corrosion such as rot and decay when exposed to moisture and fungi. **Polymers** and **plastics**, while generally resistant to many corrosive agents, can degrade under UV light or when exposed to certain chemicals. The impact of corrosion on these materials is not just economic but also safety-critical. For example, the failure of steel structures due to rust can lead to catastrophic collapses in bridges or buildings. Similarly, the corrosion of aluminum in aircraft components can compromise airworthiness. In marine environments, the corrosion of ship hulls and offshore platforms poses significant risks to both human life and the environment. To mitigate these risks, various protective measures are employed. **Coatings** such as paint or varnish provide a barrier between the material and its environment. **Cathodic protection**, where an electric current is applied to drive the corrosion reaction in the opposite direction, is commonly used for pipelines and ship hulls. **Galvanization**, as mentioned earlier, involves coating steel with zinc to protect it from rusting. Understanding which materials are most susceptible to corrosion and implementing appropriate preventive measures are essential steps in managing this pervasive issue effectively. In summary, corrosion affects a broad spectrum of materials across different industries and environments. Recognizing the specific vulnerabilities of metals like iron, aluminum, copper, and zinc, as well as non-metallic materials such as concrete and wood, is key to developing strategies for their protection. By understanding these dynamics and applying appropriate protective techniques, we can significantly reduce the economic and safety impacts associated with corrosion.
Causes and Factors Contributing to Corrosion
Corrosion, a pervasive and costly issue, is influenced by a multifaceted array of factors that collectively determine its severity and impact. Understanding these causes is crucial for mitigating the effects of corrosion and ensuring the longevity of materials. This article delves into three primary categories that contribute to corrosion: Environmental Factors, Material Properties, and Human Activities. Environmental Factors, including moisture, salinity, and temperature, play a significant role in initiating and accelerating corrosion processes. Material Properties such as reactivity and surface finish also significantly influence how materials interact with their environment. Additionally, Human Activities like poor maintenance and inadequate design can exacerbate the problem. By examining these interrelated factors, we can develop comprehensive strategies to combat corrosion. Let us begin by exploring how Environmental Factors, particularly moisture, salinity, and temperature, set the stage for corrosive processes to unfold.
Environmental Factors: Moisture, Salinity, Temperature
Environmental factors play a crucial role in the process of corrosion, with moisture, salinity, and temperature being among the most significant contributors. **Moisture** is a primary catalyst for corrosion as it facilitates the electrochemical reactions that lead to the degradation of materials. When metal surfaces are exposed to moisture, either from humidity or direct contact with water, it creates an environment conducive to the formation of electrolytes. This can accelerate the oxidation process, particularly in metals like iron and steel, leading to rust formation. In marine environments, moisture combined with salt and other contaminants exacerbates this issue, making it a critical factor in coastal and offshore infrastructure. **Salinity** further complicates the corrosion process by introducing chloride ions into the environment. Chlorides are highly corrosive and can penetrate protective coatings or passivate layers on metals, initiating pitting and crevice corrosion. In marine environments, seawater's high salinity levels make it particularly corrosive to metals such as aluminum, stainless steel, and carbon steel. Even in non-marine settings, de-icing salts used on roads during winter months can significantly increase the salinity of the environment, posing a risk to vehicles and infrastructure. **Temperature** also has a profound impact on corrosion rates. Generally, higher temperatures increase the rate of chemical reactions, including those involved in corrosion processes. Elevated temperatures can enhance the diffusion of reactants and products, accelerate the breakdown of protective films, and increase the solubility of gases in water, all of which contribute to faster corrosion rates. Conversely, lower temperatures can slow down these processes but may not eliminate them entirely. For instance, in cold climates where de-icing salts are used, the combination of salt and moisture at lower temperatures still poses a significant risk to metal structures. The interplay between these environmental factors can be particularly detrimental. For example, in coastal areas where high temperatures and humidity are common during summer months, the presence of salt in the air (sea spray) can lead to accelerated corrosion of metal components. Similarly, in industrial settings where high temperatures are generated during operations (such as power plants or chemical processing facilities), the presence of moisture and contaminants can exacerbate corrosion issues. Understanding these environmental factors is crucial for developing effective strategies to mitigate corrosion. This includes selecting materials that are resistant to specific environmental conditions, applying protective coatings or cathodic protection systems, and implementing regular maintenance and inspection protocols to detect early signs of corrosion. By acknowledging the role of moisture, salinity, and temperature in the corrosion process, engineers and maintenance professionals can design more durable infrastructure and extend the lifespan of critical assets.
Material Properties: Reactivity, Surface Finish
Material properties, particularly reactivity and surface finish, play a crucial role in determining the susceptibility of materials to corrosion. **Reactivity** refers to the inherent tendency of a material to undergo chemical reactions, especially with its environment. Metals and alloys with high reactivity, such as those in the alkali and alkaline earth groups, are more prone to corrosion because they readily lose electrons to form ions. For instance, magnesium and aluminum have high reactivity due to their low ionization energies and high electronegativities, making them more susceptible to oxidation and subsequent corrosion when exposed to air or moisture. In contrast, noble metals like gold and platinum exhibit low reactivity due to their full outer electron shells, which makes them highly resistant to corrosion. **Surface finish** is another critical factor that influences the corrosion behavior of materials. The surface finish can significantly affect the rate of corrosion by altering the contact area between the material and its environment. A smooth surface finish reduces the number of microscopic crevices and imperfections where corrosive substances can accumulate, thereby minimizing the risk of localized corrosion such as pitting or crevice corrosion. Conversely, a rough surface finish provides more sites for corrosive agents to adhere and initiate corrosion processes. Additionally, surface treatments like polishing or coating can enhance the protective properties of a material by creating a barrier against corrosive substances. For example, applying a thin layer of chromium or zinc on steel (galvanizing) not only improves its aesthetic appeal but also provides an additional layer of protection against environmental factors that could lead to corrosion. The interplay between reactivity and surface finish is complex and can be influenced by various environmental factors such as temperature, humidity, and exposure to specific chemicals. In marine environments, for instance, the combination of high salt concentrations and moisture accelerates the corrosion process in reactive metals like iron and copper unless they are protected with appropriate coatings or surface treatments. Understanding these material properties is essential for selecting appropriate materials for specific applications and implementing effective strategies to mitigate corrosion risks. In summary, the reactivity and surface finish of materials are pivotal in determining their resistance to corrosion. By selecting materials with low reactivity and ensuring a smooth surface finish through appropriate treatments or coatings, engineers can significantly reduce the likelihood of corrosion-related failures in various industrial and everyday applications. This knowledge is crucial for designing durable structures and products that withstand environmental challenges over time.
Human Activities: Poor Maintenance, Inadequate Design
Human activities play a significant role in the onset and progression of corrosion, particularly through poor maintenance and inadequate design. Poor maintenance is a critical factor that exacerbates corrosion. When equipment, infrastructure, or materials are not regularly inspected and maintained, they become more susceptible to environmental factors that accelerate corrosion. For instance, failing to clean surfaces can lead to the accumulation of corrosive substances such as salts, acids, and moisture. Similarly, neglecting to apply protective coatings or replace worn-out parts can expose underlying materials to corrosive environments. Inadequate maintenance also includes insufficient lubrication, which can lead to friction-induced wear and tear, creating micro-scratches that serve as initiation sites for corrosion. Inadequate design is another human activity that significantly contributes to corrosion. Design flaws can create conditions that are conducive to corrosion. For example, designing systems with crevices or tight spaces where moisture can accumulate but cannot be easily drained creates ideal environments for localized corrosion. Additionally, using incompatible materials in close proximity can lead to galvanic corrosion, where one material acts as an anode and another as a cathode, accelerating the corrosion process. Poor drainage systems and inadequate ventilation in structures can also trap moisture and pollutants, fostering corrosive conditions. Furthermore, designs that do not account for environmental factors such as temperature fluctuations, humidity levels, and exposure to corrosive substances can lead to premature failure of materials. The interplay between poor maintenance and inadequate design often results in a synergistic effect that accelerates corrosion beyond what either factor alone would cause. For instance, a poorly designed drainage system that is also poorly maintained can lead to chronic waterlogging, which not only corrodes metal components but also degrades concrete and other building materials. Understanding these human-induced factors is crucial for developing effective strategies to mitigate corrosion. By emphasizing regular maintenance practices and adopting robust design principles that account for potential corrosive environments, we can significantly extend the lifespan of materials and infrastructure, thereby reducing economic losses and enhancing safety. Addressing these issues requires a multidisciplinary approach involving engineers, maintenance personnel, and policymakers to ensure that both new constructions and existing infrastructure are designed and maintained with corrosion prevention in mind.
Prevention and Mitigation Strategies for Corrosion
Preventing and mitigating corrosion is a critical aspect of maintaining the integrity and longevity of various structures and equipment across multiple industries. Effective strategies to combat corrosion involve a multifaceted approach, incorporating several key methods. One of the most fundamental techniques is the use of coatings and surface treatments, such as paints and galvanizing, which provide a protective barrier against corrosive elements. Additionally, cathodic protection is a highly effective method that involves applying an electric current to drive the corrosion reaction in a direction that prevents damage. Lastly, careful material selection and design considerations are essential to ensure that the chosen materials are inherently resistant to corrosion and are designed to minimize exposure to corrosive environments. By understanding and implementing these strategies, individuals and organizations can significantly reduce the economic and environmental impacts of corrosion. This article will delve into these critical prevention and mitigation strategies, starting with the importance of coatings and surface treatments, such as paints and galvanizing.
Coatings and Surface Treatments: Paints, Galvanizing
In the realm of corrosion prevention and mitigation, coatings and surface treatments play a pivotal role in safeguarding materials against the detrimental effects of environmental exposure. Among these protective measures, paints and galvanizing stand out as highly effective strategies. **Paints** are one of the most widely used coatings due to their versatility and ease of application. They form a physical barrier between the substrate and the corrosive environment, preventing moisture, oxygen, and other corrosive agents from coming into contact with the material. Modern paint formulations often include additives such as inhibitors, which can further enhance their protective capabilities by neutralizing corrosive substances. The choice of paint depends on the specific application; for instance, epoxy paints are known for their excellent adhesion and chemical resistance, making them ideal for industrial settings, while acrylic paints offer good UV resistance and are commonly used in architectural applications. Regular maintenance, including periodic inspections and reapplication as needed, is crucial to ensure the longevity of paint coatings. **Galvanizing**, on the other hand, involves applying a protective zinc coating to steel or iron surfaces. This process leverages the sacrificial nature of zinc, which corrodes preferentially to the underlying metal, thereby protecting it from rust. Galvanizing can be achieved through hot-dip galvanizing, where the metal is immersed in a bath of molten zinc, or through electro-galvanizing, where an electric current is used to deposit zinc onto the surface. The resulting zinc layer not only acts as a barrier but also provides cathodic protection to any exposed areas of the base metal. This method is particularly effective for structural steel used in construction and infrastructure projects because it offers long-term protection with minimal maintenance requirements. Both paints and galvanizing offer significant advantages in terms of cost-effectiveness and ease of implementation compared to other corrosion prevention methods. However, their effectiveness can be maximized when combined with other strategies such as proper surface preparation, regular inspections, and the use of complementary protective measures like cathodic protection or inhibitors. By integrating these coatings and surface treatments into a comprehensive corrosion management plan, industries can significantly extend the lifespan of their assets, reduce maintenance costs, and enhance overall safety and reliability. Ultimately, the selection and application of appropriate coatings and surface treatments are critical components in a robust defense against corrosion, ensuring that materials remain durable and functional over their intended service life.
Cathodic Protection: Principles and Applications
Cathodic protection is a cornerstone in the prevention and mitigation of corrosion, particularly for metal structures exposed to corrosive environments. This technique involves applying an electric current to the structure to be protected, thereby driving the electrochemical reaction in a direction that inhibits corrosion. The principles of cathodic protection are rooted in electrochemistry, where the protected metal is made the cathode of an electrochemical cell. By introducing an external current, typically from a sacrificial anode or an impressed current system, the potential of the protected metal is shifted to a more negative value, reducing the likelihood of oxidation and thus preventing corrosion. In practical applications, cathodic protection is widely used to safeguard underground pipelines, marine structures, and other buried or submerged metallic assets. For instance, in the oil and gas industry, cathodic protection systems are essential for protecting pipelines from soil corrosion, which can lead to leaks and environmental hazards. Similarly, in marine environments, cathodic protection helps extend the lifespan of ship hulls and offshore platforms by mitigating the corrosive effects of seawater. The effectiveness of cathodic protection depends on several factors including the type of metal being protected, the nature of the corrosive environment, and the design and maintenance of the protection system. The two primary methods of cathodic protection are sacrificial anode systems and impressed current systems. Sacrificial anode systems rely on the natural potential difference between the protected metal and a more reactive metal (the anode), which corrodes in place of the protected structure. This method is simpler and often used for smaller structures or in situations where power supply is limited. Impressed current systems, on the other hand, use an external power source to drive the protective current, offering greater flexibility and control over the protection level. These systems are more commonly used for larger structures or in highly corrosive environments. Proper design and installation of cathodic protection systems are crucial for their effectiveness. This includes selecting appropriate materials for both the anodes and the protected structure, ensuring adequate current distribution, and monitoring the system's performance over time. Regular maintenance involves checking the potential of the protected metal against a reference electrode to ensure it remains within a safe range, typically between -0.85V and -1.20V versus a copper sulfate electrode for steel structures. In addition to its technical aspects, cathodic protection also offers significant economic benefits by extending the lifespan of critical infrastructure, reducing maintenance costs, and minimizing the risk of catastrophic failures. For example, in the water treatment industry, cathodic protection can protect storage tanks and distribution pipes from corrosion, ensuring the integrity of water supply systems. Overall, cathodic protection stands as a robust and reliable strategy for preventing and mitigating corrosion across various industries, underscoring its importance in maintaining the durability and safety of metal structures in diverse environments.
Material Selection and Design Considerations
When it comes to preventing and mitigating corrosion, one of the most critical strategies is the careful selection of materials and thoughtful design considerations. Material selection is a multifaceted process that involves understanding the environmental conditions in which the material will operate, as well as its inherent properties and potential interactions with other substances. For instance, in marine environments where seawater is present, materials such as stainless steel, titanium, or fiber-reinforced polymers (FRP) are often preferred due to their high resistance to corrosion. In contrast, for applications involving acidic or alkaline substances, materials like polyvinylidene fluoride (PVDF) or high-density polyethylene (HDPE) may be more suitable. Design considerations are equally important and should be integrated from the outset of any project. This includes ensuring that the design minimizes crevices and areas where moisture can accumulate, as these are common sites for corrosion initiation. Proper drainage and ventilation can also significantly reduce the risk of corrosion by preventing the buildup of corrosive substances. Additionally, the use of coatings and linings can provide an extra layer of protection against corrosive environments. For example, applying a protective coating such as epoxy or polyurethane to steel structures can significantly extend their lifespan in harsh conditions. Another key design consideration is the avoidance of galvanic corrosion, which occurs when two dissimilar metals are in contact with each other in the presence of an electrolyte. This can be mitigated by selecting materials that are compatible with each other or by using insulating materials to separate them. Furthermore, cathodic protection systems can be implemented to protect metal structures from corrosion by making them the cathode of an electrochemical cell. Incorporating these material selection and design strategies into the initial stages of a project not only helps in preventing corrosion but also reduces maintenance costs and extends the lifespan of the structure or equipment. It is essential to consult with materials engineers and corrosion specialists to ensure that the chosen materials and design elements are optimized for the specific application and environment. By doing so, industries can significantly reduce the economic and environmental impacts associated with corrosion, leading to safer, more efficient, and sustainable operations. Ultimately, a well-planned approach to material selection and design is crucial for effective corrosion prevention and mitigation.