What Is A Valve

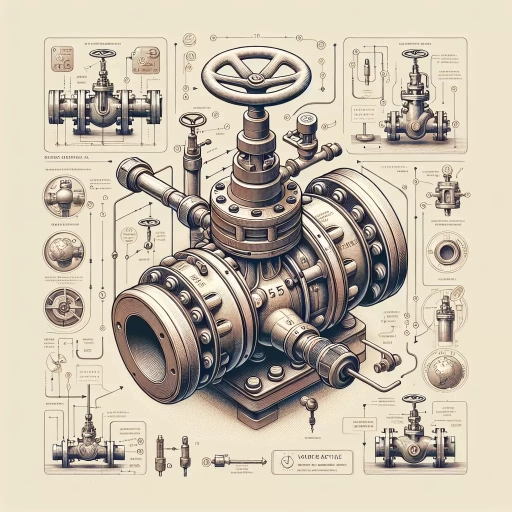
In the intricate world of mechanical engineering and fluid dynamics, valves play a crucial role in controlling the flow of fluids, gases, and even solids. These versatile components are essential in various industries, from plumbing and HVAC systems to chemical processing and aerospace engineering. Understanding what a valve is and how it functions is fundamental to appreciating its widespread applications and the importance of proper maintenance. This article delves into the multifaceted nature of valves, beginning with **Understanding the Basics of Valves**, where we explore the fundamental principles and types of valves. We then examine **Applications and Uses of Valves**, highlighting their critical roles in different sectors. Finally, we discuss **Operational Principles and Maintenance**, providing insights into how valves operate and the best practices for ensuring their longevity and efficiency. By grasping these key aspects, readers will gain a comprehensive understanding of valves and their indispensable role in modern technology. Let's start by diving into the basics of valves to lay the groundwork for this in-depth exploration.
Understanding the Basics of Valves
Understanding the basics of valves is crucial for anyone involved in engineering, plumbing, or any field where fluid control is essential. Valves are fundamental components that regulate the flow of fluids, gases, and even solids in various systems. To grasp their significance, it is important to delve into three key aspects: the definition and purpose of valves, the diverse types available, and the key components that make them functional. Firstly, understanding the definition and purpose of valves sets the foundation for appreciating their role in different applications. Valves are designed to control the flow, pressure, and direction of fluids, ensuring that systems operate efficiently and safely. This foundational knowledge is vital for selecting the right valve for specific tasks. Secondly, recognizing the various types of valves—such as ball valves, gate valves, globe valves, and butterfly valves—helps in identifying which type best suits a particular application. Each type has unique characteristics and advantages that make it suitable for different scenarios. Lastly, familiarizing oneself with the key components of valves, such as the body, bonnet, stem, and seat, provides insight into how they function and how to maintain them effectively. By exploring these three areas, one can gain a comprehensive understanding of valves and their critical role in modern engineering and technology. Let's begin by examining the **Definition and Purpose** of valves to establish a solid foundation for our discussion.
Definition and Purpose
**Definition and Purpose** At the heart of various industrial, mechanical, and plumbing systems lies a crucial component known as a valve. A valve is essentially a device that regulates, directs, or controls the flow of fluids (gases, liquids, fluidized solids, or slurries) by opening, closing, or partially obstructing passageways. The primary purpose of a valve is to manage the flow rate, pressure, and direction of fluids within a system. This control is vital for ensuring the safe and efficient operation of processes in diverse fields such as oil and gas, chemical processing, water treatment, and even household plumbing. Valves serve multiple functions depending on their design and application. For instance, **isolation valves** are used to completely stop the flow of fluid when needed, such as during maintenance or repair. **Regulating valves**, on the other hand, adjust the flow rate to maintain desired levels of pressure or temperature. **Check valves** prevent backflow by allowing fluid to flow in one direction while blocking it in the opposite direction. Each type of valve is engineered to meet specific requirements and ensure that the system operates within optimal parameters. The purpose of valves extends beyond mere flow control; they also play a critical role in safety and efficiency. In high-pressure systems, valves can prevent catastrophic failures by relieving excess pressure or shutting off the flow in case of an emergency. In chemical plants, valves help maintain precise conditions necessary for chemical reactions. In water distribution networks, valves ensure that water reaches consumers with the right pressure and quality. Additionally, valves contribute to energy efficiency by minimizing leaks and optimizing fluid flow paths. Understanding the basics of valves is essential for anyone involved in designing, operating, or maintaining fluid-based systems. Knowing how different types of valves function and their specific applications can help in selecting the right valve for a particular task. This knowledge also aids in troubleshooting issues related to fluid flow and pressure, thereby enhancing overall system performance and reliability. As technology advances, valves continue to evolve with innovations such as automated control systems and smart valves that offer real-time monitoring and adjustment capabilities. These advancements further underscore the importance of valves in modern engineering and highlight their role as indispensable components in a wide range of applications. By grasping the definition and purpose of valves, individuals can better appreciate their significance and make informed decisions regarding their use in various contexts.
Types of Valves
Valves are crucial components in various industrial, mechanical, and plumbing systems, serving to control the flow of fluids, gases, or other substances. There are several types of valves, each designed to meet specific needs and applications. **Ball Valves** are one of the most common types, characterized by a rotating ball with a hole through its center. When the ball is aligned with the flow path, the valve is open; when it is perpendicular, the valve is closed. Ball valves are known for their ease of operation and tight sealing. **Butterfly Valves** consist of a disk that rotates on a shaft to control flow. They are lightweight, compact, and often used in large pipe sizes due to their simplicity and cost-effectiveness. **Gate Valves** feature a gate that moves up and down to allow or block flow. These valves are typically used for on/off applications and are known for their minimal pressure drop when fully open. **Globe Valves** have a plug or disc that moves up and down to control flow through a narrow passageway. They are versatile and can be used for both on/off and throttling applications, making them suitable for systems requiring precise control over flow rates. **Needle Valves** are similar to globe valves but have a more precise control mechanism, making them ideal for applications requiring fine-tuning of flow rates. **Check Valves** ensure that fluid flows in one direction only, preventing backflow. They come in various designs such as swing check valves, lift check valves, and ball check valves. **Diaphragm Valves** use a flexible diaphragm to control flow and are often used in applications where contamination must be avoided, such as in food processing or pharmaceutical industries. **Plug Valves** operate by rotating a cylindrical plug to align or block the flow path. They are known for their simplicity and resistance to wear and tear. **Pinch Valves** use a flexible tube that can be pinched to shut off flow; these are commonly used in slurry applications where particulate matter could clog other types of valves. **Control Valves** are designed to regulate flow based on external signals from controllers or sensors. They are critical in process control systems where precise control over flow rates is necessary. **Safety Valves** protect systems from overpressure by automatically opening to release excess pressure when it exceeds a set limit. Understanding these different types of valves is essential for selecting the right valve for specific applications, ensuring efficient operation, safety, and longevity of the system. Each type has its unique characteristics, advantages, and limitations, making it crucial to consider factors such as flow requirements, pressure conditions, and material compatibility when choosing a valve. By selecting the appropriate type of valve, engineers and technicians can optimize system performance and maintain operational integrity.
Key Components
When delving into the basics of valves, it is crucial to understand the key components that make up these essential devices. A valve, fundamentally, is a mechanical device that controls the flow of fluids (liquids, gases, or slurries) by opening, closing, or partially obstructing passageways. The primary components of a valve include the **body**, **bonnet**, **trim**, **actuator**, and **seal**. The **body** of the valve is its main structure and houses the other components. It is typically made from materials such as stainless steel, cast iron, or PVC, depending on the application and environment in which it will be used. The body contains the inlet and outlet ports through which the fluid flows. Attached to the body is the **bonnet**, which covers the valve's internal workings. The bonnet can be screwed or bolted onto the body and may be made from the same material as the body or a different one. It provides access for maintenance and repair. Inside the valve body lies the **trim**, which includes the moving parts that control fluid flow. Key trim components include the **disc** (or plug), **seat**, and **stem**. The disc or plug is the part that moves to open or close the valve, while the seat is the stationary part against which the disc or plug seals. The stem connects the disc or plug to an actuator, allowing for controlled movement. The **actuator** is a critical component that provides the force necessary to operate the valve. Common types of actuators include manual handwheels, levers, or gears; pneumatic or hydraulic cylinders; and electric motors. The choice of actuator depends on factors such as the size of the valve, the pressure differential across it, and whether automation is required. Finally, **seals** are vital for ensuring that the valve operates efficiently without leaks. Seals can be found at various points within the valve, including between the body and bonnet, around the stem where it passes through the bonnet, and between moving parts like the disc and seat. Materials used for seals include rubber, Teflon, and metal gaskets. Understanding these key components is essential for selecting the right valve for a specific application. For instance, in high-pressure applications, valves with robust bodies and reliable seals are necessary to prevent leaks and ensure safety. In environments where corrosion is a concern, valves made from resistant materials like stainless steel or PVC may be preferred. By grasping how each component functions together to control fluid flow effectively, one can better appreciate the complexity and importance of valves in various industrial processes. This foundational knowledge also aids in troubleshooting issues and performing routine maintenance tasks efficiently. Ultimately, recognizing these components helps in optimizing valve performance and ensuring smooth operation across diverse industries.
Applications and Uses of Valves
Valves are indispensable components in various sectors, playing a crucial role in controlling the flow of fluids, gases, and other substances. Their applications span across multiple domains, each with unique requirements and benefits. In industrial settings, valves are essential for maintaining process efficiency and safety. They regulate pressure, temperature, and flow rates in complex systems, ensuring optimal performance and preventing potential hazards. Beyond industrial use, valves also find significant applications in domestic and commercial environments, where they manage water supply, heating systems, and plumbing networks. Additionally, specialized applications of valves can be seen in fields such as aerospace, medical devices, and automotive systems, where precision and reliability are paramount. This article will delve into these diverse uses, starting with the critical role of valves in industrial applications. Transitioning to the first supporting section, we will explore how valves are integral to industrial processes, highlighting their importance in maintaining operational integrity and efficiency.
Industrial Applications
Industrial applications of valves are diverse and critical, playing a pivotal role in various sectors such as oil and gas, chemical processing, power generation, and manufacturing. In the oil and gas industry, valves are essential for controlling the flow of crude oil, natural gas, and refined products. They ensure safe and efficient operations by regulating pressure, preventing leaks, and managing fluid flow rates. For instance, ball valves are commonly used in pipelines to isolate sections for maintenance or repair, while gate valves are preferred for their ability to handle high pressures and large flow volumes. In chemical processing plants, valves must withstand corrosive environments and extreme temperatures. Here, specialized materials like stainless steel or titanium are often used to construct valves that can resist chemical reactions and maintain operational integrity. Butterfly valves and globe valves are popular choices due to their precision control over fluid flow and ability to handle a wide range of pressures and temperatures. The power generation sector relies heavily on valves to manage steam flow in power plants. Control valves regulate the pressure and temperature of steam entering turbines, ensuring optimal energy production. In nuclear power plants, safety valves are crucial for emergency shutdowns and pressure relief, safeguarding against catastrophic failures. In manufacturing facilities, valves are integral to process control systems. They manage the flow of raw materials, intermediate products, and finished goods through various stages of production. Solenoid valves, for example, are used in automated systems to control fluid flow based on electronic signals, enhancing efficiency and reducing manual labor. Furthermore, in water treatment and distribution systems, valves play a vital role in managing water flow and pressure. Check valves prevent backflow, ensuring that contaminated water does not enter the potable water supply. Similarly, in HVAC systems, valves regulate the flow of heating and cooling fluids to maintain consistent indoor temperatures. The aerospace industry also utilizes specialized valves designed for high-performance applications. These valves must operate under extreme conditions such as high pressures, temperatures, and vibrations. They are used in fuel systems, hydraulic systems, and life support systems of aircraft and spacecraft. In addition to these sectors, valves are used in food processing plants to maintain sanitary conditions by controlling the flow of ingredients and cleaning agents. They are also employed in pharmaceutical manufacturing to ensure precise control over chemical reactions and product quality. Overall, the versatility and reliability of valves make them indispensable components across a wide range of industrial applications. Their ability to control fluid flow precisely under various conditions ensures safe, efficient, and cost-effective operations in diverse industries. As technology advances, the development of smart valves with integrated sensors and actuators is further enhancing their functionality and contributing to more sophisticated process control systems.
Domestic and Commercial Uses
Valves are ubiquitous in both domestic and commercial settings, playing a crucial role in managing the flow of fluids, gases, and other substances. In domestic environments, valves are essential for ensuring the smooth operation of various household systems. For instance, water valves control the supply of water to faucets, toilets, and washing machines, while gas valves regulate the flow of natural gas to stoves and heating systems. These valves not only help in conserving resources but also prevent leaks and potential hazards. In addition, thermostatic mixing valves in showers and bathtubs ensure a safe and comfortable water temperature, enhancing user safety and comfort. In commercial settings, the importance of valves is even more pronounced. Industrial plants rely heavily on valves to manage complex processes involving high-pressure fluids, chemicals, and gases. Control valves, for example, are used in manufacturing processes to regulate the flow rate and pressure of fluids, ensuring precise control over production parameters. Ball valves and butterfly valves are commonly used in chemical plants and refineries due to their durability and ease of operation. Moreover, safety valves are critical in preventing over-pressurization in boilers and pipelines, thereby safeguarding equipment and personnel. In the healthcare sector, medical gas valves are vital for delivering oxygen, nitrous oxide, and other gases to patients. These valves must meet stringent safety standards to ensure reliable performance under critical conditions. Similarly, in the food and beverage industry, sanitary valves are designed to prevent contamination and ensure compliance with hygiene regulations. They facilitate the safe processing and packaging of food products without compromising quality or safety. Commercial buildings also benefit significantly from the use of valves. Fire protection systems rely on fire hydrant valves to supply water quickly in case of emergencies, while HVAC systems use control valves to regulate air flow and temperature. In agricultural settings, irrigation valves help farmers manage water distribution efficiently, optimizing crop yields while conserving this precious resource. The versatility of valves extends to various other sectors as well. In automotive manufacturing, fuel valves control the flow of fuel into engines, while in aerospace engineering, specialized valves are used in aircraft fuel systems and hydraulic systems. The marine industry also utilizes valves extensively for managing ballast water, fuel oil, and other critical fluids on ships. In summary, valves are indispensable components across a wide range of domestic and commercial applications. Their ability to control fluid flow precisely makes them crucial for ensuring safety, efficiency, and reliability in diverse settings—from household plumbing to complex industrial processes. As technology continues to evolve, the design and functionality of valves are likely to become even more sophisticated, further enhancing their utility in various sectors.
Specialized Applications
In the realm of industrial and engineering applications, valves play a crucial role in controlling the flow of fluids, gases, and even solids. Specialized applications of valves are diverse and tailored to meet specific needs across various industries. For instance, in the oil and gas sector, high-pressure valves are essential for managing the flow of crude oil and natural gas through pipelines and refineries. These valves must withstand extreme pressures and temperatures, ensuring safe and efficient operations. In the chemical processing industry, valves are often designed with corrosion-resistant materials to handle hazardous chemicals. Here, the focus is on maintaining purity and preventing contamination, which is critical for producing high-quality chemicals. Similarly, in pharmaceutical manufacturing, sanitary valves are used to ensure that the production environment remains sterile and compliant with stringent regulatory standards. Aerospace and defense industries also rely heavily on specialized valves. For example, cryogenic valves are used in rocket propulsion systems to manage the flow of extremely cold fluids such as liquid oxygen and liquid hydrogen. These valves must be highly reliable and capable of operating under extreme conditions to support the success of space missions. In the medical field, precision is paramount. Medical gas valves are designed to deliver precise amounts of oxygen, nitrous oxide, and other gases to patients in hospitals and clinics. These valves are engineered with safety features to prevent accidental over- or under-delivery of gases, ensuring patient safety. Furthermore, in the automotive industry, fuel system valves are critical for engine performance and efficiency. These valves control fuel flow into the engine's combustion chamber, optimizing fuel consumption and reducing emissions. Similarly, in HVAC systems, thermostatic expansion valves regulate refrigerant flow to maintain consistent temperatures and humidity levels in buildings. Marine applications also utilize specialized valves to manage seawater intake for cooling systems on ships and offshore platforms. These seawater valves must be resistant to corrosion from saltwater and capable of handling high volumes of flow. Additionally, nuclear power plants employ nuclear-grade valves that are designed to withstand the unique conditions of a nuclear environment. These valves are built with materials that can resist radiation and maintain their integrity even in the event of an emergency. Lastly, in renewable energy systems like solar thermal power plants, specialized valves control the flow of molten salt or other heat transfer fluids. These valves are engineered to handle high temperatures and ensure efficient heat transfer, which is crucial for generating electricity. In summary, specialized applications of valves span a wide range of industries, each requiring unique designs and materials to meet specific operational demands. Whether it's managing high pressures in oil pipelines or delivering precise amounts of medical gases, these valves play a vital role in ensuring safety, efficiency, and reliability across diverse sectors. Their versatility underscores the importance of valves as fundamental components in modern engineering and industrial processes.
Operational Principles and Maintenance
Operational principles and maintenance are crucial components in ensuring the efficiency and longevity of industrial systems. Understanding these principles is essential for optimizing performance, reducing downtime, and enhancing overall system reliability. This article delves into three key areas that form the backbone of effective operational management: how valves work, installation and setup, and maintenance and troubleshooting. Firstly, comprehending **how valves work** is fundamental to grasping the intricate mechanisms that control fluid flow within a system. Valves are critical components that regulate pressure, flow rate, and direction, making their proper functioning vital for system integrity. Secondly, **installation and setup** play a pivotal role in ensuring that all components are correctly integrated into the system. Proper installation not only prevents immediate failures but also sets the stage for long-term operational success. Lastly, **maintenance and troubleshooting** are ongoing processes that help identify and rectify issues before they escalate into major problems. Regular maintenance ensures that systems operate at peak efficiency, while effective troubleshooting techniques minimize downtime and optimize repair processes. By understanding these interconnected aspects, operators can ensure that their systems run smoothly, efficiently, and safely. Let's begin by exploring the foundational element of this triad: **how valves work**.
How Valves Work
Valves are crucial components in various industrial, mechanical, and plumbing systems, serving as control devices that regulate the flow of fluids such as liquids, gases, and slurries. Understanding how valves work is essential for their effective operation and maintenance. At the heart of a valve's functionality lies its ability to open, close, or partially obstruct the flow path, thereby controlling pressure, flow rate, and direction. ### Operational Principles 1. **Basic Components**: A typical valve consists of a body, bonnet, trim (which includes the seat and disc), stem, and actuator. The body houses the fluid flow path, while the bonnet covers the valve internals. The trim components interact to control the flow. 2. **Flow Control Mechanism**: When a valve is operated, the disc or plug moves relative to the seat. In an open position, the disc is lifted off the seat, allowing fluid to pass through. Conversely, when closed, the disc seals against the seat, stopping fluid flow. Partial opening allows for throttling or regulation of flow. 3. **Actuation**: Valves can be actuated manually via a handle or automatically through electric motors, pneumatic or hydraulic actuators. These actuators apply force to the stem, which in turn moves the disc or plug. 4. **Types of Valves**: Different types of valves serve specific purposes: - **Globe Valves**: Used for precise control and throttling. - **Ball Valves**: Known for their quick operation and full-bore flow. - **Butterfly Valves**: Ideal for large diameter pipes due to their compact design. - **Check Valves**: Prevent backflow by allowing fluid to flow in one direction only. ### Maintenance Proper maintenance is vital to ensure valves operate efficiently and reliably over their lifespan. 1. **Regular Inspection**: Periodic checks help identify potential issues such as wear on moving parts, corrosion, or blockages. Visual inspections can reveal signs of leakage or damage. 2. **Cleaning and Lubrication**: Cleaning valve components and lubricating moving parts prevent friction and wear. This is particularly important for valves in harsh environments where contaminants may accumulate. 3. **Replacement of Parts**: Worn-out parts such as gaskets, seals, and O-rings should be replaced promptly to maintain valve integrity. The stem packing may also need periodic replacement to prevent leakage. 4. **Testing**: Functional testing ensures that valves operate correctly under various conditions. This includes checking for proper sealing when closed and smooth operation during opening and closing cycles. 5. **Documentation**: Keeping detailed records of maintenance activities helps in tracking the history of each valve, facilitating future maintenance schedules and troubleshooting. In summary, understanding the operational principles of valves—how they control fluid flow through precise mechanisms—and adhering to a rigorous maintenance schedule are key to ensuring these critical devices function optimally. By recognizing the importance of regular inspections, cleaning, lubrication, part replacement, testing, and documentation, operators can extend the lifespan of valves while maintaining system efficiency and safety. This comprehensive approach not only enhances operational reliability but also minimizes downtime and reduces maintenance costs in the long run.
Installation and Setup
When it comes to the operational principles and maintenance of valves, the installation and setup process is crucial for ensuring optimal performance and longevity. Proper installation involves several key steps that must be meticulously followed to avoid potential issues down the line. First, it is essential to select the correct valve type and size for the specific application, taking into account factors such as flow rate, pressure, and compatibility with the fluid being handled. Once the appropriate valve is chosen, the next step involves preparing the installation site by ensuring that all piping connections are clean and free from debris. The valve should then be inspected for any damage or defects before being mounted onto the piping system. This includes checking for any signs of wear on moving parts, verifying that all seals and gaskets are intact, and ensuring that any actuators or control mechanisms are functioning correctly. During the actual installation, it is vital to follow the manufacturer's instructions closely, paying particular attention to torque specifications for bolts and screws to prevent over-tightening which could lead to damage. After the valve is securely in place, it should be tested under no-load conditions to verify proper operation. This includes checking for leaks at all connections and ensuring that the valve opens and closes smoothly without any signs of sticking or binding. Additionally, any control systems or actuators should be calibrated according to the manufacturer's guidelines to ensure precise control over valve operation. Regular maintenance is also a critical component of valve setup and installation. This includes periodic inspections to check for signs of wear or corrosion, cleaning or replacing filters if applicable, and lubricating moving parts as needed. Proper documentation of maintenance activities is also important for tracking the history of the valve and identifying potential issues before they become major problems. In summary, the installation and setup of valves require careful planning and execution to ensure they operate efficiently and reliably over their lifespan. By selecting the right valve for the job, following manufacturer guidelines during installation, conducting thorough testing, and maintaining regular upkeep, users can maximize the performance of their valves while minimizing downtime and maintenance costs. This meticulous approach not only enhances operational efficiency but also contributes significantly to overall system reliability and safety.
Maintenance and Troubleshooting
### Maintenance and Troubleshooting Effective maintenance and troubleshooting are crucial for ensuring the optimal performance and longevity of valves in various industrial applications. Regular maintenance involves a series of scheduled activities designed to prevent valve failure, reduce downtime, and maintain operational efficiency. This includes routine inspections to check for signs of wear, corrosion, or damage. For instance, visual inspections can help identify issues such as leaks, misalignment, or excessive vibration. Additionally, functional tests should be conducted periodically to verify that the valve operates correctly within its specified parameters. Proper lubrication is another key aspect of valve maintenance. Lubricants help reduce friction between moving parts, thereby extending the lifespan of the valve and improving its overall performance. It is essential to use the correct type and amount of lubricant as specified by the manufacturer to avoid compromising the valve's integrity. Troubleshooting, on the other hand, involves diagnosing and resolving issues that arise during valve operation. A systematic approach is often the most effective method for troubleshooting. This begins with identifying symptoms such as erratic operation, reduced flow rates, or complete failure. Next, potential causes are analyzed based on historical data, maintenance records, and operational conditions. Common issues include clogged or dirty valve components, incorrect installation, or improper sizing for the application. In many cases, troubleshooting can be facilitated by using diagnostic tools such as pressure gauges and flow meters to measure performance metrics against baseline values. Advanced technologies like condition monitoring systems and predictive analytics can also be employed to detect anomalies before they lead to significant problems. Documentation plays a vital role in both maintenance and troubleshooting processes. Detailed records of maintenance activities, inspections, and repairs help in tracking the history of the valve and identifying recurring issues. These records also serve as valuable resources for training new personnel and ensuring compliance with regulatory standards. Moreover, adherence to manufacturer guidelines and industry standards is paramount. Following recommended maintenance schedules and procedures ensures that valves operate within their design specifications, thereby minimizing risks associated with premature failure or malfunction. In summary, a well-structured maintenance program combined with effective troubleshooting strategies is essential for maintaining valve performance, reducing operational costs, and enhancing overall system reliability. By integrating these practices into operational routines, industries can ensure that their valves function optimally over their lifespan, contributing significantly to the efficiency and safety of their operations.