What Does Cfm Stand For

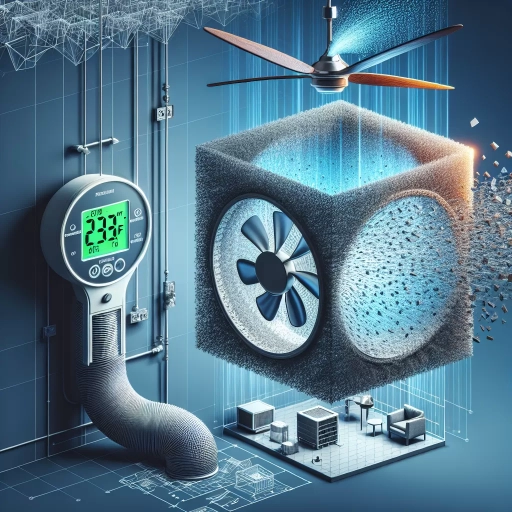
In the realm of airflow and ventilation, a crucial metric often comes into play: CFM, or Cubic Feet per Minute. This measurement is essential for understanding the efficiency and effectiveness of various systems across different industries. But what exactly does CFM stand for, and why is it so important? To delve into this, we need to start with the basics. This article will explore the definition and fundamental principles of CFM, providing a solid foundation for understanding its role. We will then examine the practical uses of CFM in various industries, highlighting how it impacts everything from HVAC systems to industrial processes. Finally, we will discuss the tools and techniques used for calculating and measuring CFM, ensuring that readers are equipped with the knowledge to apply this metric in real-world scenarios. By grasping these concepts, you will gain a comprehensive understanding of CFM and its significance. Let's begin by understanding CFM: Definition and Basics.
Understanding CFM: Definition and Basics
In the realm of ventilation and air flow, the term CFM (Cubic Feet per Minute) is a fundamental concept that underpins various industrial, residential, and commercial applications. Understanding CFM is crucial for ensuring efficient air circulation, maintaining indoor air quality, and optimizing the performance of HVAC systems. This article delves into the multifaceted nature of CFM, starting with its historical context to appreciate how this measurement has evolved over time. We will then explore the technical definition of CFM, breaking down the intricacies of how it is calculated and its significance in different settings. Finally, we will examine the common applications of CFM, highlighting its importance in sectors such as construction, manufacturing, and environmental control. By grasping these aspects, readers will gain a comprehensive understanding of CFM: Definition and Basics.
Historical Context of CFM
The historical context of CFM, or Cubic Feet per Minute, is deeply intertwined with the evolution of industrial and technological advancements, particularly in the fields of engineering and manufacturing. The concept of measuring airflow dates back to the early 19th century when industrialization was gaining momentum. As factories and machinery became more complex, the need to quantify and control airflow for ventilation, cooling, and powering machinery grew. In the late 19th and early 20th centuries, the development of HVAC (Heating, Ventilation, and Air Conditioning) systems necessitated precise measurements of airflow to ensure efficient operation. CFM emerged as a standard unit of measurement to describe the volume of air moving through a given space in one minute. This metric was crucial for designing ventilation systems that could effectively remove pollutants and maintain a healthy indoor environment. The rise of automotive and aerospace industries further solidified CFM's importance. In these sectors, accurate airflow measurements were essential for optimizing engine performance, fuel efficiency, and overall system reliability. For instance, in the automotive industry, CFM is used to measure the airflow through air filters and intake systems, directly impacting engine power and efficiency. During World War II, the demand for precise airflow measurements intensified due to the development of advanced aircraft and military equipment. The need for reliable ventilation systems in submarines and other enclosed military vehicles also highlighted the critical role of CFM in ensuring crew safety and operational effectiveness. In the post-war period, advancements in materials science and manufacturing led to the creation of more sophisticated airflow measurement tools. These innovations enabled more accurate and reliable CFM readings, which in turn facilitated better design and operation of industrial processes, HVAC systems, and automotive engines. Today, CFM remains a fundamental metric across various industries including construction, HVAC, automotive, aerospace, and even consumer electronics. Its widespread adoption underscores its importance in ensuring efficiency, safety, and performance in a wide range of applications. Understanding CFM is thus essential for anyone involved in these fields, as it provides a critical link between theoretical design and practical implementation. In summary, the historical context of CFM reflects broader technological and industrial developments over the past two centuries. From its origins in early industrialization to its current widespread use across multiple sectors, CFM has evolved into a vital metric that underpins many modern technologies and processes.
Technical Definition of CFM
**Technical Definition of CFM** CFM, or Cubic Feet per Minute, is a critical metric in various engineering and industrial contexts, particularly in the fields of HVAC (Heating, Ventilation, and Air Conditioning), fluid dynamics, and pneumatic systems. Technically, CFM measures the volume of air or gas that flows through a given space or system in one minute. It is calculated by multiplying the cross-sectional area of the flow path by the velocity of the fluid (air or gas) and is expressed in cubic feet per minute. This measurement is essential for designing and optimizing systems that require precise airflow control, such as ventilation systems in buildings, industrial processes, and even automotive applications. In HVAC systems, CFM helps determine the capacity of air handlers, fans, and blowers to ensure adequate air circulation and exchange. For instance, a higher CFM rating indicates that a fan can move more air, which is crucial for maintaining indoor air quality and comfort levels. In industrial settings, CFM is used to specify the performance of compressors, blowers, and vacuum pumps, ensuring that they meet the operational demands of various processes. The calculation of CFM involves understanding both the physical dimensions of the system and the dynamic properties of the fluid. The formula for CFM is \( \text{CFM} = \text{Area} \times \text{Velocity} \), where area is typically measured in square feet and velocity in feet per minute. This straightforward yet powerful metric allows engineers to predict and manage airflow efficiently, which is vital for maintaining system performance, energy efficiency, and safety. Moreover, CFM is often used in conjunction with other metrics such as static pressure and fan efficiency to provide a comprehensive understanding of system performance. For example, in ductwork design, knowing the CFM requirements helps in selecting appropriate duct sizes and fan configurations to minimize energy consumption while ensuring adequate airflow distribution. In summary, CFM is a fundamental technical parameter that quantifies airflow in various applications. Its precise measurement and calculation are indispensable for designing, operating, and optimizing systems that rely on controlled airflow. Understanding CFM is essential for engineers, technicians, and anyone involved in the design or maintenance of HVAC systems, industrial processes, or any application where airflow plays a critical role. By grasping the technical definition and significance of CFM, professionals can ensure that their systems operate efficiently, safely, and effectively.
Common Applications of CFM
Common Applications of CFM are diverse and widespread, reflecting the critical role this measurement plays in various industries. In the realm of **HVAC (Heating, Ventilation, and Air Conditioning)**, CFM (Cubic Feet per Minute) is essential for determining the airflow rates necessary to maintain comfortable indoor environments. For instance, HVAC engineers use CFM to design ventilation systems that ensure adequate air circulation, which is crucial for indoor air quality and thermal comfort. This metric helps in selecting the right size of fans, blowers, and air handlers to meet specific building requirements. In **industrial settings**, CFM is vital for ensuring efficient operation of machinery and maintaining a safe working environment. For example, in manufacturing plants, CFM is used to calculate the airflow needed for dust collection systems, which help in removing particulate matter and improving air quality. Similarly, in chemical processing plants, accurate CFM measurements are necessary for controlling the flow of gases and ensuring proper ventilation to prevent hazardous conditions. The **automotive industry** also relies heavily on CFM measurements. Car manufacturers use CFM to test and optimize the performance of vehicle air intakes, exhaust systems, and cabin ventilation systems. This ensures that vehicles have efficient airflow for engine performance and passenger comfort. In **medical facilities**, precise CFM measurements are critical for maintaining sterile environments. Operating rooms, for instance, require controlled airflow to prevent contamination and ensure patient safety. CFM helps in designing and operating these specialized ventilation systems effectively. Additionally, **agricultural applications** benefit from CFM measurements. In greenhouses and livestock facilities, controlled airflow is essential for maintaining optimal temperatures and humidity levels. By using CFM to manage ventilation systems, farmers can enhance crop yields and animal health. Lastly, **construction and building management** often involve CFM calculations to ensure compliance with building codes and standards related to indoor air quality and ventilation. This includes designing and installing proper ventilation systems in residential and commercial buildings to meet occupancy requirements. In summary, the applications of CFM are far-reaching and impact various sectors by ensuring efficient airflow, maintaining safety standards, and optimizing performance. Understanding CFM is fundamental to designing, operating, and maintaining systems across these diverse fields.
Practical Uses of CFM in Various Industries
Cubic Feet per Minute (CFM) is a critical measurement in various industries, playing a pivotal role in ensuring efficiency, safety, and performance. This metric, which quantifies the volume of air or gas moving through a system in one minute, is essential for optimizing operations across diverse sectors. In the realm of Heating, Ventilation, and Air Conditioning (HVAC) systems, CFM helps in designing and maintaining air flow that meets specific comfort and health standards. In the automotive and aerospace industries, precise CFM measurements are crucial for engine performance, fuel efficiency, and overall vehicle safety. Additionally, industrial processes rely heavily on CFM to manage airflow in manufacturing environments, ensuring proper ventilation and process control. Understanding the practical uses of CFM in these contexts is vital for professionals and enthusiasts alike. As we delve into the specific applications of CFM in HVAC systems, automotive and aerospace, and industrial processes, it becomes clear that a solid grasp of this concept is fundamental. To fully appreciate these applications, it is essential to start with a foundational understanding of CFM: its definition and basics.
CFM in HVAC Systems
In the realm of Heating, Ventilation, and Air Conditioning (HVAC) systems, Cubic Feet per Minute (CFM) is a crucial metric that measures the volume of air moved by a fan or blower within a given time frame. This measurement is essential for ensuring that HVAC systems operate efficiently and effectively. For instance, in residential settings, CFM helps determine the appropriate size of an air conditioning or heating unit to ensure it can handle the air exchange needs of the space. Too low a CFM rating can lead to inadequate cooling or heating, while too high can result in wasted energy and increased utility bills. In commercial and industrial environments, CFM plays an even more critical role. Large buildings require precise air flow calculations to maintain optimal indoor air quality and temperature control. This involves considering factors such as room size, occupancy levels, and specific ventilation requirements. For example, in hospitals and healthcare facilities, maintaining precise CFM rates is vital for controlling airborne pathogens and ensuring patient safety. Similarly, in manufacturing plants, accurate CFM measurements help in managing dust and fume extraction systems, thereby enhancing worker safety and productivity. Moreover, CFM is integral to the design and installation of ductwork systems. Properly sized ducts must be able to handle the CFM output of the HVAC system without causing excessive pressure drops or noise. This ensures that air is distributed evenly throughout the building without compromising system performance or energy efficiency. Additionally, understanding CFM allows HVAC technicians to diagnose and troubleshoot issues such as reduced airflow or increased energy consumption more effectively. From a practical standpoint, knowing the CFM requirements of an HVAC system also aids in selecting the right type of fans or blowers. Different applications demand different types of fans; for instance, centrifugal fans are often used in high-pressure applications like industrial ventilation systems, while axial fans are better suited for low-pressure applications such as residential ventilation. By matching the CFM needs with the appropriate fan technology, users can achieve optimal performance while minimizing energy costs. In summary, CFM is a fundamental parameter in HVAC systems that influences everything from system sizing and duct design to fan selection and overall performance. Its accurate measurement and application are critical for ensuring efficient operation, maintaining indoor air quality, and optimizing energy consumption across various industries. Whether it's a residential home or a large commercial facility, understanding CFM is essential for creating comfortable, safe, and energy-efficient environments.
CFM in Automotive and Aerospace
In the realms of automotive and aerospace, Computational Fluid Dynamics (CFM) plays a pivotal role in enhancing performance, efficiency, and safety. CFM, or more accurately CFD, is a powerful tool that simulates the behavior of fluids and gases under various conditions. In the automotive industry, CFD is used to optimize vehicle aerodynamics, reducing drag and improving fuel efficiency. Engineers employ CFD to analyze airflow around vehicles, identifying areas where aerodynamic improvements can be made. This not only enhances the vehicle's overall performance but also contributes to better fuel economy and reduced emissions. Additionally, CFD helps in designing more efficient cooling systems for engines and brakes, ensuring optimal thermal management even under extreme conditions. In the aerospace sector, the stakes are even higher, and the precision required is more stringent. Here, CFD is indispensable for simulating complex fluid dynamics involved in aircraft and spacecraft design. It aids in predicting airflow patterns around wings, fuselages, and control surfaces, allowing engineers to fine-tune designs for maximum lift and minimum drag. This technology is also crucial for analyzing the behavior of gases during rocket propulsion, ensuring that engines operate efficiently and safely. Furthermore, CFD helps in understanding and mitigating issues related to turbulence, which is critical for maintaining stable flight conditions. The use of CFD in aerospace extends to the design of wind tunnels, where it helps in creating realistic test environments that closely mimic real-world conditions. Beyond these primary applications, CFD also supports the development of advanced materials and systems. For instance, in both industries, it helps in optimizing the design of heat exchangers and other thermal management systems. This ensures that components operate within safe temperature ranges, thereby extending their lifespan and reliability. Moreover, CFD facilitates the integration of new technologies such as electric propulsion systems in vehicles and advanced propulsion systems in aircraft, by simulating their fluid dynamics and thermal behavior. The integration of CFD with other simulation tools like Finite Element Analysis (FEA) and Multi-Body Dynamics (MBD) further enriches its capabilities. This holistic approach allows engineers to model complex interactions between structural, thermal, and fluid dynamics aspects of a system, leading to more accurate predictions and better design outcomes. As computational power continues to grow, the role of CFD in automotive and aerospace will only become more pronounced, driving innovation and pushing the boundaries of what is possible in these fields. By leveraging CFD, industries can achieve significant improvements in performance, efficiency, and safety while reducing development times and costs.
CFM in Industrial Processes
In industrial processes, CFM (Cubic Feet per Minute) is a critical metric that measures the volume of air or gas flowing through a system. This measurement is essential for ensuring optimal performance, efficiency, and safety across various industries. For instance, in manufacturing facilities, CFM is used to determine the airflow required for ventilation systems to remove hazardous fumes and maintain a healthy working environment. In HVAC (Heating, Ventilation, and Air Conditioning) systems, CFM helps in sizing ducts and selecting appropriate fans or blowers to achieve the desired air circulation and temperature control. In chemical processing plants, accurate CFM measurements are vital for controlling the flow of reactants and products, thereby influencing reaction rates and product quality. Additionally, in the automotive industry, CFM is crucial for designing and testing engine intake systems to optimize engine performance and fuel efficiency. The precision of CFM measurements also plays a significant role in the pharmaceutical industry where controlled environments are necessary for drug production; here, maintaining specific airflow rates ensures compliance with stringent regulatory standards. Furthermore, in mining operations, CFM is used to calculate the ventilation requirements to prevent the buildup of dangerous gases and dust, thereby enhancing worker safety. By understanding and accurately measuring CFM, industries can optimize their processes, reduce energy consumption, improve product quality, and ensure a safer working environment. This underscores the importance of CFM as a fundamental parameter in industrial engineering and operations management.
Calculating and Measuring CFM: Tools and Techniques
Calculating and measuring Cubic Feet per Minute (CFM) is a crucial aspect in various fields such as HVAC, industrial ventilation, and automotive engineering. Understanding CFM helps in ensuring efficient airflow, maintaining optimal performance, and enhancing safety. This article delves into the essential tools and techniques required for accurate CFM calculations and measurements. We will explore the **Formulas for Calculating CFM**, which provide the mathematical foundation necessary for determining airflow rates. Additionally, we will discuss the **Tools Used to Measure CFM**, highlighting the different devices and instruments that professionals rely on to obtain precise readings. Finally, we will outline **Best Practices for Accurate Measurement**, offering practical tips to ensure that your measurements are reliable and consistent. By mastering these concepts, you will be well-equipped to handle complex airflow challenges. For a comprehensive understanding, it is important to first grasp the basics, which can be found in our companion piece, **Understanding CFM: Definition and Basics**.
Formulas for Calculating CFM
Calculating CFM (Cubic Feet per Minute) is a crucial step in various engineering and HVAC applications, ensuring that systems operate efficiently and effectively. To determine CFM, several formulas can be employed, each tailored to specific scenarios. 1. **Using Air Velocity and Duct Area**: One of the most common methods involves measuring the air velocity in feet per minute (FPM) and the cross-sectional area of the duct in square feet. The formula is \( \text{CFM} = \text{FPM} \times \text{Area} \). For instance, if the air velocity is 1,000 FPM and the duct area is 0.5 square feet, the CFM would be \( 1,000 \times 0.5 = 500 \) CFM. 2. **Utilizing Pressure Drop and Flow Coefficients**: In more complex systems, CFM can be calculated using pressure drop measurements and flow coefficients. The formula here involves the pressure drop (\( \Delta P \)) in inches of water gauge (in.w.g.), the flow coefficient (\( K \)), and the specific gravity of the gas (\( SG \)). The general form is \( \text{CFM} = K \times \sqrt{\frac{\Delta P}{SG}} \). This method is particularly useful in industrial settings where precise control over airflow is necessary. 3. **From Fan Performance Curves**: For fans, CFM can often be determined from performance curves provided by the manufacturer. These curves typically plot CFM against static pressure, allowing users to find the CFM at a given pressure point. This method is straightforward but requires accurate static pressure measurements. 4. **Using Pitot Tube Readings**: In field measurements, a pitot tube can be used to measure the dynamic pressure of airflow. By converting this dynamic pressure into velocity using Bernoulli's principle, and then multiplying by the duct area, one can calculate CFM. The formula involves the dynamic pressure (\( P_d \)) in inches of water gauge, the density of air (\( \rho \)), and the gravitational acceleration (\( g \)). The velocity is calculated as \( V = \sqrt{\frac{2P_d}{\rho}} \), and then CFM is found as \( V \times \text{Area} \). Each of these methods has its own set of requirements and limitations, but they collectively provide a comprehensive toolkit for accurately calculating CFM in various contexts. Understanding these formulas is essential for engineers and technicians to ensure that ventilation systems, HVAC units, and industrial processes operate within optimal parameters, thereby enhancing efficiency, safety, and performance. By selecting the appropriate formula based on available data and system characteristics, professionals can make informed decisions that align with project specifications and regulatory standards.
Tools Used to Measure CFM
When it comes to calculating and measuring CFM (Cubic Feet per Minute), the right tools are essential for accurate and reliable results. Several specialized instruments are designed to help professionals and DIY enthusiasts alike determine airflow rates in various settings, from HVAC systems to industrial processes. 1. **Anemometers**: These devices measure air velocity, which is crucial for calculating CFM. There are different types of anemometers, including vane anemometers, hot wire anemometers, and pitot tubes. Vane anemometers are commonly used due to their ease of use and accuracy in measuring air speed in ducts and open spaces. Hot wire anemometers offer high precision but are more sensitive and require careful handling. 2. **Pitot Tubes**: These tools measure the differential pressure between two points in an airflow stream, allowing for the calculation of air velocity. Pitot tubes are particularly useful in ducted systems where direct measurement of air speed is challenging. They are often combined with manometers or pressure gauges to provide a complete reading. 3. **Flow Hoods**: Flow hoods are versatile tools that can measure CFM directly by capturing and measuring the airflow from a vent or grille. They are widely used in HVAC applications for balancing air distribution systems. Flow hoods typically include a fan that creates a controlled environment to ensure accurate measurements. 4. **Thermal Anemometers**: These devices use heat transfer principles to measure air velocity. They are highly sensitive and can detect very low airflow rates, making them ideal for applications where precise measurements are critical, such as in clean rooms or laboratories. 5. **Duct Traverse Kits**: For larger ducts, duct traverse kits are employed to take multiple readings across the duct cross-section. These kits usually include a series of probes connected to a manometer or data logger, allowing for comprehensive airflow analysis. 6. **Balometers**: Balometers are handheld devices that combine the functions of an anemometer and a manometer, providing both air velocity and pressure readings. They are convenient for quick assessments and are often used by HVAC technicians for routine maintenance and system balancing. 7. **Data Loggers**: Advanced data loggers can record airflow data over extended periods, providing valuable insights into system performance under various conditions. These devices can be integrated with other measurement tools to offer a comprehensive view of airflow dynamics. Each of these tools has its specific application and advantages, ensuring that professionals can choose the most appropriate method for their particular needs. By understanding how to use these tools effectively, one can accurately measure CFM and ensure optimal performance in a wide range of environments. Whether it's for system design, maintenance, or troubleshooting, having the right tools at hand is indispensable for achieving precise airflow measurements.
Best Practices for Accurate Measurement
When calculating and measuring CFM (Cubic Feet per Minute), adhering to best practices is crucial for accuracy and reliability. To ensure precise measurements, it is essential to select the right tools and techniques tailored to the specific application. First, choose a high-quality anemometer or flow meter that is calibrated regularly to maintain its accuracy. These instruments should be compatible with the environment in which they will be used, whether it's in ducts, open spaces, or through vents. Proper placement of the measuring device is another critical factor. For duct measurements, position the anemometer at multiple points across the duct to account for variations in airflow. This method, known as a traverse, helps in obtaining an average velocity that accurately represents the total flow rate. In open spaces, ensure that the device is placed away from obstacles and walls to avoid interference with airflow patterns. Additionally, consider the type of measurement needed: velocity or volumetric flow. Velocity measurements are often simpler but require knowledge of the duct's cross-sectional area to calculate CFM. Volumetric flow meters directly measure CFM but may be more complex and expensive. Environmental conditions also play a significant role. Temperature and humidity can affect airflow characteristics and instrument accuracy. Therefore, it's important to adjust readings based on these factors when necessary. Regular maintenance of the measuring equipment is vital; clean sensors and check for any damage before each use. Furthermore, understanding the principles of fluid dynamics can help in interpreting data correctly. For instance, knowing how to account for pressure drops and losses due to fittings and bends in ductwork can significantly impact the accuracy of CFM calculations. Finally, documenting all measurements meticulously is crucial for future reference and troubleshooting. This includes recording the location of measurements, environmental conditions, and any adjustments made during the process. By following these best practices—selecting appropriate tools, ensuring proper placement, considering environmental factors, maintaining equipment, understanding fluid dynamics principles, and thorough documentation—you can ensure that your CFM measurements are accurate and reliable. This attention to detail not only enhances the credibility of your data but also aids in optimizing system performance and efficiency.