What Is A Sprocket

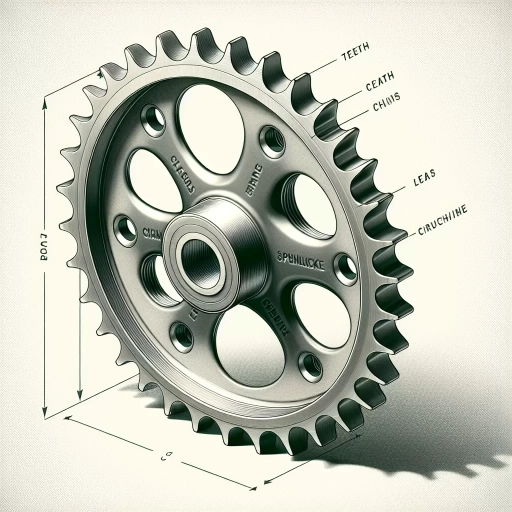
A sprocket is a crucial component in various mechanical systems, playing a pivotal role in the transmission of power and motion. These toothed wheels are integral to the functioning of bicycles, motorcycles, and industrial machinery, among other applications. To fully appreciate the significance of sprockets, it is essential to delve into their fundamental principles, explore their diverse uses, and understand the intricacies of their design and maintenance. This article will provide a comprehensive overview of sprockets, starting with **Understanding the Basics of a Sprocket**, where we will examine the core components and mechanisms that define these essential parts. From there, we will discuss **Applications and Uses of Sprockets**, highlighting their role in different industries and everyday life. Finally, we will delve into **Design, Maintenance, and Selection Criteria**, offering insights into how sprockets are engineered, maintained, and chosen for specific tasks. By exploring these facets, readers will gain a thorough understanding of what makes sprockets indispensable in modern technology. Let us begin by **Understanding the Basics of a Sprocket**.
Understanding the Basics of a Sprocket
Understanding the basics of a sprocket is crucial for anyone involved in mechanical engineering, manufacturing, or even DIY projects. A sprocket, essentially a toothed wheel, plays a pivotal role in various mechanical systems by facilitating the smooth transmission of power and motion. To grasp the full functionality of sprockets, it is essential to delve into three key areas: their definition and purpose, their key components and structure, and the different types available. Firstly, understanding the definition and purpose of a sprocket sets the foundation for further exploration. This involves recognizing how sprockets interact with chains or belts to transfer rotational motion efficiently. Secondly, examining the key components and structure of a sprocket reveals the intricate design elements that ensure durability and performance. Lastly, familiarizing oneself with the various types of sprockets—such as single-row, double-row, and idler sprockets—highlights their versatility across different applications. By exploring these aspects, one can gain a comprehensive understanding of how sprockets operate and why they are indispensable in modern machinery. Let's begin by defining what a sprocket is and its fundamental purpose in mechanical systems.
Definition and Purpose
**Understanding the Basics of a Sprocket: Definition and Purpose** A sprocket is a critical component in various mechanical systems, particularly those involving chains or belts. At its core, a sprocket is a toothed wheel that engages with a chain or belt to transmit rotational motion. The definition of a sprocket hinges on its unique design, which features evenly spaced teeth around its circumference. These teeth are precision-engineered to mesh perfectly with the links of a chain or the ridges of a belt, ensuring smooth and efficient power transmission. The primary purpose of a sprocket is to facilitate the transfer of torque from one shaft to another while maintaining precise control over speed and direction. In applications such as bicycles, motorcycles, and industrial machinery, sprockets play a pivotal role in converting rotational energy into linear motion or vice versa. For instance, in a bicycle, the front sprocket (chainring) and rear sprocket (cassette) work in tandem to adjust gear ratios, allowing riders to optimize their pedaling effort based on terrain conditions. Sprockets also serve to change the speed and torque of the output shaft relative to the input shaft. By using sprockets of different sizes, engineers can achieve specific gear ratios that are essential for various operational requirements. For example, in industrial settings, sprockets are used in conveyor systems to ensure consistent and reliable material transport. Similarly, in automotive applications, sprockets are integral to the timing chain system that synchronizes engine valve operation with piston movement. Moreover, the design and material of sprockets contribute significantly to their functionality. High-quality sprockets are typically made from durable materials like steel or aluminum to withstand the stresses of continuous operation. The precision machining of sprocket teeth ensures minimal wear and tear on both the sprocket and the chain or belt, thereby extending the lifespan of the entire system. In summary, understanding the definition and purpose of a sprocket is fundamental to appreciating its role in mechanical systems. By facilitating efficient power transmission, adjusting gear ratios, and ensuring precise control over speed and direction, sprockets are indispensable components that underpin the operation of numerous machines and vehicles. Their versatility and reliability make them a cornerstone of modern engineering, enabling the smooth functioning of everything from simple bicycles to complex industrial machinery.
Key Components and Structure
When delving into the basics of a sprocket, it is crucial to understand its key components and structure, as these elements are fundamental to its operation and functionality. A sprocket, essentially a toothed wheel, is designed to engage with a chain or other toothed belt to transmit rotational motion. The primary components include the **hub**, **teeth**, and **bore**. The hub is the central part of the sprocket that connects it to a shaft or axle, providing the necessary support and stability. The teeth, which are evenly spaced around the circumference of the sprocket, are designed to mesh perfectly with the links of a chain or the teeth of a belt. These teeth come in various shapes and sizes depending on the application, such as roller chain sprockets or timing belt sprockets. The structure of a sprocket is meticulously engineered to ensure smooth and efficient power transmission. The **pitch circle** is an imaginary circle that passes through the center of each tooth, and it is critical for determining the size and compatibility of the sprocket with its corresponding chain or belt. The **pitch** itself refers to the distance between the centers of two adjacent teeth, which must match the pitch of the chain or belt for proper engagement. Additionally, sprockets can be classified into different types based on their structure, such as **simple sprockets**, which have a single row of teeth, and **duplex sprockets**, which feature two rows of teeth for increased load-carrying capacity. The material used in the construction of a sprocket also plays a significant role in its performance and durability. Common materials include steel, aluminum, and nylon, each chosen for its specific properties such as strength, weight, and resistance to wear and corrosion. Furthermore, sprockets often undergo various treatments like heat treatment or surface coating to enhance their lifespan and performance under different operating conditions. In summary, understanding the key components and structure of a sprocket is essential for appreciating how it functions within mechanical systems. By recognizing the role of the hub, teeth, bore, pitch circle, and material selection, one can better grasp the intricacies involved in designing and using sprockets effectively. This knowledge is vital for ensuring optimal performance, reliability, and longevity in applications ranging from industrial machinery to bicycles and motorcycles.
Types of Sprockets
### Types of Sprockets Understanding the various types of sprockets is crucial for selecting the right component for your machinery or vehicle. Sprockets, which are toothed wheels that engage with chains or belts to transmit power, come in several designs tailored to different applications and performance requirements. **1. **Chain Sprockets**: These are the most common type and are designed to work with roller chains. They have teeth that mesh with the chain links, providing a smooth and efficient power transmission. Chain sprockets are widely used in bicycles, motorcycles, and industrial machinery. **2. **Belt Sprockets**: Unlike chain sprockets, belt sprockets are designed to engage with timing belts or serpentine belts. These sprockets have a smooth surface or specific tooth profiles that match the belt's design, ensuring precise timing and reduced wear. They are commonly found in automotive engines and other precision-driven systems. **3. **Idler Sprockets**: Idler sprockets are used to guide and tension chains or belts rather than transmit power directly. They are typically mounted on adjustable arms to maintain optimal tension and prevent slippage or misalignment. **4. **Drive Sprockets**: These sprockets are attached to the driving shaft and are responsible for initiating the power transmission process. Drive sprockets come in various sizes and tooth counts to accommodate different chain or belt pitches. **5. **Driven Sprockets**: Located at the end of the power transmission system, driven sprockets receive the rotational force from the drive sprocket via the chain or belt. They can be larger or smaller than drive sprockets depending on the desired gear ratio. **6. **Split Sprockets**: Designed for easy installation and maintenance, split sprockets can be divided into two halves that can be bolted together around a shaft without needing to remove other components. This feature is particularly useful in industrial settings where downtime needs to be minimized. **7. **Hubless Sprockets**: These sprockets lack a central hub and are typically used in applications where space is limited or where a lighter weight is necessary. Hubless sprockets often require specialized mounting arrangements. **8. **Custom Sprockets**: For unique applications or specialized machinery, custom sprockets can be manufactured to meet specific requirements such as non-standard tooth counts, materials, or shapes. Custom sprockets offer flexibility but may come at a higher cost due to their bespoke nature. Each type of sprocket is engineered to optimize performance under different conditions, making it essential to choose the right one based on your specific needs. Whether you're working on a high-speed industrial conveyor or tuning a motorcycle, understanding these variations will help ensure efficient and reliable operation of your machinery. By selecting the appropriate sprocket type, you can enhance system durability, reduce maintenance costs, and achieve optimal performance.
Applications and Uses of Sprockets
Sprockets, toothed wheels that engage with chains or belts, are ubiquitous components in various industries due to their versatility and efficiency. Their applications span across multiple sectors, each leveraging their unique mechanical advantages. In the realm of **Industrial Machinery and Manufacturing**, sprockets play a crucial role in power transmission systems, ensuring smooth and consistent operation of machinery. They are integral in conveyor systems, pumps, and gearboxes, facilitating the production process and enhancing productivity. Beyond manufacturing, **Cycling and Bicycles** rely heavily on sprockets to optimize gear shifting and pedaling efficiency, making them essential for both recreational and competitive cycling. Additionally, **Automotive and Motorcycle Systems** utilize sprockets in chain-driven vehicles, contributing to the overall performance and reliability of these vehicles. Understanding the diverse applications of sprockets highlights their importance in modern engineering and technology. This article will delve into these uses, starting with the critical role sprockets play in **Industrial Machinery and Manufacturing**.
Industrial Machinery and Manufacturing
Industrial machinery and manufacturing form the backbone of modern industry, driving innovation and efficiency across various sectors. At the heart of these operations are critical components like sprockets, which play a pivotal role in ensuring smooth and reliable mechanical transmission. Sprockets, essentially toothed wheels that engage with chains or belts, are integral to the functioning of industrial machinery. In manufacturing environments, sprockets are used in conveyor systems to move materials efficiently from one stage of production to another. For instance, in automotive manufacturing, sprockets help in the precise movement of parts along assembly lines, ensuring that each component is accurately positioned and assembled. Similarly, in food processing plants, sprockets facilitate the continuous movement of products through different stages of processing, packaging, and distribution. The versatility of sprockets extends beyond these examples; they are also crucial in textile mills where they drive looms and spinning machines, and in construction equipment where they power cranes and excavators. The precision engineering of sprockets ensures that they can withstand heavy loads and operate under demanding conditions without compromising performance. This reliability is particularly important in industries such as aerospace and defense, where the failure of a single component could have significant consequences. Moreover, advancements in technology have led to the development of specialized sprockets designed for specific applications. For example, idler sprockets are used to guide chains around corners or over obstacles without causing wear or misalignment. Double-pitch sprockets offer greater flexibility by allowing chains to be easily removed or replaced without dismantling the entire system. These innovations enhance the overall efficiency and lifespan of industrial machinery. In addition to their functional benefits, sprockets contribute significantly to the safety and maintenance aspects of industrial operations. Properly maintained sprockets reduce the risk of mechanical failures that could lead to accidents or downtime. Regular inspection and replacement of worn-out sprockets prevent chain breakages and ensure continuous production flow. This proactive approach not only saves time but also reduces operational costs by minimizing the need for extensive repairs. The applications and uses of sprockets underscore their importance as a fundamental component in industrial machinery and manufacturing. By facilitating smooth mechanical transmission, enhancing efficiency, and ensuring reliability, sprockets are indispensable in modern industrial settings. As technology continues to evolve, it is likely that sprockets will remain a cornerstone of industrial operations, driving innovation and productivity forward.
Cycling and Bicycles
Cycling and bicycles are integral components of modern transportation, recreation, and fitness, with sprockets playing a crucial role in their functionality. The bicycle, a simple yet ingenious invention, has evolved significantly since its inception in the 19th century. Today, it serves multiple purposes: from daily commuting to professional racing, and from leisurely rides to rigorous mountain biking. At the heart of this versatility lies the sprocket—a toothed wheel that engages with a chain to transmit power and facilitate smooth gear changes. In road cycling, sprockets are essential for optimizing speed and efficiency. Road bikes typically feature a combination of front and rear sprockets, known as chainrings and cassettes, respectively. These allow cyclists to adjust their gear ratios according to terrain, enabling them to maintain an optimal cadence whether climbing steep hills or sprinting on flat surfaces. For instance, a smaller front sprocket paired with a larger rear sprocket provides easier pedaling for uphill climbs, while a larger front sprocket paired with a smaller rear sprocket allows for faster speeds on level ground. Mountain biking further underscores the importance of sprockets. Here, the terrain is often rugged and varied, requiring quick and precise gear shifts to navigate obstacles such as rocks, roots, and steep inclines. Modern mountain bikes frequently incorporate wide-range cassettes with numerous sprockets (often up to 12 or more), allowing riders to tackle diverse landscapes with ease. The ability to switch between these various sprockets ensures that cyclists can maintain momentum and control even in challenging conditions. Beyond performance-oriented cycling, sprockets also play a vital role in commuter and hybrid bicycles. These bikes are designed for practicality and comfort rather than pure speed or agility. They often feature internal gear hubs or single-speed setups that rely on sprockets for smooth operation. For example, an internal gear hub might use a set of internal sprockets to provide multiple gear ratios without the need for external derailleurs, making the bike more durable and low-maintenance. In addition to their mechanical function, sprockets contribute significantly to the overall user experience of cycling. Properly maintained sprockets ensure quiet operation, reduced wear on other components, and enhanced safety by minimizing the risk of chain derailment or breakage. Moreover, advancements in sprocket technology have led to lighter materials and more efficient designs, contributing to improved performance across all types of cycling. The engagement between sprockets and chains also highlights the importance of precision engineering in bicycle design. Misaligned or worn-out sprockets can lead to poor shifting performance, increased wear on other components, and even safety hazards. Therefore, cyclists must regularly inspect and maintain their sprockets to ensure optimal performance and longevity of their bicycles. In conclusion, sprockets are fundamental to the operation and versatility of bicycles across various disciplines. Whether you are a professional athlete, a casual commuter, or an avid recreational rider, understanding the role of sprockets can enhance your cycling experience. Their ability to facilitate efficient power transmission makes them an indispensable component in modern bicycle design, underscoring their significance in the broader context of applications and uses of sprockets.
Automotive and Motorcycle Systems
In the realm of automotive and motorcycle systems, sprockets play a pivotal role in ensuring efficient and reliable power transmission. These toothed wheels are integral components of the drivetrain, facilitating the smooth transfer of rotational motion from one shaft to another. In vehicles, sprockets are often used in conjunction with chains or belts to drive the wheels, thereby converting the engine's power into forward motion. For instance, in motorcycles, the front sprocket is attached to the crankshaft and works in tandem with the rear sprocket, which is connected to the rear wheel via a chain. This setup allows for precise gear ratios that optimize speed and torque, enabling riders to navigate various terrains with ease. In automotive applications, sprockets are commonly found in timing systems where they synchronize the rotation of the crankshaft and camshaft, ensuring that valves open and close at the right time relative to piston movement. This synchronization is crucial for maintaining engine performance and preventing potential damage. Additionally, sprockets are used in drive systems such as those found in all-wheel-drive vehicles, where they help distribute power between different axles to enhance traction and stability. The design and material of sprockets are tailored to meet specific demands within these systems. For example, motorcycle sprockets are typically made from durable materials like steel or aluminum to withstand high stresses and wear over time. The teeth on these sprockets are precision-cut to ensure a snug fit with the chain, minimizing slippage and maximizing efficiency. Similarly, automotive sprockets must be engineered to handle the constant stress of engine operation while maintaining precise timing and synchronization. Beyond their functional role, sprockets also offer flexibility in terms of customization and tuning. In the motorcycle community, riders often upgrade or modify their sprockets to adjust gear ratios for better performance in specific riding conditions. For instance, changing the front or rear sprocket can alter the bike's acceleration and top speed, allowing riders to fine-tune their vehicle according to their preferences or the demands of different terrains. Moreover, advancements in technology have led to the development of more sophisticated sprocket designs that enhance durability and performance. For example, some modern sprockets feature hardened teeth or specialized coatings that reduce wear and tear, extending their lifespan and requiring less maintenance. These innovations underscore the ongoing importance of sprockets in automotive and motorcycle systems, where reliability and efficiency are paramount. In summary, sprockets are indispensable components within automotive and motorcycle systems, facilitating power transmission and ensuring optimal performance. Their versatility, durability, and precision engineering make them a critical part of modern vehicle design, enabling vehicles to operate efficiently across various conditions. Whether in timing systems or drivetrains, sprockets continue to play a vital role in the functionality and reliability of both cars and motorcycles.
Design, Maintenance, and Selection Criteria
When it comes to ensuring the optimal performance and longevity of machinery, the design, maintenance, and selection of critical components like sprockets are paramount. A well-designed sprocket not only enhances the efficiency of the entire system but also contributes significantly to its durability. This article delves into three crucial aspects: **Design Considerations and Materials**, **Maintenance Tips for Longevity**, and **Criteria for Selecting the Right Sprocket**. Understanding these elements is essential for engineers, technicians, and anyone involved in the operation and upkeep of mechanical systems. By focusing on the right design considerations and materials, one can create a sprocket that meets specific operational demands while minimizing wear and tear. Proper maintenance tips can extend the lifespan of these components, reducing downtime and costs associated with frequent replacements. Finally, knowing the criteria for selecting the right sprocket ensures that the chosen component aligns with the system's requirements, thereby optimizing overall performance. Let's begin by exploring the critical **Design Considerations and Materials** that form the foundation of a high-quality sprocket.
Design Considerations and Materials
When designing a sprocket, several key considerations must be taken into account to ensure optimal performance, durability, and compatibility with the system it will be part of. **Material selection** is one of the most critical factors. Sprockets are typically made from high-strength, wear-resistant materials such as steel, cast iron, or specialized alloys. For example, carbon steel is often used due to its excellent strength-to-weight ratio and cost-effectiveness. However, in applications where corrosion resistance is crucial, stainless steel or bronze may be preferred. In high-performance or heavy-duty applications, sprockets might be made from hardened steel or even advanced materials like titanium for added strength and lightness. **Design considerations** also play a pivotal role. The tooth profile and pitch must be carefully designed to match the chain or belt it will interact with, ensuring smooth engagement and minimizing wear. The number of teeth on the sprocket affects its rotational speed and torque output; more teeth generally result in smoother operation but may reduce rotational speed. Additionally, the sprocket's hub design—whether it is a plain bore, keyed, or splined—must align with the shaft it will be mounted on to prevent slippage and ensure secure attachment. **Maintenance** is another essential aspect to consider during the design phase. Easy access for inspection and replacement can significantly reduce downtime and maintenance costs. Features such as removable hubs or split sprockets can facilitate this process. Furthermore, coatings or treatments like chrome plating or nitriding can enhance wear resistance and extend the lifespan of the sprocket. **Selection criteria** should include an assessment of the operational environment. For instance, in dusty or dirty conditions, sealed sprockets may be necessary to protect against contamination. In applications involving high temperatures or extreme loads, specialized materials and designs may be required to maintain integrity. The weight and size constraints of the system must also be considered; lighter sprockets can reduce overall system weight but may compromise on strength. In summary, designing a sprocket involves a multifaceted approach that balances material properties, design specifications, maintenance needs, and operational requirements. By carefully considering these factors, engineers can create sprockets that optimize system performance while ensuring reliability and longevity. This holistic approach not only enhances the efficiency of machinery but also contributes to overall system durability and cost-effectiveness.
Maintenance Tips for Longevity
**Maintenance Tips for Longevity** To ensure the longevity and optimal performance of sprockets, regular maintenance is crucial. Here are some key tips to help extend the life of your sprockets and maintain their efficiency: 1. **Regular Inspection**: Conduct frequent visual inspections to check for signs of wear, such as tooth wear, cracks, or corrosion. Use a micrometer to measure the diameter of the sprocket teeth to determine if they have worn beyond acceptable limits. 2. **Proper Lubrication**: Adequate lubrication is essential for reducing friction between the sprocket and chain. Use a high-quality chain lube that is compatible with your system, and apply it according to the manufacturer's recommendations. 3. **Chain Tension**: Maintain the correct chain tension to prevent excessive wear on both the sprocket and chain. Over-tightening can lead to premature wear, while under-tightening can cause the chain to skip teeth. 4. **Alignment**: Ensure that the sprockets are properly aligned with each other and with the chain. Misalignment can lead to uneven wear and reduce the lifespan of your sprockets. 5. **Cleaning**: Regularly clean the sprockets and surrounding areas to remove dirt, debris, and old lubricant. This helps prevent contamination and ensures smooth operation. 6. **Replacement**: Replace sprockets and chains together if possible, as new chains on old sprockets can lead to rapid wear due to the mismatched surfaces. 7. **Environmental Considerations**: Protect your sprockets from harsh environmental conditions such as extreme temperatures, moisture, and exposure to chemicals. Use protective coatings or housings if necessary. 8. **Load Management**: Avoid overloading your system beyond its rated capacity, as this can cause excessive stress on the sprockets leading to premature failure. 9. **Documentation**: Keep a maintenance log to track inspections, lubrications, and replacements. This helps in identifying patterns of wear and planning preventive maintenance. 10. **Training**: Ensure that personnel responsible for maintenance are properly trained in handling and inspecting sprockets to avoid human error. By following these maintenance tips, you can significantly extend the lifespan of your sprockets, reduce downtime, and maintain the overall efficiency of your machinery. Regular maintenance not only saves costs in the long run but also ensures safety by preventing unexpected failures that could lead to accidents or injuries. Incorporating these practices into your routine will help you get the most out of your sprockets and keep your machinery running smoothly for years to come.
Criteria for Selecting the Right Sprocket
When it comes to selecting the right sprocket for your machinery or vehicle, several critical criteria must be carefully considered to ensure optimal performance, efficiency, and longevity. **Design Compatibility** is a paramount factor; the sprocket must be compatible with the chain or belt it will be paired with. This includes matching the pitch, tooth count, and material specifications to avoid premature wear and potential system failure. **Material Selection** is another key criterion, as different materials offer varying levels of strength, durability, and resistance to corrosion. For instance, steel sprockets are robust and suitable for heavy-duty applications, while aluminum or nylon sprockets may be preferred for lighter loads where weight reduction is crucial. **Load Capacity** must also be meticulously evaluated to ensure the sprocket can handle the operational stresses without compromising its integrity. This involves calculating the maximum torque and load that the sprocket will encounter during operation and selecting a sprocket with a corresponding load rating. **Speed and RPM** considerations are equally important; high-speed applications require sprockets designed to withstand centrifugal forces and maintain precision alignment. **Maintenance Accessibility** is another vital aspect; selecting a sprocket that is easy to inspect, clean, and replace can significantly reduce downtime and maintenance costs. **Environmental Conditions** should also be taken into account; for example, sprockets used in harsh environments such as high-temperature or corrosive settings may require specialized coatings or materials to extend their lifespan. Additionally, **Noise Reduction** and **Vibration Control** can be significant factors depending on the application. Sprockets designed with noise-reducing features or those that help in minimizing vibrations can enhance overall system performance and user comfort. **Cost-Effectiveness** is another criterion that needs careful consideration; while cheaper options might seem appealing initially, they may lead to higher maintenance costs or more frequent replacements in the long run. Finally, **Regulatory Compliance** and **Industry Standards** must be adhered to, ensuring that the selected sprocket meets all relevant safety and performance standards for the specific industry or application. By meticulously evaluating these criteria, engineers and technicians can make informed decisions that optimize system efficiency, reliability, and longevity. This comprehensive approach not only enhances operational performance but also contributes to a safer working environment and reduced maintenance overheads.