What Is Frp

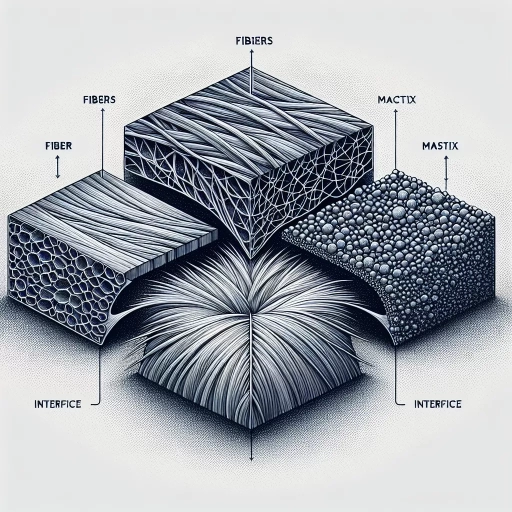
Fiber Reinforced Polymer (FRP) has emerged as a transformative material in various industries, including construction, aerospace, and automotive. Its unique blend of strength, durability, and lightweight properties makes it an attractive alternative to traditional materials. This article delves into the multifaceted world of FRP, starting with an **Introduction to FRP**, where we explore its fundamental principles and applications. We then examine the **Materials and Manufacturing Process**, detailing the components and techniques involved in producing FRP. Finally, we discuss the **Advantages, Limitations, and Future Prospects** of FRP, highlighting its benefits, challenges, and potential for future innovation. By understanding these aspects, readers will gain a comprehensive insight into why FRP is becoming a cornerstone in modern engineering and design. Let us begin our journey into the world of FRP with an **Introduction to FRP**.
Introduction to FRP
Fiber Reinforced Polymer (FRP) is a versatile and innovative material that has revolutionized various industries with its exceptional strength, durability, and lightweight properties. This introduction to FRP will delve into the fundamental aspects of this technology, starting with a clear definition and explanation of the acronym. Understanding what FRP stands for and its basic composition is crucial for grasping its broader implications. Historically, the development of FRP has been a gradual process, influenced by advancements in materials science and engineering. From its early applications in aerospace to its current widespread use in civil engineering, automotive, and marine industries, FRP has evolved significantly over the years. Today, FRP finds common applications across diverse sectors due to its unique characteristics. It is used in structural reinforcement, vehicle manufacturing, and even in medical devices. The versatility of FRP makes it an indispensable material in modern engineering. To fully appreciate the significance of FRP, it is essential to begin with a clear understanding of its definition and acronym. This foundational knowledge will provide a solid base for exploring its historical development and common applications, ultimately revealing why FRP has become such a critical component in contemporary engineering practices.
Definition and Acronym
In the context of "Introduction to FRP," understanding the definitions and acronyms associated with Fiber-Reinforced Polymer (FRP) is crucial for grasping the fundamental principles and applications of this advanced material. **FRP** stands for Fiber-Reinforced Polymer, a composite material consisting of fibers embedded in a polymer matrix. This matrix can be made from various types of polymers such as epoxy, vinyl ester, or polyester, while the fibers are typically carbon, glass, or aramid. The combination of these components results in a material that offers superior strength-to-weight ratio, corrosion resistance, and durability compared to traditional materials like steel or concrete. Key acronyms and terms include **CFRP** (Carbon Fiber-Reinforced Polymer), which is a specific type of FRP that uses carbon fibers known for their exceptional tensile strength and stiffness. **GFRP** (Glass Fiber-Reinforced Polymer) is another common variant, often used in applications where cost-effectiveness is a priority due to the lower cost of glass fibers compared to carbon fibers. **Aramid Fiber-Reinforced Polymer** or **AFRP** uses aramid fibers, which are renowned for their high tensile strength and resistance to heat and chemicals. Understanding these definitions and acronyms is essential because they denote different properties and applications within the broader category of FRP. For instance, CFRP is frequently used in aerospace and high-performance sports equipment due to its lightweight yet robust characteristics. On the other hand, GFRP is widely employed in civil engineering projects such as bridge construction and building facades because it offers a balance between performance and affordability. Moreover, terms like **pultrusion** and **hand layup** refer to different manufacturing processes used to create FRP products. Pultrusion involves pulling fibers through a resin bath and then curing them in a die to form continuous profiles, while hand layup involves manually placing layers of fibers and resin in a mold before curing. These processes can significantly impact the final product's quality and suitability for various applications. In summary, familiarity with the definitions and acronyms related to FRP is vital for appreciating its versatility and potential uses across diverse industries. By understanding what each term signifies, individuals can better navigate the complexities of FRP technology and make informed decisions about its application in different contexts. This foundational knowledge sets the stage for a deeper exploration into the world of FRP, enabling a comprehensive understanding of its benefits, limitations, and future potential.
Historical Development
The historical development of Fiber-Reinforced Polymers (FRP) is a narrative of continuous innovation and adaptation, reflecting the evolving needs of various industries. The concept of reinforcing materials with fibers dates back to ancient civilizations, where Egyptians and Phoenicians used plant fibers to strengthen clay and mud for constructing boats and buildings. However, the modern era of FRP began to take shape in the mid-20th century. In the 1940s and 1950s, the first synthetic fibers such as nylon and polyester were developed, laying the groundwork for composite materials. The introduction of glass fibers in the 1950s marked a significant milestone, as they were found to be particularly effective in reinforcing polymers. This led to the creation of the first glass fiber-reinforced plastic (GFRP), which was initially used in boat hulls and other marine applications due to its lightweight yet durable properties. The 1960s saw a surge in the use of FRP in aerospace and automotive industries. Carbon fibers, discovered in the late 1950s, became integral to these sectors due to their exceptional strength-to-weight ratio. The development of advanced manufacturing techniques such as hand layup, spray-up, and pultrusion further expanded the application scope of FRP. By the 1970s, FRP had become a staple in various engineering fields, including civil engineering, where it was used for bridge repair and construction. The 1980s and 1990s witnessed significant advancements in material science and engineering, leading to the development of new types of fibers like aramid and basalt. These fibers offered improved thermal resistance and impact strength, making FRP even more versatile. The introduction of advanced resin systems and hybrid composites also enhanced the performance characteristics of FRP. In recent years, the focus has shifted towards sustainability and environmental impact. Researchers have been exploring the use of natural fibers such as hemp, flax, and bamboo to create biodegradable composites. Additionally, recycling technologies for FRP waste have been developed to address the growing concern of end-of-life disposal. Today, FRP is ubiquitous across multiple sectors including aerospace, automotive, construction, and sports equipment. Its ability to offer tailored properties such as high strength, low weight, corrosion resistance, and design flexibility has made it an indispensable material in modern engineering. As technology continues to evolve, the historical development of FRP serves as a testament to human ingenuity and the relentless pursuit of innovation, setting the stage for even more groundbreaking applications in the future. This rich history underscores the importance of understanding FRP's origins and evolution as we delve into its current applications and future potential.
Common Applications
**Common Applications of FRP** Fiber Reinforced Polymers (FRP) have revolutionized various industries with their unique combination of strength, durability, and versatility. One of the most significant advantages of FRP is its ability to be tailored for specific applications, making it a go-to material in diverse fields. In the construction industry, FRP is widely used for structural reinforcement and repair. For instance, FRP rebar is increasingly replacing traditional steel rebar due to its resistance to corrosion and superior tensile strength, ensuring longer lifespan and reduced maintenance costs for buildings and bridges. Additionally, FRP composite materials are used in seismic retrofitting to enhance the structural integrity of existing structures, providing critical safety improvements. In the aerospace sector, FRP composites play a crucial role in manufacturing lightweight yet incredibly strong components such as aircraft wings, fuselage, and control surfaces. The reduced weight achieved through the use of FRP directly translates into fuel efficiency and enhanced performance, making it an indispensable material for modern aircraft design. Similarly, in the automotive industry, FRP is used to produce lightweight body panels and chassis components, contributing to improved fuel economy and reduced emissions. The marine industry also benefits significantly from FRP applications. Boat hulls and decks made from FRP composites offer excellent resistance to water absorption and corrosion, ensuring longevity and minimal maintenance needs. Moreover, the lightweight nature of these materials allows for faster boat speeds without compromising on structural integrity. In civil engineering projects such as pipelines and tanks, FRP composites are preferred due to their resistance to chemical corrosion and ability to withstand extreme environmental conditions. This makes them ideal for transporting corrosive substances like oil and gas over long distances without the risk of leakage or contamination. Furthermore, FRP finds extensive use in medical devices due to its biocompatibility and ability to be sterilized. Orthopedic implants such as hip replacements and dental prosthetics often utilize FRP composites because they can mimic the natural properties of bone tissue while providing necessary strength and durability. The renewable energy sector also leverages FRP composites in wind turbine blades and solar panel frames due to their high strength-to-weight ratio and resistance to fatigue under cyclic loading conditions. These characteristics ensure optimal performance over extended periods even in harsh weather conditions. Lastly, FRP is gaining traction in consumer goods such as sports equipment like bicycle frames, golf clubs, and tennis rackets where its lightweight yet robust nature enhances user performance without compromising on safety. In summary, the versatility of FRP composites has led to their widespread adoption across multiple industries where they offer significant advantages over traditional materials in terms of strength, durability, weight reduction, and resistance to environmental degradation. As technology continues to evolve, it is likely that new applications for FRP will emerge further solidifying its position as a material of choice for innovative engineering solutions.
Materials and Manufacturing Process
In the realm of materials and manufacturing, understanding the intricacies of various components and processes is crucial for producing high-quality products. This article delves into three key aspects that underpin the creation of advanced materials: types of fibers used, matrix materials and their properties, and manufacturing techniques and methods. Each of these elements plays a vital role in determining the final product's performance, durability, and functionality. The selection of appropriate fibers, for instance, can significantly impact the mechanical strength and thermal resistance of a composite material. Similarly, the choice of matrix materials influences the overall properties such as toughness, stiffness, and resistance to environmental factors. Finally, the manufacturing techniques employed can affect the uniformity, consistency, and cost-effectiveness of the production process. By examining these three critical components, manufacturers can optimize their production processes to achieve superior outcomes. Let us begin by exploring the diverse types of fibers used in modern manufacturing, which form the foundational building blocks of many advanced materials.
Types of Fibers Used
In the realm of Fiber Reinforced Polymers (FRP), the type of fiber used is a critical determinant of the material's properties and performance. Fibers serve as the primary reinforcement, providing strength, stiffness, and durability to the composite material. There are several types of fibers commonly employed in FRP manufacturing, each with its unique characteristics and applications. **Glass Fibers** are among the most widely used due to their excellent balance of mechanical properties and cost-effectiveness. They are available in various forms such as E-glass, S-glass, and C-glass, with E-glass being the most common for general-purpose applications. Glass fibers offer good tensile strength, resistance to fatigue, and chemical stability, making them suitable for a broad range of industries including automotive, aerospace, and construction. **Carbon Fibers**, on the other hand, are renowned for their exceptional mechanical properties, including high tensile strength and modulus of elasticity. These fibers are significantly lighter than glass fibers and exhibit superior resistance to fatigue and corrosion. However, they are more expensive and often used in high-performance applications such as aerospace engineering, sports equipment, and advanced automotive components. **Aramid Fibers**, known by their trade names like Kevlar and Nomex, are synthetic fibers that offer a unique combination of high strength-to-weight ratio, toughness, and resistance to heat and chemicals. They are frequently used in ballistic protection gear, composites for aircraft and automotive parts, as well as in industrial applications requiring high thermal stability. **Basalt Fibers** are gaining popularity due to their environmental sustainability and competitive performance with glass fibers. Derived from basalt rock, these fibers exhibit good thermal insulation properties, resistance to chemicals, and a lower environmental impact compared to traditional glass fibers. They find applications in construction materials, automotive parts, and various industrial products. **Natural Fibers** such as hemp, flax, and jute are increasingly being explored for their eco-friendly nature and potential cost savings. These biodegradable fibers can replace synthetic fibers in certain applications while offering comparable mechanical properties. They are particularly appealing for sustainable product development in sectors like automotive interiors and packaging materials. The choice of fiber type is influenced by factors such as the intended application, required mechanical properties, cost constraints, and environmental considerations. Each fiber has its own manufacturing process nuances; for instance, carbon fibers require a complex production process involving high-temperature treatments which contribute to their higher cost. In contrast, glass fibers can be produced through a more straightforward melt-spinning process. Understanding the different types of fibers available is crucial for optimizing the design and manufacturing of FRP products. By selecting the appropriate fiber based on specific requirements, manufacturers can ensure that their FRP materials meet performance standards while also considering economic and environmental factors. This informed approach not only enhances product quality but also contributes to the broader adoption of FRP technology across various industries.
Matrix Materials and Their Properties
Matrix materials are a crucial component in the fabrication of Fiber-Reinforced Polymers (FRP), playing a pivotal role in determining the overall properties and performance of the composite material. The matrix, typically a polymer resin, serves as the binding agent that holds the reinforcing fibers together, distributing loads and stresses across the composite structure. The choice of matrix material is critical because it influences various key properties such as mechanical strength, thermal stability, chemical resistance, and durability. ### Types of Matrix Materials 1. **Thermosetting Resins**: These are the most commonly used matrix materials in FRP production. Epoxy, polyester, and vinyl ester resins fall into this category. Thermosetting resins undergo a chemical reaction during curing, resulting in a rigid and irreversible structure. They offer excellent mechanical properties, resistance to chemicals, and good thermal stability. Epoxy resins, for instance, are known for their high tensile strength and adhesive properties, making them ideal for aerospace and automotive applications. Polyester resins are more cost-effective and widely used in marine and construction industries due to their ease of processing and good balance of mechanical and chemical resistance. 2. **Thermoplastic Resins**: Although less common as matrices in traditional FRP, thermoplastics like polypropylene, polyethylene, and polyamide are gaining attention for their recyclability and potential for reuse. Thermoplastics can be melted and reformed multiple times without undergoing significant chemical change, which is advantageous for sustainable manufacturing practices. However, they generally exhibit lower mechanical properties compared to thermosetting resins. 3. **Hybrid Matrices**: Recent advancements have led to the development of hybrid matrices that combine different types of resins to leverage their respective advantages. For example, blending thermosetting resins with thermoplastics can enhance toughness and impact resistance while maintaining good mechanical strength. ### Properties of Matrix Materials - **Mechanical Properties**: The matrix material significantly affects the tensile strength, compressive strength, and impact resistance of the FRP. High-performance matrices like epoxy resins provide superior mechanical properties, making them suitable for demanding applications. - **Thermal Stability**: The thermal stability of the matrix is crucial for high-temperature applications. Some matrices, such as phenolic resins, offer excellent thermal resistance but may compromise on mechanical properties. - **Chemical Resistance**: The chemical resistance of the matrix is vital for applications where the FRP will be exposed to corrosive environments. Vinyl ester resins, for example, are known for their excellent resistance to acids and bases. - **Adhesion and Interfacial Properties**: The adhesion between the matrix and reinforcing fibers is critical for effective load transfer and overall composite performance. Surface treatments and sizing agents are often used to enhance this interfacial bonding. - **Processability**: The ease of processing is another important factor in selecting a matrix material. Polyester resins, for instance, are popular due to their simple curing process and fast gelation times, which facilitate rapid production cycles. ### Impact on Manufacturing Process The choice of matrix material has a direct impact on the manufacturing process of FRP. For instance: - **Curing Conditions**: Thermosetting resins require specific curing conditions such as temperature, pressure, and time to achieve optimal properties. This necessitates careful control over the manufacturing environment. - **Tooling and Molds**: The viscosity and flow characteristics of the matrix influence the choice of tooling and molds. Low-viscosity matrices are easier to infuse into complex geometries using techniques like resin transfer molding (RTM). - **Fiber Wetting**: The ability of the matrix to wet out fibers efficiently affects the quality of the composite. Surface treatments on fibers can be tailored to improve compatibility with the chosen matrix. In conclusion, matrix materials are a cornerstone in FRP technology, influencing both the final product's performance and the manufacturing process. Understanding their properties and selecting the appropriate matrix is essential for optimizing FRP applications across various industries.
Manufacturing Techniques and Methods
In the realm of materials and manufacturing processes, particularly when discussing Fiber Reinforced Polymers (FRP), understanding various manufacturing techniques is crucial for optimizing production quality, efficiency, and cost-effectiveness. Several key methods are employed in the fabrication of FRP components, each with its own set of advantages and applications. **Hand Lay-Up** is one of the most traditional and widely used techniques, involving the manual placement of fibers and resin onto a mold. This method allows for high flexibility in design but can be labor-intensive and prone to human error. **Vacuum Bagging** enhances the hand lay-up process by applying vacuum pressure to remove air bubbles and excess resin, resulting in higher-quality finishes and improved mechanical properties. **Resin Transfer Molding (RTM)** is a more advanced technique where resin is injected into a mold containing pre-placed fibers under pressure. RTM offers superior surface finish and dimensional accuracy, making it ideal for high-volume production. **Pultrusion** involves pulling continuous fibers through a resin bath and then through a heated die to shape the composite. This method is highly efficient for producing long, uniform profiles such as beams and rods. **Filament Winding** is another technique where continuous fibers are wound onto a mandrel in a specific pattern, often used for cylindrical components like pipes and tanks. **Compression Molding** involves placing pre-impregnated fibers (prepregs) into a mold and applying high pressure and heat to consolidate the material. This method is particularly effective for producing complex geometries with minimal waste. **Autoclave Molding** uses high pressure and temperature within an autoclave to cure prepregs, resulting in high-performance composites with excellent mechanical properties. **3D Printing** or Additive Manufacturing is a newer approach that allows for the creation of complex geometries layer by layer, offering unprecedented design freedom and rapid prototyping capabilities. Each of these manufacturing techniques has its own set of parameters that influence the final product's quality, including fiber orientation, resin content, curing conditions, and post-processing treatments. The choice of method depends on factors such as production volume, desired mechanical properties, surface finish requirements, and cost constraints. By selecting the appropriate manufacturing technique, manufacturers can leverage the unique benefits of FRP materials—such as lightweight, corrosion resistance, and high strength-to-weight ratio—to produce innovative solutions across various industries including aerospace, automotive, construction, and marine engineering. Understanding these techniques not only enhances the efficiency of the manufacturing process but also ensures that the final product meets the stringent performance standards required in these demanding applications.
Advantages, Limitations, and Future Prospects
In the realm of modern engineering and construction, Fiber Reinforced Polymers (FRP) have emerged as a transformative material, offering a myriad of advantages while also presenting some challenges. This article delves into the multifaceted nature of FRP, exploring its strengths and benefits, challenges and limitations, and future trends and innovations. On one hand, FRP boasts exceptional strength-to-weight ratios, corrosion resistance, and ease of installation, making it an ideal choice for various applications from aerospace to civil infrastructure. However, despite these strengths, FRP also faces significant challenges such as high initial costs, limited recyclability, and sensitivity to environmental conditions. Looking ahead, advancements in manufacturing technologies and the integration of smart materials are poised to address these limitations and unlock new potential for FRP. By examining these aspects comprehensively, we can better understand the current state and future prospects of FRP. Let us begin by exploring the strengths and benefits of FRP, which underpin its widespread adoption across diverse industries.
Strengths and Benefits of FRP
Fiber Reinforced Polymers (FRP) have emerged as a revolutionary material in various industries, offering a multitude of strengths and benefits that set them apart from traditional materials. One of the primary advantages of FRP is its exceptional strength-to-weight ratio, making it an ideal choice for applications where both durability and lightness are crucial. This property is particularly beneficial in aerospace, automotive, and construction sectors, where reducing weight can lead to significant improvements in fuel efficiency, performance, and structural integrity. Another key benefit of FRP is its resistance to corrosion and chemical degradation. Unlike metals, which can corrode over time when exposed to harsh environments, FRP maintains its structural integrity even in the presence of corrosive substances. This makes it a preferred material for marine and offshore structures, as well as for use in chemical plants and other industrial settings where exposure to corrosive agents is common. The versatility of FRP is another significant strength. It can be tailored to meet specific requirements by adjusting the type and orientation of fibers, the matrix material, and the manufacturing process. This flexibility allows FRP to be used in a wide range of applications, from high-performance sports equipment to medical devices and advanced composites for renewable energy systems. Furthermore, FRP offers excellent fatigue resistance compared to many traditional materials. This means that FRP components can withstand repeated loading and unloading cycles without suffering from significant degradation, making them suitable for dynamic environments such as bridges, aircraft, and wind turbines. In addition to these mechanical advantages, FRP also provides several economic benefits. The manufacturing process for FRP can be more cost-effective than traditional methods, especially for complex geometries or large-scale productions. Moreover, the reduced maintenance needs due to its corrosion resistance and durability translate into lower lifecycle costs. From an environmental perspective, FRP offers several advantages as well. It can be designed to be recyclable or reusable at the end of its service life, reducing waste and the environmental impact associated with material disposal. Additionally, the lightweight nature of FRP can lead to reduced energy consumption during transportation and operation. In conclusion, the strengths and benefits of FRP make it a highly attractive material across various industries. Its unique combination of high strength, low weight, corrosion resistance, versatility, fatigue resistance, economic advantages, and environmental benefits positions FRP as a key player in modern engineering and construction projects. As technology continues to evolve, the future prospects for FRP look promising, with ongoing research aimed at further enhancing its properties and expanding its applications.
Challenges and Limitations
Despite the numerous advantages of Fiber-Reinforced Polymers (FRP), several challenges and limitations must be considered to fully understand their potential and practical applications. One of the primary challenges is the high initial cost associated with FRP materials and manufacturing processes. While FRP offers long-term benefits such as durability and low maintenance, the upfront investment can be prohibitive for many projects, especially in comparison to traditional materials like steel or concrete. Additionally, the lack of standardization in FRP production and testing protocols can lead to variability in product quality, making it difficult for engineers and architects to predict performance consistently. Another significant limitation is the environmental impact of FRP. The production process involves the use of non-renewable resources and generates significant amounts of waste, which can be detrimental to the environment if not managed properly. Furthermore, the end-of-life disposal of FRP materials poses a challenge due to their non-biodegradable nature and the difficulty in recycling them. This raises concerns about sustainability and long-term environmental responsibility. From a technical standpoint, FRP also faces challenges related to its mechanical properties under various loading conditions. For instance, FRP composites can exhibit poor resistance to impact and fatigue, which can compromise their structural integrity over time. Moreover, the anisotropic nature of FRP means that its properties vary significantly depending on the direction of the fibers, requiring careful design and analysis to ensure optimal performance. In terms of application, the use of FRP in construction and engineering projects is often hindered by regulatory barriers. Many building codes and standards have not yet fully incorporated guidelines for the use of FRP, leading to uncertainty and hesitation among practitioners. This lack of regulatory clarity can slow down the adoption of FRP technologies despite their proven benefits. Finally, there is a need for more comprehensive research and development to address the current limitations of FRP. Advanced manufacturing techniques, such as 3D printing, hold promise for improving the efficiency and cost-effectiveness of FRP production. However, these technologies are still in their infancy and require further investment and innovation to become viable alternatives. In conclusion, while FRP offers a range of advantages that make it an attractive material for various applications, it is crucial to acknowledge and address the challenges and limitations associated with its use. By understanding these limitations, researchers, manufacturers, and policymakers can work towards mitigating them, thereby unlocking the full potential of FRP and ensuring its widespread adoption in the future.
Future Trends and Innovations
As we delve into the future trends and innovations in Fiber Reinforced Polymers (FRP), it becomes evident that this versatile material is poised for significant advancements. One of the most promising trends is the integration of smart technologies, where FRP composites are being infused with sensors and monitoring systems to create intelligent structures. These smart FRPs can detect real-time stress, strain, and environmental conditions, enabling predictive maintenance and enhancing structural integrity. Another innovation on the horizon is the development of sustainable FRPs, where traditional resins are being replaced by bio-based alternatives derived from renewable resources such as plant oils and agricultural waste. This shift not only reduces the carbon footprint but also opens up new avenues for recycling and biodegradability. Advancements in manufacturing techniques are also set to revolutionize the industry. 3D printing technology is gaining traction, allowing for the rapid production of complex FRP structures with unprecedented precision and speed. This method reduces material waste, increases efficiency, and enables the creation of customized components tailored to specific applications. Furthermore, advancements in nanotechnology are leading to the development of nano-reinforced FRPs, which exhibit enhanced mechanical properties, improved thermal stability, and superior resistance to degradation. In terms of future prospects, FRPs are likely to play a crucial role in emerging sectors such as renewable energy and aerospace. For instance, wind turbine blades made from FRPs are becoming more prevalent due to their lightweight yet robust nature, which significantly improves energy efficiency. Similarly, in aerospace engineering, FRPs are being used to manufacture lighter aircraft components, contributing to reduced fuel consumption and lower emissions. However, despite these promising trends and innovations, there are limitations that need to be addressed. The high cost of raw materials and manufacturing processes remains a significant barrier to widespread adoption. Additionally, the lack of standardization in FRP production can lead to variability in product quality, which may hinder large-scale industrial acceptance. In conclusion, while there are challenges to overcome, the future of FRPs looks bright with numerous innovations on the horizon. As technology continues to advance and sustainability becomes a greater priority, FRPs are likely to become even more integral to various industries. By leveraging smart technologies, sustainable materials, advanced manufacturing techniques, and nanotechnology enhancements, FRPs will continue to evolve into a cornerstone material for modern engineering applications.