What Is A Manometer

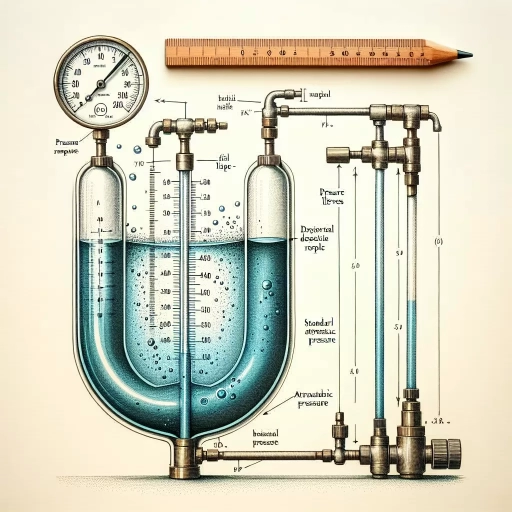
A manometer is a crucial tool in various scientific and industrial fields, designed to measure pressure in gases and liquids. Understanding its fundamental principles, operational mechanisms, and diverse applications is essential for anyone working with pressure measurements. This article delves into the core aspects of manometers, starting with **Understanding the Basics of a Manometer**, where we explore the definition, types, and key components of these devices. We then proceed to **How Manometers Work**, explaining the physics behind their operation and the different methods they employ to measure pressure. Finally, we examine **Applications and Uses of Manometers**, highlighting their importance in fields such as engineering, medicine, and environmental monitoring. By grasping these concepts, readers will gain a comprehensive insight into the role and functionality of manometers. Let's begin by understanding the basics of a manometer.
Understanding the Basics of a Manometer
Understanding the basics of a manometer is crucial for anyone working in fields such as engineering, physics, and chemistry. A manometer is an essential tool used to measure pressure differences in various systems. To grasp its significance, it is important to delve into three key aspects: the definition and purpose of a manometer, the different types available, and its historical development. Firstly, understanding the definition and purpose of a manometer sets the foundation for its practical applications. This involves recognizing how it measures pressure and why it is indispensable in various industrial and scientific contexts. Secondly, exploring the types of manometers reveals the versatility of this instrument. From U-tube manometers to digital manometers, each type has unique characteristics and uses, making them suitable for different scenarios. Lastly, examining the historical development of manometers provides insight into how this technology has evolved over time, contributing to its current precision and reliability. By starting with the definition and purpose of a manometer, we can establish a clear understanding of its role and importance, setting the stage for a deeper exploration of its types and historical background.
Definition and Purpose
A manometer is a precision instrument designed to measure pressure in various environments, including industrial, medical, and scientific settings. **Definition and Purpose** are crucial aspects of understanding its functionality. **Definition:** A manometer is a device that quantifies the pressure of a fluid (liquid or gas) relative to atmospheric pressure. It operates by comparing the pressure of the fluid being measured against a reference pressure, typically atmospheric pressure or a vacuum. Manometers can be categorized into different types, such as U-tube manometers, inclined manometers, and digital manometers, each with its own specific design and application. **Purpose:** The primary purpose of a manometer is to provide accurate and reliable pressure measurements. In industrial settings, manometers are used to monitor and control pressure levels in pipelines, tanks, and other equipment to ensure safe and efficient operation. In medical contexts, they are used to measure blood pressure and other bodily pressures. In scientific research, manometers help in studying fluid dynamics and pressure variations in experiments. Additionally, manometers serve as diagnostic tools to detect leaks or blockages in systems by identifying abnormal pressure readings. Understanding the definition and purpose of a manometer is essential for selecting the appropriate type of manometer for a specific application and ensuring accurate measurements. This knowledge also aids in maintaining and troubleshooting systems where pressure monitoring is critical. By grasping these fundamental concepts, users can effectively utilize manometers to enhance safety, efficiency, and precision across various fields.
Types of Manometers
Manometers are versatile instruments used to measure pressure in various applications, and they come in several types, each designed to cater to different needs and environments. **1. U-Tube Manometer:** This is one of the most common types, consisting of a U-shaped tube filled with a liquid, typically water or mercury. It measures the difference in pressure between two points by observing the displacement of the liquid column. **2. Inclined Manometer:** An inclined version of the U-tube manometer, this type is more sensitive and used for measuring low pressures. The inclined tube allows for more precise readings due to the increased length of the liquid column. **3. Micromanometer:** Designed for very precise measurements, micromanometers are often used in laboratory settings. They can measure extremely small pressure differences and are typically more accurate than standard U-tube manometers. **4. Digital Manometer:** These modern manometers use electronic sensors to measure pressure and display the readings on an LCD screen. They offer high accuracy, ease of use, and the ability to store data for later analysis. **5. Bourdon Tube Manometer:** This type uses a curved tube that changes shape in response to changes in pressure. The movement of the tube is linked to a pointer on a dial, providing a direct reading of the pressure. **6. Diaphragm Manometer:** Utilizing a flexible diaphragm that moves in response to pressure changes, this type is often used in applications where the pressure difference is small. It can be connected to a gauge or indicator for easy reading. **7. Capacitance Manometer:** These manometers measure pressure by detecting changes in capacitance caused by the movement of a diaphragm. They are highly accurate and commonly used in vacuum and low-pressure applications. **8. Piezoresistive Manometer:** This type uses piezoresistive materials that change their electrical resistance in response to pressure changes. They are compact, durable, and suitable for a wide range of pressures. Each type of manometer has its own set of advantages and is chosen based on the specific requirements of the application, including accuracy, range, and environmental conditions. Understanding these different types is crucial for selecting the right tool for precise and reliable pressure measurements.
Historical Development
The historical development of the manometer is a fascinating journey that spans centuries, reflecting advancements in scientific understanding and technological innovation. The concept of measuring pressure dates back to ancient civilizations, but the modern manometer as we know it today has its roots in the 17th century. In 1643, Italian scientist Evangelista Torricelli conducted an experiment using a mercury column to measure atmospheric pressure, laying the groundwork for the development of the first mercury barometer. This early device was essentially a manometer, as it measured pressure relative to a reference point—vacuum in this case. Over the next few centuries, scientists and engineers refined these early designs. In the late 18th century, French physicist Jean-André Deluc introduced improvements to the mercury barometer, making it more practical for everyday use. The 19th century saw significant advancements with the invention of aneroid barometers by French scientist Lucien Vidi in 1844. These aneroid manometers used a series of evacuated metal cylinders that expanded or contracted with changes in pressure, offering a more compact and durable alternative to mercury-filled devices. The early 20th century brought further innovations with the introduction of Bourdon tube manometers. Invented by French engineer Eugene Bourdon in 1849 but widely adopted in the early 20th century, these manometers used a curved tube that straightened or bent in response to changes in pressure. This design became ubiquitous in industrial settings due to its reliability and ease of use. Modern manometers have evolved to incorporate various materials and technologies. Digital manometers, which emerged in the latter half of the 20th century, utilize electronic sensors and microprocessors to provide highly accurate and precise measurements. These devices often feature data logging capabilities and can be connected to computers for real-time monitoring and analysis. In addition to these technological advancements, materials science has played a crucial role in the development of contemporary manometers. The use of corrosion-resistant materials such as stainless steel and advanced polymers has enhanced durability and expanded the range of applications for manometers across different industries, including aerospace, chemical processing, and medical research. Today, manometers are indispensable tools in various fields, from engineering and manufacturing to scientific research and healthcare. Their ability to accurately measure pressure has been refined over centuries through continuous innovation and improvement. Understanding the historical development of manometers provides a deeper appreciation for their importance and the significant role they play in modern technology. This historical context also underscores the ongoing quest for precision and reliability that drives the evolution of these critical measurement devices.
How Manometers Work
Manometers are essential tools in various fields, including engineering, physics, and chemistry, for measuring pressure differences in fluids. Understanding how manometers work involves delving into three key aspects: the principle of operation, components and construction, and measurement accuracy and precision. At the heart of a manometer's functionality lies the principle of operation, which is based on the balance of fluid columns and the application of hydrostatic pressure principles. This fundamental concept allows manometers to accurately measure pressure differences by equating the weight of fluid columns. Additionally, the components and construction of manometers play a crucial role in their performance, as materials and design can affect durability and reliability. Finally, ensuring high measurement accuracy and precision is vital for reliable data, which depends on factors such as calibration and environmental conditions. By grasping these elements, one can fully appreciate the intricate mechanisms behind manometers. Let's start by exploring the principle of operation in more detail.
Principle of Operation
The principle of operation for a manometer, a device used to measure pressure, is based on the fundamental concept of hydrostatic pressure and the balance of fluid columns. Here’s how it works: A manometer typically consists of a U-shaped tube filled with a liquid, such as water or mercury, which has a known density. When connected to a system where pressure needs to be measured, the difference in pressure between the two ends of the manometer causes the liquid column to rise or fall in one arm relative to the other. This movement is directly proportional to the pressure difference being measured. For instance, in a U-tube manometer, if one end is connected to a pressurized system and the other end is open to the atmosphere, the pressure difference between these two points will cause the liquid in the tube to shift. The height difference between the two liquid columns in the arms of the U-tube is then measured, and using the formula \(P = \rho g h\), where \(P\) is the pressure difference, \(\rho\) is the density of the liquid, \(g\) is the acceleration due to gravity, and \(h\) is the height difference, the pressure can be calculated accurately. In addition to U-tube manometers, there are other types such as inclined manometers and digital manometers that operate on similar principles but offer different advantages in terms of sensitivity and ease of use. Inclined manometers, for example, use an inclined tube to amplify small changes in pressure, making them more sensitive for low-pressure measurements. Digital manometers, on the other hand, use electronic sensors to measure pressure and display it directly on a screen, eliminating the need for manual calculations. Overall, the principle of operation for manometers relies on the precise measurement of fluid column heights and the application of hydrostatic principles to determine pressure differences accurately. This makes manometers versatile tools in various fields such as engineering, chemistry, and medical research where precise pressure measurements are crucial.
Components and Construction
A manometer's functionality is deeply rooted in its components and construction, which collectively enable precise pressure measurements. The primary components include the pressure-sensing element, the fluid or gas medium, and the indicating device. 1. **Pressure-Sensing Element**: This is typically a tube or chamber that responds to changes in pressure. In a U-tube manometer, for instance, it consists of two connected vertical tubes filled with a fluid such as water or mercury. The difference in fluid levels between the two tubes directly correlates with the pressure difference being measured. 2. **Fluid or Gas Medium**: The choice of fluid is crucial as it affects the sensitivity and range of the manometer. Mercury is often used due to its high density, allowing for more accurate measurements over a wider range of pressures. However, water and other liquids can also be used depending on the application. 3. **Indicating Device**: This component displays the measured pressure. It can be as simple as a graduated scale on the side of the U-tube or more complex electronic devices that convert mechanical displacement into digital readings. The construction of a manometer involves careful consideration of material selection, calibration, and sealing to ensure accuracy and durability. The tubes are typically made from materials like glass or stainless steel to minimize corrosion and ensure transparency for visual readings. Calibration involves marking the graduated scale with precise measurements to correspond with known pressures, often using a reference standard. In addition to these core components, modern manometers may include additional features such as temperature compensation mechanisms to account for thermal expansion of the fluid, and protective enclosures to shield against environmental factors like dust and moisture. Overall, the meticulous design and construction of these components allow manometers to provide reliable and accurate pressure measurements across various industrial and scientific applications, making them indispensable tools in fields ranging from engineering to medical research.
Measurement Accuracy and Precision
**Measurement Accuracy and Precision** In the context of manometers, understanding measurement accuracy and precision is crucial for reliable and meaningful readings. **Accuracy** refers to how close a measurement is to the true value. It indicates the degree of closeness to the actual value, with higher accuracy meaning less deviation from the true value. For instance, if a manometer consistently measures a pressure that is very close to the actual pressure, it is considered accurate. On the other hand, **precision** pertains to the consistency or reproducibility of measurements. A precise measurement is one that yields consistent results under the same conditions, even if those results are not necessarily accurate. For example, if a manometer always reads 10.5 psi when the actual pressure is 10.0 psi, it is precise but not accurate. To achieve both high accuracy and precision in manometer readings, several factors must be considered. First, the calibration of the manometer is critical; it should be calibrated against a known standard to ensure that its readings are accurate. Regular maintenance and checks for any mechanical or environmental factors that could affect readings are also essential. Additionally, the selection of the appropriate type of manometer for the specific application is vital. For instance, digital manometers often offer higher precision and accuracy compared to analog ones due to their ability to provide more precise digital readings. Environmental conditions such as temperature and humidity can also impact measurement accuracy and precision. Temperature changes can affect the expansion and contraction of materials within the manometer, leading to variations in readings. Therefore, using manometers that are designed to operate within specific temperature ranges or compensating for these changes is necessary. Furthermore, user error can significantly impact both accuracy and precision. Proper training on how to use the manometer correctly, including ensuring that it is properly connected and that readings are taken consistently, is essential. Following manufacturer guidelines and best practices helps in minimizing human error. In summary, achieving high measurement accuracy and precision with manometers involves careful calibration, regular maintenance, appropriate selection of equipment, consideration of environmental factors, and proper user technique. By focusing on these aspects, users can ensure that their manometer readings are reliable and trustworthy, which is paramount in various industrial and scientific applications where precise pressure measurements are critical.
Applications and Uses of Manometers
Manometers are versatile instruments that measure pressure in various environments, making them indispensable across multiple domains. Their applications span industrial settings, scientific research and laboratory use, and everyday practical uses. In industrial applications, manometers are crucial for monitoring and controlling pressure in machinery and pipelines, ensuring safety and efficiency. They are also vital in scientific research and laboratory settings, where precise pressure measurements are necessary for experiments and data collection. Additionally, manometers find practical use in everyday life, such as in plumbing and HVAC systems, helping to diagnose issues and maintain optimal performance. This article will delve into these three key areas, starting with the critical role manometers play in industrial applications.
Industrial Applications
Industrial applications of manometers are diverse and critical, reflecting their versatility and reliability in measuring pressure across various sectors. In the **petroleum industry**, manometers are used to monitor pressure in pipelines, ensuring safe and efficient transportation of crude oil and natural gas. They help in detecting any anomalies or leaks that could lead to catastrophic failures. **Chemical processing** also heavily relies on manometers to control and monitor the pressure of chemical reactions, which is crucial for maintaining safety standards and optimizing production processes. In **power generation**, manometers are essential for monitoring boiler pressure, steam pressure, and other critical parameters that ensure the smooth operation of power plants. This includes both conventional fossil fuel-based plants and nuclear power plants, where precise pressure measurement is vital for safety and efficiency. **Aerospace engineering** utilizes manometers in the testing and calibration of aircraft systems, including fuel systems and hydraulic systems, to ensure that all components operate within specified pressure ranges. **Pharmaceutical manufacturing** employs manometers to maintain sterile environments by monitoring the pressure in clean rooms and isolators. This is crucial for preventing contamination and ensuring the quality of pharmaceutical products. **HVAC (Heating, Ventilation, and Air Conditioning) systems** also use manometers to measure pressure differences across filters, coils, and other components, helping in diagnosing issues and optimizing system performance. In **water treatment plants**, manometers are used to monitor water pressure in distribution networks, helping in the efficient supply of clean water to consumers. They also play a role in wastewater treatment by measuring pressure in sludge handling systems. **Automotive manufacturing** uses manometers in the testing of vehicle components such as fuel injectors and brake systems, ensuring that they meet the required specifications. Furthermore, **medical devices** like ventilators and anesthesia machines rely on manometers to measure gas pressures accurately, which is critical for patient safety. **Food processing** industries use manometers to monitor pressure in packaging lines and pasteurization processes, ensuring that products are processed safely and efficiently. Overall, the accuracy and reliability of manometers make them indispensable tools across a wide range of industrial applications, contributing significantly to safety, efficiency, and product quality. Their ability to provide precise pressure measurements under various conditions makes them a cornerstone in many industrial processes.
Scientific Research and Laboratory Use
Scientific research and laboratory use are pivotal domains where manometers play a crucial role. In these settings, precise measurement of pressure is essential for conducting experiments, validating hypotheses, and ensuring the safety of both personnel and equipment. Manometers, with their ability to accurately measure pressure differences, are indispensable tools in various scientific disciplines. In chemistry labs, manometers are used to monitor the pressure within reaction vessels, which is critical for controlling chemical reactions and preventing potential hazards such as explosions. For instance, during the synthesis of gases or volatile compounds, real-time pressure monitoring helps researchers adjust conditions to maintain safe operating parameters. In physics and engineering labs, manometers are employed to measure pressure in fluid dynamics experiments. They help in studying the behavior of fluids under different conditions, such as flow rates and pressure drops across various systems. This data is crucial for designing efficient systems like pipelines, hydraulic systems, and aerodynamic models. Biology and biochemistry labs also rely on manometers for maintaining controlled environments. For example, in cell culture experiments, precise control over atmospheric pressure is necessary to simulate physiological conditions. Manometers ensure that the pressure within incubators or bioreactors remains stable, which is vital for cell growth and viability. Furthermore, in environmental science and geology, manometers are used to measure pressure in soil and groundwater studies. This helps researchers understand soil mechanics and groundwater flow patterns, which are essential for predicting natural hazards like landslides and assessing groundwater quality. In addition to these applications, manometers are integral in the calibration of other pressure-measuring instruments. By providing a reference point for calibration, they ensure that all measurements taken in the lab are accurate and reliable. This is particularly important in industries where precise pressure control can mean the difference between safety and disaster. Overall, the versatility and accuracy of manometers make them an essential component of scientific research and laboratory use. They enable researchers to collect reliable data, maintain safe working conditions, and advance our understanding of various scientific phenomena. As technology continues to evolve, the role of manometers will remain vital in ensuring the precision and reliability of scientific measurements.
Everyday Practical Uses
Manometers have a wide range of everyday practical uses across various industries and settings, making them indispensable tools for measuring pressure. In **industrial settings**, manometers are crucial for monitoring and controlling pressure in pipelines, tanks, and other equipment to ensure safe and efficient operations. For instance, in oil refineries, manometers help in maintaining the optimal pressure levels necessary for chemical processes. Similarly, in power plants, they are used to measure the pressure of steam and gas lines, which is vital for energy production. In **medical facilities**, manometers are essential for monitoring blood pressure and other bodily pressures. Sphygmomanometers, a type of manometer, are used by healthcare professionals to measure blood pressure accurately, which is a critical diagnostic tool. Additionally, manometers are used in anesthesia machines to ensure that patients receive the correct amount of anesthetic gases during surgical procedures. In **home maintenance**, manometers are useful for diagnosing issues with heating and cooling systems. For example, a manometer can help homeowners check the pressure in their HVAC systems to identify leaks or blockages that might be affecting system performance. This can lead to significant energy savings and extend the lifespan of the equipment. In **automotive repair**, manometers are employed to test the pressure in vehicle systems such as fuel lines, brake systems, and cooling systems. Mechanics use these tools to diagnose problems like low fuel pressure or air leaks in the brake system, ensuring that vehicles are safe to operate. In **scientific research**, manometers play a key role in experiments involving gases and liquids. Researchers use precision manometers to measure the pressure changes in various experiments, such as those involving chemical reactions or the study of atmospheric conditions. Furthermore, **in aviation**, manometers are critical for ensuring the safety of aircraft operations. They are used to check the pressure in tires, fuel tanks, and hydraulic systems, all of which are vital for safe flight operations. Overall, the versatility and accuracy of manometers make them indispensable tools across multiple sectors, contributing significantly to safety, efficiency, and precision in various applications. Their ability to provide reliable pressure measurements makes them a cornerstone in many everyday practical uses.