What Should Be Done Every Month To Prevent Fire Extinguisher From Clumping

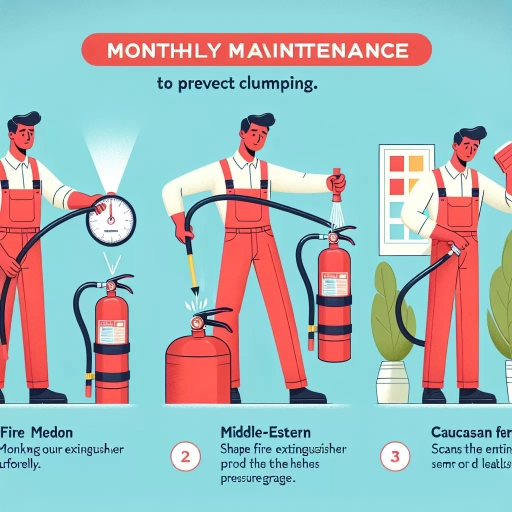
Fire extinguishers are crucial safety devices that must be in optimal working condition to ensure effective response in the event of a fire. However, over time, these devices can become less reliable due to clumping of the extinguishing agent, which can render them ineffective when needed most. To prevent this, regular maintenance and proper care are essential. This article will delve into the critical steps necessary to keep fire extinguishers in prime condition, focusing on three key areas: Monthly Inspection and Maintenance, Proper Storage and Handling, and Regular Testing and Certification. By adhering to these guidelines, individuals can ensure their fire extinguishers remain functional and ready for use. Starting with the foundational aspect of Monthly Inspection and Maintenance, it is imperative to understand the importance of regular checks to identify any potential issues before they escalate. This proactive approach sets the stage for a comprehensive fire safety strategy that safeguards lives and property. --- **Monthly Inspection and Maintenance**
Monthly Inspection and Maintenance
Regular monthly inspections and maintenance are crucial for ensuring the optimal performance, safety, and longevity of equipment and systems. These routine checks help identify potential issues before they escalate into major problems, thereby preventing downtime and reducing the risk of accidents. A comprehensive monthly inspection typically includes several key components. First, a **Visual Check for Damage or Wear** is essential to detect any visible signs of deterioration or damage that could compromise the integrity of the equipment. Additionally, **Pressure Gauge Verification** ensures that all pressure-related systems are operating within safe and specified limits, which is vital for maintaining operational efficiency and preventing catastrophic failures. Lastly, **Label and Instruction Legibility** must be verified to ensure that all necessary information is clear and accessible, facilitating proper use and maintenance by users. By incorporating these elements into a monthly inspection routine, organizations can significantly enhance their operational reliability and safety standards. Let's begin by delving into the importance of a **Visual Check for Damage or Wear**.
Visual Check for Damage or Wear
**Visual Check for Damage or Wear** As part of your monthly inspection and maintenance routine, a thorough visual check for damage or wear on your fire extinguishers is crucial to ensure they remain in optimal working condition. This step is often overlooked but is vital in preventing potential failures during emergencies. Start by inspecting the exterior of the extinguisher for any signs of physical damage, such as dents, cracks, or corrosion. Check the hose and nozzle for blockages, kinks, or damage that could impede proper function. The pressure gauge should be inspected to ensure it is within the designated operating range; if it falls outside this range, the extinguisher may need to be recharged or replaced. Next, examine the safety pin or tamper seal to verify that it has not been removed or tampered with. Ensure all labels and instructions are legible and securely attached. Look for any signs of leakage around the valve stem or other connections. If you notice any rust, corrosion, or other forms of deterioration on metal components, it may be necessary to replace these parts to maintain the integrity of the extinguisher. Additionally, check the weight of the extinguisher to ensure it has not lost pressure over time. For water-based extinguishers, inspect the liquid level through the sight gauge; if it is below the minimum mark, the extinguisher needs to be refilled or replaced. For dry chemical extinguishers, check for any signs of settling or compaction which could affect their performance. Regular visual inspections also help in identifying environmental factors that might affect the extinguisher's condition. For instance, if an extinguisher is exposed to extreme temperatures, moisture, or direct sunlight, it may degrade faster than expected. By addressing these issues promptly through regular checks and necessary maintenance actions like cleaning and drying, you can significantly extend the lifespan of your fire extinguishers. Incorporating a systematic approach to visual checks ensures that no critical aspect is overlooked. Use a checklist to guide your inspection process and document any findings or actions taken. This not only helps in maintaining compliance with safety regulations but also provides a record of maintenance activities which can be useful during audits or inspections by regulatory bodies. By dedicating a few minutes each month to conducting a thorough visual check for damage or wear on your fire extinguishers, you significantly reduce the risk of equipment failure and ensure that these critical safety devices are always ready to perform when needed. This proactive approach aligns with best practices in fire safety management and contributes to a safer environment for everyone.
Pressure Gauge Verification
**Pressure Gauge Verification** As part of the monthly inspection and maintenance routine for fire extinguishers, verifying the pressure gauge is a critical step that ensures these life-saving devices are always ready to function effectively. Pressure gauges on fire extinguishers indicate whether the internal pressure is within the acceptable range, which is essential for maintaining the extinguisher's operational integrity. Here’s why this verification is crucial: 1. **Ensuring Proper Functionality**: The pressure gauge provides a quick visual check to confirm that the extinguisher has not leaked or been compromised. If the needle is outside the green zone, it may indicate a loss of pressure, which could render the extinguisher ineffective in an emergency. 2. **Preventing Clumping**: For dry chemical extinguishers, maintaining the correct pressure helps prevent clumping of the powder. Clumping can occur if moisture enters the cylinder or if there is a significant drop in pressure, making it difficult to discharge the agent when needed. 3. **Compliance with Regulations**: Regular verification of pressure gauges is often mandated by local fire safety codes and regulations. Ensuring compliance helps avoid fines and penalties while also contributing to a safer environment. 4. **Early Detection of Issues**: Monthly checks allow for early detection of any issues with the extinguisher, such as leaks or corrosion, which can be addressed promptly before they become major problems. 5. **User Confidence**: Knowing that the pressure gauge has been verified monthly gives users confidence in the reliability of their fire extinguishers, which is vital in high-stress emergency situations. To perform this verification effectively: - **Visual Inspection**: Check the gauge for any signs of damage or tampering. - **Needle Position**: Ensure the needle is within the designated green zone on the gauge face. - **Record Keeping**: Document each inspection, noting any discrepancies or actions taken. - **Training**: Ensure that all personnel responsible for inspections are properly trained to recognize and address any issues they might encounter. By incorporating pressure gauge verification into your monthly inspection routine, you not only ensure that your fire extinguishers are in optimal working condition but also contribute to a safer and more compliant environment. This proactive approach helps prevent clumping in dry chemical extinguishers and ensures that these critical safety devices are always ready to protect lives and property.
Label and Instruction Legibility
**Label and Instruction Legibility** Ensuring the legibility of labels and instructions on fire extinguishers is a critical component of monthly inspection and maintenance. Clear and readable labels are essential for quick identification and proper use of the extinguisher in emergency situations. Over time, labels can become worn, faded, or damaged due to environmental factors such as moisture, sunlight, or physical wear. Monthly inspections should include a thorough check of all labels to ensure they remain intact and easily readable. Any signs of deterioration, such as peeling, discoloration, or illegibility, should prompt immediate replacement with new labels. Moreover, the instructions provided on the label must be clear and concise. These instructions guide users on how to operate the extinguisher effectively, including steps like the PASS method (Pull the safety pin, Aim the nozzle, Squeeze the handle, and Sweep the nozzle). If these instructions are unclear or missing, it could lead to improper use of the extinguisher, potentially exacerbating a fire rather than extinguishing it. Therefore, it is crucial to verify that all instructional text is legible and free from any obstructions. In addition to visual checks, it is also important to ensure that all personnel who may use the fire extinguishers are familiar with their operation. This includes training sessions where employees can practice reading and following the instructions on the labels. Regular training not only enhances their ability to respond effectively in an emergency but also reinforces the importance of maintaining legible labels. From a regulatory standpoint, many jurisdictions have specific guidelines regarding the maintenance and inspection of fire extinguishers. These regulations often include requirements for label condition and readability. Non-compliance can result in fines or even more severe penalties if a fire occurs due to inadequate maintenance. In summary, maintaining legible labels and instructions on fire extinguishers is a vital part of monthly inspections. It ensures that users can quickly identify and properly use the equipment in emergency situations, thereby preventing fires from spreading and potentially saving lives. By incorporating this into your monthly maintenance routine, you not only comply with regulatory requirements but also contribute to a safer working environment.
Proper Storage and Handling
Proper storage and handling are crucial for maintaining the integrity and longevity of various items, whether they are sensitive electronics, perishable goods, or delicate equipment. Effective storage practices involve a multifaceted approach that addresses several key factors. First, it is essential to **Avoid Exposure to Extreme Temperatures**, as fluctuations can cause damage, degradation, or even complete failure of the stored items. Additionally, **Keeping Away from Moisture and Humidity** is vital to prevent corrosion, mold, and other forms of deterioration. Lastly, **Securing Against Physical Impact** ensures that items are protected from accidental drops, bumps, and other mechanical stresses that could lead to breakage or malfunction. By adhering to these principles, individuals can ensure that their stored items remain in optimal condition. In this article, we will delve into each of these critical aspects, starting with the importance of avoiding exposure to extreme temperatures.
Avoid Exposure to Extreme Temperatures
Avoiding exposure to extreme temperatures is a critical aspect of proper storage and handling to prevent fire extinguishers from clumping. Fire extinguishers, particularly those containing dry chemical agents, are highly susceptible to temperature fluctuations. When exposed to extreme heat or cold, the chemical composition within the extinguisher can become unstable, leading to clumping or caking of the powder. This not only reduces the effectiveness of the extinguisher but also increases the risk of it failing during an emergency. Extreme temperatures can cause the powder to compact and stick together, making it difficult for the agent to be discharged properly. For instance, high temperatures can cause moisture to enter the extinguisher, leading to clumping due to hydration. Conversely, very low temperatures can slow down the chemical reactions necessary for proper discharge, rendering the extinguisher less effective. Additionally, repeated exposure to temperature extremes can weaken the seals and valves within the extinguisher, potentially causing leaks or other mechanical failures. To mitigate these risks, it is essential to store fire extinguishers in environments with stable temperatures between 40°F and 120°F (4°C and 49°C). This range ensures that the chemical agents remain stable and effective. It is also crucial to keep extinguishers away from direct sunlight, heating vents, and air conditioning units, which can cause rapid temperature changes. Regular inspections should be conducted monthly to check for any signs of damage or exposure to extreme temperatures. During these inspections, look for visible signs such as rust, corrosion, or physical damage that could indicate improper storage conditions. Moreover, proper placement of fire extinguishers is key. They should be mounted on wall brackets or placed in designated cabinets that protect them from environmental factors while ensuring easy access in case of an emergency. By adhering to these guidelines, you can significantly reduce the likelihood of clumping and ensure that your fire extinguishers remain in optimal condition, ready to function effectively when needed. In summary, avoiding exposure to extreme temperatures is a vital component of maintaining fire extinguisher integrity. By storing them in stable temperature ranges and conducting regular inspections, you can prevent clumping and ensure that your fire safety equipment remains reliable and effective. This proactive approach not only enhances safety but also complies with regulatory standards, providing peace of mind and protecting lives and property from potential fire hazards.
Keep Away from Moisture and Humidity
**Keep Away from Moisture and Humidity** Proper storage and handling of fire extinguishers are crucial to ensure their effectiveness and longevity. One of the key factors to consider is keeping them away from moisture and humidity. Moisture can seep into the extinguisher through various means, such as condensation, leaks, or exposure to damp environments. When moisture enters the extinguisher, it can lead to several detrimental effects. For instance, in dry chemical extinguishers, moisture can cause the powder to clump or cake, rendering the device ineffective in an emergency. Similarly, in liquid-based extinguishers like water or foam, moisture can lead to corrosion of the metal components or contamination of the agent, which compromises its fire-fighting capabilities. To prevent such issues, it is essential to store fire extinguishers in well-ventilated areas that are protected from direct exposure to rain, snow, or high humidity levels. Basements, garages, and outdoor locations are generally not ideal due to their propensity for dampness. Instead, choose locations with stable temperatures and low humidity levels. Regular inspections should be conducted every month to check for any signs of moisture intrusion or damage. This includes visually inspecting the extinguisher for rust spots, checking the pressure gauge for any deviations from the recommended range, and ensuring that all seals and valves are intact. Additionally, maintaining a clean and dry environment around the fire extinguisher is vital. Avoid placing them near areas where water may accumulate, such as bathrooms or kitchens. If an extinguisher has been exposed to moisture, it should be inspected by a certified professional immediately to determine if it needs to be serviced or replaced. By keeping fire extinguishers away from moisture and humidity, you not only extend their lifespan but also ensure they remain ready to perform their critical function in case of an emergency. This proactive approach is a cornerstone of proper storage and handling practices that help prevent clumping and maintain the overall effectiveness of your fire safety equipment.
Secure Against Physical Impact
**Secure Against Physical Impact** Proper storage and handling of fire extinguishers are crucial to ensure their effectiveness in emergency situations. One key aspect of this is securing them against physical impact, which can compromise their integrity and functionality. Fire extinguishers are designed to withstand various environmental conditions, but they are not invincible to physical damage. A single mishap, such as a collision or a fall, can render an extinguisher useless when it is most needed. To prevent this, it is essential to mount fire extinguishers securely in designated locations. Wall brackets or floor stands should be used to keep the extinguishers upright and stable, protecting them from accidental knocks or other forms of impact. Regular inspections every month are vital to ensure that these mounting systems remain intact. Check for any signs of wear or damage on the brackets and stands, and replace them immediately if necessary. Additionally, ensure that the area around the fire extinguisher is clear of clutter and obstructions, allowing easy access in case of an emergency. This not only helps in preventing physical impact but also ensures that the extinguisher can be quickly retrieved when needed. Moreover, educating personnel on the importance of handling fire extinguishers with care is paramount. Training sessions should include guidelines on how to move and inspect extinguishers without causing damage. For instance, extinguishers should be carried by their handles rather than by the hose or nozzle, which can be easily damaged. By fostering a culture of careful handling and regular inspections, you can significantly reduce the risk of physical impact and maintain the readiness of your fire extinguishers. Incorporating these practices into your monthly routine will help in preventing clumping and other issues related to fire extinguisher maintenance. By securing fire extinguishers against physical impact, you are not only ensuring their operational readiness but also contributing to a safer environment for everyone. This proactive approach underscores the importance of meticulous storage and handling procedures, ultimately safeguarding against potential hazards and ensuring that your fire safety equipment remains reliable and effective.
Regular Testing and Certification
Regular testing and certification are crucial components in ensuring the safety, reliability, and compliance of various systems and equipment. These processes involve a series of meticulous steps designed to verify that all components meet stringent standards. The importance of regular testing is underscored by three key aspects: the hydrostatic testing schedule, certification compliance with local regulations, and the documentation of test results. Firstly, adhering to a hydrostatic testing schedule is essential for maintaining the integrity of pressure vessels and pipelines. This schedule ensures that these critical components are subjected to periodic tests that simulate real-world conditions, thereby identifying potential weaknesses before they become catastrophic failures. Secondly, certification compliance with local regulations is vital for legal and operational reasons. It guarantees that all equipment and systems conform to the specific standards set by local authorities, reducing the risk of fines, shutdowns, and other penalties. Lastly, thorough documentation of test results provides a transparent and traceable record of all testing activities. This documentation not only aids in auditing and compliance but also serves as a valuable resource for future maintenance and troubleshooting. By understanding these elements, we can appreciate the comprehensive nature of regular testing and certification. Let's delve deeper into the specifics of the hydrostatic testing schedule to see how it plays a pivotal role in this process.
Hydrostatic Testing Schedule
**Hydrostatic Testing Schedule** Regular hydrostatic testing is a critical component of maintaining fire extinguishers to ensure they remain effective and safe. This process involves subjecting the extinguisher's cylinder to high pressure to verify its integrity and detect any potential leaks or weaknesses. The schedule for hydrostatic testing varies depending on the type of extinguisher and local regulations, but it is generally mandated every 12 years for most types of fire extinguishers, with some exceptions requiring more frequent testing. For example, carbon dioxide extinguishers must undergo hydrostatic testing every 5 years due to their higher risk of leakage. Similarly, certain types of dry chemical extinguishers may require testing every 6 years. It is essential to consult the manufacturer's guidelines and comply with local fire safety codes to determine the specific testing interval for each type of extinguisher in your inventory. The hydrostatic testing process typically involves several steps: first, the extinguisher is completely discharged and then inspected for any signs of damage or corrosion. Next, the cylinder is filled with water or another testing medium and subjected to a pressure significantly higher than its rated working pressure. If the cylinder withstands this pressure without showing signs of leakage or deformation, it is deemed safe for continued use. If any issues are detected during the test, the cylinder must be replaced or repaired according to the manufacturer's instructions. In addition to ensuring compliance with safety standards, regular hydrostatic testing helps prevent fire extinguishers from becoming ineffective due to internal corrosion or other forms of degradation. This is particularly important in preventing clumping within dry chemical extinguishers, which can render them useless in an emergency situation. By adhering to a rigorous hydrostatic testing schedule, you not only meet regulatory requirements but also safeguard your facility against potential fire hazards by maintaining reliable and functional fire extinguishers. Moreover, keeping detailed records of hydrostatic tests is crucial for auditing purposes and to ensure that all extinguishers are up-to-date with their testing requirements. This documentation should include the date of the test, the results, and any necessary repairs or replacements made. By integrating hydrostatic testing into your monthly maintenance routine—alongside other checks such as visual inspections and pressure gauge readings—you can ensure that your fire extinguishers remain in optimal condition and ready for immediate use in case of an emergency. In summary, a well-planned hydrostatic testing schedule is indispensable for maintaining the reliability and effectiveness of fire extinguishers. By understanding and adhering to these testing intervals, you can prevent issues like clumping in dry chemical extinguishers and ensure that your fire safety equipment is always ready to protect people and property from potential fires. Regular testing not only complies with safety regulations but also provides peace of mind knowing that your emergency response tools are in top working order.
Certification Compliance with Local Regulations
**Certification Compliance with Local Regulations** Ensuring certification compliance with local regulations is a critical component of maintaining fire safety standards, particularly when it comes to the regular testing and certification of fire extinguishers. Local regulations often mandate specific requirements for the inspection, maintenance, and certification of fire extinguishers to ensure they remain effective in the event of a fire. These regulations can vary significantly from one jurisdiction to another, making it essential for businesses and property owners to be well-versed in the specific laws governing their area. Compliance involves more than just conducting monthly inspections; it requires adherence to detailed standards that may include annual inspections by certified professionals, hydrostatic testing of cylinders at prescribed intervals, and thorough documentation of all maintenance activities. For instance, the National Fire Protection Association (NFPA) standards, which are widely adopted across many regions, specify that fire extinguishers must be inspected monthly and annually by trained personnel. These inspections check for signs of physical damage, corrosion, and leakage, as well as ensuring that the extinguisher is fully charged and easily accessible. Moreover, local regulations may require that fire extinguishers be certified by third-party inspectors who have the necessary qualifications and experience. This certification process involves verifying that the extinguisher meets all applicable safety standards and is in good working condition. Failure to comply with these regulations can result in severe penalties, including fines and legal action, as well as compromising the safety of occupants in the event of a fire. In addition to legal compliance, adhering to local regulations helps prevent common issues such as clumping in fire extinguishers. Clumping occurs when the extinguishing agent settles or becomes compacted over time, reducing the effectiveness of the extinguisher. Regular inspections and maintenance activities mandated by local regulations help identify such issues early on, allowing for prompt corrective action. This not only ensures that fire extinguishers remain functional but also contributes to a safer environment by minimizing the risk of fire-related hazards. To ensure continuous compliance, it is advisable to maintain detailed records of all inspections, maintenance activities, and certifications. These records serve as proof of adherence to local regulations and can be crucial during audits or inspections by regulatory authorities. Furthermore, engaging with local fire safety experts or certified inspectors can provide valuable insights into specific regulatory requirements and best practices for maintaining fire safety equipment. In summary, certification compliance with local regulations is a vital aspect of fire safety management that goes beyond mere monthly inspections. It involves a comprehensive approach to ensuring that fire extinguishers are regularly inspected, maintained, and certified according to stringent standards. By adhering to these regulations, businesses and property owners can ensure their fire safety equipment remains in optimal condition, preventing issues like clumping and contributing to a safer environment for everyone.
Documentation of Test Results
**Documentation of Test Results** Proper documentation of test results is a crucial component of regular testing and certification for fire extinguishers. This process ensures that all necessary inspections and tests are meticulously recorded, providing a clear audit trail that can be reviewed by regulatory bodies, insurance companies, and internal safety teams. Each month, when conducting routine checks on fire extinguishers to prevent clumping and ensure they remain operational, it is essential to document every step of the process. This includes noting the date and time of the inspection, the identity of the person performing the test, and detailed observations about the condition of each extinguisher. The documentation should cover key aspects such as visual inspections for signs of damage or wear, pressure gauge readings to ensure proper levels, and checks for any blockages in hoses or nozzles. Any issues identified during these tests must be documented along with the corrective actions taken to rectify them. For instance, if an extinguisher shows signs of clumping due to sedimentation or moisture ingress, this should be noted along with details of how it was cleaned or replaced. Using standardized forms or digital tools can streamline this process, ensuring consistency and accuracy in recording test results. These forms typically include sections for recording serial numbers, inspection dates, and specific test outcomes. Digital tools offer additional benefits such as automatic date stamping, reminders for upcoming inspections, and easy access to historical records. Maintaining comprehensive records not only aids in compliance with local fire safety regulations but also helps in identifying trends or recurring issues that may indicate broader maintenance needs. For example, if multiple extinguishers in a particular area are showing signs of clumping over time, it may suggest environmental factors such as high humidity that need addressing. Moreover, well-documented test results can serve as valuable training resources for new personnel responsible for conducting these inspections. By reviewing past records, they can gain insights into common issues and best practices for maintaining fire extinguishers effectively. In summary, thorough documentation of test results is indispensable for ensuring that fire extinguishers remain in optimal working condition. It supports regular testing and certification by providing a detailed history of inspections and maintenance activities. This not only enhances safety but also facilitates compliance and continuous improvement in fire safety protocols. By integrating robust documentation practices into monthly testing routines, organizations can significantly reduce the risk of fire extinguisher clumping and other operational failures.